Exploring the Benefits and Challenges of Polypropylene Gears
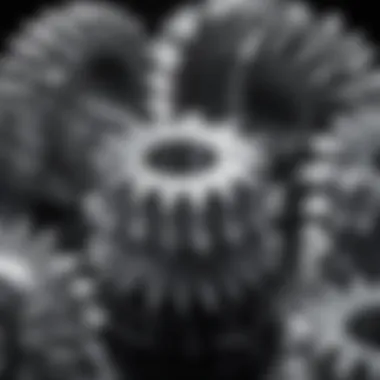
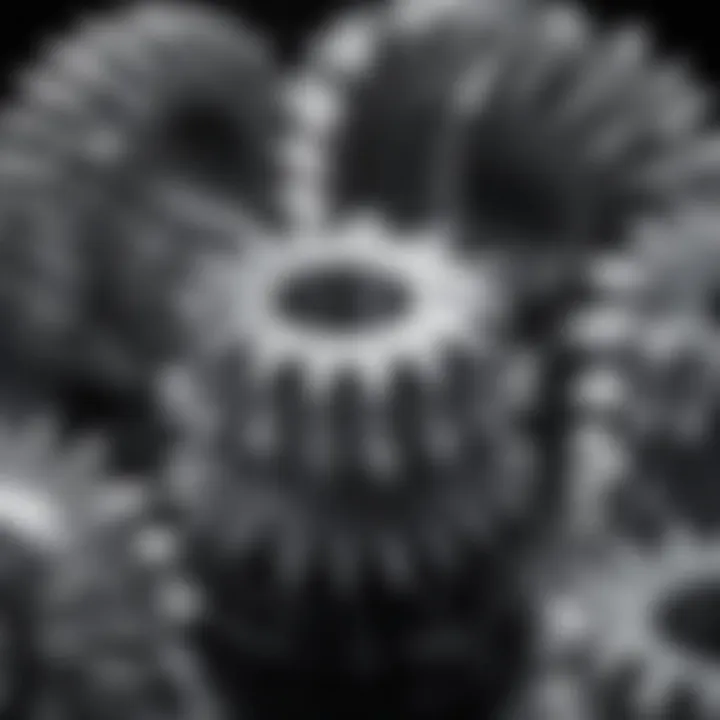
Intro
Polypropylene gears have gained significant traction in various engineering applications. Their lightweight structure coupled with remarkable chemical resistance makes them a favored choice in industries ranging from automotive to food processing. This versatility isn't merely coincidence; it's grounded in a careful selection of materials and innovative manufacturing processes that complement the unique properties of polypropylene. Understanding how these gears are produced and where they fit into the bigger picture provides valuable insights for students, researchers, and professionals alike.
Research Context
Background and Rationale
The exploration into polypropylene gears reflects growing trends in material science and mechanical engineering. As industries are increasingly pushed to reduce weight without sacrificing component performance, polypropylene emerges as a viable candidate. Companies, driven by the pursuit of efficiency and sustainability, have turned to alternative materials. The need for this discussion is underpinned by the shift towards lighter, stronger, and more sustainable engineering solutions. As we gather insights from multiple sectors, it becomes clear how polypropylene gears stand on the frontier of innovation.
Literature Review
In reviewing the existing literature, it’s apparent that polypropylene has been studied primarily in the context of its intrinsic properties, such as tensile strength and thermal stability. Noteworthy research papers, including those found on platforms like Wikipedia and studies highlighted on Britannica, discuss the polymer chain structure that contributes to these characteristics, but they often stop short of examining practical applications in gear manufacturing. Much of the current understanding lacks depth in terms of engineering challenges, which presents an opportunity for further exploration.
Methodology
Research Design
In investigating the effectiveness of polypropylene gears, a multi-faceted research design will be adopted. This includes experimental methods and case studies taken from real-world applications across various industries. By studying the manufacturing processes and performance metrics of existing polypropylene gears, we can bridge the knowledge gap recognized in current literature. The intention lays not just in theoretical knowledge but practical implementation as well.
Data Collection Methods
Data for this exploration will be collected using a combination of qualitative and quantitative approaches. Surveys and interviews with industry professionals will yield firsthand insights into design preferences and material performance. Performance data from real-world use cases will include breakdown rates, wear resistance, and the impact of environmental conditions on gear longevity.
This multi-angle approach will ensure a comprehensive understanding of polypropylene gears, gearing us toward a solid foundation for further discussion in the following sections.
Prelims to Polypropylene Gears
In today's fast-paced manufacturing and engineering environments, the materials chosen for component production play a crucial role. This is especially true for gears, where the material's characteristics can significantly influence the performance, durability, and functionality of the mechanisms they are part of. Among the various materials available, polypropylene stands out as an increasingly popular choice for gears, particularly in applications where weight and resistance to chemicals are paramount.
Understanding Gears
Gears are fundamental mechanical elements that transmit power from one component to another or change the direction of motion in machines. They need to be designed and crafted with meticulous attention to detail because even a small gear may have a massive impact on operational efficiency. Understanding the functionality and role of gears within a system is vital for any engineering professional. What’s more, the demand for lightweight gears that do not compromise on strength makes polypropylene an intriguing option. It's said that necessity is the mother of invention, and the rise of polypropylene gears is a perfect example of this adage.
The basic structure of a gear involves teeth that mesh correctly with others to transmit torque efficiently. Depending on the application, gears can be crafted in many different sizes, shapes, and materials. But when you introduce polypropylene into the discussion, several unique attributes come into play. Its lightweight features reduce the overall weight of devices, making it suitable for use in sectors like automotive and consumer products.
Polypropylene as a Material
Polypropylene is a thermoplastic polymer known for its durability, flexibility, and resistance to chemical attacks. Unlike metals or other plastics, polypropylene offers a blend of properties that makes it appealing for manufacturing gears.
- Lightweight: This material weighs significantly less than metals, allowing for easier handling and installation of gear systems.
- Chemical Resistance: Polypropylene is not affected by many chemicals, making it ideal for use in environments where exposure to such substances is likely.
- Cost-Effective: The production costs associated with polypropylene can be lower compared to traditional materials. This often translates into a reduction in the overall price of the end product.
One might argue that it is this mix of versatile properties that have prompted engineers to reevaluate their approach to gear design. It’s not only about performance; it’s also about finding solutions that meet economic and environmental standards. The challenges posed by certain applications, however, must be scrutinized. High loads or extreme temperatures can sometimes make polypropylene gear unsuitable, leading to necessary discussions about design limitations.
"Polypropylene gear technology illustrates the balance between innovation and traditional manufacturing practices."
In summary, the transition towards polypropylene gears represents a broader trend in engineering focused on efficiency, sustainability, and adaptability. Understanding both gears themselves and the materials from which they are made is crucial, particularly with the ongoing advancements shaping the future of manufacturing.
Properties of Polypropylene
Understanding the properties of polypropylene is key in appreciating why it stands out as a material for gears. Polypropylene is often regarded as a lightweight, flexible, and durable material. These traits make it a favorable choice in various industries where efficiency and reliability are paramount. Let’s delve into the specific characteristics that contribute to the effectiveness of polypropylene gears.
Chemical Resistance
Chemical resistance is one of the most notable benefits of polypropylene. This material does not react with most acids, bases, and solvents. Because of this trait, it's often deployed in environments where exposure to harsh chemicals is a concern. For instance, in the automotive sector, where gears might come into contact with petroleum products or cleaning agents, polypropylene holds up well.
Examples include gears found in components like fuel pumps and fluid transfer systems where durability amidst constant exposure to aggressive substances is essential. The fact that polypropylene can stand strong against corrosive chemicals not only means longevity for the gears but also minimizes the need for frequent replacements.
Mechanical Strength
Another important aspect is the mechanical strength of polypropylene. While this material is lightweight, it doesn’t skimp on strength. Particularly, it possesses a good tensile strength, making it suitable for gears that need to endure significant forces in operation.
Polypropylene gears can handle various loads without succumbing to structural failures. This is especially significant in industrial applications where operational efficiency is critical. To illustrate, in material handling systems, the requirement for gears that can withstand heavy load cycles is essential. The mechanical integrity of polypropylene ensures that these gears perform with minimal wear under stress, making them a solid choice in demanding environments.
Thermal Stability
Lastly, let's talk about thermal stability. Polypropylene shows proficient performance under a range of temperatures. It can retain its shape and function across a moderate temperature spectrum, which is vital in industries that experience frequent fluctuations in heat. In the realm of gears, thermal deformation can be a dealbreaker. If a gear warps due to heat, it can lead to malfunction or even complete breakdown.
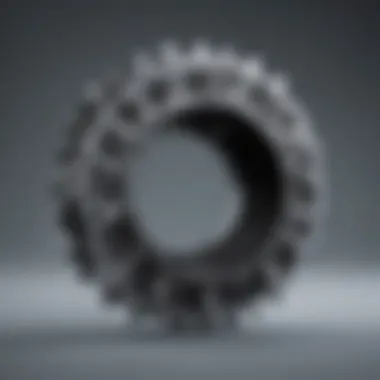
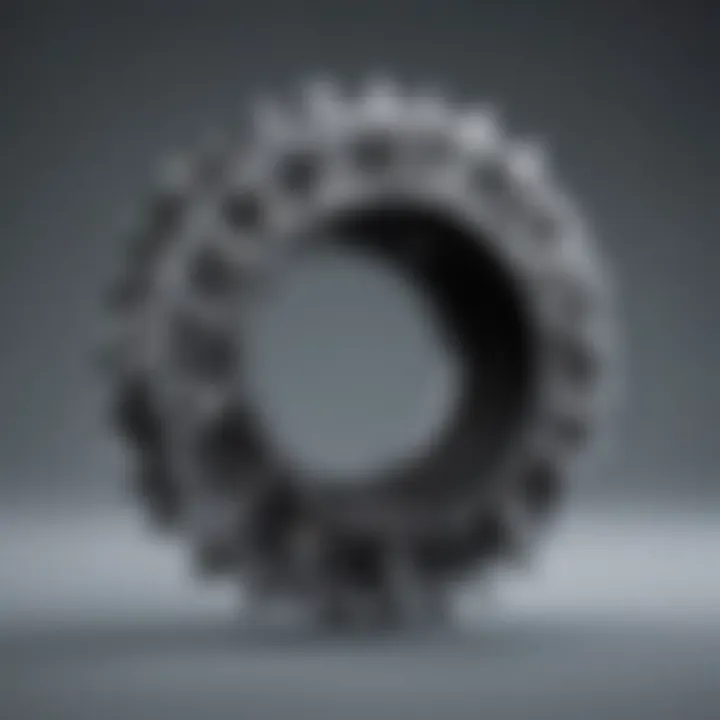
For instance, in the context of electronic appliances, where gears may be subjected to heat generated by motors, the thermal properties of polypropylene help ensure that they maintain their performance over time. This thermal resilience enables polypropylene gears to be suitable for various applications, keeping them reliable even when the heat is on.
"The robustness of polypropylene gears lies in their unique combination of chemical resistance, mechanical strength, and thermal stability, making them indispensable in modern engineering."
By comprehensively understanding these properties, we can appreciate not just the advantages but also the strategic decisions behind choosing polypropylene for gear applications.
Manufacturing Processes for Polypropylene Gears
The manufacturing of polypropylene gears requires a nuanced approach because the material itself offers unique advantages and characteristics. Understanding the different processes is essential for producing gears that meet specific performance requirements. It enables manufacturers to harness the potential of polypropylene while addressing its inherent material challenges. As various industries increasingly turn to polypropylene gears for their lightweight yet durable properties, familiarity with the manufacturing methods becomes almost imperative for innovation and efficiency.
Injection Molding Techniques
Injection molding remains the backbone of producing polypropylene gears at scale. This technique involves melting polypropylene pellets and injecting the molten material into specially designed molds. The process is not just about speed; it also allows for precision in creating complex gear geometries, which can be a significant benefit in optimizing gear performance.
- Efficiency: The method offers high production rates, reducing time and labor costs while ensuring consistent quality across batches.
- Complex Designs: It supports intricate designs that could be infeasible with traditional machining methods, allowing for innovative gear configurations.
- Material Waste: The efficiency of injection molding minimizes material waste compared to other techniques like machining.
However, care must be taken regarding the cooling rates and mold design, as these factors can affect the final gear’s dimensions and mechanical properties. Variations in temperature management during the molding process can lead to dimensional inconsistencies and impact the gear's performance.
3D Printing Applications
In recent years, 3D printing has emerged as a transformative force in gear manufacturing, offering flexibility that traditional methods cannot match. With this technology, engineers can instantaneously create prototypes or even final products based on advanced designs.
Benefits of 3D printing polypropylene gears include:
- Customization: Easily modify designs for specific applications without modifying the manufacturing setup.
- Rapid Prototyping: Speedy test cycles can facilitate innovation, allowing modifications based on real-world testing results.
- Reduction in Logistics: Local production capabilities eliminate delays often associated with shipping and handling.
Still, it’s crucial to choose the right 3D printing technology, as not all methods deliver the same strength and durability in the final parts. Additionally, one has to consider the layer adhesion characteristics of printed gears, which may affect their performance in high-load applications.
Machining Considerations
Machining techniques, though not as prevalent for producing polypropylene gears, do hold value in specific applications—particularly where higher precision is required. This segment often uses processes like milling or turning to refine gear profiles post-manufacturing. Choosing the right machining method and parameters can enhance the quality and functionality of gears produced.
Key points to consider when machining polypropylene include:
- Tool Selection: Using the correct cutting tools is vital since polypropylene can be prone to melting under heat. Selecting tools made from high-speed steel or carbide can mitigate this risk.
- Cutting Speed: Opt for moderate cutting speeds to avoid excessive heat generation that could lead to undesirable materials behavior.
- Coolants: The use of coolants is sometimes necessary to maintain appropriate temperatures and improve the life of cutting tools during machining operations.
By understanding and mastering these diverse manufacturing processes, stakeholders can effectively leverage polypropylene’s advantages to create reliable, efficient gear solutions tailored for various applications.
Applications of Polypropylene Gears
The versatility of polypropylene gears is becoming increasingly clear, especially as industries look for materials that not only perform well but also bring in costs savings and efficiency. Polypropylene is particularly attractive due to its lightweight nature, resistance to various chemicals, and the ability to mold into intricate shapes. This opens the door to numerous applications across different sectors.
Automotive Industry
Transmission Systems
In the realm of automobiles, transmission systems are fundamental. Here, polypropylene gears demonstrate their unique suitability. The key characteristic of these gears is their ability to operate under conditions that demand lightweight yet durable materials. When integrated into a transmission system, polypropylene can help reduce overall vehicle weight, thus boosting fuel efficiency without compromising performance.
One notable feature is the inherent resistance of polypropylene to wear and fatigue, which makes these gears highly desirable for long-term use in tight spaces where conventional gears may struggle. This translates to significant cost savings in manufacturing and repairs in the long run.
Accessory Gears
Accessory gears serve an essential role in automotive systems beyond just the transmission. These gears can be found in everything from windshield wiper mechanisms to air conditioning compressors. A key characteristic here is the ability to produce gear assemblies that require minimal lubrication, further enhancing mechanical efficiency. Polypropylene's chemical resistance ensures it withstands exposure to various fluids and environmental factors, making it a popular choice for these components.
However, one tradeoff is that while they excel in many applications, their performance may diminish in extremely high load scenarios. As a result, designers must carefully evaluate the mechanics involved to ensure efficiency without stress on the gear material.
Industrial Equipment
Material Handling Systems
Within industrial settings, material handling systems are pivotal for maintaining workflow. Polypropylene gears utilized in these systems provide excellent corrosion resistance, which is vital when dealing with potentially abrasive or corrosive materials. This quality allows for smoother operation and prolongs the lifespan of the machinery. The lightness of polypropylene also aids in reducing energy consumption during operation, a crucial factor for companies looking to enhance productivity while being cost-effective.
One unique aspect of using polypropylene gears in material handling is their adaptability to various shapes and forms, allowing for customized solutions tailored to specific tasks and layouts.
Pumps and Compressors
Pumps and compressors often rely on gears to help manage the movement of fluids efficiently. The use of polypropylene gears in this context highlights their resilience against chemical exposure, which is particularly advantageous in industrial environments where different types of liquids are handled. A notable feature is their ability to perform reliably at moderate pressures, offering a balance between performance and durability.
While they gather much praise, they can still be limited in terms of high-heat resistance, which may pose challenges in certain applications. Understanding these limitations is key for engineers who need to design systems that can capitalize on the advantages of polypropylene without wandering into problematic scenarios.
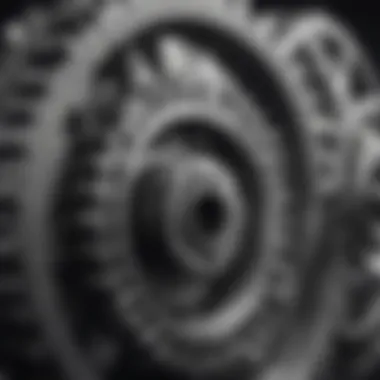
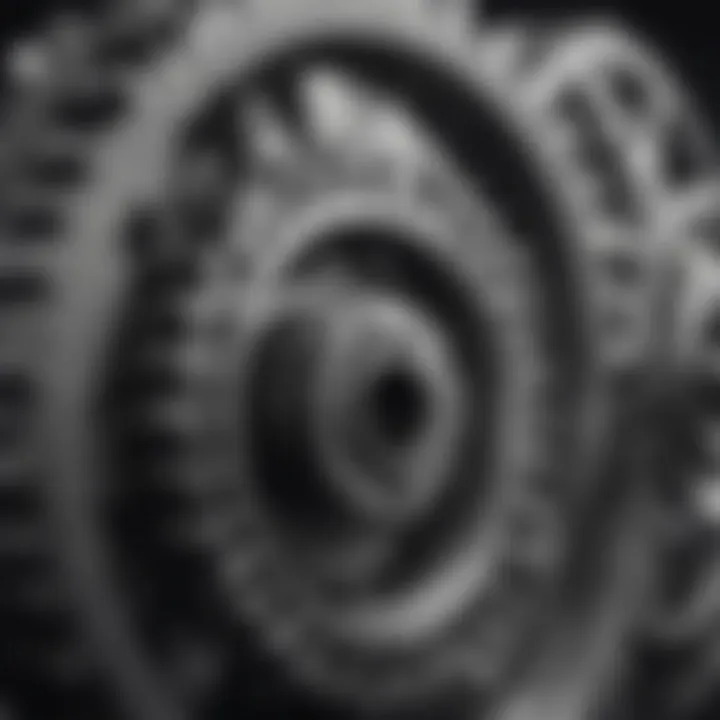
Consumer Products
Home Appliances
In the consumer market, home appliances often incorporate polypropylene gears to capitalize on their advantageous qualities. These gears can be found in devices like washing machines and food processors, where they help transmit motion efficiently and quietly. One major draw is their lightweight nature, which aids in reducing the overall weight of the appliance, naturally decreasing shipping costs and energy usage during operation.
However, there is a downside: under prolonged, strenuous usage, such gears may face wear. Thus, for high-usage appliances, consideration of gear alternatives may be warranted to guarantee robustness.
Power Tools
Power tools are another place where polypropylene gears shine. They facilitate the internal mechanisms that require both strength and precision without adding excessive weight. Their standout characteristic is the reduced noise they generate compared to metal gears, which is crucial for user comfort and practicality.
Yet, like their application in home appliances, polypropylene gears come with limitations regarding heat exposure. As power tools may generate significant heat during operation, it's essential to assess their suitability for specific tasks to ensure they don’t fall short during intense usage.
In summary, the applications of polypropylene gears span across automotive, industrial, and consumer sectors, highlighting their adaptability and advantageous features. Understanding these applications not only aids in selecting the right gears for specific needs but also underscores the importance of balancing their strengths against limitations.
Performance Metrics of Polypropylene Gears
In the realm of engineering, performance metrics are the benchmarks by which the effectiveness of materials is gauged. For polypropylene gears, understanding these metrics is crucial for engineers and industry professionals who need to evaluate suitability for specific applications. Performance metrics help in discerning the wear characteristics, load-bearing capabilities, and overall lifespan of gears made from this versatile polymer. Such information is invaluable, as it allows for informed decisions regarding design and replacement strategies, ultimately affecting the efficiency and reliability of the machinery in which these gears are utilized.
Wear Resistance
Wear resistance refers to a material's ability to withstand degradation due to friction and other mechanical interactions. In the case of polypropylene gears, this characteristic is notably significant, as these components often operate in settings where continuous contact with other surfaces occurs. While polypropylene might not boast the same wear resistance as metals like steel, its lighter weight can lead to less overall wear in certain applications.
Polypropylene shows good resistance to abrasive wear, especially when compared to many other thermoplastics.
- Polypropylene Gears in Applications
From domestic appliances to automotive parts, these gears are engineered for ensemble with components that receive frequent movement and contact. This requires a balanced approach to wear management, combining material choice with design. Incorporating additives or using surface treatments can enhance the wear performance further, which is critical in applications where gears are subject to differing load conditions.
Load Capacity
Load capacity is essentially the maximum load that a gear can handle without failing. It's a vital metric when considering polypropylene gears, as many applications may subject them to significant mechanical strain. Polypropylene offers satisfactory load capacity, enabling it to function effectively in many industrial scenarios where lighter materials are desired but high performance is still essential.
When assessing load capacity, it is important to remember:
- Static vs. Dynamic Loads
Static loads are those that remain constant over time, whereas dynamic loads fluctuate during operation. Polypropylene can handle moderate static loads well but may experience deformation under excessive dynamic loads. - Design Considerations
The geometry of polypropylene gears affects load-carrying capacity. Designing gears with optimal tooth profiles and thickness can lead to improved performance and longevity under stress.
Life Cycle Assessment
A life cycle assessment (LCA) for polypropylene gears looks at their impact from raw material extraction to production, use, and eventual disposal. Understanding the full life cycle of these gears provides insights into environmental implications and helps identify areas where improvements can be made from a sustainability perspective.
Consider the following aspects of LCA in the context of polypropylene gears:
- Resource Efficiency
Polypropylene is not only cost-effective to produce, but it also utilizes petroleum resources compared to more traditional materials like metals, which require more energy-intensive methods for manufacturing. This highlights a potential reduction in the carbon footprint during the gear's lifespan. - Recycling Potential
As a thermoplastic, polypropylene can be reheated and reformed, which creates promising prospects for recycling at the end of its life cycle. Innovations in recycling technologies mean that the environmental impact may significantly lessen over time, closing the loop for aged components.
“Assessing wear resistance, load capacity, and life cycle is essential to maximize the benefits of polypropylene gears in practical applications.”
Incorporating these performance metrics into the design and application of polypropylene gears can enhance not only device efficiency but also align with modern sustainability goals.
Challenges in Using Polypropylene Gears
Polypropylene gears are often chosen for their unique properties, but the truth is they come with their fair share of challenges. Understanding these obstacles is crucial for engineers and designers who wish to maximize the effectiveness of these gears while minimizing potential downsides. Below, we’ll dissect the main challenges, offering insight into specific elements that can significantly impact performance, durability, and design.
High Load Applications
When it comes to high-load applications, polypropylene gears can struggle under the weight. Polypropylene, while known for its chemical resistance, does not boast the same mechanical strength as some metals or even other plastics. This poses challenges in environments where high torque or substantial weight is routinely applied. It’s essential to evaluate the specific loads that these gears will face in practical applications. For instance, using polypropylene gears in heavy machinery like a crane can lead to failures if the stress exceeds their capacity.
"Design engineers should always calculate expected loads and factor in a safety margin when selecting polypropylene gears."
Some strategies might include:
- Using composite materials: Reinforcing polypropylene with fibers can enhance strength without significantly increasing weight.
- Optimizing gear design: Altering the tooth profile or adding support structures can help improve load distribution.
Temperature Sensitivity
Temperature can be a double-edged sword for polypropylene gears. They tend to perform poorly in extreme temperatures. Exposure to high heat can lead to softening of the material, whereas cold conditions might make it brittle. Maintaining temperature control is fundamental in applications like automotive systems, where engines generate significant heat. If a polypropylene gear loses its integrity in such environments, it can lead to catastrophic gear failure.
A few measures to consider include:
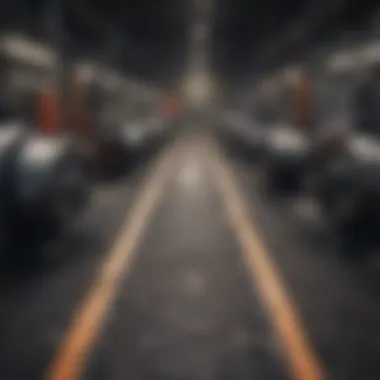
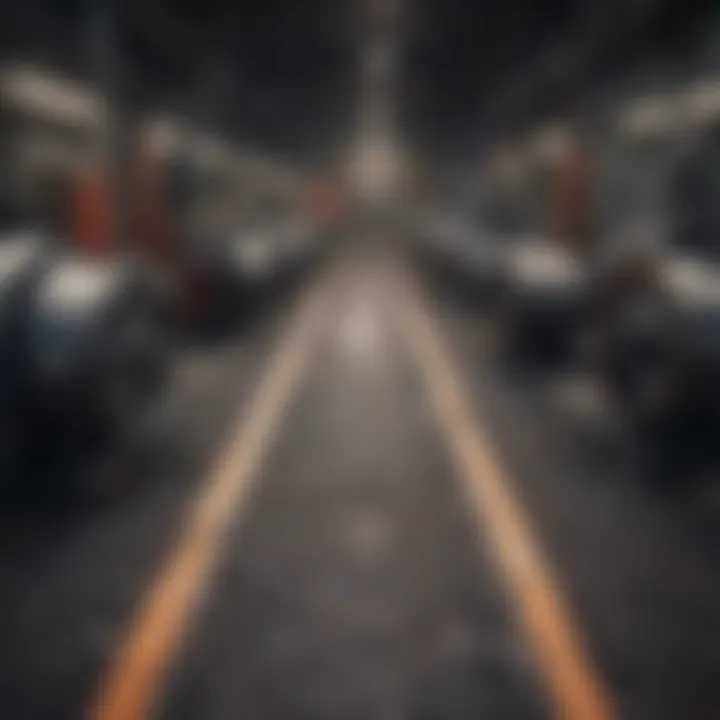
- Thermal shields: Incorporating external protective layers to reflect heat can help maintain optimal temperatures.
- Material selection: Certain grades of polypropylene have been engineered to withstand higher temperatures—choosing the right grade can mitigate many risks.
Design Limitations
Despite their many advantages, polypropylene gears aren’t always suitable for complex designs. Their limitations in machining and structural integrity can restrict creativity in custom gear systems. Specifically, intricate features such as undercuts or fine details may be challenging to achieve without compromising strength.
This limitation can lead to a few notable considerations:
- Prototyping: Before committing to full production, prototyping using 3D printing allows for adjustments and findings of better designs.
- Collaboration with designers: Teaming up with engineers who understand both the material and design can facilitate better outcomes, ensuring that the final product meets operational needs without compromising safety.
In summary, while polypropylene gears present attractive benefits such as light weight and chemical resistance, their challenges, particularly in high-load applications, temperature sensitivity, and design constraints, require careful consideration. Addressing these challenges effectively can pave the way for successful applications, making the most of polypropylene's advantages.
Future Trends in Polypropylene Gears
Understanding future trends in polypropylene gears is crucial, not just for engineers and designers but also for industries leaning towards sustainability and efficiency. As we look ahead, there are several elements to consider that can enhance the performance and applicability of polypropylene gears. With the rapid pace of technological advancement, it becomes essential to note how material properties can transform, ushering in innovations that reshape industry standards.
Advancements in Material Engineering
Material engineering is on the cusp of breakthroughs that may redefine how polypropylene gears are designed and utilized. One area of focus is the improvement of composite materials. By blending polypropylene with other fibers or fillers, engineers can enhance the gear's strength and thermal resistance, making them suitable for high-stress applications. This means less wear and tear, and longer lifespans for gears under challenging conditions.
Moreover, the introduction of smart materials—those that react to environmental changes—can also find substantial application in gear production. These materials can optimize performance dynamically based on the load and speed conditions they experience in real-time. Think of it as a responsive gear that adjusts itself to minimize friction and power loss.
Recycling and Sustainability
Recycling is becoming increasingly important as industries awaken to their environmental responsibilities. Polypropylene itself is a relatively easy material to recycle. However, moving forward, innovative recycling methods are necessary to reclaim gears more effectively. Techniques such as advanced mechanical recycling methods and chemical recycling could play pivotal roles in reducing waste.
The circular economy model places a spotlight on recovering materials efficiently with minimal energy expense, hence recycling polypropylene gears could not only minimize landfill waste but can also create economic opportunities in the long run. Investing in R&D for recycling technologies may offer significant dividends, promoting a greener pathway for production.
"The evolution of materials will not only enhance the functionality of polypropylene gears but also encourage sustainability practices imperative for the future."
In addition to recycling, there is also a significant trend towards designing for disassembly. This means creating gear assemblies that can be easily taken apart and reassembled using polypropylene gears. Such designs facilitate repairs and upgrades, ultimately prolonging the lifecycle of the equipment and mitigating the environmental footprint.
The integration of these advancements presents benefits like reduced production costs, improved energy efficiency, and major strides toward sustainable practices. As companies scramble to adapt to a landscape increasingly focused on eco-friendliness, keeping an eye on these trends can lead the way toward a more innovative future in the use of polypropylene gears.
Comparative Analysis with Other Materials
In the realm of gears, the choice of material can dramatically influence performance, durability, and cost efficiency. Understanding how polypropylene gears stack up against other materials is crucial for engineers and designers who want to make informed decisions. This section serves as a comparative analysis, dissecting the benefits and drawbacks of polypropylene gear systems alongside alternatives like polyethylene and metals. Such an examination not only gives context to polypropylene’s unique advantages but also highlights where it might fall short compared to its counterparts.
Polyethylene Gears
Polyethylene gears are often considered as a close alternative to polypropylene. They share several similarities, such as low density and good chemical resistance. Here are some key points of comparison:
- Flexibility: Polyethylene gears are known for being slightly more flexible at lower temperatures. This can be beneficial in applications where some give is required, but it may also lead to wear issues over time in high-stress environments.
- Impact Resistance: Polyethylene can handle shocks better, making it suitable for applications involving sudden impacts.
- Cost: Generally, polyethylene materials can be less expensive. However, the pricing variety can depend on the specific formulation and applications required in construction.
- Thermal Stability: Polypropylene gears tend to maintain their integrity better in higher temperature environments, outshining polyethylene in this regard. When put under prolonged heat exposure, polyethylene may degrade more quickly.
Key Insight: While polyethylene gears might excel under specific conditions, polypropylene garners an edge in thermal stability and weight, making them more suitable for high-performance applications.
Metallic Gears
When comparing polypropylene gears to metallic options such as aluminum or steel, the contrasts are even starker. Metallic gears have been a staple in engineering for decades, but they come with their own set of challenges.
- Strength: Metallic gears often boast superior load-bearing capabilities. They're generally chosen for heavy-duty applications, like in automotive and industrial machinery, where endurance is critical.
- Durability: Corrosion and wear may lessen the lifespan of metallic gears, requiring more maintenance than their polypropylene counterparts, especially in harsh environments.
- Weight: A significant advantage of polypropylene lies in its lightweight nature. This can be a game-changer in applications where reducing weight is of the essence, such as in drones or lightweight machinery.
- Cost and Ease of Production: Polypropylene gears can be less expensive to manufacture than metallic ones, particularly when considering techniques like injection molding which can lead to a faster and more efficient production cycle.
- Noise Reduction: Polypropylene gears tend to operate more quietly than their metallic counterparts, an attractive feature for applications in consumer products and automotive components.
In essence, while metallic gears may provide unmatched strength and durability for heavy loads, polypropylene gears shine where lightweight, noise reduction, and chemical resistance are prioritized.
As engineering evolves, understanding these comparisons helps professionals choose the right components for their applications. It’s essential to evaluate not just the immediate benefits but also the implications for performance, maintenance, and overall design.
Culmination
The discussion around polypropylene gears is particularly relevant in today’s engineering landscape. Throughout this article, we've peeled back the layers on not just the material's intrinsic properties, but also its far-reaching implications across various industries. Polypropylene, with its lightweight profile, chemical resistance, and specialized manufacturing capabilities, serves as a cornerstone for innovative engineering solutions.
Summary of Key Points
In anticipating the future of these gears, it's essential to highlight several key points:
- Versatility: Polypropylene gears find applications in a range of sectors from automotive functions to consumer products, proving their flexibility.
- Green Potential: The discussion about recycling and sustainability resounds loudly in our current environmental climate. Understanding the life cycle of polypropylene gears opens avenues for eco-friendly practices.
- Technical Challenges: High loading scenarios and temperature sensitivity pose challenges but also present interesting opportunities for engineers.
Thus, the importance of understanding polypropylene gears cannot be overstated; they embody an intersection of practicality and innovation.
The Future of Polypropylene Gears
Looking ahead, we can anticipate even more advancements in polypropylene gear technology. The ongoing progress in material engineering indicates smarter, more robust formulations of polypropylene. This may help address some of the existing limitations regarding load-bearing capacities and thermal thresholds.
Moreover, the industry's push towards sustainable solutions is driving research into recycling techniques. Enhancing methods for recycling these gears not only supports global sustainability targets but also could reshape material selection processes.
As industries adapt to these innovations, the role of polypropylene gears will likely evolve. They may not only retain their place in traditional applications but also expand into previously uncharted territories. The dialogue surrounding these gears remains a relevant topic, instilling curiosity and fostering continuous exploration amongst professionals and scholars alike.
"The journey of innovation is often paved with materials that can stand the test of time, adaptability, and sustainability."
In summary, the landscape of polypropylene gears is vibrant and full of opportunities. Understanding their potential can lead to breakthroughs in various fields, making it crucial for those in engineering and material science to keep an eye on what lies ahead.