Linear Actuators in Rotary Motion Applications
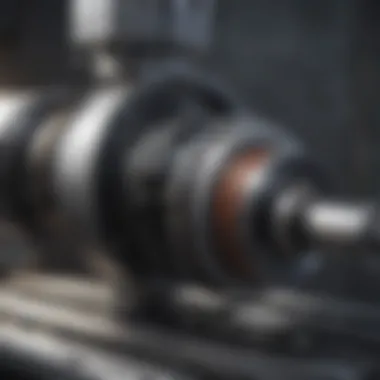
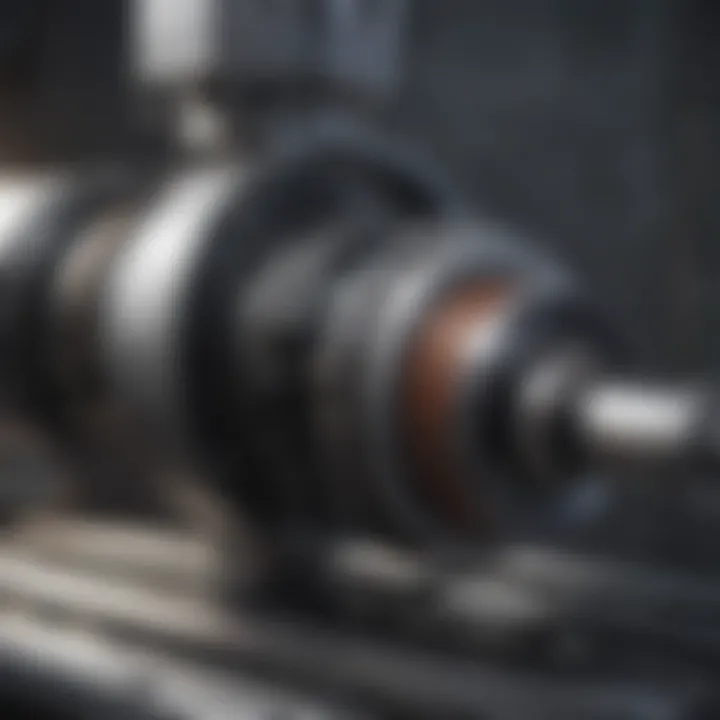
Intro
In today's fast-paced technological environment, understanding the relationship between linear actuators and rotary motion has become essential. The interplay between these two mechanisms can lead to remarkable advancements across various sectors—robotics, manufacturing, and automation, to name a few. This exploration into the dynamics of linear actuators in rotary applications aims to unpack the fundamental principles governing their interaction and offers insights that could benefit both scholars and practitioners in the field.
Research Context
Background and Rationale
At the heart of modern engineering is a constant drive for efficiency and precision. Linear actuators are pivotal in achieving motion through straight-line displacement, a principle that, when synergized with rotary motion, leads to innovative solutions. By understanding how linear force can be converted into rotational movement, we open doors to enhanced control systems and automation designs.
The need for this exploration emerges from the critical roles these technologies play in everything from everyday consumer products to high-stakes industrial machinery. With industries increasingly turning toward automation and smart technologies, an in-depth understanding of how linear actuators can optimize rotary systems is not just beneficial but necessary.
Literature Review
Numerous studies have investigated linear actuators' roles, yet few have comprehensively explored their integration with rotary motion. For instance, the works of H. K. Choi and J. Y. Toh in their 2018 publication delve into the mechanical interface, highlighting the efficiency gains achieved through hybrid systems. Another notable contribution is by R. A. Miller who, in 2020, examined the adaptability of linear actuators in robotic arms, demonstrating how they enhance operational flexibility.
These studies serve as vital stepping stones, outlining both successes and future research paths. Through synthesizing existing literature, this article aims to fill gaps by providing a holistic view of how linear actuators engage with rotary motion across various applications.
Methodology
Research Design
Adopting a qualitative approach, a blend of case studies and expert interviews guides this analysis. By examining practical applications in diverse settings—like industrial automation and robotics—the intention is to glean insights rooted in real-world experiences. This dual lens not only grounds the theoretical discussions but also highlights practical constraints facing engineers today.
Data Collection Methods
Data for this exploration is collected from several sources:
- Academic Journals: Peer-reviewed articles provide foundational theories and empirical findings.
- Industry Reports: These documents offer insights into market trends and practical implementations.
- Interviews with Industry Practitioners: Conversations with professionals who utilize linear actuators and rotary systems help illuminate common challenges and innovative solutions.
Through this comprehensive methodology, the article is poised to deliver an informative narrative that resonates with a wide audience, from students to seasoned engineers, ensuring a robust understanding of an often overlooked but critical interaction in the engineering domain.
"The beauty of design is not just in the mechanics, but in the seamless integration of motion into our everyday lives." - An audience perspective through interviews.
This exploration promises to shed light on the intricate workings at play, fostering a greater appreciation of the technology driving modern automation.
Prelude to Motion Types
Understanding the core concepts of motion is crucial when diving into the world of linear actuators and their role in rotary applications. Motion types, specifically linear and rotary, possess distinct characteristics that govern the design and use of various mechanical systems. By grasping the fundamentals of these motions, one can appreciate how linear actuators bridge the gap between them, facilitating more efficient engineering solutions.
Both linear and rotary motions are integral in diverse fields such as automation, robotics, and aerospace. Linear motion refers to movement in a straight line, while rotary motion involves turning around an axis. Recognizing these differences helps engineers and researchers design devices that optimize performance, enhance functionality, and meet specific operational needs.
Some benefits of understanding motion types include:
- Enhanced Design Efficiency: Knowledge of motion principles aids in creating systems that minimize energy loss.
- Improved Control Mechanisms: Understanding how to manipulate different motions leads to better control over machines and devices.
- Application Versatility: Many technologies can benefit from adapting linear motions to solve specific rotary challenges.
In essence, a thorough comprehension of these motion types lays the groundwork for exploring the intricate dynamics between linear actuators and rotary motion applications.
The Fundamentals of Linear Actuators
Understanding the basics of linear actuators is essential for grasping their integration into rotary motion applications. These devices serve as the backbone in various systems, converting linear motion into rotary action that is vital in industrial, robotic, and automotive settings. Their ability to deliver precision and control over movements paves the way for innovative designs and improved functionalities. The role linear actuators play can't be overstated as they form the foundation from which complexity in motion dynamics derives.
Mechanics of Linear Actuators
Linear actuators encompass various functionalities, typically relying on mechanisms that convert energy into linear motion. At their core, these devices use electric motors, hydraulic systems, or pneumatic forces to execute their operations. They convert electrical or hydraulic energy into physical movement along a straight line, a process that can be as simple as extending a rod or as complex as synchronizing multiple axes for coordinated movements.
The operational mechanics often involve several essential components, including a power source, a mechanical conversion system, and an output device that translates linear movement into the desired effect. The intricacies can range from basic push-pull actions to sophisticated movements necessitating precise coordinates. As automation grows, understanding the nuances in mechanics helps engineers and designers create better systems that leverage these capabilities effectively.
Types of Linear Actuators
Linear actuators can be categorized based on their propulsion mechanisms. Each type comes with its own unique features, suitable applications, advantages, and challenges.
Electromechanical Actuators
Electromechanical actuators stand out for their efficiency and precision in applications requiring rapid and controlled movements. These actuators combine electric motors with mechanical systems like screws or belts to produce linear motion. Their main benefit lies in their adaptability and reliability in various environments, making them a go-to choice in many industries.
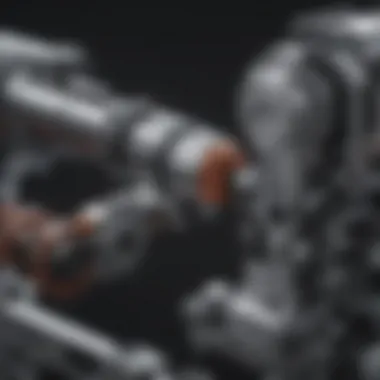
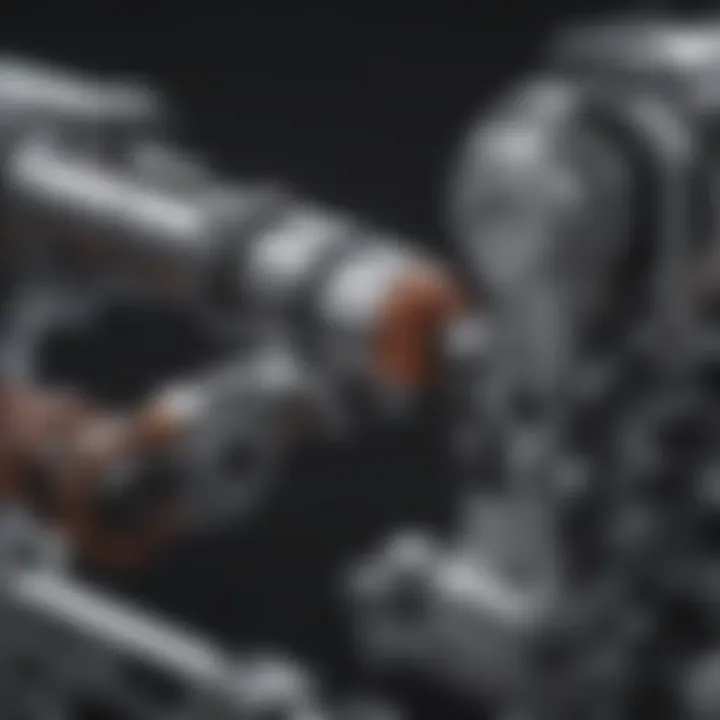
A key characteristic of electromechanical actuators is their ability to provide feedback through sensors, allowing real-time adjustments to positioning. With their simplicity of integration into control systems, they are often seen in robotics and automated assembly lines. However, these actuators can be sensitive to environmental conditions, such as temperature and humidity, which may affect performance.
Hydraulic Actuators
Hydraulic actuators are known for their ability to generate high force without occupying substantial space. These systems utilize pressurized fluid to generate movement, making them suitable for heavy-duty applications. One of the defining aspects of hydraulic actuators is their strength-to-weight ratio, which exceeds that of many other mechanisms.
Their unique feature lies in their capacity to adapt to various loads without a significant drop in performance. This makes them popular in industries like construction and manufacturing, where heavy lifting is necessary. However, the reliance on fluid means that maintenance and potential leak issues can create complications that engineers must address.
Pneumatic Actuators
Pneumatic actuators employ compressed air to create linear motion and are particularly preferred in environments where quick responses are needed. They are lightweight and provide substantial speed, making them ideally suited for tasks involving repetitive motions.
One appealing aspect of pneumatic actuators is their simplicity and low operating costs. They don’t require extensive maintenance compared to hydraulic systems. However, their reliance on air means they may provide lower force output than hydraulic systems, which can be a limiting factor in more demanding applications.
Understanding these different types of linear actuators and their mechanics provides a critical foundation for the subsequent integration of these systems into rotary motion applications. Their respective characteristics define not only how they operate but also where they find their most impactful uses in modern technology.
Principles of Transformation from Linear to Rotary Motion
In the realm of engineering, the conversion of linear motion to rotary motion is essential, combining simplicity with functionality. This transformation forms the backbone of numerous mechanical devices. Understanding the principles involved not only serves in the design of machines but also guides improvements in efficiency and performance. In various applications, from industrial automation to robotics, these principles are notably tangible, allowing engineers to refine systems for better control and output.
Basic Mechanical Conversions
The art of converting linear motion to rotary movement hinges on two primary mechanical systems: the crank and slider mechanism and rack and pinion systems. Each brings unique benefits and considerations, making them valuable in different contexts.
Crank and Slider Mechanism
The crank and slider mechanism stands out for its straightforward design and functionality. In essence, it operates by transforming the linear motion of a slider into a rotary movement experienced at the crank. The pivotal characteristic of this mechanism is its ability to generate rotation through a single revolution of the crank, allowing for efficient power transmission.
One notable aspect of the crank and slider is its simple construction, making it an appealing option for designers; it requires fewer parts compared to more complex systems. This simplicity translates into reliability and lower maintenance costs, which are significant advantages for industries prioritizing uptime and ease of servicing. On the flip side, the mechanism can face mechanical constraints, such as wear on the sliding surfaces over time, potentially necessitating replacement or repair. Regardless, its benefits often outweigh these drawbacks in applications like engine design, where it transforms the up-and-down motion of pistons into the rotational force necessary to drive the vehicle.
Rack and Pinion Systems
Conversely, the rack and pinion system offers a different approach to motion transformation. This mechanism consists of a linear rack that engages with a circular pinion gear. The key characteristic of the rack and pinion is its ability to convert linear input directly into rotational output without much intermediate movement. This provides a precise control of positioning, which is invaluable in systems requiring exact movements, like steering in vehicles and various robotic applications.
What truly sets the rack and pinion apart is its adaptability. It can be employed in various scenarios, from heavy-duty industrial machinery to smaller, precision instruments. However, while it excels in precision, one must also consider the disadvantages, such as the limited rotation angle. Over time, the continuous engagement can also result in wear that might affect performance if not maintained properly. Nonetheless, for many applications, the ability to control linear movement with reliability and accuracy makes this system a popular choice.
Motor Configurations for Rotation
Expanding on the relationship between linear and rotary motion, motor configurations play a fundamental role. Selecting the right motor to effectively harness this transformation really matters in terms of efficiency and system performance. Various configurations exist, from direct drive setups to more complex arrangements involving gears and levers. Each configuration holds its own pros and cons, and the choice usually depends on the specific application requirements. Understanding how to align motors correctly with linear actuators can lead to significant improvements in precision and efficiency in rotary motion systems.
Motor selection is crucial; the right choice can mean the difference between smooth operation and operational failures.
Ensuring that the motor matches the requirements of load, speed, and precision will go a long way in optimizing systems that rely on the linear-to-rotary motion paradigm. As designers grapple with various layout challenges and operational demands, honing in on these principles becomes invaluable for achieving reliable performance regardless of the industry.
Integration of Linear Actuators in Rotary Systems
Integrating linear actuators within rotary systems marks a significant advancement in various engineering applications. This integration is not just about connecting components; it's about synergizing distinct motion types to create efficient, flexible, and responsive systems. The use of linear actuators enhances the overall performance and reliability of rotary motion applications across diverse fields such as robotics, automotive, and industrial automation.
One of the main elements to consider in this integration is the relationship between linear force and rotary speed. Linear actuators allow for precise control over motion, which when translated to rotary systems result in improved stability and accuracy. This is particularly beneficial in scenarios requiring incremental adjustments, such as in CNC machines or automated assembly lines. Moreover, the modular nature of linear actuators enables easier maintenance and upgrades, which is a compelling aspect for industries that prioritize longevity and adaptability in their systems.
Design Considerations
Force and Speed Requirements
The force and speed requirements play a crucial role in the design and functionality of rotary systems that incorporate linear actuators. Each application has its unique demands depending on load and operational speed, making it essential to clearly define these parameters. A key characteristic of this requirement is how force dictates the actuator's capability to move an object, while speed directly affects the system's overall efficiency.
In applications like robotic arms, where the precision of movement is non-negotiable, having appropriate force specifications ensures that the actuator can manipulate objects without causing damage or error. Notably, higher force ratings often correlate with a greater degree of control—vital in delicate environments such as laboratories or during surgical procedures. However, choosing an actuator based on force can become a double-edged sword; excessive force or speed can lead to wear and tear quicker than anticipated.
Alignment and Mounting Techniques
Alignment and mounting techniques are another pivotal aspect of integrating linear actuators into rotary systems. Proper alignment ensures that the actuator operates efficiently without undue stress on the components. This not only prolongs the lifespan of the actuator but also guarantees consistent performance. An essential characteristic here is the need for precision, as misalignment can lead to mechanical failures or inaccuracies in motion.
Good alignment techniques can significantly enhance the reliability of the system. For instance, using adjustable brackets can help accommodate any discrepancies in mounting. However, this flexibility can also introduce a potential pitfall—improper adjustments could create unintended torque, impacting the functionality of the rotary system.
Control Mechanisms
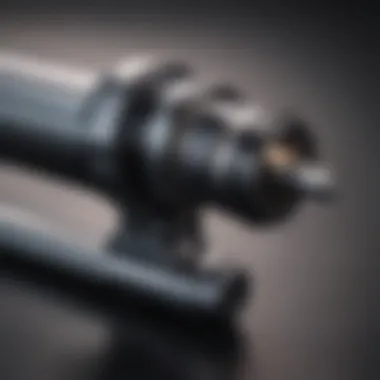
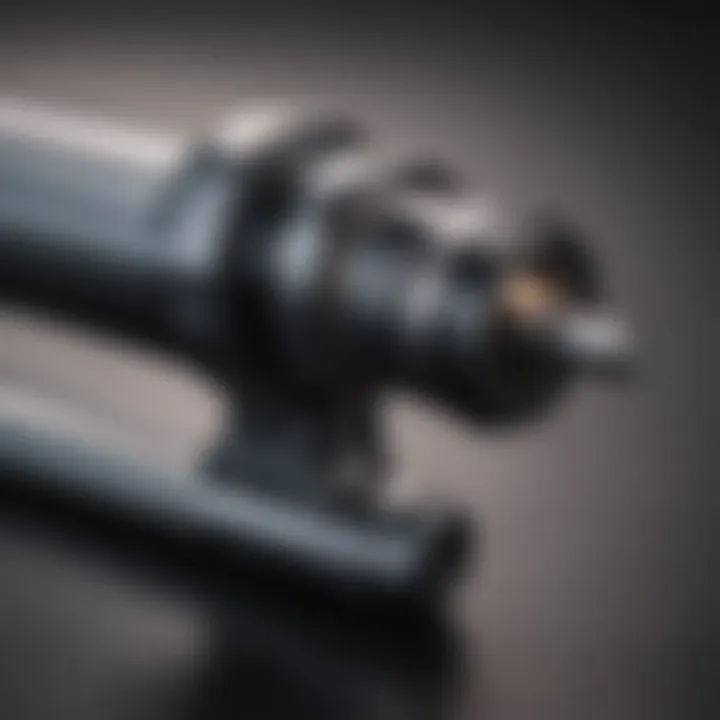
Control mechanisms are the backbone of any rotary system utilizing linear actuators. These mechanisms dictate how effectively the actuators convert the linear motion into rotary action. From simple lever systems powered by a console to complex feedback loops managed by sophisticated software, the control mechanisms chosen can drastically influence the efficiency and responsiveness of the entire system.
A strong advantage of modern control systems lies in their integration with smart technologies. This allows for real-time monitoring and adjustments, elevating performance and operational standards. Yet, this does not come without challenges. Control systems must balance precision against complexity. Overly sophisticated systems may lead to increased learning curves for operators and potentially unexpected failures.
The journey of discerning the best control mechanism should always aim for simplicity and effectiveness while ensuring a seamless interface for users.
"The integration of linear actuators in rotary systems is not merely a technical choice; it's a strategic move towards innovation and enhanced capabilities in engineering applications."
In summary, the integration of linear actuators in rotary systems presents a host of opportunities to enhance functionality, though it also brings specific challenges that demand careful consideration of force requirements, alignment techniques, and control mechanisms.
Applications of Linear Rotary Motion Systems
Understanding the applications of linear rotary motion systems is essential, as these mechanisms are at the forefront of modern engineering solutions. Their ability to convert linear movements into rotational force has made them invaluable across several domains. This section will delve into key areas where these systems are integrated, elucidating their importance, benefits, and the specific considerations to keep in mind during their implementation.
Industrial Automation
In the realm of industrial automation, linear rotary motion systems play a critical role in enhancing productivity and streamlining processes. These systems facilitate precise movements necessary for tasks such as material handling, assembly, and packaging. Here are some specific elements related to their use in industry:
- Increased Efficiency: The conversion of linear motion into rotary motion allows for faster operational speeds. As a result, equipment can perform tasks in a fraction of the time that would otherwise be required by traditional systems.
- Enhanced Precision: The accuracy of linear actuators ensures that rotary systems can achieve required positions without backlashes, minimizing the risk of production errors.
- Versatile Applications: From conveyor belts to robotic arms, these systems are adaptable to various configurations, making them suitable for diverse manufacturing settings.
Despite the numerous advantages, considerations such as load capacity and environmental factors must be assessed to maximize their effectiveness in specific use cases.
Robotics and Mechatronics
Robotics and mechatronics significantly benefit from the integration of linear rotary motion systems. These fields emphasize precision and adaptability, where the combination of linear and rotational movements paves the way for sophisticated mechanical designs. Key aspects of their application include:
- Flexibility in Design: Linear actuators coupled with rotary actuators allow engineers to create intricate movements that mimic human-like motions, crucial for tasks ranging from assembly to surgery.
- Enhanced Control Systems: The precision offered by linear to rotary transformations enables advanced control algorithms that improve the functionality and responsiveness of robotic systems.
- Real Time Feedback: Systems can be equipped with sensors that provide feedback on position and speed, optimizing real-time adjustments and enhancing overall performance.
As these technologies continue to evolve, the potential for innovative applications expands, leading to even greater advancements in both robotics and automation.
Aerospace and Automotive Sectors
In the aerospace and automotive industries, the integration of linear rotary motion systems manifests in numerous critical applications. Reducing weight while maintaining strength is a priority in these sectors, and linear actuators provide an effective solution. Consider some notable aspects:
- Robust Structural Integrity: Aircraft and vehicles require components that not only perform but also endure various environmental stresses. Linear actuators are designed to handle such challenges effectively.
- Energy Efficiency: These systems often offer better energy consumption profiles, which is vital for vehicles seeking to improve fuel efficiency or extend battery life in electric models.
- Safety Standards Compliance: The high precision involved in their operation also aids in meeting stringent safety regulations, allowing engineers to ensure that components like wing flaps and suspension systems operate flawlessly.
With advancements in actuation technology, the future holds promise for even greater innovations in aerospace and automotive applications.
As industries strive for best practices in automation, robotics, and high-performance engineering, the significance of linear rotary motion systems is more crucial than ever.
Advantages of Using Linear Actuators in Rotary Applications
The integration of linear actuators within rotary motion applications brings forth several pivotal advantages that can enhance performance across various fields. By understanding these benefits, one can appreciate how employing linear actuators transforms operational efficiency and effectiveness in tasks that require precise movement and control. This section delves into two primary advantages: precision and control, and energy efficiency. Each of these elements contributes significantly to the reliability and productivity of systems utilizing linear actuators.
Precision and Control
Precision is often the name of the game in automation sectors, and linear actuators shine in this regard. By their nature, these devices convert linear motion to rotational movement with a high degree of accuracy. This transformation enables very fine adjustments in positioning, something that’s crucial in applications like robotic surgery or high-tech manufacturing.
For instance, consider a scenario involving CNC (Computer Numerical Control) machining. In this environment, a slight error in positioning can lead to catastrophic outcomes in terms of material waste and product quality. By incorporating linear actuators, manufacturers can achieve repeatability as tight as +/- 0.01 mm, ensuring that every component meets stringent specifications.
Moreover, achieving control over motion is significantly improved when utilizing these actuators. With advanced servo control systems, engineers can program motion profiles that dictate the exact speed and direction of movement. This programmable nature means that systems can be adapted on the fly, responding to varying operational demands without a hefty redesign.
To better understand how precision and control manifest in practical settings, here are a few real-world applications:
- Robotic Arm Operations: In automation lines, robotic arms equipped with linear actuators can navigate complex paths while maintaining accuracy to execute delicate tasks such as assembly or painting.
- Automated Guided Vehicles (AGVs): These rely on precise movement control to transport products within warehouses, reducing the risk of collisions and improving workflow.
Energy Efficiency
In today’s fast-paced world, energy efficiency is not just a buzzword; it’s often a make-or-break factor for businesses. Linear actuators underline their value here through reduced energy consumption compared to traditional motor systems. By converting linear motion directly into rotary output, these actuators minimize energy losses that usually occur in gear systems or mechanical linkages.
A significant contributor to this energy savings stems from the direct drive capability of linear actuators. They can engage the load without intermediary elements like belts or pulleys that typically sap energy. Consequently, systems can operate at a lower power rating, which not only cuts utility costs but also results in a smaller carbon footprint.
The following points highlight specific aspects of energy efficiency when using linear actuators:
- Less Mechanical Wear: Fewer moving parts translate to lower maintenance costs and increased reliability. This translates to less downtime on operations.
- Adaptive Load Management: Some systems equipped with these actuators can adjust their power output depending on the load, effectively optimizing energy use in real-time.
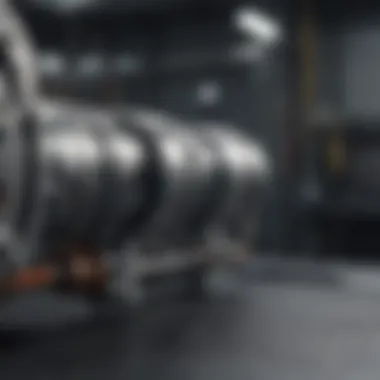
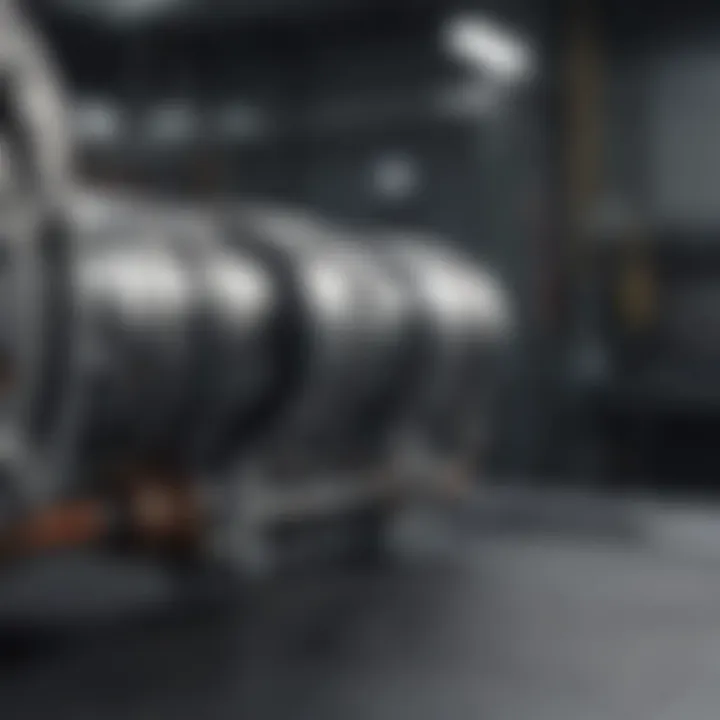
"The implementation of linear actuators has proven instrumental in improving operational efficiency, not just from a precision standpoint, but also concerning energy consumption that aligns with today’s sustainability goals."
Challenges in Linear to Rotary Motion Conversion
The conversion of linear motion into rotary motion is no walk in the park. While linear actuators boast a variety of advantages, such as speed and efficiency, their integration into rotary systems can be fraught with challenges that engineers must navigate. This section delves into these obstacles, highlighting the importance of understanding them for anyone involved in the design and implementation of motion control systems.
Mechanical Limitations
At the heart of the matter are the mechanical limitations that can hinder effective conversion between linear and rotary motion. For instance, linear actuators are primarily designed to produce straight-line motion. When tasked with contributing to rotary systems, they may present issues related to size, force, and maximum travel distances.
One major limitation is the torque produced by linear actuators. While they can exert powerful linear forces, converting that force into torque is not always straightforward. For example, a linear actuator pushing against a lever arm generates torque, but the efficiency of this conversion can vary depending on the arm's length and the angle of force application. Inefficient torque generation can lead to sluggish operation or even mechanical failure in some applications.
"Understanding these mechanical limitations is crucial, as they can dictate the efficiency and reliability of the entire system."
Furthermore, not all linear actuators can accommodate the load conditions typically found in rotary applications. Certain high-speed operations may require actuators that can withstand significant wear and tear, which not every model is capable of handling. The mismatch between actuator capacity and system demands could lead to performance bottlenecks.
Control Issues
Control mechanisms also play a pivotal role in the challenges faced during the conversion of linear motion to rotary motion. The integration of linear actuators into rotary motion systems demands precision in control strategies to ensure synchronization between the two forms of motion. Without carefully designed controls, misalignments may arise, resonating throughout the system.
One significant control issue is the feedback system required for maintaining accuracy. For instance, if a linear actuator is meant to control the position of a rotating shaft, it often relies on sensors for feedback. If these are poorly calibrated or malfunction, it may result in erratic movement, throwing the entire operation off balance. The engineer must be vigilant, continually adjusting control parameters to maintain operational integrity.
Moreover, the complexity of control algorithms compounds challenges, especially in dynamic environments where real-time adjustments are needed. Engineers often face the difficulty of developing algorithms that seamlessly integrate linear and rotary motion controls. This is particularly daunting in applications such as robotics where quick response times are vital.
In summary, while the use of linear actuators in rotary motion systems can yield significant benefits, engineers must remain aware of mechanical limitations and control issues. By addressing these challenges head-on, greater efficiencies and reliability can be achieved, fostering improved performance across a range of applications.
Future Trends in Actuation Technology
In the ever-evolving field of engineering, the future trends in actuation technology are pivotal for a multitude of applications. As industries increasingly gravitate towards automation and precision, understanding these trends can provide insights into how linear actuators will continue to reshape rotary motion systems. Not only does this discussion illuminate the path forward for actuation technologies, but it also focuses on the specific elements that enhance performance, ensuring longevity, efficiency, and adaptability.
Advancements in Materials
The materials used in linear actuators are undergoing significant advancements to meet the increasing demands of modern applications. Traditionally, heavy metals and basic plastics were the norm, often limiting weight and operational efficiency. However, newer materials such as carbon fiber composites and advanced polymers are now making waves.
These materials offer remarkable strength-to-weight ratios, allowing actuators to be both lightweight and robust.
- Cost Efficiency: While innovative materials may initially come with a higher price tag, their durability reduces maintenance costs over time.
- Wear Resistance: Enhanced materials lead to less friction and wear, extending the actuator's lifespan.
- Improved Performance: The use of advanced materials also allows for faster response times, boosting overall efficiency in rotary motion applications.
Such changes are crucial for industries relying on precision. For instance, in aerospace, where weight is a critical factor, the integration of lightweight materials significantly affects fuel efficiency and payload capacity.
Integration with Smart Technologies
As the Internet of Things (IoT) continues to expand, the integration of smart technologies into actuator systems is becoming increasingly relevant. This trend holds the potential to transform how actuators operate within rotary motion setups.
Smart technologies introduce features such as:
- Real-time monitoring: Sensor systems can track performance metrics, offering insights into potential failures before they occur.
- Adaptive control: Systems can adjust their response based on environmental conditions or operational demands, which is particularly important in dynamic environments.
- Data analytics: By harnessing big data, engineers can optimize actuator performance further, adjusting parameters for different tasks or minimizing energy use during idle periods.
Such integrations do not just benefit manufacturers; they also enhance safety and reliability in robotic applications, where precision is non-negotiable. The seamless flow of data between components ensures that any adjustments can be made in real-time, resulting in safer and more efficient operations.
"The future of actuation technology is not just about increasing efficiency and power; it's about creating smarter systems that respond and adapt to their environment."
In essence, future trends in actuation technology, particularly advancements in materials and smart technology integrations, are setting the groundwork for more sophisticated, efficient, and adaptive linear actuators in rotary motion applications. As engineers and researchers focus their efforts in these areas, the resultant innovations promise to significantly impact fields ranging from robotics to manufacturing.
The End
Summarizing Key Points
The intricate dance between linear and rotary motion comes to a head in the context of actuators. Throughout this deep dive, it has been abundantly clear that linear actuators transform linear movement into rotary functions with precision and reliability. Key elements such as mechanical conversion mechanisms, including crank systems and rack-and-pinion configurations, lay the groundwork for understanding how linear energy is translated into angular motion. These systems reside at the heart of numerous applications, notably in industrial automation, robotics, and automotive engineering, showcasing the versatility and functionality that the right actuator can provide.
One cannot overlook the advantages highlighted, including energy efficiency and enhanced control in movement. As the trends in actuation technology lean toward greater integration with smart devices and advancements in materials, the possibilities for innovation appear virtually limitless. This fusion not only streamlines existing processes but also paves the way for novel applications.
Implications for Future Research
Looking ahead, several avenues beckon for further exploration. As industries push for increased automation, the demand for more sophisticated actuation solutions grows. Future research into adaptive control systems that combine sensor feedback with linear actuators merits special attention. Such innovations may lead to advancements in precision, allowing machines to respond instinctively to variable operating conditions and enhancing overall operational efficiency.
Additionally, depths of research into new material sciences, including lighter yet stronger composites, could change the game for actuator design, enabling more compact systems with enhanced performance profiles. The marriage of smart technology with these actuators will likely drive the next wave of advancements—think IoT-enabled actuators that allow for real-time adjustments based on operational feedback.
Establishing interdisciplinary collaboration between mechanical engineering, software development, and material science may lead to research breakthroughs that redefine the capabilities of linear actuators within rotary systems. As ideas and technologies converge, a bright horizon awaits in the realm of actuation technology.
"Innovation is the calling card of the future."
In summation, emphasizing the dynamics of linear actuators in rotary motion is not just an academic exercise; it's a drive towards automating and refining how we interact with machines in various sectors. As the landscape evolves, staying ahead requires both understanding the current state of technology and anticipating the shifts of tomorrow.