Exploring the Applications of Modular PLCs
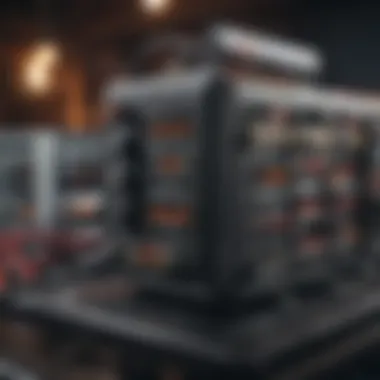
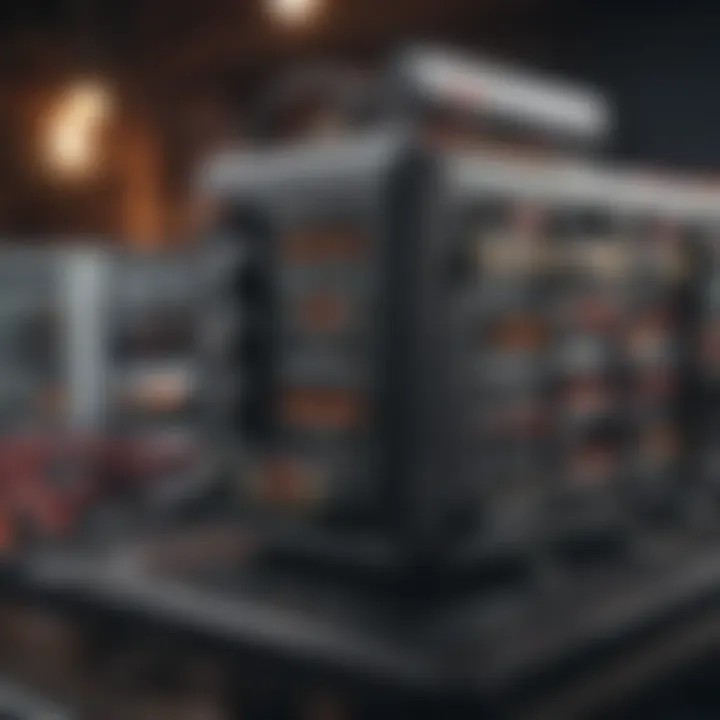
Intro
In today’s rapidly evolving industrial landscape, automation has become the backbone of efficiency and productivity. Central to this evolution is the rise of modular programmable logic controllers (PLCs), which offer unmatched flexibility and adaptability compared to their traditional counterparts. These systems allow organizations to cater to specific operational requirements, enabling streamlined processes tailored to diverse applications across various sectors.
The modular nature of these PLCs empowers industries, be it automotive, food processing, or pharmaceuticals, to interchange components as needed, thus fostering an environment of continuous improvement. This adaptability not only drives operational efficiency but also enhances scalability, allowing businesses to respond effectively to market demands without incurring excessive costs.
Understanding modular PLC applications entails going beyond mere functionality; it requires an appreciation of their design philosophies and how they can integrate with existing industrial equipment. In an age where data is king, the connectivity and interoperability provided by modular PLCs lay the foundation for smart factories and Industry 4.0 concepts.
As we break down the core aspects of modular PLCs in this article, we will delve into how these controllers can reshape operational paradigms, explore their multifarious applications, and investigate the future trends that may shape the trajectory of industrial automation.
Research Context
Background and Rationale
The imperative for enhancing process optimization in industries has never been clearer. As global competition intensifies, the need for automation systems that can swiftly adapt to changes in production demands becomes critical. Modular PLC systems answer this call by offering a design that allows for upgrades and modifications without the need for entirely new setups.
This aspect of modularity reduces downtime and allows businesses to pivot quickly, adapting to new challenges and technologies. Furthermore, with the trend toward remote management and the Internet of Things (IoT), PLCs’ modularity significantly enhances their role within the digital ecosystem, paving the way for more innovative industrial applications.
Literature Review
The existing body of literature supports the notion that modular PLCs significantly contribute to operational flexibility and efficiency. For instance, studies published in prominent industrial automation journals have highlighted case studies that illuminate the successful implementation of modular systems.
- Important findings include:
- Enhanced system interoperability.
- Reduction in operational costs through efficient upgrades.
- Improved maintenance protocols leading to minimized downtime.
By sifting through a variety of sources, we get a picture of how many organizations have fundamentally shifted their automation strategies to embrace modular PLCs. While traditional systems often come with limitations in adaptability, modular PLCs can incorporate newer technologies seamlessly, offering a glimpse into an integrated future in industrial automation.
With this understanding, we move on to examine how we can explore modular PLC applications more deeply.
Methodology
Research Design
To explore the applications of modular PLCs, a qualitative approach will be adopted. This includes case studies and interviews with industry experts to gather insights on current use cases and future trends. Exploring the lived experiences of professionals working within industries utilizing these technologies will provide invaluable perspective.
Data Collection Methods
Data will be collected through interviews, surveys, and existing case studies documented in reputable journals and industry reports. Special focus will be placed on the key performance indicators (KPIs) that define success in modular PLC implementations. This approach aims to construct a comprehensive overview that is not only informative but also reflective of real-world applications and challenges associated with modular PLCs.
By employing this multifaceted research design, this article aspires to deliver a robust examination of modular PLC applications, enabling readers to appreciate their transformative potential in the world of industrial automation.
Foreword to Modular PLCs
When discussing automation and control systems, it’s hard to ignore the pivotal role of modular programmable logic controllers (PLCs). These devices are not just pieces of tech sitting in a factory corner; they are the backbone of modern industrial operations, allowing for unprecedented levels of flexibility and scalability. Understanding modular PLCs is essential because they enable industries to adapt rapidly to changing production demands, optimize processes, and integrate seamlessly with newer technologies.
This segment will shed light on the nature of modular PLCs, discussing their key traits and how they differentiate from traditional PLCs. Overall, grasping the concepts around modular PLCs is vital for all stakeholders involved in industrial automation. Whether you are a seasoned engineer, an entrepreneur looking to delve into automation, or a student keen on understanding modern manufacturing, the insights provided here can shape your approach to leveraging technology for efficiency and innovation.
Definition and Overview
A modular PLC is primarily a system designed to control industrial equipment and processes. It does this by utilizing interchangeable components—modules that can be swapped in and out based on specific requirements. For example, a basic modular PLC might consist of a central processing unit (CPU), input/output (I/O) modules, and communication interfaces. Each module serves a specific function and can be customized to meet particular operational needs.
This modularity allows for upgrades or changes without replacing the entire system, which ultimately saves time and cuts costs. Think of it like building with Legos. Each piece serves a purpose, and when you need to build something new, you don’t have to start from scratch—you just swap out a few pieces.
In practical terms, this means a factory might start with a simple input/output module to manage lights and alarms, but as operations expand, they can add modules that control complex machinery, incorporate remote monitoring, or interact with the Internet of Things (IoT). This inherent flexibility in design provides a robust solution for evolving industrial environments.
Historical Context
The evolution of modular PLCs didn’t happen overnight. Their predecessors were monolithic systems, often bulky and less adaptable, akin to driving a tank when what you really needed was a versatile SUV. The industrial landscape was changing rapidly in the late 20th century, with demand for higher efficiency and greater adaptability in manufacturing processes. In response to these needs, engineers began experimenting with a modular approach, resulting in the first generation of modular PLCs appearing in the 1970s.
From the early beginnings, manufacturers like Allen-Bradley and Siemens recognized the potential of creating systems that could be easily modified and scaled. And so, the modular PLC came into existence—a notable shift away from the inflexible systems of yore.
Over the years, various advancements in technology led to smaller, more efficient modules that could handle complex tasks, further enriching the capabilities of modular PLC systems. This historical progression not only illustrates innovation but also highlights a fundamental shift in how industries perceive automation—moving towards customizable solutions that meet specific operational needs while maintaining a larger focus on efficiency.
The timeline of modular PLC development reflects broader trends in technology as well. For instance, the rise of digital communication and networking allowed PLCs to connect with other systems over the internet, creating opportunities for more integrated solutions in industries from manufacturing to smart building technologies.
As businesses continue to evaluate their operations in the face of economic pressures, the importance of modular PLCs in today’s landscape cannot be overstated. They represent a convergence of historical necessity and modern ingenuity, shaping the framework of future industrial automation.
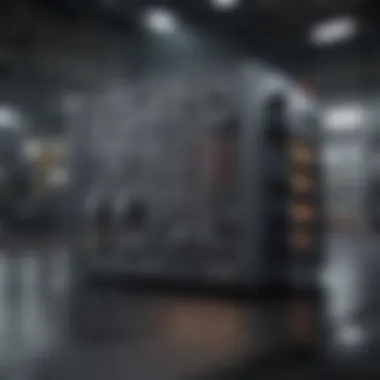
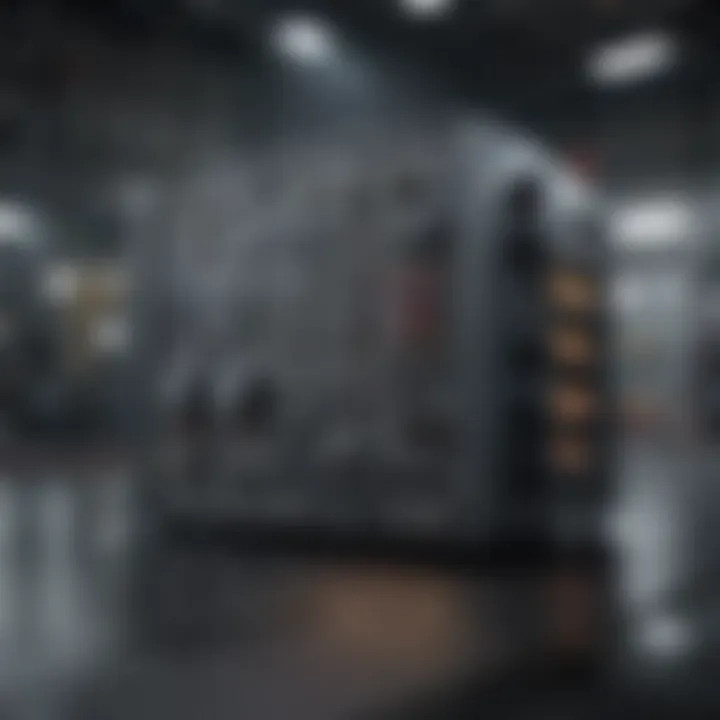
Key Components of Modular PLCs
Understanding the key components of modular PLCs is vital for anyone looking to navigate the complexities of industrial automation. These components not only define the operational capacity of the PLC but also offer insights into the overall flexibility, scalability, and efficiency of the systems. Here, we’ll break down the essential elements that compose a modular PLC and discuss how each contributes to its multifunctionality.
Processing Unit
At the heart of every modular PLC lies the processing unit. This crucial component, often referred to as the CPU, is the brain of the system. It executes the control logic and processes inputs and outputs in real time, ensuring smooth operation of the entire automation setup.
The significance of a robust processing unit cannot be overstated. It’s responsible for interpreting user commands, managing data from the input modules, and sending signals to output devices. The speed and efficiency of the processing unit directly impact the responsiveness of the entire system.
Moreover, modern processing units can manage complex algorithms, allowing for intricate programming that goes beyond basic control functions. With advancements in technology, many CPUs now come equipped with enhanced capabilities such as multi-threading and parallel processing. This means that they can manage multiple tasks simultaneously, vastly improving performance and efficiency.
Input/Output Modules
Input and output modules serve as the sensory and motor functions of modular PLCs. They play an essential role in gathering information from the physical environment and translating that into signals that the processing unit can understand.
- Input Modules: These are responsible for receiving signals from various sensors and devices, such as temperature sensors, proximity switches, or pressure gauges. They convert analog or digital signals into a format comprehensible by the processing unit. For example, a temperature sensor might send a varying voltage that the input module translates into a specific temperature reading.
- Output Modules: On the flip side, output modules take commands from the processing unit and relay them to actuators, motors, or other output devices. They essentially perform the actions based on the processed data. This could mean turning on a pump, activating a conveyor belt, or adjusting a valve.
Both types of modules can be tailored in terms of input and output capacities, making them a flexible choice for various applications. This modularity allows industries to customize their control systems according to specific operational needs.
Communication Interfaces
Communication interfaces are pivotal in how modular PLCs connect and communicate with other systems, facilitating integrated operations across different platforms. They ensure that data can flow seamlessly between the PLC and external devices or networks, which is crucial for modern automation systems.
The significance of effective communication interfaces includes:
- Interoperability: With different devices and systems often using varying protocols, reliable communication interfaces help ensure different components can work together.
- Expansion: Good communication allows for the addition of more devices or systems in the future without needing a complete overhaul of the existing setup.
- Data Exchange: Rapid data transfer is essential in making real-time decisions. Communication interfaces facilitate this by using protocols like Ethernet/IP, Profibus, or Modbus, among many others.
"The effectiveness of a modular PLC system greatly depends on how well these components work together, creating a seamless flow of information and control."
For more insights on programmable logic controllers and their functionalities, check out Wikipedia and Britannica.
Flexible Architecture of Modular PLCs
In today’s fast-paced industrial landscape, the flexible architecture of modular programmable logic controllers (PLCs) stands as a pillar of efficiency and adaptability. This flexibility is more than just a buzzword; it's about how businesses can respond to changing demands and integrate new technologies smoothly. Modular PLCs allow for a tailored approach in system design, providing an edge that is crucial for maintaining competitive advantage in various sectors.
Scalability
Scalability in modular PLCs refers to the ability to expand or reduce the system according to operational needs. Imagine a manufacturing plant that starts small and later grows to meet increased demands. A modular PLC can be expanded simply by adding new I/O modules, processing units, or communication interfaces. The process resembles adding building blocks—each piece seamlessly integrates with existing components, allowing for enhanced functionality without overhauling the entire system.
The benefits of scalability are several:
- Cost Efficiency: Companies avoid the significant costs associated with entirely new systems by upgrading incrementally.
- Tailored Solutions: Businesses can customize their systems to meet specific operational requirements, adapting to changes in production levels without unnecessary complexity.
- Future-Proofing: By designing systems that can be easily scaled, organizations can prepare for unforeseen technological advances or shifts in market demands.
However, it's essential to consider potential challenges with scalability. Compatibility must be ensured among the varied modules, as an outdated module might hinder performance. Careful planning can mitigate these issues, ensuring smooth expansion or contraction of resources.
Configurability
Configurability deals with the flexibility in how a modular PLC system can be set up and configured according to specific application needs. The modularity allows users to choose the right mix of components that best fit their tasks. For instance, a food processing plant may require specific temperature sensors and control modules that are different from those used in an automotive assembly line. The configurability ensures that each application can benefit from tailored solutions rather than one-size-fits-all setups.
The advantages of configurability include:
- Enhanced Productivity: Systems can be adjusted for optimal performance, reducing downtime and improving production efficiency.
- User-Friendly Interfaces: Many modular PLCs come with intuitive software tools that allow users to easily configure systems, making it accessible even to those with limited technical expertise.
- Rapid Integration: New technologies, such as IoT devices, can be integrated without a complete redesign of the existing system, facilitating quicker adaptation.
Despite the positive aspects, a downside to configurability might be the complexities it introduces. Users may face challenges in ensuring all parts operate harmoniously, making the initial setup and integration potentially more demanding than simpler, non-modular systems.
"In the realm of industrial automation, the adaptability of modular PLCs isn't just a nice-to-have; it's a necessity. Their design allows companies to innovate while staying grounded in practical application."
Applications in Various Industries
In the landscape of industrial automation, modular PLCs find themselves at the heart of various operational processes across multiple sectors. Their adaptability and efficiency make them invaluable tools for managing, monitoring, and optimizing production systems. As we delve further into the topic of modular PLC applications, we'll uncover specific examples highlighting their significance and advantages across diverse fields. Understanding these applications is crucial, as they reveal how modular PLC technology influences productivity, cost reduction, and operational agility.
Manufacturing and Production
The manufacturing sector arguably reaps the most benefits from modular PLC implementation. These systems serve as the backbone for production lines, enabling seamless control over equipment and processes. For instance, automotive assembly lines utilize modular PLCs to synchronize robotics, conveyor belts, and quality assurance systems. This results in a smooth workflow that minimizes downtime, maximizes output, and upholds product quality.
Moreover, the benefits of employing modular PLCs in manufacturing extend beyond simple automation. Their scalability enables production facilities to expand or modify operations without overhauling the entire control system. If a company decides to increase its production capacity, new modules can be added easily, minimizing system interruptions. This flexibility not only enhances productivity but also increases cost-effectiveness in the long term.
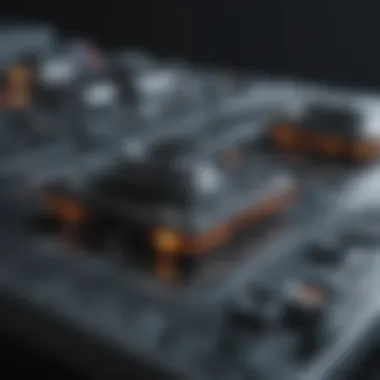

Building Automation
In the realm of building management, modular PLCs shine through their capacity to integrate various systems from heating and cooling to lighting controls. Consider a smart office building where energy efficiency and occupant comfort are paramount. Modular PLC systems can manage these elements autonomously or through a central SCADA system, adjusting temperature and lighting based on real-time occupancy data.
This approach not only optimizes energy usage but also ensures a better working environment for occupants. For property managers, the reduction in energy costs and improved tenant satisfaction are compelling incentives to implement modular PLC solutions. Additionally, the ability to retrofit existing structures with modular systems adds considerable value, allowing buildings to transition smoothly into the eco-friendly era.
Water Treatment Facilities
Water treatment facilities are increasingly harnessing the power of modular PLCs to enhance operational efficiency and ensure regulatory compliance. These systems can oversee multiple processes such as filtration, chemical dosing, and disinfection. By linking to real-time sensors, modular PLCs can adjust chemical use based on water quality parameters, ensuring the treatment process is continuously optimized.
For instance, if a drop in water quality is detected, the PLC can automatically increase the dosage of disinfectants, thus avoiding costly contamination incidents. This level of responsiveness not only safeguards public health but also streamlines operational costs. The modularity aspect also means that as treatment demands increase, facilities can add modules without major disruptions.
Oil and Gas Operations
In the oil and gas sector, the reliability of automation systems is paramount. Modular PLCs offer the robustness required for remote operations such as drilling or production. Given the often harsh environments, these systems provide fault tolerance and easy communication between components spread over vast areas.
For example, a modular PLC can effectively coordinate various equipment involved in the extraction process, such as pumps, compressors, and pressure monitoring systems. Their ability to integrate with remote communication technologies means operators can always stay connected to their systems, allowing for real-time data analysis and decision-making.
Furthermore, the availability of various modules means that companies can customize their setups based on specific operational needs. As market demands shift, modular PLCs facilitate swift adjustments, maintaining competitive advantage in a rapidly changing industry.
Modular PLCs exemplify how adaptable technology can streamline operations and enhance efficiency across diverse industries, proving they are not just tools but essential partners in modern automation.
Integration with Other Systems
The synergy between modular PLCs and other systems is pivotal in modern automation landscapes. Effective integration allows different hardware and software components to work together harmoniously, enhancing operational efficiency and decision-making capabilities. By embracing integration, industries can break silos and unite data streams, leading to smarter and more responsive operations.
SCADA Systems
Supervisory Control and Data Acquisition (SCADA) systems play a critical role in overseeing industrial processes. Integrating modular PLCs with SCADA provides a significant edge in monitoring and controlling various operations.
- Real-time Data Access: With this combination, operators gain immediate visibility into process variables. The actionable data empowers decision-makers to respond swiftly to any anomalies.
- Centralized Control: A unified SCADA interface allows operators to maintain an overview of multiple PLC systems scattered across facilities, leading to a more efficient management of resources.
- Scalability: As businesses grow, adding new PLCs to the SCADA system is relatively straightforward, ensuring that the system adapts to the evolving landscape.
Integrating modular PLCs with SCADA systems not only maximizes efficiency but also enhances the overall resilience of operations.
Sensor Networks
Sensor networks complement modular PLCs by providing critical data needed for automation. Through integration, the value of sensor inputs jumps significantly.
- Enhanced Data Collection: Modular PLCs can gather and analyze data from a multitude of sensors, enriching input for better process control.
- Faster Response Times: Sensors can relay immediate information about changes in the environment or equipment monitored. This rapid data relay enables prompt action, reducing downtime.
- Predictive Maintenance: By employing sensor networks, modular PLCs can predict failures before they occur. This can save both time and money as maintenance is timely instead of reactive.
IoT and Smart Technology
The move toward the Internet of Things (IoT) has carved a new pathway for modular PLC integration. As more devices become interconnected, harnessing that connectivity can transform operations.
- Data Interchange: Modular PLCs can connect with various IoT devices, from smart sensors to cloud computing resources. This allows for a seamless flow of information across the network.
- Remote Monitoring and Control: IoT capabilities allow operators to manage systems from afar. They can access real-time data and control operations remotely, which is crucial for maintaining productivity when conditions change unpredictably.
- Analytics and Machine Learning: By integrating with smart technologies, PLCs can utilize advanced analytics and machine-learning models. These tools provide actionable insights that drive process improvements and increase efficiencies.
Case Studies of Modular PLC Implementations
When discussing modular programmable logic controllers (PLCs), real-world implementations provide valuable insights into their effective use and advantages across varied applications. These case studies spotlight how organizations have navigated their unique challenges and leveraged modular PLCs to streamline operations, enhance productivity, and achieve better integration within their systems.
The importance of these case studies cannot be overstated. They serve as a testament to the adaptability and efficiency of modular PLCs in diverse industries. By analyzing these examples, professionals can glean best practices, identify potential pitfalls to avoid, and understand the practical benefits that can emerge from deploying these systems.
Successful Manufacturing Integration
In the fast-paced world of manufacturing, time is often equated with money. One notable case involves a car manufacturing plant that transitioned from traditional control systems to a modular PLC architecture. By employing a Modular PLC setup, the plant was able to manage multiple production lines simultaneously without the typical bottlenecks associated with less flexible systems.
Implementing modular PLCs enabled seamless communication between machines and operators. The new system allowed for rapid adjustments to production schedules based on real-time data analytics. This responsiveness ensured that the plant could quickly shift production priorities without incurring excessive downtime. Here are several perks noted during this transition:
- Increased Flexibility: Modular PLC systems allowed the plant to reconfigure machine assignments quickly in response to changes in demand.
- Enhanced Monitoring Capabilities: Operators could monitor multiple parameters through one interface, which simplified the overall operation and maintenance processes.
- Reduction in Operational Costs: Streamlined production lines minimized waste and reduced the need for extensive manual intervention.
This case exemplifies how a well-executed modular PLC integration can significantly elevate manufacturing processes, resulting in a more responsive and efficient production environment.
Building Management Systems
Another compelling example is the integration of modular PLCs within smart building management systems. In a prominent office complex, the facilities management team faced challenges with manual control systems that led to increased energy costs and inefficiencies.
By implementing a modular PLC system, they centralized the control of HVAC, lighting, and security systems. This integration allowed for precise control and monitoring of building systems in real-time, resulting in a more consolidated management approach. Some critical outcomes from this initiative included:
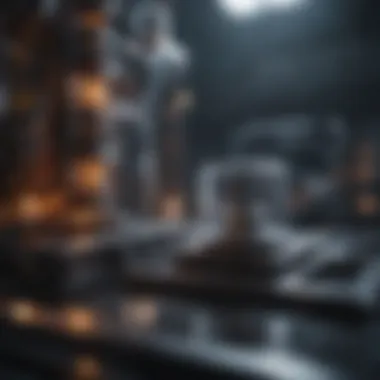
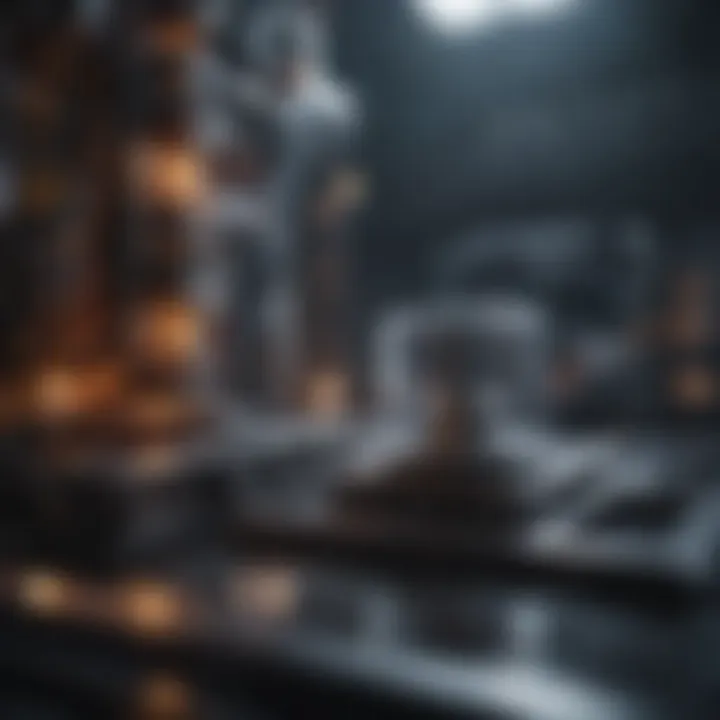
- Optimal Energy Usage: With the capability to monitor energy consumption closely, the building could optimize heating and cooling schedules based on occupancy patterns.
- Improved Security Maintenance: The system enabled automatic alerts for intrusions, fire hazards, and other emergencies, thereby enhancing overall building security.
- Sustainability Benefits: With a focus on efficient resource utilization, the building achieved significant reductions in carbon footprint, aligning with modern sustainability goals.
Overall, these case studies underscore the practicality and real-world implications of adopting modular PLC technologies. They illustrate that whether in manufacturing or facility management, the decision to implement modular PLCs transcends merely operational improvements; it is a strategic move towards future-readiness, driving significant advances in efficiency and capability.
Challenges and Limitations of Modular PLCs
Understanding the challenges and limitations of modular PLCs is paramount for industry professionals and researchers who are keen on maximizing the potential of automation technologies. Although modular PLCs offer significant advantages in terms of flexibility and scalability, they also present certain hurdles that need careful management. Recognizing these challenges can lead to better planning and implementation processes, ultimately ensuring that the advantages outweigh the drawbacks. Below, we delve into the specifics of these challenges, examining cost implications, integration complexities, and maintenance issues.
Cost Implications
When considering modular PLCs, cost can be a double-edged sword. On one hand, these systems allow businesses to tailor their automation setup, investing only in the modules necessary for their specific processes. Yet, on the other hand, the initial investment can be quite steep.
- Selecting Modules: Every module comes with its own price tag. This means that assembling an effective system requires a thoughtful approach to module selection, which can drive costs up depending on needs.
- Training and Expertise: Implementing a modular PLC system often necessitates training existing staff or hiring new talent skilled in using these systems. This additional expenditure can significantly impact budgets, particularly for smaller businesses.
- Long-Term Investment: The longevity and adaptability of modular PLCs often mean that, while the upfront costs may be high, the total cost of ownership may be lower when spread over time. However, businesses must weigh these factors carefully.
Complexity of Integration
One cannot overlook the integration challenges that come with modular PLC systems. These systems must seamlessly work with existing machinery, software, and networks, which is no small feat.
- Diverse Protocols: Modular PLCs often use different communication protocols, which can cause compatibility issues. This fragmentary nature can lead to a complex patchwork of systems that may not inspire confidence, especially in mission-critical environments.
- Customization: Customizing modules to fit unique operational needs can introduce variables that complicate integration. While each module offers adaptability, customization can counteract the straightforward benefits of modular design, escalating timeframes and costs.
- Interconnectivity: Ensuring all components are appropriately interconnected, particularly when dealing with multiple vendors, can lead to headaches. Variations in standards might require specialized knowledge to navigate effectively.
Thus, while the modular approach fosters flexibility, the complexities in integration can pose significant disruptions if not managed meticulously.
Maintenance and Support Issues
Maintenance is yet another vital consideration when employing modular PLCs. While these systems are often designed for ease of maintenance, some challenges can emerge that should not be overlooked.
- Vendor Dependencies: Different modules may come from various manufacturers, complicating maintenance. If a specific module fails, it can impact system performance and lead to lengthy downtimes while waiting for support from disparate sources.
- Skill Requirements: Maintenance tasks demand a diverse skill set as the modules may require different troubleshooting methods. Teams may need to undergo continuous training to keep up with evolving technologies, possibly leading to resource strain.
- Documentation Gaps: A lack of comprehensive documentation related to each module can complicate maintenance. When systems are not uniformly documented, the risk of misdiagnosis or incorrect repairs increases significantly, further endangering the efficiency of operations.
In summary, while modular PLCs promote efficiency and flexibility, they carry certain maintenance burdens that organizations must judiciously address.
Future Trends in Modular PLC Applications
As we look ahead, the landscape of modular programmable logic controllers (PLCs) is evolving rapidly, driven by advancements in technology and changing industrial requirements. Understanding these future trends is vital because they shape how industries adopt and implement automation solutions. This section delves into notable advancements and integration potentials that will likely influence modular PLC applications going forward.
Advancements in Automation Technology
The continuous improvements in automation technology are pushing the boundaries of what modular PLCs can achieve. For instance, the rise of edge computing is significant. It allows PLCs to process data locally, leading to reduced latency and faster response times. As operations grow more automated, having the capability to analyze data without depending on a centralized server enhances decision-making efficiency.
Moreover, the development of more sophisticated sensors and actuators contributes to richer data inputs. Here are key advancements shaping the future:
- Increased Connectivity: With protocols like MQTT and OPC UA becoming more widespread, PLCs can interface better with various devices and systems, fostering a more integrated ecosystem.
- Enhanced Processing Power: Modern microcontrollers are becoming more powerful, enabling real-time data analysis and control functionalities that were previously hard to achieve.
- User-friendly Interfaces: Advances in Human-Machine Interface (HMI) technologies are allowing users to interact with PLCs in a more intuitive way, improving overall usability.
Integration with Artificial Intelligence
The integration of artificial intelligence (AI) into modular PLC applications opens the door to unprecedented capabilities. By embedding AI algorithms within PLC systems, facilities can achieve predictive maintenance, minimizing downtime and operational disruptions.
AI-powered analytics can help in identifying patterns from vast amounts of operational data, leading to insights that can optimize production processes. Here are some key aspects to consider:
- Predictive Maintenance: Using machine learning models, PLCs can forecast equipment failures and suggest maintenance schedules, thereby reducing unexpected breakdowns and costs.
- Adaptive Control Systems: AI allows for real-time adjustments to control processes based on incoming data, enhancing efficiency and sustainability.
- Quality Control: By analyzing production data, AI can automatically adjust processes to maintain product quality, proving invaluable in competitive environments.
"The real strength of modular PLCs lies in their adaptability to emerging technologies, which ensures they remain relevant in dynamic industries."
Ending
In the realm of industrial automation, the significance of modular programmable logic controllers (PLCs) cannot be overstated. The adaptability, responsiveness, and sheer capability of these systems make them invaluable across various sectors. This article has illustrated how modular PLCs act as the backbone of modern manufacturing and other domains by driving innovation and efficiency. When one focuses on flexibility, scalability, and their role in streamlining operations, it’s clear that these controllers are players in transforming how industries operate.
Summation of Key Insights
Modular PLCs present a versatile approach to control systems, allowing firms to tailor solutions according to their operational needs. Key insights include:
- Flexibility: With their modular nature, PLCs can be configured and reconfigured to address a wide array of tasks without the need for extensive rewiring or downtime.
- Scalability: These systems grow with your business. Whether tasked with simple operations or complex processes, their design allows for easy expansion.
- Integration Capabilities: In a world increasingly reliant on smart technology, modular PLCs offer seamless integration with IoT devices and SCADA systems, positioning organizations to leverage data analytics like never before.
- Cost-Effectiveness: While there may be upfront investment costs, the long-term savings achieved through reduced downtime and increased productivity often outweigh these initial expenditures.
This synthesis reveals that companies investing in modular PLCs don't just enhance their operational efficiency; they also unlock potential for innovation and responsive growth.
The Path Forward
Looking ahead, several trends signal the evolution of modular PLC applications.
- Automation Technology Advancements: As technology progresses, so does the potential for more sophisticated modular PLC systems. Emerging technologies such as edge computing and advanced analytics are poised to deepen integration with PLCs, offering real-time monitoring and control that was previously unattainable.
- Artificial Intelligence Integration: The incorporation of AI provides intelligent decision-making capabilities, allowing for predictive maintenance and better resource management, setting the stage for smarter factories.
- Sustainability Focus: Many industries are prioritizing sustainable practices. Modular PLCs can play a pivotal role by optimizing energy use and minimizing waste in production processes.
The convergence of these trends suggests that the future for modular PLCs is bright. Organizations that embrace these innovations will not only improve their operations but will also set themselves on a path toward sustainable growth and technological leadership.
"In today's rapidly evolving landscape, agility is key. Modular PLCs are not just a trend; they represent a fundamental shift in control technology for industries seeking to thrive."
Embracing these changes, companies can better navigate the complexities of the modern market while reaping the rewards of smarter, more efficient automation solutions.