Satellite Manufacturing: A Comprehensive Overview
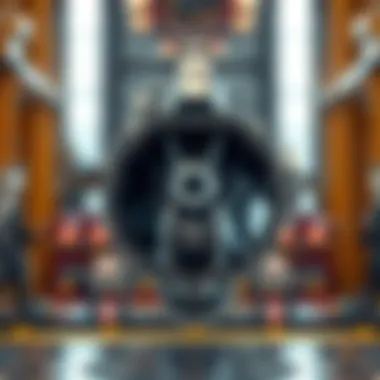
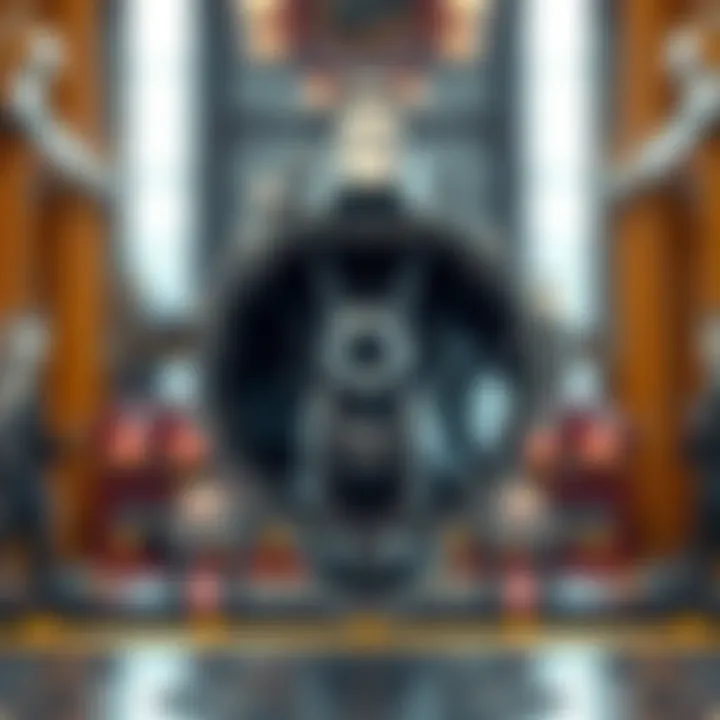
Intro
Satellite manufacturing stands as a remarkable synergy of cutting-edge science and practical engineering. As humanity extends its reach into the cosmos, the demand for intricate, reliable satellites has never been more pressing. Each satellite serves as a vital cog in the machinery of communication, weather forecasting, navigation, and countless other applications that shape our daily lives. This exploration seeks to peel back the layers of this intriguing field, revealing the complex processes and technologies that bring these high-tech instruments to life.
At the outset, it’s essential to grasp the breadth of satellite manufacturing. This encompasses not just the physical construction of satellites but also the intricate web of design, testing, and launch preparations. Emerging trends like miniaturization and sustainability practices are reshaping the industry landscape, making it imperative for stakeholders—whether they be government agencies or private companies—to keep pace with innovation.
To better appreciate the scope of satellite manufacturing, a thorough understanding of its context is necessary. This involves delving into the prevailing research, methodologies, and innovations that have characterized the field over the past few decades.
Research Context
Background and Rationale
The exploration of space has always sparked human curiosity and ambition. While early efforts in satellite design often revolved around basic functionality, the landscape has evolved dramatically. As technology advances, the design and production of satellites have become more sophisticated. This shift prompts a closer examination of the motivations behind satellite manufacturing.
Key driving forces include:
- Economic Growth: The satellite industry has become a cornerstone for many economies, providing services that facilitate not just communication but also fostering technological advancement and job creation.
- Security Concerns: In a world marked by rapid geopolitical changes, nations prioritize satellite technology for defense and intelligence purposes, which heightens the importance of robust manufacturing processes.
- Scientific Discovery: Satellites enable groundbreaking research opportunities, unlocking insights about our planet and beyond. This underlines the necessity for precise and reliable manufacturing.
Literature Review
A dive into existing literature reveals substantial information on several pivotal aspects of satellite manufacturing:
- Technical Advances: Numerous studies highlight advancements in materials science and electronics, influencing satellite capabilities.
- Environmental Considerations: Research in sustainability practices points toward minimizing waste and exploring greener materials during production.
- International Partnerships: Literature often notes the significance of collaboration between governmental entities and private firms, showcasing a cooperative spirit that fosters innovation.
When pieced together, this body of knowledge establishes a firm grounding for understanding modern satellite manufacturing, paving the way for deeper inquiry into methodologies and processes involved.
Prologue to Satellite Manufacturing
Satellite manufacturing plays a crucial role in today’s rapidly advancing technological landscape. It’s not just about putting metal in the sky; it’s about enabling communication, navigation, weather forecasting, and even scientific research. As we delve deeper into this exploration, it's essential to grasp the multifaceted nature of satellite production and its relevance in contemporary society.
Definition and Scope
To understand satellite manufacturing, we must first define what it entails. Satellite manufacturing encompasses every stage of creating a satellite, from its initial design all the way through to its final assembly and testing. This industry is a blend of advanced engineering principles, innovative technology, and in-depth knowledge of aerospace dynamics.
The scope of this field is vast. It involves not just the physical components, like the launch vehicle or the satellite body, but also the software systems that control their operations. Engineers must consider aspects such as thermal performance, electrical configuration, and even material durability when creating these high-tech spacecraft.
Some key points related to the scope of satellite manufacturing include:
- Variety of Applications: Satellites serve various purposes, from telecommunications to Earth observation.
- Technological Complexity: Manufacturing satellites requires advanced skills in fields like materials science and computer engineering.
- Collaborative Nature: The production of satellites often involves multiple stakeholders, including companies, governments, and research institutions.
Historical Context
Understanding the historical context of satellite manufacturing reveals how far we’ve come since the beginning of the space age. The launch of Sputnik by the Soviet Union in 1957 marked the dawn of satellite technology. This was the first artificial satellite and ignited a global race in space exploration.
From those humble beginnings, satellite technology evolved rapidly. The first commercial satellites followed in the early 1960s, paving the way for a booming industry. By the 1980s, satellites were being used for a multitude of applications, including weather forecasting, GPS tracking, and broadcasting signals to our homes.
Significant milestones in the history of satellite manufacturing include:
- The Moon landing (1969): This event showcased the potential of space technology, including satellites for navigation and communication.
- The launch of the Hubble Space Telescope (1990): A breakthrough in scientific capabilities, allowing us to peer deeper into the universe than ever before.
- The rise of small satellite technology (2000s): Miniaturization transformed the industry, leading to affordable and versatile CubeSats and nanosatellites.
Looking back, we see that satellite manufacturing has dramatically transformed our capabilities and understanding of the cosmos.
Design Phases of Satellites
Designing a satellite is not akin to throwing darts at a board and hoping for the best. It is a meticulous process that lays the groundwork for everything to follow in a satellite's lifecycle. The Design Phases ensure that a satellite meets mission requirements, operates correctly in space, and fits within budget constraints. In this way, the phases cater not only to the technical aspects but also to financial and operational considerations, ultimately shaping the future of satellite missions.
Conceptual Design
The Conceptual Design phase is like sketching the blueprint of a house before construction begins. It is the point where ideas blossom into tangible objectives. During this stage, engineers and designers come together to brainstorm potential solutions that align with mission goals. They assess parameters such as satellite size, weight, purpose, and operating environment, which shape the early design direction.
Key elements during this phase may include:
- Defining Mission Objectives: Clear objectives guide the design. Whether the satellite's role is communication, observational, or scientific research, the mission drives key design choices.
- Feasibility Studies: Here, teams evaluate whether the proposed concepts are realistic, considering factors such as technology readiness and cost.
"Ideas are like stars; if you go too far away from them, you might lose the way".
The Conceptual Design phase is crucial; solidifying these ideas allows teams to convey their vision to stakeholders effectively, bringing foundational support to the project before solid resources get invested.
Detailed Engineering Design
Once the Conceptual Design is pinned down, the next stop on the design train is the Detailed Engineering Design phase. This is where things get very specific and much less abstract. Engineers roll up their sleeves to break down the design into manageable components, preparing specifications that bring the satellite to life.
This stage involves:
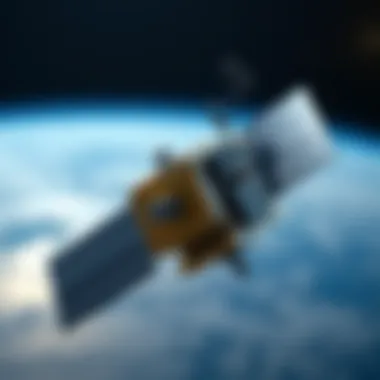
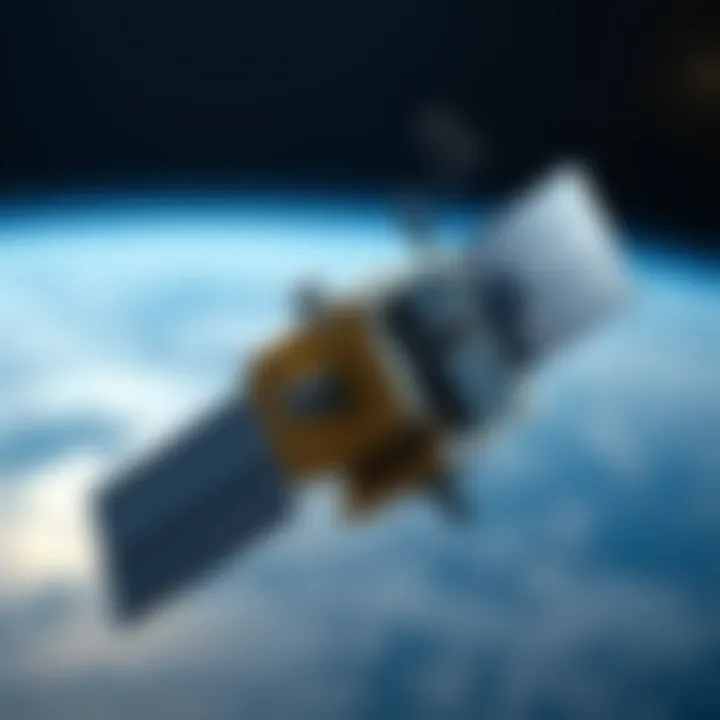
- Component Design: Each part is meticulously crafted, from the power systems to communication antennas. Each component must meet rigorous standards, ensuring compatibility and functionality.
- Thermal and Structural Analysis: Understanding how different materials will perform under the harsh conditions of space is fundamental. Engineers simulate how the satellite will withstand extreme temperatures and forces during launch.
- Documentation and Compliance: All designs are documented with detailed schematics. This documentation is essential for regulatory needs and will serve as a reference throughout the manufacturing phase.
Every small detail matters here, as overlooking a minor component can lead to significant issues down the road.
Prototyping
Once the blueprints and specifications set in stone, teams jump into the Prototyping phase, where virtual designs morph into physical forms. Prototyping is not merely about creating a test model; it's about verifying that the designs operate as planned.
In this phase, various prototypes are developed, which may include:
- Breadboard Models: Initial models focus on functionality, helping identify any design flaws early without throwing significant resources at them.
- Engineering Models: These might include closer representations of the final satellite and are subjected to performance tests to assess their reliability.
- Final Qualification Models: Designed to match the anticipated operational satellite, these undergo rigorous testing to ensure that when it's time for launch, the technology is sound and functional.
Prototyping provides a safety net. It allows engineers to test theories and ideas, adjusting as necessary before full-scale production starts. This iterative process is vital, ensuring that when the satellite indeed makes its maiden voyage into orbit, every system is primed and ready to go.
Manufacturing Processes
Manufacturing processes in satellite production are the backbone of transforming theoretical designs into tangible products ready for space. This phase covers a spectrum of activities that not only influence the final cost and efficiency but also ensure that the satellite can withstand the harsh realities of space environments. The significance of robust manufacturing processes cannot be underestimated, as they lay the groundwork for the reliability and functionality of satellites once they are deployed.
Importance of Manufacturing Processes:
- Efficiency: Streamlined processes can significantly reduce lead times and costs. A well-optimized assembly line enables manufacturers to respond swiftly to emerging demands or changes in designs.
- Quality Control: Proper manufacturing methods include stringent quality assurance checks at each phase. This minimizes errors that could be catastrophic for satellite missions, avoiding costly replacements or failures.
- Environmental Considerations: In the era of increasing focus on sustainability, manufacturing practices are evolving to minimize waste and optimize material use. A shift towards renewable or recyclable materials is a growing trend that aligns with global commitments to environmental stewardship.
Materials Selection
Material selection is paramount in satellite manufacturing, directly affecting satellite performance, durability, and overall mission success. The materials must be lightweight yet robust enough to withstand the extreme conditions of space travel and operation.
- Options: Common materials include aluminum for structural components, titanium for high-stress parts, and specialized composite materials that offer excellent strength-to-weight ratios.
- Considerations: Factors such as thermal stability, electromagnetic shielding, and resistance to radiation play a crucial role in decision-making. Selecting the wrong material can lead to mission failure or necessitate expensive redesigns.
Component Assembly
The component assembly process is where individual parts come together to form a complete satellite. This phase demands meticulous attention to detail because any small mistake can ripple through the system, jeopardizing the whole project.
- Techniques: Commonly utilized methods include manual assembly for intricate tasks, as well as automated systems to handle repetition-heavy work. Models and prototypes often guide this process, ensuring proper alignment and integration with existing technology.
- Tools and Equipment: Specialized fittings and fixtures help secure components during assembly. The use of advanced robotics is on the rise, speeding up production times while ensuring precision.
Integration of Systems
Integration of systems is the capstone of satellite manufacturing. It ensures that all the various subsystems—communication, propulsion, power management, and payload—interact seamlessly.
"Integration is not just a technical challenge; it's a dance of complex interactions that reflects the synergy of engineering and ingenuity."
- Framework: This involves not only putting together hardware but also incorporating software that controls satellite functions. Each subsystem must be tested for compatibility with others, contributing to the overall functionality of the satellite.
- Challenges: Integrating new technologies introduces complications. For example, as miniaturization progresses, ensuring that all components fit and function together efficiently can complicate the design.
In summary, the manufacturing processes of satellite production encapsulate a blend of artistry and precision engineering. From selecting the right materials to the intricacies of component assembly and system integration, each step is crucial to guaranteeing that the final product can operate in the unforgiving environment of space.
Quality Assurance in Satellite Manufacturing
Quality assurance serves as the backbone of satellite manufacturing, influencing everything from component durability to mission success. In the high-stakes realm of space exploration, where failures can lead to catastrophic consequences, a rigorous QA system becomes essential. This process not only ensures that each part and process meets stringent performance standards but also helps bolster stakeholder confidence in the technology being utilized.
Testing Procedures
Testing procedures are a cornerstone of the quality assurance process in satellite manufacturing. Each satellite must undergo an array of tests to assess its readiness for launch and operation in the harsh conditions of space. These tests can be broadly categorized into several types:
- Functional Testing: This evaluates whether all systems and components perform their intended functions. From communication systems to power supplies, every piece of technology is scrutinized.
- Environmental Testing: Satellites face extreme temperatures, vacuum, and radiation levels in space. As such, components should endure these conditions before launch. This includes thermal vacuum testing, vibration testing, and EMI (Electromagnetic Interference) testing.
- Integration Testing: After assembling the various components into a complete system, integration testing is performed. This ensures that all parts work together harmoniously, verifying that interfaces between systems are properly functioning.
Having robust testing procedures allows manufacturers to catch potential problems early in the satellite development process. If an issue is detected late, rectifying it can be quite costly and may lead to delays in launches.
Reliability Assessments
Reliability assessments focus on measuring how likely a satellite is to perform its mission successfully over time. A satellite's reliability is crucial, especially when it’s deployed for long-term missions like those conducted by the Hubble Space Telescope or the Mars rovers. These assessments involve:
- Failure Mode Effects Analysis (FMEA): This systematic approach identifies potential failure modes in a system and evaluates their causes and consequences to prioritize risk factors.
- Mean Time Between Failures (MTBF): This metric is used to predict the reliability of satellite components over time, helping manufacturers understand how often failures are likely to occur and when maintenance may be needed.
- Lifetime Testing: Components are subjected to accelerated aging tests, simulating the effects of prolonged exposure to space conditions to predict how long they will operate effectively.
Ensuring reliability is about minimizing risks and extending lifetimes. Without thorough assessments, satellites may succumb to unpredictable failures, jeopardizing mission objectives and financial investments.
Emerging Trends in Satellite Manufacturing
Exploring the latest trends in satellite manufacturing offers insight into how the industry is evolving to meet contemporary challenges and demands. As technology progresses, certain elements have become central to advancing satellite capabilities and efficiencies. Understanding these emerging trends is crucial for astute engagement in the field, shedding light on innovations that shape the narrative of satellite development.
Miniaturization of Satellites
CubeSats
CubeSats are a prime example of how miniaturization is reshaping the satellite landscape. These small, cube-shaped satellites often have a standardized size of 10x10x10 cm, making them highly adaptable and cost-effective. The key characteristic of CubeSats is their modular design, which allows for easier and quicker assembly. This quality renders them particularly favored for educational institutions and small businesses that may not have the extensive budgets of larger aerospace companies.
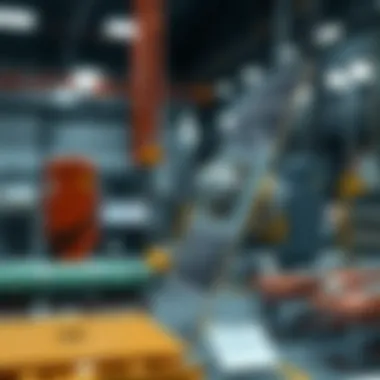
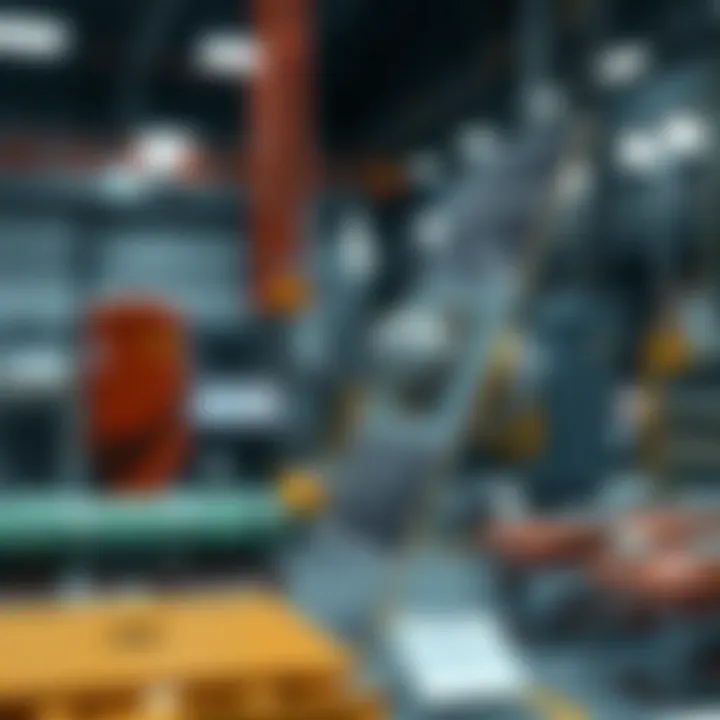
One unique feature of CubeSats is their capacity for multi-mission capabilities. They can be deployed in swarms or clusters, enabling them to carry out collaborative tasks like Earth observation or atmospheric data collection. This ability to work together showcases an advantage in data gathering, making CubeSats a strategic choice for many organizations. However, the relatively small size also poses challenges regarding payload capacity and power generation, which can limit their functionality.
Nanosatellites
Nanosatellites, typically weighing between 1 to 10 kilograms, fall in the spectrum just above CubeSats. They strike a balance between compactness and payload capacity, allowing for a diversity of missions beyond basic experiments. Their popularity stems from their versatility; they can host more complex instruments, making them suited for a broader range of applications from scientific research to commercial ventures.
A standout characteristic of nanosatellites is their robustness in handling various operational environments. They often use advanced materials and technologies to withstand the harsh conditions of space. One unique advantage is their potential for long-duration missions, giving them a greater operational lifespan compared to smaller counterparts. Nevertheless, cost and regulatory hurdles can sometimes slow down the deployment of nanosatellites in the market, underscoring the ongoing complexity in satellite manufacturing practices.
Sustainable Manufacturing Practices
Sustainability is gaining traction as a vital objective in satellite manufacturing. The focus here lies in strategies that reduce environmental impact without sacrificing performance. This includes recycling materials, optimizing resources, and exploring energy-efficient manufacturing processes. As concerns about space debris and pollution grow, the emphasis on sustainable practices has never been more pertinent. Manufacturers are now investing time and resources into research that promotes environmentally sound approaches to both the creation and operation of satellites, recognizing the shared responsibility of preserving our planet as we explore beyond it.
"The novel ideas realized by integrating sustainability in satellite production can lead to innovations that extend far beyond just the manufacturing floor."
The Role of Technology in Satellite Manufacturing
In the realm of satellite manufacturing, technology holds a pivotal role that shapes every facet of the industry. From the materials chosen to the methods of assembly, advancements in technology have paved the way for more efficient, cost-effective, and innovative solutions. This section delves into two key areas: advanced materials and technologies, and the impact of automation and robotics on the manufacturing process.
Advanced Materials and Technologies
Selecting the right materials is akin to laying a strong foundation for a house. It’s crucial not only for performance but also for longevity and adaptability in the harsh environment of space. Engineers and designers consider various factors such as weight, strength, thermal properties, and resistance to radiation when choosing materials. Here are some of the significant trends in advanced materials:
- Composite Materials: These materials, often made from carbon fibers and epoxy resin, have become increasingly popular due to their superior strength-to-weight ratio. They are lighter than traditional metals yet incredibly durable, which is essential in reducing launch costs.
- Radiation-Hardened Components: Satellites often face intense radiation, especially those operating in geostationary orbit. Utilizing radiation-hardened materials helps protect sensitive electronics, ensuring they remain functional throughout their mission life.
- Flexible Electronics: Another breakthrough is the development of flexible electronics that can be integrated into satellite surfaces. This innovation not only saves space but also allows for multifunctional capabilities such as solar energy generation.
Embracing these advanced materials and technologies not only enhances performance but also contributes to sustainability by reducing resource waste.
Automation and Robotics
Automation and robotics can be seen as the wind beneath the wings of modern satellite manufacturing. These technologies streamline processes, enhance accuracy, and drastically cut down production time. Notably, here are some key points to consider regarding automation and robotics in satellite manufacturing:
- Precision and Consistency: Machines equipped with advanced sensors and algorithms can perform tasks with a level of precision that far exceeds human capabilities. This is particularly important in tasks such as soldering, assembly, and testing of satellite components, where even the tiniest errors can lead to mission failure.
- Increased Efficiency: Robotics allow for continuous operation, meaning they can work around the clock without fatigue. This not only speeds up manufacturing timelines but also enables a more consistent output.
- Safety Improvements: By automating hazardous tasks, such as handling chemicals or performing maintenance in confined spaces, manufacturers can protect their workforce from dangerous exposures.
"The integration of robotics in satellite manufacturing is not just a trend; it’s becoming an industry standard that enhances both safety and efficiency."
Incorporating automation and robotics into the workflow fosters a smarter, safer, and more productive environment. As satellite manufacturing continues to evolve, the emphasis on technology is more critical than ever, shaping a future that promises to be both innovative and resilient.
Challenges in Satellite Manufacturing
Satellite manufacturing is a complex process fraught with challenges that can significantly impact the success of a mission. Understanding these challenges is crucial for stakeholders, including engineers, project managers, and policymakers. These hurdles are not merely obstacles; they reflect the intricate balance of technology, finance, and regulatory structures inherent in the space industry. Tacking the challenges in this area can lead to improvements not just in manufacturing but also in how satellites operate in space and how payloads are managed once deployed.
Cost Management
Creating a satellite is not a walk in the park when it comes to budgets. The costs associated with satellite manufacturing may easily spiral into billions of dollars depending on the size, complexity, and technology involved. Striking the right balance between quality and expenditure is vital, and often, compromises have to be made.
Why Cost Management Matters
Managing costs effectively ensures that projects remain feasible and sustainable. A clear understanding of where expenses arise allows companies to allocate resources wisely. Some key facets of cost management include:
- Material Costs: Selecting appropriate materials affects durability and performance, which can have long-term effects on costs. For instance, advanced composites might be pricier upfront but can save money on maintenance in the long run.
- Labor Expenses: Skilled labor is essential, and retaining qualified personnel is crucial. Companies must also consider the costs of training new workers.
- Technological Investment: Investing in cutting-edge technology can boost efficiency but requires upfront costs that need to be justified.
Projects that don't carefully consider these cost dynamics can end up stranded in the financial void. In some instances, delayed projects have resulted from unexpected expenses, forcing teams to reassess their budgets and timelines.
Regulatory Compliance
The landscape of satellite manufacturing is subject to a multitude of regulations imposed both nationally and internationally. Compliance is crucial not just for avoiding fines but for ensuring that projects can move forward without legal impediments.
The Role of Regulations in Satellite Manufacturing
There are various layers of compliance that need navigation:
- Licensing Requirements: Launching a satellite often requires several licenses from different authorities, such as the Federal Aviation Administration in the U.S. and even international bodies. Securing these can be time-consuming, impacting project timelines.
- Frequency Allocation: Satellites must operate on specific frequencies to avoid interference with other satellites or terrestrial communication. The process of frequency assignment can be competitive and complex, requiring meticulous planning.
- Sustainable Practices: With growing concerns about space debris, regulators are increasingly enforcing rules to ensure that satellites are designed with end-of-life deorbiting strategies in mind.
Collaboration in the Satellite Ecosystem
The realm of satellite manufacturing is increasingly becoming a tapestry woven with threads of collaboration. As the industry embraces advancements and faces various challenges, partnerships between government entities and commercial enterprises play a pivotal role. This synergy not only enhances innovation but also ensures that the goals of satellite production align with broader societal needs and market demands.
Governmental Partnerships
Governmental partnerships are fundamental in shaping the landscape of satellite manufacturing. These collaborations can provide substantial funding, which is critical for ambitious projects that commercial entities might find cost-prohibitive. Additionally, agencies such as NASA or the European Space Agency (ESA) offer invaluable resources, including research, technology, and expertise that may not be readily available within private sectors.
One notable example is the Artemis program, which aims to return humans to the Moon. Different countries are joining forces to leverage technical ability and budgetary allocation. As a result, nations can share data, facilities, and even satellite launches. Governmental partnerships also help in regulatory compliance, ensuring that satellites meet safety standards, which can often be a hurdle for new companies entering the market.
Collaborative projects are more likely to succeed due to shared risk and resource pooling. For instance, the International Space Station has been a successful product of international cooperation, demonstrating how pooling resources and knowledge can lead to advancements in technology.
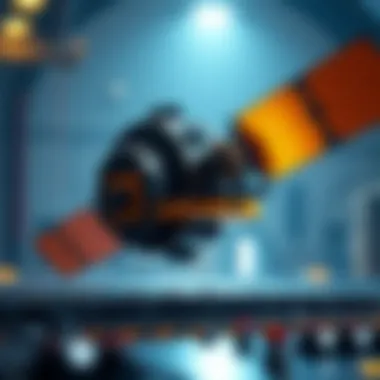
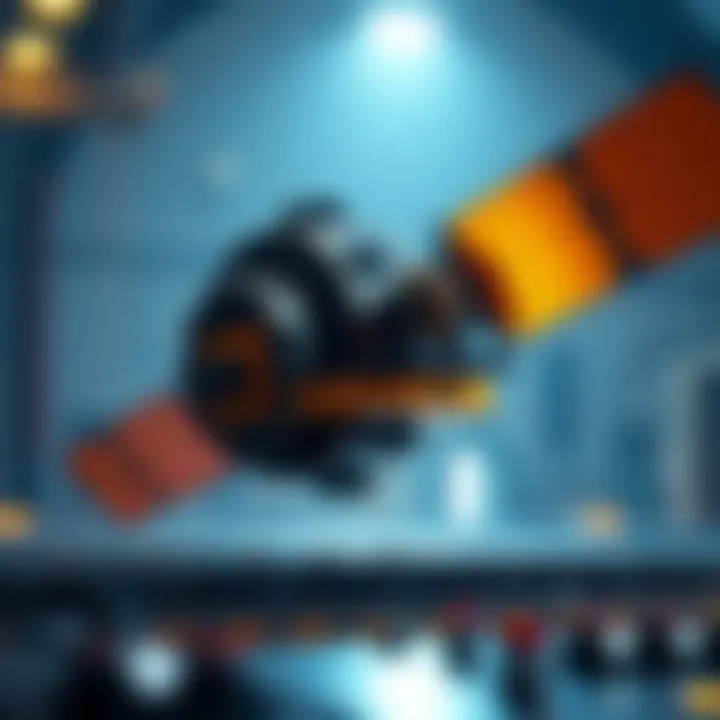
Commercial Engagements
When we turn to the commercial sector, it's clear that engagement between companies is equally crucial. Partnerships among businesses can drive down costs and stimulate innovation. By collaborating, companies can share research and development expenses. Furthermore, when smaller firms partner with larger, established corporations, they can leverage the latter's distribution channels and customer base, effectively accelerating their time to market.
A telling example is the collaboration between SpaceX and various telecommunications companies. Through these partnerships, SpaceX has been able to launch satellites more efficiently while addressing the growing demand for global internet coverage. This not only benefits the companies involved but also enhances the capacities of satellite networks to meet consumer needs.
Moreover, market trends are shifting towards a model where commercial firms look to government contracts for stability. As space-related projects become more popular, government contracts provide companies the lifeline needed for sustained growth and research, enabling them to innovate further.
“Collaboration maximizes the potential for technological breakthroughs in satellite manufacturing, bridging gaps between governmental and commercial ambitions.”
To summarize, collaboration in the satellite ecosystem—whether through governmental partnerships or commercial engagements—is integral to the advancement and sustainability of satellite manufacturing. A concerted approach will not only streamline manufacturing processes but also ensure that the resultant technologies serve humanity's interests efficiently.
Case Studies in Satellite Manufacturing
Case studies play a vital role in satellite manufacturing, showcasing real-world examples of design, engineering, and technology integration. Through analyzing specific projects, we can appreciate not only the technical feats achieved but also the lessons learned and how they shape the future of satellite production.
Understanding these case studies affords insights into the operational challenges faced, the solutions that emerged, and the innovative practices that evolved in the field. Additionally, they help to illustrate the impacts of collaboration among various stakeholders, from governmental bodies to private enterprises. In this section, notable projects and significant lessons will be discussed.
Notable Satellite Projects
A few satellite projects stand well above the rest due to their pioneering nature and impact on subsequent endeavors. One such project is the Hubble Space Telescope, launched in 1990. This marvel not only revolutionized our understanding of the universe but is also a testament to meticulous engineering and long-term collaboration between NASA and the European Space Agency. Hubble's successful deployment relied on rigorous testing protocols and advanced materials, which paved the way for more ambitious projects, like the James Webb Space Telescope.
Another project worth mentioning is Starlink, initiated by SpaceX. With a goal to provide global internet coverage, it has highlighted both the potential and challenges of deploying large constellations of satellites. Starlink's rapid deployment strategy utilizes very small satellites (V-SATs), pushing the envelope on miniaturization and operational innovation. The ongoing developments from this project not only showcase advances in satellite manufacturing but also raise crucial discussions about space traffic, regulation, and sustainability.
Moreover, the GOES-R series, which focuses on meteorological satellite services, introduces advanced sensors and a new level of data processing capabilities. It has generated significant strides in weather forecasting, disaster management, and climate monitoring, demonstrating the essential role of satellites in daily human life.
Lessons Learned
Every project carries valuable takeaways that can influence future designs. A few critical lessons emerge from the notable satellite projects mentioned above:
- Importance of Testing: Rigorously testing components and systems in space conditions is non-negotiable. For instance, Hubble's deployment troubles showcased how pre-launch simulations could potentially save time and resources by identifying issues early.
- Flexibility and Adaptation: Starlink's success stems from its ability to adapt quickly to technical challenges and regulatory requirements. This highlights that agile project management can lead to more resilient designs.
- Collaboration is Key: Successful partnerships, like those in the GOES-R series, underline that pooling resources and expertise leads to better outcomes. Engaging in cross-disciplinary collaborations oftentimes results in innovative solutions that technological silos might miss.
"Lessons learned from one project are invaluable for the next. Emphasizing adaptability, rigorous testing, and collaboration can change the game in satellite manufacturing."
In summation, analyzing these case studies elucidates the complexities and achievements in satellite manufacturing, anchoring them in real-world contexts. As the field continues to evolve, the reflections from these examples will undoubtedly guide future innovations and practices.
The Future of Satellite Manufacturing
The landscape of satellite manufacturing is evolving faster than a shooting star in the night sky. The future holds a wealth of possibilities that are set to reshape how we approach satellite design, production, and deployment. Understanding these anticipated changes is crucial for those involved in the industry, as well as for researchers and educators aiming to keep pace with technological advancements.
Predicted Trends
Emerging trends in satellite manufacturing will likely include:
- Increased Miniaturization: The trend toward smaller satellites, like CubeSats and Nanosatellites, is not just a passing phase. These diminutive devices offer cost-effective solutions with powerful capabilities. Scientists are exploring innovative ways to pack more functionality into less space, making it possible to launch larger constellations of satellites at lower costs.
- Sustainability Practices: Environmental considerations are gaining momentum. As space debris becomes a pressing issue, manufacturers are turning to eco-friendly materials and processes. Companies like Planet Labs are already focusing on sustainability in their satellite designs, using recyclable materials and optimizing energy consumption.
- Intelligent Manufacturing: The rise of AI and machine learning in production lines allows for precision akin to a surgeon's scalpel. These technologies facilitate real-time adjustments, predictive maintenance, and improve efficiency, which could lead to significant cost reductions in the manufacturing process.
- Increased Collaboration: A burgeoning trend is the collaboration between private companies and government agencies. This partnership promotes the sharing of resources and knowledge, as seen in projects like NASA’s Commercial Crew Program. Companies like SpaceX have managed to rethink old paradigms to achieve goals that were previously thought unattainable.
"Collaboration introduces a sense of shared responsibility—everyone is in it together, pushing the envelope further than we thought we could."
Long-term Visions
The long-term vision for satellite manufacturing extends beyond immediate trends to a more comprehensive outlook for the industry.
- Space-Based Internet: Companies such as Starlink by SpaceX are setting the stage for global internet connectivity via satellite. As satellite designs evolve, we can expect a more interconnected world with technology bridging the digital divide.
- Resource Utilization: There's been a buzz around the concept of mining asteroids and collecting resources that could potentially be used in space. The production of satellites that can utilize materials sourced in space may flourish, reducing the burden on Earth-based resources.
- Advanced Photonics: The integration of photonics into satellite technology could revolutionize how data is transmitted and processed. This shift will allow for faster communication channels vital for deep space exploration and Earth monitoring.
- Regulatory and Policy Framework: A structured policy landscape is necessary to manage the increase in satellite launches and operations. The future might see enhanced regulations ensuring the safety of space operations without stifling innovation.
Considering these factors, the future of satellite manufacturing not only looks promising but is also chock-full of challenges and opportunities. The interplay between technological advancements and collaborative efforts will be key in shaping the industry. As we navigate through this uncharted territory, those involved must remain adaptable, ready to pivot strategies and innovate as circumstances shift.
Closure
The conclusion of an article about satellite manufacturing stands as a pivotal section, encapsulating the crux of the extensive discussions held throughout the document. It serves not only to summarize the key findings but also to reinforce the relevance of the topic in the modern landscape of aerospace technology and its implications for future innovations.
- Importance of Conclusion
The conclusion is critical as it draws together numerous threads of discussion into a coherent tapestry. It highlights that satellite manufacturing is more than a technical endeavor; it's a collaborative effort that integrates advanced engineering, technological innovation, and sustainable practices. As the global demand for satellites continues to grow, understanding these dynamics is paramount. - Benefits and Considerations
- Understanding the lifecycle of satellite production helps professionals make informed decisions at every stage, from initial design concepts to reliability testing and final deployment.
- The exploration of challenges such as cost management and regulatory compliance equips stakeholders with the knowledge to navigate potential pitfalls, fostering an environment conducive to innovation and success.
- Focusing on future predictions and emerging trends, such as miniaturization and sustainable practices, positions companies to remain relevant in an ever-evolving market.
Thus, the conclusion functions as the final puzzle piece, emphasizing that satellite manufacturing is an intricate field influenced by historical context, technological advancements, and the pressing need for sustainable practices.
Summary of Key Findings
Throughout this article, several key findings emerged:
- Design Phases: From the initial conceptual design to the rigorous testing procedures, each phase plays a crucial role in ensuring the satellite's effectiveness and reliability.
- Manufacturing Processes: The selected materials and assembly techniques directly impact the satellite's lifespan and performance in orbit.
- Quality Assurance: Testing and assessments are vital in minimizing risk and improving long-term survivability, especially in harsh space environments.
- Emerging Trends: Miniaturization facilitates more access to space, while sustainable practices are beginning to take root in the industry.
- Collaboration: Partnerships across government and commercial sectors enhance capabilities and resources available for satellite manufacturing.
In summary, understanding these findings is essential for stakeholders aiming to influence the industry positively.
Final Thoughts
In concluding this exploration of satellite manufacturing, it’s important to reflect on the multifaceted nature of the field. As we look forward, the integration of advanced technologies and sustainable methodologies will not only enhance manufacturing processes but also ensure that the industry adapts to the evolving demands of global communication, earth observation, and exploration.
The evolving landscape of satellite manufacturing beckons for a proactive approach. Researchers, companies, and governments must remain vigilant, innovative, and open to collaboration to tackle the challenges that lie ahead. By embracing new materials, striving for sustainability, and fostering partnerships, the sector can not only meet current needs but also pioneer the future of space exploration in a way that benefits humanity as a whole.
In the world of satellite manufacturing, the readiness to adapt and innovate often defines long-lasting success.