Comprehensive Insights into CMC Packaging


Intro
Cellulose microcrystalline (CMC) packaging has carved a significant niche within various industries, particularly pharmaceuticals and food, offering an array of functionalities that align with the intricate demands of these sectors. This exploration of CMC packaging aims to demystify its uses, benefits, and challenges. With a firm grasp of its properties and production techniques, this guide seeks to equip students, researchers, educators, and professionals with the necessary insights to navigate the multifaceted landscape of CMC packaging.
Research Context
Background and Rationale
In today's fast-paced world, the packaging industry finds itself at a crossroads, where sustainability meets technological innovation. CMC stands out as a flexible and resourceful material that resonates well with the current ecological concerns. Derived from natural sources, it plays a critical role in reducing environmental footprints while fulfilling the stringent requirements of modern packaging needs.
The rationale behind focusing on CMC packaging stems from its dual nature—acting as an effective barrier while also being biodegradable. As stakeholders in various sectors increasingly seek greener alternatives, understanding CMC’s properties becomes paramount. Moreover, the shift towards ethical manufacturing practices necessitates a comprehensive evaluation of materials that contribute positively to the environment.
Literature Review
Many studies have meticulously outlined the mechanical properties of CMC, focusing on its water retention and stability, essential for maintaining product integrity during transportation and storage. Key findings reveal that CMC often outperforms synthetic alternatives due to its biocompatibility and minimal toxicological risks. For instance, a study published in the International Journal of Pharmaceutics highlights how CMC enhances the release profile of drugs, which can significantly improve therapeutic efficacy.
On the food front, the Journal of Food Science reported that CMC can effectively replace synthetic emulsifiers which have drawn criticism in recent times. Through these lenses, it becomes undeniable how critical comprehensive knowledge about CMC packaging is.
Methodology
Research Design
This article synthesizes insights from various reputable sources, employing a qualitative research design to deepen the understanding of CMC packaging. Leveraging data from empirical studies, industry reports, and expert interviews ensures a holistic view of the topic.
Data Collection Methods
Data for this narrative is collected through a range of methodologies. The primary methods include:
- Literature Surveys: Deep dives into academic journals and publications relevant to CMC and its applications.
- Expert Interviews: Engaging with professionals in the field to gain first-hand insights on the current trends and future projections of CMC packaging.
The combination of these methods offers diverse perspectives, allowing for a rich and nuanced exploration of CMC packaging and its relevance in contemporary contexts.
Prelims to Packaging
In today’s fast-paced world, the significance of packaging is often taken for granted. Yet, it plays a crucial role, especially in industries like pharmaceuticals and food. This is where CMC packaging comes into the picture. CMC, or cellulose microcrystalline, is not merely an ingredient; it embodies a convergence of innovation, practicality, and sustainability in the packaging domain.
Definition and Overview
To put it simply, CMC is derived from cellulose, a natural polymer found in plant cell walls. Its structure consists of crystalline portions interspersed with amorphous segments, which gives it unique properties. When we talk about CMC packaging, we refer to a range of materials and techniques that leverage the advantages of CMC to produce effective packaging solutions.
Because of its versatility, CMC can serve many roles. It acts as a thickening agent, stabilizer, or even film-former in various formulations. This adaptability is significant, especially in the context of enhancing shelf-life and preserving product quality in pharmaceutical and food sectors. Notably, the biodegradability of CMC aligns well with the growing emphasis on environmentally friendly materials in packaging.
Historical Context
The journey of CMC packaging is intertwined with the evolution of packaging technologies over the decades. Initially, in the early 20th century, the industrial usage of cellulose garnered attention for its mechanical strength and compatibility with other materials. However, it wasn't until the mid-century that the potential of cellulose derivatives like CMC was acknowledged in packaging applications.
During the 1960s, as global awareness about environmental issues began to take root, materials that could decompose without burdening landfills became a priority. Researchers began exploring CMC’s natural properties, prompting its gradual introduction in various packaging forms.
Fast forward to today, CMC is widely recognized for its biocompatibility and versatility, making it the go-to for many manufacturers focused on sustainable practices. From the medical realm, where it helps in drug delivery systems, to the culinary world, where it helps preserve food freshness, the historical expansion and evolution of CMC packaging signify its growing relevance.
Overall, the importance of CMC packaging is etched in its dual ability to protect products while being kind to the planet. As industries continually search for innovative and sustainable solutions, understanding CMC's role offers intriguing insights into both its past and future.
Properties of
The properties of cellulose microcrystalline (CMC) are pivotal in understanding its role in various packaging applications, particularly in sectors like pharmaceuticals and food. Each characteristic plays a significant role in leveraging CMC’s versatility and effectiveness. In this section, we'll explore the intrinsic properties of CMC that contribute to its functionality in packaging solutions, focusing on its chemical composition and key physical characteristics.
Chemical Composition
The chemical make-up of CMC is a defining factor for its performance. It's derived from cellulose, a natural polymer found abundantly in plant cell walls. When cellulose undergoes etherification, it transforms into CMC. This alteration incorporates carboxymethyl groups, enhancing the solubility and functionality of cellulose. The result is a compound that is not only biodegradable, aligning with sustainability trends, but also possesses a molecular structure that allows for diverse applications.
In nature, cellulosic materials are known for their mechanical strength. CMC maintains some of these structural advantages while gaining unique properties that are valuable for packaging. The introduction of hydrophilic carboxymethyl groups allows CMC to form stable gels and films, which can be tailored for specific uses, be it for pharmaceuticals or food preservation. This characteristic opens up pathways for multiple formulations catering to different needs, making it a valuable asset in the industry.
Physical Characteristics
The physical properties of CMC are crucial for its role in packaging. Three of these key attributes include solubility, stability, and viscosity. Each of these characteristics enhances its applicability in diverse environments.
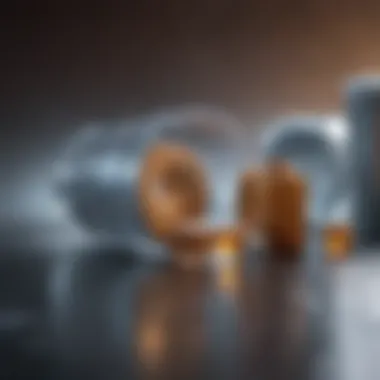

Solubility
Solubility is one of the standout features of CMC. When in contact with water, CMC dissolves and forms a colloidal solution. This behavior is beneficial for applications where moisture control is critical, such as in food packaging. The ability to modulate its solubility means manufacturers can design packaging that interacts well with various contents, ensuring optimal preservation. Furthermore, CMC's solubility enables it to act as a stabilizing agent in emulsions and dispersions.
However, the unique feature of solubility lies in its concentration. At certain levels, CMC can thicken solutions, which can be advantageous for creating sauces or dressings. Yet, too high a concentration might lead to undesired gelling, which poses a challenge when precision is required in applications.
Stability
Stability defines how well CMC performs under various conditions. Its inherent stability against thermal and light degradation means products wrapped in CMC packaging have a longer shelf life. This aspect is particularly advantageous in the pharmaceutical sector, where maintaining the efficacy of drugs is paramount.
Another key characteristic of stability is its resistance to changes in pH, which is crucial when CMC is used in complex formulations. Yet, while CMC is generally stable, it can interact negatively with certain ions leading to precipitation. Hence, the knowledge of those interactions becomes critical to its application in specific contexts.
Viscosity
Viscosity is a measure of a fluid’s resistance to flow and is another critical property of CMC. In packaging, viscosity influences how materials are processed and utilized. CMC solutions can range from thin and watery to thick and gel-like, providing manufacturers with flexibility in formulation.
This range is a beneficial quality when creating products like syrups or gels, where the texture is vital for consumer experience. However, a high viscosity can complicate manufacturing processes, as it could lead to challenges in filling and sealing packages. Therefore, adjusting the concentration of CMC to achieve the desired viscosity while keeping the production process smooth is essential.
"The properties of CMC allow it to serve diverse functions from thickener to film-forming agent, making it a remarkable choice in modern packaging materials."
In summary, the chemical and physical properties of CMC not only enhance its role in packaging solutions but also inform best practices for manufacturers and researchers alike. Understanding these attributes is fundamental to leveraging CMC’s full potential in industry applications.
Manufacturing Process of Packaging
The manufacturing process of CMC (cellulose microcrystalline) packaging serves as a cornerstone in the development of efficient and effective packaging solutions. Understanding this process is crucial not only for manufacturers looking to optimize production but also for those in research and academia who are exploring new frontiers in packaging materials. CMC is widely recognized for its unique properties, such as biodegradability and versatility, making its manufacturing process a vital focus of study.
Raw Material Sourcing
The journey of CMC packaging begins with raw material sourcing. The primary raw material for CMC is wood pulp derived from sustainably managed forests. Sourcing practices vary depending on geographical location, and many manufacturers prioritize obtaining pulp from certified suppliers to ensure minimal environmental impact. In addition to wood pulp, non-wood sources such as cotton can also be used, diversifying the materials available.
The quality of the raw materials directly affects the final product. For example, cellulose extracted from high-quality wood pulp results in superior CMC. Thus, selecting reputable suppliers and understanding the origin of materials is essential. Furthermore, local sourcing can reduce transportation emissions, contributing positively to sustainability goals.
Processing Techniques
Precipitation
Precipitation is a critical step in the manufacturing of CMC. It involves dissolving cellulose in a solvent and then inducing a chemical reaction that causes it to precipitate out. This method is particularly significant as it allows for a controlled production of CMC, leading to desired particle sizes and purity levels. The key characteristic here is that precipitation can yield a high-quality product with consistent properties, which is essential for effective packaging applications.
A unique feature of precipitation is its adaptability. Manufacturers can tweak the conditions to produce different grades of CMC, making it a preferred technique in the industry. The main disadvantage, however, can be its cost, as the required solvents may add to production expenses depending on the scale of production.
Filtration
Filtration plays a crucial role in ensuring the purity of CMC during manufacturing. The process involves separating solids from the liquid, which is essential for removing any undissolved particles and impurities. One of the key benefits of filtration lies in its ability to enhance the overall quality of the CMC product, ensuring that only the desired molecules are present.
Notably, the filtration process is also instrumental in maintaining environmental standards, as proper waste management systems can be implemented to recycle used solvents. However, if not managed properly, filtration can introduce complexities in the process, leading to potential delays or contamination issues during production.
Drying
The drying phase is where the final form of CMC takes shape. This step involves removing any residual moisture to create a stable product that can be stored and transported without degradation. A key characteristic of drying is that it iteratively transforms the physical state of CMC, preparing it for further applications.
This step is beneficial as it ensures the shelf stability of the finished product, which is critical for industries dealing with pharmaceuticals and food packaging. On the flip side, careful control of drying conditions is imperative; excessive heat or prolonged drying can compromise the structure of CMC, leading to quality issues.
Quality Control Measures
Quality control measures are indispensable in the CMC manufacturing process, safeguarding product integrity and performance. Various techniques are employed, ranging from regular sampling and testing of raw materials to final inspections of the packaged product. These measures ensure that the CMC produced meets stringent industry standards and that it adheres to regulatory guidelines.
For instance, routine tests may assess viscosity, solubility, and microbial contamination, which are common challenges that can affect CMC’s performance in its applications. Employing advanced analytical methods, manufacturers can promptly identify any deviations from expected specifications, facilitating timely interventions and quality enhancements.
Applications of Packaging
The applications of CMC packaging are myriad and substantial, reflecting its significance across diverse sectors. This section digs deep into how CMC, or cellulose microcrystalline, plays a crucial role in the pharmaceutical and food industries, demonstrating its versatility and effectiveness. Understanding these applications opens the door to a more comprehensive comprehension of the role of CMC in modern development and sustainability.
Pharmaceutical Industry
Drug Delivery Systems


In the realm of pharmaceuticals, drug delivery systems stand out due to their ability to enhance the bioavailability of medications. CMC acts as a vehicle in these systems, permitting controlled release of drugs in a manner that optimizes their therapeutic effectiveness. One of the key characteristics of drug delivery systems utilizing CMC is targeted release, which ensures that the active ingredients reach the intended site of action without being prematurely released. This precision is a huge boon for patients with chronic conditions requiring consistent dosage.
A unique feature of these systems is their solubilization properties; CMC can transform hydrophobic drugs into more soluble forms, thereby increasing their absorption in the body. However, it is worth mentioning that the success of CMC in drug delivery is influenced by various factors, such as the method of incorporation and the chemical nature of the drug itself. In this field, while CMC offers robust advantages, understanding its limitations is vital as misapplication could lead to effectiveness issues or undesirable side effects.
Stabilization of Formulations
Stabilization of formulations is another pivotal area of application for CMC. Here, CMC’s thickening and binding properties come into play, ensuring the stability and consistency of liquid formulations such as syrups, emulsions, and suspensions. This characteristic makes it a popular choice, as it prevents separation during the shelf life of the product. As a stabilizer, CMC plays an essential role in maintaining the intended viscosity and texture of pharmaceutical products.
One key aspect of this stabilization is the unique ability of CMC to form viscoelastic gels, which manage to withstand shear stress while maintaining their performance. Although beneficial, challenges may arise in terms of precise dosage control during formulation development. The balance between effectiveness and formulation complexity must be carefully managed to ensure final product efficacy.
Food and Beverage Sector
Food Preservation
In the food sector, CMC packaging plays a vital role in food preservation, which is often paramount in today's fast-paced environment. The ability of CMC to retain moisture helps prevent spoilage, extending the shelf life of products such as sauces, dressings, and dairy items. This preservation aspect enhances consumer satisfaction by ensuring that food products maintain their quality until they reach the table.
The key characteristic that sets CMC apart in food preservation is its gelling capacity, which can form a protective barrier around food items, reducing oxidation and minimizing microbial growth. This unique feature makes CMC a popular choice for manufacturers looking to achieve longer shelf lives without the need for artificial preservatives. However, as with its applications in pharmaceuticals, the concentration of CMC used in food formulations needs careful consideration to avoid alterations in taste or texture.
Modified Atmosphere Packaging
Modified atmosphere packaging is another innovative application of CMC in the food industry. This technique modifies the atmosphere inside food packaging to extend freshness and prevent spoilage. CMC assists in this process by acting as a barrier, effectively retaining volatiles and reducing moisture loss. Its popularity in this area is primarily grounded in its effectiveness at prolonging the quality of perishables like fruits, vegetables, and meats.
The unique aspect of modified atmosphere packaging involving CMC is its compatibility with various filling gases, which allows manufacturers to tailor the atmosphere according to the specific needs of different products. On the downside, the initial investment in packaging technology and materials can be significant, often deterring small-scale producers. Yet, for larger organizations, the quality retention and prolonged shelf life offered by CMC-based solutions often justify the costs involved.
"The applications of CMC in both pharmaceuticals and food preservation demonstrate its versatility, shaping the landscape of consumer goods while addressing modern challenges in safety and sustainability."
Through these sections on applications, it's apparent that CMC packaging stands as a formidable player in enhancing product stability and integrity across industries, marking its importance as both a functional and strategic component in packaging solutions.
Advantages of Packaging
The use of cellulose microcrystalline (CMC) in packaging has become a cornerstone for numerous industries, particularly the pharmaceutical and food sectors. Understanding the benefits that CMC packaging brings to the table is crucial for anyone involved in product development, sustainability efforts, or cost management. The advantages span several dimensions, from environmental impact to practical applications, showcasing its versatility in today’s fast-paced markets.
Biodegradability
One of the standout features of CMC packaging is its biodegradable nature. Unlike conventional plastic materials that persist in the environment, CMC decomposes naturally, thanks to its cellulose base.
- Environmental Protection: The decreasing lifespan of plastic waste has become a global crisis, leading many manufacturers to seek alternatives. CMC offers a pathway to reduce landfill contributions.
- Consumer Preference: With consumers becoming increasingly eco-conscious, utilizing biodegradable materials like CMC can give businesses an edge in the market. Companies that choose CMC are often perceived as more responsible and progressive.
"Incorporating biodegradable materials not only aligns with environmental goals but also speaks volumes to a brand's commitment to sustainability."
Versatility
Another notable advantage of CMC packaging is its versatility across applications. CMC can be molded and shaped into various forms, catering to different needs in both food and pharmaceutical packaging.
- Multi-Functional Uses: Whether as a protective layer for drugs or as part of packaging systems for perishable goods, CMC easily adapts to meet regulatory and performance standards.
- Compatibility with Other Materials: Its properties allow for blending with other polymers, enhancing the overall functionality of packaging solutions. This compatibility broadens its usefulness across different sectors, ensuring that it meets varying requirements.
The versatility of CMC makes it attractive to manufacturers looking to streamline operations while maintaining quality.
Cost-Effectiveness
Cost management is always a vital consideration in manufacturing. CMC packaging stands out in terms of financial efficiency. The benefits can be grouped into several categories:
- Material Sourcing: CMC can often be derived from readily available cellulose sources, making it less expensive than some synthetic alternatives that require complex processing. This availability leads to lower prices per unit.
- Operational Efficiency: The ease of processing CMC allows manufacturers to enjoy faster production cycles and reduced waste, further enhancing profitability.
- Long-term Savings: By investing in CMC, companies often find that the operational savings and consumer appeal lead to better return on investment over time.
In summary, the advantages of CMC packaging are significant. It combines environmental responsibility with versatility and cost-effectiveness, making it a smart choice for industries aiming to enhance product legitimacy and responsibility in a changing economic landscape.
Challenges in Packaging
In the realm of CMC packaging, challenges abound. While this material offers a plethora of advantages, there are significant hurdles that stakeholders face. Understanding these challenges is crucial not only for manufacturers but also for researchers and policymakers. It paints a clearer picture of the landscape in which CMC is utilized and provides insights into areas needing improvement.
Regulatory Hurdles
One of the foremost challenges involves regulatory hurdles. The directives and standards surrounding packaging materials, particularly in pharmaceuticals and food sectors, can be quite thick. Various entities such as the U.S. Food and Drug Administration (FDA) and the European Food Safety Authority (EFSA) impose strict regulations to ensure safety and efficacy.
This labyrinth of regulations can impede swift market entry for new CMC products. Companies must invest considerable resources in compliance testing and validation processes. The intricate nature of regulations, often varying from one jurisdiction to another, compounds these issues. For instance, a product approved in one country might face a complete reevaluation in another, resulting in delays and increased costs.
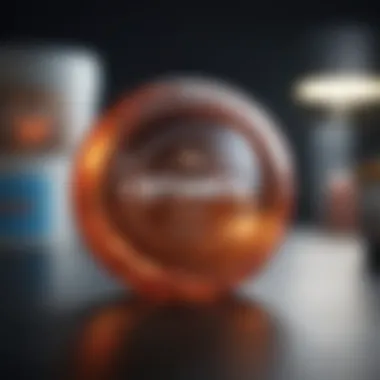

Moreover, transparency is key; regulatory bodies require detailed information on the source and processing of CMC. Failure to meet these requirements might lead to rejection or withdrawal of approval, which could be detrimental to a company’s reputation and bottom line.
Supply Chain Issues
The journey from raw material to final product isn't always smooth. Supply chain issues pose significant challenges in CMC packaging. Factors such as geopolitical tensions, natural disasters, or even unexpected market fluctuations can disrupt the supply of crucial materials necessary for CMC production.
Accurate sourcing of cellulose, the primary component of CMC, can also introduce complications. With increasing demand for sustainable practices, companies face pressure to evaluate the sustainability of their sourcing methods. This often involves dealing with multiple suppliers and logistics arrangements, which can easily lead to delays.
Just-in-time (JIT) inventory strategies, while cost-effective, can exacerbate these challenges. If a component runs low, it can halt production, leaving companies scrambling for solutions. As a result, many organizations are reevaluating their supply chain models to build more resilience.
Technical Limitations
Technical limitations represent another significant challenge in CMC packaging. While CMC presents unique properties, there are boundaries to what can be achieved with this material. For one, the scalability of CMC production is a concern. Shifting from pilot-scale production to commercial-scale operations can lead to inconsistencies in material properties.
Process variations, temperature sensitivity, and moisture control are all critical factors in maintaining quality during production. Small deviations can lead to end products that don’t meet the desired specifications. Additionally, the blending of CMC with other materials to enhance packaging functionality can present complications; compatibility issues can arise, impacting overall performance.
Moreover, while CMC is indeed biodegradable, its degradation rate can sometimes be slower than desired in certain environments. This can lead to questions surrounding sustainability claims, prompting further investigation and optimization.
Understanding the myriad challenges that come with CMC packaging can guide future innovations. A proactive approach to these obstacles can elevate the efficacy and application of CMC in numerous industries.
Future Trends in Packaging
The world of CMC packaging is evolving rapidly, driven by technological advancements, market demands, and sustainability goals. Recognizing future trends is vital for stakeholders in industries such as pharmaceuticals and food and beverage. As CMC continues to carve out its niche in packaging solutions, understanding these trends can lead to better decision-making and strategic planning. In this section, we will explore the innovations in material sourcing, advancements in manufacturing techniques, and sustainability initiatives that shape the future of CMC packaging.
Innovations in Material Sourcing
The sourcing of materials plays a crucial role in the production of CMC packaging. Recently, there has been a noticeable shift towards utilizing renewable resources. Manufacturers are looking for alternatives that minimize environmental impact while still delivering effective packaging solutions.
A prime example is the extraction of cellulose from non-food crops such as agricultural residues. This approach not only ensures a constant supply of raw materials but also reduces the pressure on food resources. By tapping into these alternative sources, companies can improve their sustainability profile and appeal to a growing audience that prioritizes eco-friendly options.
Additionally, the trend towards biosourcing materials has ignited research into developing advanced cellulose derivatives. Innovations in refining methods can enhance the properties of CMC, allowing for better performance in moisture and gas barrier applications. In the race to stay ahead of the curve, organizations are increasingly collaborating with research institutions to explore novel cellulose applications.
Advancements in Manufacturing Techniques
As technology progresses, so do the methods used in CMC packaging production. State-of-the-art manufacturing techniques contribute not only to the quality of the packaging materials but also to how efficiently they are produced.
For instance, extrusion technology has gained traction, allowing for better control over the consistency of the end product. This method offers the benefit of continuous production, meaning less waste and higher output. Furthermore, companies are investing in advanced coating processes that enhance the barrier properties of CMC without compromising its biodegradability.
Laser cutting and 3D printing are also emerging as innovative techniques. These methods provide the flexibility to design customized packages that meet specific customer needs while reducing excess material usage. Essentially, the shift towards such advanced manufacturing strategies is not just about efficiency; it is also about customization and meeting diverse market demands.
Sustainability Initiatives
In today’s context, sustainability is no longer an afterthought; it’s a key driver in the development and application of CMC packaging. Companies are increasingly adopting sustainable practices to appeal to environmentally conscious consumers and comply with regulatory standards.
A fundamental aspect of these initiatives is the improvement of the end-of-life management of CMC products. Research is ongoing into optimizing recycling processes and ensuring that CMC packaging can break down effectively in various settings, even in home composting.
Furthermore, industry bodies and organizations are pushing for guidelines that emphasize the importance of life cycle assessments. These assessments are vital in providing transparency and demonstrating the sustainability credentials of CMC packaging solutions. By actively engaging in these initiatives, companies not only enhance their brand reputation but also contribute positively to the environment.
Investing in sustainable CMC packaging is not just ethical—it’s becoming essential for business survival in a green economy.
Ultimately, the future of CMC packaging hinges on innovation, efficiency, and sustainability. By keeping a close eye on evolving trends, stakeholders can ensure that their strategies align with market demands while also contributing to a more sustainable future.
The End
The conclusion of this article profoundly emphasizes the importance of understanding CMC packaging in the broader context of modern industries. Throughout this exploration, we've touched on essential facets—its properties, manufacturing processes, application range, advantages, challenges, and the potential future directions. Each of these elements plays a pivotal role in how CMC’s characteristics can influence the efficacy and safety of packaged products.
Clear takeaways are numerous. For instance, CMC's remarkable biodegradability and versatility stand out as paramount attributes that align seamlessly with the contemporary drive towards sustainable practices. This alignment is not just a trend; it’s an urgent call for industries to evolve responsibly. As consumer awareness regarding environmental impact rises, businesses that adopt CMC packaging not only fulfill regulatory compliance but also cater to a market more inclined towards eco-friendly options.
Moreover, amidst the challenges highlighted—for example, regulatory hurdles and technical limitations— lies the opportunity for innovation. Industry professionals and researchers alike must recognize these hurdles as springboards for advancing CMC technology and its applications. As we examined, innovations in sourcing and manufacturing techniques pave the way for improved formulations that could mitigate some of these issues.
In summary, as the packaging landscape continues to evolve, CMC stands on the threshold of playing a more significant role in both pre-existing and emergent markets. The implications of embracing this material are vast, and the future of CMC packaging appears promising, contingent on concerted efforts from stakeholders across various sectors.
Summary of Key Insights
- Versatility and Applications: CMC has far-reaching applications, from pharmaceuticals to food and beverage industries, demonstrating its adaptability.
- Sustainability: The biodegradability of CMC packaging is a crucial advantage, appealing to eco-conscious consumers and tightening regulatory frameworks.
- Challenges and Innovations: Addressing regulatory hurdles and technical challenges could inspire transformative innovations, expanding CMC's market applicability.
- Material Sourcing: Innovations in sourcing raw materials for CMC can significantly enhance both quality and environmental credentials.
"Understanding the dynamics of CMC packaging today is vital for shaping a sustainable tomorrow."
Implications for Future Research
As industries progress, ongoing research into CMC packaging is crucial. Future studies should hone in on several key areas:
- New Sourcing Strategies: Investigating alternative sustainable sources for CMC could revolutionize its cost-effectiveness and availability.
- Advanced Manufacturing Techniques: Exploring cutting-edge processes can lead to improved quality and functionality of CMC packaging solutions.
- Impact Assessment: Comprehensive evaluations of CMC's environmental footprint will be necessary to substantiate claims of sustainability.
- Regulatory Compliance Innovations: Research aimed at navigating evolving legislation surrounding packaging materials can position CMC as a frontrunner in compliance.
- Consumer Behavior Studies: Understanding how consumers perceive CMC packaging can yield insights that drive marketing strategies and product development.