Fluid Mechanics Simulation: Principles and Applications
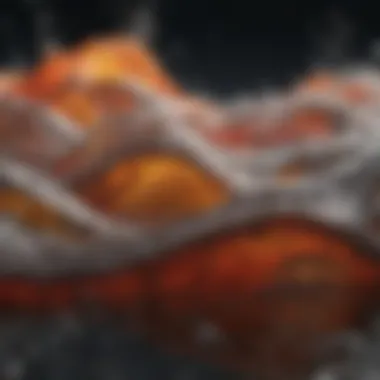
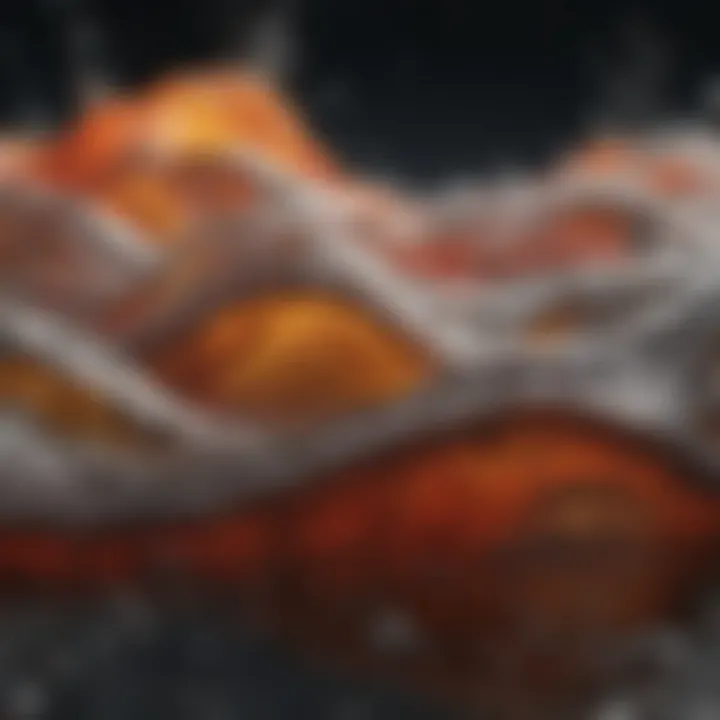
Intro
Fluid mechanics simulation is a crucial aspect of engineering and scientific research, particularly in the field of Computational Fluid Dynamics (CFD). This discipline allows for the detailed study of fluid behavior under various conditions, making it invaluable across multiple sectors like aerospace, automotive, and civil engineering. The simulation process provides insights that extend beyond theoretical understanding, enabling better design and optimization of systems that involve fluid flow.
The importance of fluid mechanics simulation stems from its ability to replicate real-world conditions in a controlled environment. This capability not only enhances predictability but also aids in developing innovative solutions to complex problems. By employing advanced computational techniques, professionals can visualize how fluids interact with different surfaces and forces under varied conditions. This understanding ultimately translates into improved efficiency and safety in engineering applications.
Fluid mechanics simulation occupies a central role in the advancement of technology. The combination of theoretical principles and practical applications forms a foundation for ongoing research and development. Understanding these principles allows engineers and researchers to create models that lead to significant improvements in performance and resource management. Furthermore, as industries evolve, the need for accurate simulations becomes increasingly crucial to stay competitive and meet regulatory standards.
In the sections that follow, this article will explore the essential principles underpinning fluid mechanics simulation, the methodologies utilized in these simulations, and the diverse applications that arise from effective CFD practices. A deeper dive into the research context will help illuminate the significance of continuous innovation in the realm of fluid mechanics.
Prolusion to Fluid Mechanics Simulation
Fluid mechanics simulation plays a critical role in modern engineering and science. It allows researchers and professionals to make informed decisions based on predictive models. This capability is especially beneficial in contexts where physical experiments can be costly or impractical. The simulation of fluid flows helps in understanding complex behaviors that may not be easily observable in real-life conditions. Furthermore, it supports innovation by streamlining design processes and optimizing system performance.
Definition and Importance
Fluid mechanics simulation refers to the computational techniques used to analyze and predict fluid behavior under various conditions. It encompasses both fluid dynamics and fluid statics, applying mathematical models to simulate how fluids interact with surfaces and other fluids. The importance of fluid mechanics simulation cannot be overstated; it fundamentally enhances our capacity to predict outcomes, refine product designs, and improve safety measures in different engineering applications.
This simulation addresses the behavior of fluids, which includes intricate factors like viscosity, density, and flow rates. The methods employed can reduce trial-and-error approaches, leading to more efficient designs across industries such as aerospace, automotive, and civil engineering. For students and professionals, mastering fluid mechanics simulation is crucial for advancing technologies and methodologies in their respective fields.
Historical Context
The roots of fluid mechanics can be traced back to ancient civilizations. Archimedes, in the third century BC, laid foundational principles still relevant today. However, the advent of modern fluid dynamics began in the 18th century with figures such as Daniel Bernoulli and Leonhard Euler. The formulation of the Navier-Stokes equations in the 19th century marked a significant development, providing the mathematical framework for examining viscous fluid flows.
With the progress of computing in the 20th century, fluid mechanics simulation transformed dramatically. The introduction of numerical methods enabled complex problems to be analyzed more efficiently than physical experiments alone. Today, computational fluid dynamics (CFD) has become an indispensable tool in the design and analysis of fluid systems.
As technology continues to evolve, the evolution of simulation software continues to outpace traditional methods. The increasing computational power offers unprecedented opportunities for more detailed and accurate simulations, making fluid mechanics simulation a central pillar in current engineering practices.
Fundamental Concepts of Fluid Mechanics
Understanding the fundamental concepts of fluid mechanics is essential in grasping the dynamics and behaviors of fluids in various conditions. These concepts provide the basis for advanced studies and applications in engineering and sciences. Crucial aspects such as the properties of fluids and the behavior under static and dynamic conditions are pivotal for successful simulations and analyses. Having a solid foundation in these principles can lead to better designs, optimizations, and predictions in relevant fields.
Basic Properties of Fluids
Viscosity
Viscosity is a measure of a fluid's resistance to deformation or flow. A specific aspect of viscosity is its significance in predicting how fluid flows under different conditions. This characteristic influences many applications, from lubrication in machinery to blood flow in biological systems. A beneficial property of viscosity, particularly in simulation, is its role in describing how fluids interact with surfaces and each other. The unique feature of viscosity is its temperature dependence; as temperature increases, viscosity usually decreases, affecting fluid behavior considerably. However, high-viscosity fluids can pose challenges in terms of computational cost and complexity of flow patterns.
Density
Density is defined as the mass per unit volume of a fluid. It plays a crucial role in buoyancy, stability, and overall fluid behavior. The key characteristic of density is that it influences how fluids stratify when mixed. This is a beneficial attribute in simulations where different materials interact, like oil and water. A unique aspect of density is its variability with temperature and pressure, leading to different flow patterns under different conditions. Accurate modeling of density is essential, as miscalculations can lead to incorrect predictions during simulations.
Pressure
Pressure in a fluid is the force exerted per unit area and is fundamental in both static and dynamic fluid situations. The specific aspect of pressure is its ability to change with depth in a fluid, a feature that is critical for understanding hydrostatic conditions. Pressure is a beneficial property for fluid simulations, as it allows for the calculation of fluid flow and responses to forces applied. The unique aspect of pressure is that it can transmit forces in all directions, affecting fluid movement and behavior comprehensively. It can also present challenges in simulations where rapidly changing pressures can lead to instabilities in results, thus requiring careful modeling and validation.
Fluid Statics and Dynamics
Hydrostatic Pressure
Hydrostatic pressure is the pressure exerted by a fluid at rest due to the weight of the fluid above it. This specific aspect is fundamental to the understanding of buoyancy and stability in fluids. A key characteristic of hydrostatic pressure is that it increases linearly with depth, which is advantageous for predictions related to submerged objects. The unique feature of hydrostatic pressure is its role in design considerations for underwater structures and systems, where knowing pressure at different depths is crucial. However, it can complicate certain computations when dynamic interactions are also involved, as transitioning from static to dynamic conditions often requires different approaches.
Conservation Laws

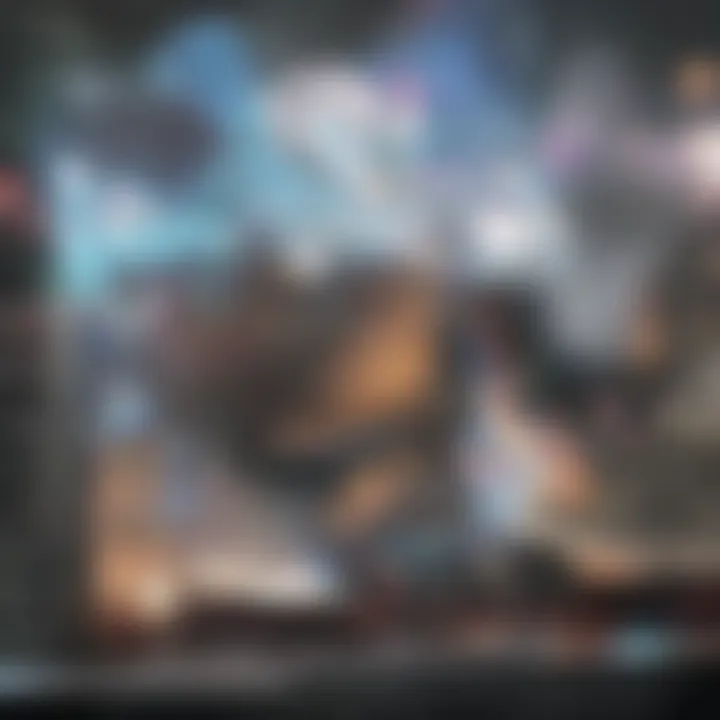
Conservation laws in fluid mechanics pertain to the fundamental principles that dictate fluid behavior, including conservation of mass, momentum, and energy. A specific aspect of these laws is their role in formulating mathematical models that simulate fluid behavior accurately. The key characteristic of conservation laws is their universality; they apply to all fluids regardless of conditions. They are beneficial in providing a framework for analyzing fluid flows and ensuring that simulations maintain realistic representations. A unique feature of these laws is their ability to simplify complex interactions through fundamental equations. However, adherence to conservation principles in turbulent flows can introduce complexities that require sophisticated modeling techniques.
Computational Fluid Dynamics (CFD)
Computational Fluid Dynamics plays a critical role in understanding fluid behavior through simulation. This complex technique merges mathematics, physics, and computer science to analyze fluid flows. Its significance is underscored by its applications across various fields, such as aerospace, automotive, and civil engineering. CFD helps in predicting fluid behavior under different conditions, allowing engineers to optimize designs before physical prototypes are created. The benefits of employing CFD include increased accuracy, reduced time for development, and cost efficiency, making it a vital tool in modern engineering.
Prelims to CFD
CFD is a specialized area that focuses on the numerical simulation of fluid dynamics. By breaking down continuous fluid flows into discrete elements, CFD can provide a detailed analysis of how fluids interact with surfaces and each other. This approach is particularly useful for solving complex equations that govern fluid motion, notably the Navier-Stokes equations. It enables researchers and engineers to visualize and predict fluid behavior in dynamic systems, which is vital for innovative design and troubleshooting.
CFD Methodologies
CFD methodologies encompass various techniques used to solve fluid dynamics problems. These methodologies are essential for achieving accurate results in simulations, and they form the backbone of CFD analysis. Let's examine a few notable ones:
Finite Volume Method
The Finite Volume Method (FVM) is a widely used approach in computational fluid dynamics. It focuses on the principles of conservation of mass, momentum, and energy within a control volume. One key characteristic of FVM is its ability to handle complex geometries and irregular grids effectively. This makes it a beneficial choice when simulating airflow around vehicles or structures. A unique feature of FVM is its inherent conservation property, ensuring that physical laws are maintained across each volume. However, it may require mesh refinement for highly detailed regions, which can increase computational costs.
Finite Element Method
The Finite Element Method (FEM) is another important methodology used in CFD, particularly for problems involving complex boundaries and structures. Its strength lies in its adaptability to various types of elements, allowing for flexibility in simulations. A key characteristic of FEM is its ability to provide precise solutions, particularly for solid mechanics and structural problems intertwined with fluid flows. A unique feature of FEM is its capability to model non-linear and time-dependent behavior, which is vital in real-world applications. Nevertheless, FEM can sometimes lead to longer computation times due to the complexity of its meshing requirements.
Mesh Generation Techniques
Mesh Generation Techniques are crucial for establishing the computational domain in CFD simulations. The quality of the mesh directly influences the accuracy and stability of the results. A key characteristic of these techniques is their ability to create grids that represent fluid domains accurately. This is particularly beneficial for simulating intricate geometries or turbulent flows. Several methods exist for mesh generation, including structured and unstructured meshing. Each has its own advantages; structured meshes generally offer simpler and faster calculations, while unstructured meshes provide greater flexibility for complex domains. However, improper mesh quality can lead to erroneous results, underscoring the importance of this step in simulation.
"A well-designed mesh can significantly enhance the accuracy and efficiency of a CFD simulation."
Mathematical Models in Fluid Simulation
Mathematical models are foundational to fluid mechanics simulations. They provide a structured way to represent the complex behaviors of fluids under different conditions. The importance lies in their ability to simplify the physical laws governing fluid behavior into a set of equations that can be solved computationally. The accuracy and reliability of a simulation heavily depend on the chosen mathematical models, hence underscoring their significance in this domain.
Models like the Navier-Stokes equations serve as the backbone of fluid dynamics. They describe how the velocity field of a fluid evolves over time. Understanding the specific equations involved enables engineers and scientists to predict how fluids will flow in various applications, from airplane wings to blood vessels.
Navier-Stokes Equations
The Navier-Stokes equations are a system of nonlinear partial differential equations. They describe the motion of viscous fluid substances. These equations are essential because they encapsulate the rules of conservation of mass, momentum, and energy in fluid flows. Solving the Navier-Stokes equations allows for insights into various fluid behaviors, which is crucial in both theoretical and applied fluid mechanics.
However, solving these equations can be challenging, especially in turbulent flow scenarios. Computational resources are often pushed to their limits. Despite these challenges, successful solutions lead to significant advancements in engineering design and predictions of fluid behavior in various systems.
Turbulence Modeling
When simulating fluid flows, turbulence is a significant factor that cannot be ignored. Turbulent flows are complex and chaotic, making them difficult to model accurately. Thus, specific turbulence models have been developed to tackle this complexity.
LES (Large Eddy Simulation)
Large Eddy Simulation (LES) focuses on capturing the large-scale structures of turbulent flows while modeling smaller scales. One of the key characteristics of LES is its ability to provide detailed spatial and temporal resolution of the turbulent flow. This level of detail makes LES a favored choice for many applications in engineering and research.
One unique feature of LES is that it allows for real-time analysis of turbulent flows, providing valuable insights into transient phenomena. The main advantage of LES lies in its balance between computational cost and accuracy. While it demands more computational power relative to simpler models, the trade-off often results in superior predictive capabilities, especially for flows with high Reynolds numbers. However, the drawbacks include the need for very fine meshes and longer computational time, which could be a limiting factor in various applications.
RANS (Reynolds-Averaged Navier-Stokes)
Reynolds-Averaged Navier-Stokes (RANS) model serves a different purpose in turbulence modeling compared to LES. RANS focuses on time-averaging the Navier-Stokes equations, which simplifies the complexity of turbulent flows. A key characteristic of RANS is its efficiency in computational resource usage, making it popular in practical engineering applications.
The unique feature of RANS is that it provides averaged results over time, making it less sensitive to transient fluctuations. However, while it is computationally cheaper, it sacrifices some accuracy for the sake of robustness in powerful industrial fluid simulations. RANS is suitable for many engineering tasks but may not capture all the intricacies of highly turbulent flows as well as LES.
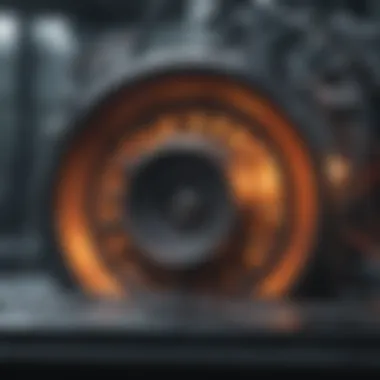
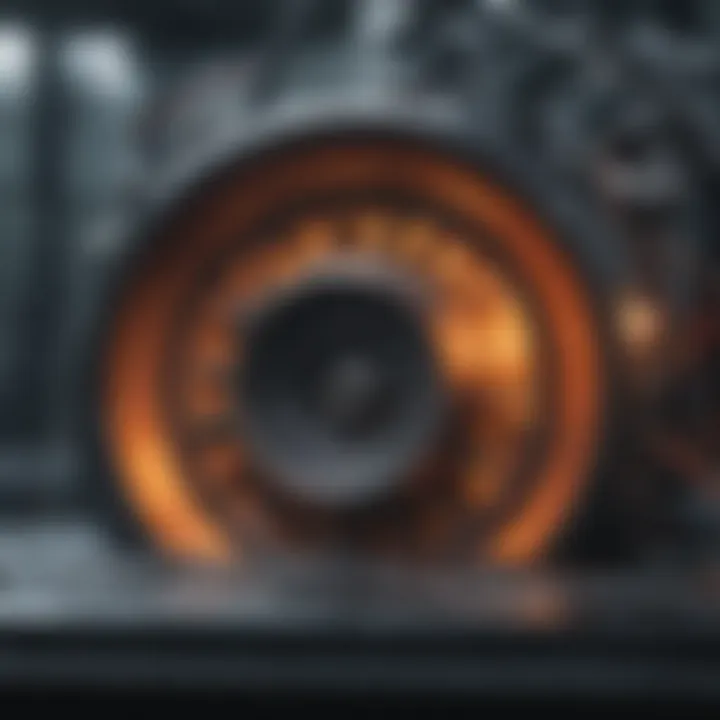
Overall, both LES and RANS have their places in fluid mechanics simulation. The choice between these models depends on the specific requirements of the project, such as the desired accuracy and the available computational resources.
Applications of Fluid Mechanics Simulation
Fluid mechanics simulation holds great significance in various sectors, enabling engineers and researchers to predict behavior, optimize designs, and enhance processes. The ability to simulate fluid flow leads to innovative solutions that can significantly improve efficiency and safety in varying applications. This section introduces key areas where fluid mechanics simulation plays a crucial role, namely aerospace, automotive, and civil engineering.
Aerospace Engineering
Aircraft Design
Aircraft design is a complex process that demands precision and innovation. Fluid mechanics simulations contribute to this aspect by allowing engineers to analyze airflow dynamics around an aircraft model. A primary goal is to minimize drag and enhance lift. This is especially important for fuel efficiency and overall performance. The key characteristic of aircraft design related to fluid mechanics is aerodynamics. Aerodynamics simulations help in understanding how different shapes and surfaces affect performance.
A beneficial factor in aircraft design is its ability to simulate real-world conditions before physical testing occurs. This saves both time and resources. However, one must be cautious about over-reliance on simulations alone, as real-world anomalies may differ from simulated environments.
Wind Tunnel Simulations
Wind tunnel simulations serve as an essential technique in studying aerodynamic properties. By using scaled models in controlled airflow environments, engineers can observe flow patterns and forces acting on these models. The key characteristic is the ability to visualize how an aircraft will interact with air at different velocities. This makes wind tunnel experiments a popular choice for validating simulation data.
A unique feature of wind tunnel simulations is that they provide direct comparison between theoretical predictions and empirical data. However, they can be costly and require significant setup time. Despite these challenges, they remain invaluable in the design and testing phases of aerospace projects.
Automotive Engineering
Drag Reduction Techniques
Drag reduction techniques are crucial in automotive engineering, particularly for enhancing vehicle performance and fuel economy. These techniques maximize the aerodynamic efficiency of vehicles, thus reducing air resistance. One key characteristic is the optimization of body shapes, which can be informed by fluid simulations.
These techniques are beneficial because they directly contribute to lower fuel consumption and improved speed. A unique feature is the incorporation of active aerodynamic systems that adjust based on vehicle speed. However, these systems can complicate vehicle design and may increase costs.
Cooling System Optimization
Cooling system optimization ensures an automotive engine operates at an efficient temperature to prevent overheating. Fluid mechanics simulation allows engineers to model coolant flow and improve the design of radiators and cooling pathways. A notable key characteristic of this application is its focus on thermal management under various driving conditions.
Optimization in this area is beneficial as it enhances engine performance and longevity. The unique aspect is the ability to model transient thermal behaviors, allowing for more accurate predictions. However, achieving the optimal configuration can demand extensive testing and modification.
Civil Engineering
Hydraulic Structures
Hydraulic structures, such as dams and levees, require careful design and implementation. Fluid mechanics simulation plays a role in predicting flow behaviors and potential erosion effects around these structures. A key characteristic is the modeling of flood scenarios and assessing how structures will hold up under various conditions. This understanding is beneficial for public safety and resource management.
A unique feature of hydraulic simulations is their ability to incorporate topographical data, enhancing the accuracy of predictions. Despite their advantages, hydraulic modeling can be data-intensive and may require significant computational resources.
Flood Modeling
Flood modeling simulates the impact of heavy rainfall or dam breaches on surrounding ecosystems and communities. It is essential for developing emergency response plans and understanding potential risks. The key characteristic of flood modeling is its predictive capability, which informs infrastructure and urban planning decisions.
This application is beneficial for risk assessment and mitigation strategies. The advanced simulations can showcase flood extents and velocities. However, flooding scenarios can be unpredictable, leading to challenges in achieving accurate models. Adjusting to real-time data further complicates the calibration of these simulations.
"Fluid mechanics simulation provides critical insights and advancements that shape the future of engineering disciplines."
Overall, the applications of fluid mechanics simulation across various fields highlight its importance in improving design and safety, ultimately leading to more efficient technologies.
Challenges in Fluid Mechanics Simulation
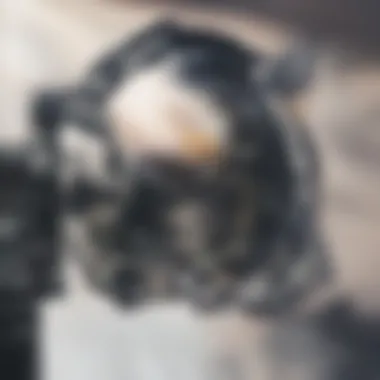
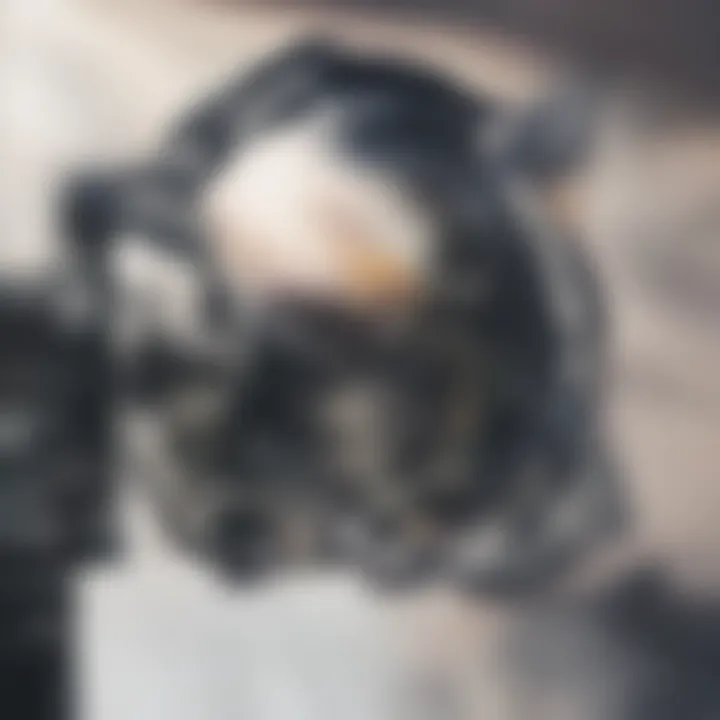
Fluid mechanics simulation encompasses various intricate processes and methodologies that reflect and predict the behavior of fluids. While these simulations offer substantial benefits across numerous engineering disciplines, embracing them involves navigating several challenges. Understanding these challenges is crucial for optimizing simulations and facilitating effective designs across industries.
Computational Limitations
The computational limitations are key challenges in fluid mechanics simulation. As simulations demand greater power to process complex fluid dynamics, computational capacity becomes a significant factor. Current computational resources need to cope with fluid simulations of increasing complexity, such as turbulent flow or multi-phase fluids. Advanced techniques like grid refinement can enhance simulation accuracy but also require significantly more computational power.
In addition, memory and storage limitations can hinder the ability to conduct large-scale simulations. High-resolution models can generate substantial amounts of data. This data needs to be analyzed and stored effectively. If not handled properly, it may result in lost insights and errors during the interpretation phase.
Often, the entry barriers to sophisticated simulation software and powerful hardware can restrict its accessibility for smaller institutions or companies. Understanding these limitations and seeking advancements in hardware can improve the feasibility and scope of fluid mechanics simulations.
Accuracy and Validation
Accuracy and validation represent another significant challenge in fluid mechanics simulation. While simulations can visualize and compute fluid behavior, their reliability hinges on the accuracy of the models used. If the underlying mathematical models are flawed, the resulting simulations may lead to erroneous conclusions.
The validation process is essential to ensure that models closely mirror reality. This involves comparing simulated results with experimental or real-world data. If discrepancies are noted, it signals potential issues in the simulation methods or assumptions made during the modeling process.
To enhance accuracy, researchers and practitioners often adopt techniques like sensitivity analysis. This involves investigating how variations in input parameters affect outcomes. Ultimately, rigorous validation ensures engineering decisions are based on reliable data, reducing the risks associated with design flaws.
By addressing these challenges in fluid mechanics simulation, engineers can improve the reliability and applicability of their findings, leading to better designs and solutions across various fields.
Future Trends in Fluid Mechanics Simulation
The field of fluid mechanics simulation is constantly evolving. As technology advances, new methods and applications emerge that significantly improve both the accuracy and efficiency of simulations. Understanding these trends is crucial for students, researchers, and professionals involved in fluid mechanics. The importance of the future trends in fluid mechanics simulation lies in enhancing predictive capabilities, optimizing designs, and solving complex engineering challenges. It enables industries to move toward more sustainable and cost-effective practices.
Advancements in Computational Power
With increasing demands on computational resources, advancements in hardware technologies have become paramount. Modern supercomputers are capable of performing billions of calculations per second, thus allowing for the simulation of complex fluid dynamics problems that were previously unattainable.
The development of graphic processing units (GPUs) has also changed the landscape of fluid simulations. Unlike traditional central processing units (CPUs), GPUs excel in handling large datasets and executing parallel processing tasks. This is particularly beneficial in computational fluid dynamics (CFD), where the simulation of turbulent flows requires immense computational resources.
Additionally, cloud computing plays a vital role. It provides scalable resources and allows for simulations without the need for extensive local infrastructure. Researchers and practitioners can store, access, and analyze large amounts of data in real-time, fostering collaboration across disciplines and geographic boundaries.
Advancements in computational power have shifted the boundary of what is possible in fluid mechanics simulation, allowing for more detailed and accurate models of complex phenomena.
Integration with AI and Machine Learning
The integration of artificial intelligence (AI) and machine learning into fluid mechanics simulation represents a transformative trend that reshapes how simulations are conducted and analyzed. These technologies offer pathways to enhance the predictive capabilities of fluid models dramatically. Machine learning algorithms can analyze vast datasets to identify patterns and make predictions that were once purely theoretical.
By employing AI techniques, engineers can automate various aspects of the simulation process. For example, optimization algorithms can be used to find the best design parameters that reduce drag or increase efficiency based on fluid flow characteristics. This not only reduces manual labor but also shortens the design cycle significantly.
Furthermore, machine learning can assist in turbulence modeling. Algorithms trained on experimental or high-fidelity simulation data can provide insights that enhance turbulence closures, improving the accuracy of predictions under various flow conditions. This integration holds promise for real-time applications where immediate feedback is essential, such as in the design of aerodynamic shapes in automotive and aerospace industries.
In summary, the future of fluid mechanics simulation is bright, propelled by advancements in computational power and the seamless integration of AI and machine learning technologies. These trends promise to enhance efficiency, accuracy, and the overall impact of fluid mechanics simulations in various engineering fields.
Culmination
Fluid mechanics simulation plays a pivotal role in understanding and predicting the behavior of fluids across various fields. In this article, the discussion centered on key principles, methodologies, and applications of fluid mechanics simulation, especially through the lens of computational fluid dynamics (CFD). The synthesis of these aspects highlights not only the practical implications of fluid dynamics but also its theoretical underpinnings.
Summary of Key Insights
Fluid mechanics simulation allows for an in-depth examination of complex fluid behavior under varying conditions. Some of the critical insights include:
- Importance of Simulation: Utilizing simulations enhances the ability to visualize and analyze fluid dynamics in real-time, which is crucial for fields like aerospace and civil engineering.
- Technological Advancements: The rapid growth in computational power has significantly improved the accuracy and efficiency of simulations, making them indispensable tools in engineering.
- Integration of AI: The incorporation of artificial intelligence in fluid simulation has the potential to revolutionize design processes by optimizing parameters and predicting outcomes based on historical data.
In summary, the use of fluid mechanics simulation is not merely a theoretical exercise but a necessary component of effective engineering practices.
Implications for Future Research
Future research in fluid mechanics simulation should focus on several key areas:
- Enhanced Turbulence Models: Continuous improvement in turbulence modeling will lead to more accurate simulations, particularly in complex flows where existing models may fail.
- Sustainability: As industries prioritize sustainability, research must explore fluid mechanics simulations to optimize processes that reduce energy consumption and environmental impacts.
- Cross-Disciplinary Collaboration: Encouraging collaboration between fluid mechanics experts and specialists from other fields could lead to innovative applications and solutions. This interdisciplinary approach can yield advanced techniques that can be applied across various engineering disciplines.