Understanding Lean Systems in Operations Management
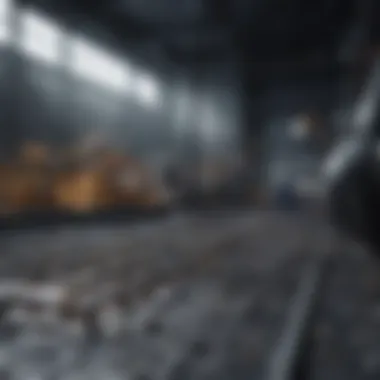
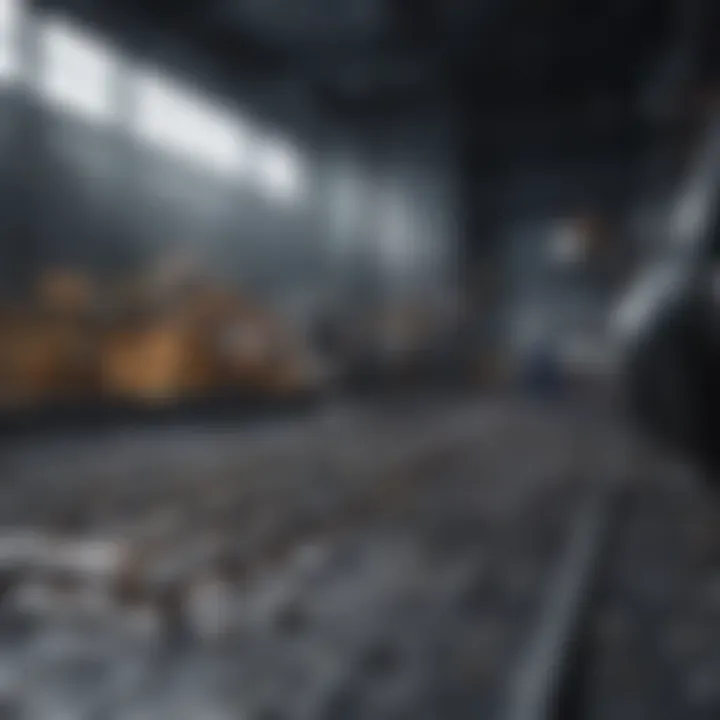
Intro
Operations management has long been the backbone of efficiency and productivity in various industries. At the core of this discipline lies the pursuit of streamlined processes and minimized waste. Among the techniques that have emerged to optimize operations, lean systems stand out for their focus on value creation through the elimination of non-value-adding activities. This article seeks to shed light on the principles, practices, and applications of lean systems in operations management, examining their evolution and current relevance.
Background and Rationale
Lean systems have their roots in the Toyota Production System, which revolutionized manufacturing practices in the mid-20th century. The primary goal was to maximize customer value while minimizing waste. In essence, lean methodologies encourage organizations to evaluate every step of a process, identifying what adds value and what does not. As industries evolve, these principles have been adapted beyond manufacturing to sectors like healthcare, service industries, and more.
The rationale behind adopting lean systems is clear. Companies often face mounting pressures to enhance efficiency and cut costs without sacrificing quality. By employing lean principles, organizations can not only boost productivity but also foster a culture of continuous improvement.
"Adopting lean is not just about reducing waste; it's about building a mindset that strives for constant enhancement and learning."
Literature Review
A wealth of academic research supports the significance of lean systems in operations management. Scholars have analyzed various methodologies, tools, and techniques, such as Value Stream Mapping, 5S, and Kaizen. Each of these tools aims to streamline processes and enhance efficiency. Through literature review, it becomes evident that while lean systems promote significant gains in operations, they also bring challenges during implementation. Resistance to change, lack of top-management support, and insufficient training are commonly cited obstacles.
Several case studies demonstrate the practical implications of lean systems. For instance, organizations like Boeing and Virginia Mason Medical Center have showcased remarkable transformations by integrating lean principles into their operations. These real-world examples underline the need for tailored strategies that suit specific organizational contexts.
Recognizing both the benefits and potential hurdles can guide professionals and researchers in effectively implementing lean systems in their organizations and studies. The ensuing sections will delve deeper into the methodologies and real-world applications, offering a clear insight into how lean principles can be harnessed in addressing contemporary challenges in operations management.
Prologue to Lean Systems
In today’s fast-paced business environment, understanding lean systems is paramount for any organization aiming to increase efficiency and reduce waste. Lean methodologies are not just a set of practices; they represent a mindset that can transform the entirety of operations management. By delving into these systems, businesses can discover innovative ways to enhance their processes, minimize costs, and increase customer satisfaction. What’s more, implementing lean principles can lead to a more engaged workforce, as employees feel empowered to make improvements and contribute to the organization's success.
Definition of Lean Systems
Lean systems, at their core, focus on creating value for customers while minimizing waste in every aspect of production processes. The essence of lean lies in understanding what adds true value from the customer’s perspective and then optimizing all operations to ensure that every step in the process contributes directly to that value.
This approach originated in the manufacturing sector, particularly through the Toyota Production System, which sought to streamline production by eliminating non-value-added activities. Imagine a restaurant kitchen where every unnecessary step, like running back and forth for ingredients, is eliminated; the end result is more time spent on delighting customers rather than tedious tasks. Lean systems encapsulate this ideal, aiming to transform all processes accordingly.
Historical Context of Lean Practices
The roots of lean practices stretch back to the post-World War II era when Japanese manufacturers, facing limited resources, needed to find ways to compete with more established Western industries. This led to the birth of 'Just-in-Time' production and other methodologies aimed at maximizing efficiency.
As the world moved into the latter half of the twentieth century, companies like Toyota innovated by focusing on customer satisfaction and continuous improvement, establishing practices that prioritize flexibility and responsiveness over sheer volume. The message was clear: efficiency is not just about doing more with less but also about being smarter with how operations are managed. The success of these practices soon spread beyond Japan, influencing global industries and leading to the widespread adoption of lean principles across various sectors, including healthcare and service industries.
"The lean approach illustrates that you don’t always need more resources; often, you just need a new perspective."
This historical context not only establishes the foundation for lean systems but also emphasizes their relevance in modern operations management, showing that these principles can adapt and evolve to meet contemporary challenges.
Core Principles of Lean Management
The core principles of lean management form the backbone of systems that aim to increase efficiency, reduce waste, and enhance productivity within organizations. Rather than just a set of tools, lean management encompasses a philosophy grounded in continuous improvement and value creation. By delving into these core principles, organizations can navigate the complexities of their operations while still achieving their goals. This section highlights the significance of each principle and how they interconnect to form a cohesive strategy.
Value Identification
Understanding what constitutes value from the customer's perspective is paramount in lean management. Value identification is about distinguishing between activities that add value and those that don’t. A product or service is considered valuable if it meets the needs and wants of the customer in a way that they are willing to pay for.
- Customer Focus: Companies must place customers at the center of their operations. Without knowledge of what the customer values, efforts to improve efficiency might miss the mark.
- Differentiation: Identified value helps an organization create a unique selling proposition. For instance, when a company realizes that customers prioritize fast delivery over free returns, it can shift its focus accordingly.
By clearly defining value, organizations will allocate resources toward high-impact activities and set a foundation for subsequent lean efforts.
Value Stream Mapping
Value stream mapping is a powerful tool that visually represents the flow of materials and information required to bring a product or service to the customer. It helps identify inefficiencies and opportunities for improvement.
- Visual Representation: It’s like drawing a roadmap. By outlining each step in the process, teams can see where value is generated and where waste occurs.
- Collaboration: Creating a value stream map usually involves cross-functional teams. Such collaboration enhances understanding across different departments by having everyone visualize the process together.
- Link to Lean Tools: This mapping sets the stage for using specific lean tools to address issues identified in the flow.
This practice fosters a team-oriented approach and provides insights that might not be apparent from individual perspectives.
Eliminating Waste (Muda)

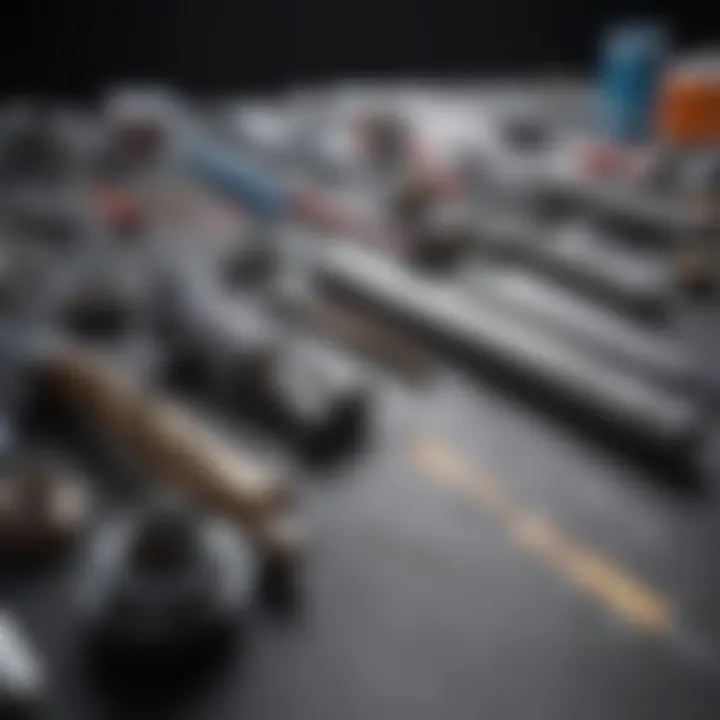
Waste, or muda, is a core concept in lean management. Lean emphasizes the relentless pursuit of eliminating anything that doesn’t add value. The different types of waste include overproduction, waiting, excess inventory, and defects, among others.
- Continuous Focus: Regularly assessing processes can lead to identifying wastes that might otherwise be overlooked.
- Cultural Mindset: Encouraging employees at all levels to spot and eliminate waste fosters a culture of awareness and responsibility.
- Examples: A classic example of waste elimination is a manufacturing line that discovers it holds too much inventory, tying up resources. By reducing inventory, the company can also minimize storage costs and improve cash flow.
By focusing on waste, organizations not only enhance efficiency but also significantly cut costs.
Continuous Improvement (Kaizen)
The principle of continuous improvement, known in Japanese as kaizen, is about making incremental changes that lead to significant benefits over time. It centers on the idea that organization's operations can always be enhanced.
- Small Steps Matter: Rather than seeking dramatic overhauls, companies are encouraged to adopt a mindset where even minor adjustments are valuable.
- Engagement: It involves everyone from the shop floor to executive leaders in suggesting changes. This empowerment creates a sense of ownership and engagement among employees.
- Problem-Solving culture: With an emphasis on being proactive, individuals learn to address issues quickly rather than allowing them to fester.
Integrating kaizen into daily operations embeds a culture of perpetual learning and adaptability.
Lean Tools and Techniques
Lean tools and techniques are foundational elements in the realm of operations management that significantly enhance efficiency and effectiveness in various processes. Implementing these strategies can help organizations streamline their operations, reduce waste, and improve productivity. Each tool serves a specific purpose and contributes to the overarching goals of a lean system, which are to create more value for customers with fewer resources.
Understanding how to effectively utilize these tools is essential for those in the industry. Here’s a deeper look at some pivotal lean tools.
Just-In-Time (JIT)
Just-In-Time is all about producing what is needed, when it is needed, and in the amount needed. JIT aims to reduce inventory costs by synchronizing production schedules with demand. This technique relies heavily on planning and forecasting to ensure that products are delivered right on time.
One of the main benefits of JIT is the significant reduction in storage costs. By decreasing inventory levels, companies can free up capital that might otherwise be tied up in unsold stock. However, successfully implementing JIT requires meticulous coordination within the supply chain. Suppliers and manufacturers must collaborate closely to ensure seamless delivery of components and materials.
5S Methodology
The 5S methodology is a structured approach to organizing the workplace and maintaining cleanliness. It revolves around five key pillars: Sort, Set in order, Shine, Standardize, and Sustain. Each step plays a critical role in enhancing operational efficiency.
- Sort: Remove unnecessary items from the workspace, which helps reduce clutter.
- Set in order: Organize tools and materials for easy access, streamlining workflows.
- Shine: Regularly clean the workplace to ensure safety and quality.
- Standardize: Develop standards for processes and organizing the workspace to maintain efficiency.
- Sustain: Implement practices to keep everything in order over the long haul.
Using 5S not only boosts productivity but also fosters a culture of continuous improvement by ensuring that the workplace remains efficient and effective.
Kanban Systems
Kanban is a visual management tool that utilizes cards, signals, or boards to track work progress. This system provides a clear picture of what is being worked on, what is completed, and what is pending. By visualizing the workflow, teams can identify bottlenecks, prioritize tasks, and improve processes in real-time.
One of the notable advantages of Kanban is its flexibility. It can be adapted to various types of environments, from manufacturing floors to software development. By managing the flow of work efficiently, organizations can reduce lead times and respond more swiftly to customer needs.
Poka-Yoke Techniques
Poka-Yoke refers to mistake-proofing methods aimed at eliminating errors in processes and systems. The essence of this technique is to design processes in such a way that mistakes are either impossible or immediately detectable.
Implementing Poka-Yoke can manifest in various forms, such as:
- Physical devices that prevent errors, like jigs or fixtures that ensure parts can only fit one way.
- Procedural designs that introduce checks and balances, such as requiring a signature at critical steps.
The impact of Poka-Yoke on productivity and quality is profound. Organizations using these techniques often see a drop in defect rates, boost employee morale, and improve customer satisfaction by delivering higher quality products.
"Lean is not just a toolset but a mindset that focuses on continuous improvement and perfection through the elimination of waste."
Incorporating these lean tools and techniques into operations management lays a solid groundwork for achieving excellence. By focusing on efficiency, waste reduction, and continuous improvement, organizations can significantly transform their operational performance.
Integration of Technology in Lean Systems
The merging of technology with lean systems marks a significant pivot in operations management, redefining how businesses can maximize efficiency and reduce waste. Modern technologies create avenues for smoother workflows, allowing enterprises to rethink traditional processes that may hinder productivity. In this section, we dissect how technology not only supports lean methodologies, but how it can actually elevate their effectiveness to previously uncharted territories.
Role of Automation
Automation acts as a linchpin in integrating technology with lean systems. By mechanizing repetitive tasks, companies free up their workforce to focus on more strategic endeavors, ultimately enhancing productivity.
Some unmistakable benefits of automation in lean practices include:
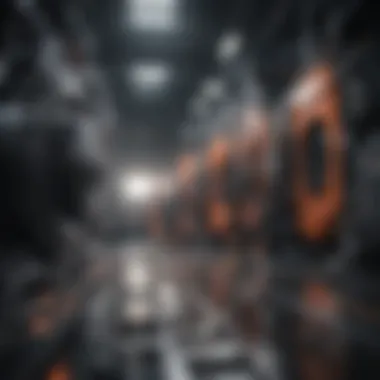
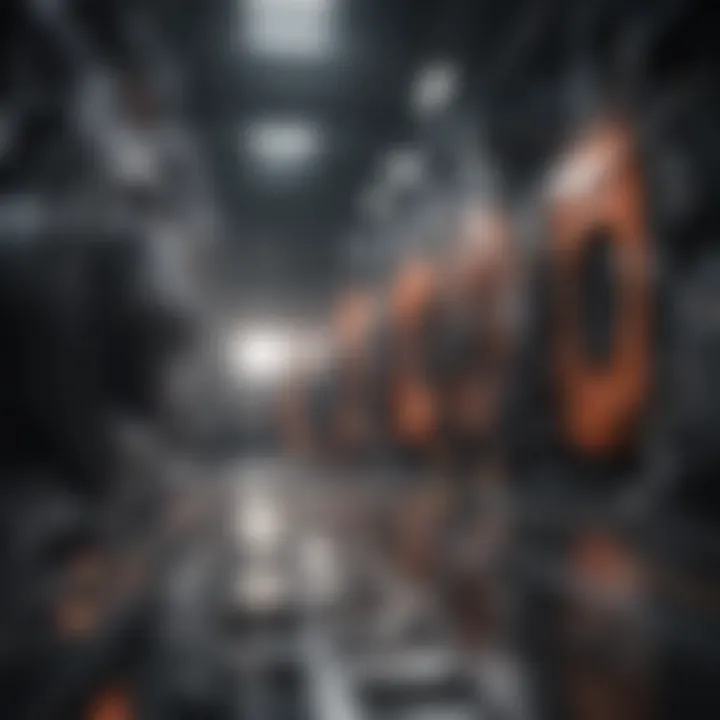
- Time Savings: Automation shrinks the duration of task completion, allowing faster turnaround on projects.
- Reduction of Errors: Machines don’t tire, reducing human error and ensuring consistency in output.
- Resource Allocation: This permits better use of resources, shifting attention from mundane tasks to value-added activities.
For instance, consider a manufacturing plant that adopts robotic process automation for assembly lines. Unlike manual assembly, which can falter due to fatigue, robots operate continuously, maintaining a superior level of quality and efficiency.
Data Analytics and Lean Operations
Data analytics invigorates lean systems by giving organizations the power to make informed decisions based on solid data rather than gut feelings. By harnessing data, firms can pinpoint inefficiencies in their operations that may have previously gone unnoticed.
Here are a few ways analytics contributes:
- Identifying Patterns: By analyzing past performance metrics, it becomes easier to recognize trends that inform future strategies.
- Performance Dashboards: These tools allow managers to visualize key performance indicators, facilitating quicker evaluations.
- Predictive Analytics: With predictive models, companies can anticipate potential bottlenecks before they arise, enabling proactive management.
An example of this is a retail chain that uses customer data to optimize inventory levels. Instead of overstocking based on assumptions, data-driven insights allow for precise ordering, reducing excess inventory and storing costs.
Lean and Industry 4.
Industry 4.0, characterized by the fusion of advanced technologies like IoT, AI, and big data, engenders a new era for lean operations. This paradigm shift encourages an interconnected network where real-time data flows seamlessly from machines directly to decision-makers.
The implications of Industry 4.0 on lean practices are profound:
- Enhanced Visibility: Real-time data feeds allow for immediate responses to issues as they arise, lessening the chances of delays.
- Smart Manufacturing: By integrating smart devices into production lines, firms can achieve more substantial customization and efficiency, adapting output to meet real-time demand.
- Supply Chain Optimization: An interconnected supply chain can drastically reduce lead times and ensure that materials arrive just when needed, aligning squarely with the lean tenet of Just-In-Time.
A pertinent illustration would be an automotive manufacturer using IoT sensors to monitor machine performance. If machines begin to underperform, maintenance can be scheduled before a breakdown occurs, maintaining production flow.
"The integration of technology within lean systems is not merely a trend; it's the future of operations management, where efficiency meets innovation."
Overall, the interplay of technology with lean systems creates an environment primed for continual improvement and operational excellence. For companies eager to stay ahead in a competitive landscape, embracing this synergy is no longer optional but essential.
Challenges in Lean Implementation
Implementing lean systems comes with its fair share of challenges. These hurdles can be both complex and deeply rooted in the fabric of an organization. While the benefits of lean practices—like waste reduction and enhanced efficiency—are well-documented, the journey towards achieving this lean utopia demands careful navigation through several obstacles. Understanding these challenges is essential for businesses aiming to maximize their operational efficiencies while fostering a culture of continuous improvement.
Cultural Resistance to Change
One of the most formidable barriers in lean implementation is often the cultural resistance to change. Employees may feel apprehensive about alterations to their routine practices, fearing that these changes could undermine their roles or workload. This apprehension isn’t just a matter of personal comfort; it’s about losing established norms that offer a sense of stability.
Organizations must engage in open dialogue, encouraging a culture that promotes feedback. For instance, hosting workshops can demystify the lean principles, helping employees see the value from their perspective. It’s like trying to get a group of friends to try a new restaurant; they might be skeptical at first but once they see the benefits of the menu, they usually come around.
Sustainability of Lean Practices
Sustaining lean practices poses yet another challenge. Many organizations, in their eagerness to embrace lean, might initiate changes that fizzle out as soon as interest wanes or leadership shifts. It’s easy to start a new project but keeping the momentum going requires ongoing commitment across all levels of the company.
Leaders must not only champion lean principles but also integrate them into the corporate landscape. This can mean revising standard operating procedures or including lean objectives in performance evaluations. Just as you wouldn’t plant a garden and neglect it, lean systems need nurturing and consistent effort to thrive. The key to sustainability revolves around embedding a culture of continuous improvement where every employee understands their role in maintaining these practices.
Measurement and Metrics
The measurement of lean efforts can be quite intricate, posing yet another roadblock. Without appropriate metrics, how can organizations ascertain whether their lean initiatives are yielding the desired results? Failure to establish clear metrics can lead to misinterpretations of performance, and ultimately, frustration.
Effective metrics should align with lean goals. Organizations can use key performance indicators such as production cycle time and defect rates. Using tools such as value stream mapping can also help visualize where improvements are necessary. Remember, it’s all about knowing where you stand to gauge progress effectively.
"What gets measured gets managed." - Peter Drucker
Adaptation and flexibility are paramount in this regard. It’s essential to continuously assess and adjust metrics as needed, aligning them to evolving company objectives and market needs.
In summary, the challenges in lean implementation are multifaceted. By recognizing cultural limitations, addressing sustainability concerns, and establishing relevant metrics, organizations can navigate these challenges more effectively. Understanding these dynamics will pave the way for a more fruitful adoption of lean practices.
Case Studies of Lean Implementation
Case studies play a pivotal role in understanding how lean systems operate and succeed in various sectors. Studying real-world applications allows us to peel back the layers of theory and examine the nuts and bolts of lean principles in action. These case studies highlight not just successes, but they often uncover challenges and missteps, providing a holistic view of lean implementation. This insight is invaluable for educators, students, and professionals alike who aim to harness best practices while remaining aware of potential pitfalls.
Furthermore, engaging with multiple case studies offers comparative analysis. It reveals patterns and strategies across different industries, thus enriching the overall comprehension of lean systems. Elements like culture, employee engagement, and technological integration emerge as critical factors influencing effectiveness.

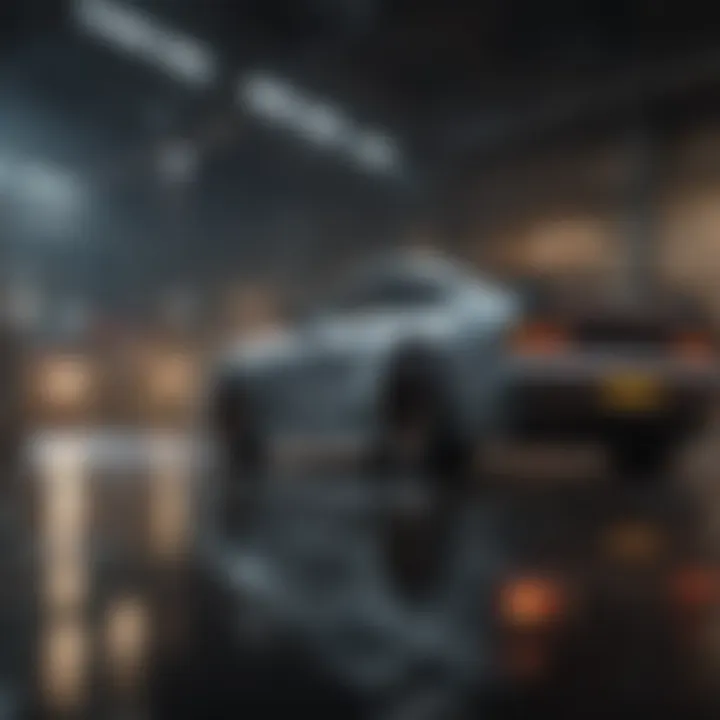
In sum, case studies serve as both a compass and a mirror, guiding organizations in their journey toward lean transformation while reflecting the myriad of realities that accompany such an endeavor.
Manufacturing Sector
Manufacturing often serves as the cornerstone for lean applications. Companies like Toyota have famously woven lean principles into their fabric, showcasing significant successes. For example, Toyota's Production System (TPS) exemplifies how crucial efficiencies can be realized. By focusing on value stream mapping and waste elimination, the company has optimized its production lines, ultimately enhancing quality while minimizing costs.
Another notable instance is GE's implementation of lean principles in their aviation sector. They have employed lean tools to streamline operations, improving lead times and boosting quality metrics significantly. This case illustrates how, in manufacturing, adopting a lean mindset can lead to increased output and, correspondingly, a healthier bottom line.
- Key Factors:
- Emphasis on teamwork and employee empowerment.
- Rigorous quality control through continuous improvement.
- Adoption of flexible manufacturing systems that can adapt to changing demands.
Healthcare Applications
Healthcare is another critical domain where lean systems have found fertile ground. Hospitals and clinics across the globe are turning to lean methodologies to streamline operations and improve patient care. Virginia Mason Medical Center in Seattle is a prime example. By applying lean principles, they minimized patient wait times and altered their processes to focus on patient-centered care.
This shift not only improved patient satisfaction metrics but also showcased how lean practices can lead to reduced operational costs – a win-win situation. Furthermore, healthcare facilities are now using value stream mapping to eliminate non-value adding activities. This ultimately results in improved patient flow and better resource utilization.
- Considerations:
- Need for buy-in from all staff levels, from administration to frontline healthcare providers.
- Education and training on lean concepts are crucial for sustaining improvements.
- Potential resistance due to entrenched organizational cultures.
Service Industries
The service industry is often overlooked when discussing lean approaches, but the principles apply just as effectively here. Companies like Amazon have set the bar high in applying lean systems to their logistics and customer service operations. Lean strategies have streamlined their inventory processes, reduced order fulfillment times, and enhanced overall customer experience.
In consulting firms, implementing lean concepts has transformed project management. For instance, the firm McKinsey & Company has employed lean practices to refine their processes, focusing on delivering value to clients without unnecessary overhead. When applied correctly, the results can lead to better project outcomes, increased client satisfaction, and improved employee morale.
- Advantages:
- Enhanced service delivery times lead to improved client experiences.
- Reduced waste allows organizations to reallocate resources effectively.
- Encourages a culture of continuous improvement among employees.
Ultimately, whether in manufacturing, healthcare, or service industries, the principles of lean systems foster growth through efficiency, but their successful application hinges on a keen understanding of the context and environment in which they are implemented.
The Future of Lean Operations Management
As we look ahead, the significance of lean operations management becomes even clearer. Lean management focuses on the elimination of waste and the enhancement of value creation. In a fast-paced world, organizations are grappling with heightened competition and ever-changing consumer demands. Therefore, lean systems are not just a trend but a critical approach to sustaining operational efficiency and effectiveness.
The future of lean operations management is being shaped by multiple forces, including technological advancements, globalization, and an increasing emphasis on sustainability. These elements converge to influence how organizations apply lean principles, making it imperative for practitioners and scholars alike to stay abreast of what is on the horizon.
Emerging Trends in Lean Practices
A few trends are gaining traction in lean practices, reflecting how organizations adapt to complexities in the modern landscape:
- Digital Transformation: Organizations are increasingly integrating digital technologies into their lean methodologies. Tools such as AI, IoT, and blockchain are streamlining operations, providing real-time data analytics, thus enabling quick decision-making.
- Sustainable Lean: There’s a growing recognition that environmental concerns cannot be overlooked. Lean practices that incorporate sustainability goals are on the rise, shifting the focus toward waste reduction not just in processes but also in resource consumption.
- Agile Practices: Agile and lean methodologies are merging, particularly in sectors where rapid responses to market shifts are necessary. This fusion allows for improved flexibility and quicker adaptation to changes.
“Lean is not a one-time improvement but a continuous journey towards excellence.”
Global Perspectives on Lean Strategies
The concept of lean is not confined to a single geographic region or culture. Different industries across the globe are adopting varied lean strategies, reflecting local values, market conditions, and operational requirements:
- North America: Companies in the automotive sector, like Ford and Tesla, are leveraging lean methodologies to enhance production efficiency and minimize waste. They focus heavily on data-driven decisions.
- Asia: Nations such as Japan have long been pioneers in lean thinking. Modern practices now emphasize a blend of traditional lean principles with innovative tech solutions, catering to evolving market needs.
- Europe: European organizations are increasingly interested in the social dimensions of lean, where employee involvement and workplace culture are emphasized to foster continuous improvements.
In sum, the future of lean operations management is promising with continuous innovation and adaptation. Organizations must be prepared to integrate these emerging trends and perspectives to maintain a competitive edge in a dynamic global landscape.
Culmination
In wrapping up this exploration of lean systems in operations management, it's essential to recognize not just the theoretical frameworks but also the myriad benefits that come with adopting these practices. Lean systems are fundamentally about optimizing processes, which can lead to enhanced productivity and quality across various sectors. By embracing such systems, organizations not only aim to reduce waste but find ways to make every minute and dollar count. This approach is crucial in today’s fast-paced environment, where every competitive edge matters.
Summary of Key Insights
- Efficiency Overhaul: Lean systems significantly boost operational efficiency by focusing on value creation and eliminating wasteful practices, which means organizations can channel resources into activities that truly matter.
- Data-Driven Decision Making: With the integration of technology and analytics, businesses are equipped with metrics that reveal insights into their processes, enabling informed decision-making that enhances the lean journey.
- Cultural Shift: Implementing lean practices often entails a considerable cultural shift within an organization. Employees must be engaged and aligned with the lean philosophy for it to take root. This employee involvement is essential for sustaining improvements over time.
- Customized Approaches: There is no one-size-fits-all in lean systems. Businesses from manufacturing to healthcare can tailor their implementation strategies to fit their unique circumstances and market demands.
- Global Perspectives: The future of lean is not just localized. As businesses expand internationally, understanding global lean strategies can provide comprehensive insights and practices that are relevant across different markets.
Final Thoughts on Lean Systems
"Lean thinking thrives on finding the best solutions to everyday problems, bringing minds together under a banner of efficiency."
Thus, as students, researchers, educators, and professionals engage with lean systems, they must appreciate the profound impact these methodologies have not only on processes but also on workplace culture and strategic positioning in a rapidly changing world.