Heat Transfer Mechanisms in Powder Coating Explained
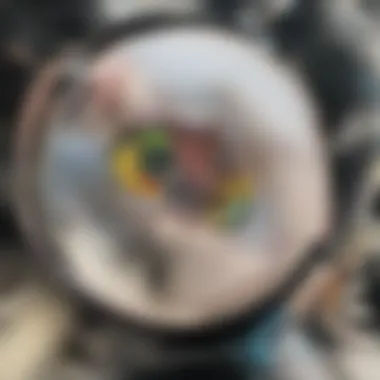
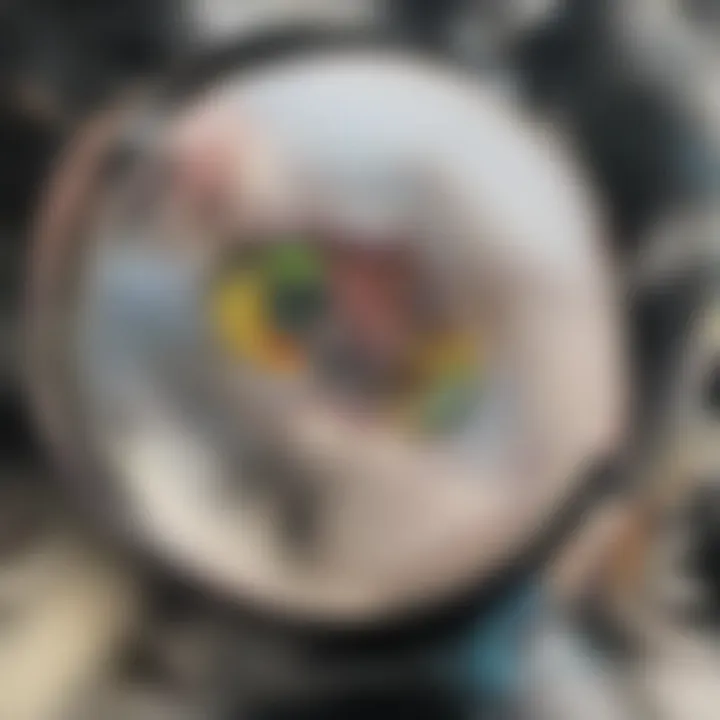
Intro
Heat transfer plays a critical role in the powder coating process. Understanding the mechanisms involved enhances the application effectiveness and overall performance. The application of powder coating involves various factors that influence heat dynamics. The interaction between temperature, substrate materials, and the powder itself determines the quality of the final coating. This section will lay the foundation for exploring these elements in depth.
Research Context
Background and Rationale
Powder coating is a widely used technique in several industries including automotive, manufacturing, and architecture. Traditional liquid coatings often run the risk of dripping and require solvents, leading to environmental concerns. Powder coating eliminates these issues while also providing a robust finish. The efficiency of this method can be significantly affected by the heat transfer mechanisms involved. Understanding these can help in optimizing processes and improving outcome quality.
Literature Review
Numerous studies have focused on heat transfer in the context of powder coating. Early research by authors like Wang and Barringer highlighted the roles of convection, conduction, and radiation in achieving optimal coating adherence and durability. More recent work has examined the impact of substrate types, coating thickness, and curing temperatures on heat dynamics.
- Research indicates that metal substrates often require different heat settings compared to plastics.
- Curing times can vary drastically based on the powder formulation used.
- Thermal conductivity of materials directly influences the coating’s performance.
The current literature suggests a need for further exploration, especially in integrating advanced technologies to gauge heat transfer rates more accurately.
Methodology
Research Design
This article synthesizes existing research with practical insights from industry professionals. By blending quantitative data from experimental studies with qualitative analyses from field observations, a comprehensive understanding of heat transfer in powder coating operations can be achieved.
Data Collection Methods
Data was collected from various literature sources along with industry surveys. Conducting interviews with experts in the coating industry provided a real-world perspective on the challenges and advancements in technology. Statistical analyses of thermal efficiency metrics were included to paint a clearer picture of the applied methodologies in heat transfer.
Through these approaches, the article aims to provide a well-rounded view of heat transfer mechanisms in powder coating, elucidating the techniques that drive performance and efficiency across different applications.
Understanding Heat Transfer in Powder Coating
Understanding heat transfer in powder coating is crucial for ensuring optimal coating performance and quality. This section discusses the various heat transfer mechanisms within the powder coating process. Knowing how heat transfers during coating application can significantly affect adhesion and durability. Proper management of these heat transfer processes leads to improved efficiency, reduced costs, and better product outcomes.
It is also important to consider that the effectiveness of powder coating is influenced by various parameters like substrate materials, environmental conditions, and application techniques. Gaining insight into these essentials enables industry professionals to refine their processes. Understanding the principles of heat transfer is not merely an academic exercise; it directly impacts the practical aspects of production, resulting in superior coatings.
Basics of Heat Transfer
Heat transfer refers to the movement of thermal energy from a region of higher temperature to one of lower temperature. In powder coating, various forces such as conduction, convection, and radiation play distinct roles in the efficiency of the coating process. Each method alters the way energy interacts with the substrate and powder. It is essential for professionals to grasp these concepts, as they lend insight into maximizing coating performance and ensuring optimal curing temperature.
Types of Heat Transfer Mechanisms
In powder coating, the following three primary mechanisms are utilized to ensure effective heat exchange:
Conduction
Conduction is the direct transfer of heat through a material without any movement of the material itself. In powder coating, conduction occurs predominantly between the substrate and the powder. When the powder particles come into contact with a heated substrate, heat is transferred through the substrate to the particles, enabling them to melt and adhere to the surface.
The key characteristic of conduction is its effectiveness in solid materials, which allows for efficient heat transfer. This makes it a popular choice in applications where consistent heat application is required. One unique feature of conduction is that it offers predictable thermal profiles, ensuring that the coating reaches the desired melting point uniformly. On the downside, conduction can be slower compared to other mechanisms, which may affect the overall curing time of the powder coating process.
Convection
Convection involves the transfer of heat through fluid motion, which can include gases and liquids. In powder coating, convective heat transfer typically occurs in the curing oven, where air movement aids in heating both the substrate and the powder.
The main advantage of convection is its ability to distribute heat evenly over larger areas. This is particularly beneficial as it helps maintain consistent temperatures across various surfaces. Additionally, convection can accelerate the curing process by improving the flow of thermal energy. However, its effectiveness heavily relies on factors such as airflow and oven design; poor circulation may lead to uneven heating and flawed coatings.
Radiation
Radiation is the transfer of heat in the form of electromagnetic waves. In powder coating, radiation contributes to heat transfer from the oven's heating elements to the substrate and coating. This is especially notable when infrared lamps are used, as they primarily emit radiant heat.
The key characteristic of radiation is that it does not require a medium for heat transfer, which allows it to heat surfaces directly. This can be a beneficial aspect in achieving quick and efficient heating of complex shapes or surfaces. However, radiation's effectiveness can be variable, influenced by factors like surface color and distance from the heat source. In some cases, it may not provide the necessary control of heat application when compared to conduction or convection.
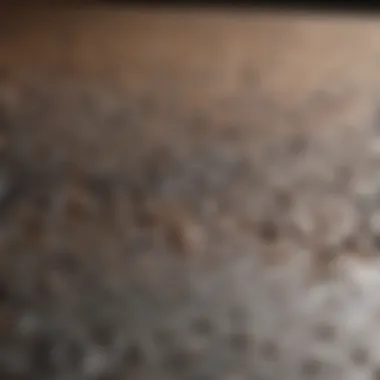
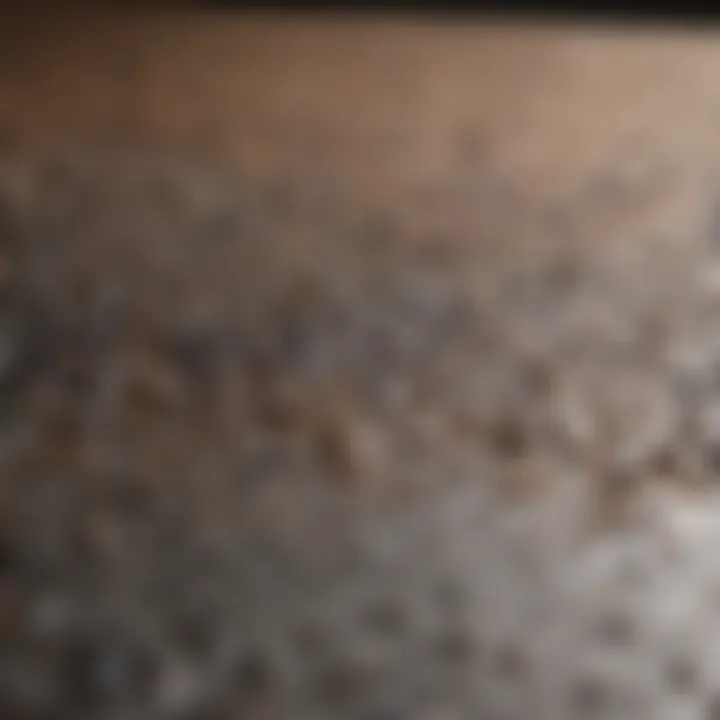
Role of Temperature in Powder Coating
Temperature plays a vital role in the powder coating process. It affects the melting point of powder particles and determines the duration of the curing stage. Correct temperature management ensures that the powder adheres well to the substrate while achieving the desired finish and durability. Moreover, maintaining optimal temperature conditions is essential for chemical reactions that enhance bond strength. An oversight in temperature control could lead to defects such as poor adhesion or incomplete curing, emphasizing the need for proper thermal regulation in powder coating applications.
The Powder Coating Process
The powder coating process is a critical phase in achieving high-quality finishes in various industrial applications. This technique offers several benefits over traditional liquid coatings. Not only does it provide a uniform application, but it also enhances durability, making it a preferred choice for many manufacturers. Understanding the intricacies of the powder coating process is essential for optimizing heat transfer and improving overall performance.
Overview of Powder Coating
Powder coating involves applying a dry powdered paint to a surface, which is then heated to create a smooth, durable finish. The method combines the principles of electrostatics and thermal dynamics to ensure effective adhesion and uniformity. Unlike liquid paints, powdered coatings do not require solvents, reducing volatile organic compounds (VOCs) emissions. This is particularly important in meeting environmental regulations. Furthermore, the process allows for a thicker application without runs or sags, providing the opportunity for improved surface protection.
Application Techniques
Electrostatic Spray
Electrostatic spray is a widely used technique where charged powder particles are attracted to the grounded substrate. This method ensures efficient transfer of the coating material while minimizing overspray. One key characteristic of electrostatic spray is its versatility, making it suitable for a variety of applications including automotive parts and consumer goods. The electrostatic charge enhances coverage even in complex geometries, reducing material waste and enhancing uniformity. However, the reliance on electricity can sometimes lead to issues if proper grounding is not established, which can impact the quality of the coating.
Fluid Bed Coating
Fluid bed coating involves suspending powder particles in an air stream, creating a fluid-like state. This technique is ideal for coating large, complex shapes. A significant advantage of fluid bed coating is its ability to apply a uniform layer without the need for electrostatic application. The unique feature here is the ease of achieving consistent thickness, which is critical for parts that require precise coating. However, fluid bed coating may require more time for post-coating curing compared to other methods, making process timing an essential consideration.
Curing Process Explained
The curing process is integral to the powder coating technique, as it solidifies the applied powder into a durable finish through heat.
Chemical Reactions
Chemical reactions during curing involve cross-linking of the resin molecules, which greatly enhances the hardness and chemical resistance of the final product. This process typically occurs at elevated temperatures and is essential for achieving the final performance characteristics of the coating. Additionally, the reactions create a bond that improves adhesion to the substrate, making this step crucial for longevity. While the benefits are significant, achieving the correct temperature range is critical; too low may result in an incomplete cure, while too high can damage the coating.
Thermal Behavior
Thermal behavior refers to how the powder coating responds to heat application during the curing phase. The key characteristic here is the temperature profile, which must be meticulously controlled to ensure even curing. Proper thermal behavior ensures that the coating cures uniformly, minimizing defects and optimizing performance. The unique feature of thermal behavior is its relationship with the application technique, as factors such as the thickness of the coating and the properties of the substrate can influence the heat transfer rates. Having good thermal management is vital for ensuring a high-quality finish and achieving the desired properties.
Factors Influencing Heat Transfer in Powder Coating
Heat transfer plays a critical role in the effectiveness of powder coating processes. Understanding the factors that influence this transfer can help optimize performance. Every element, from the materials used to environmental conditions, affects heat dynamics. A thorough examination of these factors provides insight into enhancing coating quality and efficiency.
Influence of Substrate Materials
Conductivity
The conductivity of substrate materials is vital in the heat transfer mechanisms. Conductive materials, such as metals, facilitate efficient heat transfer during the curing process. High thermal conductivity allows heat to spread evenly over the substrate, ensuring consistent coating results.
Metals like aluminum and steel are often preferred because of their high thermal conductivity. This characteristic aids in quick heat absorption and distribution, crucial for a uniform finish. However, if a substrate has low conductivity, it may lead to uneven curing, creating defects in the coating.
Roughness
Surface roughness of the substrate also affects how heat moves during coating. A rough surface can trap air pockets and create insulating barriers that hinder heat transfer. This might lead to localized cooling, which can adversely impact the curing of the powder coating.
Smoother surfaces generally provide better contact for heat transfer. Careful control of substrate preparation is essential in this regard. On the other hand, excessive smoothness can compromise adhesion. Thus, finding an optimal roughness level is critical for balancing heat transfer efficiency and coating performance.
Environmental Conditions
Humidity
Humidity levels in the air can significantly affect the powder coating process. High humidity can lead to moisture absorption in the powder before it is cured. This moisture can disrupt the curing process, leading to undesired defects like bubbling or discoloration.
Monitoring humidity closely during applications ensures proper adhesion and curing. In controlled environments, adjusting humidity levels helps maintain coating quality. However, managing humidity is sometimes challenging, especially in outdoor settings.
Ambient Temperature
Ambient temperature plays a crucial role in heat transfer efficiency. Higher ambient temperatures can enhance curing rates, facilitating a better finish. However, if the temperature is excessively high, it may lead to premature curing of the powder before it adheres to the substrate.

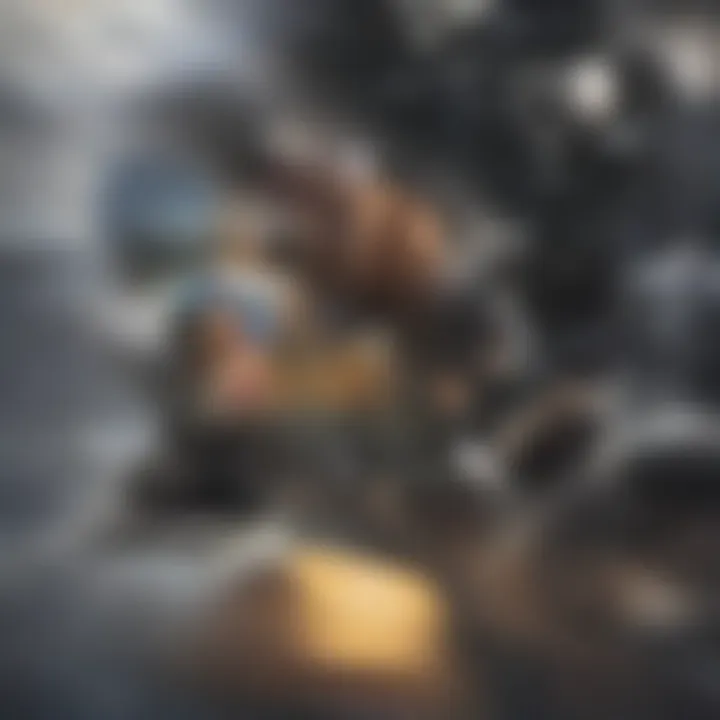
On the contrary, low ambient temperatures can slow down the curing reaction. This can cause extended processing times and, ultimately, affect throughput. Thus, maintaining an optimal ambient temperature is essential for reliable powder coating results.
Coating Thickness
Coating thickness is another vital factor impacting heat transfer. Thicker coatings can act as insulators, slowing the heat transfer process. Therefore, they may not cure effectively. This realization should guide designers and operators when selecting the appropriate thickness for specific applications.
Too thin coatings may not provide sufficient coverage or protection. The key lies in achieving a balanced thickness that allows for optimal heat transfer while ensuring durability and aesthetic quality. Managing this balance is essential for achieving the desired coating performance.
Advanced Techniques in Powder Coating
Advanced techniques in powder coating are crucial for enhancing the efficiency and effectiveness of the coating process. As industries demand higher quality finishes and better durability, these techniques can significantly improve the operational capabilities of powder coating systems. They not only address common challenges in the coating process but also facilitate innovations that contribute to environmental sustainability and economic viability.
Innovations in Heat Transfer Enhancement
Innovations aimed at enhancing heat transfer during the powder coating process are vital. Improved heat transfer can lead to better curing of the powder, resulting in higher quality finishes. One significant development is the use of advanced heating technologies, such as infrared heating systems. These systems offer quick, precise, and even heating, allowing the powder particles to melt and flow uniformly across the substrate.
Other innovations include the integration of heat exchangers to optimize temperature management during the curing stage. By facilitating the efficient transfer of heat, manufacturers can minimize energy consumption and increase coating speed.
Finally, the exploration of thermal conductive coatings plays a role in this enhancement. These materials help the substrate to distribute heat evenly, ensuring the coatings cure effectively without defects. By focusing on these innovations, the industry can expect improved performance and sustainability in powder coatings.
Alternative Powder Formulations
Another critical aspect of advanced techniques involves the development of alternative powder formulations. New formulations are designed to improve the flow characteristics of the powder, which influences how well it adheres to the surface being coated. These formulations cater to various applications by providing diverse properties, such as increased durability, improved corrosion resistance, and enhanced visual aesthetics.
Specialty powders with lower curing temperatures can expand the range of materials that can be coated. Additionally, with the rise of environmentally friendly coatings, manufacturers are increasingly producing powders that are solvent-free, reducing VOC emissions and meeting stringent regulations.
The use of hybrid formulations also presents opportunities for innovation. Combining different powder types can lead to coatings that harness the advantages of each component, resulting in superior performance and functionality.
Automation and Control Systems
Automation is transforming the powder coating landscape. Advanced control systems allow for real-time monitoring and adjustments during the coating process. This leads to increased precision in application and curing, ultimately resulting in higher quality products. Automation can minimize human error and ensure consistent results across production
Modern powder coating facilities employ robotic arms equipped with intelligent systems to optimize the application process. These robots can adjust parameters such as spray angle, speed, and coating thickness, contributing to improved uniformity and reduced waste. Automated temperature controls further enhance the curing phase by maintaining optimal conditions, which are crucial for achieving desired properties in the final product.
Applications of Powder Coating
The applications of powder coating are as diverse as the industries that utilize this technology. Understanding these applications is crucial for grasping how powder coating impacts both product aesthetics and durability. Powder coating offers several advantages over the traditional liquid coating processes. The resulting finishes are often more robust, resist corrosion, and maintain color integrity over time. Additionally, the application method generates less waste, making it a more environmentally friendly choice.
In production settings, powder coating is often employed to enhance operational efficiency. The speed at which products can be coated and cured significantly reduces turnaround time. Moreover, the durability of powder-coated surfaces means that they require less maintenance, ultimately lowering costs for manufacturers.
Overall, the significance of powder coating in various fields cannot be overstated. It allows for customization and innovation in design while meeting stringent performance standards.
Industries Utilizing Powder Coating
Many industries have adopted powder coating as a standard practice. This adoption is due to the distinct benefits it offers in terms of performance and sustainability. The following industries are particularly noteworthy:
- Automotive: Powder coating provides a tough finish that is necessary for vehicles, allowing for protection against scratches and rust.
- Furniture: Coated furniture not only looks good but also resists chips and wear, making it ideal for both indoor and outdoor use.
- Manufacturing: Industrial machinery parts often undergo powder coating to enhance their lifespan and performance.
Automotive Applications
In the automotive sector, the demands for quality and performance are critical. Powder coating serves several functions, such as providing a decorative finish and offering protection against the elements. Engine components, wheels, and bumpers are commonly powder coated.
The process allows for seamless coating over complex geometries, ensuring that every surface is protected. Additionally, this method is more environmentally friendly compared to traditional paint systems, as it generates minimal volatile organic compounds (VOCs).
Architecture and Design
In architecture and design, powder coating plays a vital role in providing aesthetic appeal. Architectural elements such as railings, window frames, and façade systems often feature powder-coated finishes. The variety of colors and textures available allows architects to achieve specific design visions while ensuring durability and weather resistance.
Furthermore, powder-coated surfaces require less maintenance and are resistant to fading, making them suitable for long-term applications. As the trend towards sustainable building practices grows, powder coating offers an attractive solution due to its environmentally friendly characteristics.
In summary, the applications of powder coating reach into various industries, each benefiting from the unique properties of powder coatings, which enhance both the functionality and aesthetic appeal of products.
Challenges in Powder Coating
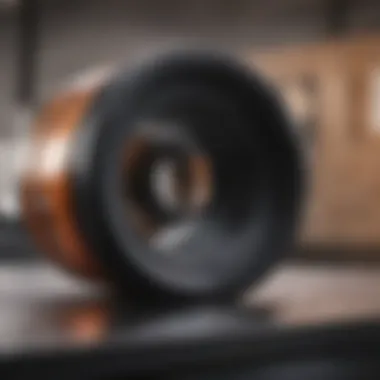
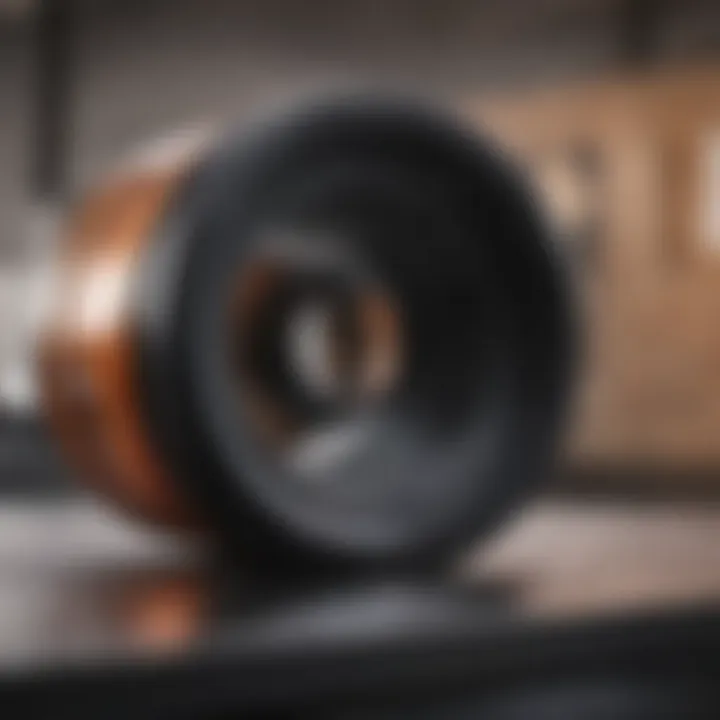
Understanding the challenges in powder coating is essential for both new and experienced professionals in this field. This section brings attention to the difficulties that may arise during the heating and application processes. These challenges can significantly affect the quality and durability of the coating. Additionally, it is important to recognize how these issues influence production efficiency and cost-effectiveness in various applications.
Common Issues with Heat Transfer
Heat transfer is a critical factor in the success of any powder coating process. If not managed properly, it can lead to undesirable outcomes, including defects and inconsistencies in the coating. Here, we explore two prominent issues in heat transfer during the powder coating process: defects and inconsistency.
Defects
Defects in powder coatings occur when the heat transfer dynamics do not align with the requirements of the coating material. Common defects include orange peel, bubbling, and poor adhesion. These defects contribute to overall quality issues, making them a significant focus for quality control. The key characteristic of defects is their visibility. For instance, orange peel can compromise aesthetic appeal, while poor adhesion can affect durability.
Understanding the root causes of defects often involves analyzing the heating process. One unique feature is that defects not only impact the visual quality but also the functional performance of the coated product. If the heat is insufficient or uneven, it may lead to incomplete curing, which diminishes the effectiveness of the coating. This can be considered a disadvantage in terms of production integrity and customer satisfaction.
Inconsistency
Inconsistency in the powder coating finish can arise from various factors, including variable heating times and uneven temperature distribution across surfaces. This challenge affects the uniformity of the coating. The key characteristic of inconsistency is its variability; coatings applied in different batches may yield different results, which becomes a problem for manufacturers aiming for high standards. Inconsistency can often lead to rejection rates that increase manufacturing costs.
The unique feature here is that even small discrepancies in heat application can lead to significant differences in color, thickness, or texture. These variations present both advantages and disadvantages. For instance, while inconsistencies can lead to creative finishes, they can also hinder batches from meeting strict quality standards.
Environmental Regulations
With the rising focus on sustainability, environmental regulations impose additional challenges on powder coating operations. These regulations govern emissions and waste management during the processes. Companies must ensure they comply with local, national, and international regulations to avoid penalties and promote environmentally friendly practices. Understanding these requirements is critical for achieving both compliance and market competitiveness.
Material Limitations
Material limitations can also present challenges in powder coating. Not all substrates can withstand high temperatures, restricting the choice of coatings that can be applied. For instance, some plastics may warp under excessive heat. This limitation requires careful material selection during the powder application phase. Understanding material properties is crucial for achieving optimal results in powder coating, and it necessitates a balance between functionality and thermal compatibility.
By addressing these challenges thoughtfully, manufacturers can enhance the performance and sustainability of their powder coating processes. This deep understanding is fundamental for any organization aiming to optimize coating applications.
Future Trends in Powder Coating Technologies
The evolution of powder coating technologies is pivotal to maintaining efficiency and effectiveness in various industries. In this section, we will explore recent advancements that shape the future of this field, focusing on emerging technologies, sustainability considerations, and market growth predictions. Understanding these trends helps stakeholders adapt and innovate, ensuring they remain competitive.
Emerging Technologies
Several new technologies are arising in powder coating processes. These advancements enhance quality and reduce costs. For instance, high-speed coating methods such as electrostatic spraying are gaining traction. This technique increases transfer efficiency while minimizing waste. The development of smart coating systems is another valuable trend, utilizing sensors and data analytics to optimize the curing process. These systems continuously monitor temperature and humidity, enabling adjustments in real time.
Additionally, 3D printing technology integrated with powder coating provides opportunities for customized solutions. This combination allows for precision applications, making it feasible to produce complex geometries with excellent surface finishes. As industries seek to enhance performance and capabilities, these emerging technologies present significant advantages.
Sustainability Considerations
Sustainability is becoming essential in powder coating operations. As regulations tighten and consumers demand environmentally friendly products, the industry must adapt. One approach is the development of low-emission powder coatings. These products reduce the release of volatile organic compounds (VOCs) during application, aligning with environmental standards. Furthermore, manufacturers are exploring bio-based resins that offer superior performance without compromising ecological integrity.
Recycling processes are also an area of focus. The potential to reclaim and reuse overspray from powder coating applications significantly reduces waste and cuts costs. Implementing closed-loop systems can enhance resource efficiency across production lines. In essence, sustainable practices are crucial for future powder coating technologies.
Predictions for Market Growth
The powder coating market is poised for steady growth. Current trends suggest an expansion driven by various factors. The automotive industry continues to embrace powder coating for its durability and aesthetic appeal. As electric and hybrid vehicles increase, the demand for advanced coatings rises. Similarly, sectors like architecture and home improvement are recognizing powder coating’s benefits, driving adoption rates.
Market research indicates the global powder coating market will grow at a compound annual growth rate (CAGR) of around 6% over the next few years. Consumers are increasingly valuing durability, environmental safety, and efficiency when selecting coating solutions. This ensures a robust demand for innovative powder coating technologies.
The integration of emerging technologies, sustainability efforts, and an optimistic market outlook coalesce to create a vibrant future for powder coating.
Closure
In concluding this exploration of heat transfer in powder coating, it is critical to emphasize the role this subject plays in the efficiency and performance of coating operations. The understanding of heat transfer mechanisms significantly influences not just the quality of the powder coating but also the operational efficiency of the processes involved. As industries continue to evolve, optimizing heat transfer will be key to ensuring products meet higher performance standards.
Summary of Key Points
- Heat Transfer Mechanisms: Understanding conduction, convection, and radiation is essential. Each mechanism plays a unique role in the curing process of powder coatings, affecting bond strength and finish quality.
- Influence of Materials: The type of substrate greatly influences heat transfer rates. High conductivity materials facilitate better coating adhesion and improved performance.
- Environmental and Process Factors: Variables like humidity and ambient temperature can alter heat transfer efficiency. Monitoring these factors during application is essential to avoid defects and maintain coating integrity.
- Advanced Techniques: Innovations such as alternative formulations and automation in the application process enhance heat transfer and overall coating quality.
- Future Considerations: The trajectory toward sustainability and market growth suggests a greater need for efficient heat transfer processes in powder coating technologies.
Final Thoughts on Heat Transfer in Powder Coating
As discussed, the intricate relationship between heat transfer and powder coating cannot be overstated. Not only does efficient heat transfer enhance the application quality, but it also opens pathways to innovation and improvement within industries. In a competitive market, companies that prioritize advanced techniques and meticulous attention to thermal dynamics will likely outperform others.
Moreover, consideration of environmental regulations and sustainability trends will become increasingly crucial. As the industry shifts, adapting to these changes while optimizing heat transfer can lead to significant benefits. Through an informed approach to heat transfer in powder coating, industries can not only improve product quality but also minimize waste and increase operational sustainability.
"Understanding heat transfer is not just a technical necessity, but a strategic advantage in powder coating processes."
With ongoing research and development, the possibilities to enhance heat transfer effectiveness are continually expanding, making this a dynamic field worthy of further exploration.