A Comprehensive Overview of Aseptic Packaging Machines
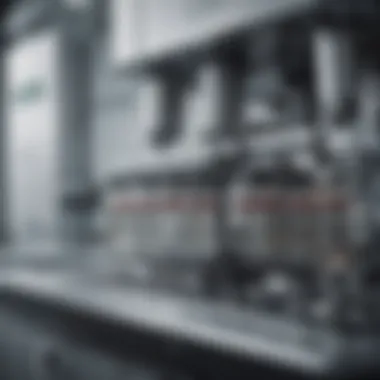
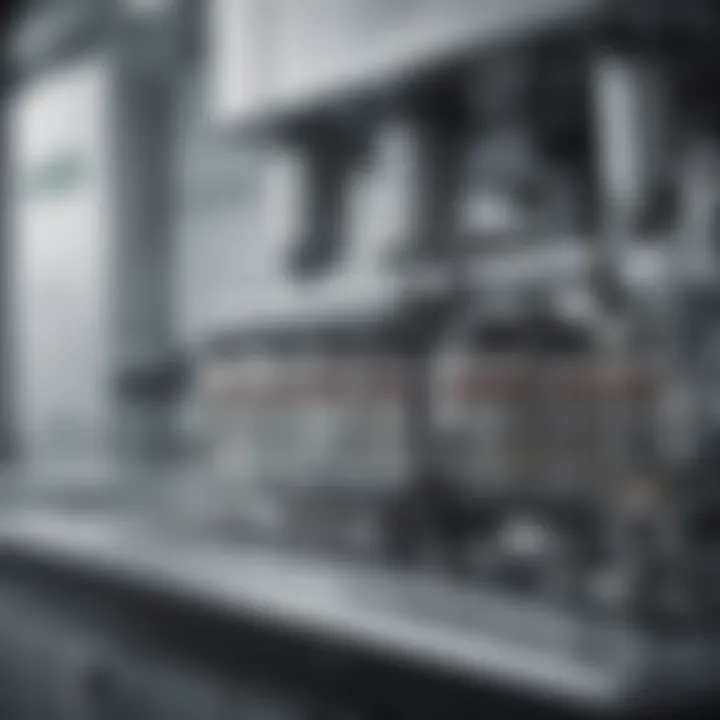
Intro
Aseptic packaging machines represent a crucial component in the modern food and pharmaceutical industries. These systems ensure that products are preserved without compromising their quality or safety. The need for such technology has grown in parallel with the demand for longer shelf life and safe consumption. This article explores the significance, design, and current innovations in aseptic packaging machines, providing a comprehensive guide for students, researchers, and professionals in the field.
Research Context
Background and Rationale
The historical development of aseptic packaging dates back to the early twentieth century when the need to preserve food effectively became apparent. The rise in consumer demand for convenience foods, along with a growing awareness of food safety, has led to advancements in packaging technologies. Aseptic packaging machines play a pivotal role in this evolution. They enable products to be sterilized and packaged in a controlled environment, thus minimizing the risk of contamination.
Literature Review
Aseptic packaging has been studied extensively in various contexts. Key research often focuses on sterilization methods, types of packaging materials, and their effects on product shelf life. Recent literature highlights innovations in machine design and performance, emphasizing their influence on both efficiency and safety. For example, studies have shown that advancements in microcontroller technology have improved the precision and reliability of these machines.
A notable source is the paper titled "Aseptic Packaging: Technology, Applications, and Issues" published in the Journal of Food Engineering. It delves into the fundamental principles of aseptic processing and packaging, offering valuable insights into the future direction of the industry.
Aseptic packaging systems are essential for maintaining product integrity in an increasingly competitive market.
Methodology
Research Design
This article adopts a comprehensive research design approach. It combines qualitative analysis of existing literature with insights gathered from industry reports and expert interviews. This dual methodology allows for a more nuanced understanding of the industry trends and challenges.
Data Collection Methods
Data was collected through various means, including:
- Reviewing academic articles and journals focused on packaging technology.
- Consulting industry reports from organizations such as the Packaging Machinery Manufacturers Institute.
- Conducting interviews with specialists in food safety and packaging technology.
The synthesis of these data sources reveals the complexity of aseptic packaging machinery and its application across different sectors, particularly as health standards and consumer expectations continue to evolve.
This comprehensive overview sheds light on the operational principles and types of machines available today, enriching our understanding for future considerations in the field.
Prolusion to Aseptic Packaging
Aseptic packaging is fundamental to ensuring the safety and longevity of food and pharmaceutical products. As consumers become more health-conscious, the demand for high-quality products increases. This underscores the significance of understanding aseptic packaging machines, which play a critical role in maintaining product integrity.
Definition of Aseptic Packaging
Aseptic packaging refers to a technique where products are sterilized and then packaged in a sterile environment. The process typically includes the sterilization of both the product and the packaging materials before the two meet. As a result, aseptic packaging minimizes the risk of contamination and preserves the quality of the contents. This method is particularly relevant for products sensitive to spoilage, such as dairy, juices, and perishable pharmaceuticals.
Importance in Food and Pharmaceuticals
The importance of aseptic packaging cannot be overstated, especially in our modern, health-focused society. Here are several key reasons:
- Preservation of Quality: Aseptic packaging helps maintain the flavor, color, and nutritional value of food and drugs. It allows products to be stored without refrigeration for extended periods.
- Safety Standards: In the pharmaceutical sector, maintaining sterility is paramount. Aseptic packaging adheres to stringent health regulations, ensuring that products are safe for consumption and free from pathogens.
- Economic Efficiency: For producers, aseptic packaging can reduce the reliance on preservatives and refrigeration, thereby lowering operation costs. This method helps in creating more cost-effective and environmentally-friendly packaging solutions.
"Aseptic packaging is a critical innovation that bridges quality with safety, ensuring that consumers receive safe and high-quality products."
Understanding aseptic packaging is essential for students, researchers, and professionals working in fields related to food science and pharmaceuticals. The next sections will explore the historical development, operational principles, and future trends, deepening our comprehension of this vital technology.
Historical Development of Aseptic Packaging
The historical development of aseptic packaging is foundational to understanding current practices and innovations in the industry. This journey began long before modern machines emerged, evolving through experimentation and technological advances. The significance of this narrative lies in how early innovations paved the way for the sophisticated systems we rely on today. Aseptic packaging is critical in maintaining the shelf life and safety of products in both food and pharmaceuticals. Its evolution reflects changing consumer demands and advancements in hygiene standards.
Early Innovations
The history of aseptic packaging can be traced back to the late 19th century. In 1861, French chemist Louis Pasteur designed a method to extend the shelf life of perishable products. His research on pasteurization laid a crucial foundation for later developments in food preservation. By heating products to kill bacteria, this process became an early stepping stone toward the aseptic technologies we see today.
By the early 20th century, technological advancements continued to emerge. In the 1920s, the introduction of glass bottles for milk pasteurization allowed manufacturers to better protect liquid dairy. This innovation not only included pasteurization but also enhanced the understanding of sterilization techniques, which are essential in today's aseptic packaging processes. The period marked the initial acknowledgment of sterilization as a cornerstone for preserving product quality.
Milestones in Technology
As the decades rolled on, several technological milestones transformed aseptic packaging. One significant development occurred in the 1960s with the introduction of Thermoforming technology. This allowed manufacturers to create a variety of packaging shapes and sizes while ensuring a sterile environment. Coupled with the advancement of plastic materials, the packaging landscape shifted towards lightweight and efficient solutions.
In the 1980s, the emergence of Blow-Fill-Seal (BFS) technology revolutionized the industry. This innovation offered a more comprehensive sterilization approach, combining the production of containers and product filling in one continuous process. BFS machines became popular for liquid products, particularly in the pharmaceutical sector, due to their thorough aseptic conditions.
"The advancements in aseptic packaging technology have enabled significant reductions in spoilage and waste, reshaping our approach to food safety and product longevity."
As we entered the 21st century, further innovations like Form-Fill-Seal (FFS) technology and increased automation began to dominate the market. These technologies presented not only advantages in efficiency and cost-effectiveness but also enhanced the overall integrity of the packaging process. Automation in packaging has allowed for consistent quality control, minimizing human error and contamination risks.
Types of Aseptic Packaging Machines
In the field of aseptic packaging, various machines play a crucial role in maintaining product integrity, enhancing shelf life, and ensuring compliance with health standards. Understanding the types of aseptic packaging machines is fundamental for professionals in the food and pharmaceutical industries. Each type not only serves a unique function but also contributes to efficiency and safety in packaging processes. Key considerations include the operational principles, production capacities, and the specific benefits each machine brings to production lines.
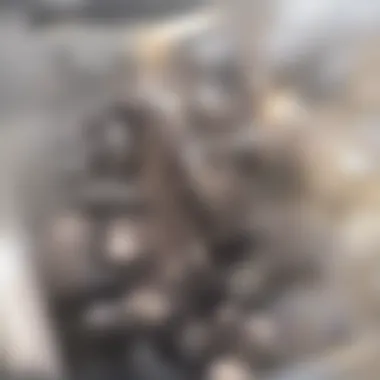
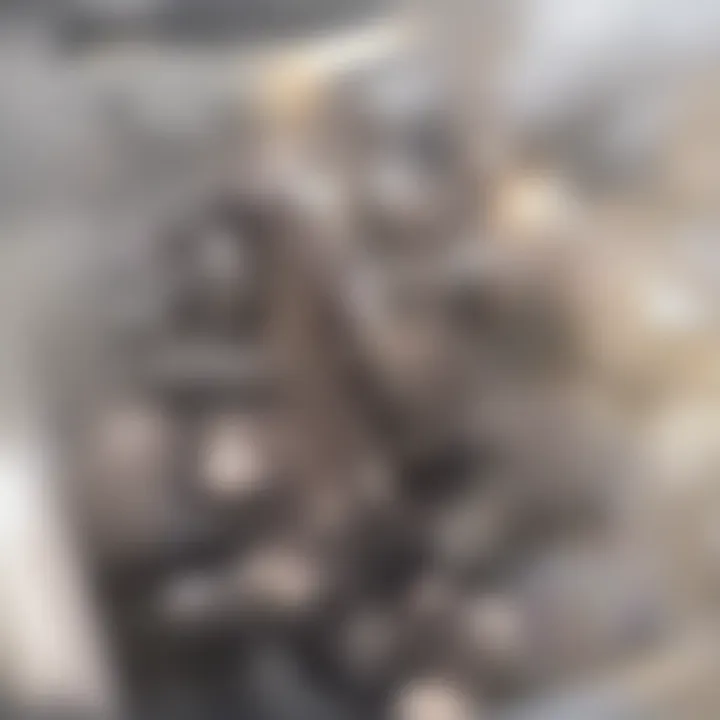
Blow-Fill-Seal (BFS) Machines
Blow-Fill-Seal machines represent a significant advancement in aseptic packaging. They integrate three essential functions: blowing the bottle, filling it with product, and sealing itβall within a sterile environment. BFS machines utilize polymers to create containers on-site, which minimizes contamination risks.
Benefits of BFS Machines:
- Higher Sterility Assurance: The entire process occurs in a closed, sterile setting, reducing exposure to environmental pathogens.
- Cost Efficiency: These machines do not require separate bottle preparation, saving both time and resources.
- Versatility: BFS technology accommodates various products, including liquids, gels, and creams, making them suitable for pharmaceuticals and food products alike.
Form-Fill-Seal (FFS) Machines
Form-Fill-Seal machines are another critical type within the aseptic packaging landscape. They operate by forming a package from a flat roll of flexible material, filling it with the product, and sealing it in one continuous operation. This method is particularly efficient and customizable.
Key Attributes of FFS Machines:
- Reduced Material Waste: By forming the package on-site, these machines minimize leftover material.
- Rapid Production Rates: FFS machines can achieve high speeds, making them ideal for high-demand environments.
- Adaptability: They can easily handle various formats, such as pouches, bags, and containers, catering to diverse market needs.
Carton Filling Machines
Carton filling machines are designed specifically for packaging liquid products into cartons. These machines emphasize efficiency and reliability, ensuring that products remain uncontaminated during the filling process. The method often involves pre-formed cartons that are typically sealed with folding mechanisms post-filling.
Advantages of Carton Filling Machines:
- Enhanced Product Protection: Cartons provide excellent barrier properties, safeguarding contents against exposure to light and oxygen.
- Sustainability: Many carton filling machines use recyclable materials, aligning with current sustainability goals in packaging.
- Branding Opportunities: Cartons provide a larger surface area for branding and product information, aiding marketing efforts.
Each type of aseptic packaging machine contributes uniquely to the quality and safety of packaged products. As these technologies evolve, they will continue to meet the challenges of the food and pharmaceutical industries effectively.
Operational Principles of Aseptic Packaging Machines
Understanding the operational principles of aseptic packaging machines is crucial for grasping how these systems maintain product integrity and safety. These machines employ a sequence of sterile procedures before product packaging, assuring minimal risk of contamination. The principles are based on three primary components: sterilization techniques, filling processes, and sealing methods. Each component plays a significant role in protecting the quality of food and pharmaceuticals throughout their shelf life.
Sterilization Techniques
Sterilization is a fundamental step in aseptic packaging, as it eliminates microorganisms that could spoil the product. There are various methods of sterilization commonly used in the industry:
- Heat Sterilization: This consits of applying high temperatures to kill pathogens effectively. Hot water or steam might be used in this approach. It is typically employed for liquid products.
- Chemical Sterilization: In this method, chemical agents like hydrogen peroxide or peracetic acid are used. These agents are effective against a wide range of microorganisms and do not leave harmful residues if managed properly.
- Radiation Sterilization: Gamma or electron beam radiation can also be used for sterilization purposes. This method penetrates packages and sterilizes contents without the heat, which is advantageous for heat-sensitive materials.
Each technique has its advantages and limitations. Choosing a method depends on factors like the product type, desired shelf life, and regulatory standards.
Filling Process
The filling process involves transferring the sterilized product into pre-sterilized containers or packages. This must be done in a sterile environment to avoid any contamination. Many machines utilize a combination of vacuum and pressure methods to facilitate this process
- Vacuum Filling: This technique creates a vacuum in the container to draw in the product. It ensures an effective seal while preventing air from entering.
- Pressure Filling: This involves using pressure to force the product into the container. It is commonly used for thicker products, such as sauces or creams.
Moreover, automation within filling systems allows for increased speed and precision. This is essential for large-scale production, helping meet market demand without sacrificing quality.
Sealing Methods
The sealing method is the last line of defense in maintaining the sterility of a package. A secure seal prevents the ingress of microorganisms and protects the freshness of the product. Various sealing methods include:
- Heat Sealing: These machines melt and bond the packaging material edges, forming a tight seal. It is widely used with thermoplastic materials.
- Ultrasonic Sealing: Through high-frequency vibrations, this method joins materials at their interface, creating a seal that is often stronger than heat sealing.
- Cold Sealing: This method relies on specialized adhesives that activate under pressure without the use of heat.
Each sealing method ensures product integrity. Selecting the appropriate sealing technique depends on the packaging material and product requirement. Effective sealing is vital to maintaining the extended shelf life and quality of aseptically packed goods.
"The operational principles behind aseptic packaging are akin to an intricate ballet, where each movement is crucial to maintaining the purity and safety of food and pharmaceutical products."
Overall, understanding these operational principles enhances knowledge of how aseptic packaging machines safeguard products against contamination, ensuring safety and quality in consumption.
Advantages of Aseptic Packaging
Aseptic packaging holds a critical position in both the food and pharmaceutical industries. Its advantages extend beyond simple preservation. This section identifies the key benefits that contribute to its significance, including extended shelf life, reduced need for preservatives, and cost efficiency. Understanding these aspects will highlight why aseptic packaging is an important technology worth consideration.
Extended Shelf Life
One of the most prominent benefits of aseptic packaging is its ability to significantly extend the shelf life of products. Manufacturers employ various sterilization techniques to eliminate microorganisms before the product is sealed. This process allows products to remain stable without refrigeration. For example, products like milk and fruit juices can last for months, which reduces spoilage and waste.
A longer shelf life also enhances distribution possibilities. Producers can transport products to distant markets without concern for rapid expiration. This aspect contributes to a larger market reach and higher sales potential.
"Extended shelf life not only improves inventory management but also enhances consumer access to fresh and safe products, making it a key advantage of aseptic packaging."
Reduced Need for Preservatives
Another significant advantage is the reduced need for chemical preservatives. Since aseptic packaging is designed to keep products sterile, the reliance on additives becomes less important. Consumers are becoming more aware of ingredients in their food and choose products with fewer chemicals. Aseptic packaging allows companies to meet these preferences effectively.
For instance, in the dairy industry, products can be kept fresh longer without relying heavily on artificial preservatives. This not only benefits consumer health but also strengthens brand reputation. As the market shifts towards cleaner label products, the lack of preservatives becomes a selling point.
Cost Efficiency
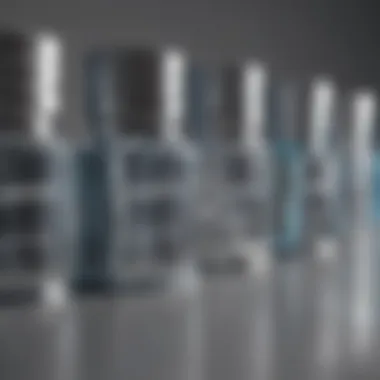
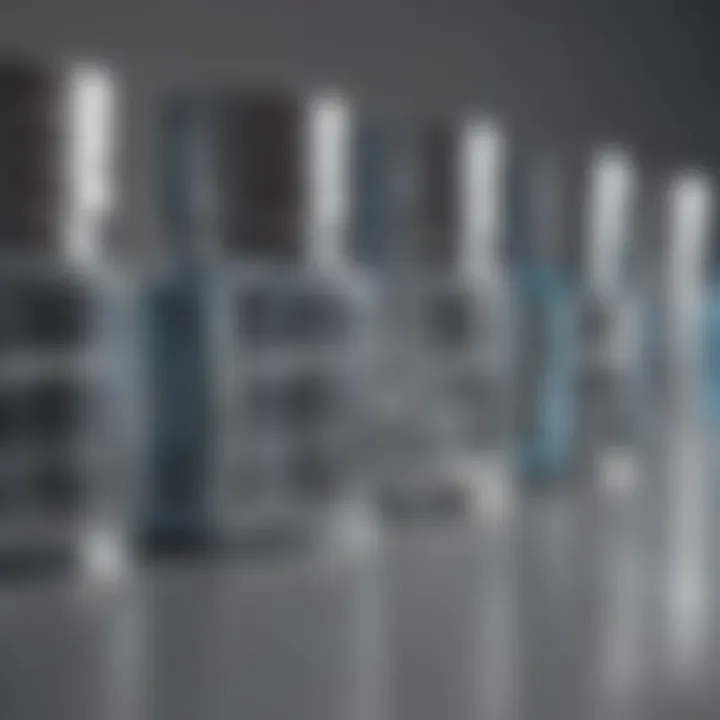
Lastly, aseptic packaging offers cost efficiency through reduced waste and spoilage. While the initial investment in aseptic machinery may be high, the long-term savings associated with extended shelf life and low spoilage rates can offset these costs. Furthermore, companies can improve their profit margins as less product loss translates to higher revenues.
In operations, optimized packaging processes can reduce labor costs as well. Automated systems minimize the need for manual intervention, thereby increasing throughput and reducing the chances of human error.
Challenges in Aseptic Packaging
Aseptic packaging machines play a vital role in preserving the quality and safety of products in the food and pharmaceuticals sectors. However, the implementation of such systems is not without its challenges. This section aims to explore the important aspects relating to the challenges faced during the adoption and operation of aseptic packaging machinery. Understanding these hurdles is crucial for stakeholders who seek to optimize production systems and ensure regulatory compliance.
Initial Investment Costs
One of the primary challenges in aseptic packaging is the initial investment cost. This investment includes not only the price of the machinery itself but also the infrastructure needed to accommodate it. Aseptic packaging machines are sophisticated pieces of equipment that often require high levels of precision, leading to elevated costs. Moreover, facilities may need to be modified or built anew to ensure sterility and compliance with regulatory standards.
Financial considerations can be daunting for small to medium enterprises. They may lack the capital to invest in aseptic packaging technology, which hinders their ability to compete in the market. In contrast, large corporations often can absorb these costs more easily. Different financing options, such as leasing or financing, can alleviate some financial burden, but businesses must still weigh the long-term benefits against upfront costs.
Operational Complexity
Another significant hurdle in aseptic packaging is the operational complexity involved. The machinery requires trained personnel to operate correctly. Operators must understand the sterilization processes, the filling techniques, and the sealing methods to maintain product integrity. This training can be time-consuming and costly.
Additionally, the machines often integrate multiple functions, which can make the workflow complicated. Any failure in the sterilization process can compromise the entire batch, leading to wastage and potential safety issues. Moreover, the systems must consistently adhere to strict hygiene and quality control protocols, which can strain resources as personnel must monitor and ensure compliance at all stages of production.
Effective training and operational oversight are critical for minimizing risks associated with aseptic packaging.
In summary, while aseptic packaging machines offer numerous advantages in extending shelf life and ensuring food safety, they come with challenges. The initial investment costs and operational complexity require careful planning and strategic management. By addressing these challenges, companies can leverage the full potential of aseptic packaging technology.
Market Dynamics of Aseptic Packaging
The market dynamics of aseptic packaging reflect a critical interface between technology, consumer trends, and regulatory influences. Understanding these dynamics is essential for stakeholders in the food and pharmaceutical industries. The growth of this market is driven by various factors, including increasing global demand for packaged products and heightened awareness regarding food safety and quality. Companies prioritize the selection of packaging solutions that not only enhance product shelf life but also maintain sterility and nutritional integrity.
Aseptic packaging serves as a linchpin in achieving these goals while addressing the needs of diverse consumer segments that favor convenience and reliability in their purchases.
Market Growth Trends
In recent years, aseptic packaging has experienced significant growth due to several trends:
- Rising Health Consciousness: As consumers become more health-conscious, there is an increased preference for products with longer shelf life without preservatives. Aseptic packaging enables this through optimal sterilization methods.
- Urbanization: The shift towards urban living often correlates with busier lifestyles, pushing consumers towards easy-to-use packaged foods. Aseptic solutions cater to this need effectively.
- E-commerce Expansion: The growth of online shopping has necessitated better packaging solutions to ensure product integrity during transit. Aseptic packaging assures consumers that they receive safe and uncontaminated products.
- Sustainability Initiatives: Companies are increasingly seeking sustainable packaging options. Innovations in materials for aseptic packaging aim to reduce environmental footprints while being efficient.
These trends indicate not only a robust demand but a transformation in consumer expectations. Companies must adapt to thrive in this competitive landscape.
Key Players in the Industry
The aseptic packaging market is populated by several key players who drive innovation and set benchmarks for quality and efficiency. Some notable companies include:
- Tetra Pak: Known for their comprehensive solutions in liquid food packaging, Tetra Pak has been a leader in the development of aseptic packaging techniques.
- SIG Combibloc: This company specializes in carton packaging and has pioneered various forms of aseptic carton drinks, further emphasizing sustainability.
- Sealed Air Corporation: They offer a variety of aseptic packaging solutions, with an emphasis on food protection and hygiene.
- Smurfit Kappa: A global leader in paper-based packaging, they focus on innovative packaging solutions including aseptic options.
- Robert Bosch GmbH: They provide equipment solutions for aseptic packaging, emphasizing technology-driven efficiency.
These players not only contribute to the technology and design improvements but also play an essential role in ensuring compliance with regulatory standards. By constantly evolving their offerings, they help maintain the integrity and safety of aseptically packaged products in the market.
Ultimately, understanding the market dynamics of aseptic packaging is crucial for anticipating consumer needs and aligning products accordingly.
Innovations in Aseptic Packaging Technology
Innovations in Aseptic Packaging Technology represent a critical aspect of the modern packaging landscape. They enhance the safety and shelf life of food and pharmaceutical products. In recent years, the industry has seen significant advancements that address various challenges faced by manufacturers. The evolution of aseptic packaging is not merely about improving current techniques but involves integrating new technologies, materials, and methods to optimize the overall packaging process.
Advancements in Materials
The development of advanced materials for aseptic packaging has the potential to revolutionize this field. Flexible films and high-barrier materials are at the forefront of these innovations. These materials can provide superior protection against microbial contamination, oxygen, and moisture, essential for maintaining product integrity.
Using materials such as polyethylene and polyamide not only improves the strength and durability of packages but also meets sustainability goals. Biodegradable and recyclable materials are increasingly being explored. Companies aim to reduce environmental impact while still providing effective packaging solutions.
Key benefits of advancements in materials include:
- Improved Protection: Enhanced barrier properties prolong shelf life and preserve the quality of sensitive products.
- Sustainability: Focus on eco-friendly materials supports global initiatives for a greener future.
- Cost-Effectiveness: New materials can lead to lower production costs due to increased efficiency in packaging processes.
Automation in Packaging Processes
Automation has become a cornerstone of innovations in aseptic packaging technology. By adopting automated systems, manufacturers can achieve consistent quality and efficiency. Automated filling, sealing, and handling reduce human error, which is crucial for maintaining sterile conditions during production.
Advanced robotics and sensors play a key role in integrating automation into packaging lines. These technologies help in monitoring processes in real-time, ensuring compliance with safety standards.
Benefits of automation include:
- Increased Speed: Automated systems enable faster production rates, meeting the demands of a growing market.
- Consistency and Precision: Machines operate with high accuracy, reducing the variability found in manual processes.
- Enhanced Safety: Automation minimizes human contact with sensitive products, reducing contamination risks.
"Innovations in materials and automation not only improve the efficiency of aseptic packaging but also contribute to sustainability goals within the industry."
Overall, innovations in aseptic packaging technology are pivotal to the success of food and pharmaceutical sectors. The combination of new materials and automated processes ensures that products remain safe and of high quality, catering to consumer demands and regulatory standards.
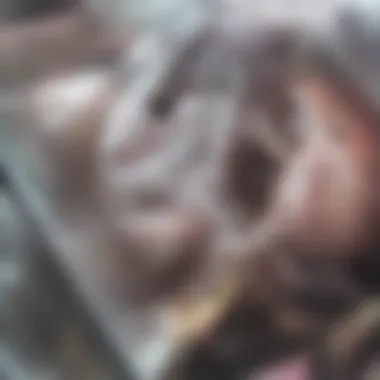
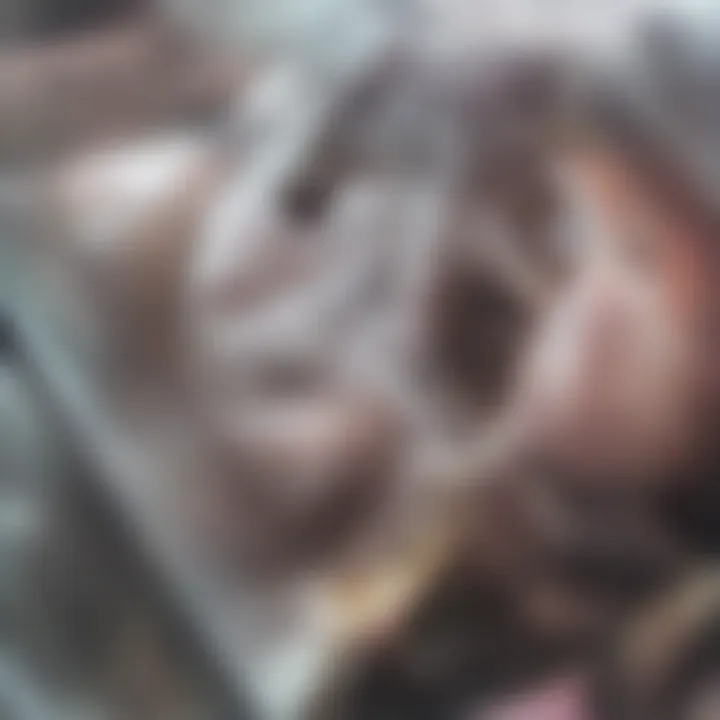
Regulatory Standards for Aseptic Packaging
Regulatory standards for aseptic packaging serve as fundamental guidelines to ensure product safety, quality, and consumer trust. These regulations are imperative for manufacturers and stakeholders in the food and pharmaceutical sectors. They not only define the minimum requirements for packaging technology but also ensure that products maintain their integrity throughout the supply chain. Understanding these standards is crucial for compliance and can considerably influence the operational dynamics of companies engaged in aseptic packaging.
FDA Guidelines
The U.S. Food and Drug Administration (FDA) sets stringent guidelines for aseptic packaging in food and pharmaceuticals. These guidelines are vital for safeguarding public health and ensuring that all packaged products are safe for consumption or use. The FDA focuses on several components:
- Sterilization Processes: The FDA mandates that equipment used in aseptic packaging must be appropriately sterilized to eliminate any harmful microorganisms. This includes the careful selection of sterilants and monitoring their efficacy.
- Quality Control Measures: Regular inspections, testing, and preventive measures must be in place to ensure consistent production quality. Each batch must adhere to FDA's standards before it can enter the market.
- Labeling Requirements: Accurate labeling that meets FDA specifications is crucial. The information on packaging must not mislead consumers and must include potential allergens, nutritional content, and expiration dates.
Adherence to FDA guidelines not only defines the operational integrity of food and drug products but also strengthens consumer confidence. Companies failing to meet these guidelines face substantial penalties and damage to their reputation.
International Standards
In addition to FDA regulations, international standards also play a key role in aseptic packaging. Organizations such as the International Organization for Standardization (ISO) and Codex Alimentarius have established guidelines that are widely recognized:
- ISO 22000: This standard outlines requirements for food safety management systems. It emphasizes risk assessment throughout the food supply chain, ensuring that every step in the aseptic packaging process adheres to food safety protocols.
- Codex Alimentarius: This set of international food standards provides guidance on food safety and consumer protection. It harmonizes regulations globally, fostering international trade while ensuring that food safety is prioritized.
- Hygiene Protocols: International regulations often include strict hygiene protocols to be followed in the production environment. This ensures that products are manufactured in a clean environment, minimizing the risk of contamination.
Compliance with these international standards not only enhances market access but also establishes a company's commitment to quality and safety on a global scale.
Future Trends in Aseptic Packaging
The future of aseptic packaging is evolving rapidly in response to changing consumer preferences, technological advancements, and increasing regulatory demands. Understanding these trends is critical not just for industry stakeholders but also for consumers who are becoming more conscious about the products they purchase. As we look ahead, several key elements will define the landscape of aseptic packaging, significantly impacting the food and pharmaceutical sectors.
Sustainability Initiatives
One of the most critical trends in aseptic packaging is sustainability. Manufacturers are increasingly focusing on environmentally friendly practices. This includes using biodegradable materials and reducing energy consumption during production.
Common initiatives include:
- Material Innovation: Development of plant-based plastics that are less harmful to the environment.
- Recyclability: Designing packaging that can easily be recycled or composted, promoting a circular economy.
- Reduction of Waste: Implementing production methods that minimize waste during the packaging process.
Sustainable practices not only appeal to eco-conscious consumers but can also reduce costs in the long term. By aligning with sustainability goals, companies can enhance their brand image and meet regulatory requirements that are increasingly focused on environmental impacts.
Smart Packaging Solutions
Another trend influencing the aseptic packaging industry is the rise of smart packaging solutions. These innovations integrate technology into packaging to enhance user experience and product preservation.
Some noteworthy developments in smart packaging include:
- Sensor Technology: Embedded sensors that monitor conditions such as temperature and humidity, providing real-time data on product integrity.
- Track and Trace: QR codes or NFC tags that allow consumers to access information about the product's journey, enhancing transparency and accountability.
- Interactive Features: Packaging that engages consumers, offering them product information, usage tips, or promotional content directly on their smartphones.
The implementation of smart technologies can lead to improved quality control, reduced spoilage, and enhanced consumer confidence in packaged products.
"The intersection of sustainability and technology is poised to redefine the future of the aseptic packaging industry, making it both environmentally responsible and consumer-friendly."
Impact of Aseptic Packaging on Consumer Behavior
Aseptic packaging has seen a considerable rise in importance due to its effects on consumer behavior. As the food and pharmaceutical markets evolve, so too do consumers' expectations regarding product safety, quality, and convenience. Aseptic packaging plays a critical role in meeting these demands, using sterile processes to ensure that products remain uncontaminated and maintain their integrity. This relevance can be broken down into various aspects influencing consumer choices.
Consumer Awareness and Perception
Consumer awareness has transformed in recent years. Thanks to the internet and social media, individuals can easily access information about food safety and product packaging. In this context, aseptic packaging stands out due to its perceived benefits. Many consumers associate aseptic packaging with higher-quality products, believing that such methods eliminate reliance on preservatives and extend shelf life naturally.
A survey from a recent industry study revealed that more than 60% of consumers consider packaging technologies that promote safety and shelf life as a purchasing factor. The visuals of products in aseptic packaging, often showcasing clean and modern designs, further enhance consumer perception. They see these products as fresher and healthier compared to those in traditional packaging.
Another vital point is the correlation between packaging and brand trust. Brands that use aseptic packaging prominently highlight this fact in their marketing efforts to boost consumer confidence. This creates a direct impact on purchasing decisions and shapes consumer habits over time. The robust nature of aseptic packaging suggests reliability in product safety, drawing customers who value these traits in their choices.
Market Demand for Aseptic Products
The market demand for aseptic products has grown substantially. This is largely due to the shifting dietary preferences of consumers and a general rise in health consciousness. More people are looking for products that retain nutrients while being free from artificial additives, and that is where aseptic packaging comes into play.
The growth in demand is reflected in various market studies. Researchers observed that the market for aseptic packaging is expanding at a compound annual growth rate (CAGR) of around 8% in some regions. Consumers are leaning towards products that offer longer shelf life without compromising quality. Popular categories include dairy products, sauces, and ready-to-eat meals, among others.
Moreover, the convenience aspect cannot be overlooked. As urban lifestyles become busier, consumers increasingly prefer products that are easy to store and consume. Aseptic packaging makes products shelf-stable for extended periods, requiring no refrigeration until opened, and this is highly appealing for today's on-the-go consumer.
The End on Aseptic Packaging Machines
In this article, we explored the expansive domain of aseptic packaging machines, highlighting their vital role in the food and pharmaceutical industries. Understanding this topic helps readers appreciate how these systems ensure product safety and longevity. Aseptic packaging machines enable numerous advantages, including extended shelf life, reduced need for preservatives, and overall cost efficiency. Each of these elements contributes to maintaining high standards for consumer goods, making them more appealing to health-conscious consumers.
Recap of Key Points
- Definition and Importance: Aseptic packaging is crucial for preserving the integrity of food and pharmaceutical products. The technology ensures that products remain uncontaminated during production and distribution.
- Operational Principles: The machines rely on advanced sterilization techniques, paired with precise filling and sealing processes to maintain the quality of the product.
- Market Dynamics: Analyzing current trends and the key players in the industry gives insight into how aseptic packaging machines continue to evolve.
- Innovations and Future Trends: The integration of sustainability initiatives and smart packaging solutions reflects the industry's commitment to innovation and addressing consumer concerns.
- Regulatory Standards: Adhering to guidelines from organizations like the FDA is essential for maintaining safety in the production process.
Aseptic packaging machines form the backbone of modern food and pharmaceutical production, ensuring quality and safety at every step.
Outlook for the Future
As we look ahead, the future of aseptic packaging machines appears bright. With growing consumer awareness regarding health and safety, the demand for efficient, high-quality packaging solutions will likely increase. Future innovations may include:
- Sustainability Initiatives: Companies are expected to implement environmentally friendly materials and processes, responding to both consumer demand and regulatory pressure.
- Smart Packaging Solutions: The rise of IoT technology may lead to more intelligent packaging systems that monitor product conditions and improve supply chain efficiency.
- Advanced Sterilization Techniques: Innovations in sterilization technology could improve the efficacy of aseptic processes, making them even more reliable.
In summary, the ongoing development of aseptic packaging technology will be crucial for meeting today's challenges in the food and pharmaceutical sectors. As public awareness and safety standards continue to evolve, so too will the methods and machines in use.