Understanding All Thread Fasteners: Comprehensive Insights
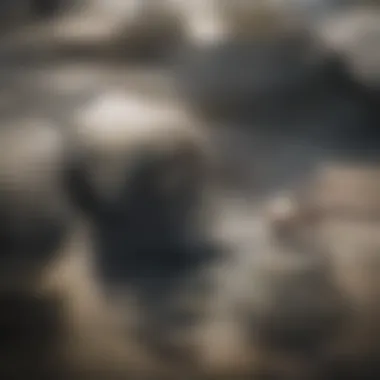

Intro
All thread fasteners play a crucial role in various sectors like engineering, construction, and manufacturing. These fasteners are designed to facilitate secure connections, ensuring the stability and integrity of structures and devices. Understanding their significance involves examining their characteristics, applications, and the standards governing their use.
However, the terminology and intricacies of all thread fasteners can be confusing. Their availability in different types and materials adds to this complexity. To make informed decisions regarding their selection and application, it is vital to consider several factors, including the specific requirements of a project, material compatibility, and installation methods.
Through this exploration, we aim to clarify these aspects. By providing comprehensive insights and practical information, this article serves as a resource for students, researchers, educators, and professionals.
Research Context
Background and Rationale
All thread fasteners, often known as fully threaded bolts or studs, have been a component of engineering for many decades. Their applications range from simple mechanical assemblies to complex structural applications. The need for reliable fastening methods has evolved with advancing technology and construction practices. In a global market, understanding the specifications and standards for these fastening systems has become increasingly important.
A detailed investigation of all thread fasteners can aid in recognizing their design efficiency. This understanding helps engineers and manufacturers optimize products and facilitate robust connections.
Literature Review
Existing literature provides valuable insights into the mechanical properties and performance of all thread fasteners. Studies highlight how factors like thread design influence fastening efficiency, while standards organizations outline specifications that ensure quality and consistency. By synthesizing current knowledge and practices, this article aims to fill knowledge gaps and provide clearer guidance.
This involves exploring the implications of material composition, thread geometry, and manufacturing processes in relation to the performance and durability of these fasteners.
Methodology
Research Design
To develop a comprehensive overview of all thread fasteners, this article synthesizes existing research, technical specifications, and industry standards. By analyzing case studies and established practices, it identifies key variables that affect the performance of all thread fasteners in real-world applications.
Data Collection Methods
Information for this article is drawn from various credible sources including academic journals, industry publications, and technical manuals. By organizing this data effectively, readers can find practical insights into the intricacies of all thread fasteners. Academic sources, like those available on Wikipedia and Britannica, contributed to the foundational understanding, while industry standards available through technical organizations provided a framework for best practices.
Preamble to All Thread Fasteners
All thread fasteners represent an essential category of mechanical components used in various constructions and applications. Understanding their nuances and applications is crucial for professionals in fields such as engineering, manufacturing, and construction. These fasteners offer versatility that makes them indispensable when securing or assembling materials. This section aims to lay the groundwork for the article by defining what all thread fasteners are, their significance in the industry, and providing a glimpse into their historical development.
Definition and Importance
All thread fasteners are characterized by a continuous threaded rod, which runs its entire length. They are used in numerous applications to join components together firmly. Their importance stems from their ability to bear heavy loads while providing necessary tensile strength. This makes them suitable for various uses, from simple household projects to complex industrial applications.
The utility of all thread fasteners can be observed in many real-world examples, such as the construction of buildings where they are often used to attach wall studs to concrete slabs or wood. Their design allows for minimal use of additional hardware, thus streamlining the assembly process. Furthermore, they can be cut to required lengths, allowing for customized solutions tailored to specific project needs.
Historical Context
To truly appreciate all thread fasteners, it is helpful to understand their evolution. The concept of threaded fasteners dates back thousands of years, with evidence found in ancient Greek and Roman engineering. These early versions employed simple threads carved into wood or metal. As mechanization progressed, the Industrial Revolution led to more standardized manufacturing processes. This resulted in the mass production of threaded rods and their variants, ultimately giving rise to the modern all thread fasteners we see today.
In contemporary applications, advancements in manufacturing technologies have enabled improved precision in thread designs. This ensures higher durability and performance in fasteners, reflecting increased demands in engineering standards and specifications. The ongoing research in materials science also plays a crucial role in the refinement of all thread fasteners, allowing for innovations that cater to specific industries.
"The integration of precise engineering and innovative manufacturing processes has elevated all thread fasteners to vital components across technological fields."
Types of All Thread Fasteners
Understanding the various types of all thread fasteners is vital as it enhances one’s ability to select the most appropriate solution for specific applications. Each type has unique characteristics, benefits, and assembly considerations. This section provides insights into three key categories of all thread fasteners: standard all thread rods, specialty threading options, and custom fastening solutions. Knowing these distinctions helps engineers and contractors make informed decisions, optimizing performance in their respective fields.
Standard All Thread Rods
Standard all thread rods are straight, cylindrical steel rods with threading along their entire length. They are commonly used in many applications because they provide versatility and strength. Typically fabricated from low or high carbon steel, these rods can be cold drawn or hot rolled.
Key advantages of standard all thread rods include:
- Availability in various diameters and lengths
- Compatibility with standard nuts and washers
- Ease of installation
- Cost-effectiveness for bulk projects
Standard all thread rods find wide usage in construction, where they hold structures together and provide critical load-bearing capabilities. Whether in bridges, high rises, or industrial buildings, their role is significant. Additionally, they are used in home improvement projects and similar endeavors, where sturdy and reliable fastening is essential.
Specialty Threading Options
Specialty threading options refer to all thread fasteners with threads designed for specific applications or environments. These may include different thread profiles like trapezoidal or acme threads, which provide unique load-bearing capabilities. The threads may also have finishes that resist corrosion or wear, such as zinc plating or black oxide treatment.
Some common specialty threading types are:
- Fine threads that offer increased tension load capacity
- Left-hand threads, which are used in applications where standard fastening may loosen
- Threaded rods with custom pitches tailored for unique machinery
Using specialty threading can enhance the longevity and efficiency of a fastening system. They are often utilized in automotive parts, high-pressure industrial environments, and other niches where standard threads may not perform adequately.
Custom Fastening Solutions
Custom fastening solutions involve designing and manufacturing all thread fasteners tailored specifically to meet client requirements. Custom solutions address unique challenges, such as unusual load specifications, environmental conditions, or specific dimensional constraints.
The customization can range from modifications in materials to alterations in thread types or lengths.
Benefits of custom fastening solutions include:
- Improved performance in unique applications
- Enhanced strength and reliability
- Potential for reduced assembly time due to tailored design
These solutions are often deployed in specialized manufacturing processes, aerospace applications, and other high-stakes environments that demand precision and reliability. Working with a manufacturer for custom solutions allows companies to ensure their specific needs are met adequately.
In summary, an understanding of the different types of all thread fasteners fuels better application in engineering and construction. Each type serves distinct purposes, optimizing performance in various environments.
Materials Used in All Thread Fasteners
Understanding the materials that constitute all thread fasteners is crucial to appreciating their functionality and durability. Different materials offer various advantages and drawbacks, impacting their performance in specific applications. The choice of material affects not only strength but also resistance to environmental factors like corrosion and temperature variations. Thus, the selection of materials must align with the intended application to ensure reliability and safety.
Metal Alloys
Metal alloys are frequently used in all thread fasteners due to their outstanding mechanical properties. Commonly employed alloys include carbon steel, stainless steel, and alloy steel. Each variant presents specific characteristics suited for particular conditions.
- Carbon Steel: Known for its high tensile strength, carbon steel fasteners are cost-effective and widely used in general construction and manufacturing. However, they are susceptible to rust, making protective coatings necessary in outdoor applications.
- Stainless Steel: This alloy combines iron with chromium and nickel, granting it excellent corrosion resistance. Stainless steel is ideal for environments exposed to moisture and chemicals, commonly used in marine, automotive, and aerospace applications.
- Alloy Steel: Alloy steels include additional elements such as molybdenum and vanadium, altering their properties for enhanced toughness and wear resistance. They are frequently applied in heavy-duty environments, like machinery and structural components.
The right metal alloy can significantly contribute to the fastener's lifespan and reliability. Thus, understanding alloy properties is vital when selecting components for specific uses.
Non-Metallic Materials
In specific circumstances, non-metallic materials are increasingly popular in manufacturing all thread fasteners. These materials offer unique benefits that metal alloys may not provide.
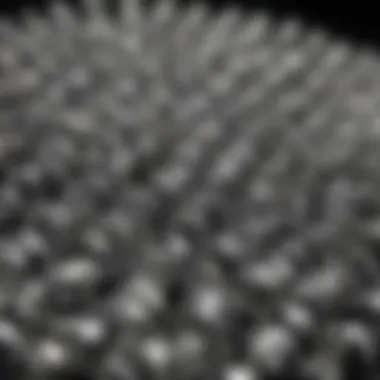

- Plastics: Synthetic options, such as nylon or polycarbonate, are lightweight and resistant to corrosion. They are used where electrical insulation is important, and weight reduction is necessary, like in electronics or automotive parts.
- Composites: Combining materials such as fibers with plastic resins, composites provide enhanced strength-to-weight ratios. They are tailored for specific applications requiring high performance without the added weight of metals.
- Ceramics: Though less common, ceramics can be used in specialized conditions, particularly where extreme temperatures are involved. Their excellent thermal stability makes them suitable for high-heat applications.
Incorporating non-metallic materials in all thread fasteners opens up possibilities in industries focused on reducing weight or enhancing insulation.
"Material selection in fastener design can dramatically impact performance and longevity, underscoring the need for meticulous analysis of application requirements."
Choosing the appropriate materials for all thread fasteners is not just a matter of preference but a critical aspect that impacts safety, reliability, and overall project success. It is essential to thoroughly evaluate the environment in which the fasteners will be used, ensuring compatibility and performance reliability.
Manufacturing Processes
The manufacturing processes for all thread fasteners play a critical role in determining their quality, performance, and reliability. It is essential to understand these processes because they directly impact the durability of the fasteners and their suitability for various applications. By comprehensively analyzing these manufacturing techniques, professionals can make informed decisions about the types of all thread fasteners to use.
Cold Forming Techniques
Cold forming is a crucial method used in the production of all thread fasteners. This technique involves shaping the metal at room temperature, which avoids the thermal stresses associated with heating processes. It offers several advantages:
- Enhanced Strength: Cold forming enhances the material's strength by increasing its density. The process causes the metal's grain structure to align, resulting in a stronger product.
- Material Efficiency: This method helps in reducing waste as it uses nearly the entire volume of material to create the fasteners.
- Cost-Effectiveness: Cold forming typically requires less energy compared to hot forging, resulting in lower production costs.
However, there are challenges to consider with cold forming, such as the need for precise tool design and die adjustments to prevent defects in the fasteners. The choice of method impacts the final product’s attributes significantly.
Machining Processes
Machining processes complement cold forming by allowing for precision manufacturing of all thread fasteners. After initial forming, the fasteners often undergo machining to achieve tighter tolerances, complex shapes, and finer details. Common machining operations include:
- Turning: This involves rotating the fastener against a cutting tool to remove excess material, shaping it into the desired dimensions.
- Milling: This process uses rotary cutters to remove material from the workpiece, creating intricate designs and features.
- Drilling: Drilling involves creating cylindrical holes in the fasteners for applications where threading is required.
These operations provide flexibility in design and precision. However, they can also introduce production costs and time. It is essential to balance the complexity of the machining process with the benefits it brings to the final product.
Heat Treatment Considerations
Heat treatment is another vital step in the manufacturing of all thread fasteners. It affects the physical properties of the fasteners, enhancing their performance in various applications. Common heat treatment processes include:
- Annealing: This process reduces hardness and enhances ductility, making the material easier to shape or cut.
- Quenching and Tempering: Quenching involves rapidly cooling the heated metal, increasing hardness. Tempering follows to reduce brittleness, ensuring the fastener can withstand operational stresses without failing.
Effective heat treatment not only improves strength and durability but also makes all thread fasteners resistant to wear and fatigue. It is critical to follow specific heat treatment protocols tailored to the material and application in question.
Appropriate selection of manufacturing processes enhances the performance and reliability of all thread fasteners, leading to increased safety and efficiency in their applications.
Thread Design and Its Implications
Thread design plays a crucial role in the performance and utility of all thread fasteners. It encompasses various aspects such as the type of thread profile, pitch, and whether the thread is right-handed or left-handed. Each of these elements can significantly influence how a fastener interacts within the assembly, impacting load distribution, ease of installation, and overall stability. Understanding these factors is essential not only for effective use but also for achieving long-term reliability in applications.
Types of Thread Profiles
There are several thread profiles used in all thread fasteners, including but not limited to, triangular, square, and rounded shapes. Each type of thread profile has its specific applications:
- Triangular Threads: This is the most common type, often found in standard screws and bolts. The sharp angles provide good engagement and resistance to stripping under load.
- Square Threads: These offer a larger surface area for load distribution, making them ideal for heavy-duty applications. They are often found in lead screws and other mechanisms where high torque is needed.
- Rounded Threads: These are less common but can be beneficial in reducing wear and tear, especially in dynamic applications.
When selecting a thread profile, one must consider the specific forces that will act on the fastener during its service life.
Pitch Considerations
The pitch of a thread refers to the distance between adjacent threads. It can influence the strength and engagement of the fasteners. A finer pitch allows for more precise adjustment but can be less robust under heavy loads. Conversely, a coarser pitch may provide better strength but could compromise the adjustability of a connection.
Considerations include:
- Load Requirements: Assessing how much weight the fastener needs to support helps determine the appropriate pitch.
- Adjustment Needs: In applications where adjustments are frequent, a finer pitch could be preferable.
- Compatibility: Ensuring that the pitch matches with corresponding nuts or tapped holes is crucial for installation success.
Right-Hand vs. Left-Hand Threads
Fasteners can feature either right-hand or left-hand threads. Right-hand threads are the conventional choice, used in most applications where the fastener is tightened by turning it clockwise. However, left-hand threads have specialized applications, including:
- Rotating Applications: In devices where rotational forces may loosen standard threads, left-hand threads offer a viable alternative.
- Specific Machinery: Some equipment, like certain types of valve systems, require left-hand threads to function correctly.
Choosing the correct direction of the thread is vital not only for the efficiency of the assembly but also for safety and performance.
"Understanding thread design is key to ensuring proper fastener function and longevity in your projects."
By carefully considering these thread design elements, professionals can enhance the performance and reliability of all thread fasteners in various applications. The right choices lead to not only effective installations but also durable connections that withstand the test of time.
Applications of All Thread Fasteners
All thread fasteners play a crucial role in numerous industries, reflecting their versatility and essential function within various applications. The importance of understanding these applications lies not just in recognizing the specific instances where all thread fasteners are utilized, but also in comprehending the broader implications of their use. By examining these different applications, professionals can assess efficiency, safety, and reliability across various fields. This section will explore three primary sectors: construction, automotive, and aerospace, highlighting the benefits and considerations of each.
Construction Industry Uses
In the construction industry, all thread fasteners are integral components that facilitate the assembly and stability of structures. These fasteners are often used in applications such as:
- Anchoring: They provide strong support for structures by securing them to concrete or masonry.
- Suspension: All thread rods hold suspended ceilings, HVAC systems, and other elements in place.
- Reinforcement: These fasteners add strength to concrete, enabling the safe transfer of loads across various components.
Their ability to withstand heavy loads and resist deformation makes them essential for construction safety and integrity. Additionally, the ease of customization allows for specific designs tailored to unique project needs. However, considerations like corrosion resistance and proper torque specifications must be made during installation to ensure longevity.
Automotive Applications
In the automotive industry, all thread fasteners are employed in various applications, ensuring safety and performance in vehicles. Common uses include:
- Suspension systems: These fasteners help secure components that provide stability and safety during operation.
- Engine assembly: All thread rods maintain crucial connections between engine parts and ensure efficient performance.
- Chassis connections: They play a vital role in the structural integrity of vehicles, contributing to overall safety.
The demand for precision in manufacturing automotive components makes all thread fasteners indispensable. Their reliability and strength directly affect vehicle longevity and operation. It’s worth noting that proper selection according to load specifications and environmental factors is vital for optimal performance.
Aerospace and Defense
The aerospace and defense industries utilize all thread fasteners in critical applications where performance and safety are non-negotiable. Key areas of use include:
- Aircraft assembly: Fasteners hold together various components in airframes, ensuring structural integrity during flight.
- Military equipment: Applications in defense systems, where vibrations and extreme conditions are common, highlight the need for durability.
- Satellite construction: Precision in fastening is crucial to withstand the harsh environment of space.
The strict regulations governing these industries demand adherence to rigorous standards and specifications, thus emphasizing the importance of understanding both the thread design and materials used. Ensuring corrosion resistance and securing proper torque is essential for the success of any aerospace application.
Fasteners are not just components; they are the connectors of safety, ensuring that structures hold and perform as expected in their environments.
Understanding the applications of all thread fasteners enhances the broader comprehension of their qualities and requirements. The insights gained from examining these sectors provide professionals with the knowledge to make informed decisions when selecting and implementing fastener solutions.
Standards and Regulations


Understanding the standards and regulations relevant to all thread fasteners is crucial for ensuring safety, performance, and compliance within various industries. These standards serve as benchmarks for quality control and help manufacturers and users alike adhere to recognized practices. Regulations can help mitigate risks associated with product failure, thus enhancing user trust and operational reliability.
Primarily, these standards inform the manufacturing processes, testing procedures, and compliance metrics necessary for all thread fasteners. Compliance with established norms ensures uniformity in dimensions, strength characteristics, and safety measures. This reduces the risk of defects, thereby lowering the likelihood of operational failures in critical applications.
Furthermore, a deep understanding of these standards allows professionals to select appropriate fasteners tailored to specific needs and conditions. For engineers, procurement teams, and quality assurance professionals, being familiar with the relevant regulations aids in decision-making and enhances overall project efficiency. It can also streamline the process of inspections and certifications, saving time and resources.
Detailed knowledge of standards allows organizations to maintain their competitive edge in a global market increasingly driven by demands for quality and reliability.
ISO Standards on Fasteners
ISO (International Organization for Standardization) standards provide universal guidelines aimed at ensuring the quality and safety of fasteners, including all thread variants. For instance, ISO 898 covers mechanical properties of fasteners with specified property classes. This international standard specifies the requirements for bolts, screws, and nuts used in engineering applications, ensuring they can withstand specific loads under varied conditions.
In essence, adherence to ISO standards translates to:
- Enhanced reliability of fasteners
- Reduced uncertainty in international trade
- Streamlined communication across technical specifications
By utilizing ISO standards, companies can demonstrate their commitment to quality and safety to clients and stakeholders. It is also significant for exporters, as compliance with these internationally recognized standards facilitates entry into global markets.
ASTM Specifications
ASTM International (formerly known as the American Society for Testing and Materials) sets comprehensive materials standards including those specific to fasteners. ASTM standards address critical aspects such as mechanical properties, testing methods, and product classifications. For example, ASTM F1554 details specifications for anchor bolts, which directly relate to all thread fasteners used in concrete and other structural applications.
By following ASTM specifications, manufacturers ensure that their products meet critical performance benchmarks. Key benefits include:
- Assured performance through rigorous testing and validation
- Consistency in quality across varied manufacturing lots
- Easier legal compliance in respective jurisdictions
These standards impact quality control processes and influence procurement decisions within industries such as construction, automotive, and aerospace.
Best Practices for Selection
Selecting the right all thread fasteners is crucial for ensuring structural integrity and functionality in various applications. This section elucidates the best practices that professionals should consider when making selection decisions. The discussion is centered on several key elements, including load calculations, environmental considerations, and corrosion resistance factors.
Load Calculations
Load calculations are fundamental to selecting all thread fasteners. They involve determining the forces that will act on the fasteners in service. Engineers must assess both static and dynamic loads to ensure that the selected fasteners can handle the required stress without failure. Often, manufacturers provide load limits for their fasteners, which can serve as guidelines.
When performing load calculations, it is essential to consider:
- The type of load: tensile, shear, or lateral.
- The safety factor: this is a margin of safety added to the calculated loads, typically ranging from 1.5 to 3, depending on application and industry standards.
- The materials involved: different materials have different strength profiles.
Utilizing the appropriate equations ensures that the selected fasteners meet both performance and safety criteria in the intended application.
Environmental Considerations
Environmental conditions play a significant role in the selection of all thread fasteners. Factors such as temperature, humidity, and exposure to chemicals can influence the performance of fasteners. For instance, in a marine environment, fasteners are subject to saline exposure, necessitating the selection of corrosion-resistant materials such as 316 stainless steel.
When considering environmental factors, one should evaluate:
- Temperature extremes that may affect material performance.
- Potential exposure to aggressive chemicals, necessitating non-reactive materials.
- The likelihood of physical wear or erosion due to environmental elements.
Overall, understanding the operational environment allows for informed decisions that ensure long-term reliability and performance of all thread fasteners.
Corrosion Resistance Factors
Corrosion resistance is paramount in fasteners that are exposed to adverse environmental conditions. Selecting materials designed to resist corrosion is essential to prevent structural failure over time. Fasteners such as zinc-plated steel and polypropylene are common choices due to their protective properties.
Important considerations for selecting corrosion-resistant fasteners include:
- The type of corrosion: galvanic, pitting, or stress corrosion cracking.
- Coatings and treatments: choosing appropriate surface coatings such as galvanization or passivation to enhance resistance.
- Maintenance and inspection plans: regular checks can prevent unexpected failures and enhance the durability of fasteners.
Installation Techniques
The section on installation techniques plays a critical role in understanding all thread fasteners. Proper installation ensures that these fasteners perform as intended, providing the necessary strength and reliability in various applications. When done correctly, installation can prevent issues such as loosening due to vibration, structural failure, or reduced load bearing capability. Key elements include the tools required, torque specifications, and common installation errors that should be carefully considered.
Tools Required for Installation
Using the right tools is essential for effective installation of all thread fasteners. The tools allow for accurate handling and application, leading to secure and efficient fastening.
- Wrenches and Sockets: Adjustable wrenches and socket sets are vital for tightening and loosening all thread fasteners. The size of the wrench or socket must match the diameter of the rod.
- Torque Wrench: This tool is crucial for achieving the specified torque during installation. A torque wrench helps ensure that the load is distributed correctly, preventing over-tightening or under-tightening.
- Pneumatic Tools: Air-powered tools can greatly speed up the installation process, especially in high-volume applications. These tools are designed to provide consistent torque and reduce physical strain on the user.
Each of these tools serves to facilitate a more successful installation process, enhancing the overall integrity of the fastening system.
Torque Specifications
Torque specifications are fundamental in the installation of all thread fasteners. They denote the amount of rotational force that should be applied to achieve optimal fastening results. Following correct torque specifications significantly impacts both safety and performance.
- Manufacturer Guidelines: Always refer to the manufacturer's specifications for the recommended torque. These guidelines are based on extensive testing and can vary by material and diameter.
- Mechanics of Torque: Torque is measured in units such as foot-pounds or Newton-meters. Understanding how to measure and apply torque precisely can prevent errors in tightening and potential failures under load.
- Calibration of Tools: Regularly calibrating torque wrenches is essential to maintain accuracy in measurements. An uncalibrated tool can lead to inconsistencies in applied force, risking the integrity of the installation.
Adhering to torque specifications is not just a best practice; it is integral to maintaining safety and performance standards in fastening processes.
Common Installation Errors
Despite having the right tools and specifications, installation errors can still occur. Recognizing and avoiding these mistakes is crucial for effective installation of all thread fasteners.
- Over-Tightening: This leads to twisted or weakened fasteners. Care should be taken to apply torque as specified, avoiding excessive force.
- Under-Tightening: This can cause the fastener to loosen over time. It is essential to ensure that the specified torque is achieved during installation.
- Misalignment: Fasteners must be aligned properly to avoid uneven load distribution, which may lead to failure.
- Ignoring Joint Conditions: The condition of the surfaces that the fasteners are mated to must be assessed. Dirty or uneven surfaces can result in improper fastening.
By being aware of these common errors and understanding their implications, professionals can mitigate risks and improve the overall reliability of all thread fasteners in their respective applications.
Proper installation is as critical as selecting the right fastener. Ignoring installation techniques can lead to significant failures.
Quality Control Measures
Quality control measures in the realm of all thread fasteners are crucial as they ensure that the products meet specific standards and perform reliably under stress. Fasteners are fundamental components in various applications, and failure of these components can lead to significant safety hazards and financial losses. Thus, implementing rigorous quality control processes is not only advisable but essential.
To achieve a high level of quality, manufacturers utilize various testing and inspection procedures. These methods aim to identify any defects or discrepancies in the fasteners before they reach the market. Key aspects of quality control include the following:
- Material Verification: Ensuring that the materials used comply with required specifications.
- Dimensional Checks: Measuring the dimensions of the fasteners to confirm they meet design tolerances.
- Functional Testing: Checking the performance of fasteners under load conditions to predict behavior in real-life applications.
The benefits of maintaining high-quality standards in fastener production include enhanced reliability, improved customer satisfaction, and compliance with industry regulations. By prioritizing quality control measures, manufacturers not only reduce the risk of failures but also strengthen their market position through reliability and trustworthiness.
Testing and Inspection Procedures
Testing and inspection procedures are critical components of quality control. These procedures begin well before the fasteners are assembled into products. Each phase of production, from raw material selection to final packaging, must be meticulously examined. Common practices include:
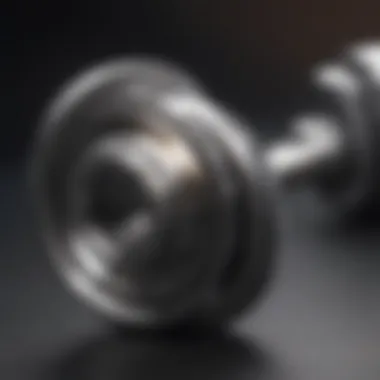

- Visual Inspections: Workers examine fasteners for obvious defects such as cracks or irregular finishes.
- Mechanical Testing: This involves subjecting fasteners to stress tests to determine their tensile strength and yield strength. For instance, tensile tests expose the fasteners to stress until they reach their breaking point.
- Non-Destructive Testing (NDT): Techniques like ultrasonic testing or magnetic particle testing allow manufacturers to detect internal flaws without damaging the fasteners.
The comprehensive nature of these procedures ensures that any faulty fasteners are identified and rectified, safeguarding end-users.
Certifications for All Thread Fasteners
Certifications play a vital role in the all thread fastener industry. They provide assurance that the fasteners meet predetermined standards set by recognized organizations. Some important certifications include:
- ISO 9001: This certification indicates a robust quality management system in the manufacturing process.
- ASTM Standards: Compliance with ASTM standards guarantees that the fasteners have met specific material and performance criteria.
Having certifications not only affirms the quality of fasteners but also enhances marketability. Manufacturers who can showcase their certified products are more likely to gain the confidence of their customers, thereby establishing long-term business relationships.
"Quality isn’t just a requirement; it’s a commitment to excellence that must be practiced at every level of manufacturing."
By understanding these quality control measures, those involved in engineering and manufacturing can appreciate the importance of reliability in all thread fasteners.
Trend Analysis in Fasteners Industry
The fasteners industry, particularly the segment of all thread fasteners, is undergoing significant evolution. Understanding these trends is imperative for industry professionals and stakeholders. It allows for informed decision-making, optimizes resource management, and enhances product development. In a rapidly changing market, the ability to foresee trends can provide a competitive edge. This section analyzes two critical trends: innovations in fastener design and the emergence of new materials and technologies.
Innovation in Fastener Design
Design innovation in fasteners is driven by the need for enhanced performance and efficiency. Advances in design theory and engineering practices lead to the development of fasteners that are not only stronger but also more versatile. This is particularly relevant for all thread fasteners, which are integral in various applications ranging from construction to automotive.
- Computer-Aided Design (CAD): The use of CAD software accelerates design iterations, leading to products that meet precise specifications with greater accuracy.
- Finite Element Analysis (FEA): FEA tools are utilized to simulate how fasteners behave under stress, which enhances reliability and performance.
- Custom Threading Techniques: Innovative thread designs improve grip and reduce the likelihood of loosening over time.
These innovations enable manufacturers to cater to the unique demands of different industries, thus broadening their market reach.
Emerging Materials and Technologies
The materials used in all thread fasteners are crucial in determining their strength, durability, and suitability for specific applications. Emerging materials are making a remarkable impact in the production of these fasteners.
- Advanced Composite Materials: Materials such as carbon fiber and thermoplastics are being explored for specific applications. Their reduced weight and corrosion resistance make them attractive in aerospace and automotive sectors.
- Smart Materials: The introduction of materials with self-healing capabilities or that can respond to environmental stimuli presents exciting new avenues for fastener applications.
- 3D Printing Techniques: Additive manufacturing allows for complex geometries that traditional methods cannot achieve. This technological evolution is critical for custom fastener production, allowing for rapid prototyping and reducing waste in the manufacturing process.
Incorporating these advanced materials and technologies not only enhances product performance but also addresses sustainability concerns.
"Innovation and the integration of emerging materials are no longer options but necessities in the fasteners industry."
Through careful trend analysis, manufacturers and users of all thread fasteners can optimize their processes, reduce costs, and stay ahead in a competitive landscape. Understanding the shifts in design and material science will shape the future of fasteners and their applications.
Challenges Facing the All Thread Fastener Market
The market for all thread fasteners is not without its difficulties. Understanding these challenges is essential for any stakeholder. This section discusses the issues of market volatility, pricing, and disruptions in supply chains. Both elements play significant roles in the manufacturing and application of these fasteners. By recognizing and addressing these challenges, companies can better navigate complexities and guide their operations toward efficiency and profitability.
Market Volatility and Pricing
Market volatility refers to the fluctuations in the prices and demand for all thread fasteners. This instability can arise from various factors including global economic conditions, raw material costs, and competitive pressures. For instance, economic downturns can lead to decreased construction activity, reducing the demand for fasteners. Conversely, a booming economy can increase demand, leading to shortages and price hikes.
There are several considerations regarding pricing:
- Raw Material Costs: The prices of steel and other metals directly affect the costs of all thread fasteners. Any increase in these materials can cause suppliers to raise prices.
- Competitive Landscape: The entry of new manufacturers can create increased competition. This can drive prices down but may also lead to quality compromises if not monitored.
- Global Events: Events like pandemics or geopolitical tensions can disrupt production, sending supply prices soaring.
As a result, those involved in the fastener market must continually assess their pricing strategies. It’s critical to react swiftly to shifts in market conditions to maintain competitiveness.
Supply Chain Disruptions
Supply chain issues are a significant challenge facing the all thread fastener market. These disruptions can occur due to various factors such as shipping delays, material shortages, and even increased regulation. A well-functioning supply chain is essential for timely delivery and cost management of fasteners.
Key elements of supply chain disruptions include:
- Logistical Delays: Transportation issues can slow down the delivery of raw materials needed for the production of fasteners. Whether due to natural disasters or political unrest, these delays can halt production, impacting overall business performance.
- Material Shortages: As industries across the globe ramp up production, shortages of specific materials may occur. This creates bottlenecks, making it difficult for manufacturers to obtain the necessary components to create fasteners.
- Regulatory Changes: New trade laws or safety standards can impede the free flow of materials and products, leading to increased costs and delays.
Addressing these supply chain disruptions requires a proactive approach. Businesses are encouraged to diversify their suppliers and invest in technology that enhances their logistics capabilities. This can help mitigate risks associated with reliance on single suppliers or transportation methods.
In summary, the challenges facing the all thread fastener market—market volatility and supply chain disruptions—require constant attention and strategic planning. By understanding these factors, stakeholders can better prepare and respond.
Future Directions in Fastener Technology
The field of fastener technology is continuously evolving. As the demands of engineering and manufacturing sectors grow more complex, so too must the innovations that drive this industry forward. Future directions in fastener technology will focus on improving efficiency, safety, and sustainability. These advancements are crucial for meeting the stringent requirements of modern projects, especially in sectors like aerospace, automotive, and construction. Understanding these trends is essential, not only for professionals but also for researchers and educators who are shaping the next generation of engineers and technologists.
Advancements in Fastening Techniques
The advancements in fastening techniques are primarily aimed at enhancing the performance and reliability of fasteners. These include innovations such as:
- Self-adhesive Fasteners: These fasteners use advanced adhesives that provide equivalent or superior strength to traditional methods of fastening, eliminating the need for additional tools.
- Smart Fasteners: Integrating sensors into fasteners allows for real-time monitoring of tension and application, significantly improving safety and efficiency.
- Hybrid Fastening Solutions: Combining various fastening technologies to optimize strength and versatility, hybrid solutions accommodate varying load conditions.
These advancements are not just about improvement in technology. They also focus on addressing challenges such as installation ease and material compatibility. As fasteners become more complex, the need for well-trained personnel to handle new fastening techniques also increases. It’s important that education systems adapt to include these advancements to create a workforce ready for future challenges.
Sustainability Initiatives in Manufacturing
Sustainable manufacturing practices are becoming increasingly prevalent within the fastener industry. As companies strive to reduce their carbon footprint, several initiatives are taking shape:
- Recyclable Materials: Manufacturers are beginning to utilize materials that are fully recyclable or made from recycled sources, minimizing waste and conserving resources.
- Energy-Efficient Production: New methodologies in production cut down on waste and energy consumption. This results in a lower environmental impact.
- Green Coatings: Traditional coatings often contribute to environmental harm. New water-based, eco-friendly coatings are now available, providing durability without the associated environmental costs.
"Sustainability is not just a trend; it’s a crucial necessity in the modern manufacturing landscape."
These initiatives are essential for ensuring that fastener production aligns with global environmental goals. As regulations become stricter, the fastener industry must adapt. Innovation in sustainability will not only benefit the environment but also enhance product appeal, as consumers increasingly favor environmentally friendly products.
In summary, the future directions in fastener technology will place a strong emphasis on advancements in fastening techniques and sustainable manufacturing. These trends are reshaping the industry and offer opportunities for growth and improvement in both performance and environmental impact.
The End
The conclusion serves as a critical component of this article by summarizing essential insights while also exploring the future landscape of all thread fasteners. It emphasizes the importance of understanding the nuances of all thread fasteners in various applications, from construction to aerospace. The effectiveness of fasteners hinges not only on their design and material composition but also on the awareness of industry standards and best practices. This section aims to encapsulate the essence of the preceding discussions with substantial clarity.
Summary of Key Points
Throughout this article, several crucial points have been illuminated regarding all thread fasteners:
- Definition and Importance: All thread fasteners are versatile components that hold structures together. Their role spans multiple disciplines including construction and manufacturing.
- Material Variety: Different materials, including metal alloys and non-metallic substances, contribute to the performance and suitability of fasteners for specific applications.
- Manufacturing and Thread Design: Techniques such as cold forming, machining, and various thread profiles can significantly influence the mechanical properties and usability of the fasteners.
- Installation and Quality Control: Proper installation techniques, alongside rigorous quality measures, ensure that the fasteners perform optimally in real-world applications.
Understanding these elements is vital for anyone engaged in engineering or construction fields. Recognizing the significance of each aspect will lead to higher standards of work and enhanced safety measures in projects.
Final Thoughts on Future Trends
Looking ahead, the fastener market is poised for notable changes driven by advancements in technology. Here are some key trends to monitor:
- Innovation in Fastener Design: Ongoing research and development efforts are likely to produce fasteners that provide better performance, including higher tensile strength and improved corrosion resistance.
- Emerging Materials: The exploration of composite materials and smart materials could revolutionize how all thread fasteners are used. These materials may offer unique properties that could lead to lighter yet stronger applications.
- Sustainability: With increasing focus on environmental impact, manufacturers are expected to adopt more sustainable practices in producing fasteners. This includes recycling materials and reducing waste in the production process.
Additionally, regulatory changes may influence the standards governing fasteners, ensuring they meet not only safety criteria but also environmental considerations.