Gas Check Valves in Low Pressure Systems Explained
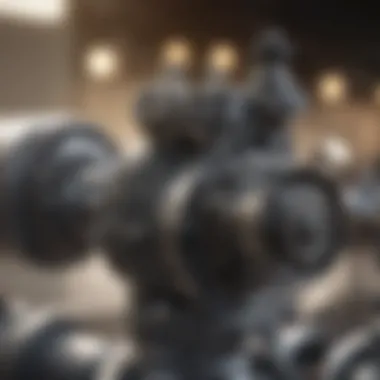
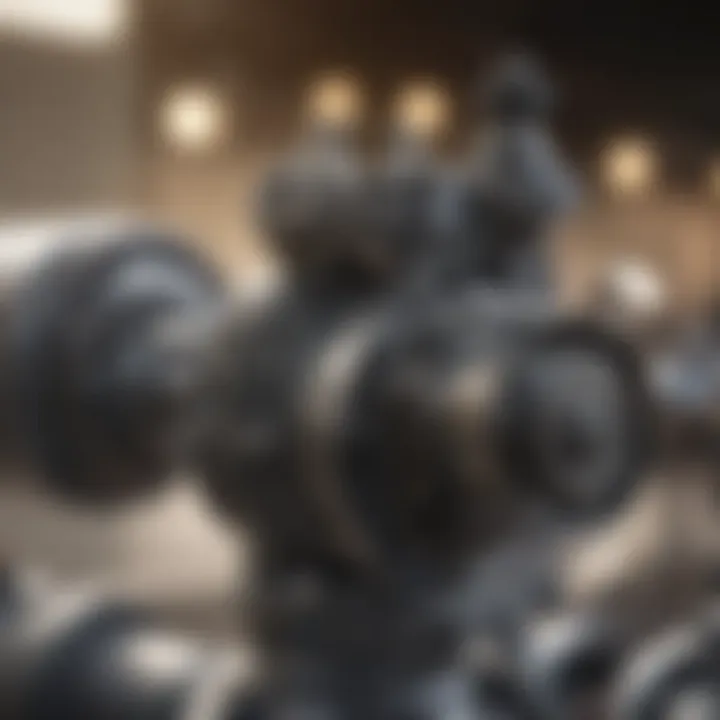
Intro
In the world of engineering and fluid dynamics, the subtle intricacies of components can often be overlooked. One such element that plays a pivotal role in the functionality of low-pressure systems is the gas check valve. Understanding what these valves do, their design considerations, and best practices for their use is crucial for anyone involved in working with low-pressure gas systems. This is not just for the sake of comprehension; the reliability and efficiency of an entire system can hinge on the role of these valves.
Gas check valves prevent backflow, ensuring that the gas travels in the intended direction. They are like the guardians of the gas system, allowing flow only when conditions are right. Without them, a myriad of issues could arise, from pressure drops to system failures. Engineers and technicians alike must grasp the full span of this technology to optimize their systems.
Delving deeper, we will explore critical aspects of gas check valves, including their design, materials, installation guidelines, and maintenance practices. This foundational knowledge will be vital for future improvements and troubleshooting within low-pressure systems.
Research Context
Background and Rationale
Gas check valves serve multiple applications across various industries, from residential heating to industrial processes. These devices function effectively under low pressure where the potential for backflow poses risks to safety and efficiency. In recent years, increased focus on energy efficiency has prompted a reevaluation of these components within existing systems. Thus, understanding the nuances of gas check valves becomes not merely an academic exercise, but a practical necessity in ensuring system integrity.
Literature Review
Several studies have examined the operational aspects of gas check valves, shedding light on their structural and functional characteristics. For example, a study published in the Journal of Fluid Mechanics explored different valve designs, indicating that the shape and material of a valve can significantly impact its resistance to backflow. Additionally, resources like the Encyclopedia of Fluid Dynamics provide extensive insights into the flow dynamics that affect these systems, while community forums on platforms like Reddit often discuss real-world applications and troubleshooting tips.
Methodology
Research Design
This article employs a comprehensive approach, synthesizing existing literature alongside expert insights to guide readers in optimizing their gas check valve use. The objective is to create a well-rounded narrative that provides clarity and actionable knowledge.
Data Collection Methods
Information was gathered through various avenues, including academic journals, industry reports, and online resources. Engaging with professional forums ensures that the data reflects not only theoretical understandings but also practical experiences and challenges faced by users in the field.
Throughout this article, we will navigate various dimensions of gas check valves, from choosing the right materials to addressing common installation pitfalls. The goal is to arm our audience with insights that lead to enhanced reliability and efficiency in low-pressure gas systems.
Prelude to Gas Check Valves
Gas check valves play a pivotal role in maintaining the integrity of low-pressure systems by ensuring that the flow of gas remains in the desired direction. They act as a barrier to prevent backflow, which can lead to contamination and operational inefficiencies. A clear understanding of these valves is essential for engineers and technicians who design and maintain such systems.
These check valves not only enhance the safety of operations but also contribute to the longevity and reliability of equipment. Their proper selection and application can mean the difference between seamless functionality and potential system failure. Therefore, delving into the specifics of gas check valves becomes imperative.
Definition and Purpose
At its core, a gas check valve is a mechanical device designed to allow gas to flow in one direction while preventing backflow. This device functions primarily through the use of a spring-loaded mechanism or a weight that responds to the flow of gas. When the gas pressure exceeds a certain threshold, the valve opens to allow passage; however, when that pressure drops or reverses, the valve closes, blocking reverse flow.
Understanding the anatomy of these valves enables one to appreciate how crucial they are in low pressure settings. Depending on design, some may feature a simple ball that seals against a seat, while others may utilize a diaphragm mechanism. The choice varies based on specific requirements like gas type, pressure ratings, and installation constraints.
Importance in Low Pressure Applications
In low-pressure systems, where gas delivery must often remain consistent and reliable, check valves become indispensable. The consequences of backflow can be particularly severe in such environments—contaminants can infiltrate the system, leading to hazardous conditions or equipment damage.
Utilizing check valves ensures not only the safety of the system but also its efficiency. Here are some reasons why they are crucial in low-pressure applications:
- Prevention of Contamination: They safeguard systems from backflow of undesired materials, maintaining purity in critical operations.
- Efficiency Maintenance: By optimizing flow direction, check valves facilitate better performance of the gas systems, minimizing pressure drops.
- Cost-Effectiveness: Avoiding system failures that can arise from backflow issues reduces the potential for costly repairs and downtime.
In summary, the importance of gas check valves in low-pressure systems cannot be overstated. Their role as guardians against backflow is vital, offering stability and reliability in various industrial applications.
Fundamentals of Low Pressure Systems
Understanding low pressure systems is fundamental when dealing with gas check valves, as these components are designed specifically to function optimally within them. Low pressure systems are typically characterized by their operational mechanisms, which rely heavily on maintaining certain pressure levels for efficient performance. The pressure usually remains below 15 psi, distinguishing them from high-pressure systems where flow dynamics and related components might differ significantly. Thus, a grasp of these systems enhances one’s ability to troubleshoot and optimize their performance.
Characteristics of Low Pressure Systems
Low pressure systems exhibit several distinctive features:
- Pressure Levels: As mentioned earlier, these systems operate under low pressure, which affects how gases move through pipes and fittings.
- Flow Rate: The flow rates in low pressure applications are often lower compared to high-pressure systems, meaning gas travels at a slower velocity. This characteristic necessitates careful design in components such as valves, ensuring they function correctly without causing backflow or interruptions.
- Components: These systems generally involve various fittings, hoses, and valves that are built specifically to meet the demands of lower resistance to flow while considering potential pressure drops.
- Safety Measures: Due to the nature of low pressure operations, safety measures often differ. Components need not withstand extreme forces, but they should still prevent leaks and allow for controlled gas release. This aspect brings gas check valves into play, crucial for maintaining system integrity.
Ultimately, these characteristics play a pivotal role when selecting and implementing gas check valves, as they need to be synchronized with the system's requirements.
Common Applications
Low pressure systems find their footing in a myriad of applications where gas flow needs tight control but not under high pressure. Here are some common arenas where these systems thrive:
- HVAC Systems: Low pressure systems are frequently utilized in heating, ventilation, and air conditioning units to regulate airflow efficiently without creating too much strain on the components.
- Natural Gas Distribution: In residential settings and smaller commercial buildings, low pressure natural gas distribution systems deliver fuel safely and efficiently, making use of check valves to prevent backflow that could lead to hazards.
- Industrial Processes: Certain manufacturing processes involve low pressure gas systems that require careful control of gas flow and pressure to ensure product quality and consistency.
Proper management and understanding of low pressure systems facilitates productivity and safety across various industries.
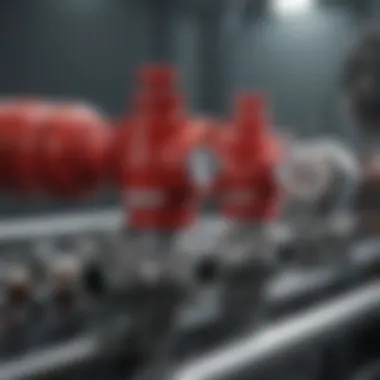
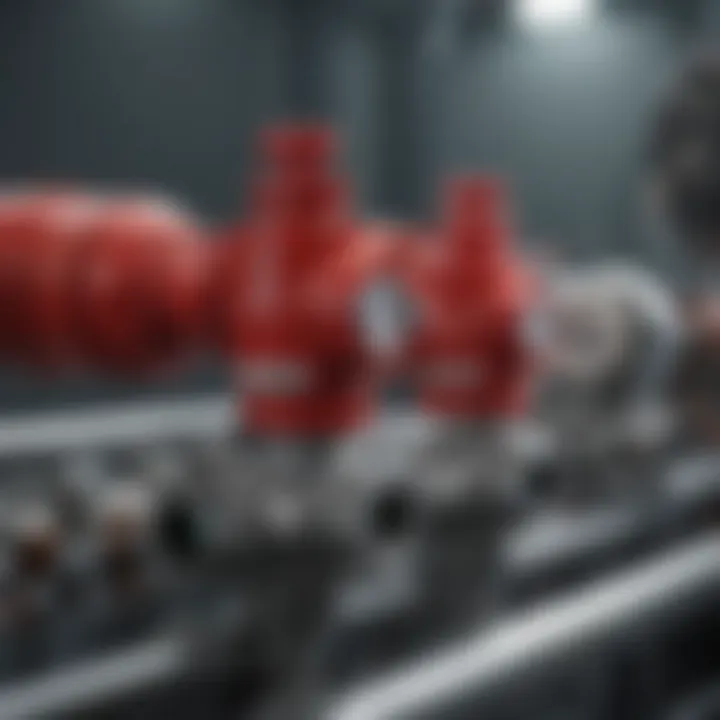
With these applications, it becomes evident how gas check valves serve as a linchpin in maintaining system functionality and reliability. The nuanced interplay between pressure, flow rates, and the selection of the right materials further dictates how these systems perform, underscoring the need for a solid understanding of low pressure mechanics.
Types of Gas Check Valves
Gas check valves are pivotal in maintaining the flow integrity in low-pressure systems. Understanding the various types available can dramatically influence the effectiveness, efficiency, and safety of a system. Each type has its specific operating mechanism and suitability for different applications. The following sections dive into three primary types of gas check valves: spring check valves, ball check valves, and diaphragm check valves. Each possesses unique characteristics that can either enhance or hinder system performance depending on the context of their application.
Spring Check Valves
Spring check valves utilize a spring mechanism to control the flow direction of gases or liquids. The design allows fluid to flow in one direction while simultaneously preventing backflow. This is particularly significant in low-pressure applications where backflow can lead to contamination or system malfunctions.
One of the main benefits of spring check valves is their ability to maintain functionality even at very low pressures, where some other valve types may struggle. Their relatively simple design contributes to ease of maintenance, as they typically rarely require significant repair work.
Moreover, these valves are often favored in residential and commercial applications, particularly in heating and cooling systems. Spring check valves can be installed in various orientations, making them versatile for different piping layouts. However, one should consider the spring tension because it can affect the valve's responsiveness. If too stiff, it might hinder low-flow situations, while too weak can risk premature failure.
Ball Check Valves
Ball check valves function using a spherical ball that sits in a seat within the valve body. During normal flow, the ball lifts off the seat, permitting fluid passage. However, if backflow occurs, the ball returns to the seat, effectively sealing the valve shut. With their robust construction, ball check valves are known for their durability and reliability. This design is extremely effective in minimizing leaks and is popular in applications that involve varying pressures and flow conditions. They are often found in oil, gas, and water systems, where backflow prevention is crucial.
On the flip side, one should note that ball check valves can be sensitive to debris and sediment in the fluid as this can cause the ball to jam. Therefore, maintaining clean upstream conditions is paramount to ensuring their reliable operation. It’s also worth noting that the size and type of ball should match the intended application to avoid issues with responsiveness under low-pressure conditions.
Diaphragm Check Valves
Diaphragm check valves rely on a flexible diaphragm that acts as a sealing element. They are particularly useful in systems where flow needs to be controlled very precisely. The diaphragm's movement is excellent at sealing off backflow, making these valves highly effective in various applications, especially in chemical processing and systems that handle corrosive fluids.
An advantage of diaphragm check valves is their ability to accommodate varying flow rates without losing effectiveness. The flexible nature of the diaphragm allows it to respond dynamically to changes in pressure and flow, ensuring a tight seal whenever needed.
However, considerations around installation are essential to ensure optimal performance. The diaphragm must be correctly oriented and free from mechanistic interference to function well. Regular inspection is also necessary since diaphragms can wear or degrade over time, particularly when exposed to harsh materials or operating conditions.
Material Considerations
Understanding the materials used in gas check valves is paramount, especially in low-pressure systems. This is because the material choice directly impacts not only the valve's durability but also its performance and efficiency in preventing backflow. When gas travel through a system, it can be subject to various conditions that may affect both its properties and the materials that come in contact with it.
One key aspect of material consideration is assessing the chemical compatibility with gases being handled. For example, a valve designed to control natural gas must be crafted from materials that can resist any potential reactions. Ignoring this can lead to severe operational failures and create hazards within the system.
- High-density polyethylene (HDPE)
- Stainless steel
- Brass alloys
These materials are often chosen due to their distinctive elements, such as strength, resistance to corrosion, and longevity under varying pressure and temperature scenarios. Understanding these materials allows engineers to tailor their valve selections to the specific requirements of each installation.
Another point of focus is the overall weight of the valve. In vessels where space and weight restrictions are critical, lighter materials can enhance the overall efficiency of the system without sacrificing functionality.
"The right materials make the difference between a reliable system and one prone to failure. It’s more than just choice; it’s about understanding the purpose."
Incorporating a diverse array of material properties not only augments the life of gas check valves but also enhances the reliability of low-pressure systems by ensuring they can endure.
Common Materials for Construction
When discussing the common materials for gas check valves, a few notable contenders emerge that demonstrate versatility in construction.
- Stainless Steel
This material is particularly favored for its robustness and inherent resistance to rust and corrosion, making it suitable for various environmental conditions. Its suitability extends to handling a wide spectrum of gases and liquids. - Brass
Frequently used in lower-cost applications. It has decent tensile strength and corrosion resistance, especially in systems where temperatures are moderate, but particular care is necessary if aggressive gases are involved. - Polymer Composites
These materials are gaining traction, especially in specific applications where weight reduction is critical. They boast good resistance against various chemicals but may not stand up to extreme temperatures as well as metals. This makes them suitable for tailored applications where weight plays a crucial component.
Given these options, the selection process should take into account not just the gas’s nature but also the operational environment, such as potential exposure to chemicals or temperature fluctuations.
Corrosion Resistance and Its Importance
Corrosion resistance is a heavyweight in the ring of material considerations. Low-pressure systems can expose metals to various corrosive elements, impacting their performance—and hence the entire system's reliability—over time. A valve that lacks suitable corrosion resistance risks premature failure, leading to costly repairs and possibly hazardous leaks.
Materials like stainless steel shine here, boasting excellent resistance to many corrosive agents, but they come at a higher price. On the flip side, a more affordable choice like brass may succumb to corrosion more quickly in harsh environments, suggesting that cost considerations should always be weighed against the potential for greater long-term costs associated with failed components.
In various industrial applications, failure to identify suitable corrosion-resistant materials not only leads to financial loss but also compromises safety. Thus, engineers must understand the service environment and evaluate the long game when it comes to material selection. In practice, thorough inspections should accompany any replacement decisions for valves, ensuring that new installations not only perform well under pressure but also stand strong against corrosion for years to come.
Installation Guidelines
Installing gas check valves in low-pressure systems is not just a mechanical task; it’s a critical procedure that directly impacts the efficiency and safety of the system. Proper installation ensures that the valves function correctly, preventing backflow and maintaining pressure. Here, we will delve into important aspects of installation, covering pre-installation checks, orientation and mounting techniques, and post-installation testing.
Pre-Installation Checks
Before any installation takes place, taking a moment to perform pre-installation checks can save a lot of headaches down the road. This step helps in identifying potential issues that may compromise the effectiveness of the gas check valve. Items to consider include:
- Condition of the Valve: Inspect the valve for any visible signs of damage or defects. A cracked body or damaged seals can lead to operational failures.
- Compatibility Factors: Ensure that the valve materials match the gas type and any other fluids that may interact with it. Certain materials degrade faster in specific chemical environments.
- System Pressures: Verify the operating pressures of the system. Using a valve rated for higher pressures in a low-pressure system can lead to unnecessary complications.
- Size and Fit: Confirm that the valve size is appropriate for the existing piping. A poor fit may lead to significant losses in performance.
Essentially, these checks are like laying down a solid foundation before building a house. Without them, the risk of costly repairs or replacements increases significantly.
Proper Orientation and Mounting
Once the pre-installation checks have been completed successfully, the next step is to focus on orientation and mounting. Failing to mount a gas check valve correctly can lead to system flaws, where the valve might not function as intended.
- Manufacturer Guidelines: Always refer to the manufacturer's installation instructions. They provide crucial details on the correct orientation—like whether it should be horizontal or vertical.
- Flow Direction: Pay attention to the flow direction indicated on the valve. Installing the valve backward will lead to backflow, rendering its purpose void.
- Secure Mounting: Use appropriate mounting hardware to brace the valve securely in place, preventing vibrations or potential leaks during operation.
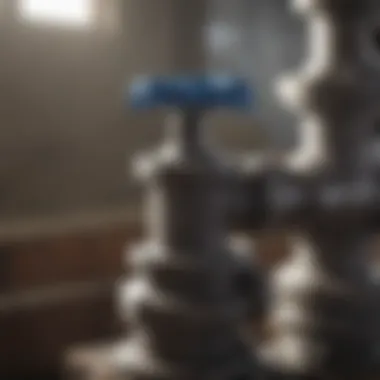
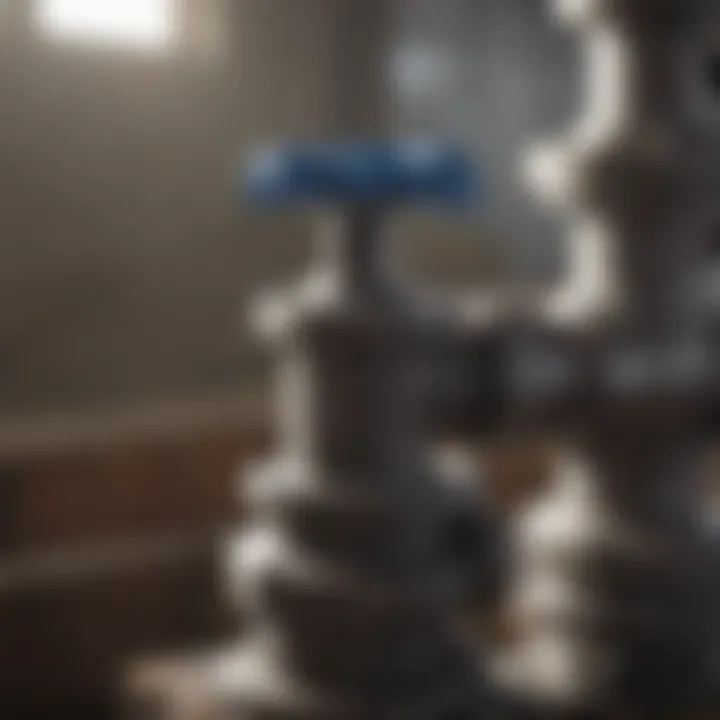
In general, the motto is: measure twice, cut once. This detail-oriented approach on orientation can save time and resources.
Testing Post-Installation
Once the installation is complete, it's vital to conduct thorough testing. This phase verifies that the valve operates as expected under functioning conditions.
- Visual Inspection: Start with a simple visual check. Look for leaks around the mounting joints and the valve body.
- Pressure Tests: If possible, conduct pressure testing to ensure the valve holds up under system pressure requirements. This step may require specialized tools to measure.
- Functional Testing: If safe to do so, operate the system briefly to observe the valve during operation. This helps in identifying correct flow and backflow prevention.
Testing post-installation is akin to putting the finishing touches on a reliable machine. It ascertains that all components are working together harmoniously.
"Installation might seem straightforward, but the details spell the difference between success and failure in low-pressure systems."
In summation, proper installation guidelines are the cornerstone for effective functioning of gas check valves in low-pressure systems. Adhering to careful checks, thoughtful orientation, and rigorous testing processes can lead to increased reliability and extended lifespan of the entire system.
Operational Mechanism
Understanding the operational mechanism of gas check valves is crucial in optimizing their use within low-pressure systems. This component plays a pivotal role in maintaining system integrity and efficiency. Grasping the dynamics involved in how these valves operate not only helps in selecting the right type for a specific application but also informs routine operations and maintenance strategies. Unpacking the intricacies of these mechanisms gives insight into effective management of gas flow, ensuring that unwanted reversals or leaks do not compromise the system.
Flow Dynamics in Low Pressure Systems
Gas flow within low-pressure systems showcases unique behaviors that differ vastly from those in high-pressure environments. The dynamics at play are influenced by a multitude of factors including the gas type, temperature, and pressure gradients. Gas can behave like a fluid in certain stages, where the velocity and pressure can fluctuate significantly. Understanding these aspects helps in selecting the right model of gas check valve tailored to system requirements.
In low-pressure systems, the velocity of gas flow tends to be slower, creating a scenario where even minor fluctuations may cause disruptions. A properly functioning check valve reacts instantly to these changes, allowing gas to flow in the intended direction while preventing backflow. Without an adequate comprehension of flow dynamics, engineers might misjudge valve sizes or types, leading to inefficiency or failure.
"Choosing the right gas check valve involves understanding not just the gas properties, but flow behavior in real-world applications. Miscalculations can be costly."
How Check Valves Prevent Backflow
Check valves operate on the principle of preventing backflow, a phenomenon where gas could potentially flow back into the system. This mechanism is typically designed using one of several configurations, such as spring-loaded or gravity-operated setups. When the pressure in the forward direction exceeds the pressure behind the valve, the valve opens, allowing gas to flow smoothly. In contrast, if the pressure on the opposite side rises, the valve automatically closes, effectively blocking any reverse flow.
• Understand the right operational mechanism behind check valves to enhance:
- Flow integrity
- System performance
- Safety measures
By ensuring a robust design and understanding the operational mechanism, engineers can considerably increase the lifespan and reliability of gas systems.
Maintenance Practices
Ensuring that gas check valves function properly in low-pressure systems is an ongoing task that is critical for maintaining overall system reliability. It’s not just about installing these components; regular maintenance can save you time, money, and headaches down the road. Properly maintained gas check valves can enhance efficiency, reduce the risk of leaks, and prolong equipment life. Here we explore the essential aspects of maintenance practices, emphasizing routine inspections, cleaning and repairs, and knowing when to replace valves.
Routine Inspections
Regular inspections are the bread and butter of effective valve maintenance. Think of inspections as a health check-up for your system. They help identify issues early before they escalate into major problems. During routine checks, consider examining the following:
- Leakage: Always look for any signs of gas escaping around the valve. Even a tiny leak can lead to significant losses.
- Seals and Gaskets: They might wear out over time due to stress or environmental factors. Check them for any signs of degradation.
- Mechanical Integrity: Ensure that the valve is securely fitted and there are no signs of corrosion or physical damage.
Using a diligent approach to inspections helps ensure that potential problems are caught sooner rather than later, thus ensuring the effective performance of the system without unexpected interruptions.
Cleaning and Repairs
Cleaning gas check valves is just as vital as inspecting them. Dust, debris, or buildup can impede the valve's ability to function correctly. How to effectively clean:
- Disassemble Carefully: When cleaning, it’s essential to take the valve apart with care to avoid damaging any components.
- Use Appropriate Solutions: Select a non-corrosive cleaner to wash down the internal components. Avoid harsh chemicals that could cause further damage.
- Inspect During Cleaning: As you clean, inspect each part for wear and tear, looking specifically for cracks or stiffness in movable parts.
If repairs are needed, sourcing the right parts is crucial. Using incompatible materials can lead to further issues down the line, resulting in increased costs.
When to Replace Valves
Knowing when to replace gas check valves isn’t always easy. There are tell-tale signs, however:
- Persistent Leakage: If repeated inspections confirm leakage issues despite cleaning and minor repairs, it may be time to consider replacement.
- Deterioration of Material: Valves made from materials that haven’t stood up over time might need replacing. For example, plastic valves in corrosive environments will often show signs of wear faster than metal ones.
- Reduced Performance: If a valve that once shut off effectively begins to allow backflow regularly, the likelihood is that it has reached the end of its life.
"Investing time in maintenance not only safeguards your systems but also paves the way for longevity."
Checking these aspects regularly and replacing parts timely can enhance system efficiency and ultimately support the durability and performance of the entire low-pressure gas system.
Deal with these maintenance practices as you would a well-loved antique; care and attention will keep it functioning beautifully for years to come.
Troubleshooting Common Issues
Troubleshooting common issues related to gas check valves in low-pressure systems is essential for maintaining system integrity and operational efficiency. Understanding these challenges can greatly enhance the reliability of your system. Taking the time to diagnose problems leads to timely interventions, reducing the risk of extensive damage or costly downtime.
Identifying Backflow Problems
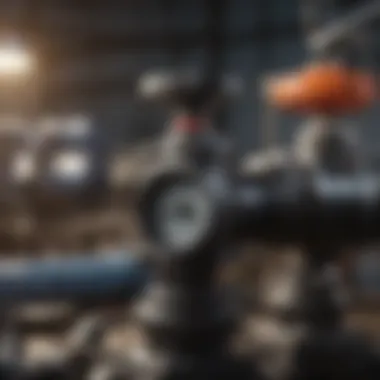
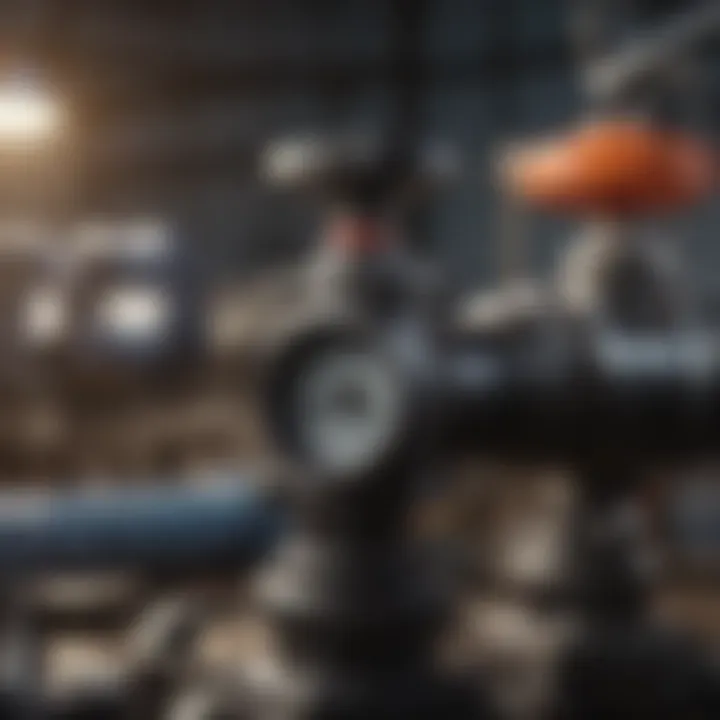
Backflow can be a sneaky foe in any gas system, particularly in low-pressure setups where pressure differentials are minimal. Identifying backflow issues often starts with monitoring pressure levels across the system. If you observe a significant drop in pressure downstream, that could be a sign that gas is traveling in the opposite direction of what you intended.
- Check Pressure Indicators: If you find pressure gauges displaying erratic readings, it may indicate backflow.
- Visual Inspections: Look for signs of gas leakage or unusual depressurization at connections and valves. Leaks are a telltale sign that the gas flow is interrupted.
- Testing Equipment Use: Utilizing flow meters can help gauge if gas is moving in an unintended direction. Setting the meter to monitor flow direction explicitly can flag anomalies.
Moreover, system design plays a pivotal role. If there are too many bends or improper elevation in piping, these factors can contribute to backflow susceptibility. It’s imperative to ensure that your gas check valves are appropriately positioned and functioning as intended.
Leak Detection Techniques
Detecting leaks is a critical aspect of troubleshooting gas check valves. Even minor leaks can lead to significant safety hazards and operational inefficiencies. Implementing a systematic approach helps to spot these issues before they escalate.
- Smell for Gas: A distinct odor (often likened to rotten eggs) may indicate a leak. When working in a gas environment, being vigilant about smells can save you from potential disasters.
- Soapy Water Test: A traditional but effective trick—apply soapy water around joints and valves. Bubbles forming indicate escaping gas.
- Ultrasonic Leak Detectors: For more advanced settings, ultrasonic detectors can detect high-frequency sounds of gas escaping through leaks, providing a non-intrusive method to pinpoint issues.
- Pressure Testing: This is a more systematic method where you isolate a section of the system and pressurize it using inert gases, like nitrogen. Any drop in pressure indicates leaks in the setup.
It's crucial to remember that the sooner leaks are detected and addressed, the less likely the issue will escalate into damage. This proactive approach helps maintain the overall health of low-pressure gas systems.
Regulatory Standards and Compliance
When it comes to gas check valves in low pressure systems, understanding and adhering to regulatory standards and compliance is not just an option; it’s a necessity. These standards ensure that installations are safe, reliable, and efficient while minimizing the risk of accidents and failures. Regulatory frameworks are designed to protect both people and the environment, making compliance a key factor in the engineering and implementation of gas check valves.
These standards serve several critical purposes including:
- Safety Assurance: With proper regulations in place, the risk of accidents due to faulty valves is significantly reduced.
- Quality Control: Regulatory standards often dictate the materials and manufacturing processes used, ensuring a reliable end product.
- Environmental Protection: Compliance helps in minimizing the environmental impact of gas leaks and other failures.
- Market Acceptance: Often, industries won't accept operations involving sub-standard equipment, making compliance vital for business relations.
Understanding Industry Standards
Industry standards governing gas check valves may vary slightly based on the region or country, but most conform to internationally recognized principles. Familiarity with organizations such as ISO (International Organization for Standardization), API (American Petroleum Institute), and ASME (American Society of Mechanical Engineers) provides a framework for manufacturers and engineers alike.
For instance, ISO 9001 outlines quality management principles applicable to a variety of industries. When manufacturers comply with these guidelines, it not only enhances reliability but also increases consumer trust. Industry standards cover aspects like:
- Material Properties: Specifications on materials that withstand corrosive environments in low-pressure systems.
- Testing Methods: Established procedures for testing the valves for durability and performance before they hit the market.
- Installation Criteria: Guidelines on proper installation techniques to prevent premature failures.
Compliance and Certification Processes
Once a product is designed and manufactured, it doesn’t just get an automatic thumbs-up. There are several steps involved in compliance and certification processes that ensure everything is up to snuff. Typically, these involve:
- Documentation Review: All design specifications, materials used, and manufacturing processes must be meticulously documented.
- Testing: Gas check valves undergo rigorous testing to ensure they meet the laid out safety and performance standards. This can include pressure tests and flow tests under low-pressure conditions.
- Third-party Inspection: Often a non-affiliated entity performs an independent review of the product to verify conformity to industry standards.
- Certification Issuance: If the valve passes all inspections and tests, it receives certification that asserts its compliance with relevant standards. This certification must be kept current, frequently requiring re-evaluations to maintain its validity.
"Adhering to these regulatory standards not only fortifies public trust but substantially augments the operational longevity of gas check valves in low pressure systems."
Ensuring compliance is not merely an administrative tick-box exercise; it’s about building systems that are trustworthy, responsible, and designed for the realities of their operational environments. By recognizing the significance of regulatory standards and actively engaging in the compliance processes, engineers and technicians can optimize the functionality and reliability of low-pressure gas systems.
Future Trends in Gas Check Valve Technology
Understanding the future trends in gas check valve technology is crucial for anyone involved in low-pressure systems. As industries continue to evolve, so do the requirements for reliability and efficiency. Incorporating advancements in materials, design, and technology can lead to improved performance of gas check valves. This is not just about keeping up with the times, but rather ensuring that systems are safer, more efficient, and can handle contemporary challenges.
Innovations in Materials and Design
The future is leading us toward exciting innovations in both materials and design for gas check valves. Traditional materials, often metal and rubber, are being replaced or enhanced with advanced composites and alloys. This shift is significant because new materials can offer better resistance to corrosion and wear, which are critical factors in low-pressure systems. For instance, valves made from nylon composites may weigh less and resist some chemicals that can degrade standard metals.
Furthermore, the design process is becoming increasingly sophisticated thanks to computer-aided design (CAD) techniques and simulations. These advancements can help enhance flow dynamics significantly, minimizing turbulence and improving overall efficiency.
Key Points Regarding Innovations:
- Weight Reduction: Advanced materials can lead to lighter components, making handling easier.
- Enhanced Functionality: Improved design can result in better control over flow and backflow prevention.
- Improved Lifespan: With better materials, gas check valves can potentially have longer operational lives, reducing the need for frequent replacements.
"Innovative material choices can redefine the standards for reliability and performance, setting the stage for future developments in gas system technology."
The Role of Smart Technology
The integration of smart technology into gas check valves is gradually becoming a game changer. This incorporation means that valves are not just mechanical components anymore; they can be equipped with sensors and monitors that provide real-time data about valve performance and system status. Imagine valves that alert technicians of pressure changes or possible blockages—this could prevent significant issues before they manifest.
The benefits are manifold. Firstly, predictive maintenance becomes a reality as this technology can indicate when a valve might fail or require servicing, thus greatly reducing downtime. Secondly, automated systems can now gather data that help in better understanding system performance and in identifying areas for improvement.
Main Aspects of Smart Technology in Gas Check Valves:
- Data Collection: Sensors track performance metrics that can be analyzed for efficiency optimizations.
- Preventive Maintenance: Instead of following a set schedule, maintenance can be done when it's actually needed, saving time and resources.
- Enhanced Safety: Real-time alerts can provide immediate feedback, ensuring safer operation in low-pressure systems.
In summary, as the industry shifts to embrace modern technology, the role of gas check valves in low-pressure systems will undoubtedly scale with it, evolving to meet the demands of a rapidly changing environment.
The End
Gas check valves are not just mechanical components; they play a pivotal role in ensuring the safety, reliability, and efficiency of low-pressure systems. Understanding their significance provides several benefits, especially for professionals involved in system design, installation, and maintenance.
Key Considerations in the Culmination
When summarizing the insights from this article, a few specific elements stand out.
- Functionality: Gas check valves serve as a one-way gate, critical in preventing backflow and potential hazards. Missteps in this area can lead to malfunctions or even safety incidents, underscoring the necessity of proper valve selection and installation.
- Material Selection: The choice of materials, which was discussed in detail, affects everything from longevity to corrosion resistance. Selecting the right material is paramount for maintaining integrity and performance, particularly in challenging environments.
- Maintenance Practices: Regular inspections and proper maintenance keep these valves operating smoothly. Neglect can lead to system failures, emphasizing a proactive approach in monitoring valve health.
- Compliance with Standards: The relevance of adhering to industry regulations cannot be overstated. Compliance ensures that systems operate within safe parameters, which is crucial for both personnel and environmental safety.
In sum, this article highlights that understanding gas check valves in low-pressure systems is an imperative endeavor. It has far-reaching implications, not just for technical efficacy, but for safety and compliance in an industry that holds high stakes. The integration of the discussed themes can greatly enhance one’s approach to managing gas systems effectively.