Exploring the Chemical Composition of 316L Stainless Steel
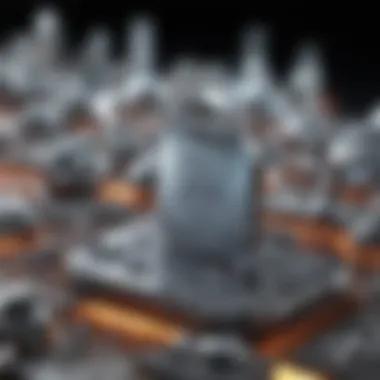
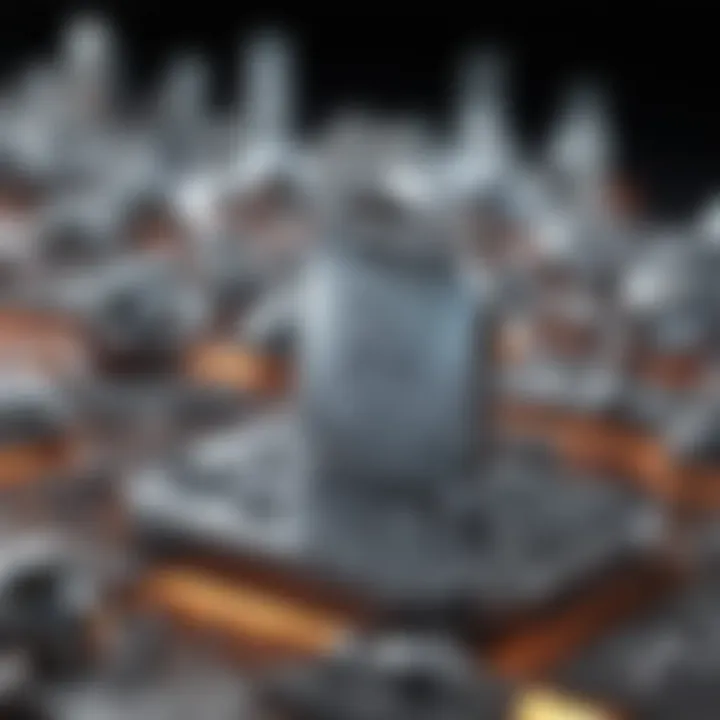
Intro
Revisiting the significance of 316L can provide valuable insights into material selection for specific applications. By grasping how the composition affects mechanical and chemical properties, professionals can make informed decisions that impact productivity and safety.
Research Context
Background and Rationale
The study of 316L stainless steel began in response to the need for materials that could withstand corrosive environments. Initially developed from 304 stainless steel, 316L has fewer carbon content and higher molybdenum levels. This modification is a deliberate choice to improve resistance to pitting corrosion, especially in chloride-rich settings. The rationale behind using 316L over other grades is clear. It not only maintains structural integrity but also ensures longevity in demanding applications.
Literature Review
Previous research reveals a comprehensive understanding of how each element in 316L contributes to its overall properties. For example,
- Nickel enhances ductility and toughness, improving the alloy's formability.
- Chromium plays a vital role in increasing oxidation resistance, particularly in high-temperature environments.
- Molybdenum significantly reduces the risk of pitting, especially in acidic surroundings.
Various studies compare 316 and 316L grades, revealing that the lower carbon content in 316L does not compromise strength; rather, it enhances suitability for many applications.
Methodology
Research Design
A series of experiments can yield significant data regarding the elemental composition of 316L. These investigations typically employ spectroscopy and mass spectrometry techniques for precise analysis. Understanding both the qualitative and quantitative aspects of the alloying elements is essential for drawing conclusions about performance standards.
Data Collection Methods
To gather relevant information, both qualitative and quantitative data collection methods can be implemented. Techniques might include:
- Analyzing metallurgical microstructures to determine phase distribution.
- Conducting corrosion tests in simulated environments that mimic real-world conditions.
- Reviewing current literature for advancements in alloy production.
By comprehensively examining these elements and methodologies, professionals can enhance their understanding of 316L stainless steel. This knowledge will be influential for both research and practical applications.
Prolusion to 316L Stainless Steel
Stainless steel is a group of iron-based alloys known for their corrosion resistance, strength, and versatility. Among the various grades, 316L stainless steel stands out due to its unique chemical composition and resulting properties. This introduction aims to highlight the significance of 316L in providing solutions across multiple industries, including healthcare, food processing, and marine applications. Understanding the fundamental attributes of 316L can clarify its role in advanced engineering and design.
Overview of Stainless Steel Alloys
Stainless steel alloys are categorized primarily by their microstructure. This classification includes austenitic, ferritic, martensitic, and duplex grades. 316L is a type of austenitic stainless steel, characterized by its high chromium and nickel content. The presence of these elements not only improves corrosion resistance but also enhances durability and mechanical properties.
In more technical terms, 316L contains a lower carbon content compared to other grades, ensuring increased weldability and reduced susceptibility to corrosion after welding. This specification makes it highly desirable in critical applications.
Austenitic steels like 316L exhibit non-magnetic properties, which is advantageous in environments where magnetic interference must be minimized. These features play a critical role in defining the alloy's performance and suitability for various environments, particularly those with harsh conditions where failure is not an option.
Importance of Chemical Composition
- Chromium: Enhances corrosion resistance.
- Nickel: Improves ductility and strength.
- Molybdenum: Increases resistance to pitting and crevice corrosion.
- Carbon: Limited presence allows for enhanced weld performance.
Furthermore, the careful balancing of these elements determines the versatility of 316L. Its composition allows this steel to withstand a wide range of temperatures and corrosive environments.
Fundamental Elements of 316L
Chromium Content
Role in Corrosion Resistance
Chromium is a key element in 316L stainless steel. It creates a passive layer that protects the metal from corrosion. This layer forms when chromium reacts with oxygen in the environment. As a result, the material becomes highly resistant to corrosion, especially in saline conditions.
The high chromium content significantly enhances the alloy's durability. For environments where corrosion is a concern, this attribute makes 316L an ideal option. It shows strong performance in various corrosive environments, making it a popular choice in the chemical processing and marine industries.
"Chromium is essential for the corrosion resistance of stainless steels."
Contribution to Mechanical Strength
In addition to corrosion resistance, chromium also plays a role in enhancing mechanical strength. It contributes to the overall hardness and tensile strength of the alloy. Hence, 316L remains stable under stress and heavy loads.
The stability imparted by chromium ensures that the material can withstand challenging conditions. However, it should be noted that excessive chromium can lead to brittleness, which may affect performance in specific scenarios.
Nickel Coordination
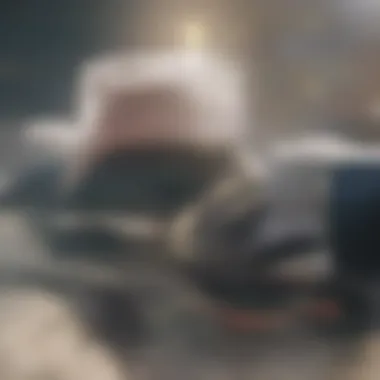
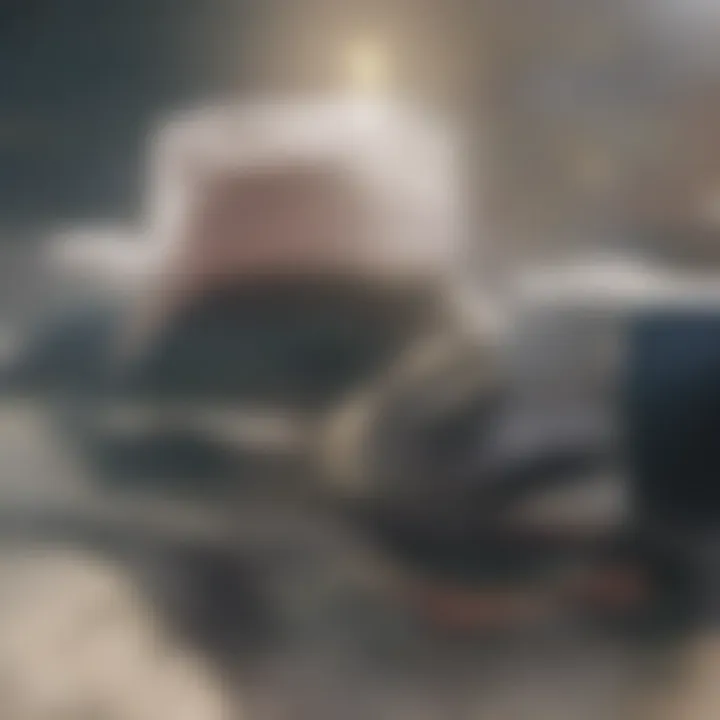
Impact on Strength and Ductility
Nickel is another fundamental element in 316L. It plays a vital role in improving both strength and ductility. The presence of nickel allows the stainless steel to deform without breaking, making it suitable for applications that require shaping and bending.
The ductility provided by nickel allows for ease in fabrication processes. This quality makes 316L popular in industries that demand versatile applications. However, an elevated nickel content may lead to increased costs, which is a consideration for manufacturers.
Effects on Aesthetic Appearance
Nickel also affects the aesthetic properties of 316L. It provides a shiny finish which is often desirable for architectural and decorative applications. The aesthetic appeal can enhance the visual quality of designing products.
However, while aesthetic aspects are essential, they can add to the cost of production. This factor needs weighing against practical benefits when deciding on material selection for specific projects.
Molybdenum Addition
Enhancement of Pitting Resistance
Molybdenum is added to 316L to improve its pitting resistance. This is particularly important in environments with chloride ions present, which can lead to localized corrosion. The unique feature of molybdenum is its ability to strengthen the passive layer formed by chromium.
Thus, the addition of molybdenum makes 316L a preferred choice for applications in marine environments or chemical processing where exposure to aggressive agents occurs. However, higher molybdenum levels may increase costs.
Influence on Heat Treatment
Furthermore, molybdenum influences heat treatment processes. It allows 316L to retain strength at elevated temperatures, which is crucial for specific industrial applications. The stable performance under heat ensures reliability, particularly in processes that involve temperature fluctuations.
Nonetheless, the heat treatment of 316L can be more complex due to molybdenum's effects, which may need careful considerations during processing.
Trace Elements in 316L
The inclusion of trace elements in 316L stainless steel plays a vital role in influencing its overall properties and performance. Understanding these elements is essential to comprehend how they interact within the alloy, contributing to various characteristics that make 316L suitable for a wide range of applications. Among the trace elements, carbon, silicon, and manganese stand out due to their distinct contributions to the metal's behavior in both fabrication and service environments.
Carbon Implications
Effects on Welding
Carbon's role in 316L is multifaceted, particularly when it comes to welding processes. While it is an alloying element, excessive carbon content can undermine the quality of welds. Higher levels may lead to carbide precipitation at the grain boundaries, making the material susceptible to intergranular corrosion. Maintaining an optimal carbon level is therefore crucial, as it helps in achieving the desired mechanical properties without sacrificing weld quality. The key characteristic here is the balanced approach towards carbon content, which supports the integrity of welded joints.
The beneficial choice for maintaining low carbon content is specifically designed to avoid these corrosion issues. This characteristic of carbon in welding is what makes 316L desirable in critical applications, as it allows for reliable performance in harsh conditions, such as those found in chemical processing and marine environments.
Limitations on Strength
While carbon can enhance hardness and strength, its limitations are equally significant in 316L. The main limitation is that too much carbon can affect the alloy's toughness, particularly at lower temperatures. This reduction in toughness can lead to brittleness, especially during non-destructive testing. Thus, although carbon can improve some aspects of strength, it is imperative to manage carbon levels effectively. This uniqueness also leads to a trade-off; for some applications where ductility and toughness are essential, lower carbon levels are preferred.
Silicon and Manganese Contributions
Influence on Casting Quality
Silicon plays a crucial role in improving the fluidity of molten metal during the casting process. By enhancing the alloy's casting quality, silicon allows for better filling of molds and reduces the likelihood of casting defects. This characteristic of silicon is particularly crucial in manufacturing processes, where high-quality finished products are necessary. As a beneficial aspect, the incorporation of silicon can lead to a smoother surface finish and improved dimensional accuracy in cast parts. However, the uniqueness of this feature means that balancing silicon with other elements is essential; too much might lead to oxidation issues or other casting anomalies.
Role in High-Temperature Applications
Manganese serves a critical function in high-temperature applications, as it acts as a deoxidizer and stabilizes the austenitic structure of stainless steel. This property is especially valuable in environments subjected to extreme heat, where maintaining structural integrity is necessary. The ability of manganese to enhance high-temperature service allows 316L to be utilized effectively in various industrial settings, including power generation and chemical environments. However, while manganese improves high-temperature characteristics, attention must be given during the alloying process to ensure that its levels remain optimal, preventing adverse effects on other mechanical properties.
Comparison with Other Stainless Steel Grades
Understanding the distinction between different grades of stainless steel is vital for materials engineering and manufacturing. The comparison not only informs about material performance but also provides insights into application suitability. Selecting the right alloy can greatly affect both the performance and longevity of components in various industries.
vs 316L
Composition Differences
The primary distinction between 316 and 316L grades resides in their chemical compositions, particularly in carbon content. 316 stainless steel typically contains up to 0.08% carbon, while 316L is limited to a maximum of 0.03% carbon. This lower carbon content in 316L plays a crucial role in its resistance to sensitization during welding. Welding elevates temperatures, which can lead to chromium carbide precipitation. Reduced carbon decreases this risk, making 316L suitable for areas where welding is necessary.
Moreover, the lower carbon content allows for improved properties in corrosive environments. While both grades offer excellent resistance to pitting and crevice corrosion, the enhanced corrosion resistance of 316L positions it as the favored option in environments with high salinity or chlorides, such as marine applications.
Applications and Performance
The applications of 316 and 316L differ considerably, mainly due to their respective compositions. 316 is often utilized in environments where conditions are severe but do not require post-weld treatments. It is suitable for applications like pressure vessels and tanks where mechanical strength is a priority.
In contrast, 316L is increasingly preferred for welded structures due to its superior corrosion resistance and strength post-welding. This makes it an excellent choice for surgical instruments in the medical field as well as components in corrosive environments such as chemical processing or marine contexts, where durability is non-negotiable.
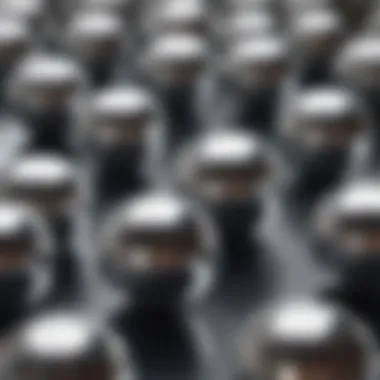
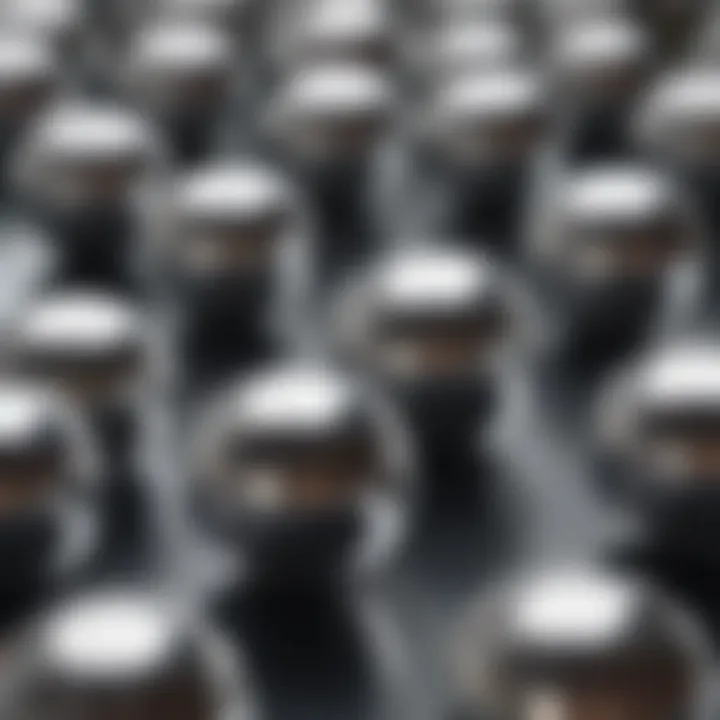
Common Substitutes
Comparative Analysis of and Grades
While 304 stainless steel is a popular choice due to its lower cost and decent corrosion resistance, 316 offers stark advancements, particularly regarding pitting resistance in chloride environments. The main difference in composition is the presence of molybdenum in 316, which significantly enhances its performance in harsh conditions.
The greater durability of 316 gives it advantages in applications like food processing, chemical, and pharmaceutical industries. By contrast, 304 may still be sufficient for food and water applications but lacks the resilience against aggressive environments where 316 and 316L excel.
Suitability in Different Environments
When assessing the suitability of these grades in various environments, 316 and 316L demonstrate exceptional versatility. 316 stands out in moderately corrosive atmospheres, while 316L excels in highly corrosive or salty conditions. This makes 316L an essential choice for sectors such as marine construction and offshore drilling, where exposure to seawater is a constant.
The selection is crucial, as a misstep can lead to early material failure and significant financial consequences. Being informed about the unique characteristics and performance metrics of these grades not only allows designers to achieve their desired outcomes but also optimize material life cycles across applications.
"Choosing the appropriate stainless steel grade can dramatically impact both structural integrity and operational longevity in demanding environments."
The insights detailed above highlight fundamental comparisons that guide professionals in their choices.
Processing and Fabrication of 316L
The processing and fabricating of 316L stainless steel are critical for ensuring its performance and longevity in various applications. This section focuses on the key elements that define the practical aspects of working with this alloy. Understanding the nuances of welding techniques and forming processes is essential for achieving optimal results in construction and manufacturing.
Welding Techniques
Recommended Practices
When welding 316L stainless steel, certain recommendations can help achieve the best results. Using low heat input, for example, is a recommended practice. This approach minimizes the risk of overheating and distortion, which can negatively impact the properties of the material. A specific method, such as TIG (Tungsten Inert Gas) welding, is popular due to its precision. TIG welding allows for better control over the heat and ensures a clean weld.
An important characteristic of TIG welding is its ability to produce high-quality welds with minimal contamination. This is because it uses a non-consumable tungsten electrode and an inert gas to protect the weld area from atmospheric exposure. However, this technique can be more time-consuming compared to others, requiring skilled labor. Overall, the recommended practices in welding for 316L aid in maintaining the structural integrity and corrosion resistance of the final product.
Challenges in Welding
Despite best practices, challenges can arise when welding 316L stainless steel. One significant aspect is the risk of sensitization. Sensitization occurs when the alloy is heated to the temperature range of 400 to 800 °C, leading to chromium carbide precipitation. This process can impair corrosion resistance. Another challenge includes warping due to differential cooling rates. These challenges necessitate careful consideration of joint design and welding procedures.
A key characteristic of these challenges is the need for proper pre-weld preparation and post-weld treatments. Techniques like solution annealing can help mitigate some risks. Knowing the unique features of these challenges provides professionals with insights that are essential for preventing issues during the welding process.
Forming Processes
Machining Considerations
Machining 316L stainless steel demands specific considerations due to its properties. The alloy’s toughness makes it harder to machine compared to other stainless steel grades. This factor can lead to increased wear on cutting tools, which necessitates the use of sharper tools and reduced feeding speeds. Use of high transverse rupture strength tools also ensures better outcomes.
An important characteristic is the need for coolants during machining. They help in reducing heat generation, which can otherwise affect the material's properties and finish. This attention to detail in machining ensures a high-quality product while extending the life of tooling equipment.
Impact of Composition on Workability
The chemical composition of 316L directly affects its workability. For instance, the presence of nickel and molybdenum in the alloy improves its ductility, allowing for easier shaping and forming. This characteristic is beneficial in applications that require intricate designs and shapes. However, additional alloying elements can also lead to lower strength in some scenarios.
Another feature is the presence of nitrogen in some variants of 316L, which further enhances hardness and strength. This adds complexity, as different compositions can result in variations in formability. Ultimately, understanding how composition influences workability is vital for professionals who aim to optimize their use of 316L stainless steel in end products.
"Attention to processing and fabrication can make or break the effectiveness of 316L stainless steel in critical applications."
In summary, the processing and fabrication considerations of 316L stainless steel encompass various aspects, including best practices for welding and the nuances of machining. The unique properties of the material require careful management to achieve high performance in various industrial applications.
Applications of 316L Stainless Steel
The relevance of 316L stainless steel lies significantly in its broad range of applications across various industries. Its complex chemical composition contributes not only to its durability but also to its remarkable ability to resist corrosion, making it a preferred material for critical uses.
In sectors like healthcare and marine engineering, 316L serves essential functions where performance is paramount. The stabilization of elements such as nickel and chromium, combined with low carbon content, provides superior resistance against pitting and crevice corrosion. Hence, understanding the applications of 316L stainless steel offers insight into its value and versatility.
Medical Applications
Use in Surgical Instruments
The use of 316L stainless steel in surgical instruments is pivotal due to its outstanding resistance to corrosion and mechanical wear. Surgical tools require a material that maintains integrity in sterilization processes, which 316L readily provides. The durability of these instruments under repeated sterilization cycles showcases a key characteristic of 316L.
Its low susceptibility to rust and discoloration makes it a beneficial choice, particularly in environments requiring stringent hygiene standards. One unique feature is the smooth surface finish achieved during fabrication, which helps in reducing bacterial adherence. The advantage here is clear: sterile conditions are upheld, reducing the risk of postoperative infections.
Biocompatibility Considerations
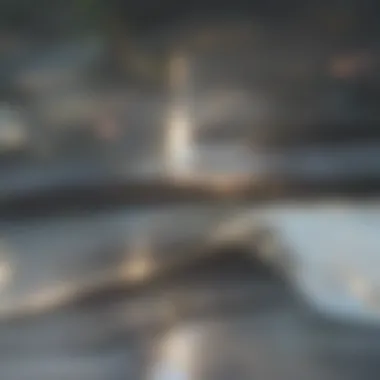
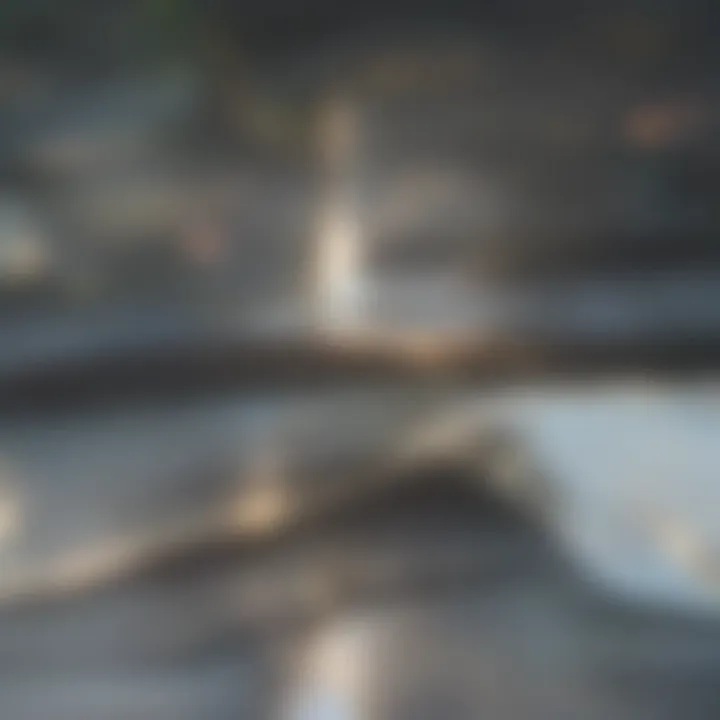
When discussing biocompatibility, 316L stainless steel stands out as a preferred material in medical applications. Its inherent properties diminish the likelihood of adverse reactions when implanted in the human body. This characteristic is crucial in devices such as stents or surgical implants.
The careful balance of alloying elements allows for high compatibility with biological tissues. However, the potential stress corrosion risks must be managed through proper alloying and fabrication methods. Thus, while the advantages of using 316L are compelling, careful consideration of processing techniques is necessary for ensuring long-term performance in medical applications.
Marine and Coastal Applications
Performance in Harsh Environments
316L stainless steel thrives in harsh marine environments due to its tailored chemical composition. The alloy effectively withstands extreme conditions such as high humidity and salty air, which would typically lead to rapid corrosion in other materials.
A notable characteristic of 316L is its ability to maintain strength and integrity despite being in constant exposure to the sea. This durability provides confidence for use in ship fittings, coastal constructions, and offshore platforms. Moreover, this performance extends the service lifespan of marine structures, reducing the need for frequent replacements or repairs.
Corrosion Resistance in Saltwater
The corrosion resistance of 316L stainless steel in saltwater is one of its defining advantages. This property is vital for components such as boat fittings, railings, and underwater structures. The presence of molybdenum within the alloy enhances its defense against localized corrosion, specifically pitting prevalent in saltwater conditions.
The unique feature of having increased nickel content along with specific chromium levels helps in providing a stable protective layer against corrosive environments. Consequently, while 316L is more expensive than some alternatives, the long-term savings from reduced corrosion-related maintenance justify its selection in marine applications.
In summary, the applications of 316L stainless steel underscore its importance in a variety of demanding environments, demonstrating that its chemical composition plays a critical role in performance and longevity.
Quality Control Measures
Quality control measures play a crucial role in the production and application of 316L stainless steel. Systematic assessments ensure that the material meets specific industry standards, which is essential for its performance in various environments. The importance of quality control extends beyond just adhering to specifications; it includes enhancing safety and reliability in practical applications. Ensuring that 316L stainless steel has the required chemical composition is pivotal for its resistance to corrosion and its overall mechanical properties.
Testing Chemical Composition
Analytical Techniques
A unique feature of analytical techniques is their ability to detect impurities at very low levels, which is important for understanding how these factors impact the overall material properties. However, there can be disadvantages, such as the need for specialized equipment and expertise.
Standards for ASTM Compliance
Standards for ASTM compliance establish crucial guidelines that 316L stainless steel must meet. These standards ensure quality consistency across batches and suppliers, making it a popular choice for various industries. The key characteristic of these standards lies in their rigorous nature, which includes defined limits on alloying elements and permissible impurities.
A unique feature of ASTM standards is their role in enhancing market trust and regulatory compliance. Adherence to these standards often leads to better customer assurance and smoother acceptance in many industrial applications. On the downside, achieving compliance can add to manufacturing costs and requires a commitment to quality management systems.
Performance Testing
Corrosion Tests
Corrosion tests are essential in evaluating the performance of 316L stainless steel in real-world applications. These tests examine how well the material can withstand various corrosive environments, especially important in industries like marine and medical. A key characteristic of corrosion tests is their ability to simulate long-term exposure to hostile conditions. This simulation offers valuable insights into potential failures and durability.
The unique feature of these tests is that they help identify the limits of a material’s lifespan under specified conditions. However, such tests can be time-consuming and costly, potentially delaying project timelines.
Mechanical Property Evaluations
Mechanical property evaluations assess how 316L stainless steel behaves under stress, stretch, and pressure. These evaluations are vital for determining the material's suitability for specific applications, such as structural or fabrication purposes. A distinguished aspect of these evaluations is their focus on properties such as tensile strength, yield strength, and ductility, which are crucial for ensuring safe and effective use.
One unique characteristic of mechanical property evaluations is their ability to inform adjustments in material design or treatment processes, optimizing performance. Nevertheless, these evaluations can also require extensive testing programs, adding to the project’s complexity and expense.
Environmental Considerations
The environmental considerations for 316L stainless steel are crucial to understand as they have direct implications for its application and performance. Various factors influence the longevity and effectiveness of 316L in different settings, particularly its corrosion resistance, sustainability, and overall impact on the environment. By examining these elements, one can appreciate the material’s enduring characteristics and its role in reducing environmental liabilities.
Corrosion Resistance Factors
Importance of Environment
The environment plays a significant role in determining how 316L stainless steel behaves over time. Corrosion resistance is one of its hallmark attributes, largely influenced by environmental factors. High chromium content elevates its protective oxide layer, which is further enhanced in salty and humid atmospheres. Consequently, employing 316L in marine applications is common due to its superior resistance to saltwater corrosion.
This unique feature not only extends the lifespan of components but also minimizes maintenance and replacement costs, making 316L a favorable option for industries that operate in challenging conditions.
Impact of Temperature and Salinity
Temperature and salinity affect the performance of 316L stainless steel as well. Elevated temperatures can accelerate corrosion, especially in aqueous environments, while high salinity can lead to pitting and crevice corrosion. Understanding this interaction is pivotal when designing or selecting materials for specific applications. For instance, systems operating at high temperatures, combined with saline exposure, may require additional protective measures or the use of higher alloyed grades.
The awareness of these impacts helps in tailoring the application specifics, thus preserving integrity under various operational conditions.
Sustainability and Recycling
Life Cycle Assessment
Life cycle assessment (LCA) evaluates the environmental impacts associated with all the stages of 316L’s life, from production to disposal. This comprehensive approach helps in identifying areas for improvement and promoting more sustainable practices in manufacturing and usage. LCA highlights that while stainless steel production is energy-intensive, the longevity and reusability of 316L mitigate such initial environmental costs. The capacity to recycle minimizes waste and makes it a sustainable option for various applications in multiple industries.
Recyclability of Stainless Steel
The recyclability of stainless steel is one of its significant advantages. 316L can be recycled without degradation in its properties. This fact not only conserves resources but also reduces the overall carbon footprint associated with new steel production. The recycling process is efficient, allowing for the recovery of scrap material to be reprocessed into usable steel products.
This inherent recyclability ensures that 316L remains a responsible choice in a world increasingly focused on sustainability. Its reusability contributes positively to reducing environmental impacts, aligning well with global efforts toward resource conservation.
"The ability to recycle stainless steel significantly decreases the environmental burden of producing new materials, making it essential for sustainable development in industries."
Both the performance aspects and environmental benefits of 316L stainless steel not only enhance its applications but also contribute to responsible material use, emphasizing the importance of considering environmental factors in material selection.