Exploring Carbon Fiber Reinforced Nylon Filament
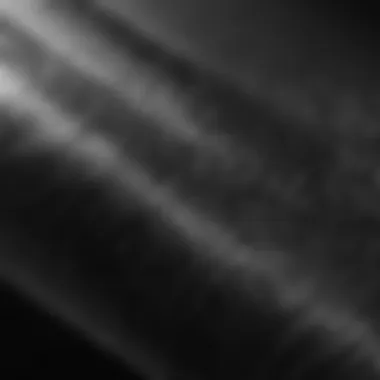
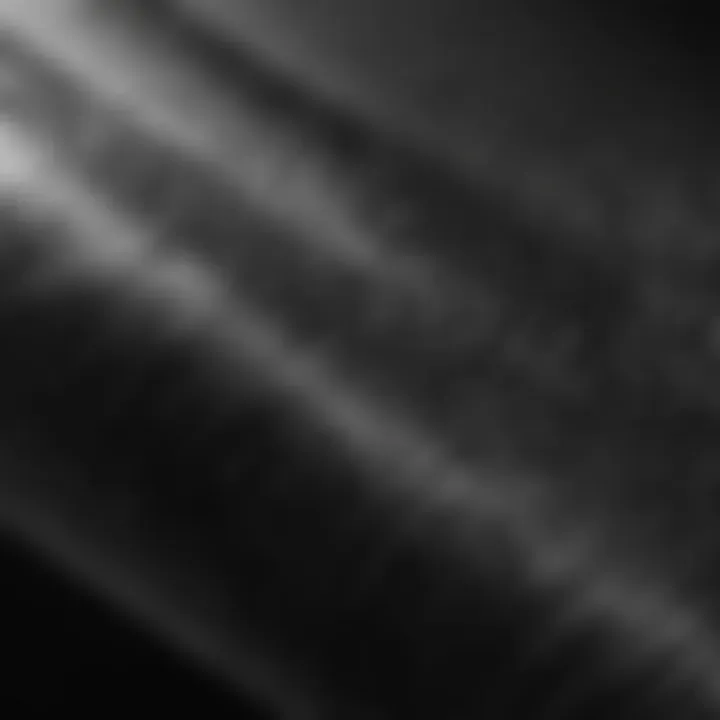
Intro
Carbon fiber reinforced nylon (CFRN) 3D printing filament stands out as a significant advancement in the field of additive manufacturing. Its unique composition combines the strength and rigidity of carbon fiber with the flexibility and durability of nylon. This combination results in a material that not only meets the demands of complex engineering applications but also offers enhanced performance characteristics when compared to standard nylon filaments.
As 3D printing technology evolves, understanding materials such as CFRN becomes essential for various stakeholders, including students, researchers, and professionals. The relevance of CFRN lies in its ability to produce parts that require high strength-to-weight ratios, making it suitable for applications in automotive, aerospace, and industrial sectors.
The following sections will explore the research context surrounding CFRN, delve into its methodology of production, and analyze its applications. This exploration will provide insights into why CFRN is a material of interest and how it can be effectively utilized in various contexts.
Research Context
Background and Rationale
The development of CFRN filament arose from the need for materials that can withstand greater stress during performance. Traditional nylon has limitations in load-bearing capabilities, particularly in high-demand environments. By integrating carbon fiber into the nylon matrix, manufacturers created a composite material that significantly improves mechanical properties.
Researchers have shown that CFRN exhibits better tensile strength and stiffness than standard nylon. This improvement opens new avenues for its application in areas where conventional materials might fail.
Literature Review
Numerous studies have explored the properties of CFRN, including its processing techniques and end-use performance. Some key findings indicate:
- CFRN prints exhibit reduced warping, enhancing the ease of printing.
- The thermal properties of CFRN allow it to be used in applications requiring thermal stability.
- Certain printing parameters, such as nozzle temperature and print speed, directly affect the final properties of the printed parts.
A comprehensive review of the existing literature reveals that while CFRN offers substantial advantages, it also poses challenges in terms of printability and material handling. For those interested in deepening their understanding of CFRN, resources such as Wikipedia and Britannica provide valuable foundational knowledge.
Methodology
Research Design
The analysis of CFRN can be approached through both qualitative and quantitative research methodologies, depending on the focus of the study. Qualitative studies may explore user experiences and application-specific requirements, while quantitative approaches assess physical properties and performance metrics.
Data Collection Methods
Data collection methods could include:
- Experimental Studies: Conducting tests to assess mechanical properties under varying conditions.
- Surveys: Gathering user feedback on printability and performance from professionals who work with CFRN.
- Literature Reviews: Analyzing existing studies to gather information on best practices and challenges in CFRN usage.
This structured approach ensures a comprehensive understanding of CFRN's capabilities, limitations, and practical applications in the world of 3D printing.
Intro to Carbon Fiber Reinforced Nylon Filament
The evolution of 3D printing technology has led to the exploration of specialized materials that can enhance both the quality and the applicability of printed objects. Among these materials, carbon fiber reinforced nylon (CFRN) filament stands out due to its exceptional properties, leading to its growing significance in various industries. This introduction serves to lay the foundation for a deeper understanding of CFRN, focusing on its definition, composition, and historical context.
CFRN filament combines the lightweight and flexible nature of nylon with the superior strength characteristics of carbon fiber. This unique amalgamation results in a printing material that offers improved strength without a significant increase in weight. Whether for industrial applications or prototyping, the benefits of CFRN are noteworthy. However, it is essential to recognize the unique considerations that come with working with this filament, such as print settings and equipment compatibility.
By understanding the components and history of CFRN, users can make informed decisions in their applications. This section introduces the fundamental aspects of carbon fiber reinforced nylon filament, providing essential insights that amplify its relevance in the modern 3D printing landscape.
Definition and Composition
CFRN filament is defined as a hybrid material composed primarily of nylon, typically polyamide, enhanced with short strands of carbon fiber. The carbon fibers are usually distributed throughout the nylon matrix, providing reinforcement that significantly elevates the mechanical properties of the filament. The composition allows for improved tensile strength, stiffness, and overall durability compared to traditional nylon materials.
The primary components of CFRN include:
- Nylon Matrix: This polymer serves as the base material, offering flexibility and thermal stability.
- Carbon Fibers: These fibers contribute to enhanced mechanical properties, specifically increasing rigidity and strength without adding considerable weight.
The blending of these two materials results in a filament that can withstand demanding applications while retaining ease of printability.
Historical Development
The development of carbon fiber reinforced nylon can be traced back to the advancements in both nylon polymers and carbon fiber technology. Nylon itself has been used in various industrial applications since its introduction in the 1930s, valued for its flexibility, chemical resistance, and strength. As 3D printing technology emerged, particularly in the realms of additive manufacturing, researchers sought to improve the performance of existing polymers through reinforcement techniques.
Carbon fiber technology started gaining traction in the mid-20th century, known for its rigidity and strength. As these two materials became more accessible, innovators began experimenting with their combination, ultimately leading to the creation of CFRN filament.
This development aligns with the industry's shift toward high-performance 3D printing materials, enabling engineers and designers to produce components that could withstand greater mechanical stresses while remaining lightweight. Today, CFRN filament is increasingly recognized across various sectors, particularly in aerospace, automotive, and consumer products, marking a significant milestone in the journey of 3D printing materials.
Properties of Carbon Fiber Reinforced Nylon
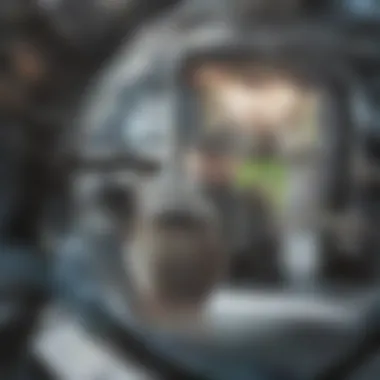
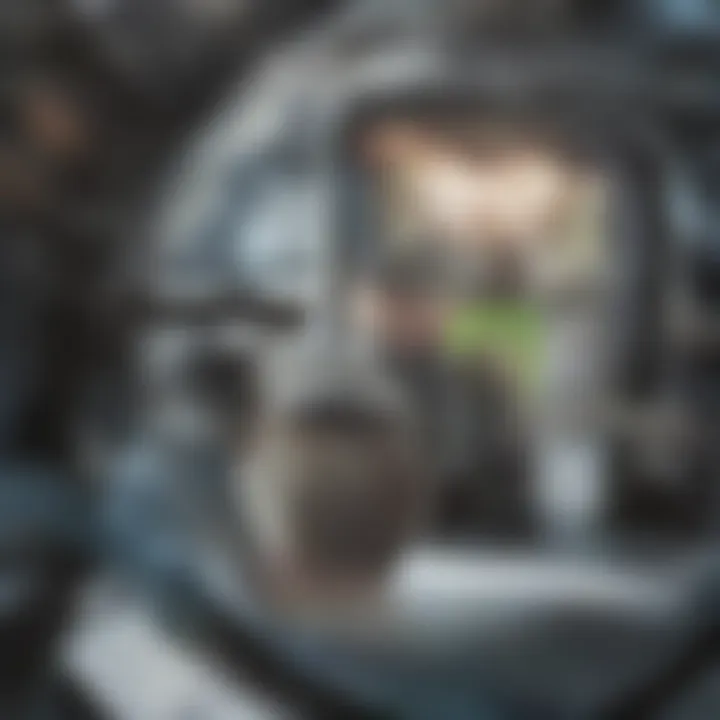
Understanding the properties of carbon fiber reinforced nylon (CFRN) is vital for anyone involved in 3D printing. These properties dictate how this material performs under various conditions, impacting everything from print quality to end-use applications. By analyzing these attributes in detail, users can better appreciate the advantages and challenges that come with CFRN, enabling more informed decisions when integrating it into their projects.
Mechanical Properties
CFRN is recognized for its impressive mechanical properties. One of the most notable attributes is its high tensile strength. The carbon fiber component greatly enhances the filament's ability to withstand stress without deforming. This strength allows for the creation of strong, lightweight parts that can endure rigorous applications.
In terms of rigidity, CFRN exhibits a significant improvement over standard nylon. The addition of carbon fiber results in a filament that resists bending and flexing, making it suitable for applications where shape retention is critical. Moreover, the toughness of CFRN helps it absorb impact, reducing the risk of failure in real-world conditions.
"The incorporation of carbon fibers provides CFRN with a competitive edge in applications requiring high strength-to-weight ratios."
Additionally, the layer adhesion of CFRN is typically quite strong, facilitating the production of durable prints that maintain structural integrity over time. However, a notable consideration is that while it's stronger, CFRN can also be more brittle compared to pure nylon. Users need to balance the desire for strength against potential fragility in specific applications.
Thermal Properties
Thermal properties of CFRN also play an important role in its usability. This filament can withstand elevated temperatures better than many standard 3D printing materials. The heat deflection temperature of CFRN is significantly higher than that of standard nylon. This resistance is crucial for applications that may encounter warmer environments or higher operational temperatures.
Moreover, CFRN exhibits lower thermal expansion compared to traditional nylons. This characteristic contributes to dimensional stability, which is essential in creating precision parts. The minimized warping during the cooling phase means that complex geometries can be printed with greater accuracy, leading to more reliable end products.
Users should, however, still consider printing at higher temperatures to ensure optimal layer bonding. This practice promotes enhanced thermal fatigue resistance, a vital aspect for components subjected to thermal cycling.
Chemical Resistance
CFRN also stands out due to its chemical resistance. The nylon matrix already offers a decent level of resistance to many solvents. When combined with carbon fiber, this characteristic is further enhanced, making CFRN suitable for exposure to various chemicals found in industrial and consumer environments.
It's worth noting that while CFRN does resist many chemicals, no material is universally resistant to every solvent. Users should still conduct tests or refer to chemical resistance charts to ensure compatibility with specific substances.
In summary, the properties of carbon fiber reinforced nylon filament illustrate its status as a powerful material in the 3D printing domain. Its mechanical strength, thermal stability, and chemical resistance position CFRN as a preferred choice for high-performance applications. As users explore these properties, they can effectively align CFRN's strengths with their specific project needs, maximizing the benefits of this advanced filament.
Advantages of Using CFRN Filament
The introduction of carbon fiber reinforced nylon filament (CFRN) has significantly transformed 3D printing. In this section, we will analyze the specific benefits that CFRN filament offers. Understanding these advantages is crucial for anyone looking to utilize 3D printing technology effectively. Whether you are a professional or a hobbyist, knowing why you should choose CFRN can enhance your printing experience and results.
Strength-to-Weight Ratio
One of the most compelling characteristics of CFRN is its excellent strength-to-weight ratio. This property makes it particularly appealing in industries where preventing excess weight is essential while maintaining structural integrity. The addition of carbon fibers enhances the tensile strength of nylon, allowing for the production of lightweight parts that do not sacrifice strength.
In practical applications, this strength-to-weight efficiency can lead to the replacement of heavier materials, promoting overall performance. For example, in aerospace and automotive industries, this advantage translates into more fuel-efficient designs and components. Users can print intricate designs with confidence that the final product will withstand demanding conditions.
Durability and Longevity
Durability is another notable advantage of CFRN filament. The combination of carbon fiber and nylon creates a material that is remarkably resistant to wear, impact, and environmental conditions. This durability is particularly beneficial in applications that experience constant stress or exposure to harsh elements.
Parts produced with CFRN can outperform those made with standard nylon or other traditional materials. This longevity not only reduces the frequency of part replacement but also decreases waste and overall maintenance costs. For businesses, this means less downtime and greater productivity, which is critical in today’s fast-paced market.
Printability and Finish Quality
CFRN filament is not only strong and durable but also offers superior printability. It adheres well during the printing process, leading to minimal warping and excellent layer adhesion. This quality ensures that complex geometries can be printed accurately without the risk of failure.
In terms of finish quality, parts printed with CFRN often exhibit a smooth, professional appearance. Users can achieve high-detail prints, which is especially important in applications where aesthetic considerations are paramount. Whether for prototyping or final products, the finish quality contributes to the overall effectiveness and appeal of the printed object.
In summary, the advantages of using CFRN filament—its strength-to-weight ratio, durability, and printability—position it as a leading choice for various 3D printing applications. Understanding these benefits allows users to make informed decisions, ensuring optimal use of this advanced material.
Applications of CFRN in Various Industries
Carbon fiber reinforced nylon (CFRN) is transforming many sectors due to its unique combination of properties. The strength and lightweight nature of this filament make it highly versatile. Industries such as aerospace, automotive, consumer products, and medical applications are increasingly leveraging the benefits of CFRN. Understanding its applications can help professionals make informed decisions regarding materials for specific projects.
Aerospace
In aerospace engineering, the weight of materials is critical. CFRN offers an ideal solution because it combines strength and reduced mass, enhancing overall fuel efficiency. For components like brackets, housings, and guides, CFRN can withstand high-stress situations.
Using CFRN, manufacturers can create complex geometries that traditional metal components cannot achieve. Its resistance to fatigue is another essential factor that contributes to its use in this field. Additionally, the ease of 3D printing allows for rapid prototyping, thus shortening development cycles.
Automotive
In the automotive industry, CFRN is prominent due to its potential for lightweight designs. As manufacturers seek ways to improve fuel efficiency and performance, CFRN components become more beneficial.
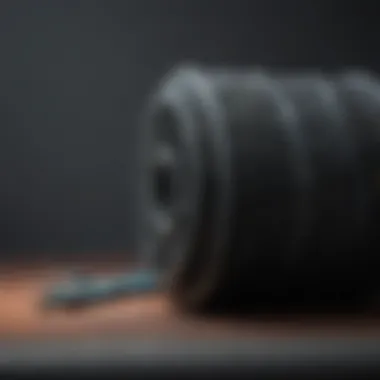
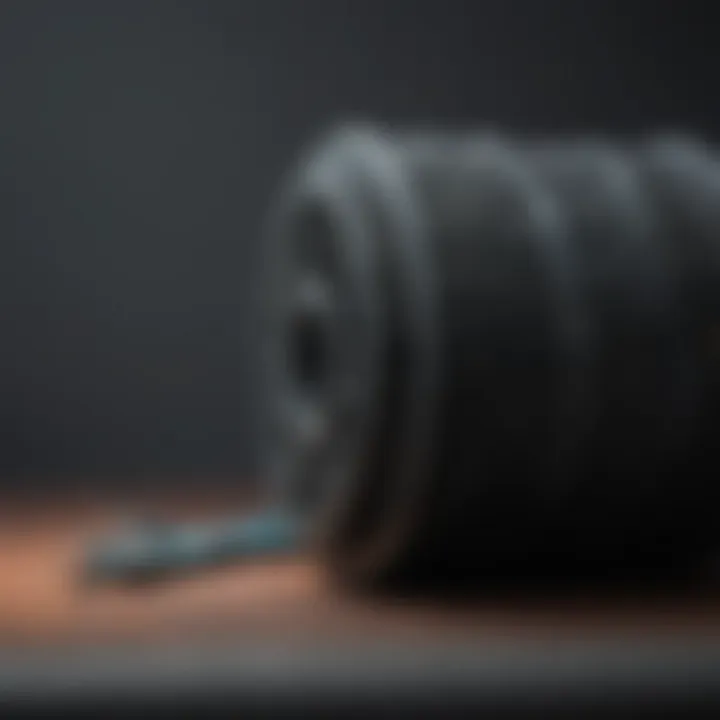
Applications include interior parts, frames, and structural components that require a fine balance between strength and weight. The durability of CFRN against impact and heat also offers advantages in various automotive designs, enhancing safety. Its ability to be tailored through 3D printing enables customization for specific vehicle models, allowing for innovation in design.
Consumer Products
Consumer products benefit from CFRN in a variety of ways. 3D printing technologies allow companies to produce items that are not only lightweight but also durable. Items like custom-designed gadgets, protective cases, and sporting goods greatly benefit from the material's characteristics.
The stylish finish that can be achieved with CFRN is appealing to consumers. Businesses can produce aesthetically pleasing designs without compromising strength. Moreover, the adaptability of CFRN makes it useful for small batch productions tailored to niche markets.
Medical Applications
CFRN is making strides in the medical sector for various applications. Its strength is essential for manufacturing prosthetics and other medical devices, where both durability and lightweight properties play a crucial role.
Medical professionals now utilize CFRN for custom products, such as orthopedic braces and supports that can be tailored for each patient's needs. Additionally, the sterilization capability of CFRN is vital for ensuring safety in medical environments. As research advances, the potential future applications may include surgical tools and implants.
In summary, CFRN provides solutions across critical sectors by blending lightweight properties with high strength, proving beneficial for performance and design.
As industries explore CFRN’s potential, the ongoing development promises to uncover even more applications, further enhancing its role in modern manufacturing.
Comparing CFRN with Other 3D Printing Materials
The comparison of carbon fiber reinforced nylon (CFRN) with other 3D printing materials is vital. Understanding these differences helps users select the right filament for their projects. Each material has unique characteristics, advantages, and challenges. This ensures informed decisions for specific applications in various industries.
CFRN vs. Carbon Fiber PLA
CFRN and carbon fiber PLA are both strong materials but cater to different user needs. PLA is easier to print, making it ideal for beginners. However, it lacks the same level of toughness and heat resistance as CFRN.
- Strength and Flexibility: CFRN offers superior strength-to-weight ratio and flexibility, compared to carbon fiber PLA.
- Thermal Stability: CFRN withstands higher temperatures, which means it can be used in more demanding environments.
- Cost Involvement: Carbon fiber PLA is typically less expensive, appealing for cost-sensitive projects. Nevertheless, CFRN may save costs in the long run due to its durability.
In summary, while carbon fiber PLA is suitable for simple prints, CFRN is recommended for high-performance applications.
CFRN vs. ABS
CFRN and ABS each bring distinct strengths to the table. ABS is widely used for its impact resistance and versatility. Yet, CFRN surpasses ABS in key performance areas.
- Mechanical Properties: CFRN exhibits greater rigidity and enhanced tensile strength, beneficial for structural components.
- Printability: ABS tends to warp during printing, necessitating additional care in the setup. Conversely, CFRN maintains more stable properties.
- Chemical Resistance: ABS is susceptible to certain chemicals which can affect print quality. CFRN’s formulation offers better resistance in such cases.
For users requiring durable, high-quality models, CFRN is a more suitable choice over ABS.
CFRN vs. Nylon
Nylon is a popular material in 3D printing, known for its flexibility and strength. When comparing CFRN to nylon, it’s evident that each has unique advantages.
- Composition Differences: CFRN is a blend of nylon with carbon fibers, enhancing its properties significantly compared to standard nylon.
- Dimensional Stability: CFRN reduces warping compared to nylon, making it easier to achieve accurate prints.
- Application Scope: While nylon is favored for its elastic properties, CFRN's enhanced strength makes it ideal for applications where performance is critical.
Overall, CFRN is recommended for applications needing a balance of flexibility and rigidity over regular nylon.
"Understanding differences between CFRN and other materials can greatly impact the success of a project."
By examining the similarities and differences between CFRN and these materials, users can make the best choice for their specific needs.
Best Practices for Printing with CFRN
When engaging with carbon fiber reinforced nylon (CFRN) filament, understanding the best practices for printing is crucial for achieving optimal results. This section delves into critical elements that not only enhance print quality but also prolong the lifespan of your 3D printer. Mastering these aspects leads to effective utilization of CFRN, allowing for the exploration of its full potential in various applications.
Printer Settings Tuning
Optimal printer settings are fundamental for successful printing with CFRN. This filament exhibits unique properties that necessitate adjustments in standard settings. First, ensure you configure the nozzle temperature around 240°C to 260°C. This range facilitates proper melting of the filament while reducing the risk of stringing.
In addition, the bed temperature should be set around 80°C to 100°C. Proper bed heating enhances adhesion during printing, reducing the likelihood of warping.
Layer height and print speed also require attention. A layer height between 0.1 mm and 0.3 mm is advisable, while print speeds should generally be kept between 30 mm/s and 50 mm/s. Slower speeds afford better layer adhesion and improve print integrity, particularly for complex geometries.
Nozzle and Bed Preparation
Preparation of the nozzle and print bed is paramount to achieve high-quality prints with CFRN. The nozzle should be cleaned regularly to eliminate carbon residue that may impact flow. Using a hardened steel nozzle is advisable, as CFRN's abrasive nature can wear down standard nozzles over time.
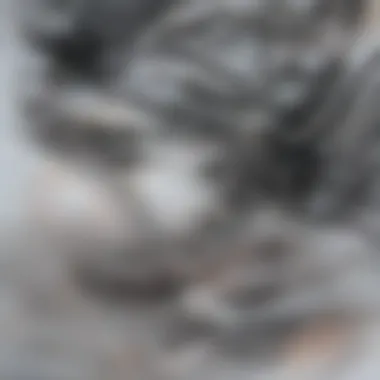
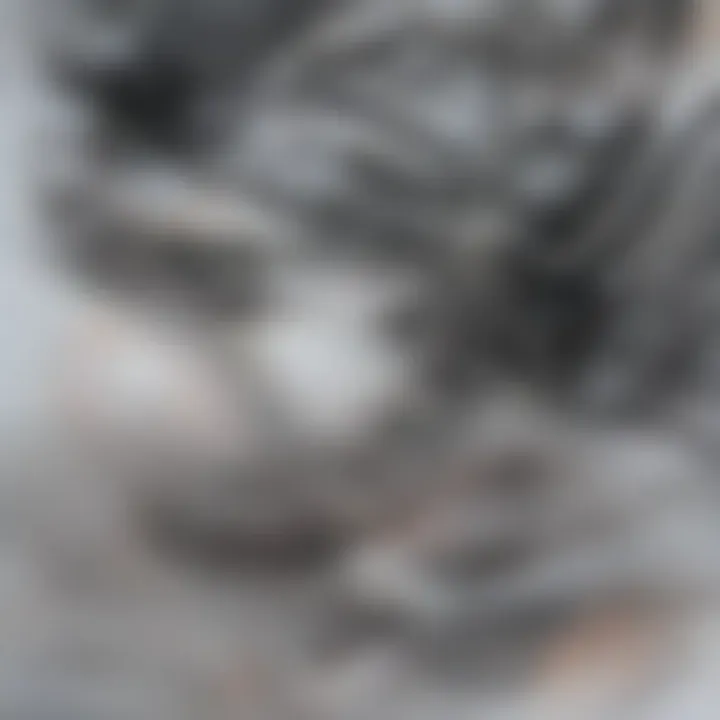
For bed preparation, a suitable surface such as a PEI sheet or glass plate is recommended. Applying a thin layer of adhesive, like PVA glue, enhances bed adhesion. Clean the print surface with isopropyl alcohol before each print to ensure optimal adhesion and to remove any contaminants that might affect the print quality.
Post-Processing Techniques
Post-processing plays a vital role in enhancing the appearance and properties of CFRN prints. Once the print completes, allow it to cool down gradually on the bed before removal. This reduces the risk of warping and ensures dimensional accuracy.
After print removal, surface finishing techniques such as sanding can improve aesthetics. Sanding not only smoothens surfaces but can also enhance inter-layer adhesion by providing a rougher surface for subsequent coatings. If desired, applying a clear coat can protect the print from environmental influences and enhance durability.
"The success in utilizing CFRN greatly relies on understanding and implementing these best practices, ensuring the prints meet the desired quality standards and functionality."
Lastly, it is essential to keep track of print parameters, as different printers and environmental factors may yield varying results. Adjust settings based on previous print outcomes to foster improvements in future projects. This iterative process is key for fostering expertise in using CFRN filament effectively.
Challenges Associated with CFRN Filament
Carbon fiber reinforced nylon (CFRN) offers numerous benefits in the realm of 3D printing. However, these advantages are accompanied by specific challenges that users must navigate. Understanding these challenges is crucial for researchers, educators, and professionals alike. By addressing aspects such as cost, printing limitations, and environmental impact, one can better appreciate both the potential and the hurdles of using CFRN filament in various applications.
Cost Considerations
One of the primary challenges with CFRN filament is its cost. Compared to more common materials like standard nylon or PLA, CFRN can be significantly more expensive. This price point can be a barrier for small businesses or individual hobbyists. The higher costs are due to several factors, including the addition of carbon fibers, which improve the material's properties but also increase manufacturing complexity. Furthermore, the specialized equipment needed for printing with CFRN can also drive up the overall expense.
For instance, users may need to invest in a high-quality 3D printer capable of handling the abrasive nature of CFRN. This includes having a hardened nozzle and a heated print bed to prevent warping. The budget considerations must be weighed against the benefits, ensuring that the enhanced mechanical and thermal properties justify the investment.
Printing Limitations
While CFRN provides exceptional strength and rigidity, it is not without its printing limitations. The material can be difficult to work with, particularly for less experienced users. Some common printing issues include:
- Adhesion Problems: CFRN may struggle with bed adhesion, especially on non-heated surfaces. Properly preparing the print bed and selecting the right type of surface for better adhesion is essential.
- Nozzle Clogging: Due to the carbon fibers in the filament, there is an increased risk of clogging the nozzle. A hardened nozzle is recommended to mitigate this risk.
- Warping: The risk of warping is also heightened with CFRN, which can lead to failed prints. Users must ensure that their printers maintain consistent temperatures to combat this issue.
These printing limitations necessitate careful planning and adjustment of printer settings. Users must become proficient in tweaking settings to achieve optimal results while minimizing print failure rates.
Environmental Impact
The environmental impact of CFRN filament is another significant challenge that requires thoughtful consideration. While carbon fiber itself offers many benefits in terms of strength and weight savings, the production process of carbon fibers and nylon can pose environmental hazards. The extraction and processing of these materials can generate waste and emissions.
Moreover, CFRN filament is not biodegradable, which raises concerns about long-term waste management. As the awareness of sustainable practices grows, users are increasingly considering the life cycle of products and materials used in 3D printing.
Future Trends and Innovations in CFRN Filament Development
The future of carbon fiber reinforced nylon (CFRN) filament development is promising and essential in maintaining its relevance in the 3D printing landscape. As industries continue to seek stronger, lighter, and more cost-effective materials, the emphasis on innovation becomes increasingly critical. Exploring upcoming trends can better prepare users for changes that the market may see. This section will discuss material improvements and technological advancements that are poised to shape the future of CFRN.
Material Improvements
Material enhancements in CFRN filaments focus on refining the chemical composition and overall performance of the product. Manufacturers are investing in research to find ways to improve not just the mechanical properties, but also the usability of the filament.
- Enhanced Fiber Quality: New types of carbon fibers are developed that offer superior tensile strength and flexibility. The integration of these high-quality fibers can result in better performance and durability in printed parts.
- Combination Materials: There’s potential for creating hybrid materials that blend CFRN with other polymers or additives to improve qualities such as impact resistance or thermal stability. Such combinations can open new applications in various domains, from aerospace to consumer products.
- Sustainability Initiatives: As environmental concerns grow, innovations are looking towards more sustainable practices in sourcing and producing CFRN filaments. Biodegradable options or recycling capabilities may present future developments in materials.
"The exploration of sustainable materials in 3D printing is not only a necessity, but also a pathway toward better industry practices."
Technological Advancements
Technological improvements in printing processes and equipment are another critical component of the evolution of CFRN filaments. Advances in printer technology can fundamentally alter the effectiveness and efficiency of 3D printing.
- Improved Printing Techniques: Strategies such as enhanced extrusion processes and advanced filament handling systems can lead to higher efficiency and better results. These techniques can minimize errors during printing and improve the final quality of the printed object.
- Print Quality Monitoring: Innovations in real-time print monitoring and adaptive control systems are emerging. Such systems provide continuous feedback to printers, allowing adjustments on the fly based on the properties of the material being used. This can help eliminate common defects associated with CFRN prints.
- Digital Fabrication Tools: The rise of generative design and AI-assisted manufacturing tools presents a frontier for CFRN filament usage. These tools can optimize designs specifically for CFRN, ensuring that the material's strengths are maximized in the resulting parts.
The incorporation of these material improvements and technological advancements create a dynamic landscape where CFRN continues to evolve. This evolution not only strengthens its current applications but also introduces new opportunities, enhancing the material's overall utility in various fields.
End and Recommendations
The exploration of carbon fiber reinforced nylon (CFRN) 3D printing filament has provided valuable insights into its unique properties, various applications, and considerations for effective use. Understanding the significance of CFRN in the landscape of additive manufacturing is essential for students, researchers, and professionals alike. It is a material that not only stands out for its strength and lightweight characteristics but also offers versatility across multiple industries. As this article has highlighted, making informed decisions entails understanding both the benefits and challenges associated with CFRN.
Summary of Key Insights
In summary, several key points arise from the in-depth analysis of CFRN filament:
- Mechanical Strength: CFRN works best in applications demanding high mechanical strength. It excels due to its impressive strength-to-weight ratio compared to other filaments, like PLA or ABS.
- Thermal and Chemical Resistance: Its ability to withstand higher temperatures and diverse chemicals makes it a preferred choice in environments that may degrade standard materials.
- Printability: Despite its strengths, printing with CFRN presents unique challenges such as nozzle clogging and delamination. Understanding printer settings is crucial.
- Widespread Applications: The material's adaptability allows it to be utilized in aerospace, automotive, and medical sectors, among others.
- Future Innovations: As technology advances, the development of enhanced CFRN materials promises further improvements in performance and sustainability.
Final Recommendations for Users
For those considering CFRN filament, several recommendations can enhance user experience:
- Conduct Tests: Always run tests on sample prints before committing to larger projects. This helps in understanding how different printer settings affect the final output.
- Maintain Equipment: Regular maintenance of 3D printers ensures optimal performance. This is especially important when using composite materials like CFRN, which can cause more wear on components.
- Stay Informed: Keep abreast of developments in materials science. Innovations in the properties of CFRN could lead to better print quality and new applications.
- Consider Cost vs. Benefit: Weigh the costs of CFRN filament against its benefits for specific projects. Price may initially be higher than standard filaments, but the long-term advantages can justify the investment.
- Follow Best Practices: Adhere to established best practices for printing with CFRN, such as optimal nozzle size, temperature settings, and post-processing techniques, to achieve the best results.
"Understanding the strengths and limitations of CFRN is vital for those aiming to utilize its full potential in their 3D printing endeavors."