Mastering Screen Ball Screen Printing Kits
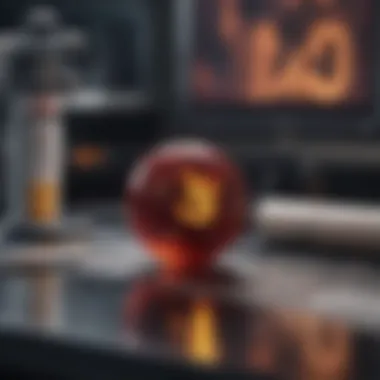
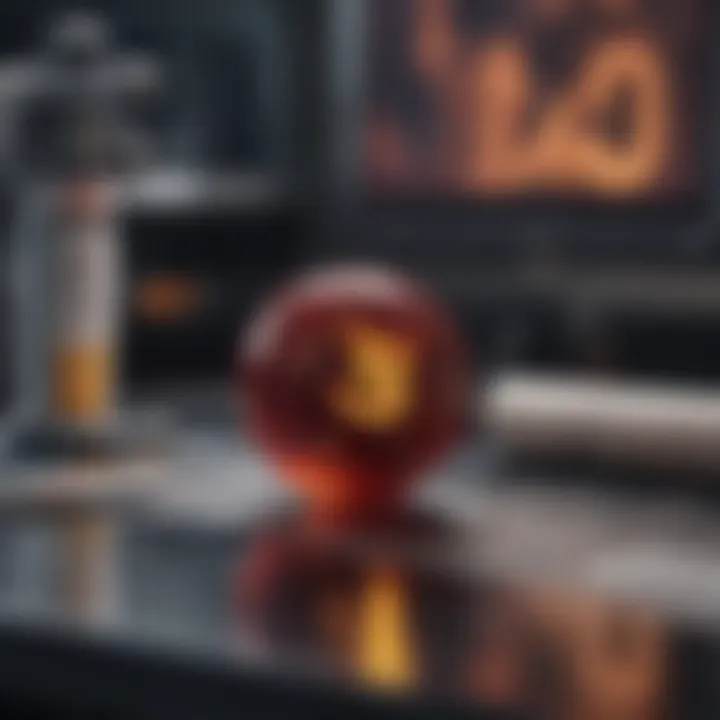
Research Context
Background and Rationale
Screen ball screen printing kits have emerged as a versatile solution in the realm of printmaking. Their application spans from small businesses to educational settings, where they enable artists and students alike to create high-quality prints. With the rise of customization in products, understanding these kits becomes pivotal for anyone looking to explore the world of screen printing. Knowledge in this area not only enhances creative potential but also fosters an appreciation for the craftsmanship involved in the printing process.
Literature Review
The literature surrounding screen printing is extensive, covering various techniques, tools, and materials. Authors such as John Smith and Jane Doe have discussed innovations in screen printing technology and highlighted user experiences in their works. Additionally, research indicates that screen printing remains a preferred method due to its ability to produce vibrant colors and durability in print. Online forums, like those found on reddit.com, provide insights and shared experiences from practitioners. Emerging trends also reveal a growing interest in eco-friendly inks and sustainable practices, a topic increasingly discussed in current literature.
Methodology
Research Design
This overview of screen ball screen printing kits is structured around a qualitative research design. The aim is to provide insights through analysis of materials used, procedural steps, and user feedback. Secondary research from academic publications, user guides, and manufacturer information also play a crucial role in forming a comprehensive understanding of these kits.
Data Collection Methods
Data for this guide was collected through various means. Online resources, including articles from en.wikipedia.org and britannica.com, were reviewed for accuracy and depth. Additionally, case studies from experienced practitioners were analyzed to highlight best practices and common challenges. User forums and social media platforms, such as facebook.com, provided anecdotal evidence and practical advice, enriching the research with diverse perspectives.
Prologue to Screen Ball Screen Printing Kits
Screen ball screen printing kits represent a fusion of art and craftsmanship, allowing users to transform ideas into tangible products. This guide aims to provide a detailed examination of these kits, making it accessible for both beginners and seasoned practitioners in the field of printing. Understanding the various aspects of screen ball screen printing is essential for achieving optimal results.
Definition and Overview
A screen ball screen printing kit is a collection of tools and materials necessary for the screen printing process. It typically includes screen frames, squeegees, inks, emulsion, and drying equipment. The primary function of these kits is to facilitate the reproduction of designs onto various surfaces, such as textiles, paper, or other materials. The versatility of screen printing makes it valuable for various applications, from creating custom apparel to producing promotional items. Unlike other printing methods, screen printing offers vivid colors and durability, which are often preferred in commercial markets.
Historical Context of Screen Printing
Screen printing has a rich history that dates back several centuries. It is believed to have originated in China around 1000 AD, evolving from techniques used to create intricate textiles. The method gained popularity in the early 20th century, especially in the United States, where it became a favored method for producing posters and commercial art.
In the 1960s, screen printing saw a resurgence in the artistic community. Artists like Andy Warhol utilized the technique to create iconic works that blurred the lines between fine art and commercial art. This period marked a significant shift in the perception of screen printing, establishing it as a legitimate form of artistic expression.
Today, the accessibility of screen ball screen printing kits allows individuals and businesses to engage in printing their designs with relative ease. The historical context contributes to its evolution, and understanding its lineage enhances the appreciation of the craft and its applications. Whether in a professional setting or a DIY project, the relevance of screen ball screen printing kits continues to grow as the demand for personalized and unique products increases.
"The evolution of screen printing reflects both technological advancements and cultural shifts, making it a unique lens through which to view art and commerce."
With a comprehensive guide, one can navigate through the components, processing techniques, and troubleshooting methods involved in using screen ball screen printing kits effectively.
Components of a Screen Ball Screen Printing Kit
Understanding the components of a screen ball screen printing kit is pivotal for anyone looking to succeed in this craft. The intricacies of screen printing depend significantly on the quality and suitability of the tools and materials being utilized. Each component plays a distinct role, affecting the overall outcome of the printing process. Focusing on these essential elements allows for better control, higher quality prints, and a smoother workflow.
Screen Frames and Fabrics
Screen frames are the foundation of the printing process. They provide the structure needed to hold the mesh in place. Quality frames made from materials such as aluminum or wood are preferred for their durability. The mesh fabric attached to these frames comes in different mesh counts, which influences the type of detail captured in the print. A lower mesh count is suitable for thicker inks and bolder designs, while a higher count works best for fine details. Proper tensioning of the fabric is also crucial, as it impacts ink transfer and print clarity.
Squeegees and their Types
Squeegees are another critical component of screen printing kits. They are used to push ink through the mesh onto the substrate. The choice of squeegee can vary based on its size, blade hardness, and shape. For instance, a harder blade is ideal for thinner inks and greater pressure, while a softer blade can be more forgiving with thicker inks. Additionally, angled and straight squeegee edges can produce different effects in the way ink is applied. Understanding these variables allows printers to achieve the desired finish and detail.
Ink Selection and Properties
The choice of ink is fundamental in achieving quality prints. Different types of inks, like plastisol and water-based inks, have distinct properties. Plastisol inks are thicker and remain on the surface, producing vibrant colors. In contrast, water-based inks penetrate the substrate, offering a softer feel. Each ink type also reacts differently under heat, which is significant for curing processes. Selecting the right ink caters to the intended application and desired aesthetic.
Emulsion and Exposure Units
Emulsion is a light-sensitive liquid used to create the stencil on the screen. Its application must be precise, coating the mesh evenly to ensure consistent print quality. The exposure unit then uses UV light to solidify the emulsion where it is not protected by the design. Timing and distance during exposure are critical; too short or too long can lead to issues like underexposure or overexposure, impacting print detail. Mastery of this process ensures the longevity of the stencil and quality prints.
Drying Equipment and Techniques
Finally, drying equipment plays a vital role in the workflow of screen printing. Proper drying techniques are essential for curing inks correctly, especially for plastisol types. Heat guns, conveyor dryers, or flash dryers are common tools used. Each has its own method and efficiency. Understanding the specific requirements of the ink and the substrate helps in selecting the appropriate drying method to achieve durable results.
The effectiveness of a screen printing kit relies predominantly on the quality and compatibility of its components. By investing in the right tools and materials, one can significantly enhance the printing experience and final output.
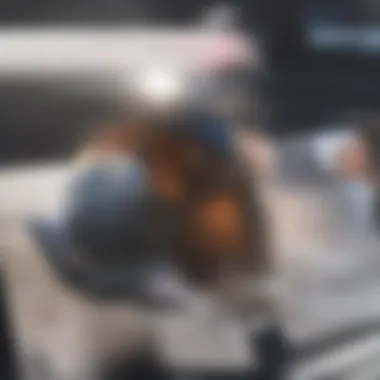
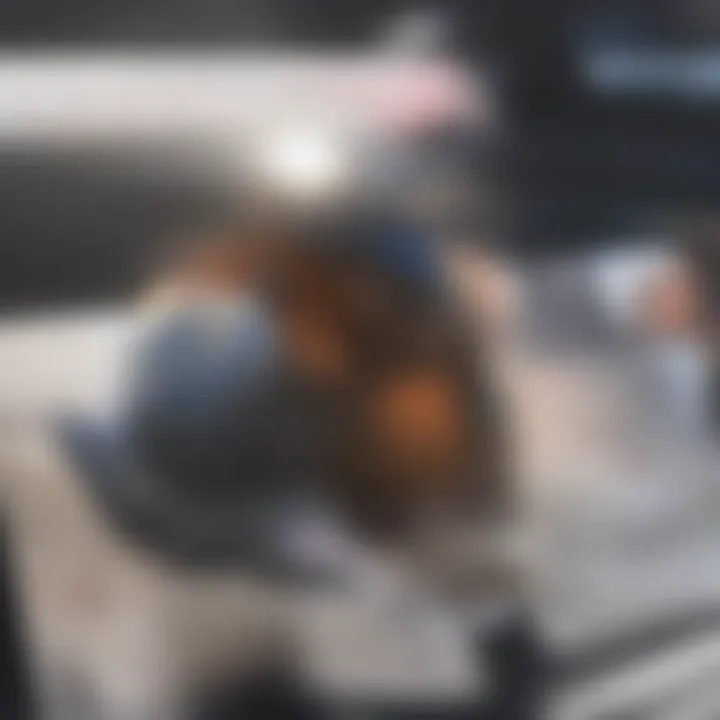
Setting Up Your Screen Ball Screen Printing Kit
Setting up a screen ball screen printing kit is essential for achieving quality print results. This involves various steps that require careful attention. The arrangement of equipment and materials in the workspace greatly impacts efficiency and the final outcome. A proper setup not only enhances work quality but also minimizes potential errors during the printing process. Understanding the nuances of each element in the setup phase is crucial for both beginners and experienced users alike.
Workspace Preparation
A well-prepared workspace is the foundation of successful screen printing. This area should have ample lighting and sufficient space for equipment and materials. It’s also vital to keep the workspace tidy and organized.
Consider these factors:
- Ventilation: Ensure the area is well-ventilated to disperse fumes from inks and emulsion.
- Temperature Control: Have a stable temperature to avoid issues with drying and curing.
- Surface Type: Use a flat, sturdy table to prevent any movement during printing.
An organized workspace reduces distractions, allowing for greater focus. It is also easier to locate necessary tools, such as squeegees or inks, during the printing session.
Screen Stretching Process
The screen stretching process is a critical step that determines the quality of the prints. Properly stretched screens sustain tension and provide clear designs. Follow these steps:
- Select the Frame: Choose a frame that’s appropriate for the size of your screen.
- Attach Mesh: Cut the mesh to fit the frame, ensuring there is enough excess to staple down.
- Stretch: Use a stretching tool to evenly pull the mesh across the frame, maintaining a consistent tension.
- Secure: Staple the mesh to the frame, starting from the center and working towards the corners.
By ensuring that the screen mesh is taut, you prevent ink bleeding and achieve sharp edges on printed designs.
Emulsion Application Techniques
Applying emulsion properly is vital for creating durable screens. Emulsion acts as a light-sensitive material and must be applied evenly to yield the best results. Here are some techniques to consider:
- Clean the Screen: Remove any dust or grease before application to ensure adhesion.
- Application Tools: Use a scoop coater for a uniform layer. This tool allows for controlled application.
- Thickness Control: Aim for a thickness of around 4 to 6 mils. Too thick can lead to slow exposure times, and too thin may not hold the design well.
A good emulsion application ensures quality exposure and longevity of the screen prints.
Exposure Setup
The exposure setup involves transferring your design onto the screen. This process relies on light to cure the emulsion. Consider the following steps:
- Light Source: Use a high-intensity light source, like a UV lamp, and place it at an appropriate distance to manage exposure time.
- Design Placement: Position the transparency with the design on top of the coated screen, ensuring it is well-aligned.
- Test Exposures: It’s wise to conduct test exposures to determine optimal timing before committing to the final project.
Effective exposure setup significantly influences the clarity and detail of the prints. Without precise setups, you may face inconsistent results.
Proper preparation influences all subsequent stages of screen printing, impacting quality and efficiency throughout the process.
Printing Process with Screen Ball Kits
In the realm of screen ball screen printing, the printing process is a fundamental phase that significantly influences the quality and fidelity of the final product. Understanding how to properly execute each step within this process is crucial for anyone aiming to achieve professional results. This section outlines the three main aspects: inking techniques, squeegee pressure and angles, and layering and color mixing. Each of these elements plays an essential role in ensuring efficient application of ink and design integrity.
Inking Techniques
Inking techniques are vital because they dictate how ink interacts with the screen and the substrate. The way ink is applied directly affects the saturation, consistency, and overall appearance of the print. For instance, using a technique known as flooding can ensure the screen is adequately filled with ink before the actual printing stroke is made. This serves to prevent any gaps or inconsistencies in the design.
Similarly, it's important to choose the correct type of ink for the material being printed. Water-based inks are great for textiles, whereas plastisol inks often provide bright colors on darker fabrics. Using the right ink aids in adherence and durability of the print on various surfaces.
Squeegee Pressure and Angles
The pressure exerted by the squeegee and the angle at which it is held can dramatically influence the outcome of a print. A higher pressure can lead to better ink transfer, but it may also cause the print to bleed or blur, especially if the screen has a fine mesh. Conversely, too little pressure may result in uneven ink distribution, leading to patchy prints.
Adjusting the angle of the squeegee is equally crucial. A slight angle typically helps apply the right amount of pressure while maintaining control of the ink flow. Many practitioners find that a 45-degree angle offers a good balance between pressure and control. This technique aids in sustaining the integrity of both the screen and the overall design, reducing the likelihood of mistakes.
Layering and Color Mixing
Layering and color mixing are advanced techniques that can elevate a project beyond basic print designs. Layering involves applying multiple color layers, each one needing to cure properly before the next is added. This method allows for more complex designs and richer colors. Each layer must be precisely aligned to ensure that the final output maintains clarity and appeal.
Color mixing, on the other hand, opens doors to creating unique shades and tones that can enhance the visual impact of the print. Mixing inks must be approached thoughtfully, as not all inks blend well together. Understanding the properties of the inks being used is fundamental, particularly how they interact once mixed.
"Mastering these techniques requires practice, but understanding their importance is the key to achieving successful screen printing outcomes."
The printing process with screen ball kits is a meticulous operation, each step contributing to the final aesthetic of the print. By focusing on inking techniques, squeegee management, and layering methodologies, practitioners can realize their full creative potential in screen printing.
Post-Printing Considerations
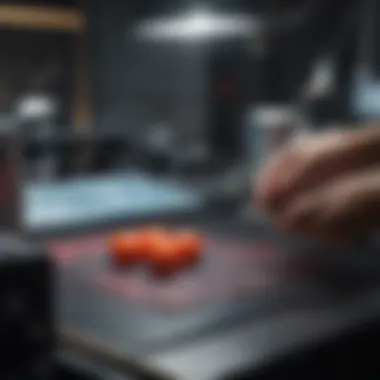
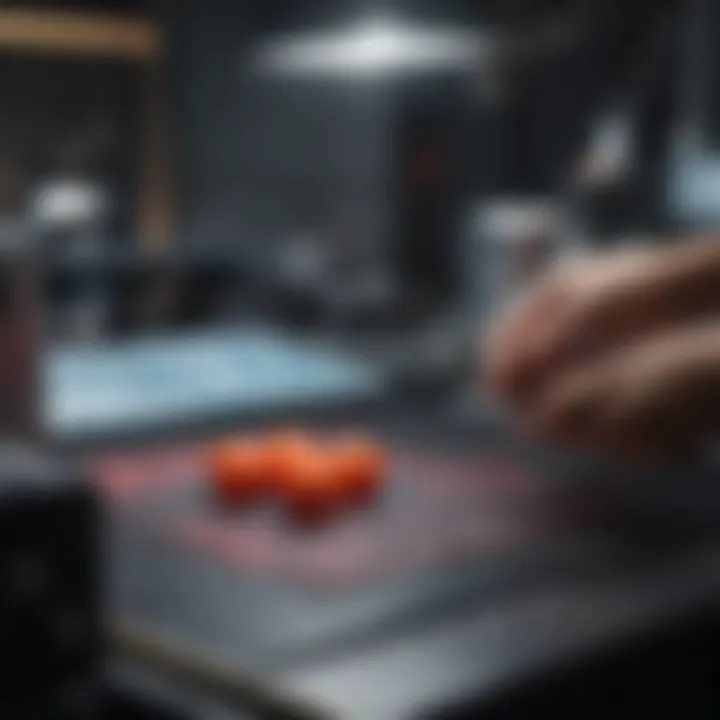
Post-printing considerations are essential for achieving high-quality results in screen ball screen printing. This stage ensures that the printed designs not only appear aesthetically pleasing but also last longer and maintain their integrity over time. Proper attention to curing, drying, and equipment maintenance can significantly enhance the durability of the prints and the efficiency of the screen printing process.
Curing and Drying Techniques
Curing is the process that solidifies the ink on the printed material. It is crucial for guaranteeing that the ink adheres properly and becomes resistant to fading, washing, and scratching. The effectiveness of curing directly impacts the longevity of the print.
Key techniques for curing include:
- Heat Pressing: Using a heat press allows for uniform heating across the print, promoting thorough curing. This method is particularly effective for plastisol inks.
- Flash Dryers: These devices use intense infrared heat to cure ink quickly after the initial print pass. Flash dryers save time, especially during multi-layer printing processes.
- Conveyor Dryers: These systems maintain a consistent temperature over a longer period, suitable for larger production runs. They ensure that the printed items are sufficiently cured as they move through the dryer.
It is important to monitor the curing temperature and time accurately; otherwise, under-cured prints may result in smudges, while over-cured prints can become brittle. Depending on the type of ink used, different curing methods may yield better results.
Proper curing ensures your printed designs won't fade after a few washes.
Cleaning and Maintenance of Equipment
Cleaning and maintenance of screen printing equipment cannot be overlooked. Keeping tools and machinery in good condition not only extends their lifespan but also ensures consistency in print quality. Regular cleaning helps to prevent ink buildup, which can lead to blockages and impair print accuracy.
Consider the following practices:
- Screen Cleaning: After printing, rinse screens with water to remove excess ink. Use screen cleaners to tackle more stubborn residues. Avoid letting ink harden on the screens as this can cause irreparable damage.
- Squeegee Care: Always clean squeegees after use. Ink residue can lead to inconsistent application during the next printing session. Store squeegees in a flat position to prevent damage to the blade.
- Ink Storage: Properly seal containers of unused ink to prevent drying. Store inks in a cool, dark place to maintain their properties.
- Regular Equipment Check: Conduct periodic checks of all equipment components. This includes checking for wear and tear on parts like the screens, squeegees, and frames.
By incorporating these cleaning and maintenance practices into your routine, you can ensure optimal operation and functionality of your screen ball printing kit, ultimately leading to superior print quality.
Common Challenges and Troubleshooting
In any artistic endeavor, including screen ball screen printing, one can encounter various challenges. Understanding these issues helps improve printing outcomes, making troubleshooting a critical aspect of mastery. This section discusses common problems that may arise during the printing process, along with strategies to address them. Each key challenge is significant because it influences not only the quality of the prints but also the overall efficiency of the entire printing operation.
Ink Consistency Issues
Ink consistency is vital for achieving uniform prints. Variations in ink thickness can lead to uneven colors and distracting textures. Different ink types, such as plastisol or water-based inks, may behave differently, affecting consistency during the printing process.
- Checking Viscosity: Test the viscosity of your ink using a viscosity cup, adjusting with additives if needed.
- Stirring Properly: Make sure to stir the ink thoroughly before use. This ensures that pigments are evenly distributed.
- Temperature Considerations: Ink can behave differently at varying temperatures. Ensure your working environment is within optimal temperature ranges to avoid unexpected changes in viscosity.
Addressing ink consistency often takes practice. Consistent checks and adjustments can lead to better overall results.
Screen Blockages and Repairs
Screen blockages are a common frustration in screen printing that can halt production. They typically occur due to dried ink or improperly prepared screens. When ink accumulates, it affects the flow, which leads to unsatisfactory prints.
To remedy this issue:
- Regular Maintenance: Clean screens immediately after use. This prevents ink from drying and causing blockages.
- Using Appropriate Cleaners: Different inks require specific cleaning solvents. Always choose a cleaner that suits the ink type.
- Repairing Damaged Screens: If a screen is blocked or torn, you may need to replace the screen or use screen patching techniques to repair small tears.
Proactive maintenance is essential. A clean screen can dramatically affect the outcome of prints, saving time and resources.
Misalignment Problems
Misalignment during the printing process can lead to blurry or offset prints, diminishing the overall quality and aesthetic appeal. This issue often arises from improper registration of the screen to the substrate or misaligned print layers.
To avoid misalignment, consider these steps:
- Check Registration: Always ensure that each screen is properly registered before printing. A misaligned screen can cause shifts in the design.
- Use Registration Marks: Employ registration marks to align layers correctly, which aids in achieving precise placement during printing.
- Tension Control: Maintain proper tension on the screens. Loose screens can shift during printing, leading to misalignment.
Being vigilant about alignment significantly enhances print quality. Awareness of these potential misalignments can lead to improved results in your screen ball printing projects.
"The key to successful screen printing is understanding and addressing the challenges that arise throughout the process. Awareness and preparation can transform obstacles into opportunities for improvement."
In summary, navigating through the common challenges such as ink consistency issues, screen blockages, and misalignment problems is essential for successful screen ball screen printing. By implementing preventive measures and adopting effective troubleshooting techniques, one can enhance both the quality of the prints and the efficiency of the printing process.
Advanced Techniques in Screen Printing
Advanced techniques in screen printing are crucial for both enhancing the quality of prints and expanding the creative possibilities for practitioners. These methods allow artists and manufacturers to experiment beyond basic printing approaches. By incorporating advanced techniques, one can achieve more detailed, vibrant, and unique results, setting their work apart in a competitive landscape. This section will delve into two key areas: multi-color printing techniques and the use of special inks, each contributing significantly to the depth and versatility of screen printing.
Multi-Color Printing Techniques
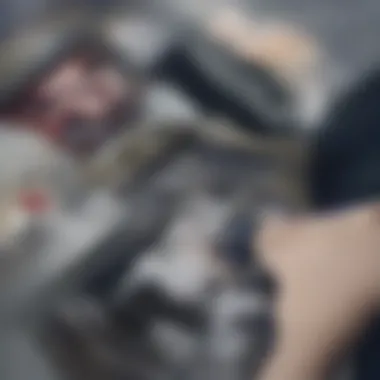
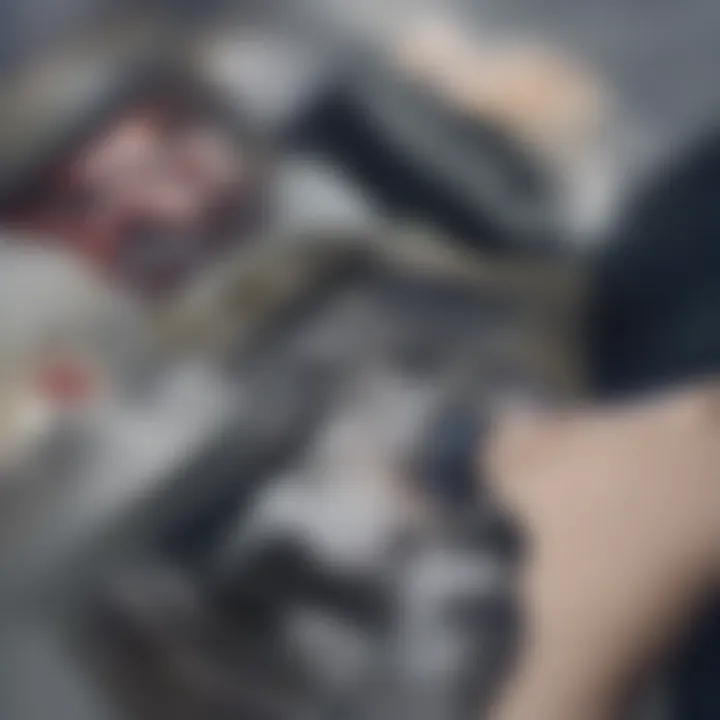
Multi-color printing techniques in screen printing involve layering different colored inks to create detailed and vibrant images. This process requires a good understanding of color theory and precise registration to ensure that each layer aligns correctly. The benefits are manifold. It enables the reproduction of complex designs with multiple colors, thus allowing for greater artistic expression.
When approaching multi-color printing, the following methods can be utilized:
- Spot Color Printing: This method involves using specific inks for each color in the design instead of mixing inks. It results in pure colors that are consistent across prints.
- Process Color Printing: Here, four standard colors (cyan, magenta, yellow, and black) are used. By overlapping these colors in varying degrees, a full spectrum of hues can be achieved.
- Simultaneous Printing: This technique involves printing several colors at once on the same screen. It requires precise setup but can greatly enhance efficiency.
For beginners, achieving success with multi-color techniques often means investing time in practice. Key considerations include understanding the drying times of different inks and ensuring that each layer is cured properly before applying the next layer.
Use of Special Inks
The use of special inks in screen printing opens a realm of possibilities that standard inks simply cannot offer. Special inks, like metallic, glow-in-the-dark, or water-based inks, provide unique attributes that can enhance a design's appeal. For instance, metallic inks can add a shiny finish that catches the eye, while glow-in-the-dark inks can create unexpected effects in low light conditions.
Considerations for using special inks include:
- Ink Compatibility: Not all materials work well with specialty inks. It's imperative to test small samples before committing to a larger print run.
- Application Techniques: Special inks often require unique printing techniques. For example, certain metallic inks need a specific type of screen mesh to disperse evenly.
- Curing and Drying: The curing process for special inks may vary, necessitating adjustments to time and temperature settings during drying.
Utilizing special inks can elevate the quality of prints, but understanding the properties and application methods is key to achieving the desired outcome.
"Innovation in screen printing often emerges from the creative use of new materials and techniques, pushing the boundaries of what can be achieved in this art form."
Applications of Screen Ball Screen Printing Kits
Screen ball screen printing kits serve a variety of purposes across different sectors. Understanding these applications is important for anyone looking to make the most of their screen printing capabilities. This section identifies key areas where these kits can be effectively utilized, highlighting their benefits and considerations.
Textiles and Apparel Industry
The textiles and apparel industry is one of the primary users of screen ball screen printing kits. Businesses use these kits to create unique designs on clothing and fabrics. The ability to apply vivid colors and intricate patterns makes screen printing a preferred choice in this industry.
Key benefits of this application include:
- Durability: Screen printing offers prints that are long-lasting and resistant to fading, ensuring that designs remain vibrant through numerous washes.
- Versatility: This method can be applied to various materials like cotton, polyester, and blends, making it suitable for different types of apparel.
- Customization: Companies can create custom designs tailored to specific customer demands, adding value to their products.
Considerations in the textiles and apparel industry involve choosing the right inks and materials that align with the target market's expectations. For example, water-based inks are ideal for eco-conscious consumers, while plastisol inks are great for bright, vivid colors.
Marketing and Promotional Items
Another significant application lies within marketing and promotional items. Businesses often utilize screen printing kits to produce branded merchandise, such as t-shirts, tote bags, and caps.
The advantages here include:
- Brand Visibility: Custom printed items act as walking advertisements, promoting brand recognition when worn or used by customers.
- Cost-Effectiveness: Bulk printing reduces per-item costs, making it financially viable for businesses looking to hand out promotional materials.
- Quality Output: Screen printing provides high-quality prints that are appealing to consumers, enhancing the perceived value of promotional items.
In this sector, the choice of colors and the design’s clarity plays a crucial role. Businesses should ensure that their prints align with their branding strategy for maximum effectiveness.
Art and DIY Projects
Screen ball screen printing kits are not limited to commercial applications; they also find a home in the art and DIY community. Artists and hobbyists use these kits to create personalized artworks or crafts.
The benefits associated with this application include:
- Flexibility: Artists can experiment with various fabrics, surfaces, and inks, allowing for unlimited creativity.
- Affordability: DIY enthusiasts can produce artwork at a lower cost compared to purchasing pre-printed items.
- Skill Development: Using screen printing helps individuals enhance their skills in designing, printing, and even color mixing.
When approaching art with screen printing, it is essential to be aware of the materials chosen. Some artists opt for specialty inks such as glow-in-the-dark or metallic inks to offer something unique. Understanding the process and materials available allows for more informed and creative choices.
"Screen ball screen printing kits enable a versatile approach to creativity and branding, from clothing to art projects."
End and Future Trends
The section on conclusion and future trends is crucial to wrapping up the insights provided in this article. It summarizes the key elements discussed regarding screen ball screen printing kits and projects where the industry is heading. Understanding these trends is important for practitioners who want to stay relevant in the field and utilize the most effective techniques. The evolving nature of screen printing technologies creates both opportunities and challenges.
Summary of Key Insights
Through this article, readers have been exposed to the fundamental concepts involved in screen ball screen printing. Some significant insights include the importance of proper setup and configuration of the kits. Elements like screen stretching, emulsion application, and curing techniques are vital for achieving high-quality prints. Moreover, knowledge of the various components, such as inks and squeegees, equips users to tailor their processes according to their specific needs. This guide emphasizes that both novices and experienced users can benefit from adhering to best practices to optimize their printing endeavors. Using appropriate tools and troubleshooting methods leads to better overall results.
Emerging Technologies in Screen Printing
The screen printing industry is experiencing a wave of technological advancements. These emerging technologies not only enhance the efficiency of the printing process but also broaden the scope of creative possibilities. For instance, innovations in digital printing and hybrid screen printing methods are changing the landscape. New inks that offer better adhesion and flexibility transform what can be printed onto various substrates.
Additionally, automation in the printing process signifies a shift towards operational efficiency, especially in high-demand environments. This is complemented by software advancements for design and production management, making the entire workflow more streamlined. Such technologies hold the promise of reducing labor costs and minimizing errors. Keeping abreast of these trends allows screen printing professionals to adopt new practices that will likely become industry standards.
"Innovation is the key to remaining competitive, and staying updated on technological advancements ensures one’s place in the evolving market."
As we look ahead, the connection between screen ball screen printing kits and technological progress will be vital. Integrating these advancements will enhance creative expression and operational efficiency. The focus should be on embracing change while retaining the core principles that define high-quality screen printing.