The Unique Properties and Uses of Carbide Ceramics
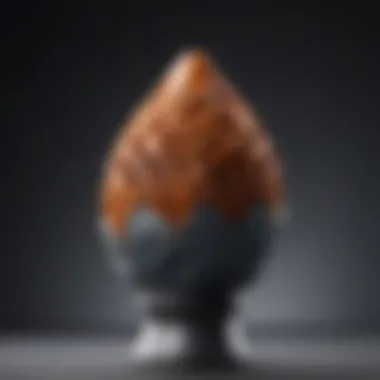
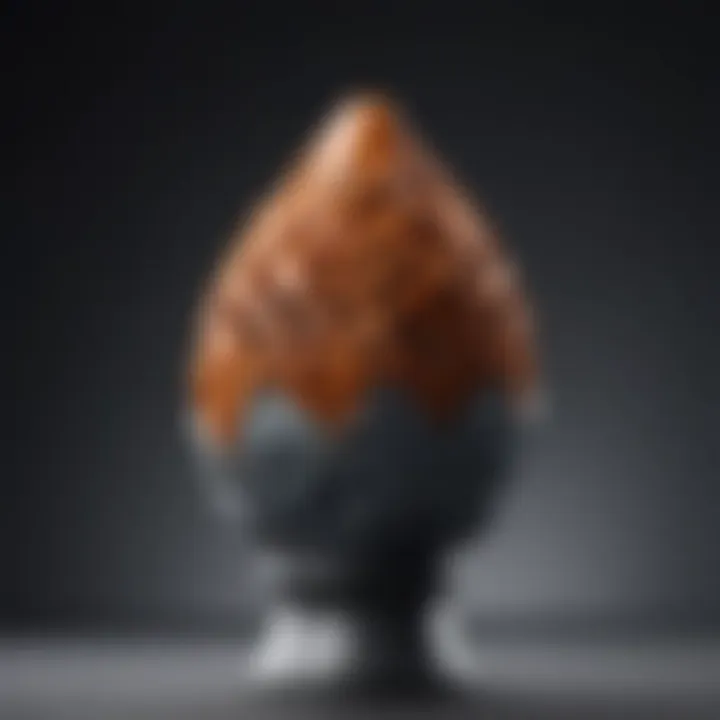
Intro
Carbide ceramics are becoming the talk of the town in materials science. Their remarkable properties, such as extraordinary hardness and superior thermal stability, present a myriad of opportunities across various industries. As we dive deeper, it is essential to understand the foundation of these materials, their diverse applications, and the emerging trends that are reshaping their future.
The charm of carbide ceramics lies not just in their raw characteristics but also in how they are expertly crafted. Their unique blend of toughness and durability makes them particularly relevant in a fast-paced technological landscape, where demands are ever-increasing.
By taking a closer look at the composition, production methods, and practical outcomes, one can recognize the integral role that these materials play today. Whether in creating cutting tools that last longer or wear-resistant coatings that stand up to the rigors of usage, understanding carbide ceramics can offer valuable insights for students, researchers, and professionals alike.
This article aspires to systematically peel back the layers of carbide ceramics, offering a deep dive into their fascinating properties and the recent trends that promise to further their evolution.
Research Context
Background and Rationale
The need for high-performance materials is more crucial than ever. Industries ranging from aerospace to manufacturing depend heavily on components that can withstand extreme conditions. Carbide ceramics have emerged as frontrunners in meeting these needs due to their intricate composition, typically comprising metallic carbide and ceramic phases. This combination yields materials known not only for their hardness but also for resisting wear and thermal degradation.
In recent years, researchers have concentrated on enhancing the performance of carbide ceramics further. Innovations in processing techniques, such as hot pressing and sintering, are enabling the discovery of new properties, broadening their applicability. This demand for lighter yet stronger materials is pushing the boundaries of traditional applications into areas once thought unsuitable for ceramics.
Literature Review
Multiple studies have documented the diversity and effectiveness of carbide ceramics, influencing various sectors. For instance, recent articles detail their significance in cutting tool technology, highlighting improvements in productivity brought about by enhanced tool life due to the hardness of carbide ceramics.
New advances have also been noted in additive manufacturing, where carbide ceramics are being explored for 3D printing applications. This evolution not only lowers production costs but also opens doors to designing complex geometries that align closely with specific use cases.
Collaborative research from sources like Wikipedia, and various academic journals have laid the groundwork for current understandings while paving the way for upcoming trends in carbide ceramics.
Methodology
Research Design
The exploration of carbide ceramics involves a multi-faceted approach. The research not only involves theoretical analysis but also experimental methodologies that facilitate a comprehensive study of these materials. The distinct phases in designing such research may involve comparing physical properties, mechanical assessments, and exploring potential use scenarios in real-world situations.
Data Collection Methods
To gather relevant data, a combination of laboratory experiments and computational models is employed. The experimental setups typically include:
- Performance tests under high-stress conditions
- Thermal stability assessments through controlled heating experiments
- Wear tests simulating real-world application conditions
These methods ensure that collected data is robust, facilitating a thorough analysis of carbide ceramic performance compared to traditional materials. Tools such as X-ray diffraction and scanning electron microscopy are often utilized to characterize the materials further, providing invaluable insights into their integrity and structure.
Preface to Carbide Ceramics
Carbide ceramics stand at the forefront of materials technology, embodying a unique intersection of durability and versatility. These materials are not merely scientific curiosities; they are practical solutions in an array of industries, from cutting tools to aerospace applications. This section serves as a cornerstone, introducing the critical characteristics and historical backdrop of carbide ceramics, laying the groundwork for a deeper dive into their properties and uses.
Definition and Overview
Carbide ceramics are primarily composed of carbide compounds such as silicon carbide (SiC) and tungsten carbide (WC). These materials are known for their exceptional hardness and resistance to wear, making them invaluable in sectors that demand performance under extreme conditions.
In simpler terms, when you think of carbide ceramics, visualize substances that can withstand the forces that would easily wear down metals or other materials. Their toughness and ability to operate at elevated temperatures make them perfect for challenging applications where conventional materials might falter. These ceramics often exhibit low thermal expansion, excellent stability, and impressive chemical resistance, which contribute to their broad appeal.
The unique properties of carbide ceramics emerge not just from their composition but also from carefully engineered microstructures that enhance their performance. Each of these materials has a tale of its own regarding how it interacts with its environment, which sets it apart from traditional ceramic materials.
Historical Development
Delving into the historical trajectory of carbide ceramics reveals a fascinating evolution. Their origins can be traced back to the early 20th century when scientists first synthesized carbide materials in controlled environments.
The development of tungsten carbide dates to the 1920s, initially gaining traction in the manufacturing sector. Companies recognized early on that these ceramics offered superior performance in cutting tools, revolutionizing fabrication techniques. As industries progressed, the demand for more resilient materials propelled research into not only enhancing the specific properties of tungsten carbide but also exploring other carbide compounds like silicon carbide.
Over the years, advancements in manufacturing processes have transformed carbide ceramics from niche materials to mainstream solutions. Today, they play a crucial role in everything from medical device components to high-performance sporting goods.
Understanding the historical context helps elucidate why carbide ceramics have become foundational choices in high-tech applications. As we continue to explore the intricate properties, compositions, and current innovations surrounding these materials, it is clear that their journey is still unfolding, marked by ongoing research and new applications.
Chemical Composition and Structure
Understanding the chemical composition and structure of carbide ceramics is crucial for grasping their remarkable properties and potential applications. The interplay of various chemical elements defines the characteristics of these materials, influencing their behavior under different conditions, including stress, temperature, and environmental exposure. This section delves into the primary materials utilized in the creation of carbide ceramics and their microstructural features, shedding light on how these factors contribute to the performance and reliability of the materials across diverse sectors.
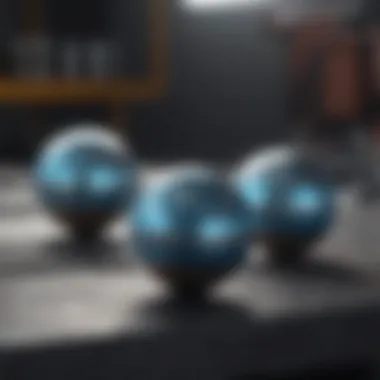
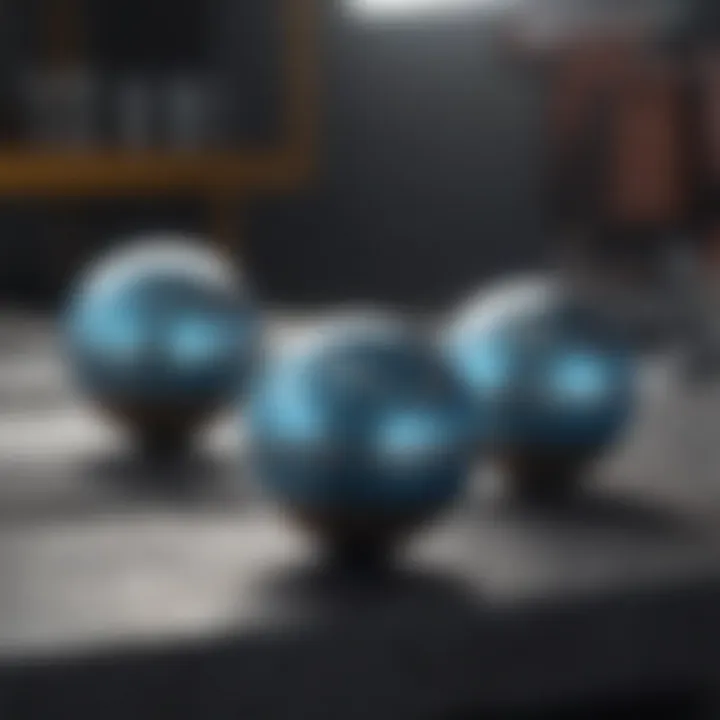
Primary Materials Used
Carbide ceramics are primarily composed of carbon and metallic elements, with tungsten carbide and silicon carbide being the two most prominent types. The selection of these materials is not casual; rather, it is a calculated decision based on their distinct properties:
- Tungsten Carbide: Known for its exceptional hardness and resistance to wear, tungsten carbide is indispensable in manufacturing cutting tools and industrial machinery components. Its high melting point and strength make it ideal for applications that endure significant mechanical stress.
- Silicon Carbide: This material is revered for its thermal stability and excellent electrical conductivity. These traits make silicon carbide particularly useful in high-temperature applications and semiconductor technologies. Its robustness against chemical corrosion further enhances its appeal in various fields.
The choice of these materials directly affects the final characteristics of the carbide ceramics. For instance, the proportion of metal to carbon in tungsten carbide can be adjusted to create a product that balances hardness with toughness. This versatility is essential in meeting specific operational demands.
Microstructural Characteristics
The microstructure of carbide ceramics is another pivotal aspect of their overall performance. It typically consists of interlocking crystalline grains which contribute to their high strength and durability. A few key features that underpin the microstructural properties include:
- Grain Size: Smaller grains in carbide ceramics often lead to improved hardness and strength. This is due to the grain boundary acting as a barrier to dislocation motion, which enhances resistance to deformation.
- Porosity: The density and porosity of these materials significantly impact their mechanical properties. Lower porosity usually correlates with better strength and wear resistance, making the manufacturing process critically important.
- Phase Composition: The presence of different phases within the carbide structure can influence its thermal and mechanical performance. For example, the secondary phases often present in tungsten carbide can help in tuning certain properties, such as the material's brittleness or hardness.
"The microstructure is the backbone of carbide ceramics; changes at this level can lead to entirely different performance outcomes."
To summarize, the chemical composition and structure of carbide ceramics are not just technical details; they are fundamental elements that empower these materials to excel in demanding environments. By understanding the specific materials used and how their microstructural features contribute to overall performance, researchers and practitioners can better harness the capabilities of carbide ceramics in advanced applications.
Manufacturing Processes of Carbide Ceramics
The manufacturing processes of carbide ceramics are crucial in determining their quality and performance. These processes lay the groundwork for shaping the raw materials into materials capable of withstanding extreme conditions. Given the demands of various industries—from aerospace to medical devices—understanding how carbide ceramics are produced can reveal insights about their effectiveness and longevity.
When discussing manufacturing methods, two prominent ones stand out: sintering and additive manufacturing. Each method has unique advantages and challenges, shaping not just the physical properties of the final products but also influencing their cost, scalability, and environmental impact.
Sintering Techniques
Sintering is at the heart of producing carbide ceramics. This process entails heating powdered substances to a temperature below their melting point, allowing particles to bond without fully liquefying. Foreign substances often serve as binders to enhance the consolidation of the powder particles.
One common approach used in sintering is the high-temperature sintering technique. In this method, temperatures often reach over a thousand degrees Celsius. The heat induces diffusion, resulting in improved hardness and density of the material. The challenges here often relate to uniform heat distribution and managing the evaporation of elements present in the carbide mixture. If these factors are overlooked, the final product may suffer from defects.
There is also pressure-assisted sintering, including methods like hot isostatic pressing. This technique enables densification under both elevated temperature and applied pressure, which often enhances the mechanical strength further. The cost associated with equipment and energy consumption raises considerations about long-term sustainability.
Overall, the sintering process takes center stage. Here, the delicate dance of temperature and pressure determines the final characteristics of the carbide ceramic. Without a well-optimized sintering stage, you're left with lackluster performance and diminished capabilities.
Additive Manufacturing Implications
Additive manufacturing presents an exciting frontier in the realm of carbide ceramics. Unlike traditional methods, which often rely on subtractive approaches, additive manufacturing builds parts layer by layer, providing significant freedom in design.
The implementation of techniques like 3D printing allows for intricate geometries and greater material efficiency. When additively manufacturing carbide ceramics, the process typically involves using a resin or binder that is later cured to solidify the object. One must be mindful of the post-processing steps, as they often include additional sintering to achieve the desired mechanical properties. Nonetheless, these processes can reduce waste and enable faster production times, capturing interest in modern manufacturing landscapes.
There are certain limitations to consider, such as achievable resolution and consistency. Each layer in 3D printing can introduce variations that, if not precisely controlled, could impact the material’s overall performance. However, despite these challenges, the benefits of additive manufacturing in carbide ceramics can be game-changing, paving the way for innovative applications that previously seemed out of reach.
The manufacturing processes of carbide ceramics reveal a world of complexity and potential. Each technique contributes distinctively to the properties of the ceramics, ultimately influencing their applications across various industries.
Mechanical Properties
The mechanical properties of carbide ceramics play a critical role in understanding their performance and applications across various industries. These properties dictate how the materials behave under stress, temperature changes, and wear conditions. The significance of studying these properties cannot be overstated, especially in fields that demand high durability and structural integrity. By analyzing aspects such as hardness, tensile and compressive strength, and thermal properties, one can grasp why carbide ceramics are often the material of choice for challenging environments.
Hardness and Wear Resistance
Hardness is perhaps the most distinguishing characteristic of carbide ceramics. It's measured by ability to resist deformation under load, and this trait is what makes these materials highly sought after in applications where wear is a concern. For instance, in cutting tools, carbide ceramics maintain their sharpness longer than traditional materials, reducing the frequency of replacements. Their toughness allows for extended lifespan and improved productivity in industrial processes.
Moreover, wear resistance is intrinsically linked to hardness. When materials are exposed to abrasive conditions, those with superior hardness typically experience less degradation. This results in lower operational costs over time, as the need for maintenance and replacement diminishes. Cleaner operations with enhanced efficiency are achieved as a result.
Examples of applications that showcase this unique strength include tooling in aerospace manufacturing and the production of high-performance machinery components. In such high-demand settings, the failure of materials can lead to substantial economic losses and productivity dips, and carbide ceramics help mitigate these risks.
Tensile and Compressive Strength
Tensile strength refers to a material's ability to withstand pulling forces, while compressive strength pertains to resistance against pressing forces. Carbide ceramics often exhibit impressive levels of both, making them outstanding materials for applications that require load-bearing capabilities. Their resistance to breaking under tension or crushing under compression is noteworthy.
Many industries utilize this property in components like turbine blades and high-stress bearing surfaces, which must endure demanding operational conditions. The ability to maintain structural integrity under a variety of stresses is crucial. It ensures longevity and reliability, factors that can't be compromised in sectors such as automotive or construction.
The advanced microstructural arrangements in carbide ceramics contribute significantly to these strengths. Fine grain structures enhance performance, offering a balance between ductility and brittleness. This interplay determines the suitability of these materials for specific uses, making ongoing research essential for optimizing their deployment.
Thermal Properties
Thermal stability is another essential aspect of carbide ceramics. Their ability to resist thermal shock and maintain performance at elevated temperatures speaks volumes about their versatility in demanding settings. In applications such as furnace linings or parts exposed to intense heat, the ability to maintain integrity without deforming is vital.
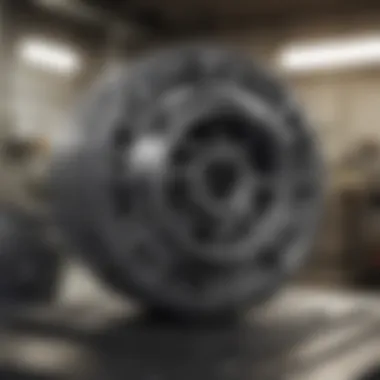
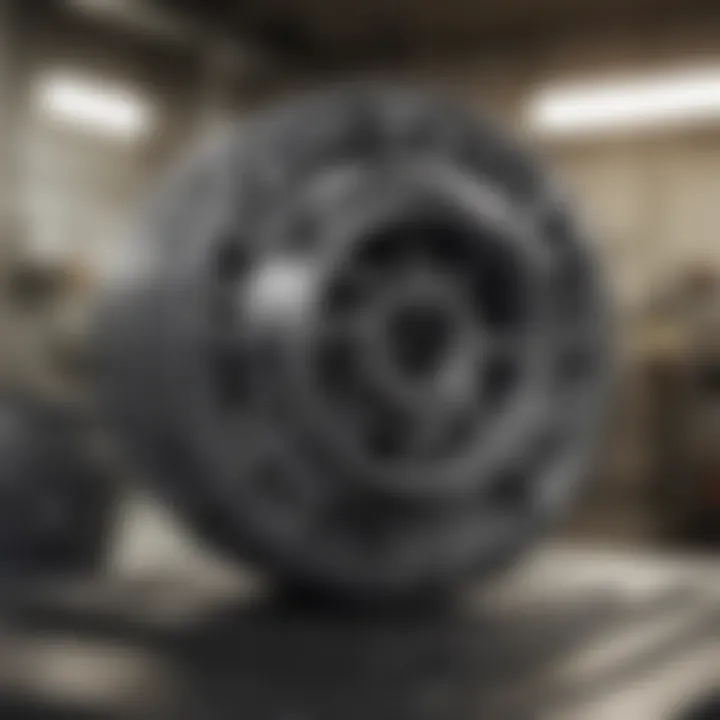
Carbide ceramics exhibit low thermal expansion, which means they do not undergo significant dimensional changes with temperature fluctuations. This stability is fundamental not only for operational reasons but also for safety and reliability across applications. In the technology sectors, for example, this reduces the likelihood of component failure, which can lead to catastrophic results.
"Carbide ceramics are not just materials; they are solutions for modern engineering problems that demand reliability and durability in extreme conditions."
In summary, the mechanical properties of hardness, tensile and compressive strength, and thermal properties combine to position carbide ceramics as an exceptional choice for various applications. Understanding these elements helps researchers, students, and professionals alike in discerning the full capabilities of these remarkable materials.
Applications of Carbide Ceramics
Carbide ceramics are not just technical marvels; they offer a mosaic of potential across various industries. Their superior hardness, thermal conductivity, and resilience make them perfect for tough applications that demand more than conventional materials can provide. Each application area reveals unique benefits of carbide ceramics, thereby solidifying their place in the evolving landscape of advanced materials.
Cutting Tools and Machinery
Cutting tools stand as a prime example where carbide ceramics shine brightly. These tools, often found in manufacturing environments, endure relentless wear and tear. Carbide ceramics, particularly tungsten carbide, offer excellent hardness and wear resistance, ensuring longer lifespans and reduced frequency of tool changeovers. This translates to decreased downtimes in production, a vital consideration for maintaining productivity.
"Using carbide ceramic tools can boost operational efficiency significantly, leading to cost savings in the long run."
The ability to withstand high temperatures without losing integrity further enhances their performance in cutting applications. For instance, modern CNC machines equipped with carbide ceramic tooling can operate at speeds far beyond what traditional tools could handle. This not only increases throughput but elevates the quality of the finished products.
Aerospace and Defense
In the realms of aerospace and defense, the stakes are high where reliability is paramount. Carbide ceramics have carved a niche here due to their remarkable strength-to-weight ratio and thermal stability. Aircraft components, like engine parts and heat shields, often utilize these ceramics to withstand intense operational conditions without compromising safety.
Additionally, the use of carbide ceramics in armor systems has sparked interest. These materials can offer ballistic resistance that meets stringent military standards. The development of advanced ceramic composites often involves combining carbide ceramics with other materials, enhancing their protective capabilities. Thus, they are integral not only for functional performance but also for ensuring adherence to regulatory mandates.
Medical Devices
In the medical field, where precision and biocompatibility are essential, carbide ceramics are gaining traction. These materials are increasingly found in dental applications, like crowns and bridges, owing to their aesthetic appeal and durability. Carbide ceramics present minimal wear on opposing teeth while maintaining a lifespan that rivals or exceeds traditional materials.
Moreover, the orthopedic sector is benefiting from the production of prosthetic joints made from carbide ceramics. Their resistance to wear and ability to perform under mechanical stress are crucial; thus, patients experience improved mobility and reduced post-surgical complications. This adoption of carbide ceramics signifies an exciting intersection of technology and healthcare, with many patients enjoying enhanced outcomes due to this innovation.
Sports Equipment
When it comes to sports equipment, carbide ceramics are not the first material that springs to mind, but their impact is undeniable. In high-performance sports gear—like tennis rackets, golf clubs, and bicycle frames—carbide ceramics are utilized to enhance the robustness of the equipment. Their light weight, coupled with superior strength, allows manufacturers to create products that perform better and last longer.
For example, some tennis rackets incorporate carbide ceramic inlays to provide an efficient energy transfer during play, allowing for maximum power and control. Athletes benefit from both the performance enhancements and the longevity of their equipment, thanks to these materials. Hence, carbide ceramics are slowly but surely, changing the sporting landscape by improving player experience and outcomes.
In summary, the applications of carbide ceramics are varied and poignant. Their properties not only meet but exceed the demands of industry, healthcare, and sport, establishing them as a cornerstone of modern material science. As industries continue adapting and evolving, the role of carbide ceramics will likely expand even further, promising new solutions and innovations.
Comparative Analysis with Other Ceramics
In the realm of materials science, assessing the performance of carbide ceramics in relation to other ceramics is crucial. Such an analysis not only sheds light on where carbide ceramics excel but also helps identify their limitations and areas for improvement. This comparative perspective offers valuable insights for manufacturers and engineers in selecting materials for specific applications.
Understanding Performance Metrics
When we look at performance metrics, several factors come into play. The following are some key areas of focus:
- Hardness: Carbide ceramics are revered for their exceptional hardness, which often surpasses that of alumina and silica ceramics. This property makes them highly suitable for abrasive environments.
- Fracture Toughness: While carbide materials can be quite sturdy, they sometimes lag behind in fracture toughness when set against materials like zirconia. Understanding this metric can aid in making informed decisions in applications where impact resistance is paramount.
- Thermal Stability: The ability to withstand high temperatures is a significant factor for ceramics used in demanding industrial settings. Carbide ceramics generally exhibit superior thermal stability compared to their alumina counterparts, which can lose structural integrity under high heat.
A quantitative comparison can provide a clearer perspective. For instance, while the Vickers hardness of carbide ceramics can reach values of up to 3000 HV, alumina ceramics usually sit around 1500 HV. This stark difference underscores the potential of carbide ceramics in fields requiring high wear resistance.
"A thorough comparative analysis leads to astute material choices, poised to enhance performance in diverse applications."
Cost-Benefit Considerations
Evaluating the cost-effectiveness of carbide ceramics against other materials involves a multi-faceted approach. Several factors influence this decision:
- Raw Material Supply: The extraction and processing of tungsten carbide, the key component in carbide ceramics, can entail higher initial costs than more commonly available materials like alumina or silicate. It's a balancing act between quality and expense.
- Longevity and Maintenance: The initial high cost of carbide ceramics may be offset by their long lifespan and reduced maintenance in harsh applications. The longevity reduces the frequency of replacements, making a strong case for their use in industries like mining and manufacturing.
- Market Demand: The increasing adoption of carbide ceramics across various industries translates to a growing market. This can lead to economies of scale, potentially lowering costs as demand increases.
When weighing these considerations, it’s essential to align them with the application’s specific demands. Industries prioritizing durability over cost might find carbide ceramics an invaluable investment despite their higher price point.
Environmental Considerations
The growing emphasis on sustainability in material science cannot be overstated, especially within the context of carbide ceramics. As industries strive to meet stringent environmental standards, the focus on eco-friendly practices is becoming central to their operations. Carbide ceramics offer a dual advantage: they not only exhibit remarkable performance characteristics but also align with the principles of environmental stewardship. Evaluating how these materials can be produced sustainably and how they can be effectively reclaimed at the end of their life cycle are critical aspects that this section will address.
Sustainability in Production
When we talk about sustainability in the production of carbide ceramics, we wade into the waters of resource efficiency and energy consumption. One of the primary materials used in the creation of carbide ceramics is tungsten carbide, derived from natural resources. The extraction and processing of raw materials can have a significant environmental impact—from mining activities that disturb ecosystems to the carbon footprint associated with their manufacturing.
However, manufacturers are increasingly adopting practices aimed at reducing these impacts. For instance, some companies have begun to utilize recycled materials as feedstocks, which lowers the demand for virgin resources. Using recycled tungsten carbide not only conserves natural resources but also minimizes waste generated from production processes. In addition, advancements in sintering technology—especially in controlling temperature and time—have resulted in reduced energy consumption during the manufacturing phase.
- For instance, a facility that previously required excessive energy input to sinter components can now operate at lower temperatures, thus reducing its overall carbon emissions.
- Moreover, implementing closed-loop water systems in manufacturing helps in conserving water, a critical factor in sustainability.
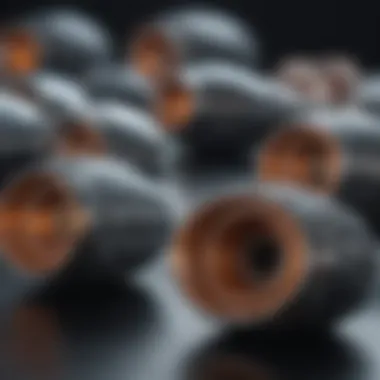
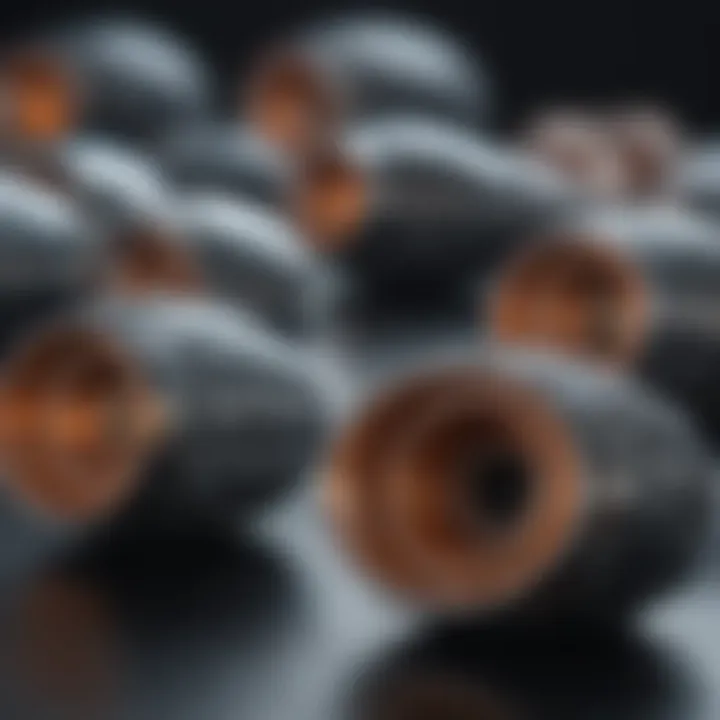
In sum, the path to aligning carbide ceramics production with environmental goals is becoming increasingly clear. Companies that prioritize sustainable practices are likely to gain a competitive edge, as both consumers and regulatory bodies are placing more value on eco-conscious operations.
Recycling and Reclamation
Recycling and reclamation of carbide ceramics emerge as crucial components in achieving a circular economy. Carbide ceramics, with their durable nature, do not readily degrade, which places them in a unique position concerning waste management. The challenge, however, lies in how effectively these materials can be recycled or reclaimed after their end-of-life use.
Current practices for recycling carbide ceramics involve several methodologies. One approach includes mechanical recycling, which involves grinding used carbide tools into fine powders. This recyclate can then be blended with virgin materials to produce new carbide components. The economic benefits linked to this method can be substantial, as it allows manufacturers to cut costs on raw materials and reduces waste.
"Recycling carbide ceramics is not just about reducing waste; it’s also about leveraging existing materials to create new value."
Another avenue of reclamation involves chemical recycling, where complex processes are employed to recover pure metal contents from worn-out carbide products. This process is often more involved but can yield high-quality feedstocks. Industries will need to further invest in research and develop efficient methods for recycling that are both economically and environmentally viable.
With ongoing innovations and increased awareness regarding material sustainability, the future looks promising for carbide ceramics in the context of recycling and reclamation. The commitment towards developing these practices will not only benefit the environment but also create economic opportunities within the material science sector.
Future Trends in Carbide Ceramics Research
The exploration into future trends of carbide ceramics is not just an academic pursuit; it's a pivotal aspect of adapting to ever-evolving industrial demands. New developments in this field reveal significant potential, focusing on enhancing performance characteristics and broadening the applications of these materials. By aligning research efforts with pressing industry requirements, the evolution of carbide ceramics can lead to a marked improvement in efficiency and sustainability in manufacturing and technology.
Innovations in Material Design
Designing better materials often requires reshaping our understanding of how constituents interact at the atomic level. Recent advancements in the material design of carbide ceramics focus on the integration of nanotechnology and composite materials. Researchers are experimenting with altering particle sizes and distributions, which, in turn, influence grain growth and phase stability. This intricate dance between particle dynamics and properties holds the key to unlocking new functionality in carbide ceramics.
For example, by utilizing nanoparticles in the synthesis of carbide ceramics, it’s possible to engineer materials with unprecedented mechanical strength and thermal stability. This has implications far beyond the laboratory; these advancements can lead to stronger cutting tools and wear-resistant parts that extend operational lifespans.
"Innovating at the atomic level isn't just science fiction; it's the future of material creation."
Furthermore, developing biomimetic designs—those that mimic natural structures—can also enhance toughness without compromising lightweight characteristics. The potential here not only lies in industrial application but might also extend into areas like aerospace engineering, where both strength and weight are critical concerns.
Potential New Applications
The potential applications of carbide ceramics are vast, and the future trends hint at a greater role in sectors that urgently need innovative solutions. One noteworthy focus is the integration of carbide ceramics in the realm of renewable energy. For instance, in solar energy production, improved thermal resistance embraces the efficiency of solar panels. As the world pivots towards sustainability, the applications in energy efficiency can significantly reduce the carbon footprint associated with energy systems.
Additionally, carbide ceramics are being researched for their potential in advanced electronics. Their insulating properties combined with high thermal conductivity make them suitable candidates for thermal management in electronic devices. As technology continues to shrink in size while increasing in capability, the demand for efficient heat dissipation is greater than ever.
- Construction Materials: The durability of carbide ceramics makes them ideal for high-stress environments, such as construction or mining applications.
- Wear-resistant Coatings: Their excellent wear performance could lead to coatings that enhance not only tool life but also the longevity of machinery components in various industries.
The adaptability and robustness of carbide ceramics are critical as we move towards smart manufacturing and the Industry 4.0 paradigm. Tailoring materials through ongoing research and technological innovation positions carbide ceramics at the forefront of modern engineering solutions.
Challenges in the Field
In discussing carbide ceramics, it becomes essential to address the challenges in the field. While these materials hold great potential due to their unique properties, several obstacles hinder their broader adoption and optimization in various sectors. Tackling these challenges not only facilitates better understanding but also guides researchers and engineers in innovating solutions that can enhance the utility and effectiveness of carbide ceramics.
Technical Limitations
One of the primary concerns related to carbide ceramics is their technical limitations. Despite their impressive hardness and thermal stability, these materials can present significant challenges during processing and application. For instance:
- Brittleness: Carbide ceramics often exhibit high rigidity but low toughness, making them susceptible to fracture under impact or stress. This brittleness can limit their application in high-stress environments.
- Processing Difficulties: The high melting points of carbide materials necessitate specialized processing techniques, such as ultra-high temperature sintering, which can complicate manufacturing and increase costs.
- Dimensional Precision: Achieving precise dimensions during fabrication can be difficult, as shrinkage during cooling often leads to dimensional changes that impede end-use performance.
These limitations prompt researchers to look for innovative processing methods or composite materials to enhance the toughness without compromising the hardness that carbide ceramics are known for. Addressing these issues will be crucial for the advancement of applications in sectors ranging from aerospace to medical devices.
Market Competition
Another significant hurdle relates to market competition. The field of advanced materials is vast, with numerous options available to manufacturers and consumers alike. For carbide ceramics to carve their niche, several factors come into play:
- Cost Effectiveness: The production of carbide ceramics can be expensive compared to other materials like metal or conventional ceramics. If a cheaper alternative provides adequate performance, potential users might opt for those instead.
- Awareness and Education: There may be a lack of understanding regarding the benefits of carbide ceramics among manufacturers and end-users. This can result in reluctance to adopt them, especially where traditional materials have established a stronghold.
- Rapid Technological Advancements: With ongoing developments in competing materials, such as advanced polymers and hybrid composites, carbide ceramics must continually evolve. Staying ahead in terms of innovation is crucial to retain interest and market share.
As it's laid out, overcoming market competition through a combination of education, cost-benefit analysis, and persistent innovation becomes vital for promoting these materials. Only then can carbide ceramics achieve the recognition they deserve in the increasingly crowded space of advanced materials!
Ending
Concluding an exploration into carbide ceramics is not just a summary of what was discussed, but it serves as a fundamental reflection on the topic’s significance in modern material science. The importance of understanding carbide ceramics is manifold; they embody critical properties that enhance their applicability across varied industries, from manufacturing to the aerospace sector. The deep dive into their unique chemical structures, mechanical traits, and manufacturing processes has unearthed not only their strengths but also the challenges that lie in this field.
Summary of Key Points
In this article, we traversed various facets of carbide ceramics:
- Chemical Composition: We discerned the unique elements that constitute carbide ceramics, emphasizing their robustness and stability.
- Manufacturing Techniques: The discussion around sintering and additive manufacturing highlighted how innovations are redefining production methods.
- Mechanical Properties: Hardness, wear resistance, and thermal stability were showcased as the cornerstone attributes that make carbide ceramics vital for cutting tools and industrial applications.
- Applications: An extensive look into industries utilizing these ceramics demonstrated their adaptability and necessity.
- Emerging Trends: We noted the future directions for research and development, indicating a promising horizon for further advancements.
- Challenges: The obstacles faced, including market competition and technical limitations, were discussed to provide a balanced view of the current landscape.
Final Thoughts on Carbide Ceramics
Carbide ceramics are more than just a technical marvel; they demonstrate the interplay between material properties and engineering solutions. As industries continue to push the limits of efficiency and performance, the role of these materials cannot be overstated. Their continued development hinges on addressing existing challenges while leveraging new technological strides. As researchers and professionals examine their full potential, carbide ceramics are poised to remain at the forefront of material science. Their relevance is only expected to grow as new applications emerge, leading us into a future where the insights gained today pave the way for tomorrow's innovations.
"The future is not a gift. It is an achievement."
This encapsulates the essence of what carbide ceramics can offer—an ongoing journey of innovation and application in materials science.