3D Printing with Carbon Fibre: Innovations and Applications
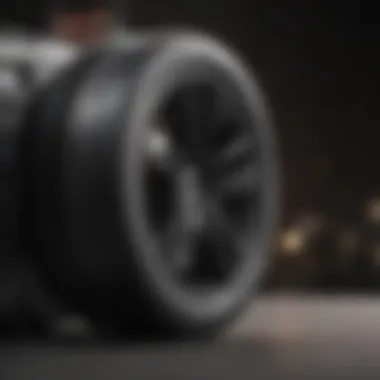
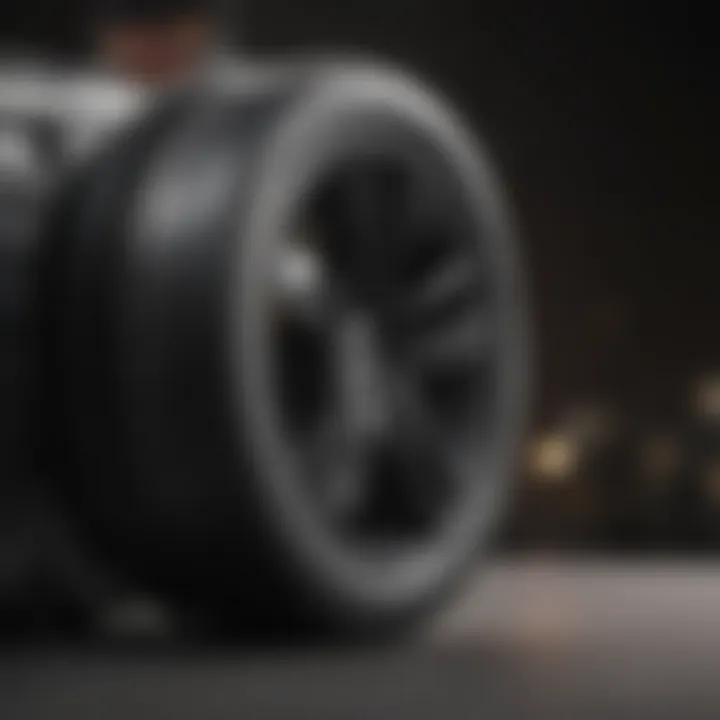
Intro
3D printing technology has evolved significantly over the past decade. One exciting development is the incorporation of carbon fibre into additive manufacturing processes. This integration offers numerous advantages, particularly in enhancing the structural integrity and mechanical properties of 3D-printed components. The current landscape of this technology is both innovative and challenging, making it crucial for professionals and researchers to explore its applications and benefits.
As industries continue to seek lighter, stronger, and more durable materials, carbon fibre emerges as a viable option. Its unique properties provide remarkable enhancements that traditional materials cannot offer. This article will cover the blended aspects of carbon fibre in 3D printing, including practical applications and future directions.
Research Context
Background and Rationale
The demand for high-performance materials in manufacturing has increased, driven by aerospace, automotive, and healthcare sectors. Incorporating carbon fibre into 3D printing meets these requirements effectively. Carbon fibre reinforced composites offer high strength-to-weight ratios and excellent rigidity, making them ideal for a wide range of applications, including prototyping and end-use parts. However, this technology has not yet reached its full potential. Challenges remain in processing, material costs, and quality control, necessitating further exploration.
Literature Review
Current research highlights the significant advancements in 3D printing methods that enable the use of carbon fibre. Studies have explored various aspects, such as:
- Material Properties: The unique characteristics of carbon fibre composites,
- Production Techniques: Innovations in additive manufacturing techniques for carbon fibre,
- Application Areas: Diverse fields where these materials are being increasingly adopted.
Emerging literature indicates a growing body of work focused on optimizing processes and addressing challenges. For example, a study published in the Journal of Composite Materials examined the mechanical performance of carbon fibre reinforced parts produced using Fused Deposition Modeling (FDM) technique. These findings indicate that fine-tuning the printing parameters can maximize the benefits while minimizing defects.
"As the market for carbon fibre 3D printing expands, it is evident that research on this material will continue to evolve, leading to more refined methods and innovative applications."
Collaborative efforts among researchers, manufacturers, and industry stakeholders have begun to bridge the gap between theoretical advancements and practical implementations. Such synergy is essential for the continued growth and optimization of carbon fibre 3D printing technologies.
Intro to 3D Printing and Carbon Fibre
The integration of carbon fibre in 3D printing represents a significant advancement in additive manufacturing. This development has opened new avenues for industries that demand high-performance materials. Carbon fibre is prized for its numerous desirable properties, including exceptional strength and lightweight characteristics. Its use within 3D printing enables the creation of components that are both strong and cost-effective to produce.
In this article, we will explore how carbon fibre enhances the 3D printing process. We will highlight innovations and practical applications, addressing how professionals and researchers can benefit from this technology. Furthermore, the challenges and future potential of carbon fibre printing will be discussed, enriching the reader's understanding of its role in industry developments.
Understanding 3D Printing
3D printing, also known as additive manufacturing, involves the layer-by-layer construction of objects from digital files. This technology has evolved rapidly, and its applications span various sectors, from aerospace to medical devices. Unlike traditional manufacturing methods, 3D printing allows for greater design flexibility and material efficiency. The ease of creating complex geometries with less waste sets it apart.
As 3D printing becomes more mainstream, there is a growing interest in incorporating advanced materials. Carbon fibre is one such material that brings unique benefits to the table. Its adoption in 3D printing can significantly enhance the mechanical properties of printed parts while maintaining a reduced weight profile.
What is Carbon Fibre?
Carbon fibre is a strong, lightweight material made from thin strands of carbon atoms bonded together in a crystalline structure. The result is a material exhibiting high tensile strength and rigidity. Carbon fibre is often combined with other substances, typically epoxy resins, to form composite materials that further improve its performance characteristics.
This material has applications in various industries, such as aerospace, automotive, and sports equipment. Its use in 3D printing allows for the fabrication of complex components without compromising durability. Understanding the properties of carbon fibre is essential for recognizing how it elevates the capabilities of 3D printing.
"Carbon fibre composites can reduce weight while improving strength, making them ideal for advanced manufacturing."
The inclusion of carbon fibre into the additive manufacturing process marks a turning point in how industries approach design and production. This study will set the stage for further exploration of its mechanical properties in subsequent sections.
Properties of Carbon Fibre
Understanding the properties of carbon fibre is crucial in the context of 3D printing. This material exhibits unique characteristics that greatly enhance the performance of 3D-printed components. It is essential for professionals and researchers to comprehend these properties, as they can influence material selection and design decisions in various applications.
Mechanical Strength
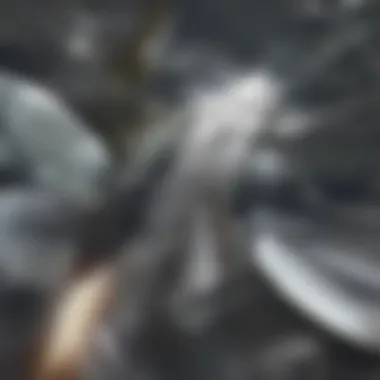
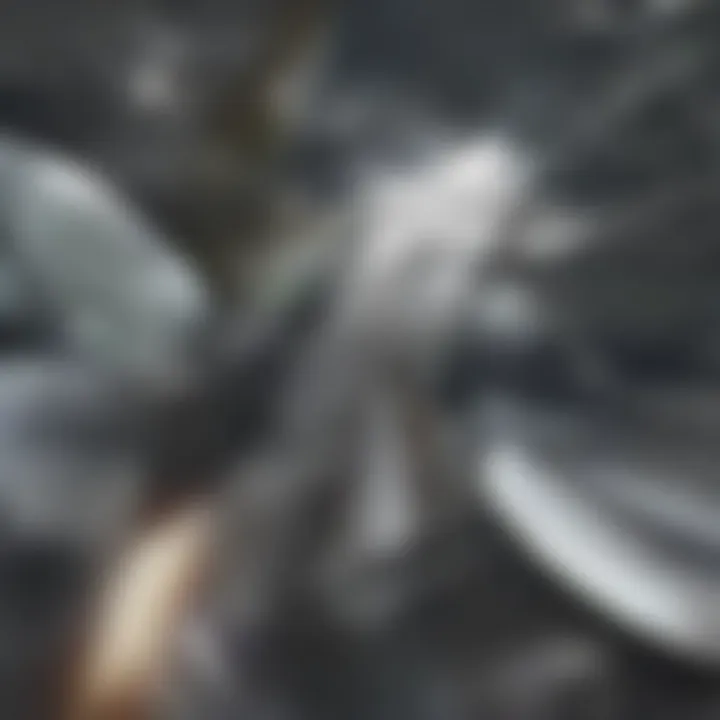
Mechanical strength is one of the standout properties of carbon fibre. It can withstand significant forces without deforming, making it an excellent choice for components that face high stress. For instance, in aerospace and automotive sectors, parts made from carbon fibre often outperform those made from conventional materials like aluminum or steel. This resilience comes from its high tensile strength, which is beneficial for structures that need durability and reliability. The ability of carbon fibre to hold up under intense stresses ensures its growing popularity in demanding sectors.
Weight-to-Strength Ratio
Another significant aspect of carbon fibre is its impressive weight-to-strength ratio. Carbon fibres are lightweight yet incredibly strong, which allows for the creation of components that do not compromise on strength while reducing overall weight. This characteristic is particularly valuable in industries such as aerospace, where reducing weight can lead to improved fuel efficiency and performance. For example, when integrated into composite structures, carbon fibre enables manufacturers to produce lighter and more efficient aircraft.
Chemical Resistance
Carbon fibre also displays excellent chemical resistance. It is less susceptible to corrosion and degradation when exposed to various chemicals compared to metal materials. This property is vital in environments where components may encounter harsh substances, such as in medical devices or chemical processing industries. The ability to maintain integrity in such conditions can extend the lifespan of products significantly, representing a strong advantage for manufacturers.
"The unique properties of carbon fibre not only enhance performance but also offer new avenues for design and engineering innovations."
3D Printing Methods for Carbon Fibre
In the context of 3D printing, the choice of method significantly influences the quality and properties of the final product. When dealing with carbon fibre, these methods enable the effective integration of the material's distinctive attributes into the additive manufacturing process. This section will explore the various techniques utilized to print with carbon fibre, focusing on their advantages, limitations, and conditions for optimal results.
Fused Deposition Modelling
Fused Deposition Modelling (FDM) is one of the most widely used methods in 3D printing. It involves melting a thermoplastic filament that contains carbon fibre and extruding it layer by layer to create an object. This approach is advantageous for its simplicity and accessibility. It can be operated with various desktop printers, thus appealing to both professionals and hobbyists.
When employing FDM with carbon fibre, the benefits include:
- Increased Strength: Carbon fibre reinforcement enhances the mechanical properties of the thermoplastic, leading to stronger and more durable parts.
- Weight Reduction: This combination offers a lower weight without compromising on strength compared to traditional materials.
- Cost-Effectiveness: FDM equipment and filament are relatively affordable, making it an attractive option for many applications.
However, specific considerations must be taken into account:
- Nozzle wear: Due to the abrasive nature of carbon fibre, the print nozzles may wear down faster, requiring regular replacement.
- Limited precision: Compared to other methods, FDM may not achieve the same level of detail, especially in complex geometries.
Selective Laser Sintering
Selective Laser Sintering (SLS) utilizes a high-powered laser to fuse powdered material into solid structures. This technology is particularly well-suited for carbon fibre applications due to its capability to produce intricate parts with excellent mechanical properties. The process allows for the creation of complex geometrical shapes that are not feasible with traditional methods.
Key advantages include:
- High Accuracy and Precision: SLS achieves fine detail and dimensional accuracy, resulting in carefully crafted components.
- Material Flexibility: It can work with a variety of materials in a single build, enhancing design versatility.
- No Support Structures Needed: The unsintered powder can support the object during printing, eliminating the need for separate support structures, thus reducing waste.
Nonetheless, there are some challenges with SLS printing:
- High Equipment Cost: The machinery required for SLS is generally more expensive, which may limit accessibility for smaller operations.
- Post-Processing: Parts typically require cleaning and finishing steps, which can prolong production time.
Binder Jetting
Binder Jetting is another prominent method for 3D printing with carbon fibre. This technique follows a layer-by-layer approach where a binding agent is selectively applied to powdered material, leading to a solidified object once sintered or cured. This method is particularly effective for producing large parts quickly and with minimal wastage.
Some inherent benefits include:
- Rapid Prototyping: The speed of the process allows designers to produce prototypes in a short time frame, making it ideal for testing.
- Variety of Materials: Binder Jetting can incorporate various materials, offering ample opportunities for innovation.
- Cost Efficiency: Generally, the materials and operation costs tend to be lower than some other printing methods.
However, important factors must be considered:
- Weaker Bonding: The mechanical strength can be lower compared to SLS and FDM, which may limit its use in load-bearing applications.
- Need for Post-Processing: Final parts often require additional treatments to achieve desired strengths and finishes.
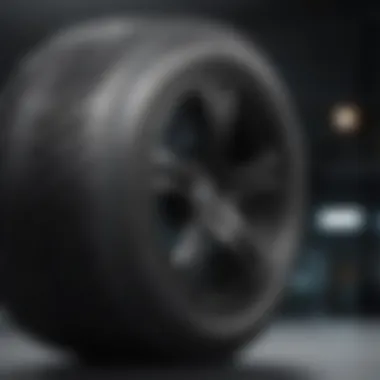
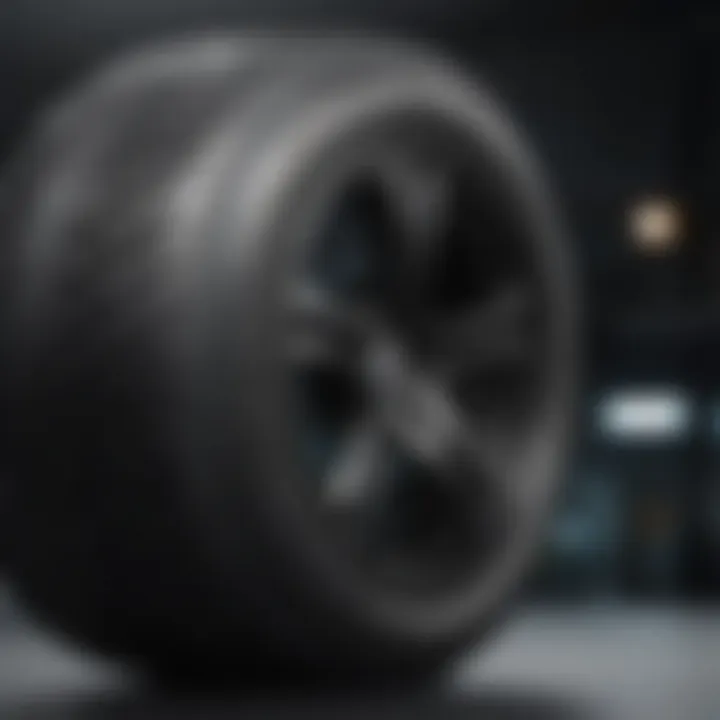
By understanding each method’s characteristics, one can choose the most suitable technique for specific applications in carbon fibre 3D printing.
Applications in Industry
The integration of carbon fibre into 3D printing has opened new pathways for various industries. The lightweight, strong nature of carbon fibre gives it a marked advantage in practical applications. This section will delve deeper into the specific sectors where these materials demonstrate the most potential, discussing the benefits as well as considerations that come into play. Understanding these applications is crucial for professionals seeking to innovate within their fields, especially as materials science evolves.
Aerospace Sector
In the aerospace sector, the significance of weight savings and improved mechanical properties cannot be overstated. Aircraft components often require materials that can withstand extreme conditions while reducing overall weight. Carbon fibre-reinforced 3D printing provides a solution by enabling the manufacturing of custom parts that meet these stringent requirements.
- Benefits:
- Weight Reduction: With reduced weight in aircraft design, fuel efficiency improves, resulting in lower operational costs.
- Customizable Parts: Designers can easily iterate and create complex geometries tailored to specific aircraft models.
- Strength: Carbon fibre enhances the tensile strength of components, crucial for safety and durability.
Despite its advantages, challenges exist, such as the need for strict regulations and certification processes before parts can be deployed in aircraft. Innovations in material science within this sector continue to push boundaries, making it a focus area for research and application.
Automotive Manufacturing
Automotive manufacturing has also started to reap the benefits of 3D printing with carbon fibre. Car manufacturers look for ways to enhance performance, aesthetics, and sustainability. Carbon fibre composites can replace heavier materials, optimizing vehicle structures.
- Benefits:
- Performance Enhancements: Vehicles become more agile and responsive due to the weight savings, improving handling and acceleration.
- Customization: 3D printing facilitates unique product offerings, like personalized car interiors or bespoke parts tailored to specific customer needs.
- Reduced Waste: Additive manufacturing minimizes material waste compared to traditional subtractive methods.
The shift toward electric vehicles, which require lightweight materials for better battery efficiency, further solidifies the role of carbon fibre in automotive innovation.
Medical Devices
In the medical industry, the demand for precision and customization has led to increased interest in carbon fibre 3D printing. Medical devices often have rigorous demands for both function and biocompatibility.
- Benefits:
- Customized Implants: Tailoring implants to fit patients improves outcomes and satisfaction.
- Durable Construction: Carbon fibre’s strength and lightweight properties enhance device functionality while also reducing patient discomfort.
- Rapid Prototyping: The ability to quickly produce prototypes aids in faster development cycles for new technology.
However, the medical sector faces regulatory challenges unique to its environment. Ensuring biocompatibility and regulatory compliance adds complexity to the adoption of these advanced materials.
Consumer Products
Carbon fibre is not just for industrial applications; it also makes its mark on consumer products. From sports equipment to electronics, the lightweight and strong properties offer compelling advantages in this market.
- Benefits:
- Enhanced Performance: Sporting goods made with carbon fibre often improve performance, like better racquet power and control.
- Aesthetic Appeal: The unique look of carbon fibre can add an element of luxury and style to consumer goods.
- Durability: Products experience higher resistance to wear and tear, extending product life.
In summary, carbon fibre's applications across multiple sectors underscore its transformative potential in improving both functionality and aesthetics. This material's advancement is pivotal for engineers, designers, and industry stakeholders focused on innovation in 3D printing. The conversation surrounding carbon fibre's role will only continue as technology advances, driving further exploration and application.
Challenges in Carbon Fibre 3D Printing
The integration of carbon fibre in 3D printing presents a host of challenges alongside its benefits. Understanding these obstacles is crucial for professionals and researchers aiming to optimize additive manufacturing processes. The key issues include material costs, the complexity of the printing process, and stringent post-processing requirements. Addressing these concerns is vital not only for achieving efficient production but also for enhancing overall product quality.
Material Costs
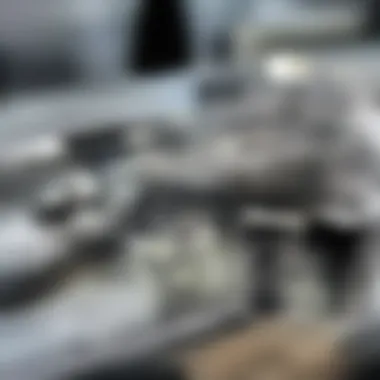
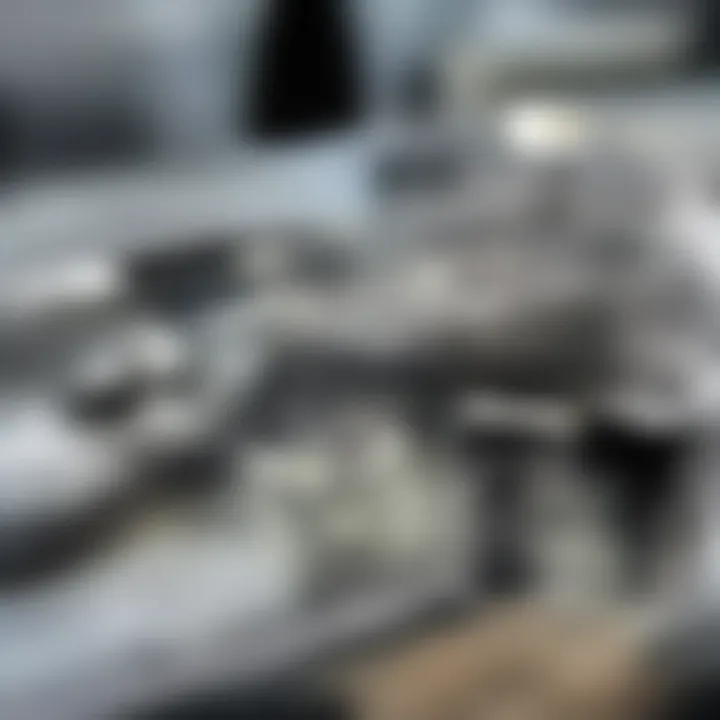
The use of carbon fibre in 3D printing can incur significant costs. The raw materials are often pricier compared to traditional plastics. This high initial investment can deter many businesses from adopting carbon fibre printing. Prices vary due to factors such as type, supplier, and demand. Generally, carbon fibre filaments can be three to ten times the price of standard filaments like PLA or ABS.
Furthermore, the process of creating carbon fibre composites can contribute to these costs. The need for specialized equipment and technology to handle such materials adds another layer of expense. For smaller companies or startups, this may make the utilization of carbon fibre impractical if not paired with a solid market strategy that justifies the investment.
Printing Process Complexity
The complexity involved in carbon fibre 3D printing cannot be overlooked. The unique properties of carbon fibre require particular attentiveness in the printing process. For example, high-temperature extruders and reinforced nozzles are essential because standard components may wear quickly. This is a result of carbon fibre’s abrasive nature, which leads to wear and tear of the machinery.
Moreover, the layer adhesion in carbon fibre printing necessitates specific settings such as temperature and speed adjustments. If not well-calibrated, printed objects may suffer from structural weaknesses or warped geometries. Because of this added complexity, more training is required for technicians and engineers to operate the machinery effectively. Ultimately, a steep learning curve exists for those transitioning to this advanced form of 3D printing.
Post-Processing Requirements
Post-processing is another critical aspect of carbon fibre 3D printing that adds to its challenges. Once the printing phase is complete, many objects require finishing steps to enhance their strength and appearance. This might include sanding, curing, or coating to address surface quality or to improve mechanical properties.
Each post-processing step can be labor-intensive and time-consuming. Some techniques, like curing, require specialized ovens or chambers where conditions must be meticulously controlled. Failing to properly finish parts can lead to a significant reduction in performance, particularly for applications in aerospace and automotive sectors where precision is paramount.
Overall, these challenges serve as important reminders that while carbon fibre offers numerous advantages, careful consideration and planning are required to mitigate the associated complications. As technology advances, however, innovation may lead to solutions that lower costs and simplify processes, ultimately enhancing the adoption of carbon fibre in 3D printing.
Future Trends in 3D Printing with Carbon Fibre
The advancement of technology in 3D printing with carbon fibre brings significant potentials for future applications. As industries strive for innovation, keeping an eye on emerging trends is critical. This section will explore essential elements such as biocompatible materials, sustainability practices, and the integration of smart technologies. Each aspect is vital for the evolution of additive manufacturing, especially in relation to carbon fibre.
Biocompatible Materials
The use of biocompatible materials in 3D printing is becoming increasingly prevalent. This development is crucial for creating medical devices and components that interact with the human body. Researchers are focusing on developing carbon fibre composites combined with biopolymers. These materials can offer mechanical strength while remaining compatible with biological systems. Such advancements could lead to better implants, prosthetics, and tissue engineering products. The potential of biocompatible carbon fibre materials presents exciting opportunities for innovating healthcare solutions.
"The future of medical applications relies on biocompatibility and functional strength of materials."
Sustainability Practices
Sustainability is a major focus in today’s production methods. 3D printing with carbon fibre must incorporate sustainable practices to address environmental concerns. One approach is to use recycled carbon fibres, which reduces waste and lowers the carbon footprint. Another important trend is the development of bio-resins that can replace traditional polymer resins, thus making the process more eco-friendly. Organizations are also seeking to optimize energy consumption during the printing process. Implementing these sustainable practices not only benefits the environment but enhances the brand reputation of companies involved in additive manufacturing.
Integration with Smart Technologies
The rise of smart technologies in various fields is creating new possibilities for 3D printing with carbon fibre. This integration allows for the production of components that are not only strong but also intelligent. Smart sensors can be embedded within printed carbon fibre parts to monitor structural health and performance metrics in real-time. Additionally, integrating IoT capabilities can enhance production processes through better data analytics and predictive maintenance. As these trends continue to develop, companies will increasingly leverage this technology to gain a competitive edge in the market.
In summary, the future of 3D printing with carbon fibre lies significantly in its ability to innovate through biocompatible materials, adopt sustainable practices, and embrace smart technologies. These trends not only promise to enhance current applications but also position industries for groundbreaking advancements in the years to come.
Finale
The conclusion ties together the various threads of discussion presented throughout the article on 3D printing with carbon fibre. It highlights the importance of these advancements, which are reshaping manufacturing landscapes in various sectors. By integrating carbon fibre materials, industries can benefit from exceptional mechanical strength, lightweight structures, and superior durability. The concluding sections address not just the innovations but also the practical applications that have emerged as a direct result of these advancements.
Summary of Key Points
In summary, carbon fibre combined with 3D printing technology presents numerous benefits:
- Enhanced mechanical properties leading to stronger components.
- Reduction in weight, resulting in overall efficiency improvements in sectors like aerospace and automotive.
- Versatility across different applications, from high-performance sports equipment to complex medical devices.
These factors collectively contribute to the growing adoption of 3D printing techniques using carbon fibre, making it a focal point for future innovations.
Implications for Future Research
Future research in this field should focus on:
- Developing more cost-effective methods to produce carbon fibre materials for 3D printing.
- Enhancing printing technologies to reduce complexities and increase accessibility for diverse industries.
- Exploring bio-compatible carbon fibre for medical applications, which aligns with the growing demand for sustainable practices in materials science.
Investing in these areas may unlock new potentials for carbon fibre applications, further broadening its benefits. As researchers and practitioners engage in this exploration, the implications for improved product performance and sustainability will be significant.