Recycled Plastic Extrusion: Comprehensive Analysis
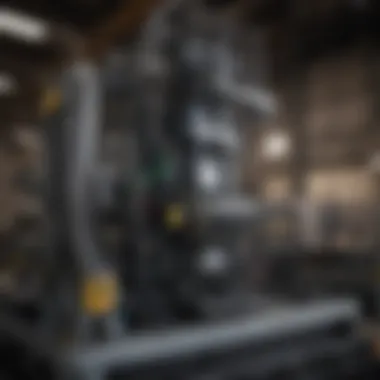
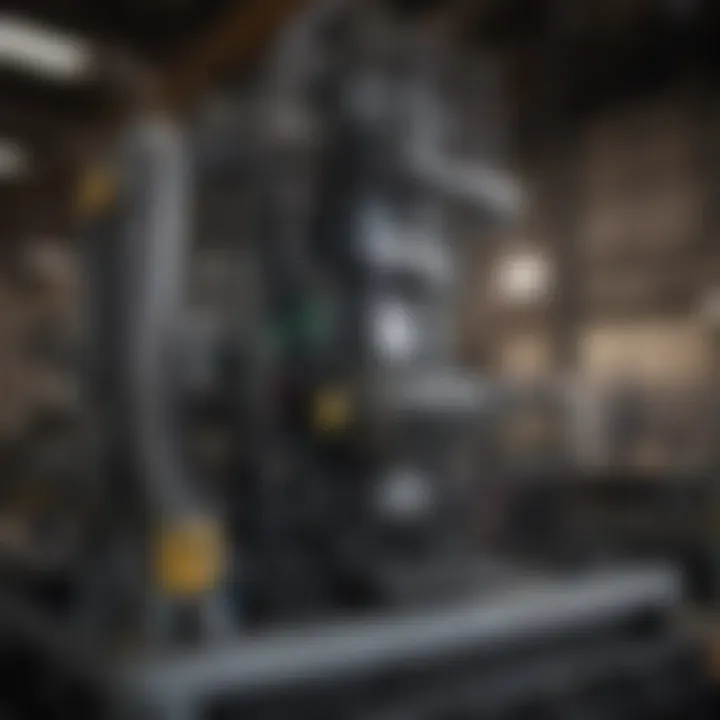
Intro
In today's world, the plastic industry faces immense scrutiny due to the environmental challenges posed by plastic waste. Recycled plastic extrusion emerges as a significant solution, addressing these issues while delivering tangible benefits. This process not only repurposes discarded plastics but also transforms them into valuable products. Understanding the intricacies of recycled plastic extrusion allows students, researchers, educators, and professionals to grasp its significance within sustainable manufacturing processes.
Research Context
Background and Rationale
The need for recycling plastics has become urgent. With millions of tons of plastic produced annually, the overwhelming majority ends up in landfills or oceans. The recycling process enables the recovery of this material, converting waste into economically viable goods. Recycled plastic extrusion stands at the forefront of this process, facilitating the transformation of raw recycled content into usable products.
Literature Review
Research on recycled plastic extrusion has expanded significantly over the past decades. It encompasses various studies on material properties, recycling methods, and technological advancements. A notable body of work explores the efficiency of different extrusion techniques and their impact on the quality of recycled products. For instance, works by researchers highlight the importance of material selection in achieving optimal extrusion performance and maintaining product integrity. This literature serves as a foundation for understanding the challenges faced in the field, as well as the potential for future innovations.
Methodology
Research Design
The exploration of recycled plastic extrusion can be both qualitative and quantitative. A qualitative approach gathers insights through case studies and interviews with industry experts, emphasizing real-world applications and experiences. Conversely, quantitative research might involve experiments that measure the performance of recycled materials in various extrusion settings, providing empirical data to support findings.
Data Collection Methods
Data collection can include several methods:
- Surveys: Gathering information from professionals in the recycling and manufacturing sectors about their practices and perceptions.
- Experimental Studies: Conducting controlled experiments in laboratories to test specifications of different plastics during the extrusion process.
- Field Observations: Documenting real-world applications in manufacturing plants to understand the challenges and successes faced in recycled plastic extrusion.
As the field advances, there remains a need for ongoing research and development. The ultimate goal is to improve techniques, reduce costs, and enhance the overall impact of recycled plastics in manufacturing.
Foreword to Recycled Plastic Extrusion
Recycled plastic extrusion plays a vital role in the sustainability of manufacturing processes. As the world grapples with escalating plastic waste, the importance of finding innovative ways to recycle these materials cannot be overstated. This section provides an overview of the fundamentals and significance of recycled plastic extrusion, guiding readers through its definition and the broader relevance of recycling plastics.
Definition of Extrusion
Extrusion is a manufacturing process used to create objects of a fixed cross-sectional profile. Materials, typically thermoplastic polymers, are forced through a die to form shapes such as pipes, sheets, or profiles. The process begins with loading plastic pellets into an extruder. Heat melts the material, which is then pushed through the die. This method is particularly beneficial for recycled plastics, as it can use a variety of feedstocks, ranging from post-consumer waste to industrial scrap.
Importance of Recycling Plastics
The recycling of plastics serves multiple critical functions in today’s economy and environment. First and foremost, it aids in reducing the finite extractive pressure on natural resources like petroleum. By reusing existing materials, companies can lower the demand for virgin plastics, thereby contributing positively to environmental conservation.
The significance of recycling plastics extends beyond resource savings. It also plays a key role in waste management. Plastics constitute a substantial portion of global waste, often taking hundreds of years to decompose in landfills. Effective recycling processes result in the reduction of landfill mass, mitigating adverse ecological impacts.
Furthermore, recycled plastics can drive economic growth through job creation in recycling facilities and manufacturing sectors. As industries strive to meet sustainability goals, there is an increasing market for products made from recycled materials. Companies that embrace recycled plastic extrusion often find themselves at the forefront of innovation, providing eco-friendly products that meet consumer demand.
In summary, understanding the definition of extrusion and recognizing the importance of recycling plastics sets the stage for a deeper exploration into the processes, technology, and applications that will follow in this article.
"Recycling turns things into other things. Which is like magic." - Anonymous
By comprehensively addressing these topics, this article aims to elevate awareness and knowledge of recycled plastic extrusion and its integral role in fostering a sustainable future.
The Recycling Process
The recycling process stands as a critical segment of the overall narrative on recycled plastic extrusion. It encompasses a series of systematic procedures that not only help in regenerating plastic materials but also contribute significantly to environmental sustainability. The intricacies involved in this process determine the quality and viability of the recycled plastics that find new life in various applications. Understanding this process is essential for anyone engaged in the field of environmental science, manufacturing, or sustainable practices.
Collection and Sorting of Plastics
The first phase in the recycling process is the collection of plastics. This stage requires a strategic approach, as the effectiveness of subsequent steps largely depends on the quality of the collected materials. Plastics can be sourced from various channels, including households, industrial waste, and commercial entities. Once collected, sorting takes precedence. During sorting, different types of plastics are separated based on resin identification codes and material types.
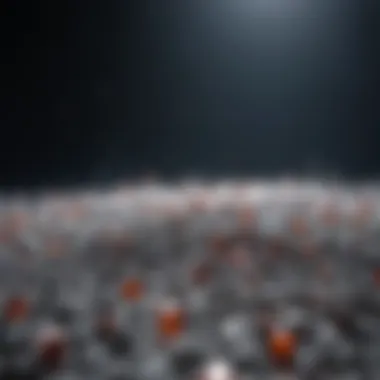
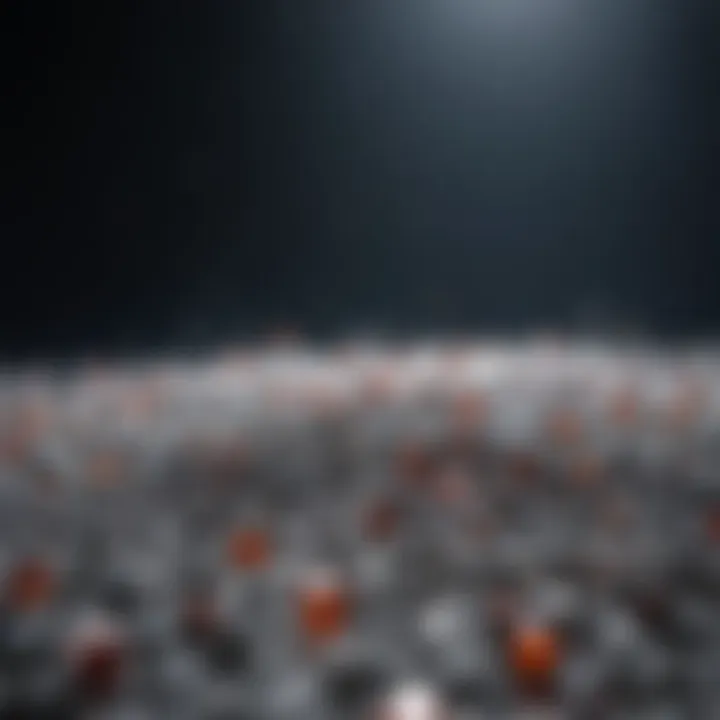
Efficient sorting is vital due to the fact that not all plastics are recyclable in the same manner. For example, Polyethylene Terephthalate (PET) and High-Density Polyethylene (HDPE) can often be recycled more easily than others like Polystyrene (PS). The sorting process can utilize a combination of manual labor and automated technologies, like optical sorting machines, to ensure an accurate division. This meticulous effort helps to eliminate contamination, which is critical for achieving high-quality recycled materials.
Cleaning and Shredding
After sorting, the next step involves cleaning the plastics. This stage addresses the removal of labels, adhesive residues, and any other contaminants that could affect the integrity of the recycled product. Washing systems that employ both water and specialized detergents are often used to achieve a satisfactory level of cleanliness.
Once cleaned, the plastics undergo shredding, which reduces them into smaller, manageable pieces. Shredding is an essential action that enhances the efficiency of the melting process. The size reduction facilitates a consistent melting process, which is crucial for ensuring uniformity in the final extruded products. Clean and uniformly sized plastic flakes set the stage for effective melting and extrusion down the line.
Melting and Extrusion
The final step in the recycling process is melting and extrusion. During this phase, the shredded plastic flakes are fed into an extruder, which applies both heat and pressure to melt the material. This transformation is a complex interplay of temperature control and mechanical processing.
As the plastic melts, it is pushed through a die, which shapes the material into specific forms like pellets or sheets, ready for further processing. A category of machinery termed extruders is central in this stage. Single-screw extruders or twin-screw extruders are utilized based on the extent of mixing and homogenization required.
This melting and extrusion process not only repurposes waste materials but also embodies a significant reduction in energy consumption compared to producing virgin plastics. The efficiency gained from the recycling process reinforces its importance as an eco-friendly practice, contributing to a more sustainable material lifecycle.
Key Insight: The recycling process of plastics enhances resource efficiency and reduces environmental impact. It transforms discarded materials into usable products, fostering a circular economy in the plastics industry.
Machinery Used in Recycled Plastic Extrusion
The machinery utilized in recycled plastic extrusion plays a critical role in enhancing the efficiency and effectiveness of the recycling process. Proper machinery ensures that plastics can be transformed from waste materials into usable products through various stages of extrusion. Understanding the types of machines involved is essential for optimizing production and addressing environmental concerns associated with plastic waste.
Extruders
Single-Screw Extruders
Single-screw extruders are one of the most commonly used machines in the extrusion of recycled plastics. They consist of a single screw rotating within a barrel. This design allows for continuous feeding and melting of plastics, making it a preferred choice in many recycling plants.
One key characteristic of single-screw extruders is their simplicity and ease of operation. They require less maintenance compared to more complex systems. This is beneficial for facilities looking to minimize operational costs while maximizing output. The continuous operation also allows for a steady flow of material, which increases productivity.
However, the single-screw design has limitations in processing materials with varying rheological properties. The mixing and conveying efficiency may be compromised, leading to potential inconsistencies in product quality. Despite these disadvantages, they remain a popular choice due to their effective heat distribution and straightforward design.
Twin-Screw Extruders
Twin-screw extruders, on the other hand, are characterized by two parallel screws that rotate in either the same or opposite directions. This configuration permits better mixing and homogeneity of materials, which is vital in the recycling of plastics that have undergone different forms of contamination.
The primary advantage of twin-screw extruders is their ability to process a wide variety of plastics, even those that contain additives or are not homogeneous. This capability enhances their versatility, making them a strong candidate for facilities focusing on diverse plastic types. The high shear forces generated enable efficient melting, compounding, and mixing, resulting in higher-quality recycled products.
Nonetheless, these machines can have higher operational costs due to their complexity and maintenance requirements. The investment in twin-screw technology may lead to improved product quality but also requires careful consideration of budgetary constraints.
Granulators
Granulators are integral to the recycling process as they are responsible for reducing solid plastics into smaller, more manageable particles. This process of size reduction is crucial for the subsequent extrusion stages. Granulators can handle large quantities of pre-processed materials, ensuring that the feedstock for extrusion is uniform and of a quality suitable for melting. They often come equipped with features such as adjustable screens that allow for control over particle size, thereby facilitating tailored processing as per specific material requirements.
Cooling Systems
Cooling systems are necessary to solidify the melted plastic once it exits the extruder. Without proper cooling, the shape and properties of the final product may be compromised. Various cooling solutions are available, ranging from water baths to air-cooling technologies. Efficient cooling not only preserves the integrity of the extruded product but also enables faster production rates. This part of the machinery setup requires careful design and maintenance to ensure optimal performance, reducing the risk of thermal deformation in the final plastic products.
Overall, understanding the machinery involved in recycled plastic extrusion allows professionals in the field to innovate and improve recycling processes. Knowledge of the strengths and weaknesses of each type of equipment aids in making informed decisions that can lead to higher product quality, sustainability, and efficiency in the recycling sector.
Types of Recyclable Plastics
Understanding the types of recyclable plastics is essential for optimizing the extrusion process and enhancing environmental sustainability. Different types have unique properties, which affect their recyclability and applications. Knowing these properties helps industries adopt more effective recycling strategies.
PET (Polyethylene Terephthalate)
PET is one of the most widely recycled plastics. Its high strength and clarity make it popular for bottling beverages and food containers. The recycling process for PET involves collecting the plastic, which is then sorted, cleaned, and shredded into flakes. These flakes are melted and then extruded into filament or sheets for various applications. Its recyclability means that it significantly reduces raw material consumption and energy use, compared to producing new PET from crude oil.
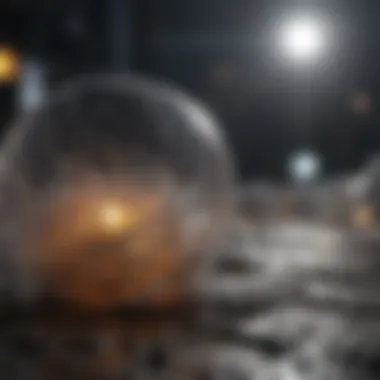
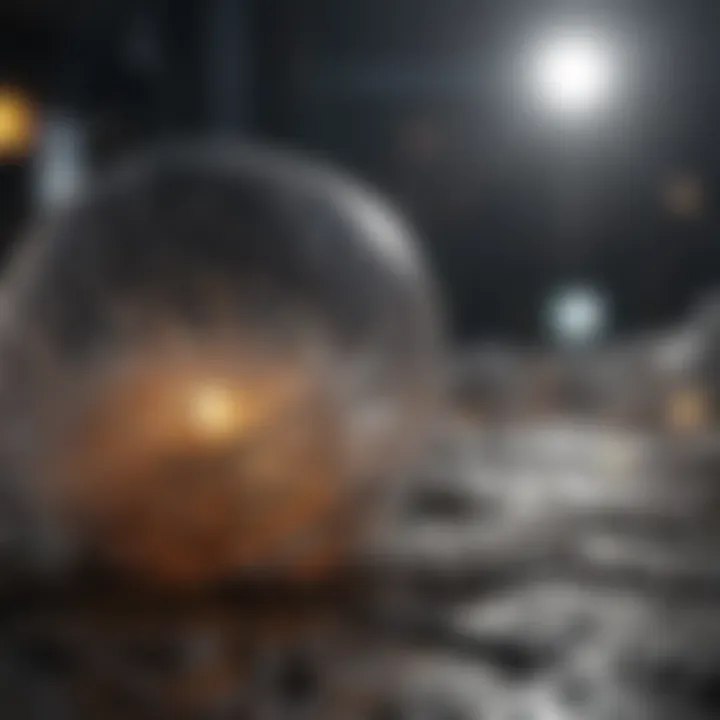
HDPE (High-Density Polyethylene)
HDPE is known for its strength and resistance to impact and chemicals. It is commonly used in containers for household goods, milk jugs, and pipes. Recycling HDPE is efficient due to its simple structure, which allows for easy sorting and cleaning. The material can be reutilized in a multitude of products, such as toys, recycling bins, and even durable piping. Recycled HDPE often keeps its properties, making it a valuable resource in manufacturing.
LDPE (Low-Density Polyethylene)
LDPE, known for its flexibility and toughness, is often used in bags and wraps. It poses unique challenges in recycling due to its lighter weight and tendency to become tangled in machinery. However, innovations are being made to improve its recycling process. LDPE can be transformed into new materials like floor tiles and rubbish bin liners. Its lower density can mean less energy required to transport it, making recycling economically viable under appropriate logistical circumstances.
PP (Polypropylene)
Polypropylene is characterized by its high thermal resistance and durability, making it suitable for automotive parts, consumer goods, and packaging. Recycling PP is complicated compared to PET and HDPE, but it is still possible and valuable. It often requires advanced sorting technologies to separate it from other plastics effectively. The demand for recycled polypropylene has been on the rise, especially in sectors looking for lightweight and recyclable solutions.
In summary, each type of recycled plastic brings distinct advantages and challenges. Understanding these differences allows manufacturers and recyclers to develop targeted approaches that enhance recycling efficiency and boost sustainability outcomes.
Applications of Recycled Plastic Products
The applications of recycled plastic products are critical in understanding the broader impact of plastic recycling initiatives. By transforming waste plastics into usable materials, this segment contributes not only to waste reduction but also to the fabrication of new, innovative products. The importance of applying recycled plastics lies in their versatility and sustainability.
Using recycled plastics leads to a more sustainable future. It mitigates the demand for virgin raw materials and reduces the carbon footprint linked to new plastic production. The lifecycle of these products highlights the effectiveness of resource efficiency in manufacturing processes.
Packaging Solutions
Packaging solutions are perhaps the most visible application of recycled plastic products. In an era where consumers are increasingly environmentally conscious, brands emphasize packaging made from recycled materials. Notably, recycled PET, commonly known as rPET, is frequently used in beverage bottles and food containers. Its ability to retain the purity of food products while minimizing environmental impact makes it a favorable choice.
The benefits include:
- Reduced environmental impact from packaging waste
- Closed-loop recycling potential
- Enhanced brand image through sustainable practices
Recycled packaging solutions fulfill both functional and aesthetic needs for both manufacturers and consumers.
Construction Materials
Construction materials represent an emerging and innovative use of recycled plastics. The construction industry is constantly seeking materials that not only meet safety and durability standards but also add sustainability credentials to building projects.
Recycled Plastic Lumber
Recycled plastic lumber is a significant development in construction applications. It offers a robust alternative to traditional wood, providing a long-lasting and low-maintenance option. One key characteristic of recycled plastic lumber is its resistance to rot, insects, and moisture. This quality makes it a beneficial choice for outdoor applications like decks, fences, and park benches.
A unique feature of recycled plastic lumber is its aesthetic flexibility. It can be designed in various colors and textures, allowing it to fit seamlessly in various architectural styles. However, the main disadvantage can be its initial cost, which may be higher than traditional wood. Despite that, its longevity often offsets the upfront investment over time, providing financial benefits in the long term.
Insulation Materials
Insulation materials made from recycled plastics are also gaining traction. They contribute significantly to energy efficiency in buildings. One key characteristic of these insulation materials is their excellent thermal properties, offering superior resistance to heat flow compared to traditional insulation products.
The unique feature of recycled insulation is the reduced environmental footprint. This material lowers the energy requirements for heating and cooling homes, ultimately contributing to lower utility bills for homeowners. Nevertheless, there can be concerns about the flammability of certain recycled plastic insulation forms, requiring adherence to strict building codes.
Consumer Products
The consumer product market comprises a broad spectrum of items that utilize recycled plastics. From household goods to electronics casings, the adaptive use of recycled materials offers a unique approach to creating functional products.
Products produced from recycled plastics present a compelling case for consumers seeking sustainable options. Moreover, the constant innovation in this area leads to the development of new product lines, fulfilling market demand while addressing environmental issues.
In summary, applications of recycled plastic products reflect a shift towards sustainable practices across various industries. The ongoing exploration and integration of recycled materials underscore the necessity of addressing plastic waste while meeting the diverse needs of consumers and industries alike.
Environmental Impact of Recycled Plastic Extrusion
The environmental impact of recycled plastic extrusion is significant. As more industries look to minimize their ecological footprint, the role of recycled plastics has grown. This section will discuss how the process affects waste management, energy consumption, and the challenges related to contaminants that enter the recycling stream.
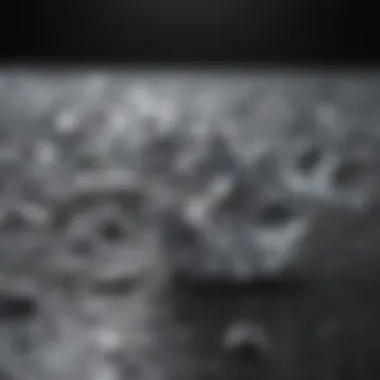
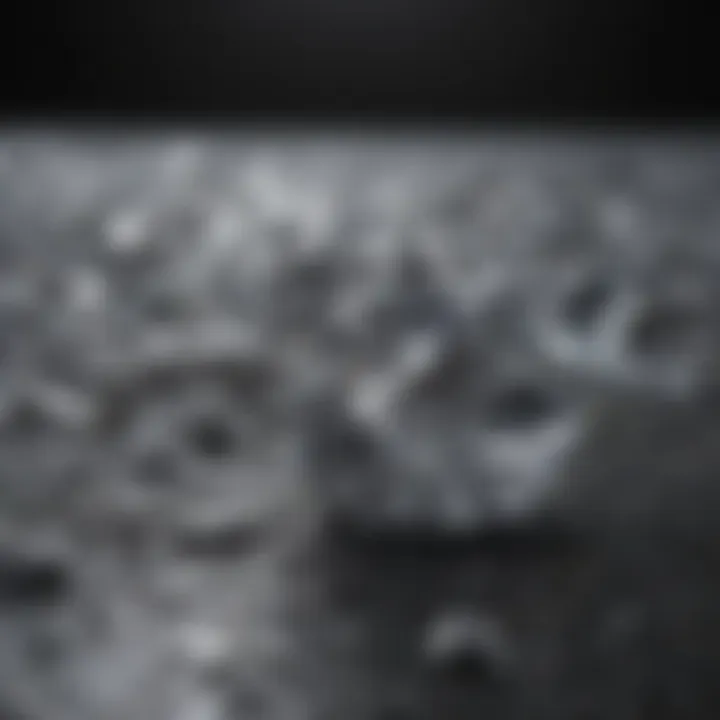
Reduction of Plastic Waste
The first and foremost benefit of recycled plastic extrusion is the reduction of plastic waste. Plastics often end up in landfills or oceans, creating severe environmental issues. The extrusion process transforms discarded plastic materials into new products, effectively diverting waste from these harmful outcomes. By incorporating waste plastics into production, manufacturers not only minimize the volume of waste but also help to alleviate the demand for virgin raw materials. This can have a cascading effect on the environment, as less extraction of natural resources is needed.
In cities and countries that actively recycle, the impact can be drastic. For instance, programs that promote recycling can lead to significant reductions in landfill waste, improving local ecosystems. Effective recycling also encourages a circular economy, where materials are reused multiple times, contributing to sustainability on a broader scale.
Energy Savings Compared to Virgin Plastics
Another critical benefit of recycled plastic extrusion lies in the energy savings it provides. Recycling plastics requires considerably less energy compared to producing new plastics from raw materials. For instance, the recycling of polyethylene terephthalate (PET) can save up to 75% of the energy that would otherwise be needed if virgin materials were used.
The lightweight nature of recycled materials also contributes to lower transportation costs and emissions. These energy savings can lead to lower production costs, encouraging more manufacturers to consider recycled options. As industries aim for sustainability, the push for energy-efficient processes is becoming a focal point in the debate surrounding plastic production and management.
Challenges with Contaminants
Despite the benefits, the recycling process is not without its challenges. Contaminants play a significant role in the effectiveness of recycled plastic extrusion. The presence of foreign materials can affect the quality of the recycled products. When plastics are mixed with contaminants—like food residues or non-recyclable products—the quality of the material diminishes. This can lead to higher rates of rejection and waste during the recycling process.
Additionally, the removal of these contaminants can be costly and time-consuming. Companies may invest in advanced cleaning technologies to improve the quality of recycled plastics, which can further complicate the economic viability of recycling programs. Education on proper recycling practices among consumers and industries is essential in minimizing contamination and maximizing the effectiveness of recycling efforts.
"Effective recycling systems not only simplify the process but also enhance the quality of the output."
Future Trends in Recycled Plastic Extrusion
The future of recycled plastic extrusion hinges on several emerging trends that promise to reshape the industry. These trends are not only potential advancements in technology but also vital shifts in market demands and material science. By focusing on these future trends, stakeholders can understand how to position themselves strategically in a market that increasingly values sustainability and innovation.
Innovations in Material Science
Material science is the backbone of any advancement in recycling technologies. One significant innovation is the development of bio-based plastics. These materials, derived from renewable sources, can offer a more sustainable alternative to conventional plastics while still benefiting from the qualities that make plastics desirable, such as durability and versatility. Research is also focused on improving the recyclability of existing petroleum-based plastics, making them easier and more efficient to process.
Another area of innovation involves the creation of additives that enhance the quality of recycled materials. For instance, researchers are exploring the use of specific chemical treatments that can help remove contaminants and restore the integrity of the plastic. Furthermore, continuous advancements in polymer blends are allowing for more robust recycled materials that can be used across a wider array of applications.
Technological Advancements in Machinery
Machinery plays a crucial role in the efficiency of recycled plastic extrusion. Future trends are heavily leading towards more sophisticated and energy-efficient extruders. For instance, the integration of Artificial Intelligence (AI) in monitoring and controlling extrusion processes can significantly enhance operational efficiency. AI can predict when maintenance is needed, reducing downtime and improving throughput.
Additionally, advancements in robotics may streamline the automation of sorting and processing recycled plastics. Automated systems tend to minimize human error and maximize the speed of production, resulting in lower costs and less waste.
"Technological improvements can potentially double the efficiency of recycled plastic extrusion processes, leading to more sustainable manufacturing practices."
The use of advanced sorting technologies, such as near-infrared spectroscopy, is also set to become more prevalent. These systems can better identify and segregate different plastic types, thereby increasing the purity of feedstock used in extrusion.
Market Demand for Sustainable Products
The market for sustainable products is on the rise, with consumers increasingly preferring goods made from recycled materials. This shift is prompting manufacturers to adopt recycled plastic extrusion more broadly. The trend correlates strongly with environmental awareness and corporate social responsibility initiatives. Brands that utilize recycled plastics often gain a competitive advantage by appealing to eco-conscious consumers.
Additionally, regulations are becoming stricter across many nations, pushing industries to reduce their reliance on virgin materials. As policymakers implement more stringent standards on plastic waste and recycling, businesses that align with these regulations will likely thrive.
The demand is particularly pronounced in sectors like construction, automotive, and packaging, where companies seek more sustainable options without compromising quality. Overall, the growing market demand is not just a trend; it represents a significant realignment of product development strategies in favor of sustainability and responsible sourcing.
Ending
Recycled plastic extrusion represents a vital process in addressing the growing issue of plastic waste and its impact on the environment. The conclusion of this article synthesizes the key points discussed and emphasizes the role of recycled plastic materials in sustainable manufacturing. Understanding the intricacies of this process allows stakeholders to make informed decisions that promote environmental health and resource efficiency.
Summary of Key Points
Throughout the article, several significant points emerge about recycled plastic extrusion:
- Recycling Process: The journey of plastics from collection to extrusion includes critical steps like cleaning, shredding, and melting. Each phase influences the quality of the final product.
- Machinery and Technology: Specialized machinery, such as single-screw and twin-screw extruders, plays a crucial role in the effectiveness of the extrusion process. Technological advancements in this area are improving efficiency and product quality.
- Types of Plastics: Different types of recyclable plastics, like PET and HDPE, have varying properties that affect their usability and application in products.
- Applications: The application of recycled plastics spans diverse sectors, including packaging, construction, and consumer goods, demonstrating the versatility and necessity of these materials.
- Environmental Impact: By recycling plastics, manufacturers can significantly reduce waste, save energy, and mitigate the harmful effects of contaminants in the process.
Implications for the Future
The future of recycled plastic extrusion holds several implications that industry professionals, researchers, and policymakers should consider:
- Innovation in Materials: Ongoing research in material science is expected to yield new forms of recycled plastics with improved characteristics. These innovations could broaden the possibilities for their application.
- Technological Advancements: Continued investments in machine technology will likely enhance efficiency and sustainability. The development of smarter, more efficient systems can create a competitive edge in the industry.
- Market Dynamics: As consumer demand for sustainable products increases, businesses that adopt recycled plastic solutions may find new market opportunities. Awareness of environmental issues among consumers will shape future product design and manufacturing practices.
Understanding the dynamics of recycled plastic extrusion is no longer optional; it is essential for a sustainable future.