Exploring the Impact and Innovations of Injection Moulding
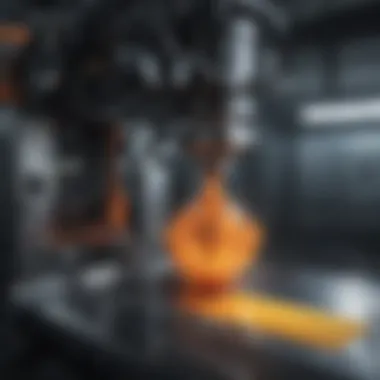
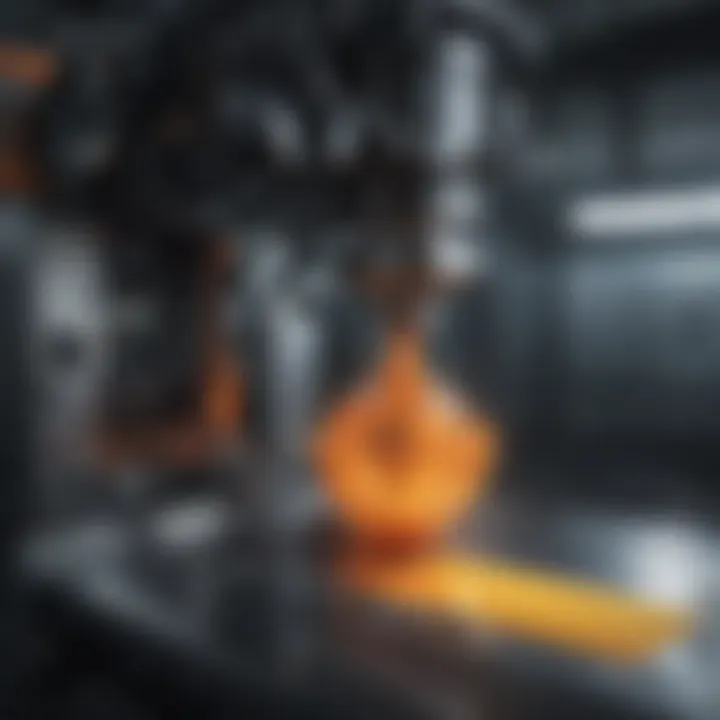
Intro
Injection moulding, as a manufacturing technique, serves as the backbone for a multitude of products we often take for granted. It's fascinating to think about how this process shapes everything from automobile parts to household items. A machine meticulously molds heated material into precise shapes, creating functional pieces from the ground up. With such a broad reach across industries, one can appreciate the engineering marvel that lies at the heart of our daily lives.
This article aims to pull back the curtain on injection moulding—a process that not only revolutionizes manufacturing but also ensures efficiency and consistency. By delving into its fundamental principles, the various materials employed, and the diverse array of products that emerge from it, we can better understand its significance. As we traverse this subject, we will also touch on important aspects such as the environmental impact of this process and the innovative products that are continuously being developed.
Embarking on this exploration reveals not just the mechanics, but also the mind-bending ingenuity that underpins much of the plastic world around us. Whether you are a student wanting to grasp manufacturing basics or a seasoned professional in search of deeper insights, this article offers a treasure trove of information about a vital technique that has made a permanent mark on modern production.
Understanding Injection Moulding
Injection moulding stands as a cornerstone of modern manufacturing, deeply influencing a myriad of industries. Its significance can hardly be overstated. At its core, understanding the process of injection moulding provides insights into how diverse products—ranging from everyday items to complex components—come to life. This section aims to break down the foundational elements of injection moulding, contemplating its benefits and considerations that make it a preferred method in contemporary production.
Definition of Injection Moulding
Injection moulding is essentially a manufacturing process that involves injecting molten material into a mould to create a specific shape. This method often employs materials like thermoplastics, thermosetting plastics, and elastomers, tailored for various applications. When one thinks about the toys children play with or the intricate parts found within appliances, it becomes clear that injection moulding is the invisible hand that shapes these products.
In its simplest form, the process can be understood as taking raw material, heating it until it becomes liquid, and forcing it into a mould. Once the material cools and solidifies, the finished product emerges. This method's efficiency is rooted in speed, precision, and scalability, thus making it indispensable for high-volume production. In short, injection moulding transforms raw materials into functional and intricate designs with remarkable consistency.
Historical Context
The inception of injection moulding dates back to the mid-19th century. Initially, it was a hand-operated process crafted to shape materials such as ivory and wood. An example can be found in the year 1868 when John Wesley Hyatt patented a machine that could inject material into a mould. This breakthrough marked a significant shift in how products were manufactured, allowing for more intricate designs that were previously unthinkable.
Over the decades, the development of synthetic plastics—especially post-World War II—revolutionized injection moulding. As materials evolved, so too did the machines, integrating advanced technologies to increase production efficiency and precision. Today’s injection moulding machinery harnesses computer controls and automated systems, vastly improving both speed and quality while reducing waste. Understanding this rich history helps grasp the current innovation trajectory within the injection moulding sector and sheds light on future potentials.
Mechanics of the Injection Moulding Process
Understanding the mechanics of injection moulding is crucial to grasp how this innovative manufacturing method operates and influences various industries. This section dives into the essential phases of the mechanical process involved in injection moulding, shedding light on its operational intricacies, advantages, and the considerations that come into play throughout the procedure. The injection moulding process not only enables the mass production of precise and detailed components but also underscores efficiency, thereby playing a significant role in industries ranging from consumer goods to automotive parts.
Phase One: Material Preparation
Material preparation is the first step in injection moulding, setting the stage for everything that follows. It involves converting raw materials—primarily thermoplastics, thermosets, and elastomers—into a form suitable for melting and injection. This phase includes drying and feeding the material into the hopper, which serves as the starting point of the manufacturing process.
Drying is particularly important for hygroscopic materials, as absorbed moisture can lead to defects like bubbles or weak spots in the end product. Materials should be processed in a fully controlled environment since even a small amount of moisture can derail the entire process and compromise product quality.
Once the materials are ready, they flow into the barrel where they are heated, preparing them for the next phase—ready to be injected into the mould with precision.
Phase Two: Injection
After the materials are adequately prepared, they move on to the injection phase. This is where the magic happens. The heated material is injected into a closed mould at high pressure through a nozzle. This pressure is critical, as it ensures that every nook and cranny of the mould fills completely.
Think about it: a good injection will define product intricacy. The design of the mould and the speed of the injection can greatly influence the final product’s quality. The process has to be tightly controlled, as variations in pressure, temperature, or speed can lead to defects or unintended variations in the components. In devices like bottles or containers, for instance, tiny differences can hugely impact functionality and aesthetics.
Phase Three: Cooling
Cooling forms the bridge between injection and ejection, acting as a fundamental step to solidify the newly formed plastic. This phase involves circulating cooling water through channels within the mould to hasten the solidification of the injected material.
The timing is everything. If the cooling is too quick, it can lead to surface defects, while slow cooling may take forever and reduce entire production efficiency. Depending on the material and the complexity of the part, cooling times may vary. For intricate parts, this step requires meticulous planning and management to ensure that the product maintains its shape and structural integrity as it hardens.
Phase Four: Ejection
Finally, we arrive at the ejection phase, where the cooled and solidified product is ejected from the mould. A series of ejector pins usually extend to push the item out once it has sufficiently cooled.
It’s often an underappreciated phase, but the ejection process can be quite delicate. Too much force can damage the product while too little might leave it stuck in the mould. Moreover, the timing overlaps with the cooling phase to optimize production cycles.
In sum, understanding these phases offers invaluable insights into the mechanics of injection moulding. Each step contributes its part to the final quality of the product, from material preparation to successful ejection. Recognizing how these elements interact is vital for anyone engaged in, or learning about, this versatile production method.
Materials Utilized in Injection Moulding
The materials selected for injection moulding play a critical role in determining the quality, functionality, and performance of the end products. Understanding these materials can help industries optimize their manufacturing processes and enhance the characteristics of the products they create. Each type of material brings its unique attributes and challenges, fueling the diversity within the injection moulding landscape.
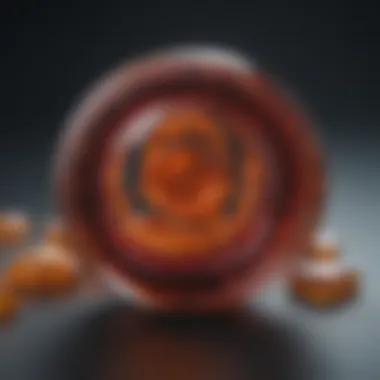
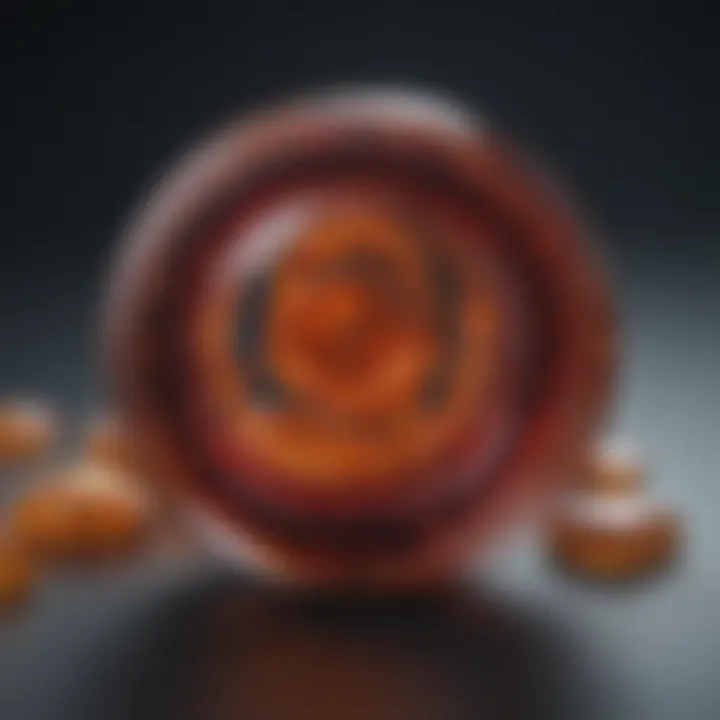
Thermoplastics
Thermoplastics are arguably the most widely used materials in injection moulding. These materials are fantastic because they can be heated and reshaped multiple times without undergoing any significant chemical change. This property not only allows for greater flexibility in design but also makes recycling easier than other types of plastics.
Some common thermoplastic materials include polypropylene, polyethylene, and polystyrene. They are widely used in manufacturing various consumer goods due to their excellent durability and relatively low cost.
Consider polycarbonate, a type of thermoplastic used in everything from safety glasses to automotive parts. Its remarkable strength and optical clarity make it an ideal choice for items that need to withstand high impact or require transparency. The ability to mold it under high pressure while keeping its necessary properties intact has made it a go-to choice for many industries.
In terms of production efficiency, thermoplastics allow for faster production cycles. The rapid heating and cooling in the injection process result in shorter cycle times, leading to a more cost-effective manufacturing workflow.
Thermosetting Plastics
Unlike thermoplastics, thermosetting plastics undergo a curing process that changes their physical properties permanently. Once set, these materials cannot be remolded or reheated. This characteristic lends thermosetting plastics exceptional strength and thermal resistance, making them suitable for more demanding applications.
Common examples include epoxy resins and melamine formaldehyde. Epoxy resins, for instance, serve well in electrical components and adhesives due to their excellent adhesive properties and resilience to heat.
One significant advantage of thermosetting plastics is their longevity and ability to withstand various environmental factors without degrading. In applications such as automotive components or components for electronics, this added durability translates into more reliable performance over time.
Elastomers
Elastomers are a unique category of materials that combine the properties of rubber with those of plastic. These materials are extremely versatile. They offer high elasticity and flexibility, making them especially valuable in applications where some stretch or deformation is necessary.
Common elastomers used in injection moulding include thermoplastic elastomers (TPE) and silicone elastomers. TPEs are often used in the grips of tools and various consumer products, offering a soft touch and a comfortable grip. Silicone, on the other hand, finds its way into medical devices and kitchenware due to its high stability and resistance to extreme temperatures.
It's crucial to note that while elastomers provide these beneficial properties, the moulding process can be slightly different compared to thermoplastics. Careful control of temperature and pressure is essential to ensure that the final product retains its desired characteristics.
Advantages of Injection Moulding
Injection moulding has become a cornerstone in modern manufacturing, but what’s the story behind its growing popularity? The advantages of injection moulding provide a compelling reason for its widespread use in diverse industries. From its efficiency in production to its ability to create complex designs, this technique serves businesses looking for speed, quality, and overall cost reduction.
Efficiency
When it comes to production speed, injection moulding is the gold standard. Once a mould is created, it can be filled with molten material at alarming rates. In fact, during a single cycle, multiple parts can be produced simultaneously, greatly enhancing productivity. This efficiency translates into shorter lead times—a crucial factor for businesses aiming to meet tight deadlines. Companies can turn around large quantities of items in mere hours or days instead of weeks. Furthermore, automation and machinery advancements have made the process even swifter; with the right setups, one machine can operate nearly non-stop, only requiring occasional maintenance.
"Efficiency is about doing better what you already do."
— Peter Drucker
This high throughput not only maximizes production but also optimizes resource use. By minimizing waste during the manufacturing process, companies can enjoy increased profitability. In terms of energy use, injection moulding processes are designed to operate more sustainably than older manufacturing methods, further boosting their appeal.
Precision and Detail
Precision is another standout feature of injection moulding. The ability to create intricate designs with a high level of accuracy opens the door for innovative product development. Thanks to advanced technology, modern injection moulding systems can ensure that every piece is made to exquisite specifications, keeping tolerances tight and consistent. This trait is vital across many sectors, particularly in medical and automotive industries, where precision can be a matter of safety.
Moreover, the complex geometries achievable through this method include features like undercuts, intricate textures, and multi-material components, making it feasible to produce components that would be challenging with other manufacturing techniques. This ability not only adheres to strict design standards but does so with reduced assembly needs.
Cost-effectiveness for Mass Production
The cost-effectiveness of injection moulding shines brightest during mass production. Once a manufacturer has invested in creating a mould—an upfront cost quite justified by subsequent savings—the costs per unit plummet as the volume of production increases. Unlike processes that require multiple manufacturing steps, injection moulding consolidates steps into one, allowing for streamlined operations that save both time and labor costs.
Furthermore, the material efficiency of injection moulding contributes significantly to lowering production costs. When using thermoplastics, for instance, the leftover material from the injection process can often be reused in future runs, making it a circular process that minimizes waste.
Key Applications of Injection Moulding
Injection moulding has permeated various industries, becoming a cornerstone for producing a multitude of products. Its key applications span from everyday consumer goods to complex medical devices, showcasing its versatility and efficiency. Understanding these applications is crucial as it illustrates not only how the process functions but also the benefits it brings to different sectors. The efficiency, precision, and cost-effectiveness inherent in injection moulding make it a preferred method across industries.
Consumer Goods
The realm of consumer goods relies heavily on injection moulding. Products ranging from kitchen utensils, plastic bottles, and household appliances are often manufactured through this method. One prominent example is the production of containers for popular brands like Tupperware. These items require durability, redesign flexibility, and aesthetic customization, all achievable via injection moulding.
Key benefits include:
- Rapid Production: Large volumes of identical items can be generated quickly, ensuring market demands are met.
- Cost-Effectiveness: Once the moulds are created, each subsequent item is produced at a minimal cost.
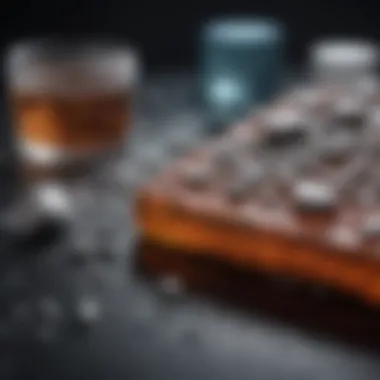
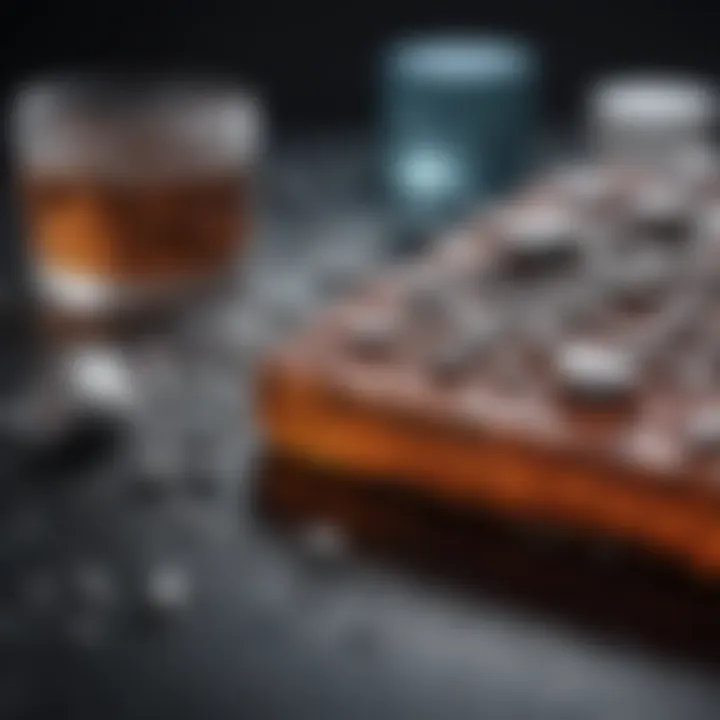
Automotive Components
In the automotive industry, injection moulding is indispensable. Components such as dashboards, interior panels, and even intricate parts like fuel systems benefit from this technology. The production of items like the center console of a Ford Mustang highlights how injection moulding can yield complex shapes while maintaining structural integrity.
Key benefits in this context include:
- Weight Reduction: Plastic components weigh less than metal equivalents, contributing to fuel efficiency.
- Safety and Compliance: The ability to mould parts with specific properties aids in meeting stringent safety standards.
Medical Devices
The medical field also leverages injection moulding for making devices that require both precision and hygiene. Items such as syringes, surgical instruments, and various diagnostic tools are common products of this process. For instance, disposable syringes produced by brands like BD feature precise tipping to enhance user safety and comfort.
In this domain, advantages include:
- High Precision: The capability to produce intricate designs ensures that medical devices perform reliably.
- Cleanliness: The controlled production environment reduces the risk of contamination, essential for medical applications.
Packaging Solutions
Packaging is another crucial application area. Injection moulding facilitates the creation of containers, caps, and closures that are often required in both consumer and industrial settings. For example, products from Coca-Cola or other beverage companies frequently utilize moulded plastic containers that are lightweight yet sturdy.
Key considerations include:
- Customization: Moulding can provide tailored shapes that enhance branding and usability.
- Sustainability: Advances in materials allow for the production of recyclable packaging solutions, addressing environmental concerns without sacrificing performance.
"The versatility of injection moulding not only meets industrial needs but also adapts to modern sustainability expectations."
Through these applications, it’s clear that injection moulding is more than just a manufacturing process; it shapes how we use and interact with products daily. Its significance in various sectors presents considerable scope for innovation without compromising on quality.
Notable Products Created via Injection Moulding
Injection moulding serves as a cornerstone of modern manufacturing, producing a myriad of products that permeate our daily lives. It offers design flexibility and efficiency, making it a go-to choice for creating high-volume items. In this section, we will explore three notable categories of products created through injection moulding: plastic containers, toys, and electronic housings. Each product type showcases the versatility and significance of injection moulding in various industries.
Plastic Containers
Plastic containers are ubiquitous in households and industries alike, from food storage to industrial applications. Injection moulding is pivotal in their production, allowing for the creation of complex shapes and sizes with high precision. These containers, often made from durable thermoplastics such as polypropylene and polyethylene, have several notable benefits:
- Lightweight and Durable: They are easy to handle and resistant to breakage, making them practical for transport and storage.
- Cost-Effective: Mass production through injection moulding reduces costs significantly, making them accessible to consumers.
- Recyclability: Many plastic containers can be recycled, promoting environmental sustainability when managed properly.
From lunchboxes to large storage bins, plastic containers demonstrate how injection moulding meets both consumer needs and environmental considerations. The ability to produce customized designs further enhances their appeal in an increasingly eco-conscious market.
Toys
Toys represent another vibrant realm of products shaped by injection moulding. The manufacturing process allows for highly intricate designs, colors, and textures that captivate children’s imaginations. The safety and durability of these toys are paramount, leading to certain specifications in the materials used. Common benefits include:
- Design Versatility: Complex shapes and features can be created, enhancing play and learning experiences.
- Safety Standards: Manufacturers ensure that materials comply with stringent safety regulations, crucial in the toy industry.
- Affordability: The efficiency of injection moulding translates into lower retail prices for consumers, facilitating mass appeal.
Toys produced through this process range from simple building blocks to advanced electronic playsets, showcasing a mixture of creativity, engineering, and consumer safety that the industry demands.
Electronic Housings
Electronic housings are vital for the protection and durability of devices that we depend on daily, like smartphones and computers. Injection moulding is critical in their production, providing a streamlined process for efficient manufacturing. Key considerations in this category include:
- High Precision: Housings require exact specifications to ensure proper fitting and functionality of electronic components.
- Heat Resistance: Many electronic housings incorporate materials that endure heat and other environmental factors, safeguarding sensitive electronics.
- Aesthetic Appeal: These housings often come in various colors and finishes, aligning with design trends while maintaining functionality.
The importance of injection moulded electronic housings cannot be underestimated—they play a crucial role in consumers’ confidence and satisfaction with their devices. The combination of durability and design meets the complex needs of an ever-evolving technological landscape.
Injection moulding not only optimizes production efficiency but also integrates safety, sustainability, and consumer satisfaction into its core, making innovation possible across multiple sectors.
Environmental Concerns and Alternatives
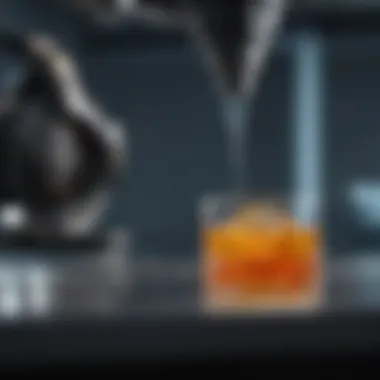
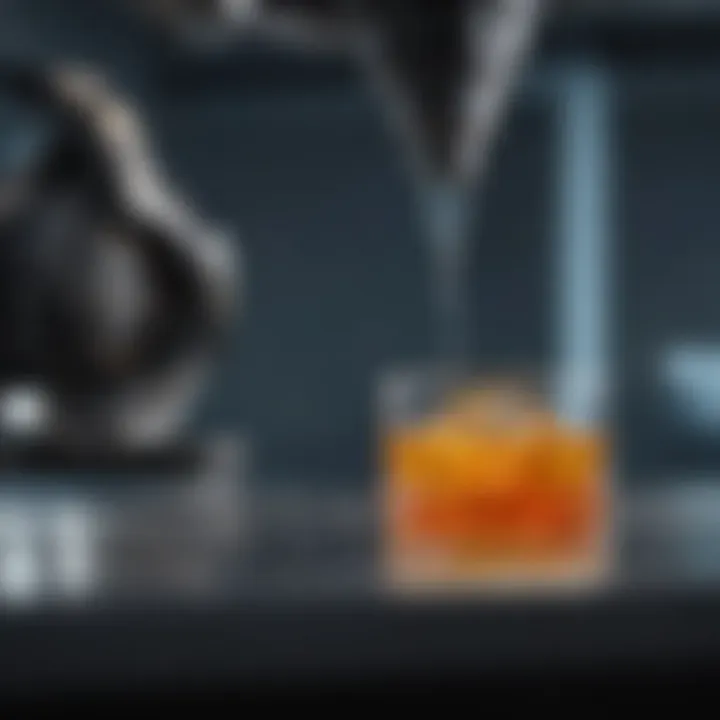
Environmental concerns related to injection moulding have gained traction as awareness of plastic pollution continues to rise. As the industry flourishes, so does the responsibility to address the environmental impact of plastic waste. This section dives into three major aspects: waste management, sustainable materials, and recycling initiatives, each playing a critical role in shaping a more eco-friendly future for injection moulding.
Plastic Waste Management
Plastic waste, a byproduct of injection moulding, poses significant challenges to the environment. A common sight in landfills and oceans, this waste is often slow to decompose and can harm wildlife and ecosystems. Effective waste management strategies are crucial for mitigating these issues. Companies are increasingly adopting practices such as:
- Waste Reduction: Finding ways to minimize leftover materials during production. Techniques like optimizing designs and layouts can lead to less waste at the outset.
- Reusing Scraps: Some manufacturers carefully repurpose and recycle excess materials during the injection moulding process, reducing the amount that becomes waste.
- Correct Disposal: Educating both consumers and manufacturers about proper disposal techniques is key. This involves ensuring that plastic products are disposed of correctly to facilitate recycling.
Effective plastic waste management not only helps in lessening the burden on ecosystems but also generates a positive impact on a company's bottom line.
Sustainable Materials
The shift toward sustainable materials is vital in making injection moulding a greener process. This doesn't just mean substituting traditional plastics with biodegradable options. It also involves embracing a holistic approach that encompasses:
- Bioplastics: Derived from renewable resources, these materials decompose more easily than conventional plastics. They hold promise for both consumer goods and industrial applications.
- Post-consumer Recycled Plastics: Using plastics that have already been in circulation cuts down on new resource extraction and processing. Products made from recycled materials help close the loop in the plastic lifecycle.
- Environmentally Friendly Additives: The inclusion of certain additives can improve the properties of biodegradable plastics, making them a viable choice for various applications.
Contemporarily, manufacturers are under pressure from both consumers and regulations to adopt these sustainable alternatives. This not only decreases the reliance on fossil fuels but enhances the public image of brands committed to environmental stewardship.
Recycling Initiatives
Recycling initiatives serve as a crucial pillar in tackling the plastic crisis linked to injection moulding. Engaging localities and ecosystems in the recycling process can yield impressive results. Key components of these initiatives include:
- Collection Programs: Implementing robust collection systems ensures that more plastic waste can be captured for recycling. It’s about making it easier for individuals and businesses to return their plastic products.
- Education Campaigns: Awareness programs that educate the community about the significance of recycling can drive participation. Knowledge is power, and when people understand the benefits, they are more likely to engage.
- Investment in Technology: Advanced recycling technologies are being developed to improve the efficiency of plastic recycling. From chemical recycling to enhanced sorting systems, innovation plays a pivotal role in recovery rates.
"With higher recycling rates, we not only divert plastics from landfills but also minimize the need for virgin materials, directly impacting environmental degradation."
In summary, each layer of concern offers both a challenge and an avenue for improvement. By focusing on effective waste management, shifting toward sustainable materials, and implementing impactful recycling strategies, the injection moulding industry can align itself more closely with a sustainable future. Readers, be it students or professionals, should understand that the way forward lies in these multifaceted approaches to addressing environmental concerns.
Future Trends in Injection Moulding
As we stroll into the era of modern manufacturing, the relevance of understanding future trends in injection moulding cannot be overstated. This segment reveals how advancements in technology, coupled with shifting consumer demands, shape the landscape of injection moulding. These trends not only enhance efficiency but also promise sustainable practices that resonate well with environmental considerations.
"The future belongs to those who believe in the beauty of their dreams." — Eleanor Roosevelt
Technological Advancements
The brainchild of the injection moulding industry lies in its technological advancements. From automated processes to sophisticated software, innovations are spilling over like a cup full of hot coffee. One significant advancement includes the integration of artificial intelligence. AI-driven machines can analyze production processes in real-time, which helps in optimizing resource use and reducing waste.
Another noteworthy change is the advent of 3D printing and additive manufacturing. While traditionally seen as a rival to injection moulding, it now complements this process. Manufacturers are harnessing 3D printing for rapid prototyping, enabling quicker revisions and significantly shorter lead times before actual production begins.
Moreover, IoT (Internet of Things) is steadily making waves. Industry 4.0 is ushering us into a realm where smart machines communicate with each other, streamlining operations further. Sensors embedded in machines gather data that can predict maintenance needs, thus preventing downtime and prolonging machinery life.
Customization and Rapid Prototyping
In a world where cookie-cutter solutions just won’t cut it, customization emerges as a powerful trend in injection moulding. Consumers today seek products that cater to their individual preferences, and manufacturers are stepping up to the plate. The agility of injection moulding allows for specialized designs without sacrificing efficiency.
Rapid prototyping is perhaps the most thrilling aspect. It allows designers and engineers to create and test products swiftly. For instance, a new toy design can be molded in a matter of days rather than weeks. This not only lowers costs but also brings products to market faster than a cheetah on its feet.
Additionally, the focus on small batch production is growing. Unlike the old days where high volumes were the name of the game, manufacturers are now able to offer limited runs of unique items efficiently. This flexibility keeps businesses nimble and ready to adapt in an ever-changing market.
Finale
The exploration of injection moulding throughout this article has clarified its significance in modern manufacturing. This technique is not merely a method but a cornerstone of producing a myriad of products that we encounter daily. Understanding the mechanics and applications of injection moulding allows stakeholders—from businesses to consumers—to appreciate the innovation behind the products that enhance our lives.
Summation of Key Findings
In summary, several key points arise from our deep dive into injection moulding:
- Versatility: This process can create a wide range of shapes and sizes, making it applicable across diverse industries including automotive, consumer goods, and medical devices.
- Material Variety: The ability to use different materials such as thermoplastics, thermosets, and elastomers affords manufacturers the flexibility to design products tailored to specific functionalities and market needs.
- Efficiency and Cost-effectiveness: The automated nature of injection moulding leads to reduced labor costs and shorter production cycles, making it a preferred choice for mass production.
- Environmental Perspectives: Though challenges such as plastic waste persist, efforts in recycling initiatives, sustainable materials, and innovations in the field offer pathways toward greener solutions.
The Future of Injection Moulding
Looking ahead, the future of injection moulding is poised for transformation driven by:
- Technological Advancements: Innovations in machine design, automation, and software will likely streamline processes further, improving precision and reducing energy consumption.
- Customization and Rapid Prototyping: With the rise of demand for specialized products, the capacity for rapid prototyping will enable companies to respond swiftly to market demands, employing injection moulding to create unique, client-specific designs.
In the grand scheme, the evolution of injection moulding reflects broader trends within manufacturing—where efficiency, sustainability, and customization become paramount. The insights garnered from this discussion reiterate the importance of adapting to these trends, ensuring that injection moulding not only persists but thrives in contributing to a sustainable future.