Building a Hoist: Comprehensive Construction Guide
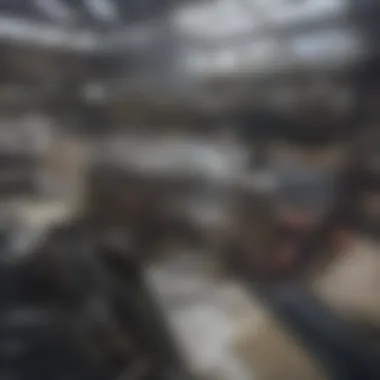
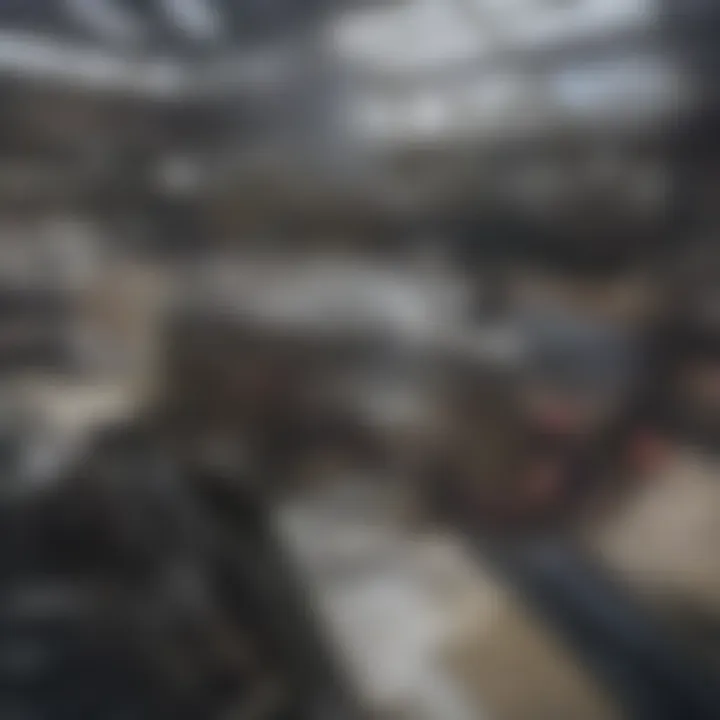
Intro
Building a hoist is a formidable task that combines elements of engineering, safety, and practical application. Understanding the nuances of hoist design is essential for students and professionals seeking to engage in this domain. As technology evolves, the demand for efficient lifting solutions increases. A hoist serves not only in construction but also in various industries such as manufacturing, shipping, and even theater production. The significance of this topic cannot be overstated. In this comprehensive guide, we will explore every facet of building a hoist, ranging from foundational principles to advanced operational mechanics.
From material selection to safety protocols, mastering these topics equips readers with the requisite knowledge to navigate the complexities involved in hoist construction effectively.
Prolusion to Hoists
Understanding hoists is fundamental in various engineering and construction fields. Their role is to facilitate the lifting and movement of heavy objects, contributing greatly to efficiency in multiple applications. In this section, we will explore the definition of hoists, their common applications, and the different types available in the market. This foundational knowledge is critical for anyone looking to design, build, or utilize hoists effectively.
Defining Hoists
A hoist is a mechanical device used to lift or lower loads. It functions by using a drum or lift-wheel around which a rope or chain wraps. Hoists can be operated manually or powered, depending on their type and intended application. They are essential tools in construction, manufacturing, and other industries where heavy lifting is necessary. Knowing how hoists work is important to select the right type for a specific task and to understand their limitations.
Common Applications of Hoists
Hoists serve a wide range of applications, making them versatile tools in various industries. Common uses include:
- Construction Sites: Lifting heavy materials such as steel beams and concrete blocks.
- Manufacturing Plants: Moving heavy machinery and assembly line components.
- Warehouses and Distribution Centers: Assisting in the loading and unloading of cargo.
- Theatrical Productions: Raising and lowering stage equipment and scenery.
Each of these applications requires careful consideration of the hoist type to ensure safety and efficiency.
Types of Hoists
Hoists are categorized into several types based on their operation and mechanism. Understanding these types is crucial to determining which hoist is suitable for a particular task.
Manual Hoists
A manual hoist is operated by hand. They are often used in environments where electrical power is not available or when the load is not excessively heavy. Their simplicity makes them a popular choice for smaller projects and individual tasks.
Key characteristics:
- Portability: Easy to move and set up in different locations.
- Cost-Effective: Lower initial costs compared to powered hoists.
Advantages and disadvantages: While manual hoists are reliable, they require physical effort, which may not be suitable for all users or all jobs.
Electric Hoists
Electric hoists are powered by electric motors. They provide significant lifting power and are suitable for heavier loads. Electric hoists can dramatically reduce the time and effort required for lifting tasks, making them ideal for industrial applications.
Key characteristics:
- Efficiency: Quick operation reduces lifting time significantly.
- Consistent Power: Offers steady lifting without the need for manual input.
Advantages and disadvantages: Electric hoists are less labor-intensive, but they require a power source and may come with higher maintenance needs.
Pneumatic Hoists
Pneumatic hoists use compressed air to lift loads. They are often used in environments where sparks are a concern, such as factories dealing with flammable materials. Their design is efficient and reliable in rigorous conditions.
Key characteristics:
- Safety: Reduced risk of electric shock.
- Powerful Performance: Able to lift heavy loads quickly.
Advantages and disadvantages: While pneumatic hoists are very safe, they depend on the availability of compressed air, which may limit their applications in some settings.
Hydraulic Hoists
Hydraulic hoists operate on the principle of using fluid pressure to lift heavy loads. They are known for their stability and strength, making them suitable for heavy-duty tasks in various industries.
Key characteristics:
- High Load Capacity: Ideal for very large and heavy items.
- Precision Control: Provides better control over lifting speed and movement.
Advantages and disadvantages: Hydraulic hoists offer great power but require periodic maintenance to avoid leaks and ensure operational safety.
Understanding these types of hoists and their characteristics is essential for making informed choices in hoist selection and utilization.
Understanding Hoist Mechanics
Understanding hoist mechanics is crucial in the construction and operational phases of hoists. It provides insight into the physical principles that govern lifting operations. By grasping these fundamentals, both engineers and operators can ensure that hoists function effectively and safely. Proper knowledge of hoisting mechanics contributes to improved design choices, load handling, and safety standards.
The mechanics of hoisting deals primarily with the forces involved in raising and lowering loads. A comprehensive understanding helps to maximize efficiency while minimizing the risk of accidents. In this section, we will break down the basic principles of lifting and provide a glimpse into the calculation of forces associated with hoisting.
Basic Principles of Lifting
Lifting involves overcoming the gravitational force acting on an object. When a hoist is engaged, several physical principles are at work. To lift an object, the hoist must exert a force greater than the weight of the load. The basic formula that describes this is given by:
Force = Mass x Acceleration due to gravity
The acceleration due to gravity on Earth is approximately 9.81 m/s². Knowing this value is fundamental when calculating how much force is necessary to lift an object safely.
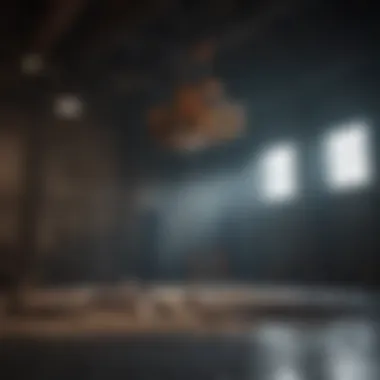
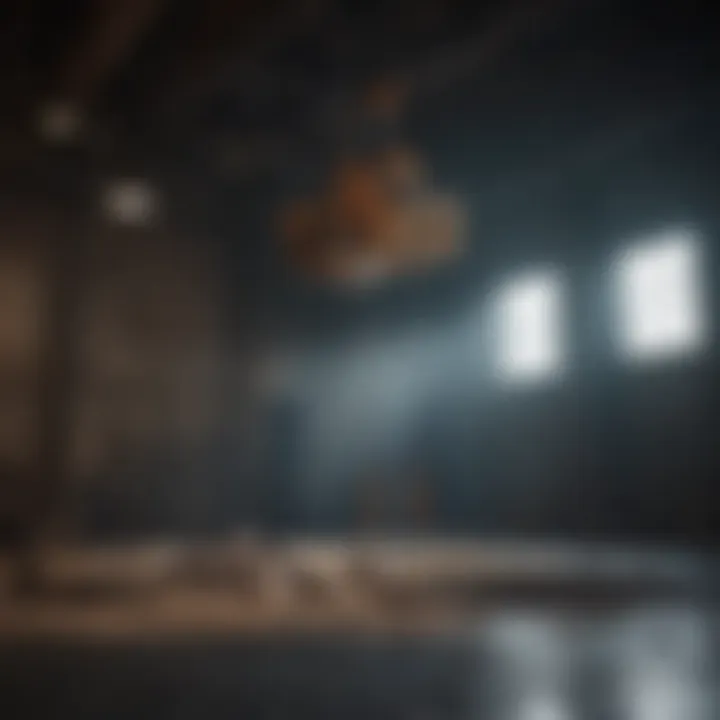
Another important principle is mechanical advantage. Hoists use various arrangements of ropes, pulleys, or hydraulic elements to distribute the load. Understanding how different configurations affect lifting efficiency is vital. A common setup, such as a block and tackle system, significantly reduces the effort needed to lift a heavy load by distributing forces across multiple lines.
Force Calculation in Hoisting
Calculating force in hoisting applications is essential for determining appropriate hoist types and specifications. This involves more than just the weight of the load. Environmental factors, the angle of lifting, and dynamic forces during operation must be considered.
When initiating a lift, it’s important to account for the total load including:
- The weight of the object itself
- Any additional components, such as slings or lifting forks
- Potential dynamic loads, which occur during movement
To calculate the required force for lifting, you can use the following formula:
Additionally, as the angle of the lifting mechanism changes, so does the required force. For example, lifting at an angle creates challenges since you need to counteract not only the weight of the load but also any lateral forces that could affect stability.
Understanding these calculations helps in selecting the right hoist and ensuring that it meets safety and operational standards. Engineers often use simulation software to assess the performance of the hoist under various conditions, allowing for more precise designs.
With an understanding of these basic principles and calculations of force in hoisting, the subsequent design and building processes will be better informed. This knowledge lays the groundwork for discussions on material selection and safety considerations in future sections.
Materials for Building a Hoist
Choosing the right materials for constructing a hoist is crucial. The materials must ensure the strength, stability, and safety of the system. The characteristics of the materials directly affect the overall performance and durability of the hoist. This section will cover some of the main materials typically used in hoist construction and the considerations associated with their selection.
Choosing the Right Materials
Steel
Steel is a primary choice in hoist construction due to its high tensile strength. It offers excellent resistance to deformation, making it suitable for heavy loads. The most significant characteristic of steel is its durability, which translates to longevity in construction. Steel's ability to withstand extreme conditions also adds to its appeal.
When building a hoist with steel, one must consider its weight. Steel can make the overall structure heavy, which could affect the hoist's performance. However, the strength-to-weight ratio is typically favorable for high-capacity hoist applications. A unique feature of steel is its weldability, allowing for versatile designs. The disadvantages involve susceptibility to corrosion if not properly protected. Proper coatings or galvanization are essential to prolong the life of steel hoists.
Aluminum
Aluminum has gained popularity in the construction of hoists mainly due to its lightweight nature. This characteristic reduces the total weight of the hoist system, enhancing mobility and ease of installation. Aluminum offers commendable resistance to corrosion, making it suitable for outdoor use or damp environments.
Unlike steel, aluminum does not require extensive protective coating, which saves both time and money. However, its key feature is limited load capacity compared to steel. This means while aluminum hoists are flexible and practical, they may not be suitable for all applications. They excel in situations where weight reduction is critical. One disadvantage of aluminum is that it is more susceptible to damage under extreme stress, which may limit its use in high-load scenarios.
Plastic Components
Plastic components are increasingly being integrated into hoist designs due to their lightweight and resistant properties. These components often include the pulley systems or guides, which can be efficiently produced and maintained. The primary feature of plastic is its ability to be molded into complex shapes, allowing for innovative designs.
The benefit of using plastic lies in its resistance to corrosion and chemical exposure. Unlike both steel and aluminum, plastic components do not rust, making them ideal for specific conditions. However, they usually have lower strength compared to metal options. While plastic can be cost-effective, its long-term durability in high-stress areas is a concern. This makes careful consideration necessary when integrating plastic into a hoist system.
Durability and Load Requirements
The durability of the hoist materials is directly linked to the load requirements of the hoist. Each material has a specific threshold for load capacity, and understanding this is vital for safety and functionality. Using materials that do not match the load requirements can result in structural failure.
Consider the operational environment and the typical loads the hoist will handle. Hoists used in industrial settings may require stronger materials like steel due to heavier loads. In contrast, hoists used in light-duty applications might utilize aluminum or plastic due to their sufficient capabilities and reduced weight. Attention to details, such as potential wear and tear, plays an important role in material selection.
Design Considerations for Hoists
Design is a critical phase in the construction of a hoist. It serves multiple functions, including safety, functionality, and usability. A well-thought-out design not only increases the hoist's efficiency but also ensures that it meets the required safety standards. Without proper design principles, hoists can become hazardous, leading to serious accidents and damage.
Load Capacity Calculations
Calculating the load capacity is fundamental when designing a hoist. This involves determining the maximum weight the hoist will handle safely and efficiently. Load capacity is influenced by factors including the material strength, lift mechanism, and angle of operation.
To properly calculate load capacity, engineers usually follow these steps:
- Identify the maximum expected load: This could be determined from previous data or industry standards.
- Factor in dynamic loads: This includes additional forces such as wind or jerking from lifts.
- Calculate the safety factor: This is generally a ratio that reflects how much extra weight the hoist can support.
Overall, accurate load capacity calculations ensure the hoist operates within safe limits, reducing the risk of failure.
Safety Factors in Design
Safety factors are numerical expressions that provide a margin of safety over the expected loads during operation. Integrating safety factors into a hoist design is essential for protecting both the operators and the equipment. Generally, a safety factor of at least 5 is advisable, which means that the hoist can handle five times the maximum expected load. Factors influencing these calculations include:
- Material properties: Different materials have varying tensile strength.
- Design specifications: Complexity of the design may influence the safety factor.
- Environmental impact: External factors such as temperature and humidity can affect the materials involved over time.
By accounting for these factors during the design, potential failures due to overload or material fatigue can be mitigated.
Space and Dimensioning
Proper dimensioning is crucial in the design of a hoist. It combines both the physical size of the hoist and its operational space requirements. This subheading includes:
- Physical dimensions: Determining how much room is needed for the hoist's installation, operation, and maintenance.
- Movement space: Ensuring that there is ample space for the load while in transit, as well as additional room for potential swings or impact.
- Clearances: Adequate clearances from obstructions is necessary to avoid collisions.
In summary, adequate space and dimensioning will not only improve hoist functionality but also enhance safety by providing clear pathways for operations and maintenance.
Construction Steps for Building a Hoist
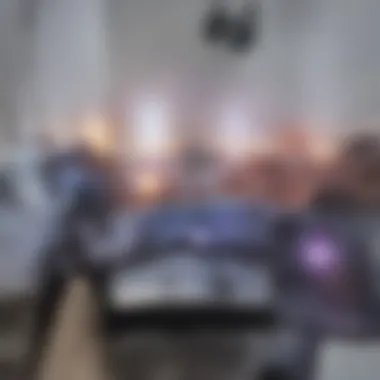
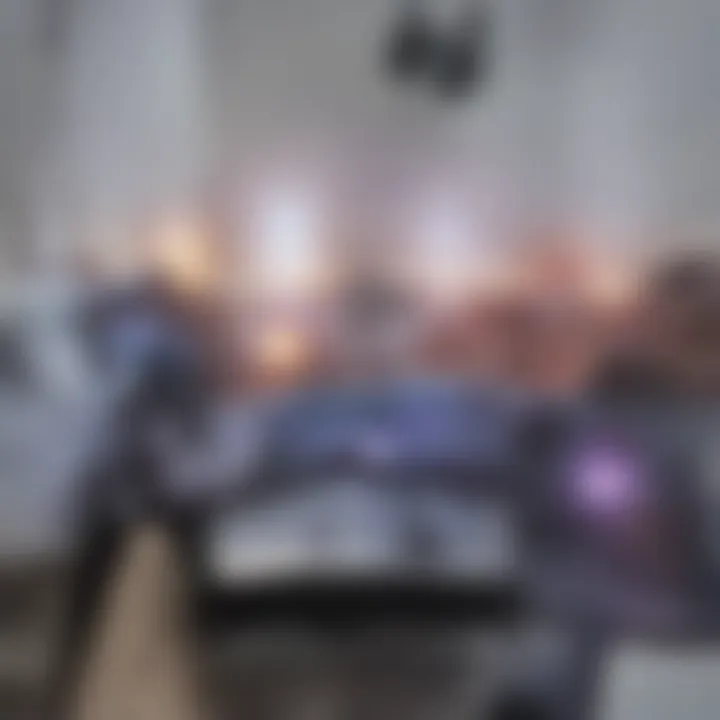
Building a hoist is a precise task. Each step is critical to ensure functionality, safety, and reliability. The construction steps divide into several phases, each requiring attention to detail. These phases guide the builder through the processes, ensuring that no vital elements are overlooked.
Preparing the Site
Before any materials can be used, preparing the site is essential. This involves assessing the location where the hoist will operate. Evaluate the ground stability, available space, and environmental factors vulnerable to affecting performance.
- Ground Stability: Ensure the ground can support the weight of the hoist and the maximum load it must carry. Unstable soil can lead to failure.
- Space Assessment: Confirm the area meets dimensions to accommodate hoist operation. There should be clear paths for movement of both the hoist and the loads.
- Environmental Protection: Consider weather conditions, as exposure to moisture can rust metal components. Ensure covered or sheltered areas when necessary.
Assembling Components
Once the site is ready, the next step involves assembling components. Each part of the hoist must be pieced together methodically. Ensure that components fit together correctly, following specifications in design plans.
- Equipment Needed: Use standard tools like wrenches, screwdrivers, and potentially power tools to facilitate assembly.
- Component Check: Before assembly, verify that all components are present and undamaged. These include ropes, pulleys, and the main frame.
- Step-by-Step Assembly: Follow manufacturer guidelines if available. Methodically attach the frame first, then integrate the lift and pulley system.
Integrating the Hoist Mechanism
Integrating the hoist mechanism requires precision. This is the stage where mechanics come to life. Align all components correctly to avoid malfunctions.
- Alignment: Ensure that all moving parts are properly aligned. Misalignment can cause excessive wear or failure during operation.
- Connection Setup: Attach the hoisting means, whether it be chains or ropes, directly to the lift system. Check all connections for security.
- Operational Checks: Manually operate the mechanism before finalizing. Observe any friction points and rectify them to improve smooth operation.
Testing and Calibration
Before the hoist can enter service, thorough testing and calibration are non-negotiable. These steps guarantee safety and reliability.
- Initial Load Tests: Start with no load, gradually adding weight to assess performance. Monitor for any unusual behavior during operation.
- Calibration: Ensure all measuring tools provide accuracy. This includes the load cells and any sensors in the system. Adjust if necessary to calibrate properly.
- Safety Checks: Review all safety features and emergency stops. Confirm functionality under various scenarios like overload and sudden stops.
"Rigorous testing reveals weak points that could lead to catastrophic failure later."
Completing these steps lays a solid foundation for building a hoist. Each phase contributes to the overall integrity of the final product. Proper preparation, assembly, and testing can lead to a fully operational hoist that meets safety standards.
Safety Protocols in Hoist Construction
In the process of building a hoist, safety protocols play a crucial role. These protocols protect not just the workers but also the integrity of the equipment itself. Understanding and implementing the right safety measures can significantly reduce the risk of accidents and failures during operation. Therefore, it is paramount to prioritize safety at every stage of hoist construction.
Personal Protective Equipment
A fundamental aspect of safety involves the use of Personal Protective Equipment (PPE). Selection of appropriate PPE is vital. Workers should be equipped with safety helmets, goggles, gloves, and steel-toed boots. This gear helps mitigate injuries caused by falling objects or sharp components. Other equipment such as harnesses may be necessary when working at heights, ensuring that individuals are secure and can operate safely.
Here are key components of PPE for hoist construction:
- Helmets: Protects the head from impact.
- Goggles: Shields the eyes from debris.
- Gloves: Prevents hand injuries from handling materials.
- Steel-toed boots: Offers foot protection against heavy loads.
- Harnesses: Essential for work at elevated levels.
"Safety is not a cost. It's an investment in your workforce."
Operational Safety Measures
Following PPE, operational safety measures are equally significant. These involve established procedures that guide the operation of hoists. Conducting a risk assessment before starting work aids in identifying potential hazards. Additionally, maintaining a clean and organized workspace minimizes the chance of accidents. It is important to ensure that all workers are trained on how to operate the hoist equipment. The operation should be supervised, especially during load lifts, to ensure adherence to safety protocols. Some important operational safety measures include:
- Clear communication: Use signals or radios to maintain contact among team members.
- Load testing: Regularly check the load limits of hoists to prevent overloads.
- Emergency procedures: Clearly defined actions for a range of incidents, like equipment failure or accidents.
A solid foundation of safety protocols installation can reduce injuries and enhance productivity.
Regulatory Compliance
Adhering to regulatory compliance is critical in ensuring that safety standards are met during hoist construction. Various organizations like the Occupational Safety and Health Administration (OSHA) provide guidelines that set the minimum safety requirements for construction projects. Compliance with these regulations not only protects workers but also helps companies avoid potential legal issues.
Key regulatory considerations include:
- Compliance with local laws: Always check state and local requirements.
- Regular inspections: Equipment should be regularly inspected to ensure it meets safety standards.
- Documentation: Keeping thorough records of safety training and inspections supports accountability.
Operational Guidelines for Hoists
Operational guidelines are crucial for the effective functioning and safety of hoists. They serve as a framework that ensures everyone involved in the use and management of hoists understands their roles, responsibilities, and the specific procedures that must be followed. This section addresses several key elements, including the need for routine inspections, operator training, and maintenance practices. Each of these components plays a significant role in maintaining hoist safety and reliability.
Routine Inspections
Routine inspections are a fundamental aspect of hoist operation. These inspections are necessary to identify any potential issues before they escalate into serious problems. Regular checks help ensure that all components of the hoist are functioning properly and safely. The frequency of inspections can depend on the hoist's usage and the environment in which it operates.
Some common aspects to inspect include:
- Load capacity: Ensure the hoist can handle the intended weight.
- Braking systems: Check for reliable operation to prevent accidents.
- Electrical components: Verify connections are secure and free from damage.
Regular inspections not only enhance safety but also increase the lifespan of the hoist. This proactive approach prevents costly repairs or replacements in the long run.
Training for Operators
Proper training for operators is essential. Trained personnel are crucial in avoiding accidents and ensuring that the hoist operates within its designed parameters. Training covers various aspects, including:
- Operational Procedures: Understanding how to operate the hoist correctly.
- Safety Protocols: Knowledge of safety measures to mitigate risks.
Certification may be required to demonstrate that operators have completed necessary training. This ensures that all personnel are equipped with the skills needed to operate hoists safely and effectively.
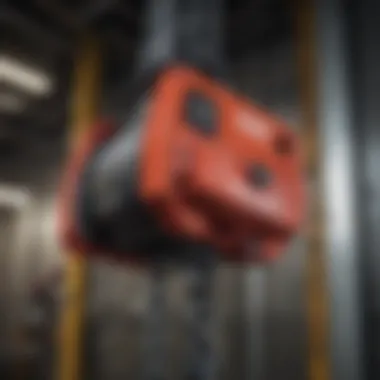
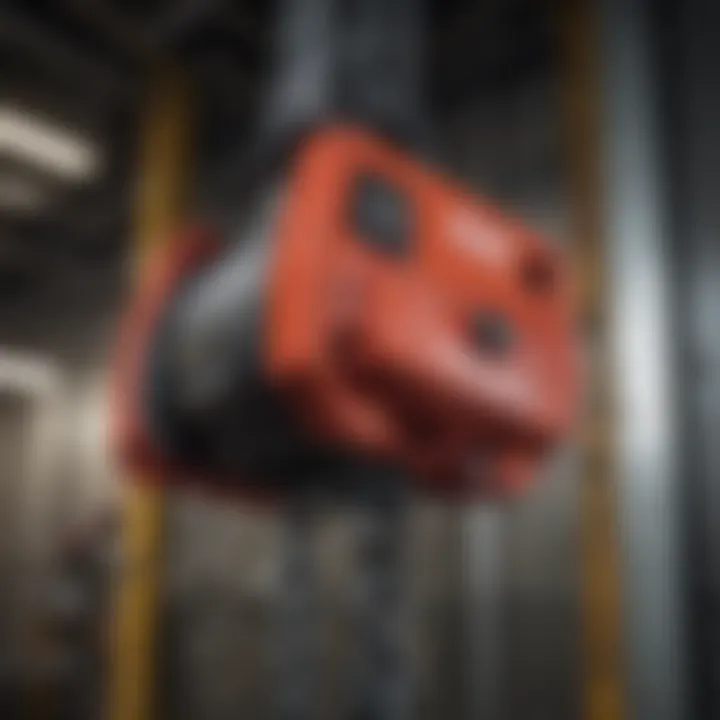
Maintenance Practices
Maintenance practices are vital for both preventive and corrective measures. Regular maintenance helps avoid unexpected failures and prolongs the life of the hoist. It can be divided into two main categories:
Preventive Maintenance
Preventive maintenance consists of routine checks and tasks that aim to prevent failures before they occur. This approach is effective in identifying issues early. Common tasks include:
- Lubrication: Ensuring that moving parts are properly lubricated.
- Inspection of Wear and Tear: Regularly assessing components for signs of deterioration.
The key characteristic of preventive maintenance is its proactive nature. By addressing potential problems, it can greatly reduce the possibility of downtime and enhance operational efficiency. One unique feature is the ability to schedule maintenance during non-peak hours, minimizing disruption to operations. However, this requires careful planning and resource allocation.
Corrective Maintenance
Corrective maintenance is performed after a malfunction occurs. It involves fixing issues that have already led to failure. This category typically requires more immediate action than preventive measures. Key aspects include:
- Diagnosis: Identifying the exact issue and its cause.
- Repairs or Replacements: Implementing solutions to restore functionality.
The main benefit of corrective maintenance is its responsiveness. While it may appear less favorable due to potential downtime, it is crucial in maintaining operations. However, reliance solely on corrective measures can lead to higher overall costs. Balancing preventive and corrective maintenance practices will help in efficient hoist management.
Troubleshooting Common Hoist Issues
Troubleshooting common hoist issues is a critical aspect of maintaining safety and efficiency in hoisting operations. Proper identification and resolution of problems can prevent workplace accidents, reduce downtime, and extend the service life of the hoist. Knowledge in this area is essential for engineers, technicians, and operators alike, as it empowers them to address malfunctions effectively.
Identifying Malfunctions
Identifying malfunctions in a hoist involves a thorough understanding of their operational mechanics. Various symptoms can indicate issues, which can include but are not limited to:
- Unusual Noises: Sounds like grinding, clanking, or hissing can signal problems with gears, chains, or motor components.
- Strange Movements: If the hoist does not lift or lower loads smoothly, it may indicate mechanical issues.
- Electrical Failures: A hoist that fails to operate when the controls are activated could point to electrical faults, such as wiring issues or blown fuses.
- Load Shifting: If loads sway or shift unexpectedly during lifting, this can indicate improper installation, inadequate load securing, or mechanical failure.
Regular inspections should be part of the hoisting operations. Identifying signs of malfunction early on can mitigate risks before they escalate into serious problems. Some common inspection techniques include visual checks, operational tests, and monitoring load limits. These practices help maintain the integrity of the hoist while ensuring compliance with safety standards.
Repair Strategies
Once malfunctions are identified, implementing effective repair strategies is essential for restoring hoist functionality. The following steps detail a systematic approach:
- Assess the Problem: Evaluate the symptoms and pinpoint the source of malfunction. Document findings to ensure clarity on what needs fixing.
- Consult Manuals: Manufacturer manuals often provide guidance for common issues. Refer to them for troubleshooting tips and repair instructions specifically tailored to the model in use.
- Replacement Parts: In case of damaged components, identify the requisite replacement parts. Using original equipment manufacturer (OEM) parts can improve reliability and performance.
- Professional Assistance: If repairs are complex or beyond in-house capabilities, enlisting qualified technicians may be necessary. They possess the required expertise and tools to carry out the repairs safely.
- Testing Post-Repair: After completing repairs, it is essential to conduct tests. Ensure the hoist operates correctly under load, and that all functions return to normal. This step is non-negotiable for operational safety.
Following these strategies, operators can effectively address issues that arise during hoist use, ensuring that potential hazards are minimized and operational efficiency is maintained.
Proper troubleshooting and repair of hoist malfunctions not only ensure safety but also maximize productivity and longevity of the equipment.
Advancements in Hoist Technology
In recent years, advancements in hoist technology have significantly transformed the construction and industrial sectors. These innovations not only enhance performance but also improve safety, efficiency, and user experience. Understanding these developments is essential for individuals involved in engineering and construction, as it allows for the integration of modern solutions that meet contemporary demands.
Smart Hoists
Smart hoists represent a leap forward in hoisting technology. These systems incorporate advanced features like sensors, IoT connectivity, and automation. The integration of these technologies enables real-time monitoring of hoist operations. For instance, users can receive alerts about potential overloads or maintenance needs. This prevents accidents and extends the lifespan of equipment.
Some key benefits of smart hoists include:
- Increased Efficiency: Automated systems can optimize lifting operations, reducing manual interventions and ensuring that tasks are completed more quickly.
- Enhanced Safety: Continuous monitoring helps in identifying issues before they become problems. This reduces the likelihood of accidents on the job site.
- Data Analytics: Built-in analytics provide insights into hoist performance, helping operators make informed decisions for future projects.
Employing smart hoists is not merely about convenience; it addresses several critical operational concerns. For example, smart hoists can significantly minimize human errors, which are often the cause of mishaps in construction environments.
"As technology advances, the workplace becomes safer and more efficient, utilizing systems that think ahead to prevent issues before they arise."
Eco-friendly Hoisting Solutions
The push for sustainability is influencing many industries, and hoisting technology is no exception. Eco-friendly hoisting solutions are being developed to minimize environmental impact while maintaining high performance and reliability. This category encompasses various innovations that reduce energy consumption and improve material use.
Key aspects of eco-friendly hoisting solutions include:
- Energy-efficient Motors: Many modern hoists utilize motors designed to consume less power while providing the same lifting capacity. This reduction in energy use translates to lower operational costs.
- Recyclable Materials: The use of recyclable materials in hoist construction not only supports sustainability but also aligns with industry regulations favoring environmentally conscious practices.
- Reduction of Emissions: Electric and pneumatic hoists generate fewer emissions compared to traditional models fueled by fossil energy sources. This is crucial for companies looking to reduce their carbon footprint.
Investing in eco-friendly hoisting solutions is not just a matter of regulatory compliance; it represents a commitment to social responsibility. Organizations adopting such technologies often experience improvements in brand image and customer loyalty, as more consumers favor businesses that prioritize environmental sustainability.
Ultimately, advancements in hoist technology are steering the industry towards smarter, safer, and greener solutions. This trend is expected to continue shaping the future of hoisting systems, making it imperative for stakeholders to stay informed and adapt.
Culmination
The conclusion of this guide emphasizes critical insights relevant to the construction and operation of hoists. This section underscores the necessity for comprehensive understanding when designing and building hoists. A well-built hoist not only meets the required load capacities but also ensures operational safety and efficiency.
Furthermore, by acknowledging the potential obstacles and solutions as outlined throughout the guide, one can significantly improve project outcomes. The importance of adhering to safety protocols and regulations cannot be overstated. Awareness of these protocols minimizes risks associated with hoist operations, safeguarding both equipment and personnel.
Ultimately, this conclusion encapsulates the entire process from the initial planning stage to final testing and integration. It signifies the need for a methodical approach to construction and highlights the benefits of advanced technology. In the hoisting field, staying informed on innovations can enhance productivity and safety measures.
Summary of Key Points
- Defining Hoists: Understanding the basic concept of hoists and their functionality aids in grasping how they operate in various applications.
- Material Selection: Choosing appropriate materials like steel or aluminum affects the durability and load capacity of hoists.
- Safety Protocols: Implementing safety measures ensures safe operation and compliance with regulatory standards.
- Operational Guidelines: Regular inspections and maintenance practices help in the longevity and efficient functioning of hoists.
- Advancements in Technology: Recognizing smart and eco-friendly hoisting solutions promotes sustainability within the industry.
Future Trends in Hoisting Technologies
The hoisting industry is continually evolving, with several emerging trends reshaping how hoists are designed and operated. These include:
- Automation: The integration of automation facilitates lower operational costs and reduces human error. Designs that incorporate AI can enable predictive maintenance and streamline operations.
- Sustainability: As the focus on eco-friendly solutions rises, advancements in material science lead to stronger yet lighter materials that reduce energy usage.
- Smart Technology: Incorporating advanced sensors and IoT capabilities into hoisting systems allows for better monitoring of loads and operational metrics.
- Enhanced Safety Features: Future designs will likely include more robust safety measures, such as overload protection systems and real-time monitoring capabilities to further minimize workplace hazards.
- Modular Designs: These designs promote easier and faster assembly and disassembly, making hoists more versatile for various applications.
Staying updated with these emerging trends is essential for engineers and constructors to remain competitive and effective in their hoist projects.