Twin Jet Nozzles: Design, Functionality & Applications
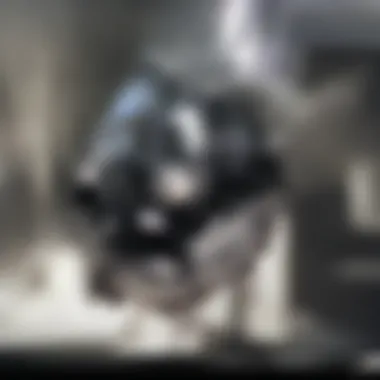
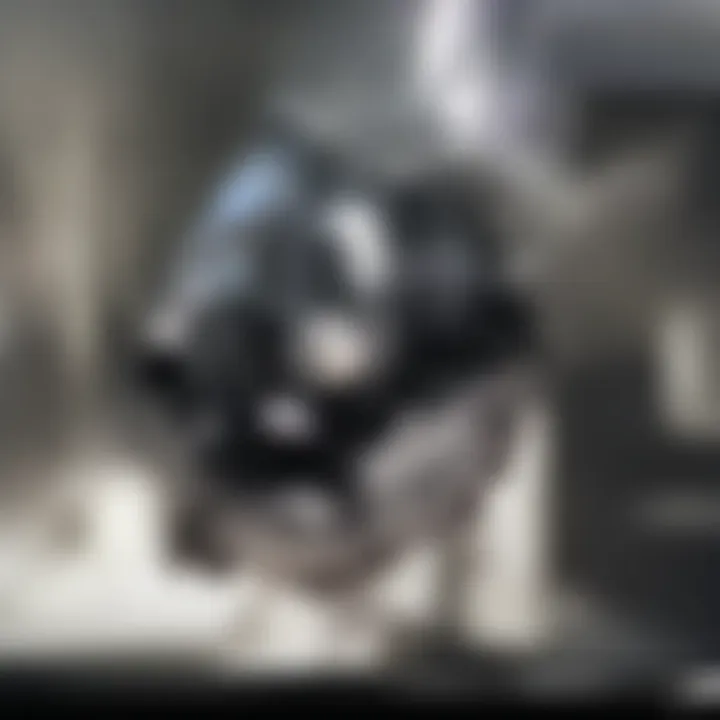
Intro
Twin jet nozzles are a pivotal component in the realm of fluid dynamics. They find their applications in multiple engineering domains. From aerospace engineering to industrial processes, understanding their design and functionality has become crucial. This article aims to peel back the layers of twin jet nozzles, exploring not only their operational principles but also their advantages over more conventional single jet systems. The discussion herein is tailored for students, researchers, educators, and professionals who seek to deepen their knowledge and application of fluid mechanics.
Research Context
Background and Rationale
In the field of fluid dynamics, efficient flow control and management are essential. Traditional single jet nozzles have served many purposes over the years, but the emergence of twin jet nozzles has prompted a shift in design philosophy. The rationale for this evolution lies in the enhanced performance metrics offered by twin jet configurations. These nozzles allow for greater thrust generation, improved mixing, and reduced drag in various applications.
The focus on twin jets arises from the need for improving efficiency in applications like propulsion systems and thermal management. Researching twin jet nozzle mechanics can yield insights that lead to superior designs and implementations. Previous works have explored the basic functionalities; however, there remains a gap in comprehensive examinations of their extended applications and nuanced design considerations.
Literature Review
A substantial body of literature exists on fluid dynamics, with twin jet nozzles receiving some attention in recent studies. Notably, various papers have outlined the fundamental physics governing nozzle behavior. Some key research includes investigations into the mixing performance of twin jets in combustion processes. Significant contributions have also been found in works exploring the effects of geometric modifications on jet interaction dynamics. The findings in these studies form a vital foundation for the further development of twin jet nozzle technologies.
However, gaps still persist in understanding the broader implications of design choices on overall performance. To bridge this gap, a more focused approach to the design and applicability of twin jet nozzles is necessary.
Methodology
Research Design
The research design revolves around a mixed-methods approach. Combining qualitative and quantitative analysis, this framework allows for a holistic view of twin jet nozzles. Understanding the principles behind their design necessitates both experimental data and theoretical context.
Data Collection Methods
Data collection involves two primary methods:
- Experimental Analysis: Conducting experiments using prototypes of twin jet nozzles in controlled settings provides real-time data on performance metrics. This includes examining flow rates, pressure drop, and mixing efficiency.
- Simulation Tools: Computational Fluid Dynamics (CFD) software assists in modeling the behavior of twin jet nozzles under various operational conditions. These simulations help predict performance outcomes without the associated costs of extensive physical experimentation.
Through these methodologies, a clearer perspective on the principles of twin jet nozzle design is expected to materialize, supporting the overall mission of this article.
Preface to Twin Jet Nozzles
The study of twin jet nozzles holds significant importance within the realms of fluid dynamics and engineering. These systems, which eject fluid in two parallel jets, offer advanced functionality and specialized applications. Understanding how they work not only improves design efficiency but also enhances performance metrics in various fields.
In many industrial processes, twin jet nozzles provide several distinct advantages over traditional single jet systems. For instance, twin jets can facilitate superior mixing, greater mass flow rates, and improved thrust capabilities in aerospace applications. They are essential in increasing the operational efficiency of combustion engines, optimizing chemical reaction rates, and enhancing fluid control.
Definition and Overview
Twin jet nozzles are devices designed to emit two separate jets of fluid, usually gas or liquid, from a common inlet. The principle behind their operation relies on the interaction between the two jets. This interaction can dramatically alter flow characteristics, ranging from turbulence to pressure distribution. Typically, they significantly improve the mixing and dispersion of fluids in various applications, which enhances overall system performance.
Key features include:
- Dual jet formation, which facilitates better mixing
- Adjustable configurations tailored for specific requirements
- Potential for reduced noise output during operation
Understanding the operational dynamics of twin jet nozzles is critical for engineers and researchers focusing on fluid mechanisms and their applications.
Historical Background
The concept of using multiple jets can be traced back to early advancements in fluid mechanics. However, the targeted design of twin jet nozzles gained traction in the mid-20th century with the emergence of aerospace technologies. The integration of these nozzles in jet propulsion systems allowed engineers to optimize performance metrics like thrust and fuel efficiency. As industries evolved, so too did the sophistication of twin jet designs.
In the 1980s, fundamental research into computational fluid dynamics enabled designers to simulate complex fluid behaviors in twin jet systems. This research has led to considerable advancements in nozzle technology, influencing various sectors such as automotive, environmental engineering, and chemical processing.
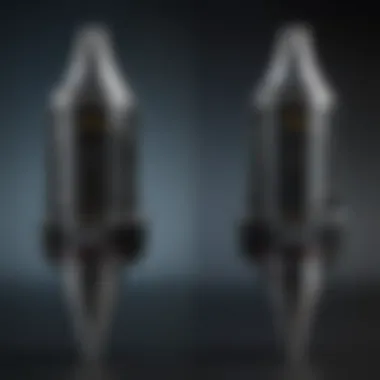
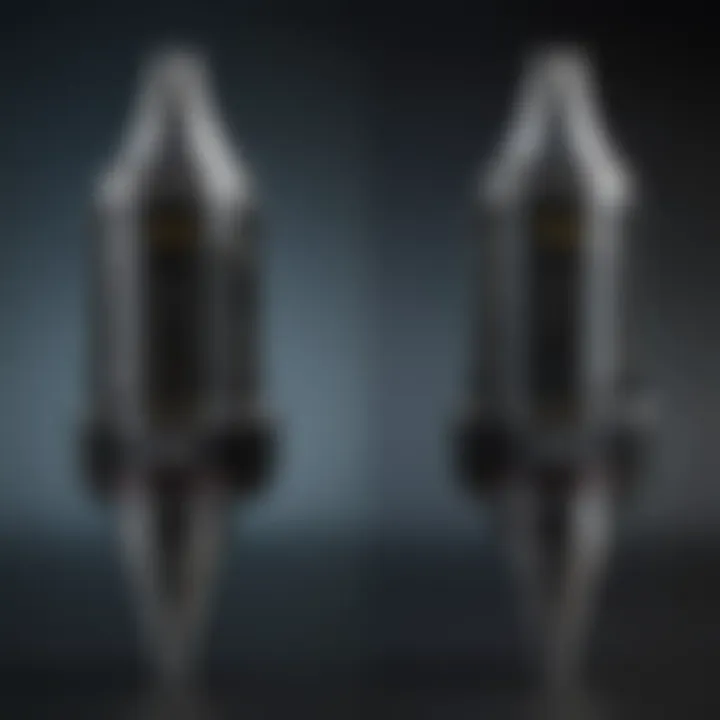
"The proper design of twin jet nozzles not only enhances performance but also ensures compliance with environmental standards."
This idea has driven innovation and focus on developing quieter and more efficient nozzle systems.
The historical developments and foundational science behind twin jet nozzles reveal their integral role in modern engineering applications, establishing themselves as a pivotal area of study in fluid dynamics.
Principles of Operation
The principles of operation for twin jet nozzles are crucial for understanding their functionalities and benefits in various applications. These principles dictate how twin jet nozzles perform, interact with fluids, and deliver efficiency in their applications. An in-depth exploration reveals the underlying mechanisms that allow for enhanced performance over traditional single jet nozzles. Understanding these principles is vital not only for designers and engineers but also for researchers who seek to innovate in this area.
Fluid Dynamics Fundamentals
Fluid dynamics is the branch of physics that studies the behavior of fluids in motion. In the context of twin jet nozzles, this refers to how the jets are formed and the interactions that occur within the fluid streams. The basic equations governing fluid dynamics, like the Navier-Stokes equations, play a significant role in predicting jet behavior. Key concepts such as velocity, pressure, and density help explain how twin jets optimize mixing and reduce turbulence when compared to other designs. Here are some pivotal points regarding fluid dynamics:
- Continuity Equation: This principle ensures mass conservation in the flow. For twin jet nozzles, maintaining a constant mass flow is key to consistent jet formation.
- Bernoulli's Principle: Explains how an increase in fluid speed leads to a drop in pressure, critical for understanding jet expansion.
- Viscosity's Role: The viscosity of fluid affects flow characteristics, impacting the efficiency and stability of the jets produced.
By exploring these fundamentals, engineers can design better twin jet nozzles, enhancing their applications.
Mechanics of Jet Formation
Understanding the mechanics of jet formation helps in elucidating how twin jets differ from their single-jet counterparts. When fluid exits a nozzle, it experiences rapid acceleration, forming a jet. In twin jet nozzles, two jets are created, often angled or positioned to optimize flow dynamics. The alignment and spacing of these jets can significantly influence performance qualities such as:
- Jet Velocity: The speed at which fluid exits impacts mixing and momentum transfer.
- Jet Spacing: Proper spacing between jets ensures efficient coalescence and prevents interference, which can degrade performance.
- Nozzle Geometry: The design and shape of the nozzle itself determine how efficiently jets are formed and maintained.
By mastering the mechanics of how jets form and interact, engineers can leverage these characteristics for specific applications.
Physics of Twin Jets
The physics behind twin jets involves understanding how they interact with their surroundings and each other. Twin jets can exhibit complex behaviors, including non-linear interactions, which may lead to beneficial outcomes such as enhanced mixing. Factors to consider include:
- Interaction Effects: The behavior of twin jets can be modified by the distance between them, creating regions of varying pressure and velocity that enhance mixing.
- Flow Separation: The occurrence of flow separation can influence the stability and efficiency of the jets produced.
- Shock Waves: In high-velocity applications, shock waves may be generated which can affect jet characteristics significantly.
Understanding these physical principles helps in tailoring twin jet nozzle designs for optimal performance across various industrial sectors.
Design Considerations
The design considerations for twin jet nozzles are paramount to their functionality and overall performance. This segment explores several aspects that must be taken into account during the design process. Understanding these facets not only ensures optimal jet performance but also significantly impacts the efficiency of the systems in which these nozzles are employed.
Geometric Configurations
Geometric configurations of twin jet nozzles play an essential role in determining their operational characteristics. The shape and size of the nozzles influence how fluid is accelerated and how jets are formed. Some common configurations include convergent, divergent, and combined shapes that are tailored to specific applications. For example, converging nozzles are typically efficient for accelerating subsonic flows, while diverging nozzles are critical when transitioning to supersonic speeds.
Tuning the geometry enables engineers to optimize the velocity profile and mixing properties of the jets. Change in angle or length can lead to different flow patterns and mixing efficiency. Moreover, the spacing between the nozzles must also be carefully considered. Close proximity may enhance mixing but could potentially lead to interference between the jets, while wider spacing could reduce the effectiveness of interaction, affecting performance.
Material Selection
Material selection for twin jet nozzles is crucial for ensuring durability and efficiency. The operating environment, including temperature, pressure, and the specific type of fluid being used, must guide this decision. Common materials include stainless steel, titanium, and various composites that withstand corrosive fluids and high pressures.
High-temperature applications might necessitate the use of heat-resistant alloys or ceramic composites. Selecting a suitable material not only improves the lifespan of the nozzle but also affects the overall performance. For instance, using lighter materials can lead to a lower weight of the nozzle assembly, enhancing ease of installation and performance metrics in aerospace applications.
Computational Fluid Dynamics Modeling
Computational fluid dynamics (CFD) modeling has become an indispensable tool in the design process of twin jet nozzles. Through CFD simulations, engineers can visualize how fluids behave around the nozzle structures under various operating conditions. This technology provides insights into pressure distributions, velocity fields, and potential areas of turbulence.
By utilizing CFD models, designers can iterate on different geometric configurations and material choices before physical prototyping. This not only saves time but also significantly reduces costs associated with material wastage and experimental trials. The ability to predict flow behavior can lead to the optimization of nozzle designs and enhance performance metrics across different applications. Moreover, integrating CFD in early design stages helps in identifying potential challenges and reliability issues, ensuring that end products meet specified requirements.
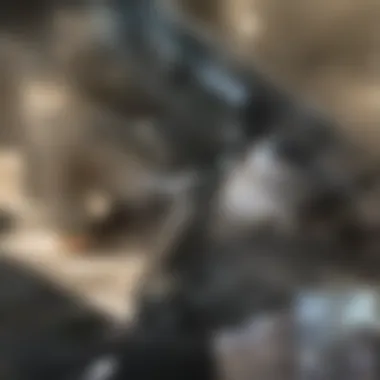
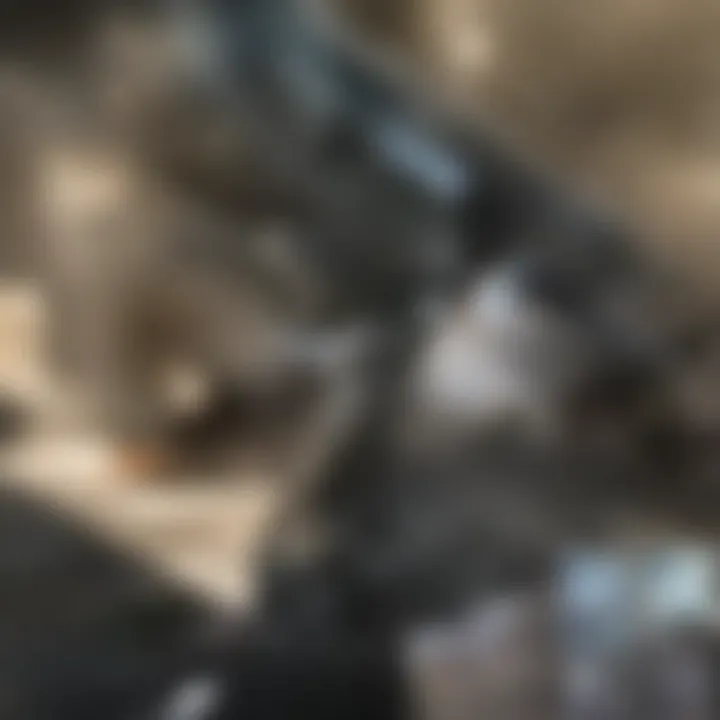
The combination of thoughtful geometric design, appropriate material selection, and advanced computational modeling is critical to the success of twin jet nozzle technologies.
Advantages of Twin Jet Systems
Twin jet systems are reknowned for their several advantages compared to traditional single jet configurations. Their design can greatly improve performance in various engineering applications. In this section, we will cover increased efficiency, enhanced mixing capabilities, and reduced noise levels, showcasing the benefits that these systems present.
Increased Efficiency
Twunj Jet systems significantly increase efficiency over conventional designs. This can be attributed to their superior fluid dynamics, which allow for better energy distribution. The twin jet design helps in optimizing thrust and ensuring that the jet streams work collaboratively. This cooperative action results in a more effective momentum transfer. It minimizes energy losses, leading to a reduction in fuel or power consumption in various applications.
Furthermore, the symmetry of twin jets balances forces on the system, allowing for smoother operation. When utilized in aeronautics or automotive applications, this can translate into lower operational costs and improved performance metrics. Research has shown that twin jet nozzles can yield performance gains of 10% or more under certain conditions.
Enhanced Mixing
The mixing efficiency of twin jet systems proves to be superior due to the interaction of two co-flowing streams. This configuration promotes turbulence between the jets, facilitating a rapid and more uniform mixing of fluids or gases. Industries that rely on precise blending of materials find these designs particularly advantageous. For example, in chemical processing, enhanced mixing considerably impacts reaction rates, resulting in better product yield and consistency.
The design is especially beneficial when different temperature fluids must be mixed. The turbulence created by the twin jets can ensure uniform heat transfer and minimize thermal gradients. This can lead to improved process control and energy utilization in many applications.
Reduced Noise Levels
One notable advantage of twin jet systems is their potential for reduced noise emissions. The dual-jet action often results in lower sound levels compared to single jet systems. This notable feature is critical in applications like aviation, where noise regulations are stringent. By carefully designing the nozzle and optimizing the flow rates, significant noise reduction can be achieved.
Moreover, the configuration allows for noise suppression strategies, such as using acoustic liners or optimizing jet spacing. These methods can be tailored to specific operational needs, improving not just performance but also aligning with environmental standards.
"The considerations of noise reduction in twin jet systems lead both to regulatory compliance and improved user experience in various industries."
Applications in Various Industries
The versatility of twin jet nozzles makes them invaluable across various industries. Their unique design and operational capabilities allow for enhanced performance in numerous applications. Each sector benefits from the specific advantages that twin jet systems provide, from increased efficiency to improved mixing. Understanding these applications is crucial for professionals and researchers who seek to leverage fluid dynamics in innovative ways.
Aerospace Engineering
In aerospace engineering, twin jet nozzles play a vital role in propulsion systems. They are utilized in both commercial and military aircraft. The twin jet configuration can improve thrust levels while maintaining efficient fuel consumption. Moreover, these systems are designed to reduce noise emissions, which is a significant consideration in aviation. This reduction in noise enhances passenger comfort as well as meeting regulatory standards.
One key aspect is the development of thrust vectoring capabilities, which improves maneuverability in fighters and drones. This level of precision in jet formation is paramount for missions demanding high agility. With the implementation of computational fluid dynamics, designers can simulate various scenarios, optimizing nozzle design before production.
Automotive Sector
In the automotive field, twin jet nozzles are increasingly utilized in fuel injection systems. By providing improved atomization of fuel, these nozzles enhance combustion efficiency. This translates into lower emissions and better fuel economy—two critical performance metrics in today's automotive industry.
Furthermore, the advancement in twin nozzles also allows for precise control over fuel delivery. This is beneficial for both conventional internal combustion engines and emerging hybrid technologies. Engineers can leverage these benefits to create cleaner, more efficient vehicles that meet stringent emission standards.
Chemical Processing
Twin jet nozzles are instrumental in chemical processing applications, where mixing different substances efficiently is critical. Their design allows for enhanced mixing patterns in reactors, leading to improved reaction rates. This, in turn, can reduce processing times and costs.
Moreover, in processes such as spray drying or atomization, twin jets enable finer particle sizes of produced materials. This is especially relevant in pharmaceuticals, where precise formulations are pivotal. Adaptations of twin jet nozzles also allow for varying pressure conditions, contributing to versatility across different processes.
Environmental Engineering
In environmental engineering, twin jet nozzles are used primarily in water treatment and air pollution control systems. Their ability to enhance mixing allows for better dispersal of chemicals in water treatment plants. This leads to improved efficiency in contaminant removal.
Additionally, in air scrubbers, twin jet systems help in capturing pollutants more effectively. The enhanced jet formation helps in achieving the necessary contact surface area between the pollutant and cleaning agents. In this way, industries can fulfill environmental regulations while promoting sustainability.
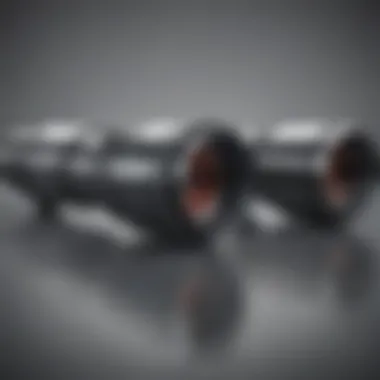
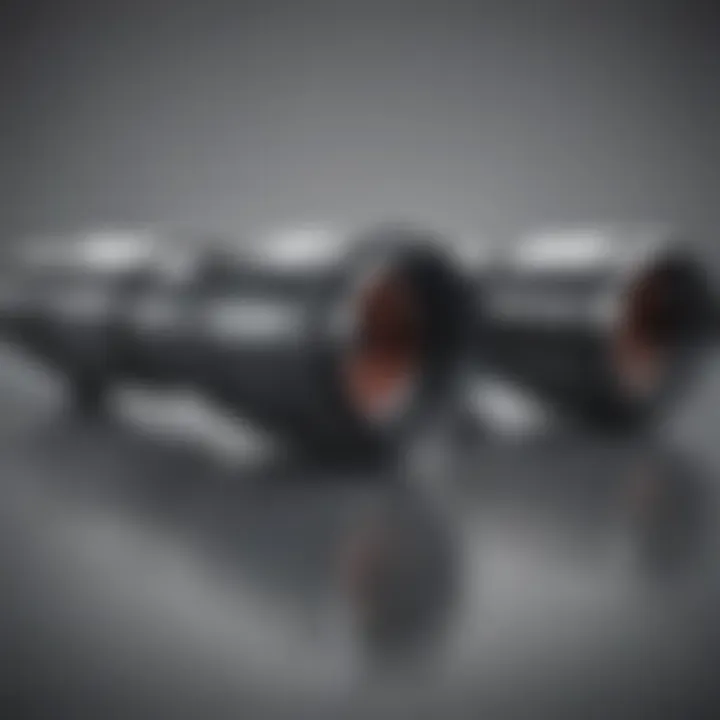
"Twin jet nozzles support a range of industries due to their adaptability and efficiency in various applications."
Understanding the diverse uses of twin jet nozzles across these industries highlights their importance. It drives innovation and progress while also addressing contemporary challenges. The potential for future developments in this technology is vast, promising additional efficiencies and enhancements ahead.
Challenges and Limitations
Understanding the challenges and limitations of twin jet nozzles is crucial for engineers and researchers engaged in fluid dynamics. These nozzles are often viewed as superior to single jet systems, yet they come with their own intricacies. Grasping these challenges allows for better design decisions and optimizes efficiency in various applications. This section looks at two main areas: manufacturing complexities and performance under variable conditions.
Manufacturing Complexities
The manufacturing of twin jet nozzles involves several sophisticated processes that can introduce significant complexities. For instance, the requirement for precise geometrical configurations demands high tolerances in production. Manufacturing techniques must account for the intricate designs, which often incorporate advanced materials and special coatings.
Precision engineering is vital here. The alignment of the nozzles must be perfect to achieve the desired performance. Misalignment can lead to uneven jet formation, which can negatively impact mixing and velocity profiles. Furthermore, the production processes, such as additive manufacturing or CNC machining, can require specialized expertise and equipment, increasing the cost and time needed to produce these nozzles.
"The precision required in manufacturing twin jet nozzles defines not only their functionality but also their applicability across industries."
Moreover, repeatability in manufacturing is essential to maintain quality across batches. Variability can make it hard to predict how each nozzle will perform under operational conditions. As a result, the industry needs to adapt its quality control measures to accommodate these complexities.
Performance Under Variable Conditions
Twin jet nozzles are designed for high efficiency, but their performance can be sensitive to changes in operational conditions. Factors such as temperature, pressure, and fluid properties can significantly influence their behavior.
For example, fluctuations in temperature can modify fluid viscosity, thereby affecting flow rates. If the material composition of the fluid changes, say from a liquid to a gas, it disrupts the coherent jet formation expected from twin nozzles. In some cases, environmental factors can lead to cavitation, which can cause erosion over time and decrease performance.
Designing for variable conditions requires an understanding of how these elements interact with jet dynamics. Engineers often apply computational fluid dynamics (CFD) to model these scenarios. This simulation helps predict performance across a range of conditions, but it also adds another layer of complexity during the design phase.
In essence, while twin jet nozzles have advantages over their single-jet counterparts, acknowledging their challenges enhances their application in various fields. Identifying areas of concern enables continual refinement, promoting innovations that can lead to more robust designs.
Future Developments in Twin Jet Nozzle Technology
The domain of twin jet nozzles continues to evolve. Future developments are essential in enhancing their efficiency and effectiveness across multiple applications. As industries demand greater performance and sustainability, innovation in design and materials will become increasingly critical. Engineers and researchers need to prioritize advancements in these areas.
Innovations in Design and Materials
Innovations in both design and materials can significantly impact the performance of twin jet nozzles.
Key areas of focus include:
- Additive Manufacturing: This technique allows for creating complex geometries that are often impossible to produce using traditional methods. By integrating additive manufacturing, designers can optimize the flow dynamics within the nozzle, enhancing performance and efficiency.
- Advanced Materials: The exploration of composite materials or lightweight alloys can lead to greater durability and resistance to various environments, whether they are high temperatures in aerospace settings or corrosive atmospheres in chemical processing.
- Smart Technologies: The adoption of sensor technology within nozzle designs can enable real-time monitoring of performance metrics. This data can assist in the optimization of fluid dynamics and reveal opportunities for further enhancements.
- Multifunctional Designs: Future designs will likely incorporate multiple functionalities, allowing for applications beyond the traditional uses of twin jet nozzles. This could include integrating mixing capabilities, allowing for better control of fluid dispersal in automotive or chemical applications.
"The future of twin jet nozzle technology relies heavily on integrating novel materials and advanced design principles to address modern engineering challenges and requirements."
The exploration of these advancements will not only enhance performance but also contribute to developing more sustainable engineering practices. As this field grows, collaboration between academia and industry will play a vital role in bringing these innovations to fruition. Engaging in these discussions within platforms like reddit.com can garner insights from a wider audience, promoting knowledge exchange.
End
The conclusion of this article encapsulates the multifaceted aspects of twin jet nozzles and their implications in various fields. This final section synthesizes the vital points discussed throughout the text, emphasizing the relevance of understanding the twin jet design and functionality. In the evolving landscape of engineering and technology, twin jet nozzles present several benefits that are worthy of consideration.
One significant aspect is their efficiency. Twin jet systems deliver enhanced mixing and improved aerodynamic performance compared to traditional single jet configurations. This translates directly into better resource utilization in applications such as aerospace and automotive engineering. The reduced noise levels associated with twin jets also contribute to more sustainable designs, highlighting their role in environmental considerations.
Moreover, the article has pointed out the diverse applications across industries, showcasing the versatility of twin jet technology. Engineers and researchers can leverage insights into design considerations and operational principles to drive innovation in their respective fields.
Adopting advancements in materials and computational fluid dynamics can lead to future developments that will push the boundaries of what is currently achievable with jet nozzle technology. Therefore, continuous exploration in this domain is not just beneficial but essential for maintaining competitiveness in various sectors.
In summary, recognizing the capabilities and applications of twin jet nozzles adds valuable knowledge for students, researchers, educators, and professionals involved in fluid dynamics. The exploration of design, functionality, and application has revealed a noteworthy area of study that will undoubtedly develop further in upcoming years.
Summary of Key Points
- Definition and significance: Twin jet nozzles are designed to optimize fluid dynamics through dual jet formation.
- Advantages: These systems enhance mixing efficiency, reduce noise levels, and improve aerodynamic performance.
- Applications: Relevant in aerospace engineering, automotive, chemical processing, and environmental engineering.
- Challenges: Manufacturing complexities and varying operational conditions need to be addressed for effective implementation.
- Future Developments: Innovations in design and material science hold promise for advancing twin jet technology.