Understanding Aluminum Bonding Wire in Semiconductors
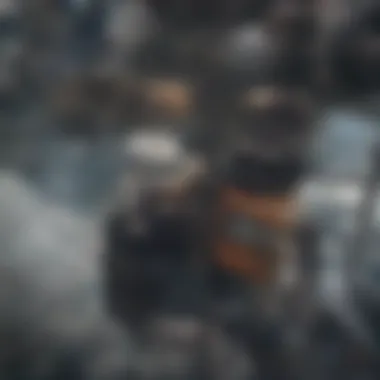
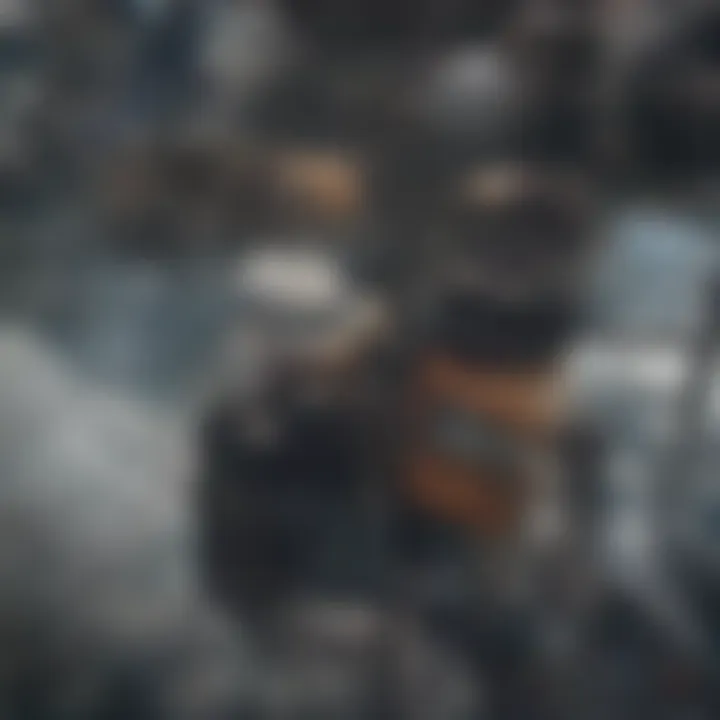
Intro
Aluminum bonding wire is often overlooked in discussions regarding semiconductor packaging yet it plays a pivotal role in determining the performance and reliability of electronic devices. The industry has been under pressure to evolve due to rapid technological advancements. This demands a closer examination of aluminum bonding wire's unique properties, manufacturing processes, and applications.
The purpose of this article is to provide a comprehensive understanding of aluminum bonding wire. It will analyze various bonding techniques that utilize this metal, compare aluminum against competing materials, and identify challenges that manufacturers face. By gathering insights from different corners of the industry, we provide a robust resource full of essential information that caters to students, researchers, educators, and professionals.
Research Context
Background and Rationale
The use of aluminum bonding wire has been predominately driven by its favorable characteristics. Aluminum is lightweight, cost-effective, and offers excellent thermal and electrical conductivity. Its attributes make it a preferred choice for advanced applications in semiconductor packaging. However, the shift from gold to aluminum wire in many applications raises questions on reliability and performance.
This article seeks to delineate not only the manufacturing processes but also the subtleties of how aluminum bonding wire can influence the overall performance of electronic devices. The relevance of this exploration cannot be overstated, especially as the shift toward miniaturization in electronics continues.
Literature Review
Existing literature on aluminum bonding wire offers segmented insights focused primarily on individual aspects such as manufacturing technologies or specific applications. However, a holistic approach is often absent. Notable research has covered the
- mechanical properties of bonding wire
- innovative bonding techniques
- market trends in semiconductor packaging.
As we gather more data and insights, this article aims to synthesize available knowledge and present a unified analysis. The goal is to compile salient information that reflects the current state and the future direction of aluminum bonding wire usage in the semiconductor industry.
Methodology
Research Design
The article will integrate both qualitative and quantitative data, enabling a well-rounded view of aluminum bonding wire. Key themes will emerge through analyses of various peer-reviewed articles, industry reports, and expert interviews. By grouping insights thematically, the research aims to clarify complex issues surrounding the topic.
Data Collection Methods
To ensure the credibility of our findings, data will be sourced from a range of reputable outlets including academic journals, trade publications, and industry experts. Online databases and platforms like Wikipedia, Britannica, and specialized forums will supplement this information. This multi-faceted approach will strengthen the validity of our conclusions and enhance the article's relevance.
Preamble to Aluminum Bonding Wire
Aluminum bonding wire is a critical component in the field of semiconductor packaging. Its importance lies in its capacity to ensure reliable electrical connections within electronic devices. In the context of this article, understanding aluminum bonding wire involves examining its manufacturing processes, properties, and various applications. The insights gained can inform design choices and material selections in numerous industries, particularly those where performance and reliability are paramount.
Definition and Context
Aluminum bonding wire is a conductive wire utilized primarily to connect semiconductor devices to their packaging. This wire is made from high-purity aluminum, and its average diameter typically falls between 17 to 50 micrometers, allowing for the intricate connections needed in microelectronic circuits. The use of aluminum in wire bonding has gained prominence due to its excellent electrical conductivity and cost-effectiveness when compared to gold or copper alternatives.
The context of aluminum bonding wire is crucial in semiconductor manufacturing. With technological advancements driving the miniaturization of electronic components, the size and weight of bonding materials have become increasingly important. Aluminum wire has emerged as a preferred choice because it provides a balance between efficiency and reliability in various applications, particularly in microelectronics and consumer electronics.
Historical Background
The use of aluminum for wire bonding can be traced back to the mid-20th century. Initially, gold wires were the standard in the semiconductor industry due to their superior conductivity. However, as the demand for cost-effective solutions increased, manufacturers began exploring materials like aluminum. By the 1970s, aluminum bonding wire had started gaining traction, driven by its affordability and lighter weight compared to gold.
Over the years, advancements in manufacturing techniques have enhanced the quality and reliability of aluminum bonding wire. This evolution is closely tied to the development of new bonding technologies, including ultrasonic and thermo-compression bonding methods. These methods have allowed aluminum wires to bond effectively in a wide range of temperatures and conditions. Today, aluminum bonding wire is an essential aspect of semiconductor packaging, serving an array of sectors such as the automotive industry and consumer electronics.
Manufacturing of Aluminum Bonding Wire
The manufacturing of aluminum bonding wire is a critical process in the semiconductor industry. It serves as the backbone for effective electrical connections in microelectronic devices. Understanding this process is crucial for professionals involved in semiconductor packaging. It provides insights into how the properties of aluminum contribute to performance and reliability in various applications.
With rising demand for smaller and more efficient electronic devices, the production of aluminum bonding wire must keep pace. The focus is not only on innovation and efficiency but also on maintaining high standards of quality.
Raw Material Sources
Aluminum bonding wire starts with high-quality aluminum alloys. These alloys are selected for their superior conductivity and strength. The primary sources of raw materials are:
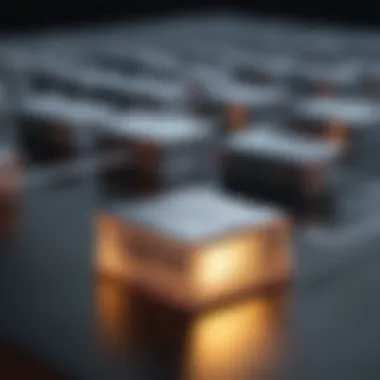
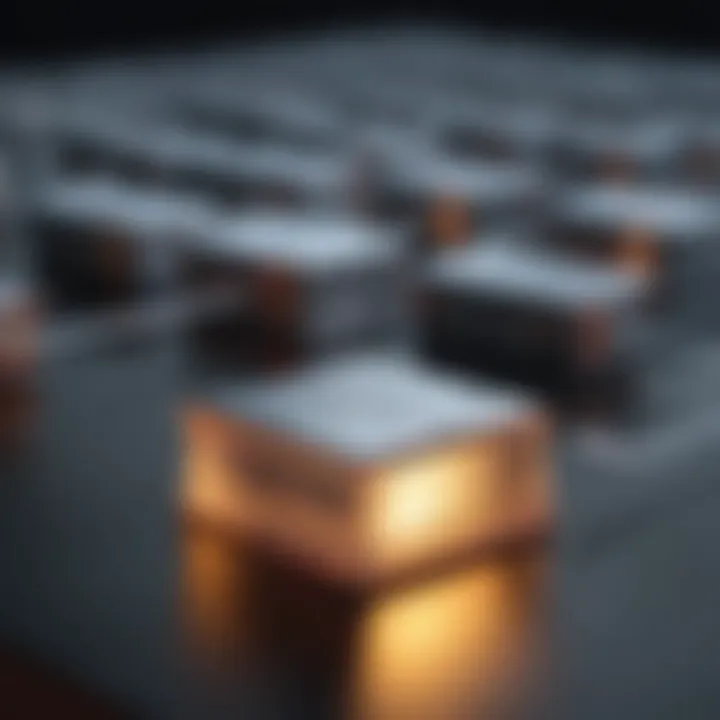
- Aluminum ingots: These are produced from bauxite ore, refined through various processes.
- Recycled aluminum: A significant portion of aluminum bonding wire is derived from recycling, reducing environmental impact.
The choice of raw material significantly affects the properties of the final product. Manufacturers often seek alloys with optimal purity to enhance electrical and mechanical performance. The use of recycled materials can lead to cost savings. However, it necessitates rigorous quality assessments.
Production Techniques
The production of aluminum bonding wire involves several techniques to transform raw materials into the desired wire form. Key techniques include:
- Drawing: This process reduces the diameter of the aluminum rod while increasing its length. Precision in drawing is crucial for achieving the correct wire gauge.
- Annealing: This heat treatment process strengthens the wire, improving its ductility and conductivity. Proper annealing ensures the wire can withstand the bonding process.
- Coating: Some manufacturers apply a thin layer of material to enhance bondability and protect the wire from oxidation.
These methods must be optimized to ensure the consistency and reliability of the bonding wire. Technological advancements continue to improve production efficiency, impacting cost and performance.
Quality Control Measures
Quality control is a fundamental aspect of manufacturing aluminum bonding wire. Ensuring that the wire meets specified standards is vital for its application in electronics. Key quality control measures include:
- Dimensional checks: Regular assessment of wire diameter and length is essential.
- Electrical testing: Conductivity tests help confirm that the wire meets electrical specifications.
- Visual inspections: Any defects or surface irregularities must be identified early in the manufacturing process.
Implementing these quality control measures helps prevent failures in the field. A focus on quality enhances not only the reliability of the final products but also increases trust within the market.
"Quality in manufacturing is not an option; it is a necessity in the semiconductor industry."
Overall, the manufacturing processes of aluminum bonding wire are complex and demand precision. With the right practices in place, manufacturers can assure high-quality wire that meets the evolving needs of the semiconductor industry.
Properties of Aluminum Bonding Wire
The properties of aluminum bonding wire are essential in determining its suitability for various applications. These properties include mechanical, electrical, and thermal characteristics. Understanding these elements helps researchers and professionals make informed decisions about the usage of aluminum bonding wire in semiconductor packaging and other fields. Each of these categories contributes to the wire's performance, reliability, and overall effectiveness in practical applications.
Mechanical Properties
Mechanical properties define how the wire behaves under different physical conditions. These include tensile strength, ductility, and fatigue resistance.
- Tensile Strength: This refers to the maximum amount of tensile (pulling) stress that a material can withstand before failure. Aluminum bonding wire typically exhibits high tensile strength, making it capable of enduring significant forces during application without breaking.
- Ductility: Ductility is the ability of a material to deform under tensile stress. Aluminum is well-known for its ductility, allowing the wire to be drawn into very thin strands. This is crucial in microelectronics, where smaller, more compact connections are favored.
- Fatigue Resistance: Aluminum bonding wire must endure repeated stress cycles, especially in dynamic applications. Good fatigue resistance ensures that the wire will maintain its integrity over time, reducing failure rates in critical devices.
These mechanical properties make aluminum bonding wire a favorable choice for applications where reliability is paramount.
Electrical Conductivity
Electrical conductivity is a vital aspect in many electronic applications. Aluminum as a conductor is widely used due to its favorable conductivity characteristics.
- Conductivity Gradient: Aluminum bonding wire has around 60% the conductivity of copper, which is often used in similar applications. This conductivity is sufficient for many microelectronic applications, particularly when weight and cost are considered.
- Skin Effect: In high-frequency applications, the skin effect can influence the performance of the wire. The skin depth in aluminum is crucial for ensuring that the wire can handle high-frequency signals without significant losses.
Understanding the electrical conductivity of aluminum bonding wire helps in determining its capacity for various electronic applications. This factor plays a key role in the efficiency and performance of electronic devices.
Thermal Properties
Thermal properties are significant for the overall functioning of electronic components. These include thermal conductivity, specific heat, and thermal expansion coefficient.
- Thermal Conductivity: Aluminum has a high thermal conductivity, allowing heat to dissipate quickly. This property prevents overheating of the electronic components, which could lead to failure.
- Specific Heat: The specific heat of aluminum affects how quickly it can absorb and transfer heat. A lower specific heat indicates that the wire will reach operational temperatures faster, impacting device performance.
- Thermal Expansion: Aluminum exhibits a moderate thermal expansion coefficient. This means that as temperatures rise, the wire expands at a predictable rate, allowing for reliable thermal management in devices.
"Understanding the properties of aluminum bonding wire is vital for its successful application in semiconductors. This knowledge aids in optimizing design and improving reliability."
By focusing on these properties, stakeholders in microelectronics and other relevant fields can better evaluate and leverage aluminum bonding wire in their projects.
Bonding Techniques
Bonding techniques are critical to the performance and reliability of aluminum bonding wire in semiconductor applications. Each method utilized offers unique benefits and challenges, shaping the overall manufacturing process. Understanding these techniques allows for better selection based on specific requirements, ensuring optimized performance in diverse applications.
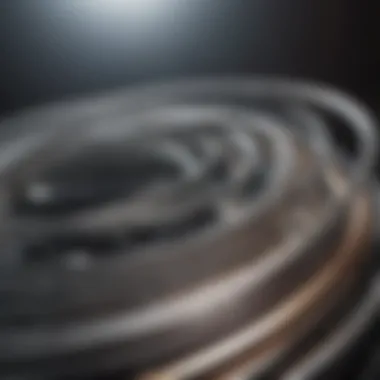
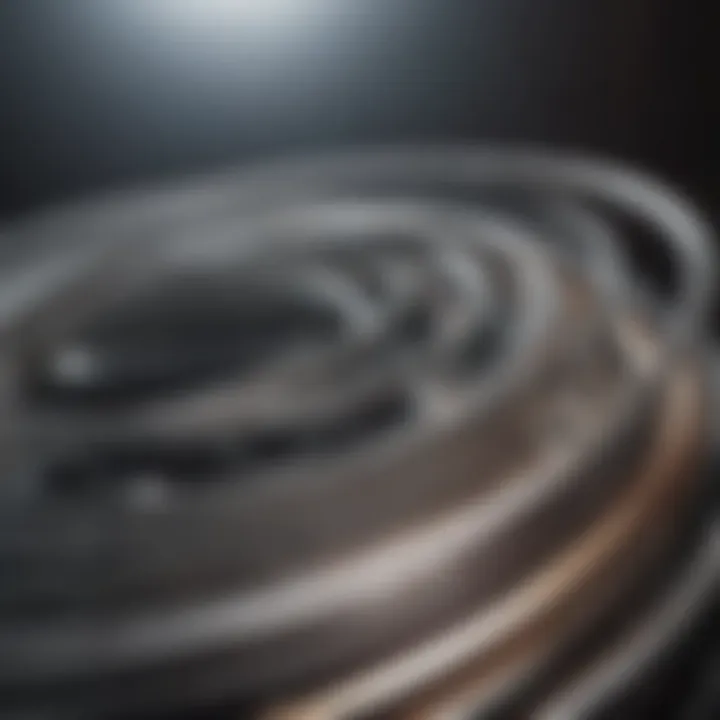
Ultrasonic Bonding
Ultrasonic bonding is a prevalent technique used in the semiconductor industry. This method employs high-frequency sound waves to create a bond between the aluminum wire and the substrate. The process is known for its advantages, primarily its capability to produce strong connections with minimal heat input.
One key benefit of ultrasonic bonding is its speed. The bonding happens quickly, improving overall manufacturing efficiency. Additionally, the technique is less likely to cause thermal damage to sensitive components, an essential consideration in microelectronics. However, ultrasonic bonding requires precise control of parameters such as pressure and vibration frequency. Misalignment can lead to weak bonds or defects.
Thermo-Compression Bonding
Thermo-compression bonding is another vital technique for bonding aluminum wire. This method utilizes a combination of heat and mechanical pressure to form a bond. The application of heat softens the wire and enhances the adhesion process, creating a robust connection.
The main advantage here is the strong bond that can withstand thermal cycling, which is crucial for applications in automotive and aerospace industries. However, the process demands careful attention to temperature control. Excessive heat can damage the wire or the underlying substrate, resulting in reliability concerns. Therefore, optimizing conditions is vital for achieving high-quality bonds.
Laser Bonding
Laser bonding represents a more advanced approach in aluminum bonding wire technology. This innovative technique uses laser energy to create localized heating, allowing for precise and effective bonding. The key advantage of laser bonding is its adaptability. It can be employed on various substrates, making it versatile in application.
Moreover, laser bonding minimizes heat-affected zones, reducing the risk of damage to nearby components. This precision aspect is particularly beneficial in microelectronics where space is limited. On the downside, the complexity of laser systems may lead to higher initial equipment costs and a steeper learning curve for operators.
"The choice of bonding technique directly influences the quality and reliability of the final product. Each method has its unique advantages and challenges that must be carefully weighed."
Applications of Aluminum Bonding Wire
Aluminum bonding wire is integral to various industries due to its unique properties. Its applications span across sectors like microelectronics, the automotive industry, and consumer electronics. Understanding these applications is essential as they showcase the wire's versatility and significance in modern technology.
Microelectronics
In the field of microelectronics, aluminum bonding wire is critical for ensuring reliable connections within semiconductor devices. Its lightweight nature and good electrical conductivity make it ideal for wire bonding processes. Many chips used in mobile devices, computers, and other electronics rely on aluminum wire for packaging. With the growing demand for miniaturization, the size and thickness of this wire have seen a reduction without sacrificing performance.
The importance of aluminum bonding wire in microelectronics also extends to cost-efficiency. Compared to gold, aluminum offers a more economical alternative without compromising on necessary properties. This is a key consideration in reducing overall production costs for manufacturers. Additionally, advanced bonding techniques, such as thermo-compression bonding, have enhanced the performance and reliability of connections, minimizing failure rates in devices.
Automotive Industry
The automotive sector has recognized the potential of aluminum bonding wire in achieving lightweight vehicle designs. As the industry increasingly shifts towards electrification and fuel efficiency, reducing overall vehicle weight is paramount. Aluminum's properties help manufacturers meet safety standards while improving performance and fuel economy.
Moreover, aluminum bonding wire is used in various components, including sensors and control units. It connects different parts of vehicles efficiently, which is significant for electronic stability programs, braking systems, and other advanced driver-assistance systems. As smart vehicles evolve, the demand for reliable and efficient wiring becomes even more crucial.
Consumer Electronics
In consumer electronics, aluminum bonding wire plays a vital role in the manufacturing of devices such as smartphones, tablets, and laptops. The necessity for high-speed data transfer and connectivity in these gadgets has amplified the industry’s reliance on aluminum wires. Their high thermal conductivity also ensures efficient heat dissipation, which is essential for device longevity and performance.
Furthermore, as manufacturers strive to produce more energy-efficient devices, aluminum's recycling capabilities become advantageous. This aligns with sustainability goals and enhances the appeal of aluminum bonding wire in a crowded market.
"Aluminum bonding wire is not only a practical solution but a driving force in the innovation of new technologies across various industries."
In summary, the applications of aluminum bonding wire illuminate its significance in shaping the future landscape of technology across microelectronics, automotive, and consumer electronics. Each sector recognizes the wire's ability to enhance performance and efficiency while remaining economically viable. As industries continue to adapt and evolve, aluminum bonding wire will likely remain at the forefront.
Advantages and Disadvantages of Aluminum Bonding Wire
Understanding the advantages and disadvantages of aluminum bonding wire is essential for professionals working in semiconductor packaging. This section explores both sides, which is vital for making informed decisions.
Benefits
Aluminum bonding wire has several advantages that contribute to its popularity in various applications:
- Cost-Effectiveness: Compared to gold or copper, aluminum is less expensive. This can significantly reduce manufacturing costs, especially in large-scale production.
- Excellent Electrical Conductivity: Aluminum has good conductivity, which makes it suitable for connecting components in microelectronics. It maintains performance in high-frequency applications.
- Lightweight Nature: Aluminum's low density allows for reduced overall weight in electronic assemblies. This is especially critical in industries where weight is an important consideration.
- Resistance to Corrosion: Aluminum forms a natural oxide layer that protects it from corrosion. This property increases the durability of connections in various environments.
"Using aluminum for bonding wire can reduce costs while maintaining reliability."
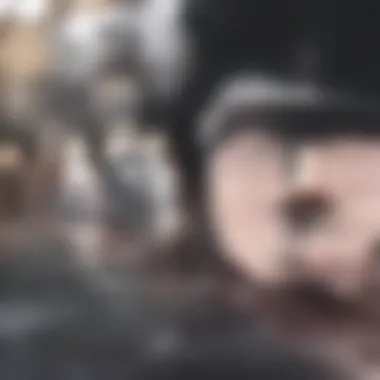
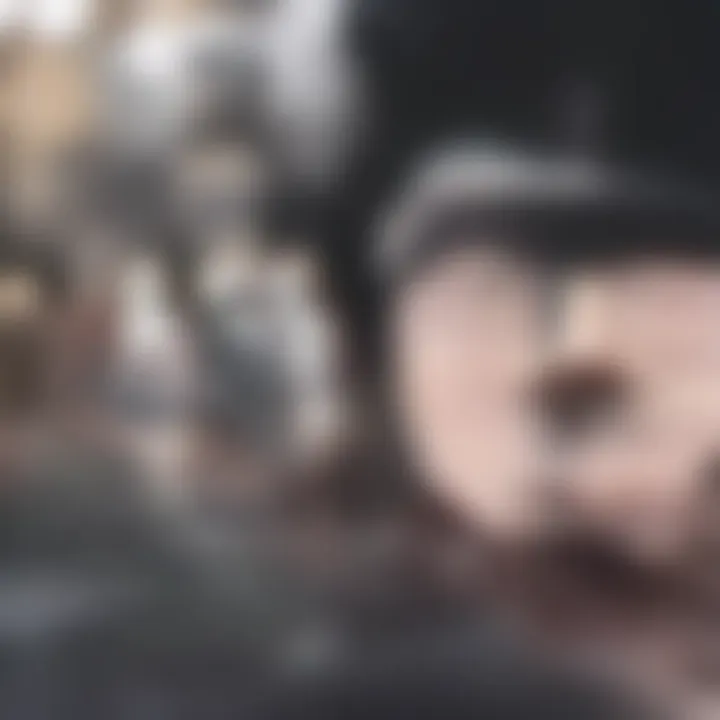
- Thermal Performance: It features good thermal properties, aiding in heat dissipation. This is beneficial in preventing overheating in electronic components.
Limitations
Despite its advantages, aluminum bonding wire also comes with certain limitations that warrant consideration:
- Brittleness: Aluminum can become brittle under certain conditions, making it less ideal for applications requiring flexibility. This brittleness could lead to failure in some environments.
- Oxidation Issues: While the oxide layer protects against corrosion, it can create problems during the bonding process. Careful handling is necessary to ensure the oxide layer does not interfere with adhesion.
- Lower Mechanical Strength: Compared to copper, aluminum has lower tensile strength. This might necessitate thicker wires or more careful handling during manufacturing.
- Solderability Challenges: Soldering aluminum can present difficulties due to its oxide layer. Special flux and techniques are usually required to achieve reliable solder joints.
- Heat Sensitivity: Aluminum can be sensitive to high temperatures, which may lead to deformation or other issues in high-heat applications.
In summation, aluminum bonding wire presents a mix of benefits and limitations. Professionals in the field must weigh these factors to determine the optimal use of aluminum in specific applications.
Challenges in the Industry
In the aluminum bonding wire sector, there are numerous challenges that manufacturers face. Understanding these challenges is crucial for improving the production process and the adaptability of aluminum in various applications. Two prominent issues are material availability and technological limitations. Addressing these factors does not only enhance the material’s performance but also drives innovation within the industry.
Material Availability
The sourcing of high-quality aluminum is essential for effective bonding wire production. Increasing demand across various sectors often leads to a rise in raw material prices, making it difficult for manufacturers to maintain cost-effectiveness. The global supply chain is influenced by political, economic, and environmental aspects. For instance, trade disputes or regulations within major aluminum-producing countries can affect material availability on a large scale. Consequently, manufacturers need to diversify their suppliers or invest in alternative sourcing strategies. This is important to ensure that the production of aluminum bonding wire is not interrupted by shortages or price fluctuations. The exploration of recycled materials can also be a beneficial alternative. It presents an opportunity to reduce dependency on fresh resources while contributing to sustainability goals.
Technological Limitations
While aluminum bonding wire has many advantages, there are limitations tied to the existing technology used in its bonding techniques. Ultrasonic and thermo-compression bonding are commonly employed methods, yet they require precise conditions to ensure quality yields. Variations in temperature, pressure, or speed can lead to defects in the bond, compromising the reliability of the component. Moreover, advancements in automation are slow. Many manufacturers still rely on manual processes, cultivating a labor-intensive environment with higher chances for error.
To address these limitations, investment in research and development is necessary. Advanced techniques, such as laser bonding, remain underexplored yet hold potential to improve bond strength and reduce production times. Continuous training for operators is equally important, ensuring that they are proficient in handling modern equipment.
"Advancements in technology not only enhance the efficiency of aluminum bonding wire production but also broaden its applicability in cutting-edge industries."
Addressing material availability and technological limitations is vital for the future viability of aluminum bonding wire. By overcoming these challenges, the industry can ensure a stable supply chain and leverage technological advancements, ultimately benefiting various high-tech applications.
Market Trends and Future Outlook
The market trends and future outlook for aluminum bonding wire are crucial for understanding its evolving role in semiconductor packaging. Ongoing technological advancements continue to shape the landscape of this industry. As companies innovate, the demand for reliable and efficient bonding techniques has grown significantly. The transition towards more complex electronics has made a robust understanding of these trends essential for manufacturers and stakeholders in the market.
Emerging Technologies
Emerging technologies are at the core of the development within the aluminum bonding wire sector. Innovations in bonding techniques and materials have been pivotal. For instance, the improvement in ultrasonic bonding technology has led to better adhesion properties and finer bond quality. Other technologies, such as advanced laser bonding, offer precision not achievable with traditional methods. These cutting-edge techniques are designed to increase production speed, reduce defects, and boost overall efficiency. This level of sophistication allows manufacturers to meet the higher demands placed by industries like microelectronics and automotive applications.
In addition, hybrid bonding techniques are gaining attention. This involves combining different bonding methods to exploit their individual strengths. Integrating these novel approaches can enhance performance metrics and widen the potential applications of aluminum bonding wire.
Demand Dynamics
Understanding the demand dynamics is essential in navigating the aluminum bonding wire market. Several sectors heavily influence this demand, notably the microelectronics and automotive industries. The increasing use of aluminum for its lightweight and cost-effective properties has created a strong preference for it over gold in many applications.
Factors affecting demand include:
- Technological Advancements: As electronics become smaller and more complex, the need for dependable bonding solutions rises.
- Sustainability: There is a growing emphasis on sustainable manufacturing practices. Aluminum presents a more environmentally friendly option compared to other bonding materials.
- Market Growth: Expanding sectors such as electric vehicles and renewable energy systems stimulate demand.
The balance between these dynamics will shape the future demand for aluminum bonding wire. Keeping abreast of these factors enables professionals to position themselves accordingly in the market.
End
The conclusion serves as a pivotal element in this article about aluminum bonding wire. It synthesizes the crucial insights discussed throughout the content, framing the significance of aluminum bonding wire in the context of semiconductor packaging. This aspect is particularly relevant in today's technology-driven landscape, where efficiency and reliability are paramount factors.
Summary of Key Points
The key points of this article are numerous. First, we discussed the definition and context of aluminum bonding wire, establishing its importance in manufacturing and technology. Then, we moved on to the manufacturing processes, highlighting techniques and stringent quality control measures that ensure product excellence.
We also explored the properties of aluminum bonding wire, including mechanical, electrical, and thermal characteristics, all of which affirm its advantageous role in various industries. The section on bonding techniques delved into methods like ultrasonic bonding and thermo-compression bonding, which are essential for achieving strong connections.
Additional focus was placed on applications across microelectronics, automotive industries, and consumer electronics, illustrating the versatility of aluminum bonding wire. We assessed both advantages and disadvantages, weighing its benefits against limitations compared to other materials. The article also touched upon challenges in the industry, including material availability and technological constraints, offering a realistic view of current obstacles faced by manufacturers. Finally, the market trends and future outlook reveal where the industry is headed, particularly in terms of emerging technologies and demand dynamics.
Final Thoughts
In closing, understanding aluminum bonding wire is crucial for professionals, researchers, and students in technology fields. As we advance into more sophisticated applications and products, the need for reliable bonding solutions only increases. The ongoing developments and innovations in this field underscore that aluminum bonding wire will remain a topic of significance. A deeper comprehension of its properties, applications, and challenges can inform better design choices and strategic decisions in semiconductor packaging.
Staying informed about the evolution of aluminum bonding wire can unlock opportunities in various sectors. Its adaptability and performance make it an indispensable material in modern technology.