Innovations in Prefabricated Construction Materials
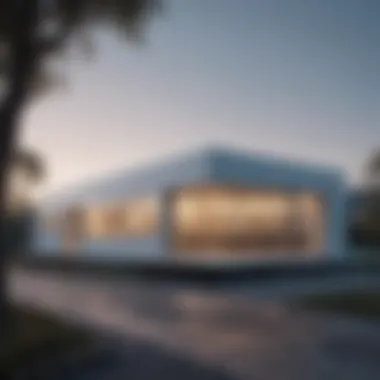
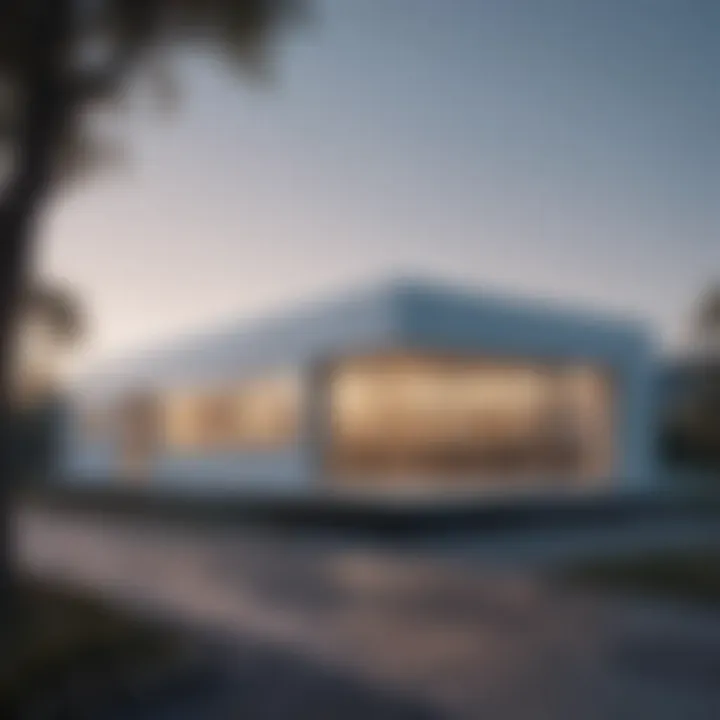
Intro
Prefabricated construction materials represent a significant shift in the building industry, promising enhanced efficiency, sustainability, and adaptability. Rooted in the principles of off-site construction, these materials are produced in controlled environments before being transported to the construction site. This article aims to dissect the evolution, types, and implications of prefabricated materials, critical for understanding their rising popularity.
The exploration of prefabricated construction materials intersects with broader discussions about sustainable architecture and modern engineering solutions. As urbanization accelerates and the demand for rapid building techniques increases, prefabrication has gained traction among various stakeholders including builders, architects, and engineers. Each of these groups contributes to the discourse around the efficiency and practicality of prefabricated elements.
Furthermore, technological advancements have facilitated innovations in this field, transforming traditional practices. Such innovations include improvements in manufacturing processes, which aim to minimize waste while maximizing quality. Understanding the journey of prefabricated materials—from initial conception to current applications—helps illuminate their potential future in the construction ecosystem.
In this context, we will delve into multiple aspects of prefabricated construction materials, offering insights into their diverse applications and the challenges they face. This exploration will serve as a valuable resource for students, researchers, and professionals keen on grasping the fundamentals and future trends within this dynamic sector.
Prologue to Prefabricated Construction Materials
Prefabricated construction materials have transformed the landscape of the building industry. Understanding these materials is essential for several reasons. First, they offer a practical response to the increasing demand for housing and infrastructure. As urbanization intensifies, the need for efficient construction methods rises. Prefabrication addresses this need by streamlining the building process.
Furthermore, prefabricated materials are inherently linked to advancements in technology. Innovations in manufacturing and design allow for improved speed and precision in construction. This can lead to significant cost savings, making these materials attractive to developers and builders alike.
Additionally, prefabrication plays a crucial role in sustainability. The construction industry is one of the largest contributors to waste and environmental degradation. By producing materials off-site, waste can be minimized, and energy consumption optimized. This important element of prefabricated construction further solidifies its value in modern building practices.
As we delve deeper into the specifics, we can appreciate the extensive impact of these materials on both the economy and environments. With these factors in mind, let’s define what prefabricated construction entails.
Defining Prefabricated Construction
Prefabricated construction refers to a practice where components of a building are manufactured in a factory setting and then transported to the construction site for assembly. This method contrasts with traditional building techniques, which typically involve constructing structures entirely on-site. The prefabricated approach allows for greater control over the production environment, which can result in better quality materials.
A variety of materials can be prefabricated, including walls, roofs, and entire structural systems. These components are often designed to fit together seamlessly, reducing the time required for assembly on-site. The efficiency of this method also allows for more accurate budgeting and scheduling, important factors in any construction project.
Historical Context and Evolution
The concept of prefabrication is not new. Its roots can be traced back to the Roman Empire, where standardization became a focus to streamline the construction process. However, the modern interpretation of prefabrication gained traction in the mid-20th century. Post World War II, there was a significant demand for rapid housing solutions. This need led to the rise of prefabricated systems in various countries.
As technology advanced, the manufacturing processes for prefabricated materials also evolved. The introduction of new materials and methods has made these systems more versatile and adaptable. Today, prefabricated construction is not only a means of solving housing shortages but also a method favored for its ability to reduce construction timelines and costs significantly.
"Prefabricated construction materials signify a shift towards more efficient and sustainable building practices, reflecting broader trends in technology and environmental awareness."
As we explore further sections, we will examine the specific types of prefabricated materials available, their manufacturing processes, and the benefits they provide in construction.
Types of Prefabricated Materials
Understanding the different types of prefabricated materials is essential for anyone looking to grasp the full scope of this construction method. Each type offers unique benefits and applications, making them suitable for various projects. By identifying the specific characteristics and uses of these materials, stakeholders can make informed decisions potentally enhancing construction efficiency and effectiveness.
Modular Systems
Modular systems consist of pre-manufactured sections or modules. These are typically constructed off-site and then transported to the construction site for assembly. This approach allows for quick installation and reduced on-site labor requirements. One significant advantage is the potential for customization; these modules can be designed to meet specific client needs while maintaining structural integrity and aesthetic appeal.
In addition, modular systems often incorporate sustainable practices, such as using recycled materials. This eco-conscious design contributes to a reduced environmental footprint of the overall project. The flexibility to expand or modify these systems without significant disruptions to the existing structure is also a key benefit.
Panelized Components
Panelized components refer to wall, floor, or roof panels that are manufactured in a factory setting. They can be made of various materials, including wood, metal, or composites. Panelized construction emphasizes speed and accuracy, allowing for a seamless fit during assembly. As a result, there is often less waste generated compared to traditional building methods.
With the use of pre-insulated panels, energy efficiency can also be significantly enhanced. These components can lead to improved thermal performance, ultimately reducing heating and cooling costs. Furthermore, panelized construction can support a variety of architectural designs, making it a versatile option for different types of buildings.
Prefabricated Concrete
Prefabricated concrete involves the casting of concrete components in a controlled factory environment before transporting them to the construction site. This method often results in higher quality products compared to those cast on-site, as the controlled conditions allow for precise mixing and curing. Items like beams, walls, and slabs can be efficiently produced and easily assembled.
Additionally, using precast concrete leads to significant time savings during the fitting stage of construction. It can enhance structural durability and is best suited for buildings that demand high strength and resilience. Prefabricated concrete also benefits from lower maintenance needs over time.
Steel and Other Structural Materials
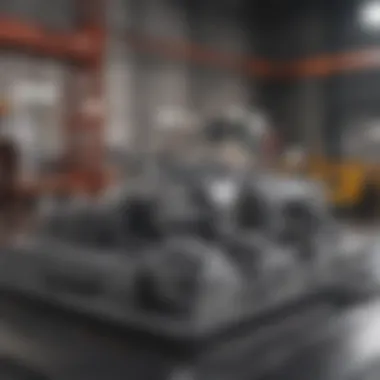
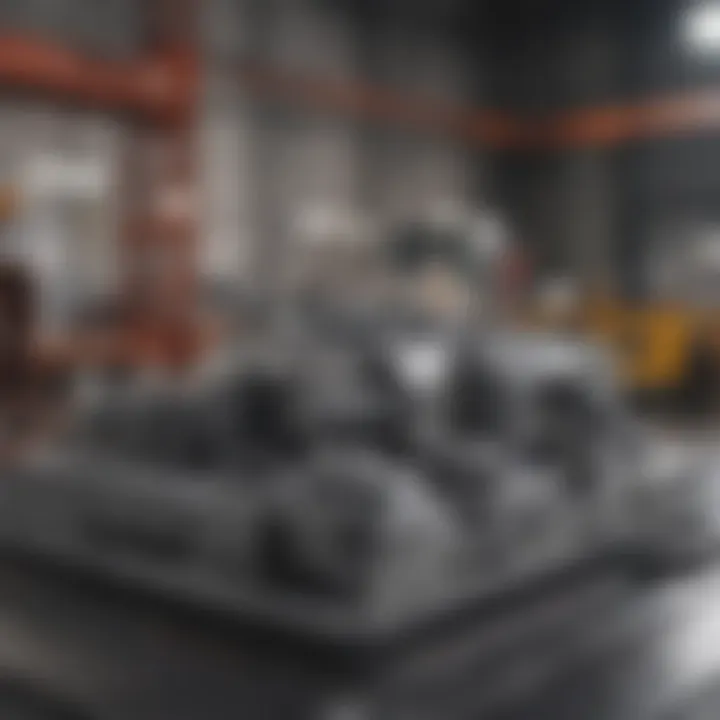
Steel has become a popular choice in prefabricated construction due to its strength and flexibility. Components such as beams, columns, and trusses can be pre-manufactured and assembled on-site. The use of steel allows for the creation of larger, open spaces within buildings, contributing to modern architecture's aesthetic needs.
Other materials, like cross-laminated timber, are also gaining traction. They combine sustainable characteristics with strength, appealing to environmentally conscious developers. Steel and wood prefabricated materials not only expedite construction timelines but also enhance overall project efficiency.
The right choice of prefabricated materials can influence both the cost and quality of construction significantly.
Understanding the different types of prefabricated materials provides invaluable insight into their potential applications. With a clear grasp of each option, architects, builders, and clients can collaborate more effectively to meet project goals.
Manufacturing Processes
The field of prefabricated construction relies significantly on manufacturing processes. These processes not only affect the overall quality and efficiency of construction materials but also contribute to the sustainability goals of the industry. Focusing on the way materials are produced helps identify advantages such as cost reduction, time efficiency, and improved quality control. A well-optimized manufacturing process allows for consistent repetition and accuracy, leading to fewer errors during assembly on site. This section delves into critical components of these processes, examining factory design and workflow, quality control procedures, and current innovations in manufacturing technology.
Factory Design and Workflow
An efficient factory design is crucial for the successful prefabrication of construction materials. The layout of the factory determines how materials flow from one stage of production to the next. A streamlined workflow is essential in minimizing waste and maximizing productivity. Factors such as equipment placement, worker accessibility, and material storage can greatly impact overall efficiency.
In a prefabricated environment, modularity is often key. Factories are designed to facilitate the assembly of modules off-site, which are then transported to construction sites. This requires precise logistics and planning to ensure that materials arrive correctly and on schedule. Effective communication systems and digital management tools play a prominent role in coordinating these activities.
Quality Control Procedures
Quality control is another essential facet of the manufacturing processes in prefabrication. Successful implementation of quality control procedures ensures that materials meet specified standards before reaching the construction site. These procedures can include rigorous testing protocols, periodic inspections, and adherence to established guidelines.
One prevalent practice involves the use of Statistical Process Control (SPC), which monitors production processes through data collection and analysis. This approach allows manufacturers to identify deviations from quality standards early, enabling corrective actions before products leave the factory. Emphasizing quality control not only enhances the reputation of manufacturers but also reduces costs associated with rework and material waste.
Innovations in Manufacturing Technology
The prefabrication sector witnesses ongoing innovations in manufacturing technology. Advances in automation, robotics, and digital modeling have enhanced production capabilities. For instance, Building Information Modeling (BIM) allows for detailed planning and visualization of structures before actual construction begins. This technology empowers manufacturers to foresee and tackle potential challenges early in the process.
Additionally, the application of 3D printing technology in prefabricated construction offers exciting possibilities. It allows for the creation of intricate components with minimal material waste. Innovations like these accelerate the production cycle and lead to unique design opportunities.
"Manufacturing processes in prefabricated construction not only streamline workflows but also enhance sustainability and efficiency across the industry."
In summary, a thorough understanding of manufacturing processes enhances the effectiveness of prefabricated construction materials. The elements of factory design, quality control, and technological advancements create a framework that supports efficient and sustainable construction practices.
Benefits of Prefabricated Materials
Prefabricated materials offer a range of advantages that influence the construction industry positively. The trend toward these materials is not just a temporary phase; it is backed by substantial evidence of their effectiveness. Through various angles, prefabrication provides many benefits, which are critical to consider. They address critical needs, such as cost, time, sustainability, and quality. Understanding these benefits can aid in making informed decisions about construction methods and materials.
Cost Efficiency
Cost efficiency is a foremost reason why stakeholders choose prefabricated materials. By using prefabrication, projects can save significant money compared to traditional methods. In essence, factory production allows for bulk purchasing of materials, reducing costs. Furthermore, the time saved during construction translates to less labor expenditure. In traditional building, unexpected delays often lead to increased budgets. However, with prefabricated components, timelines are much more predictable.
Moreover, many prefabricated systems are designed for easy assembly. This reduces labor costs on-site and minimizes errors that can occur during construction.
"Cost efficiency in prefabricated construction can reduce overall project budgets by up to 20%, making it an attractive option for investors and developers."
Time Savings
Timelines in construction projects can be significantly shortened through the adoption of prefabricated materials. With components manufactured off-site, the building process does not have to wait for every stage to be completed before moving forward. Different tasks can happen simultaneously, such as site preparation and assembly of modules.
The decrease in construction time results not only from faster building processes but also from fewer weather-related delays. Traditional raw materials are often affected by seasons, while prefabricated materials can be produced regardless of external conditions.
Sustainability and Waste Reduction
Sustainability continues to grow as a pivotal focus in construction, with prefabricated materials playing a critical role. They help in reducing waste produced during construction. In conventional building, much raw material is discarded or damaged, leading to a substantial environmental footprint.
On the other hand, controlled factory environments allow for precise cutting, creating minimal waste in the manufacturing process. Also, many companies are adopting sustainable practices by using reused or recycled materials.
Using prefabricated systems not only lowers waste but also promotes energy efficiency. Their design often allows for better insulation and energy use, contributing to lower operating costs and a reduced carbon footprint throughout the building's lifespan.
Enhanced Quality and Durability
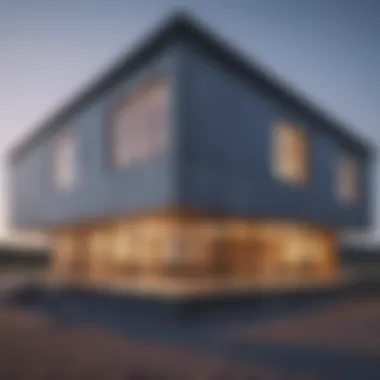
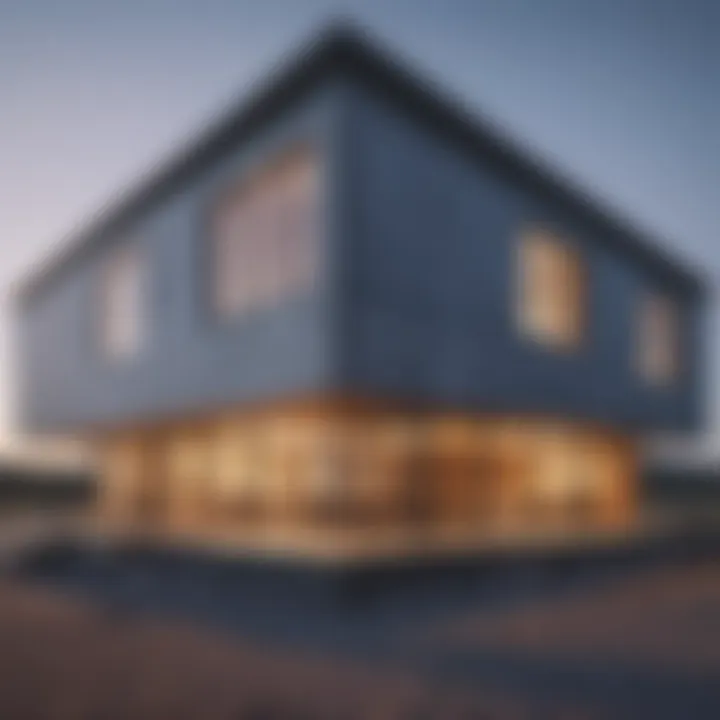
Quality control is an essential aspect of construction, and prefabrication often excels in this regard. Factory settings allow for rigorous quality assurance and inspections that are challenging to implement on-site where conditions vary. Each piece of prefabricated material is produced under controlled conditions, ensuring consistency and reliability.
Furthermore, prefabricated structures are often more durable than traditional methods. They are designed to withstand specific conditions, enhancing longevity. As a result, building owners may find they incur lower costs over time due to less frequent repairs or replacements.
Challenges and Limitations
Understanding the challenges and limitations of prefabricated construction materials is crucial for stakeholders in this field. Such awareness allows for informed decision-making and strategic planning. Despite the advantages of prefabrication, several elements can hinder its adoption and effectiveness. Addressing these issues is essential to elevate prefabrication from its current status to a more mainstream approach in construction.
Logistical Issues
Logistical concerns are one of the primary hurdles in the adoption of prefabricated materials. The transportation of large components can become problematic, especially in urban areas with restricted access.
- Transportation Costs: The cost associated with transporting prefabricated modules can sometimes outweigh the potential savings in production. Tight delivery schedules further complicate logistics.
- Storage Requirements: Large components require adequate storage space before assembly. If not managed properly, this can lead to delays and additional costs.
- Site Coordination: Effective synchronization between factories and construction sites is vital. Poor communication can result in misalignments, requiring on-site adjustments that may negate the benefits of prefabrication.
To mitigate these logistics issues, a robust project management strategy is paramount. Collaboration with experienced logistics providers can enhance efficiency and streamline the entire process.
Design Flexibility Concerns
Another challenge related to prefabricated construction is design flexibility. While prefabrication allows for rapid assembly, it can limit customizations in a project.
- Standardization Limitations: Many prefabricated components are standardized, which can stifle creative architectural designs. This may lead to buildings that lack uniqueness.
- Modification Difficulties: Once components are manufactured, altering their design can be complex and costly. Any revisions might impact the whole production line.
- Client Expectations: Clients often have specific visions for their projects. If prefabrication restricts these visions, it can lead to dissatisfaction and perception issues regarding the technology.
To address concerns about design flexibility, engaging architects and designers early in the process is critical. Utilizing modular designs that allow for some customization can also help keep client expectations in line.
Market Perceptions and Acceptance
Market perception plays a vital role in the pace of change towards adopting prefabricated construction materials. Generally, the construction industry can be resistant to change due to traditional practices.
- Public Misunderstandings: Many consumers still associate prefabricated structures with low quality or temporary constructions. Educating the market is essential to alter this perspective.
- Industry Resistance: Established firms may hesitate to invest in new technologies, fearing that it could disrupt their current business models.
- Regulatory Challenges: In some regions, regulations suit traditional building methods better than prefabricated ones, which can hamper acceptance and growth.
"Changing market perceptions requires ongoing education and effective communication focusing on the benefits of prefabrication, such as efficiency and sustainability."
For prefabrication to gain traction, the industry must work collectively to share successful case studies and educate all stakeholders, including clients, regulatory bodies, and construction workers.
Prefabrication and Sustainability
The convergence of prefabrication and sustainability is increasingly significant in the context of modern construction. This section discusses how prefabrication can align with sustainable building practices. As construction continues to evolve, its environmental impact becomes more scrutinized. This heightened awareness necessitates innovative approaches, and prefabrication emerges as a viable solution.
Prefabricated construction materials can reduce waste and improve resource efficiency. This is essential when considering the construction industry's traditionally high levels of waste. Building components manufactured off-site often result in less pollution and lower energy consumption during production. Not only does this contribute to sustainability, but it also enhances overall project efficiency.
"Utilizing prefabrication in construction markedly reduces the ecological footprint of building projects."
Environmental Impact Considerations
The environmental impact of construction is substantial, incorporating carbon emissions, resource depletion, and ecological disturbance. Prefabrication addresses these issues effectively. One major advantage is the ability to manufacture components under controlled conditions. This setting allows for greater accuracy and less waste than traditional building sites. When components are made in factories, the management of materials becomes easier, permitting recycling and better use of recycled materials.
Additionally, reducing the time spent on-site lessens the disturbance to the environment. For example, ground disruption is minimized, which aids in preserving local ecosystems. The efficiency gained from prefabricated construction can lead to a dramatic decrease in carbon emissions associated with transportation and logistics.
Energy Efficiency of Prefabricated Structures
Energy efficiency is another critical area where prefabrication showcases its benefits. Prefabricated structures are often designed with energy conservation in mind. This includes features like enhanced insulation and optimized architectural designs that maximize natural light. These designs can greatly reduce the energy consumption of a building over its lifecycle.
In many instances, prefabricated components are produced with energy-efficient materials and technologies. For example, the integration of sustainable insulation materials within wall panels can significantly minimize heating and cooling needs.
By implementing advanced manufacturing techniques, prefabrication can also facilitate the installation of renewable energy systems, such as solar panels and green roofs, into buildings. This consideration not only enhances efficiency but also aligns with broader goals of increasing the use of renewable energy in the construction sector.
In summary, the integration of prefabrication and sustainability reflects a growing realization of the need for environmentally conscious practices in construction. The focus on reducing carbon footprints, managing resources more effectively, and enhancing energy efficiency positions prefabricated construction as a key player in the future of sustainable building.
Case Studies in Prefabrication
In recent years, the field of prefabricated construction has gained significant attention, and case studies serve as a vital tool in understanding its practical applications. These real-world examples not only highlight the benefits of prefabrication but also offer insights into challenges and lessons learned along the way. By examining various case studies in residential, commercial, and public infrastructure projects, stakeholders can grasp the tangible impacts of prefabricated materials and take informed decisions that enhance construction practices.
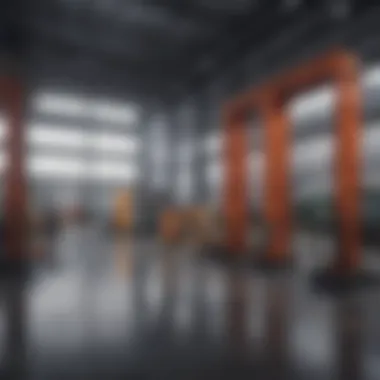
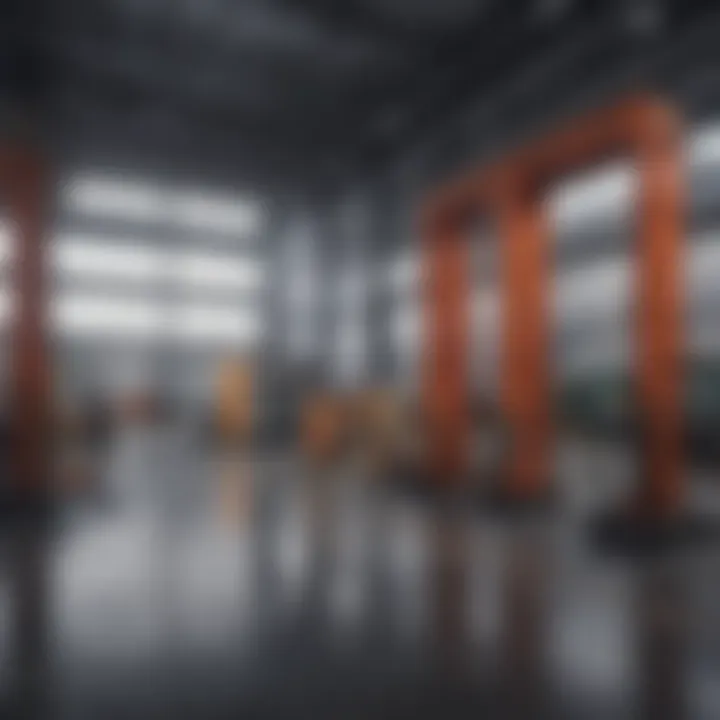
Residential Applications
Residential applications of prefabricated construction materials often demonstrate efficiency and quality in building homes. One prominent example is the use of modular homes, which are manufactured in sections and assembled on-site. This approach significantly reduces construction time, allowing homeowners to move in sooner than traditional building methods permit. A notable project is the development of Katerra, which employed a comprehensive off-site manufacturing strategy to construct multifamily housing efficiently.
These homes offer various advantages like lower energy consumption and reduced waste. Prefabrication minimizes on-site errors, which can be common in conventional builds. Additionally, residents benefit from enhanced design flexibility as manufacturers can adapt modules to specific needs or preferences.
Commercial Developments
Commercial projects are also increasingly leveraging prefabrication techniques. One case study that stands out is the Virgin Hotel in New York City, which utilized off-site construction for its hotel rooms. By modularizing the guest suites, the project not only achieved significant time savings but also ensured a level of quality that sets it apart in the competitive hospitality market.
The efficiency of prefabricated construction allows buildings to be completed with less disruption to surrounding businesses and communities. Furthermore, the predictability of costs associated with prefabricated materials minimizes budget overruns, a common issue in traditional commercial construction projects.
Public Infrastructure Projects
The application of prefabricated materials in public infrastructure projects such as bridges and schools has shown promising results. A notable example is the I-35W St. Anthony Falls Bridge in Minneapolis, where precast concrete elements were used, speeding up the construction process and reducing traffic disruptions during the building phase.
These projects underline the advantage of quick assembly while maintaining structural integrity. When applied in schools, prefabricated classrooms can be erected swiftly, addressing urgent housing requirements for students in a timely manner. It allows government bodies to allocate resources more effectively under tight timelines.
Utilizing case studies across these varied sectors reinforces the understanding that prefabrication can address contemporary challenges in construction while adhering to cost and time efficiency goals. Integrating insights from these projects into future developments will empower architects, builders, and policymakers towards a more innovative approach to construction.
Future Directions in Prefabricated Construction
The landscape of prefabricated construction is continuously evolving, reflective of advancements in technology, shifts in regulatory frameworks, and the dynamic marketplace. Understanding the future directions in this field is crucial for stakeholders keen on optimizing their construction processes and enhancing sustainability.
Emerging Technologies
Recent innovations are altering the way prefabricated materials are manufactured and integrated into construction practices. Technologies such as 3D printing and advanced robotics are increasingly adopted in factory settings. For instance, 3D printing enables the creation of complex designs with reduced material waste. Robotic assembly lines enhance precision and speed. As these technologies become mainstream, the potential for customization and efficiency increases profoundly.
Furthermore, building information modeling (BIM) is transforming design processes. BIM allows for digital visualization of projects before any physical work begins. This enhances collaboration among teams and leads to more organized workflows. The integration of Artificial Intelligence (AI) in project management promises further improvements in predictive analytics and resource optimization, which can mitigate risks commonly faced in construction projects.
Regulatory Changes and Their Impact
Regulatory frameworks are adapting to the changing paradigms of construction. Updated building codes and standards increasingly recognize the benefits of prefabricated materials. This shift enhances market acceptance and creates greater demand. Regulations that promote sustainable construction practices will also likely influence prefabrication techniques. For example, incentives for using eco-friendly materials could drive growth in this sector.
Stakeholders must stay informed about these regulatory changes. They can influence project approvals, funding availability, and compliance requirements. Adhering to a more rigorous regulatory landscape will require prefabricated construction companies to implement robust quality control measures and strategic planning approaches.
Market Trends to Watch
In the coming years, certain market trends will shape the prefabricated construction industry. One significant trend is the growing interest in sustainable building practices. As clients and developers increasingly demand lower carbon footprints, prefabrication can address these concerns through enhanced energy efficiency and reduced waste.
Another trend is the movement towards modular construction. This approach allows for greater flexibility in design and quicker assembly times. As urban areas expand, there is a rising demand for housing solutions that prefabrication can readily fulfill.
Key trends to monitor include:
- Increased collaboration between builders and technologists
- Emerging materials that are eco-friendly and cost-effective
- Global shifts towards urbanization demanding innovative construction solutions
The focus on these trends not only provides insight into future possibilities for prefabrication but also emphasizes its role in shaping the modern construction landscape.
Culmination
The conclusion section is pivotal in encapsulating the essence of the discussions held throughout this article. It serves as the synthesis of key insights, enabling the reader to grasp the significance of prefabricated construction materials within the broader context of modern building practices. The synthesis of ideas here highlights not only the advancements made in prefabrication but also elucidates the driving forces behind its increased adoption.
Summarizing Key Insights
In reviewing the various sections of the article, it is clear that prefabricated construction materials offer numerous advantages. These include cost-efficiency, significant time savings, and enhanced sustainability. The historical context outlined shows that while prefabrication is not a new concept, the current technological advancements have transformed its application. The modularity and adaptability of these materials aid in addressing the challenges observing in traditional construction methods. Moreover, a consistent focus on quality control during the manufacturing processes ensures that the end products meet high standards ready for real-world applications.
"Prefabrication bridges the gap between efficiency and sustainability in construction, making it a compelling solution for future needs."
The case studies highlighted showcase successful implementations across various sectors, ranging from residential developments to public infrastructure projects. Such examples solidify the notion that prefabricated construction is a viable alternative that provides multiple benefits. Furthermore, understanding the challenges and limitations acknowledges areas that need attention to leverage the full potential of this construction method.
The Road Ahead for Prefabrication
Looking forward, the future of prefabricated construction holds promising potential. As new technologies emerge, the integration of automation and smart technologies into prefabrication processes can drive further efficiencies. Regulatory changes may also foster an environment for innovation, allowing for flexibility and adaptation to modern construction needs.
Market trends suggest a growing acceptance of prefabrication within the construction industry. Increased public awareness regarding sustainability will further push for more environmentally-friendly practices in building. It is imperative for professionals within the field to stay informed about these trends and advancements, as they will shape the landscape of construction in the coming years.
In summation, the journey towards a more efficient, sustainable, and effective construction methodology is well underway. The insights from the exploration of prefabricated materials pave the way for a clearer understanding of both current capabilities and future directions. Building upon this foundation can lead to innovative practices that not only make construction practices more effective but also environmentally cognizant.