Caustic Scrubber for Effective HCl Removal
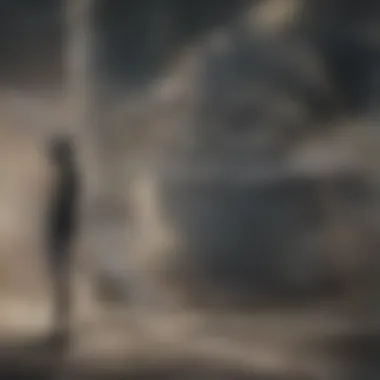
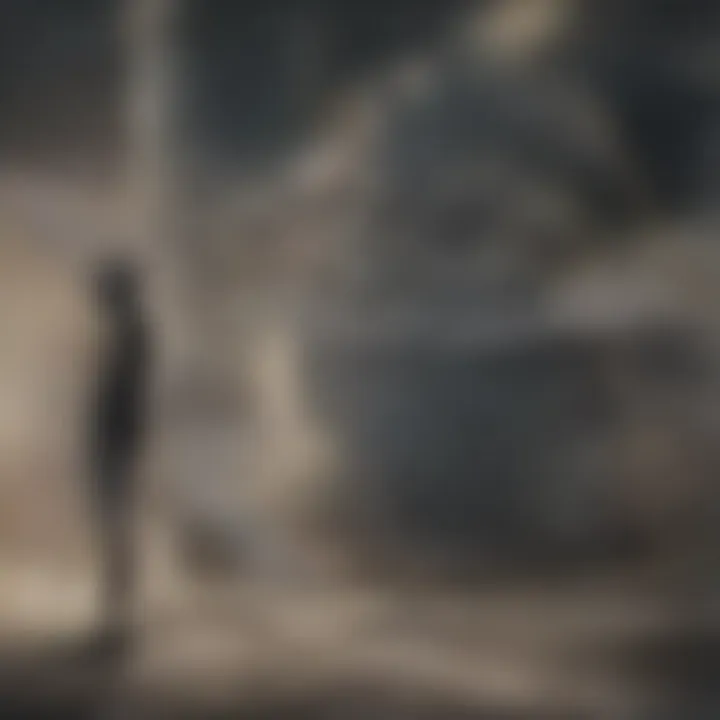
Intro
In the realm of industrial emissions, the management of hazardous substances is paramount. Hydrochloric acid (HCl) is one such substance requiring careful handling due to its corrosive nature and potential environmental impact. Industrial processes often generate HCl as a by-product, necessitating effective removal systems to ensure compliance with environmental regulations and protect both worker health and safety. One common solution for HCl removal is the use of caustic scrubbers. These systems leverage chemical reactions to neutralize HCl, transforming it into less harmful substances. Understanding the mechanics behind these scrubbers, their design intricacies, and operational challenges is vital for achieving both efficiency and regulatory compliance.
Research Context
Background and Rationale
The rising awareness of air quality issues has pushed industries to adopt advanced scrubbing technologies. With environmental regulations tightening, industries are often compelled to seek solutions not just for compliance, but also for sustainable practices that minimize environmental footprint. Caustic scrubbers offer a dual advantage. They effectively neutralize acidic gases like HCl while simultaneously providing a pathway for industries to embrace greener technologies.
Literature Review
Various studies explore the effectiveness of caustic solutions against HCl. Research reveals that materials such as sodium hydroxide or calcium hydroxide are commonly employed. These solutions undergo neutralization processes with HCl, forming harmless salts and water as by-products. Moreover, literature suggests that optimizing the concentration of caustic solutions can enhance scrubber efficiency. Key findings have emerged regarding:
- The impact of temperature on reaction rates.
- The need for precise pH monitoring during the scrubbing process.
- Various design configurations that can lead to improved gas contact time within scrubbers.
These findings illuminate both the challenges and potentials of caustic scrubbers in operational settings. Evaluating previous research offers a solid foundation for assessing current practices and informing future advancements in scrubber technology.
Methodology
Research Design
A systematic approach is essential in understanding the complexities of caustic scrubber operation. This research adopts an integrative design, combining both experimental data and case studies from various industrial plants employing caustic scrubbers. The primary goal is to derive insights that inform best practices for HCl removal.
Data Collection Methods
Data was gathered through multiple avenues:
- Field observations at industrial sites to assess current operational practices.
- Interviews with engineers and operators to gain qualitative insights into challenges faced in scrubbing processes.
- Reviewing emissions data provided in official environmental assessments, offering quantitative measures of scrubber performance.
By synthesizing data from these sources, the research aims to provide a comprehensive understanding of caustic scrubbers specific to HCl removal, thereby aiding in both academic and practical applications.
Prelims to Caustic Scrubbing
Caustic scrubbing is an essential technology used in various industrial applications to remove hydrochloric acid (HCl) from gas emissions. This process plays a crucial role in not only meeting regulatory requirements but also in protecting both the environment and human health. Understanding the mechanisms involved in caustic scrubbing is fundamental for professionals engaged in environmental management and compliance.
Definition and Purpose
Caustic scrubbing refers to the treatment of gas streams containing acidic compounds, primarily with the aim to capture and neutralize them. In this context, hydrochloric acid, which can manifest as a byproduct in several manufacturing processes, can have detrimental effects on air quality if not adequately managed. The purpose of caustic scrubbers is twofold: to eliminate HCl from emissions and to convert it into less harmful substances. Typically, alkaline solutions, such as sodium hydroxide, are employed for this task. They react with HCl, resulting in salt and water.
Scope of Application
The application of caustic scrubbers extends across numerous industries, including chemical production, petroleum refining, and metal processing. In these sectors, HCl is often generated as a result of various chemical reactions.
- Chemical Manufacturing: In this industry, significant quantities of HCl are produced and released if not controlled. The implementation of caustic scrubbers can minimize emissions, helping firms comply with environmental standards.
- Oil and Gas: During the refining and treatment of petroleum, HCl is utilized and can be released. Caustic scrubbers, therefore, are vital in capturing these emissions.
- Metal Processing: In processes like pickling where metals are cleaned, the resulting fumes can contain HCl. Here, scrubbers serve as a necessary countermeasure to protect both worker safety and the environment.
Overall, caustic scrubbing is an impactful strategy for reducing HCl emissions, rendering it a critical component in the effort towards cleaner industrial practices.
Chemical Properties of Hydrochloric Acid
Hydrochloric acid (HCl) is one of the most widely used strong acids in various industrial applications. Understanding its chemical properties is essential for improving the design and efficiency of caustic scrubbers intended for HCl removal. Within the context of this article, the focus on the molecular characteristics and the reactivity of HCl plays a crucial role in the overall effectiveness of scrubbing technologies.
Molecular Characteristics
HCl is a diatomic molecule, composed of hydrogen and chlorine. Its molecular formula is HCl, and it exists as a colorless gas at room temperature. When dissolved in water, it forms a strong acid solution. The ionization of HCl in water produces hydrogen ions (H⁺) and chloride ions (Cl⁻), contributing to its high acidity. This property is significant because it directly affects how HCl interacts with caustic solutions in scrubbers.
The molecular weight of HCl is approximately 36.46 g/mol. The bond between hydrogen and chlorine is polar covalent, leading to a partial positive charge on the hydrogen atom and a partial negative charge on the chlorine atom. This polarity enhances the molecule's reactivity, especially when mixed with alkaline substances such as sodium hydroxide or calcium hydroxide during scrubbing operations.
Reactivity and Implications in Industrial Processes
Hydrochloric acid is highly reactive. This is crucial when considering its implications in industrial processes. When HCl is released into the atmosphere, it can contribute to environmental pollution and pose health risks. The reactivity of HCl allows it to readily combine with various materials, including metals, and can lead to corrosion and material degradation in industrial operations.
In scrubber systems, the reactivity of HCl with caustic solutions is an advantageous factor. Effective scrubbing involves the neutralization of HCl, converting it into harmless substances through chemical reactions. For example, when sodium hydroxide is used, the neutralization reaction can be summarized as:
HCl (aq) + NaOH (aq) → NaCl (aq) + H₂O (l)
This reaction illustrates the conversion of hydrochloric acid into sodium chloride (table salt) and water, emphasizing the importance of selecting appropriate caustic materials to maximize scrubbing efficiency.
The implications of HCl's reactivity are not limited to the scrubbing process itself but extend to safety and maintenance. The potential for HCl to corrode equipment necessitates careful material selection and maintenance protocols to ensure the longevity and effectiveness of scrubbers. Understanding these chemical properties provides a foundational knowledge base for engineers, operators, and researchers involved in the design and operation of caustic scrubbers.
A thorough understanding of hydrochloric acid's characteristics ensures better design and operational efficiency in industrial scrubbers, ultimately safeguarding environmental integrity and public health.
Mechanism of Caustic Scrubbing
Understanding the mechanism of caustic scrubbing is crucial in appreciating how effectively hydrochloric acid (HCl) can be removed from industrial emissions. This process relies heavily on the interactions between caustic solutions and HCl, which leads to significant reductions in harmful emissions. The efficiency of this process can directly impact both regulatory compliance and environmental health. Therefore, a thorough understanding of this mechanism is beneficial for engineers and environmental scientists alike.
Interaction Between Caustic Solutions and HCl
When caustic solutions, such as sodium hydroxide, calcium hydroxide, or potassium hydroxide, come into contact with HCl, a neutralization reaction occurs. This reaction is exothermic, which means it releases heat. Specifically, the hydroxide ions (OH⁻) from the caustic solution interact with the hydrogen ions (H⁺) present in hydrochloric acid.
The resulting products from this interaction are water (H₂O) and a corresponding salt, which in the case of sodium hydroxide, produces sodium chloride (NaCl). Here is a simple representation of the reaction:
HCl + NaOH → NaCl + H₂O
This reaction not only reduces the concentration of HCl in the gas stream but also leads to the formation of less harmful byproducts that can be more easily managed or treated. The effectiveness of this interaction will depend on several factors:
- Concentration of the Caustic Solution: Higher concentrations can lead to more effective scrubbing, but cost must be considered.
- Temperature: As temperature increases, reaction rates can also increase, potentially enhancing efficiency.
- Contact Time: Sufficient time must be allowed for the caustic solution to fully interact with HCl.
Careful monitoring of these variables is essential to maximize the efficacy of the caustic scrubbers.
Subsequent Reaction Products
Post-reaction, the products formed during the interaction of caustic solutions and hydrochloric acid have various implications for scrubber operation and waste management.
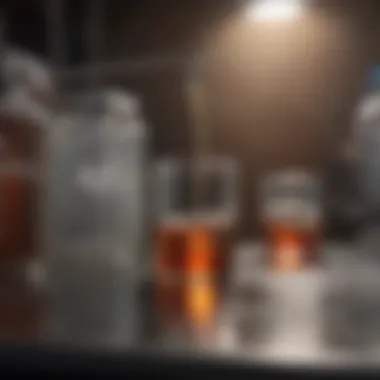
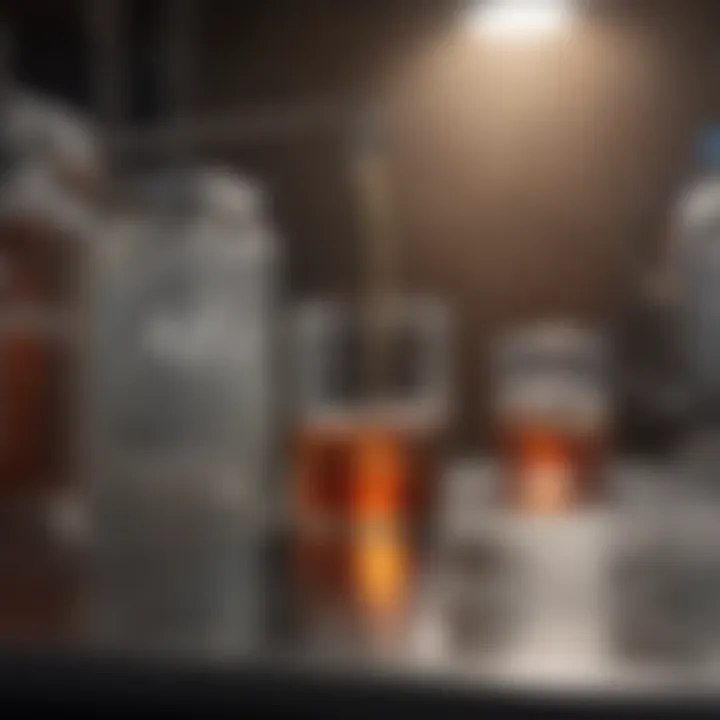
The main products are water and salts, which can seem harmless compared to HCl. However, their presence and concentration must be carefully monitored.
- Sodium Chloride (NaCl) - This is a common byproduct when sodium hydroxide is used. While harmless in small quantities, accumulation can lead to operational issues in the scrubber system.
- Calcium Chloride (CaCl₂) - If calcium hydroxide is applied, the resultant calcium chloride can be produced. This compound can be hygroscopic, absorbing moisture from the environment, which may complicate disposal.
- Potassium Chloride (KCl) - In the case of potassium hydroxide usage, potassium chloride is formed, and like sodium chloride, it needs attention regarding its safe disposal.
The handling of these byproducts dictates the subsequent processes needed for waste management. Consequently, incorporating efficient treatment systems for byproducts into scrubber design can enhance overall effectiveness.
Design Considerations for Caustic Scrubbers
Designing an effective caustic scrubber for hydrochloric acid (HCl) removal involves multiple considerations that dictate its success and sustainability in operations. Various factors influence the scrubber's efficiency, reliability, and compliance with environmental regulations. This section outlines the critical design elements, benefits, and considerations involved in constructing effective scrubber systems.
Physical Layout and Flow Dynamics
The physical layout of a caustic scrubber significantly determines its operational efficiency. The enclosed structure must allow for optimal interaction between the caustic solution and the HCl gas. Proper airflow design is crucial; it ensures that the gas to liquid ratio facilitates maximal absorption and minimizes residual emissions.
Key factors to consider in layout include:
- Gas Flow Direction: The method of gas introduction, whether horizontal or vertical, impacts the residence time of the gas within the scrubber.
- Liquid Distribution: Uniform distribution of the caustic solution enhances contact area and ensures effective reactions.
- Height of Scrubber: A taller scrubber can increase contact time, but it must fit within site space constraints.
Balancing these elements creates an efficient flow dynamic, reducing the chance of dead zones where gas can escape unreacted. Accurate modeling tools can provide predictive insights into flow patterns, significantly influencing design choices.
Selection of Materials
Material selection is another paramount design consideration for caustic scrubbers. The caustic solution’s corrosive nature demands materials that can withstand harsh environments.
Common materials include:
- Stainless Steel: Highly resistant to corrosion and suitable for numerous chemical reactions involving caustics.
- FRP (Fiberglass Reinforced Plastic): Effective in minimizing corrosion at lower costs while offering adequate strength.
- Polypropylene: A viable option for less aggressive environments, providing chemical resistance at a lower cost.
Beyond material corrosion resistance, the chosen materials should also have appropriate mechanical strength and thermal stability. They should be capable of handling pressure variations without compromising safety or performance.
In selecting materials, it's essential to evaluate long-term performance and potential degradation.
Moreover, implementing coatings or linings may enhance resistance and extend the lifespan of the scrubber. Regular assessments help ensure the materials selected continue to operate efficiently without significant wear or failure.
Types of Caustic Solutions
The choice of caustic solution is a critical component in the operation of caustic scrubbers for HCl removal. The right caustic agent influences the efficiency of the scrubbing process and the overall effectiveness of emission control. Each type of caustic solution has its properties, benefits, and considerations that must be carefully evaluated. Understanding these different caustic solutions helps in optimizing scrubber operations and ensuring compliance with environmental regulations.
Sodium Hydroxide
Sodium hydroxide, commonly known as caustic soda, is one of the most prevalent caustic agents used in scrubbing systems. It is highly effective in neutralizing hydrochloric acid, which is essential for reducing HCl emissions. Sodium hydroxide reacts with HCl to produce sodium chloride and water, facilitating a straightforward removal process.
- Availability: This compound is widely available and produced on a large scale, making it a cost-effective option for many industries.
- Effectiveness: It offers high reaction rates, allowing for efficient scrubbing even at lower concentrations.
- Considerations: Handling sodium hydroxide requires careful attention, as it is highly corrosive and can pose safety risks.
Calcium Hydroxide
Calcium hydroxide, also termed as slaked lime, is another viable caustic option for scrubbing applications. It is often used in scenarios where large volumes of alkaline material can be advantageous, especially in facilities with significant exhaust gas volumes.
- Chemical Reaction: The reaction between calcium hydroxide and hydrochloric acid results in the formation of calcium chloride and water, reducing acidity effectively.
- Environmental Benefits: Calcium hydroxide is less corrosive compared to sodium hydroxide, reducing the risks of corrosion to scrubber components and associated infrastructure.
- Limitation: The solubility of calcium hydroxide in water is limited compared to sodium hydroxide, which may necessitate larger amounts to achieve desired scrubbing effectiveness.
Potassium Hydroxide
Potassium hydroxide, known as caustic potash, represents a more specialized option among caustic solutions for HCl removal. It shares similar properties with sodium hydroxide while offering some unique characteristics.
- Efficiency: Like sodium hydroxide, it reacts exothermically with hydrochloric acid, yielding potassium chloride and water in a rapid reaction.
- Uses: Due to its higher cost and specific applications, its use is often limited to situations where premium performance is required, or specific regulatory standards must be met.
- Considerations: Operators must weigh the cost against its benefits when deciding on potassium hydroxide over other caustics, particularly in scalable operations.
Understanding the properties and reactions of these caustic solutions is essential for correctly implementing scrubbing technologies. It enables industries to make informed decisions that enhance both efficiency and safety in their operations.
Performance Metrics in Scrubber Operations
The performance metrics in scrubber operations are crucial for assessing the efficiency and effectiveness of caustic scrubbers in removing hydrochloric acid from industrial emissions. Understanding these metrics allows industries to optimize their operations, ensuring compliance with environmental regulations while maintaining cost-effectiveness. Several key aspects contribute to this evaluation, including efficiency ratings and comparative analyses between different systems.
Efficiency Ratings
Efficiency ratings measure how well a caustic scrubber operates in reducing HCl concentrations in flue gases. A higher efficiency rating typically indicates that a system is effectively neutralizing acid gases before they are released into the atmosphere. Evaluating the performance often involves the following components:
- Removal Efficiency: This is the percentage of HCl removed from the gas stream, providing insight into scrubber performance.
- Loading Rates: Measurement of HCl concentrations at the inlet versus the outlet helps in determining how much acid gas is treated per unit time.
- Liquid-to-Gas Ratio: This ratio needs careful adjustment; a low liquid flow may not achieve sufficient scrubbing, while high flow can lead to operational issues such as flooding.
These metrics help identify the operational limits of a scrubber, allowing adjustments to be made for optimal performance over time.
Comparative Analysis of Different Systems
Engaging in a comparative analysis of various scrubber systems can also yield significant insights. Different caustic scrubbers employ various technologies, including packed towers, spray towers, or venturi scrubbers. Each system has its own advantages and limitations regarding hydrogen chloride removal. Considerations in this analysis may include:
- System Design: Different designs affect how effectively gases interact with caustic solutions. For example, packed towers may improve contact time and efficiency compared to simpler designs.
- Cost-Effectiveness: Though some systems might demonstrate higher removal efficiencies, they may also entail increased operational and maintenance costs.
- Adaptability to Varied Conditions: Some systems may perform better under specific conditions, such as varying inlet concentrations or flow rates.
The outcomes of these comparisons not only offer guidance for industries in selecting the appropriate scrubber technology but also help in pinpointing operational best practices that align with environmental compliance demands.
"Achieving optimal performance in caustic scrubbers is key not only for regulatory compliance but also for sustainable industrial practices."
Regulatory Considerations in HCl Scrubbing
Regulatory considerations in hydrochloric acid (HCl) scrubbing play a vital role in ensuring safety and environmental protection. These regulations are established by various regulatory agencies at both local and national levels. They dictate how scrubbers should be designed, operated, and maintained. Compliance with these regulations is essential for manufacturers, as they impact operational practices and material choices. Adhering to local and national standards helps minimize emissions of harmful substances into the environment, thereby reducing potential health hazards for workers and surrounding communities. Moreover, understanding these regulations informs the overall design and efficiency of caustic scrubbers, ensuring that they meet necessary performance measures.
Local and National Standards
Local and national standards provide a framework for the regulation of HCl emissions from scrubber systems. These standards can vary significantly based on jurisdiction and the specific industrial processes involved.
Some important elements of these standards include:
- Maximum Allowable Emission Levels: These are limits set for the amount of HCl that can be released into the atmosphere.
- Performance Testing Requirements: Often, facilities must conduct regular tests to show compliance with emissions limits.
- Record-Keeping: Many regulations require detailed documentation of emissions and operational data to ensure accountability.
These standards not only promote environmental protection but also enhance the operational effectiveness of scrubbers. Facilities that strictly adhere to these regulations are better positioned to maintain their operational licenses and avoid hefty penalties.
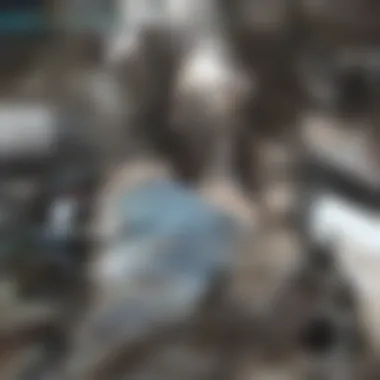
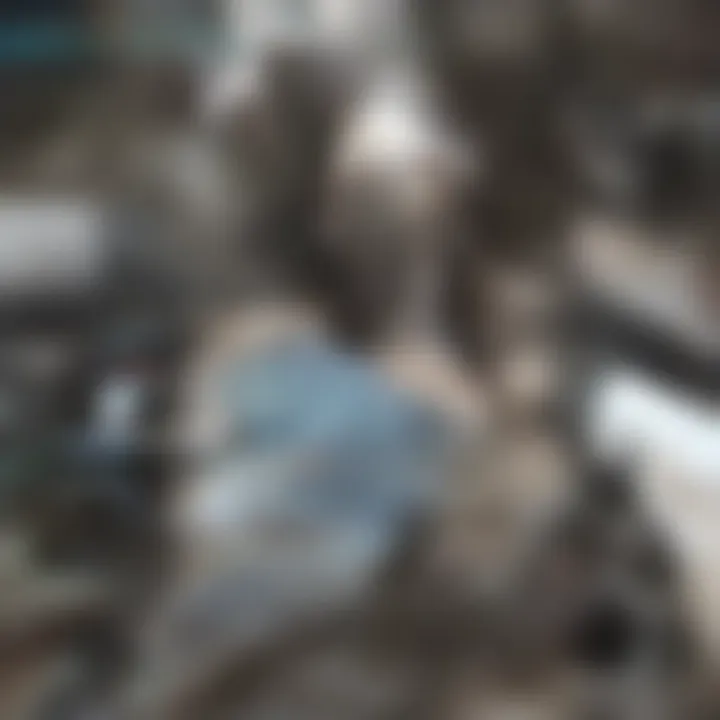
Impact of Regulations on Scrubber Design
Regulatory requirements have a substantial effect on the design of caustic scrubbers. Facilities must plan their scrubber systems in a way that meets stringent criteria specified by authorities. Key impacts include:
- Materials Selection: Regulations influence the choice of materials used to construct scrubbers to prevent corrosion and degradation. This is crucial, as some materials may not withstand the highly caustic nature of scrubbers.
- Design Complexity: Regulatory compliance often leads to the adoption of more complex designs that integrate advanced features, such as multiple stages of scrubbing or enhanced monitoring systems.
- Operational Flexibility: Design flexibility can become necessary to allow operators to adjust their processes in response to regulatory changes.
Ensuring compliance with these regulations aids in optimizing scrubber system efficiency. It guarantees that operations not only meet legal requirements but also contribute to broader environmental goals.
"Effective regulatory compliance can lead to both economic and environmental benefits for industries engaged in HCl operations."
In summary, staying informed and compliant with local and national standards in HCl scrubbing is not merely a legal obligation but a pathway to sustainability and operational excellence.
Challenges in Caustic Scrubbing Operations
Caustic scrubbing is crucial in the context of industrial applications focused on removing hydrochloric acid (HCl) from emissions. However, operations often face significant challenges that affect the efficiency and longevity of the scrubbing systems. Understanding these challenges is essential for optimizing the use of caustic scrubbers and ensuring compliance with environmental regulations.
Corrosion and Material Degradation
Corrosion is a primary concern in caustic scrubbing operations. The chemical reactions between hydrochloric acid and caustic solutions, particularly sodium hydroxide, can lead to the degradation of materials used in scrubber construction. Common materials like carbon steel and stainless steel may not withstand the harsh environment, resulting in structural weaknesses over time.
The impact of this degradation is twofold: operational interruptions and higher costs. Corrosion can necessitate unplanned maintenance, leading to downtime which affects productivity. Therefore, when selecting materials for construction, it is important to choose corrosion-resistant alloys and coatings. Examples include the use of nickel alloys or specialty coatings that mitigate corrosive effects.
Operational Limitations and Downtime
Operational limitations often arise from various factors. For instance, the temperature and concentration of the scrubbing solutions can affect the overall efficiency of the process. If either parameter exceeds suitable ranges, it can lead to decreased scrubbing performance and potential system failures. Furthermore, the inherent complexity of scrubbing systems may result in situations where routines need to be halted for technical adjustments or repairs.
Downtime not only incurs costs but may also disrupt production schedules, causing delays in meeting market demands. To mitigate these effects, operators must establish a regular maintenance program, conduct performance assessments, and implement proper training protocols for personnel.
"Identifying and addressing issues related to corrosion and operational downtime leads to enhanced performance of caustic scrubbers."
Maintenance Protocols for Caustic Scrubbers
Maintaining the efficiency of caustic scrubbers is critical for various industrial processes that manage hydrochloric acid. Proper maintenance protocols safeguard the functionality of these systems while ensuring compliance with environmental regulations. Without diligent upkeep, performance may decline, leading to increased emissions and potential fines. This section explores essential maintenance practices, focusing on regular inspections and the replacement of crucial components.
Regular Inspection Guidelines
Regular inspections are at the heart of effective scrubber maintenance. These inspections allow for the early detection of potential issues that could affect system performance. Operators should implement a scheduled inspection regime that includes:
- Visual Checks: Look for signs of leaks, corrosion, or wear on scrubber components. Regular visual assessments help in identifying obvious problems that may escalate if neglected.
- Operational Audit: Review operational data against expected performance metrics. Inconsistencies may indicate underlying issues requiring further investigation.
- Fluid Analysis: Analyze the caustic solution for concentration levels and contaminants. Maintaining optimal chemical balance ensures the scrubber operates effectively.
Implementing a checklist during inspections can enhance thoroughness. Here’s a sample checklist for operators:
- Inspect caustic solution levels.
- Verify pump functioning and pipeline integrity.
- Check pH levels and adjust if necessary.
- Assess filter conditions and replace if clogged.
- Document findings and schedule follow-up actions.
By adhering to these guidelines, facilities can preemptively address maintenance needs. This minimizes downtime and maintains operational efficiency.
Replacement of Components
Eventually, components will degrade due to continuous exposure to caustic substances and operational stress. Identifying when to replace parts is as crucial as the inspections themselves. Effective component management can lead to substantial performance improvements. Key points concerning component replacement include:
- Timing of Replacement: Operators should closely monitor the age and condition of critical components, such as pumps, fans, and scrubber media. Each part has a lifespan that may be dictated by time or operational wear.
- Standard Operating Procedures: Establish clear procedures for replacing components, detailing steps to ensure safety and efficiency. Involving the right personnel in these processes is vital.
- Supplier Coordination: Collaborate with manufacturers for replacement parts to ensure quality and compatibility. Some components may need custom fabrication, and maintaining a good relationship with suppliers can expedite this process.
Properly scheduling replacements as part of a holistic maintenance plan can reduce operational disruptions. The strategy extends the life of the scrubber and boosts its overall efficiency.
Maintaining caustic scrubbers is not merely about compliance; it enhances operational integrity while minimizing negative environmental impacts. As the industry advances, keeping up with maintenance protocols can lead to innovations in efficiency and sustainability.
Environmental Impact of Scrubbing Technologies
The environmental implications of scrubbing technologies are critical to understand as industries increasingly face scrutiny regarding their emissions. The installation and operation of caustic scrubbers for hydrochloric acid (HCl) removal are not just technical challenges; they also carry great responsibilities towards ecological sustainability. By effectively neutralizing harmful emissions, these systems play a vital role in mitigating air pollution. This section delves into two key aspects of the environmental impact of scrubbing technologies: the evaluation of emission reductions and the long-term environmental compliance.
Evaluation of Emission Reductions
Assessing the efficiency of caustic scrubbers in reducing HCl emissions is essential for both regulatory compliance and environmental stewardship. Various studies indicate that deploying these technologies can lead to significant reductions in HCl concentrations in industrial exhaust streams. The effectiveness of scrubbers varies based on design specifications, caustic solution choice, and operational parameters.
Key metrics that are often considered include:
- Capture efficiency: This measures the percentage of HCl removed from the gas stream. A well-designed scrubber may achieve capture efficiencies exceeding 99%.
- Emission levels: Comparison of HCl concentrations pre and post-processing reveals the tangible reductions achieved through scrubbing technologies.
Additionally, continuous monitoring devices ensure compliance with emission standards established by local and national regulations. This not only contributes to cleaner air but also supports industries in mitigating their environmental footprint.
"Effective evaluation of emission reduction claims helps in maintaining transparency and accountability among industries, ensuring that environmental standards are met consistently."
Long-term Environmental Compliance
Long-term compliance with environmental regulations is a significant concern for industries operating caustic scrubbers. Authorities regularly update guidelines, which compel industries to adapt swiftly to new requirements. Scrubber systems must not only demonstrate efficacy in emission reduction today but also be adaptable for future compliance.
This obligation encompasses various aspects, including:
- Material Durability: As caustic solutions interact with both HCl and other compounds, scrubbers must be made from materials that resist corrosion and degradation over time, ensuring sustained efficiency.
- Operational Training: Proper training for operators fosters awareness regarding the importance of maintaining emission reductions and adhering to compliance standards.
- Maintenance Strategies: Regular assessment and maintenance protocols prolong the lifespan of scrubbers and allow for optimal performance.
Investing in robust monitoring systems and employee training programs not only facilitate meeting current regulations but also prepare industries for future challenges. Firms that prioritize environmental compliance are likely to enhance their reputation and operational longevity within the market.
Future Directions in HCl Removal Technologies
The topic of future directions in HCl removal technologies holds profound relevance in the context of environmental protection and industrial efficiency. As industries face increasingly stringent regulations regarding emissions, caustic scrubbers are critical for ensuring compliance. Innovations in this area could lead to significant advancements in performance, reducing the environmental footprint of hydrochloric acid emissions while maintaining cost-effectiveness.
Modern challenges in emission control necessitate a multi-faceted approach. Stakeholders must consider not only the efficiency of scrubbers but also their adaptability to emerging regulatory standards. As technology evolves, new methodologies may emerge that facilitate the efficient capture of HCl, thus fostering more sustainable practices in industries that generate this pollutant.
Innovations in Scrubber Design
Innovations in scrubber design are central to enhancing the efficiency and effectiveness of HCl removal processes. As research progresses, several key advancements have emerged:
- Modular Designs: These allow for flexibility and easier scaling. Industries can modify scrubber configurations to meet changing production needs without significant overhauls.
- Advanced Materials: Utilization of corrosion-resistant and high-temperature materials reduces maintenance downtime while extending the lifespan of the scrubber.
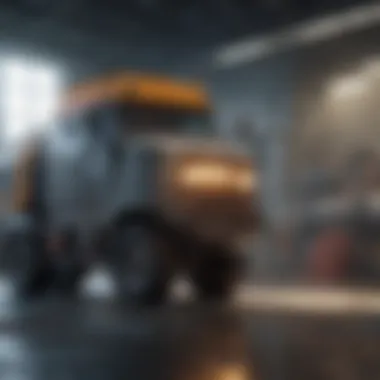
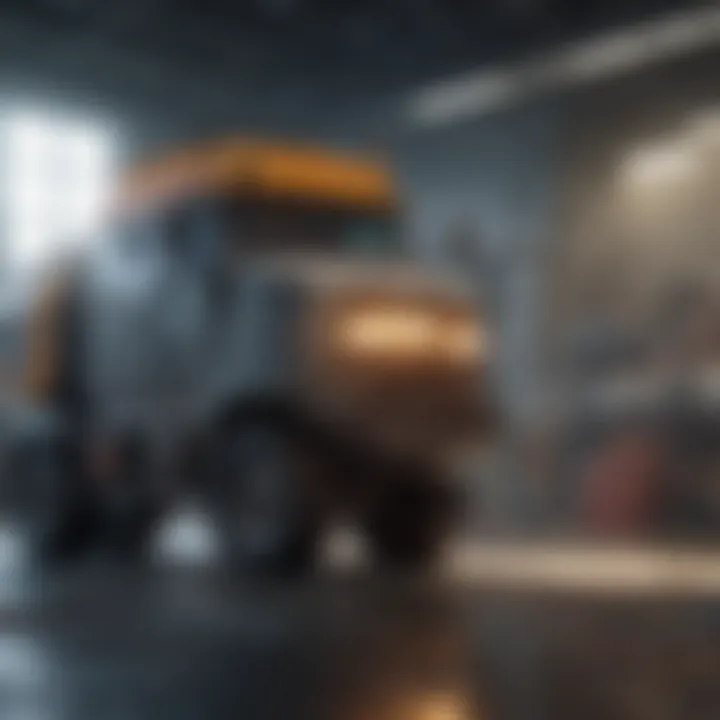
Innovations will also likely incorporate smart technology. Digital monitoring systems can optimize performance by adjusting operational parameters in real-time based on emission levels. This responsiveness reduces waste and increases the reliability of compliance with regulations.
As an industry, we must stay ahead by embracing technological advances in caustic scrubber design to mitigate environmental impacts efficiently.
Emerging Caustic Alternatives
The exploration of emerging caustic alternatives is essential for future HCl removal efforts. Various compounds are being assessed for their ability to effectively neutralize hydrochloric acid with reduced environmental impacts:
- Ammonium Hydroxide: This compound shows promise due to its ability to form less hazardous by-products.
- Organic Bases: Certain organic bases may be more effective at lower concentrations, offering cost benefits over traditional sodium hydroxide.
The focus on alternative caustics is driven by several considerations, including eco-friendliness and cost efficiency. Adopting alternatives could not only help in HCl removal but also lessen the overall environmental burden associated with traditional caustic solutions.
Case Studies of Successful Caustic Scrubber Implementations
Examining case studies of caustic scrubber implementations provides valuable insights into practical applications and lessons learned from real-world scenarios. These case studies not only showcase the effectiveness of caustic scrubbing systems for controlling hydrochloric acid emissions but also help to identify best practices and potential pitfalls in industrial settings. As industries increasingly face stringent regulations regarding emissions and waste management, successful case studies serve as important benchmarks for future projects.
Industrial Applications
Understanding various industrial applications of caustic scrubbers illustrates their versatility and effectiveness. Many sectors use these systems to mitigate the release of HCl and enhance environmental compliance.
- Chemical Manufacturing: In facilities where hydrochloric acid is produced, caustic scrubbers are essential. They treat emissions from reactors, helping to neutralize HCl before it enters the atmosphere.
- Metal Processing: Operations such as galvanizing and acid pickling often generate HCl gases. Implementing caustic scrubbers in these processes not only reduces emissions but also recycles the caustic solutions used, thus promoting sustainability.
- Waste Incineration: Facilities that incinerate hazardous waste may produce harmful HCl gases. Utilizing scrubbers ensures that these emissions are significantly reduced, minimizing the environmental impact.
These applications demonstrate how caustic scrubbers can efficiently handle HCl emissions across various industries, leading to improved air quality and regulatory compliance.
Lessons Learned from Failures
Analyzing failures provides equally important lessons that contribute to advancing the technology and design of caustic scrubbers. Some common issues encountered in previous implementations include:
- Inadequate Material Selection: Scrubbers made from materials that couldn’t withstand the corrosive nature of caustic solutions led to extensive maintenance costs and operational downtime.
- Poor System Design: Cases where scrubbers lacked proper airflow dynamics resulted in ineffective scrubbing. Optimizing the design and layout of scrubbers is crucial to ensure maximum efficiency.
- Neglecting Maintenance Protocols: Failing to implement regular maintenance often resulted in failures. Systems that experienced corrosion or blockage needed immediate attention to avoid catastrophic results.
These lessons underscore the importance of thorough planning, material selection, and regular maintenance in the design and operation of caustic scrubbers. Learning from the experiences of others is vital for increasing the reliability and effectiveness of HCl removal technologies.
"Real-world examples not only validate theoretical approaches but also highlight areas needing improvement in future designs."
Economic Considerations of Caustic Scrubbing
Economic considerations play a crucial role in the implementation and operation of caustic scrubbers designed for hydrochloric acid (HCl) removal. In the current industrial landscape, where regulatory pressures and environmental concerns are rising, understanding the cost dynamics associated with scrubbing technologies is essential. Various factors influence both the initial and ongoing expenses of scrubbers, including design complexity, material choices, and maintenance needs.
The importance of this topic cannot be overstated. A comprehensive economic analysis helps stakeholders make informed decisions that align with budget constraints while ensuring compliance with environmental regulations. Proper investment in caustic scrubbing can lead to enhanced operational efficiency and long-term financial viability for businesses.
Cost Analysis of Installation and Operation
The cost analysis of installation and operation of caustic scrubbers encompasses several elements:
- Initial Capital Outlay: This includes expenses for purchasing scrubber units, auxiliary equipment, and installation services. Factors such as scale of operation and complexities in integration with existing systems can significantly impact the total cost.
- Operating Costs: These costs involve the energy utilized by scrubbers, the procurement of caustic solutions, and routine labor for operation. Energy consumption will often vary based on the design and efficiency of the system.
- Maintenance Expenses: Regular maintenance is crucial for optimal performance, which includes both scheduled and unscheduled repairs. The choice of materials and technology can affect the frequency and cost of maintenance activities.
An accurate cost analysis provides insights for budgeting and assessing the financial feasibility of adopting caustic scrubbing technology. It is essential to conduct a detailed review that includes all potential costs to avoid unexpected expenditures post-implementation.
Return on Investment
Evaluating the return on investment (ROI) for caustic scrubbing systems is vital for justifying the capital expenditure and operational decisions made by businesses. Key factors influencing ROI include:
- Reduction in Environmental Fines: Efficient operation of caustic scrubbers can lead to significant reductions in emissions. This compliance can prevent costly fines and improve corporate reputation.
- Productivity Gains: Enhanced air quality translates to a better working environment, potentially increasing workforce productivity and reducing health-related absences.
- Long-term Cost Savings: Investing in high-quality scrubbing technology can result in longer equipment life and reduced maintenance costs, leading to savings over the operational lifespan of the equipment.
Strong ROI analysis helps organizations not only to justify costs but also to evaluate future investments in environmental technologies efficiently.
Training and Competency in Scrubber Operations
Training and competency in scrubber operations are crucial for ensuring the effective and safe removal of hydrochloric acid (HCl) from industrial emissions. Well-trained personnel contribute to the operational efficiency, safety, and reliability of caustic scrubbers. The complexities of these systems require operators to have a solid understanding of the equipment, chemical interactions, and emergency protocols.
Trained operators can optimize the performance of scrubbers, leading to improved removal rates of HCl. They are also equipped to identify and troubleshoot problems that may arise during operation. Moreover, skilled workers reduce the risk of accidents or failures that could harm employees or the environment.
Regular training sessions should include hands-on practice with equipment, understanding of chemical properties, and maintenance protocols. This ensures that operators are competent in handling various situations and can adapt to changes in operational conditions. Ensuring a high level of competency within the workforce results in more efficient scrubber operations and minimizes operational downtime.
Effective training enhances the ability to manage scrubbers, maximizing efficiency while ensuring safety.
Essential Skills for Operators
Operators need a range of essential skills to manage caustic scrubbers successfully. Key competencies include:
- Technical Knowledge: Understanding the chemical processes involved in scrubbing HCl is fundamental. This includes knowledge of the reactions between caustic solutions and HCl.
- Equipment Proficiency: Familiarity with the specific scrubber systems used in their facility. Operators must know how to operate, monitor, and maintain scrubber components.
- Problem-Solving Abilities: The ability to quickly identify issues and implement solutions is vital. Operators often face unexpected changes in operational parameters that require immediate attention.
- Safety Awareness: Knowledge of safety procedures is essential. Operators must recognize potential hazards and understand emergency response strategies.
By fostering these essential skills, organizations can empower their workforce and enhance the overall efficiency of HCl removal processes.
Compliance with Safety Standards
Compliance with safety standards is a fundamental aspect of caustic scrubber operations. Adhering to regulatory guidelines ensures that operators work in a safe environment and that the scrubber systems function effectively. Safety standards cover a wide range of practices, including:
- Proper Handling of Caustic Solutions: Operators must be trained to handle caustic materials safely, minimizing risks of exposure and chemical accidents.
- Regular Safety Audits: Facilities should conduct regular audits to ensure compliance with local and national regulations. This helps identify areas for improvement.
- Emergency Preparedness: Operators must be trained in emergency response protocols specific to incidents involving caustic scrubbers and HCl emissions. This includes understanding procedures for spills, equipment failures, and other emergency situations.
- Documentation and Reporting: Maintaining accurate records of safety inspections, incidents, and training sessions is important for compliance and accountability.
By fulfilling these compliance requirements, organizations not only ensure the safety of their personnel but also protect the surrounding environment from potential harm.
Ending and Recommendations
The conclusion of an in-depth exploration of caustic scrubbers for hydrochloric acid (HCl) removal encapsulates critical insights gained from understanding their design, operation, and regulation. A holistic appreciation of caustic scrubbers contributes significantly to their effective implementation in various industrial settings. By synthesizing the knowledge shared throughout the article, we can appreciate how caustic scrubbers not only serve in emission control but also align with environmental regulations.
Summary of Key Insights
Throughout the article, several key points emerged:
- Chemical Interaction: The chemical processes involved in the interaction between caustic solutions, especially sodium hydroxide, calcium hydroxide, and potassium hydroxide, with hydrochloric acid are pivotal. Understanding these reactions ensures optimal design and operational efficiency.
- Performance Metrics: Efficiency ratings and comparative analysis highlight the importance of selecting the appropriate caustic solution and scrubber design. This directly affects the long-term operational success and compliance with environmental standards.
- Regulatory Framework: Awareness of local and national regulations guides the design and operational protocols, influencing choices made in the use of caustic scrubbers. Compliance not only enhances safety but also sustains environmental health.
- Maintenance and Challenges: Regular inspection and addressing challenges such as corrosion and operational limitations are mandatory for ensuring the longevity and reliability of caustic scrubbers.
Incorporating these insights into practice promotes better scrubber design and implementation.
Future Research Directions
The field of caustic scrubbing for HCl removal presents numerous avenues for further research. Potential areas include:
- Innovations in Material Science: Exploring new materials could lead to more resistant components and enhance scrubber lifespan.
- Alternative Caustic Solutions: Investigating low-cost and environmentally friendly alternatives to traditional caustic solutions can present significant benefits.
- Automation and Control Systems: Enhancing automation in scrubber operations could improve efficiency and reduce human error.
- Long-Term Environmental Impact Studies: Comprehensive studies on the long-term environmental impact of caustic scrubbing technologies can ensure continued compliance and adaptation to stricter regulations.
As technology continues to evolve, ensuring that the caustic scrubbing methods adaptation meets future environmental requirements stands crucial. Ensuring research investments align with industrial needs will not only benefit operational efficiency but also foster sustainable practices in HCl emission management.