Optimal Heat Sink Designs for Enhanced Thermal Efficiency
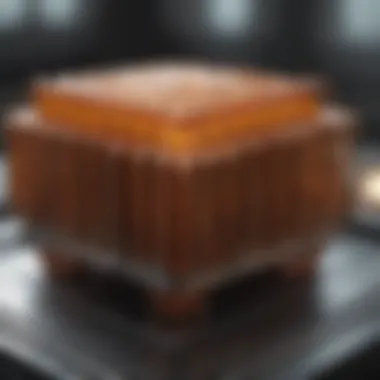
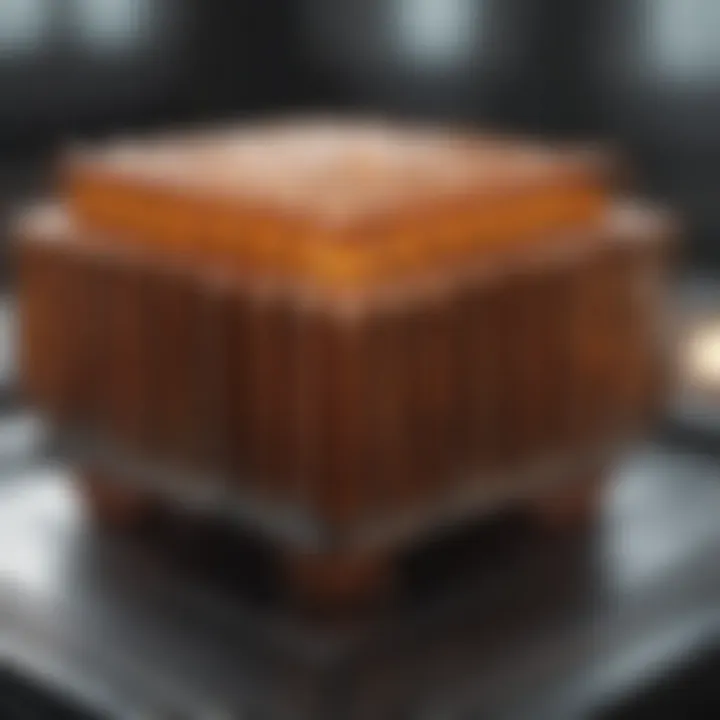
Intro
Thermal management is an essential piece of the puzzle when it comes to modern engineering. Effective heat sink design is vital in ensuring that electronic components operate within safe temperature limits. As technology continues to evolve, so does the need for innovative approaches to optimize thermal efficiency. This article seeks to unravel the multifaceted aspects of heat sink design, emphasizing not only the criteria for selection but also the performance metrics and real-world applications that shape today's industry standards.
A heat sink, in simplest terms, is a device that dissipates heat away from a component, maintaining a regulated operating temperature. This is especially crucial in electronics, where unseen thermal issues can lead to catastrophic failures. Consequently, engineers must equip themselves with a nuanced understanding of various factors—such as material properties, geometry, and airflow characteristics—that influence thermal performance.
"A well-designed heat sink is like a good referee in a game—keeping things cool under pressure without drawing attention to itself."
By diving deep into the complexities of heat sink design, this article will foster a greater appreciation for the choices engineers face, as well as provide a framework for making informed decisions in their projects. Understanding the art and science behind heat sinks opens up a dialogue that incorporates the latest findings and practices across the sector.
As we embark on this exploration, readers should expect to encounter a blend of technical know-how, a review of relevant literature, and a glimpse into the future of thermal management solutions. From students to seasoned professionals, this guide aims to enlighten and inspire.
Research Context
Background and Rationale
The function of a heat sink extends far beyond mere heat dissipation; it is foundational in the architecture of reliable electronic systems. As devices become faster and more compact, thermal challenges multiply. Traditional strategies may no longer be adequate, positioning heat sink design as a crucial area of research and application. Understanding the interplay between efficiency and effective thermal management has become paramount.
Not only does a well-designed heat sink prevent overheating, but it also enhances operational longevity, performance, and energy efficiency. Industries spanning from telecommunications to automotive manufacturing are increasingly prioritizing thermal solutions that deliver consistent results under varying conditions.
Literature Review
Current literature reveals a plethora of studies focusing on the optimization of heat sink designs through various methodologies. Recent advancements in materials, such as innovative composites and advanced alloys, offer new opportunities for improving thermal conductivity. For instance, materials like aluminum and copper remain staples for their excellent heat transfer properties, but emerging ceramic composites are gaining traction due to their lightweight yet effective nature.
More specifically, several researchers emphasize the role of computational fluid dynamics (CFD) in simulating airflow around a heat sink, thus allowing for more nuanced designs that can outperform traditional models.
Additionally, academic articles and case studies have documented real-world applications, showcasing successful implementations in high-performance computing and renewable energy sectors, piquing interest in novel heating and cooling strategies.
Intro to Heat Sink Design
Heat sink design is a pivotal aspect of thermal management, playing a crucial role in ensuring the reliability and performance of various electronic devices, automotive applications, and aerospace instruments. A well-designed heat sink effectively dissipates excess heat generated in these systems, preventing overheating and enhancing operational efficiency. In essence, it acts as a vital boundary between components that function at high temperatures and the environment, preserving both functionality and longevity.
Importance of Thermal Management
The intricacies of thermal management cannot be overstated. With modern electronics becoming more compact and powerful, the volumetric density of heat generated increases significantly. Effective thermal management guarantees not only optimal performance but also the safety of the components involved. Various studies have shown that inadequateheat dissipation can decrease the lifespan of components dramatically. For instance:
- Overheating can lead to thermal runaway scenarios, especially in sensitive applications like lithium-ion batteries.
- Performance Throttling, where systems automatically reduce operating speed to manage heat, can detract from user experience and efficiency.
Successfully managing thermal conditions elevates performance and reliability, thus avoiding costly downtimes and failures.
Overview of Heat Sink Functions
Heat sinks serve multiple functions, which may not be immediately apparent. Primarily, their role revolves around creating a larger surface area for heat transfer away from the source. However, the actual mechanics involve several key actions:
- Conduction: Heat flows from the hot component through the material of the heat sink, showcasing the significance of selecting materials with high thermal conductivity.
- Convection: Air or fluid passing over the heat sink carries heat away, making the design and orientation crucial to maximize airflow.
- Radiation: While less significant in many applications, radiation can also facilitate heat transfer, notably at elevated temperatures.
Moreover, when integrated with advanced cooling techniques—like fans or liquid cooling—heat sinks can bolster thermal efficiency further. They must be specifically tailored based on their intended application, taking into account not just thermal conditions but environmental factors like humidity and temperature swings.
"A well-designed heat sink is akin to an efficient highway system; it ensures a seamless flow of heat away from critical areas, facilitating optimal performance."
In this lively landscape of technology, understanding and implementing solid heat sink design becomes paramount. It ensures that as devices evolve, they do not fall prey to the unforgiving laws of thermodynamics, thus enabling sustained progress and innovation.
Fundamentals of Thermal Physics
Understanding the fundamentals of thermal physics is crucial in heat sink design because it lays the groundwork for effectively managing heat in various applications. Thermal physics deals with how heat moves and interacts with materials, guiding engineers in creating efficient thermal management systems. A solid grasp of these principles enables professionals to make informed decisions regarding material selection and design, ensuring better performance with less energy waste.
Heat Transfer Mechanisms
Heat transfer is the process by which heat energy moves from a hotter object to a cooler one. The primary mechanisms of heat transfer are conduction, convection, and radiation. Each plays a unique role in the functionality of heat sinks, contributing differently based on design and application.
Conduction
Conduction is the direct transfer of heat through a material, occurring when two objects are in physical contact. One specific aspect to note is the rate of heat transfer, influenced by the material's thermal conductivity. A key characteristic of conduction is its dependence on the temperature gradient; the larger the difference in temperature, the faster the heat transfer.
In the context of heat sinks, conduction is a beneficial and popular choice since metals such as aluminum or copper with high thermal conductivity are often used. These materials ensure that heat quickly travels from the hot component (like a CPU) to the heat sink, where it can be dissipated into the environment.
However, a unique feature of conduction is that it only works effectively with direct contact. Therefore, if there’s a gap or a layer of insulation, heat transfer via conduction slows down significantly, leading to lower thermal efficiency.
Convection
Convection is another significant mechanism of heat transfer, which involves the movement of fluids (liquids or gases). The specific aspect of convection important for heat sinks is the natural versus forced convection. Natural convection occurs due to buoyancy forces, while forced convection involves a fan or other mechanisms that circulate air.
The graphic representation of airflow over a heat sink highlights convection’s key characteristic: it enhances the cooling rate by moving the warm air away from the surface, allowing cooler air to take its place. This mechanism is particularly popular in designing heat sinks for electronics, as it can effectively manage elevated temperatures without the need for direct contact.
One advantage here is the ability to tailor the airflow and cooling, but a disadvantage is that it highly depends on the ambient temperature and fluid movement, which could be less effective in static conditions.
Radiation
Radiation, distinct from the previous mechanisms, involves the transfer of heat through electromagnetic waves. A vital characteristic of radiation is that it doesn’t require a medium to transfer heat, which means it can occur across a vacuum. In situations where heat sinks are exposed to environments like space, the radiation becomes critical for thermal management.
Radiation’s unique feature is its ability to operate in conjunction with the other mechanisms; it can contribute to overall heat dissipation, especially when the heat sink is at a higher temperature than its surroundings. This can be particularly advantageous when working with devices that produce a lot of heat. However, a downside is that radiation is less effective at lower temperatures and may require increased surface area or specific coatings to maximize efficiency.
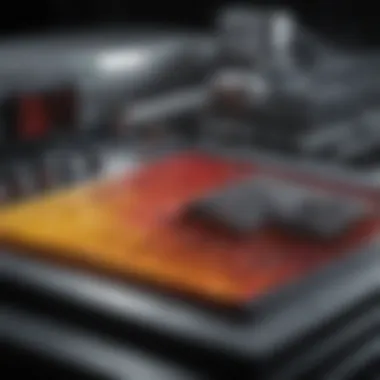
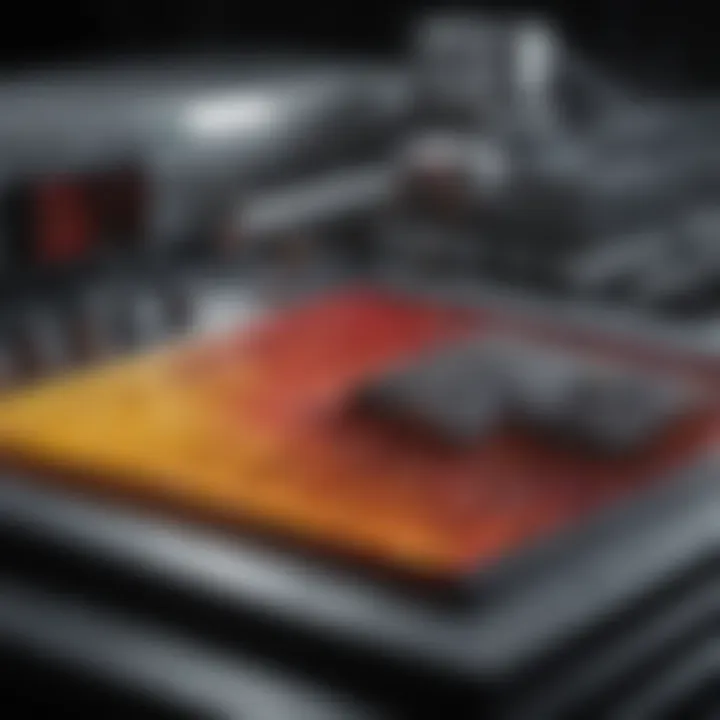
Thermal Resistance in Components
Thermal resistance is a crucial concept when evaluating the efficiency of heat sinks. Every layer of material through which heat must pass contributes to the overall thermal resistance, which can impact performance significantly. This resistance dictates how effectively a heat sink can transfer heat away from the component it’s cooling. Thus, understanding and minimizing thermal resistance in design choices is imperative for optimizing thermal management solutions.
By considering the principles of thermal physics—specifically focusing on heat transfer mechanisms and thermal resistance—engineers and designers can make grounded, strategic choices in their heat sink designs. This not only supports effective thermal management but also enhances the longevity and performance of the systems they’re employed in.
Criteria for Effective Heat Sink Design
Heat sinks play a critical role in the efficient dissipation of heat from various electronic components. Their effectiveness is rooted in a few key criteria that directly influence their thermal performance. Understanding these criteria helps designers craft solutions that not only extend the lifespan of components but also enhance overall device functionality.
Surface Area Considerations
The surface area of a heat sink is paramount in determining its efficiency. In thermal dissipation, the larger the surface area, the more heat can be transferred away from the component. Various designs focus on increasing surface areas, whether that be through the use of fins or by employing a complex geometrical shape. For instance, a heat sink with many small, closely spaced fins provides significant amounts of surface area without taking up too much volume. This design caters well to compact applications where space is a premium.
An important aspect to consider is how the increase in surface area also affects airflow. More surface area can help trap more heat, but if airflow is restricted, it can have the opposite effect. Thus, achieving a balance between surface area and airflow is essential for optimal heat sink performance.
Material Selection
Selecting the right materials for heat sink construction is crucial. Not only do materials determine thermal conductivity, cost efficiency, and weight, but they also affect the manufacturing process and the final product’s durability.
Thermal Conductivity
Thermal conductivity is a defining characteristic when choosing materials for heat sinks. Materials like aluminum and copper are popular due to their high thermal conductivity. Aluminum, for example, is often favored because it offers a good balance between cost and weight, making it particularly beneficial in consumer electronics where portability is important. Copper, while more expensive, outshines aluminum in terms of thermal conductivity. This means it can transport heat away more efficiently, which is vital for high-performance applications, such as in some gaming consoles.
One unique feature of high thermal conductivity materials is that they often allow for thinner designs without sacrificing performance. This can offer advantages in tighter spaces but can also lead to higher costs, which vendors must weigh against the performance gains.
Cost Efficiency
Cost efficiency ties closely with material selection. The materials chosen for a heat sink must not only meet thermal requirements but also fit within budget constraints. Although materials like aluminum represent a cost-effective choice, designers sometimes lean towards copper for high-end applications, despite its higher price point. The additional costs can often be justified with the improved longevity and reliability.
An interesting aspect of cost efficiency is how it can influence the entire manufacturing process. Lower-cost materials might allow for an easier production process, but can also mean trade-offs in performance over time. Thus, balancing initial material costs with overall lifecycle expenses is critical in achieving a successful design.
Weight
Weight is another important aspect. Depending on the application, a heavy heat sink may not be feasible—think of laptop designs versus desktop units. Lightweight materials like aluminum allow for effective thermal management without weighing down portable devices. This is a significant consideration for mobile technology, where every gram counts. However, while lighter materials are beneficial in many ways, they often necessitate more careful engineering to ensure they still handle heat effectively under varying conditions.
The challenge lies in finding a material that strikes an optimal balance between weight, thermal performance, and budget.
Fin Configuration and Geometry
The design of fins, including their type and orientation, plays an instrumental role in heat dissipation. Proper fin configuration can greatly enhance a heat sink’s efficiency by allowing for greater airflow and increased surface area, enabling heat to escape quicker and more effectively.
Type and Orientation
The type and orientation of fins matter when crafting an effective heat sink. Certain shapes, such as pin fins, provide more surface area, allowing for improved thermal performance compared to flat or extruded fins. In addition, the orientation of these fins can either promote or diminish airflow capabilities. For example, vertical fins work well in natural convection scenarios, while horizontal may be better in forced air systems.
An interesting feature of well-designed fin configurations is their adaptability for various applications. Electric cars and computers have different cooling needs, yet a flexible fin design can cater to both.
Spacing and Thickness
The spacing and thickness of fins must also be strategically assessed. A typical trade-off is between thick fins, which can absorb heat better, and thinner fins, which offer greater overall surface area but may not conduct heat as effectively. Proper spacing between fins is essential to maintain airflow while avoiding turbulence that can hamper performance. Too close, and air won't circulate; too far apart, and you’re wasting valuable surface area.
The right balance must be struck based on the intended application and environmental conditions.
Achieving an effective heat sink design requires meticulous attention to the interplay among surface area, materials, fin configuration, and geometry. Improper balance can yield poor thermal performance, resulting in overheating and shortening the lifespan of electronic components.
Overall, understanding these criteria creates a foundation for successful heat sink designs, leading to greater efficiency and product reliability.
Materials Used in Heat Sink Manufacturing
Choosing the right materials for heat sink manufacturing is a fundamental aspect that greatly influences thermal performance and overall effectiveness. The right materials not only dictate the efficiency of heat transfer but also impact the weight, cost, and durability of the final product. For engineers and designers, understanding the benefits and considerations related to various materials is crucial for effective thermal management in diverse applications.
Aluminum vs. Copper
When it comes to materials, aluminum and copper are the two heavyweights of the heat sink industry. Aluminum has emerged as a popular choice for many reasons. It is lightweight, corrosion-resistant, and relatively inexpensive compared to copper. With thermal conductivity around 205 W/mK, aluminum offers an efficient pathway for heat dissipation. It is easy to fabricate into intricate designs, making it a go-to for many applications, especially where weight is a factor.
Copper, on the other hand, boasts higher thermal conductivity—approx. 385 W/mK—making it exceptionally efficient at conducting heat. This property allows for effective thermal management in high-performance settings like processors and power amplifiers. However, the downside to copper is that it comes with a heftier price tag and is considerably heavier than aluminum, which can be a disadvantage in applications where weight is a critical factor.
In many scenarios, a combination of the two materials may be used to take advantage of their respective strengths. For instance, a heat sink could utilize a copper base for its superior thermal conductivity, while aluminum fins could be employed to reduce overall weight and material costs. This kind of hybrid design maximizes efficiency without compromising on durability and manufacturing ease.
Advanced Materials: Carbon Nanotubes and Graphene
New materials are constantly emerging that could very well revolutionize heat sink design. Carbon nanotubes, with their remarkable thermal conductivity—reportedly around 4000 W/mK—hold great promise. Their unique structure allows them to conduct heat more efficiently than both aluminum and copper, making them an exciting area for future research and development. Given their lightweight and high tensile strength, carbon nanotubes can also considerably reduce the overall size and mass of heat sinks, which is a significant advantage in compact electronics.
Similarly, graphene, another frontier material, exhibits extraordinary thermal properties along with high mechanical strength. While its commercial applications are still in infancy, the potential for graphene in heat sink manufacturing is impressive. Like carbon nanotubes, graphene has a very high conductivity and can be engineered into various forms to meet specific design requirements.
However, the integration of these advanced materials into mainstream manufacturing poses challenges. The scalability of production and the costs associated with these materials are still under scrutiny. Nonetheless, as technology continues to evolve, one may expect these materials to find their place in high-performance heat sinks in the near future.
"The advancement of materials science is paving new paths that could redefine efficiency in thermal management."
In summary, the choice of material plays a pivotal role in the performance of heat sinks. Understanding the strengths and weaknesses of aluminum and copper, alongside rising stars like carbon nanotubes and graphene, allows manufacturers and designers to tailor their heat sink solutions according to specific operational requirements. This insight is valuable not only for maximizing thermal efficiency but also for maintaining a balance between cost, weight, and manufacturability.
Design Techniques for Optimal Performance
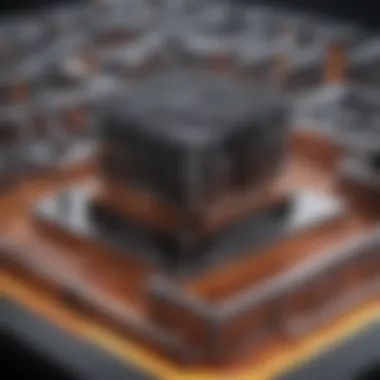
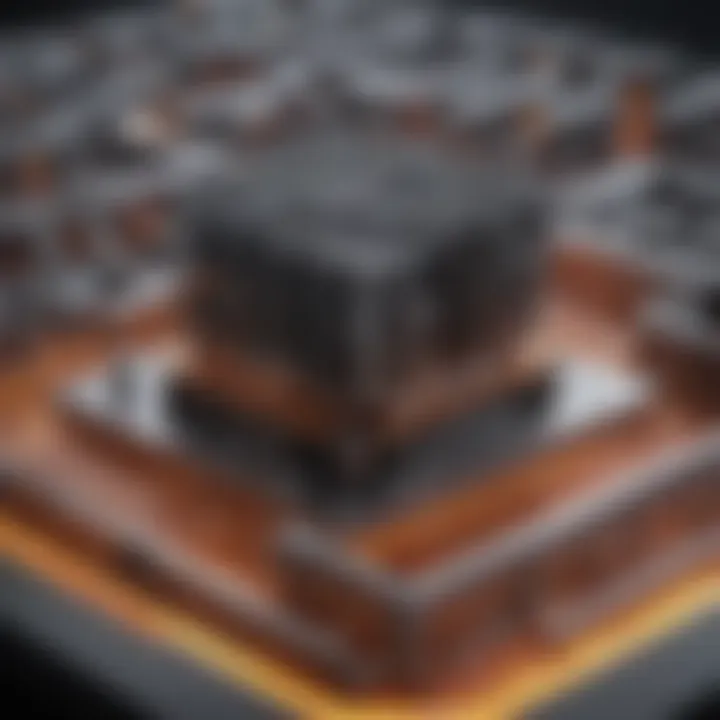
When it comes to heat sink design, the techniques employed to optimize performance play a pivotal role in ensuring that thermal efficiency is maximized. The significance of utilizing advanced design techniques cannot be overstated; they allow engineers and designers to effectively cool critical components while balancing other factors such as size, weight, and cost. These techniques involve sophisticated modeling, simulation, and practical testing, all of which contribute to achieving superior thermal management.
Computational Fluid Dynamics (CFD) in Design
Computational Fluid Dynamics, or CFD, has swiftly become a cornerstone in the design process of heat sinks. This tool enables engineers to simulate the fluid flow and heat transfer processes that occur within a thermal system, providing invaluable insights that would be difficult to grasp through traditional methods. By visualizing airflow patterns and thermal distributions, designers can identify and rectify potential hotspots and inefficiencies prior to building physical prototypes.
The primary advantages of integrating CFD in the design phase include:
- Enhanced Accuracy: CFD offers precise predictions about thermal performance, which translates into more effective cooling designs.
- Design Flexibility: Engineers can easily modify parameters such as fin shape or spacing to evaluate their effects on thermal performance without incurring additional costs.
- Time and Cost Efficiency: By reducing the reliance on trial-and-error, CFD contributes to shorter development cycles and lesser resource waste.
One should consider that the accuracy of CFD simulations hinges on the quality of input parameters. Factors like material properties, surface roughness, and environmental conditions must be meticulously defined to avoid misleading results. This highlights the importance of a thorough understanding of thermal dynamics and fluid mechanics for the engineers involved.
Prototyping and Experimental Validation
While computational modeling lays the groundwork, real-world experimentation is essential to validate design predictions and ensure their practical applicability. Prototyping allows engineers to gather empirical data about thermal performance, and this information is critical for refining and optimizing designs.
Experiments can take various forms, but typically involve creating a physical model of the heat sink as per the design specifications derived from CFD analysis. Once fabricated, the prototype undergoes testing under controlled conditions to assess its thermal characteristics. Key elements to focus on during this phase include:
- Measurement of Thermal Resistance: Determining how effectively the heat sink transfers heat away from its source is fundamental for assessing its performance.
- Temperature Distribution: Monitoring temperature gradients across the heat sink helps identify potential thermal bottlenecks.
- Durability Testing: It’s crucial to ensure that the heat sink can withstand the operational stresses it will face over its lifetime.
"Empirical data from prototyping provides a clear picture of performance gaps that simulations might miss, leading to truly optimized designs."
Eventually, feedback from experimental validation not only fine-tunes the current design but also informs future projects. This iterative approach—where design and testing inform one another—culminates in more reliable, efficient heat sinks that directly address the challenges posed by modern electronics, automotive applications, and beyond.
Thermal Performance Metrics
Understanding thermal performance metrics is crucial when evaluating heat sink designs. These metrics provide insight into how effectively a heat sink can manage and dissipate heat generated by electronic components. By focusing on quantitative measurements rather than subjective evaluations, we can gauge whether a design adheres to its thermal management objectives.
Benchmarking Effectiveness
Temperature Drop
Temperature drop is a significant metric in assessing a heat sink's performance. This value indicates how much the heat sink can reduce the temperature of a component, relative to its designated operating environment. A more considerable drop signifies better cooling efficiency, which is essential in preventing overheating and prolonging component life.
Key characteristics of temperature drop include:
- Comparison Basis: It provides a clear standard against which heat sinks can be compared, essential for selecting the right design.
- Simplicity: It’s straightforward to measure and understand, making it accessible for engineers and technicians monitoring system performance.
When looking deeper, one unique feature of temperature drop is its ability to highlight inefficiencies in thermal design. High temperature drops can be indicative not only of effective heat sinks but also prompt a closer examination of component placement within a system.
However, it's important to consider some disadvantages as well. Sometimes, a large temperature drop might necessitate larger or bulkier heat sinks that can be challenging to fit into compact systems. Thus, understanding this metric is pivotal for achieving the right balance between space constraints and cooling needs.
Power Dissipation
Power dissipation, in essence, refers to the amount of heat energy that a heat sink can successfully remove from a component before it reaches a critical temperature point. This metric directly correlates with a system’s ability to maintain optimal operating conditions, making it a focal point in heat sink design discussions.
The key characteristic of power dissipation lies in its relevance to the maximum allowable temperature of the components being cooled. When the dissipation rate aligns with the thermal load generated by the components, optimal performance is achieved.
A notable unique feature of power dissipation is its integration with system performance. Systems that push the limits in performance often produce higher thermal loads. Thus, assessing heat sinks under various power dissipation scenarios is integral for practical applications, especially in high-performance computing or automotive industries.
Nevertheless, there are considerations to keep in mind. For instance, measuring power dissipation can sometimes be influenced by external environmental factors, such as airflow or ambient temperature. Engineers must take this into account to avoid misleading results and thereby ensure reliable thermal management solutions.
Measuring Temperature Distribution
Measuring temperature distribution across a heat sink can reveal critical information about its effectiveness. It shows whether the heat is being evenly dissipated or if there are any hotspots that could indicate poor design. Overall, captured temperature data can guide improvements in future designs or operational adjustments to achieve better thermal management.
Real-World Applications of Heat Sink Designs
Heat sinks find their footing in an array of industries, transforming how devices manage heat. The practical implications of heat sinks stretch beyond theory snuggled in textbooks. Heat sinks are vital in real-world applications, marrying efficiency with longevity. In a landscape where thermal management grows increasingly crucial, understanding the relevance of heat sink designs becomes paramount.
Heat sinks serve the essential function of dissipating heat generated by electronic components. This is not just a matter of operational efficiency but also a matter of reliability and safety. A well-designed heat sink can mean the difference between a device that performs optimally and one that falters under pressure. Let’s dive deeper into specific sectors where heat sinks play a transformative role.
Electronics Cooling Solutions
In the realm of electronics, heat sinks are indispensable. Devices, such as computers and smartphones, generate substantial heat during operation. Without efficient thermal management, performance diminishes, and the risk of component failures soars.
Heat sinks come in various configurations, often made from materials like aluminum or copper for effective heat conduction. They are designed to maximize surface area, promoting airflow and thereby enhancing heat dissipation. Consider gaming laptops, which require cooling solutions that can handle intense workloads. Here, innovative heat sink designs ensure that components remain cool even under significant stress.
- Common Applications:
- CPUs and GPUs
- Power amplifiers
- LED lighting
The importance of good cooling cannot be overstated. A study shows that optimal cooling leads to a more stable system and can extend the lifespan of devices significantly.
Automotive Industry Insights
In automotive engineering, heat sinks have carved a niche, ensuring the reliability of critical systems. With vehicles becoming more electrified, the generation of waste heat has intensified. Here, the role of heat sinks in battery management systems takes center stage.
As electric vehicles (EVs) zoom into the mainstream, their thermal management strategy must evolve. Efficient heat sinks are crucial in managing battery temperatures, improving charging efficiency, and enhancing overall vehicle performance.
An electric vehicle's performance can drop sharply if battery temperatures soar. Thus, the automotive industry invests heavily in advanced thermal management solutions, including incorporating liquid cooling alongside traditional heat sink designs.
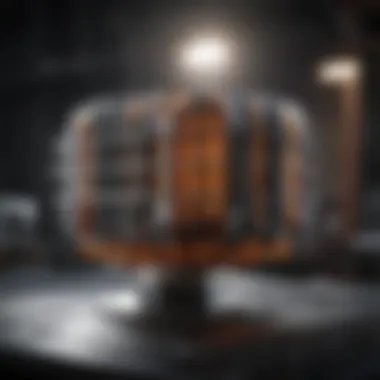
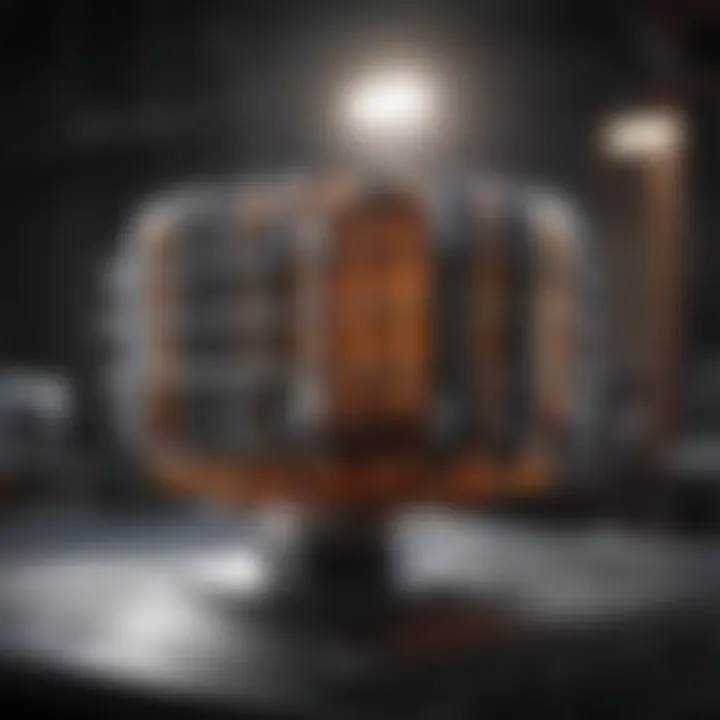
- Key Considerations:
- Corrosion resistance
- Weight efficiency
- Durability under harsh conditions
Aerospace and Defense Applications
In the high-stakes world of aerospace and defense, the reliability of systems is paramount. Heat sinks in this sector need to withstand extreme temperatures and environmental conditions. The integration of sophisticated designs is crucial here, as they must cope with the rigors of space travel or military operations.
For satellites and aircraft, electronic systems and sensors often operate in isolated areas where heat build-up can become critical. Advanced materials such as carbon nanotubes are making waves in this space, offering exceptional thermal conductivity while minimizing weight.
- Challenges Faced:
- Thermal cycling and fatigue
- Weight constraints
- Material endurance in extreme operations
In summary, heat sinks are not mere metallic pieces squeezed into designs but rather integral components that influence device performance across industries. By understanding their real-world applications, stakeholders can better appreciate their role in furthering tech advancements in electronics, automotive, aerospace, and defense.
Challenges in Heat Sink Optimization
In the world of heat sink design, optimization is crucial. It ensures not only the efficient dissipation of heat but also the longevity and performance of electronic components. Addressing challenges associated with this optimization can significantly impact product robustness and reliability. As technology advances, heat sinks must adapt to evolving requirements, making it essential to examine specific elements such as miniaturization, weight versus performance, and environmental considerations.
Impact of Miniaturization
Miniaturization is a double-edged sword. On one side, the push for smaller devices—especially in electronics—has led to significant innovations. Yet, the reduction in size poses substantial challenges for heat sink design.
Smaller devices generate considerable heat in a confined space, thereby increasing thermal density. Consequently, an efficient heat sink must maintain effective thermal management without occupying too much space. A common approach is to integrate advanced materials that provide higher thermal conductivity in less volume.
Moreover, sophisticated technologies such as microchannel heat sinks leverage miniature channels to enhance cooling efficiency in a limited area. These channels facilitate enhanced fluid flow, improving heat transfer rates. However, designing these intricate channels requires precise manufacturing capabilities, which can drive up costs.
Balancing Weight and Performance
When it comes to heat sink optimization, striking the right balance between weight and performance is no easy feat. In many applications, especially in automotive and aerospace fields, weight is a critical parameter. A lighter heat sink can lead to significant overall weight reduction in the final product, facilitating increased energy efficiency.
However, performance should never be sacrificed for the sake of weight. Engineers often explore various materials to achieve this delicate balance. For example, aluminum might be preferred for its lightweight properties. Still, the effective thermal performance can sometimes necessitate a trade-off that professionals must navigate carefully.
Ultimately, the challenge lies in crafting designs that optimize both weight and thermal performance without compromising either aspect. Prototypes may go through several iterations to find that fine line where thermal efficiency meets weight concerns effectively.
Environmental Considerations in Design
The pressing issue of climate change implies that environmental considerations cannot be pushed aside during heat sink design. Sustainability in materials and manufacturing processes is becoming increasingly important. Choosing materials that are not only effective but also recyclable or sustainable significantly enhances a product’s appeal.
Furthermore, designs must comply with regulations to minimize environmental impact. For instance, it may be essential to avoid certain materials known to harm the environment during production or disposal. An effective heat sink may also need to address energy use during operation, ensuring that it does not contribute excessively to carbon emissions.
Future Trends in Heat Sink Design
As technology continues to evolve at a dizzying pace, so does the need for enhanced thermal management solutions. The journey toward efficient heat sink design doesn't stop at traditional methods and materials; rather, it constantly welcomes innovative trends that push the boundaries of what's possible. This section highlights the pertinent trends reshaping the heat sink landscape and their implications for industry practice.
Integration with Advanced Cooling Techniques
In the realm of heat sinks, integrating advanced cooling techniques represents a game-changing approach. Traditional cooling, while effective, often encounters limitations regarding efficiency and adaptability. As devices shrink, the need for effective cooling becomes crucial. Advanced techniques such as phase change materials (PCMs) and active cooling systems are taking center stage.
- Phase Change Materials: These materials absorb and release heat during phase transitions. By leveraging their properties, heat sinks can maintain a stable temperature even under heavy loads.
- Active Cooling Systems: Employing thermoelectric coolers (TECs) or refrigeration techniques allows for direct temperature management. This combination can yield significant temperature drops, optimizing device performance considerably.
The interplay between these advanced techniques and traditional heat sink design is significant. By combining passive and active methods, one can minimize thermal resistance while maximizing heat dissipation, leading to more reliable and efficient systems.
Emerging Nanotechnology Solutions
Nanotechnology is reshaping several fields, and heat sink design is no exception. The integration of nanomaterials brings forth enhanced thermal conductivity and improved structural integrity. Materials such as graphene and carbon nanotubes are at the forefront, granting engineers access to solutions that were previously considered unfeasible.
- Graphene: Renowned for its exceptional thermal conductivity, graphene can be implemented to create ultra-thin heat sinks without compromising performance. This can lead to lighter and more efficient cooling solutions.
- Carbon Nanotubes: These structures offer excellent thermal properties and can be incorporated into composite materials for heat sinks. Their lightweight nature means they can provide significant thermal management without adding undue strain to the overall system.
The reach of nanotechnology in heat sink design is profound. Not only does it enhance efficiency, but it also allows for the creation of components tailored to specific applications, such as those found in aerospace or high-performance electronics.
"The advent of nanotechnology in heat sink design opens pathways for advancements we once only dreamed about, making thermal efficiency a reality rather than a distant goal."
In closing, understanding these future trends is pivotal for students, researchers, and industry professionals alike. By keeping an eye on innovations like advanced cooling techniques and emerging nanotechnology solutions, the path to optimized thermal efficiency seems clearer, paving the way for smarter, more efficient designs in heat sink technology.
Epilogue and Further Research
In wrapping up our exploration of heat sink design, it's crucial to acknowledge the immense role thermal management plays across diverse sectors. As technology continues to advance, the need for efficient cooling systems becomes ever more pressing. This significance extends beyond merely keeping devices operational; it can directly influence performance, longevity, and overall success in any application. The knowledge acquired through this article serves as a springboard for further inquiry, pushing practitioners and researchers to delve deeper into innovative solutions.
The realm of heat sink design isn't static. Each leap in materials science or thermal physics opens new doors to maximizing thermal efficiency. Continuing education, whether through formal avenues or self-driven research, can uncover techniques that aren't widely heralded yet. For instance, the integration of nanomaterials could revolutionize traditional designs, offering both weight reduction and enhanced performance. Staying abreast of such developments can provide a competitive advantage in fast-paced industries.
In summary, ongoing research in heat sinks holds great promise, not just for academic curiosity but for practical applications in our everyday world. As we confront new thermal challenges brought on by smaller, faster, and more powerful devices, a deep understanding of the principles discussed can guide the evolution of heat sink technology into the future.
Summary of Key Insights
The deep dive into heat sink design highlights several crucial insights that are pivotal to maximizing thermal efficiency:
- Thermal Management Significance: Effective thermal management is not an afterthought; it's foundational in ensuring optimal functioning of electronic and mechanical systems.
- Performance Metrics: Understanding metrics such as temperature drop and power dissipation can provide tangible benchmarks for evaluating designs.
- Material Innovations: The shift towards advanced materials like graphene and carbon nanotubes showcases the potential for breakthrough designs that surpass traditional limitations.
- Design Techniques: Employing advanced computational methods such as CFD can lead to smarter and more innovative designs, ensuring greater efficiency.
These insights pave the way for exciting advancements, reinforcing the need for continued exploration and experimentation.
Recommendations for Practitioners
For those actively engaged in heat sink design and related fields, the following recommendations can assist in navigating the complexities of thermal efficiency:
- Embrace Continuous Learning: Keep up with the latest research developments in material science and thermal dynamics. Attend workshops and read the latest journals to remain informed.
- Experiment with Prototyping: Don’t shy away from rapid prototyping. The sooner you can validate concepts through real-world testing, the better.
- Prioritize Sustainability: As environmental concerns grow, choose materials and processes that are eco-friendly. It not only reduces your footprint but can also attract clients looking for sustainable solutions.
- Collaborate Across Disciplines: Engage with professionals from different fields, such as materials engineering or software development. Multidisciplinary approaches often lead to innovative solutions.
- Document Findings: Maintain thorough records of your designs and experiments. Sharing findings through platforms such as Reddit or academic social media may spark insightful discussions or further collaborations.
Ultimately, the path toward improving heat sink design is paved with knowledge, curiosity, and collaboration.