3D Printing in Denture Fabrication: A New Era for Dentistry
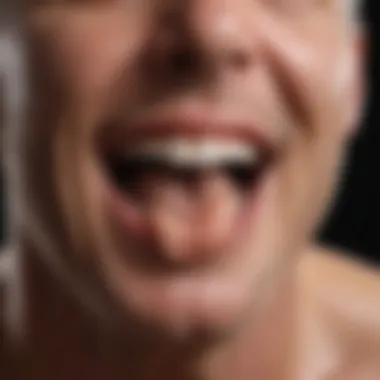
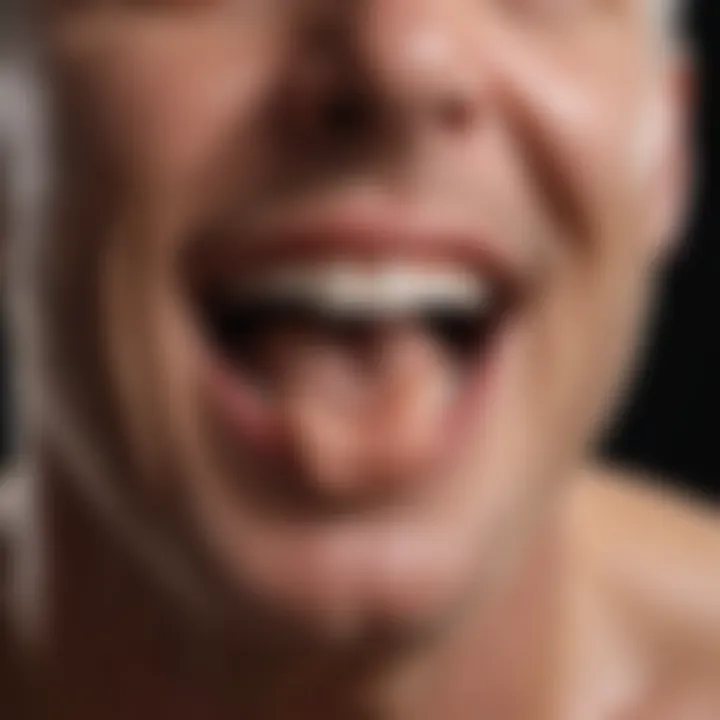
Research Context
Background and Rationale
The advent of 3D printing technology has fundamentally transformed various fields, and the dental sector is no exception. Traditional methods for fabricating dentures often come with numerous challenges, such as the time-consuming process and the limitations of materials in providing an accurate fit. By integrating 3D printing, there's potential not only to streamline production but also to enhance personalization for each patient. This shift from conventional practices to innovative technological applications presents numerous opportunities, significantly influencing patient satisfaction and practice efficiency.
Literature Review
Research surrounding 3D printing in dental prosthetics is gaining traction. A multitude of studies illustrate how digital workflows can optimize the production and design of dentures. For instance, relevant literature highlights how materials such as photopolymer resins exhibit strong mechanical properties while being biocompatible. Moreover, the iterative nature of 3D printing facilitates the creation of personalized, precise, and lightweight dentures, which can significantly improve the comfort and experience for users. Experts in dental materials have begun to advocate for the shift towards this technology, suggesting that it brings forth not only improvements in quality but comes with cost efficiencies as well.
"The transition to 3D printing in dentistry isn't just a trend; it's a paradigm shift that allows for custom solutions tailored to individual needs."
Methodology
Research Design
To delve deeper into the multi-faceted impacts of 3D printing in dental prosthetics, a descriptive research design is utilized. This design facilitates a thorough exploration of how materials, methods, and technologies converge to provide solutions for dental professionals. Understanding the existing practices as well as the emerging technologies creates a rich context for evaluating their effectiveness and practicality.
Data Collection Methods
Data for this exploration is collected through a blend of qualitative and quantitative sources, including:
- Reviews of academic journals and publications for relevant studies.
- Insights gathered from interviews with dental practitioners whoāve adopted 3D printing technology.
- Patient feedback specifically regarding the comfort and functionality of 3D printed dentures.
- Analysis of case studies to illustrate both the benefits and challenges encountered in real-world scenarios.
This varied approach ensures a comprehensive understanding of 3D printing's role in denture manufacturing, allowing for an informed discussion on its future in dental practices.
Preface to 3D Printing in Dentistry
The dental industry is shuffling its deck as 3D printing emerges as a game-changing option for producing dentures. Understanding this technology is not just for tech-savvy innovators; it plays a crucial role in enhancing patient care and streamlining dental practices. This article sets the stage for an in-depth conversation about how 3D printing is altering the landscape of denture manufacture, making it a focal point for practitioners, educators, and researchers.
The shift from traditional methods to 3D printing techniques brings several tangible benefits. First and foremost, personalized care has become more feasible. No longer do patients have to settle for one-size-fits-all solutions. Instead, denture fabrication can now incorporate each patientās unique anatomy, significantly improving comfort and functionality. Beyond customization, the speed at which these dentures can be produced also stands out. Instead of weeks or months, patients can often receive their dentures in a fraction of the time.
However, itās essential to consider not just the perks but also the challenges attached to this newfangled approach. Regulatory hurdles and material limitations can complicate the process and might make some practitioners wary. Therefore, understanding both the pros and cons is imperative for anyone involved in dental prosthetics.
In summary, the significance of 3D printing in dentistry extends beyond mere trends. It's reshaping how dental professionals interact with their patients, confirming the technological mindset thatās increasingly taking hold in dental practices.
Historical Overview of Denture Manufacturing
The journey of denture manufacturing is a tale that reflects the technological progression within dentistry. Initially, dentures were crafted using materials like ivory and animal bone, requiring artisans to rely heavily on their manual skills. These early dentures were often uncomfortable and not particularly aesthetically pleasing. Patient satisfaction was typically low, and many patients had to endure ill-fitting and cumbersome appliances. The methods and materials varied widely, and the lack of standardization meant reliability was an issue.
As time progressed, the introduction of vulcanized rubber in the 19th century revolutionized the industry. Dentists began to embrace this material for its durability and more natural appearance. However, the same problems lingered for many; adjustment processes took long, and the time needed to fabricate a pair of dentures could span several visits.
The late 20th century saw the adoption of computer-aided design in dental practices, laying the groundwork for current digital approaches. Traditional methods remained predominant, but an exciting shift was on the horizon.
The Emergence of 3D Printing Technology
The advent of 3D printing technology in the manufacturing of dentures can be likened to a breath of fresh air. While traditional methods relied heavily on time-consuming processes and the skill of technicians, 3D printing introduces automation and precision. Whatās more, it empowers dental practitioners to create tailored solutions efficiently.
From the first prototypes in the mid-1990s to the current state-of-the-art models, the timeline of 3D printing is a fascinating one. Early applications focused on quick prototypes; however, advancements have led to the production of actual dental components. Today, one can find machines that sculpt, mold, and refine materials into highly accurate dentures, sometimes with astounding efficiency.
3D printing has also opened doors to a variety of materials that were previously difficult or impossible to utilize in denture manufacturing. This evolution provides dentists with tools that align better with patient needs while maintaining strong performance standards.
The technological evolution in denture manufacturing mirrors the rapid changes in dental practices and patient care methods, often enhancing the overall experience for both parties.
Understanding 3D Printing Techniques
In the realm of dentistry, understanding 3D printing techniques is crucial for grasping how this technology reshapes the fabrication of dentures. The right method impacts everything from design precision to the durability of the final product. This section digs into the core of techniques that fuel 3D printing, examining the merits and specifics that make each one unique. Knowing these techniques allows dental professionals to select the most suitable options, enhancing patient outcomes and streamlining production efficiency.
Common 3D Printing Methods Used in Dentistry
Several methods of 3D printing are utilized in dental applications, each with its strengths. Here are the most common ones:
- Stereolithography (SLA): This technique deploys a UV laser to cure photosensitive resin layer by layer, yielding highly accurate models with smooth finishes.
- Selective Laser Sintering (SLS): In this approach, powdered materials are fused together using a laser, creating durable and flexible products.
- Fused Deposition Modeling (FDM): FDM extrudes thermoplastic filaments through a heated nozzle, building objects layer by layer, which is often more accessible and cost-effective.
Being familiar with these methods provides invaluable insight for those venturing into the world of 3D printed dentures. Each method has its unique characteristics that cater to different needs in the dental realm.
Comparative Analysis of Printing Technologies
Diving deeper into the specifics, letās compare these primary technologies, revealing how they contribute uniquely to denture production.
SLA (Stereolithography)
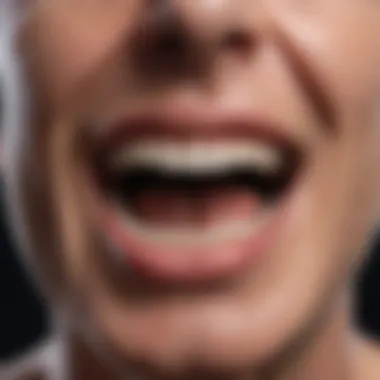
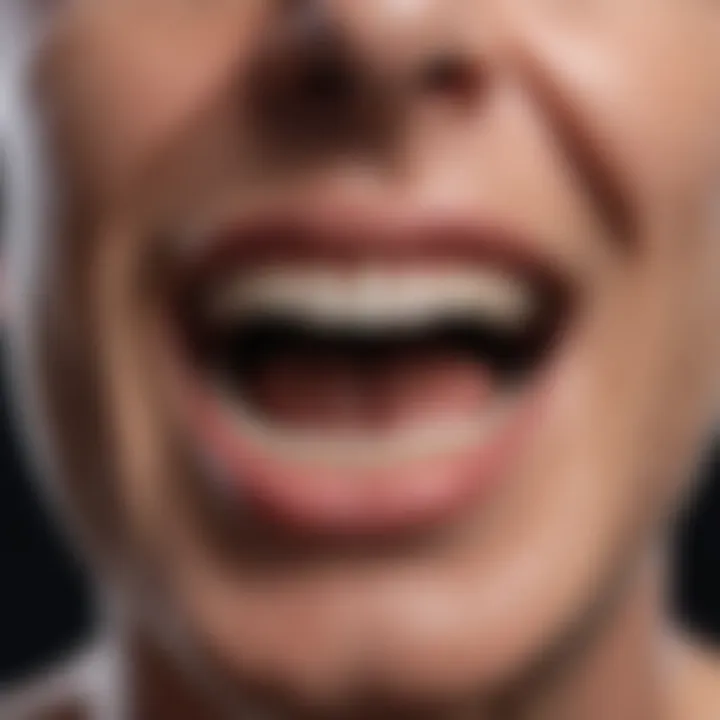
Stereolithography is admired for its pristine accuracy, making it a popular choice for detailed dental work. One of its significant advantages is the smooth surface finish it imparts, minimizing post-processing effort. The key characteristic of SLA is its use of photopolymer resins, which allows for fine-tuned detail in complex denture designs. However, this technology comes with a higher cost of materials and print time, potentially placing it out of reach for some practices.
"The clarity of detail available with SLA can transform prosthetics from merely functional to visually pleasing, thus enhancing patient satisfaction."
SLS (Selective Laser Sintering)
Selective Laser Sintering stands out due to its ability to handle multiple material types, providing versatility over rigid materials. This adaptability makes it an appealing choice when durability is crucial. A key characteristic is its ability to produce parts that are generally more robust compared to those made by SLA, due to the fusion of particles creating a denser structure.
Yet, while SLS is powerful, it often demands specialized equipment and a more significant upfront investment. Balancing this may be worth it for practices emphasizing strength in their prosthetics.
FDM (Fused Deposition Modeling)
FDM is the everyday choice for many dental practices, owing to its affordability and ease of use. With a straightforward setup and relatively low material costs, it's ideal for rapid prototyping. The key characteristic lies in its use of thermoplastics, which can be suitable for various applications, even if its surface finish is not as polished as SLA or SLS.
Although FDM may not produce the same level of detail as its counterparts, it remains valuable for standard denture fabrications and can significantly reduce lead time in producing initial models.
By comprehensively understanding these printing techniques, dental professionals can better navigate the landscape of 3D printing in their field. Each method comes laden with its advantages and parameters, making a strategic choice essential in maximizing patient care and ensuring successful practices.
Materials for 3D Printed Dentures
The choice of materials in 3D printing plays a pivotal role in the outcome of denture production. Selecting the right material not only affects the durability and aesthetics of the dentures but also significantly influences the fit and comfort for the patient. With the rise of 3D printing in dental prosthetics, understanding the various materials available becomes crucial to harnessing the full potential of this technology.
In the realm of dental prosthetics, materials must not only possess structural integrity but also offer a level of biocompatibility for safe contact with oral tissues. Moreover, different materials come with unique properties and functionalities, making it vital for dental professionals to choose wisely based on individual patient needs and clinical requirements.
Types of Printable Materials
Photopolymer Resins
Photopolymer resins stand out in the world of 3D printed dentures due to their remarkable capacity to form precise models under UV light. Their high detail resolution makes them a favorite among dental technicians, producing intricate designs that cater to specific patient needs. These resins are liquid in their base state, transforming into solid structures when exposed to light, thus allowing for thin layers that enhance printing speed.
A key characteristic of photopolymer resins is their variety, which includes different types tailored for specific applications, such as denture bases and surgical guides. The benefit of using these resins lies in their rapid curing time and ability to capture complex geometries. However, they can be somewhat brittle compared to other materials, making them less suitable for areas requiring excessive wear.
Thermoplastics
Thermoplastics are another pivotal material in the manufacturing of 3D printed dentures. Easily molded and reshaped upon heating, these materials offer flexibility and resilience, which are essential characteristics in dental applications. A strong selling point for thermoplastics is their durability, as they can withstand the daily rigors of chewing and biting without compromising structural integrity.
Furthermore, thermoplastics are often utilized for fabricating flexible partial dentures and aligners, making them a go-to for many dental practices. However, the limitation lies in the longer print times compared to resins due to the processing required for solidification. This can impact overall production efficiency, making strategic planning essential.
Metal Alloys
Metal alloys come into play primarily in strong frameworks for dentures, particularly in cases where significant resistance and durability are critical. When discussing metal-based dental prosthetics, often chromium-cobalt alloys are highlighted due to their strength and biocompatibility. The noteworthy aspect of metal alloys is their superior structural integrity, which allows for long-lasting dentures that can endure significant stresses.
Though metal alloys offer extensive durability, they are less flexible in aesthetic customization, which can restrict their use in certain cases. The challenge lies in their higher printing complexity and the need for post-processing, which can add time and costs.
Properties and Suitability of Materials
Understanding the properties of these materials is critical in determining their suitability for various applications in 3D printing dentures. Each material exhibits unique attributes that cater to different requirements:
- Photopolymer Resins: High detail and fast printing but potentially fragile.
- Thermoplastics: Durable and molded easily but can result in longer production times.
- Metal Alloys: Strong and resilient yet may require more complex processing and have limited aesthetic options.
The Process of 3D Printing Dentures
The procedural flow of 3D printing dentures is crucial to understanding its transformative potential in dentistry. This process not only simplifies traditional methods but also enhances accuracy and creativity in producing dental prosthetics. By incorporating technology, dentists can cater to individualized needs, which is a game-changer for patient care. Furthermore, the reduced turnaround time allows for rapid responses to patient demands, aligning better with modern expectations.
Digital Scanning and Design
The first step in creating 3D printed dentures is digital scanning and design. This phase involves capturing precise measurements of the patientās mouth. Using intraoral scanners, practitioners obtain detailed three-dimensional images that highlight every nook and cranny. The dental expert then imports this data into specialized design software, enabling the construction of a digital denture model tailored to fit the patient's unique anatomy.
This technology heralds a significant shift from traditional impression techniques, which often caused discomfort and could yield inaccurate results. It allows for meticulous alterations without the burden of physical materials. In some cases, the dentist can even visualize the final denture in the simulation. This practiceāoften called virtual try-insāfacilitates discussions between the dentist and the patient about aesthetic preferences and functional requirements.
Not to forget, using digital tools dramatically reduces the probability of errors. Mistakes commonly arise from human handling of traditional molds, but digital designs have a much higher margin of accuracy. This transition not only streamlines the workflow but enhances patient trust as they see how their new smile will look right from the start.
Printing and Post-Processing Steps
After the design phase, itās time to move to the printing stage. The selected technology, whether itās SLA, SLS, or FDM, dictates the capabilities of the final product. Each printing method comes with its specifics and best practices, allowing dental professionals to choose based on the material they intend to use.
Once it's printed, thereās a crucial phase known as post-processing. This generally entails cleaning and curing the printed denture. For example, if photopolymer resins were used, soaking the denture in isopropyl alcohol removes any uncured resin. This step ensures that the denture is safe for use and that it maintains its structural integrity. Following cleaning, the denture is typically exposed to UV light to solidify its form further.
It's noteworthy to mention that while these advancements significantly increase efficiency, they also demand a proper understanding of the technology by practitioners. Training becomes essential to leverage the full potential of 3D printing effectively and safely.
Advantages of 3D Printed Dentures
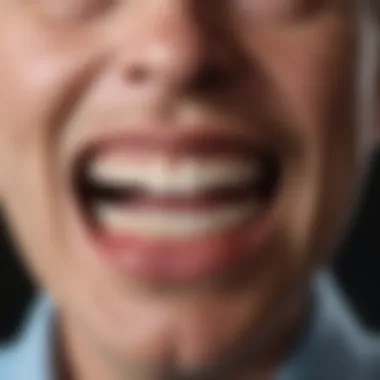
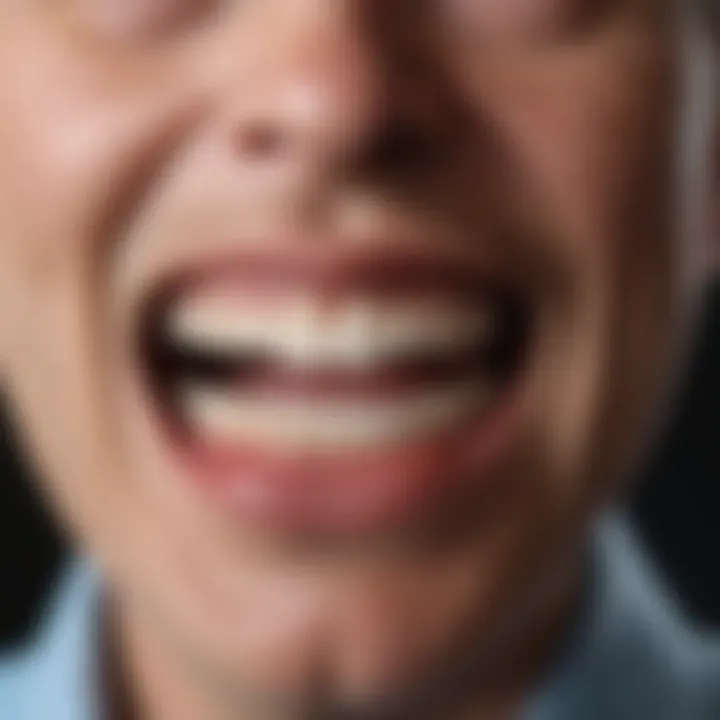
The realm of denture manufacturing is witnessing a seismic shift, courtesy of 3D printing technology. This change isnāt just technical; it holds immense value for both dental professionals and patients alike. This section will unveil several advantages that distinctly highlight the merits of opting for 3D printed dentures.
Customization and Patient Fit
One of the standout features of 3D printing is its capability for customization. Conventional methods often lead to one-size-fits-all solutions, which can leave patients with ill-fitting dentures. With 3D printing, dentists can now create tailored solutions that account for the unique anatomy of each patientās mouth.
- Digital Scanning: Before the printing begins, a digital scan of the patientās oral structure is taken, ensuring that the denture design conforms accurately to their specific needs.
- Adjustments Without Hassle: If adjustments are needed after the initial fitting, a new digital model can be easily created and printed. This is much faster than traditional methods where molds had to be reshaped, poured, and set again.
The combination of precision in design and rapid prototyping allows for a better fit, resulting in enhanced comfort for users. Patients can experience immediate relief, as properly fitting dentures can alleviate sore spots and enhance their overall wellbeing.
Time Efficiency in Production
Time is often of the essence in dental practices, and 3D printing significantly cuts down on the time taken to produce dentures. Unlike traditional methods that can take weeks, the additive manufacturing process can produce finished products in mere days.
- Streamlined Workflow: The integration of digital design and printing minimizes the back-and-forth between the patient and the dental lab, making the process more efficient. One visit for scans and another for fitting are usually all it takes.
- Rapid Prototyping: Iterating on designs becomes much faster. Once a digital model is created, alterations can be applied instantly, leading to quick modifications without the wait time for laboratory work to be completed.
This time-saving aspect not only benefits the practice by allowing more patients to be treated within a certain timeframe but also improves patient satisfaction due to quicker turnaround for their denture solutions.
Cost-Effectiveness Compared to Traditional Methods
3D printing isn't just a technological marvel; it also brings financial benefits. When comparing costs, traditional denture fabrication often incurs hefty laboratory fees and prolonged production times. 3D printing helps in reducing several of these expenses.
- Decreased Material Waste: The additive nature of 3D printing means that materials are used more efficiently, cutting down on waste. Less waste translates to lower material costs, a significant factor when you factor in high-quality resins and other materials.
- Reduced Labor Costs: With simplified workflows, fewer man-hours are needed to produce both the design and final product. This reduction in labor not only decreases overall costs for clinics but can also lead to lower prices for patients.
By effectively lowering production costs, dental practices using 3D printing can provide more affordable options for patients seeking dentures, making dental care more accessible overall.
"The future of dental prosthetics is not just about improvement in technology, but about improving lives through better fit, efficiency, and cost."
Challenges Facing 3D Printed Dentures
As the field of dentistry pivots towards 3D printing, itās critical to delve into the corresponding hurdles that accompany these advancements. Understanding the nuances of 3D printed dentures encompasses more than just acknowledging their advantages. Challenges, such as evolving regulatory landscapes and material limitations, pose significant implications for dental practitioners and patients alike. Each challenge carries weight, influencing the adoption and execution of 3D printing technologies in dental practices. By addressing these roadblocks, the potential for innovation can be maximized, ensuring that patient care is prioritized while also enhancing operational efficiencies.
Regulatory and Compliance Issues
One of the foremost challenges in the realm of 3D printed dentures is navigating the regulatory frameworks established by authoritative bodies. These regulations are imperative to safeguard public health and maintain high standards within dental practices. Given that 3D printing technologies are relatively new, many regulatory guidelines are still in their infancy, often leading to confusion among dental professionals.
Dentists must stay updated on the evolving compliance requirements from organizations such as the FDA in the United States and similar entities worldwide. As it stands, many practitioners might find the approval process for new materials cumbersome, often creating delays in bringing innovations to market.
- Key considerations include:
- Ensuring materials used meet safety and biocompatibility standards
- Adhering to documentation and quality control mandates
- Navigating varying regulations across different regions
"Keeping abreast of regulations isnāt just vital for compliance; it's essential for fostering trust with patients who rely on our expertise."
Additionally, the lack of clear guidelines tailored for the specific application of 3D printed devices adds another layer to the complexity. These uncertainties could hinder the growth of 3D printed dentures, as practitioners might hesitate to invest in new technologies without a clear understanding of legal implications.
Material Limitations and Performance Concerns
Coupled with regulatory challenges, the limitations of available materials pose another substantial hurdle in the realm of 3D printed dentures. While the variety of printable materials has increased, not all of them are suitable for the long-term functionality required in dental applications.
- Some common material limitations include:
- Durability: Many thermoplastic materials, while usable, may not withstand the same level of wear and tear as traditional denture materials.
- Biocompatibility: The adaptability of certain resins or alloys might lead to allergic reactions or other adverse side effects in patients.
- Aesthetic Quality: Achieving the natural look and feel of traditional dentures often requires a combination of optimal material properties and specialized printing techniques.
Moreover, the performance of 3D printed dentures under real-world conditions raises questions. While studies and trials have demonstrated promising results, widespread long-term data is still lacking. This absence of comprehensive documentation can lead to skepticism among both practitioners and patients regarding the reliability of 3D printed solutions.
Future Trends in 3D Printing for Dentistry
The realm of dentistry is undergoing a transformative journey, greatly influenced by advancements in 3D printing technologies. As we delve into the future trends for this area, it's vital to recognize how these innovations stand to redefine dental practices, improve patient outcomes, and streamline operations.
Emerging Technologies and Innovations
A few exciting technologies are on the horizon. One notable example is the evolution of bioprinting. This method, which utilizes living cells, could lead to the creation of dental tissues that more closely mimic natural structures. Furthermore, researchers are investigating the potential of incorporating smart materialsāthose that can alter properties in response to stimuliāwithin 3D printed dentures.
- Artificial Intelligence is becoming intertwined with 3D printing, optimizing design processes and enabling predictive modeling for dental restoration.
- Machine Learning algorithms are also being employed to enhance customization based on an individualās unique anatomy, facilitating a personalized approach.
These technologies are not just buzzing fads; they promise tangible benefits. Improved material properties lead to better biocompatibility, while more sophisticated designs can result in enhanced functionalities.
"With each technological stride, the convergence of 3D printing and AI brings dentistry closer to truly individualized care."
Potential Impact on Dental Practices
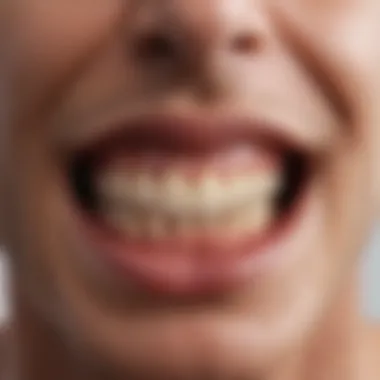
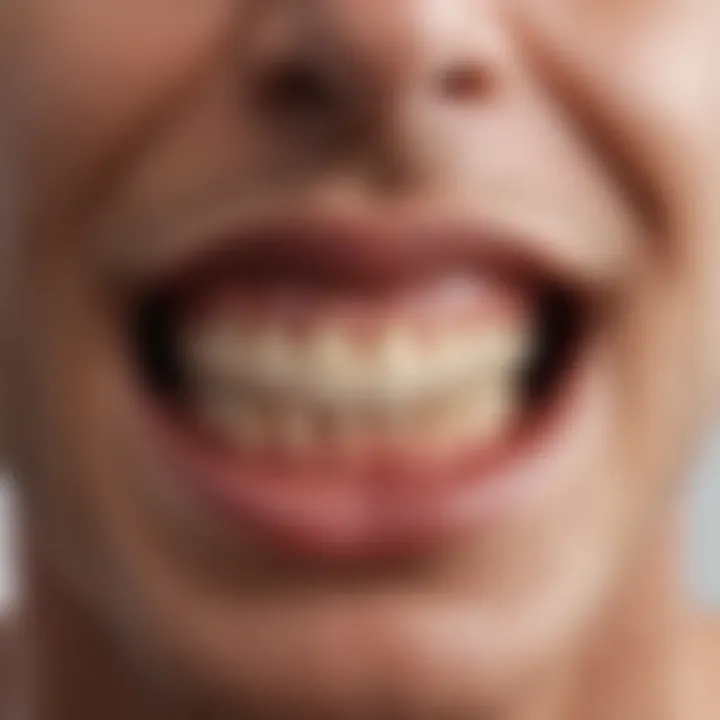
The implications of 3D printing advancements on dental practices can be profound. As these technologies continue to unfold, several key benefits emerge:
- Enhanced Efficiency: The integration of 3D printing often accelerates the production of dentures. This means less waiting time for patients, which is always a plus.
- Cost Reduction: Traditional denture manufacturing methods can be resource-intensive. However, 3D printing is proving to be a cost-effective alternative, reducing waste and utilizing materials more efficiently.
- Adaptation Beyond Prosthetics: As dental professionals become adept at leveraging 3D printing, they might start to use it for more than just dentures. They can explore applications in orthodontics, crowns, and even dental implants, making this technology pivotal in various areas of dentistry.
Adaptation to these technologies can also elevate patient satisfaction. Shorter lead times and highly customized products contribute to improved experiences. Yet, the transition may require additional training for dental professionals, ensuring they have the necessary skills to effectively integrate these innovations into daily practice.
In summary, the future of 3D printing in dentistry holds significant promise, paving the way for advancements that could enhance both practice efficiency and patient care. With ongoing research and development, it's clear that the industry is just scratching the surface of what these transformative technologies can offer.
Case Studies and Real-World Applications
Understanding the practical implications of 3D printing in denture fabrication is crucial. The real-world applications reveal how this technology is changing the landscape of dental prosthetics. By examining case studies, we can glean vital insights into the practicalities, benefits, and challenges that dental professionals encounter when incorporating this modern approach into their practices.
Successful Implementations of 3D Printed Dentures
Across various dental settings, numerous real-life examples stand out, showcasing the successful use of 3D printed dentures. One memorable case involved a small dental clinic in Canada that embraced 3D printing technology to enhance its service offering. Initially, they were facing long fabrication times and often dealt with patient dissatisfaction due to imperfect fits.
With the introduction of 3D printing, they reported significant improvements:
- Reduced Turnaround Times: Traditional methods often required multiple visits. Now, with efficient digital scanning and printing, the process is streamlined, often allowing for same-day fittings.
- Increased Comfort and Fit: Thanks to the precise nature of digital impressions, patients experienced a better fit right out of the gate. This not only improved patient satisfaction but also reduced the number of adjustments required post-delivery.
- Cost Reduction: Streamlined processes led to cost savings, which, in turn, allowed the clinic to offer competitive pricing without compromising service quality.
Another notable context involved a research study at a university dental program, where students engaged in creating custom 3D printed dentures. This hands-on approach not only enhanced their practical skills but also sparked professional interest in new technologies. Reviews from participants highlighted the newfound confidence in handling modern dental apparatus, necessary for todayās evolving industry.
Patient Testimonials and Outcomes
Patient experiences provide invaluable feedback and often reveal the emotional weight held in dental prosthetics. One patient, a retiree who had struggled with ill-fitting dentures for years, shared her experience after receiving a newly 3D printed set. She expressed how the comfort level was a game changer, allowing her to enjoy meals without worry. This kind of satisfaction is revealing:
"Before, it felt like I was always adjusting my dentures. Now, I can eat my favorite foods without a second thought. Itās like I got my life back!"
Such testimonials validate the shift towards 3D printed denturesānot just from a technical standpoint but also from a personal, quality-of-life perspective.
In another instance, a young patient undergoing orthodontic treatment benefited from a 3D printed retainer that seamlessly integrated with her dental plan. Her family's feedback emphasized the appreciation for less time spent in the dental chair and more time enjoying daily activities.
Gathering these insights shows that beyond just the clinical advantages, there is a transformative impact on the lives of patients. Implementing 3D printing technology allows practitioners not only to meet but exceed patient expectations in ways that lead to enhanced quality of care and life.
The landscape of 3D printing in dental prosthetics is nothing short of dynamic, with successive case studies continuing to inform best practices and potential advancements. Through these narratives, dental professionals can be better prepared to embrace changing technologies, benefiting both their practices and the communities they serve.
The Role of Dentists in 3D Printing
The integration of 3D printing into dental practices has fundamentally shifted the landscape of denture fabrication. As specialists at the forefront of patient care, dentists are uniquely positioned to harness the capabilities of this technology. Their involvement is not just beneficial; it is crucial for the successful adoption and implementation of these advancements. The role of dentists in 3D printing encompasses various elements, including training, skill enhancement, and the seamless integration of new processes into their practices.
Training and Skill Enhancement
For dentists, the shift to 3D printing is like learning a new language. It demands a solid grasp of both the technology and the associated materials. Educators and professional organizations are stepping up, offering continual education programs that delve into the nuances of 3D printing technology.
- Hands-on Workshops: Workshops are cropping up across the country focusing on the practical application of 3D printing. These sessions are designed to build competency, giving dentists a chance to operate printers and engage with software tools.
- Online Learning Modules: Many dentists are turning to online courses that cover everything from the basics of digital scanning to advanced printing techniques. Flexibility in learning allows professionals to fit this training into their busy schedules.
- Certification Programs: Accredited certification programs provide credentials to help dentists navigate regulatory issues, ensuring they adhere to safety and quality standards.
These programs not only enhance technical skills but also foster a deeper understanding of how 3D printing can improve patient outcomes. With proper training, dentists can confidently recommend and utilize 3D printed dentures, tailored precisely to the needs of each individual patient.
Integration into Dental Practices
Integrating 3D printing into existing dental practices can be a game-changer, but it requires thoughtful planning and execution. The transition is rarely as simple as flipping a switch; it involves substantial restructuring and aligning with the latest practices.
- Infrastructural Changes: Dental offices need to invest in 3D printers and related technology. This initial overhead can be daunting, yet the long-term benefits often outweigh these costs. Factors like space for equipment and workflow modifications must be taken into account.
- Collaboration with Dental Labs: Local dental laboratories that have adopted 3D printing can serve as partners. Professionals should consider collaborating with labs already proficient in digital fabrication. This partnership can reduce the learning curve and help practices gain a foothold in this innovative arena.
- Patient Education: Dentists must also play a role in educating their patients about the benefits of 3D printed dentures. Communicating the advantages, such as improved fit and faster production times, can help alleviate patients' hesitations.
āThe successful integration of 3D printing responsibly blends traditional craftsmanship with modern precision, elevating patient care.ā
As 3D printing technology continues to dual its influence in dentistry, the dentist's role is expected to evolve further. By focusing on training and integration, dental professionals can leverage this cutting-edge technology to enhance their practice and improve patient experiences.
Finale
In discussing the impact of 3D printing on denture manufacturing, it becomes increasingly clear how significant this technology is in shaping the future of dental prosthetics. The advantages that 3D printing brings ā customized designs, efficient production timelines, and potentially lower costs ā position it as a frontrunner in modern dentistry. This conclusion will synthesize key insights on how these benefits are not just theoretical but practical implications in real-world scenarios.
Summarizing Key Insights
Throughout the article, we emphasized the various facets of 3D printing that are revolutionizing the field of dental prosthetics. Here are some of the most compelling points:
- Customization: With 3D printing, dentists can create dentures that fit a patient's unique oral structure more precisely than traditional methods. This enhanced fit can significantly improve comfort and usability for patients.
- Production Efficiency: The time from design to final product can be drastically reduced, allowing for quicker turnarounds. This makes treatments more accessible, enabling patients to receive their necessary prosthetics without prolonged delays.
- Cost Savings: Although initial investment in the technology may be substantial, the overall costs can decrease due to less waste and reduced labor expenses associated with traditional denture fabrication processes. In the long run, this could make quality dental care more affordable for a broader audience.
"3D printing is not just a tool; itās a pathway to new standards of care in dentistry."
Future Considerations for Practitioners
Looking forward, there are several considerations for dental professionals as they adapt to this evolving landscape of denture production:
- Continuing Education: Dentists must stay informed about the latest technologies and methods related to 3D printing. This involves not only understanding the technical aspects but also learning to use specific software designed for dental applications.
- Integrating Technology: Moving forward, the integration of 3D printing into practice should be strategic. Practitioners need to consider how this technology fits within their existing workflows and what changes might need to be made for optimal functioning.
- Regulatory Awareness: Considering the changing landscape of materials and manufacturing processes, itās crucial for dentists to remain vigilant about regulatory compliance. Keeping abreast of local and international standards will ensure safety and efficacy in the dentures they provide.
A thorough understanding of these factors is essential, shaping not only patient care but also the operational viability of dental practices in a technology-driven future.