Understanding Concrete Mortar Mix: Key Insights and Applications
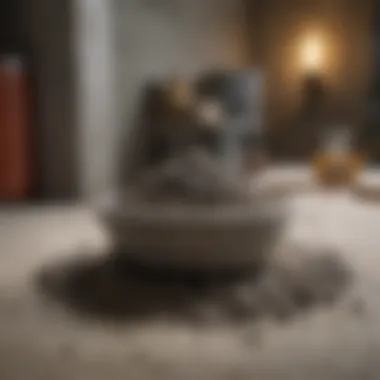
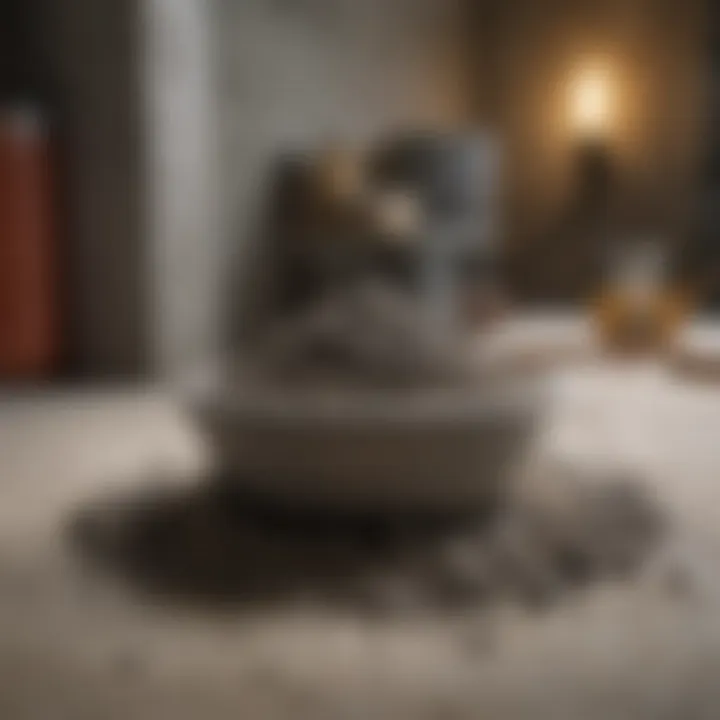
Intro
Concrete mortar mix is a vital element in the construction and repair industry, playing a pivotal role in ensuring the strength and durability of structures. Understanding the nitty-gritty of concrete mortar mix is essential for students, researchers, and professionals who aim to optimize material usage and achieve superior results. In this comprehensive guide, we will dissect every facet of concrete mortar mix—from its fundamental composition to practical applications and methodological best practices.
Diving deeper into concrete mortar mix not only broadens your knowledge but also equips you with the necessary skills to tackle diverse construction challenges. This article uncovers the ins and outs of the materials that constitute concrete mortar, the intricacies of mixing and application, and strategies to overcome common hurdles in the field.
As we lay down the groundwork for this exploration, it's essential to grasp why understanding concrete mortar mix matters. Whether you're laying bricks, patching a wall, or constructing a new edifice, the right mix will make all the difference.
So buckle up; we are about to embark on a journey that promises clarity and depth, enabling you to approach your projects with newfound knowledge and confidence.
Preface to Concrete Mortar Mix
Concrete mortar mix plays a pivotal role in construction, serving as the backbone for many structural and non-structural projects. It’s not just about mixing a few ingredients; it encompasses a scientific approach to material selection, composition, and application. Understanding the nuances of concrete mortar mix can significantly influence the durability and reliability of any construction work.
Definition and Importance
Concrete mortar mix generally refers to a mix that includes cement, sand, and water, often serving as a binding agent for various construction materials. Its importance cannot be overstated; it is essential for creating strong bonds between bricks, blocks, and stones. A well-prepared mortar mix ensures that structures can withstand environmental factors, loads, and stresses over time. The right mixture aids in preventing common issues like cracking and separation, which can lead to costly repairs down the line.
Additionally, mortar is crucial in providing aesthetic finishes. Customizing the mix allows for various textures and colors, enhancing the overall look of a construction project. Choosing the right type of mortar affects both practical performance and visual appeal.
Differences Between Concrete and Mortar
While both concrete and mortar share common ingredients, their purposes and properties differ significantly. Concrete, in essence, is a heavy-duty material designed for structural elements like foundations, slabs, and walls. It comprises larger aggregates such as gravel and sand, imparting strength and stability.
On the other hand, mortar is formulated primarily for binding and filling spaces between masonry elements. Its aggregate size is generally smaller, leading to a more workable paste that can easily spread and fill gaps.
A few distinguishing points:
- Composition: Concrete includes coarse aggregates, while mortar primarily contains sand involved primarily in smaller scales.
- Strength: Concrete is stronger due to its aggregate size and proportions, while mortar focuses on adhesion rather than structure.
- Applications: While concrete serves diverse structural roles, mortar is specifically targeted for applications in masonry, such as bricklaying and stone setting.
Understanding these differences is key for anyone involved in construction or engineering. Selecting the appropriate mix for each purpose can mean the difference between long-lasting structures and frequent repairs.
Composition of Concrete Mortar Mix
Understanding the composition of concrete mortar mix is paramount in ensuring robust outcomes in construction endeavors. The blend of materials not only determines the performance of the mortar but also its suitability for diverse applications. By focusing on the right components, builders can tailor the mix to meet specific structural requirements, thereby enhancing the longevity and durability of the resulting installations.
Primary Ingredients
Cement Types
Cement serves as the backbone of any mortar mix. There are various types of cement, and each type brings its own set of characteristics to the table. For example, Ordinary Portland Cement (OPC) is both widely recognized and favored due to its versatility and relative affordability. This type is known for its strength and setting time which appeals to many construction projects.
On the other hand, other cements such as Sulphate Resisting Cement showcase unique features, making them beneficial for specific environments, like those exposed to aggressive chemical conditions. Each type of cement can offer a different set of advantages or disadvantages, depending on the application context. For instance, while OPC is commonly used, it might not perform well in marine settings, where alternatives would be preferable.
Aggregates
Aggregates are another fundamental ingredient, often comprising a large part of the mix. Typically, aggregates are classified as coarse or fine, and their size affects the overall stability of the mortar. Coarse aggregates, like gravel, contribute strength and weight, while fine aggregates, such as sand, enhance cohesion and help in achieving a smooth finish.
When selecting aggregates, one must consider their cleanliness and size distribution. Impurities can compromise the integrity of the mix, leading to issues down the road. The unique feature about using high-quality aggregates in the mix is their ability to improve workability while minimizing shrinkage risks. However, the use of subpar materials can lead to drastic failures, making high-quality aggregates a worthy investment.
Water Quality
Water often plays a neglected role in the mix but it's pivotal to achieving optimal properties. The quality of water used can significantly influence the hydration process of the cement. Clear, clean water is essential; if the water contains impurities, it may hinder cement hydration and could lead to compromised strength.
Additionally, the ideal water-to-cement ratio is a crucial aspect to consider. Too much water can lead to a weaker mix and increased shrinkage, while too little can make it challenging to achieve desired consistencies. For instance, a well-controlled water mix results in stronger, more durable mortar.
Additives and Admixtures
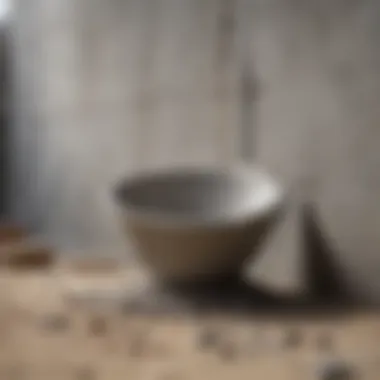
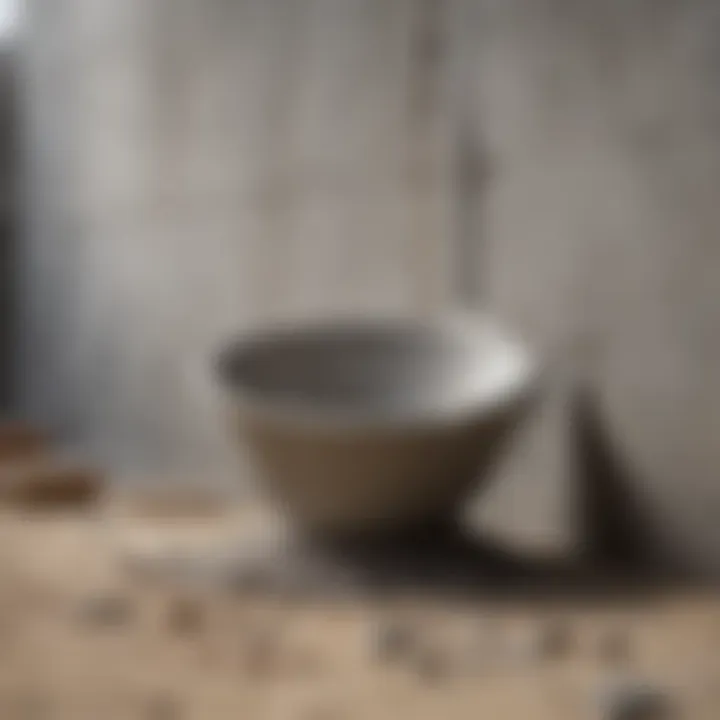
Plasticizers
Plasticizers are used to enhance workability without altering the water-to-cement ratio significantly. These additives can be a game-changer when working with high-strength mortar mixes that require a smooth application without excess water.
The key characteristic of plasticizers is their ability to allow for easier handling and placement. This is especially advantageous in projects where precision and finish are crucial. However, it's important to note that the overuse of plasticizers can lead to issues like increased shrinkage, therefore balance is essential.
Accelerators
In conditions where speed is of the essence, accelerators come into play. They hasten the setting time of mortar, which can be critical in colder environments or during tight project timelines. Calcium chloride is one of the commonly utilized accelerators, as it has been well-established in the industry.
While these additives are beneficial, they do come with cautions: they may increase the risk of cracking if not effectively managed. Knowing when and how to use them ensures that project deadlines are met without compromising the quality of the work.
Retarders
Conversely, there are instances where extending the setting time is necessary, and that’s where retarders come into play. These compounds are particularly useful in hot weather conditions where rapid curing can pose challenges. The smooth application of the mix can be achieved, allowing for the finer details to be executed properly.
An important detail is that while retarders add valuable time, they need to be used with care. Excessive use can lead to delayed strength gain, which might result in vulnerability during the initial curing phase. Balancing between different additives is thus essential for the desired outcome.
"Choosing the right mix is akin to laying a strong foundation; it dictates the success of the structure to come."
In summary, the composition of concrete mortar mix is more than just a mixture of ingredients; it's about achieving harmony among the elements that create a reliable and durable construction product. Selecting the appropriate cement type, aggregates, and water quality, along with the effective use of additives and admixtures, forms the groundwork for any successful plastering, tiling, or masonry work.
Properties of Concrete Mortar Mix
Understanding the properties of concrete mortar mix is essential for anyone involved in construction and repair projects. These properties significantly influence the performance and longevity of the structures built with mortar. Through grasping these characteristics, builders and engineers can make informed decisions that lead to optimal results.
Strength Characteristics
Strength is often the first trait that comes to mind when discussing concrete. For mortar mixes, this translates to the ability to withstand various loads without deforming or failing. Several factors contribute to the strength characteristics of a mortar mix:
- Cement Type: Different types of cement yield different strengths. For instance, Portland cement generally provides good compressive strength but may vary when mixed with others.
- Water-Cement Ratio: Striking the right balance here is crucial. Too much water can dilute the mix, leading to weaker bonds and reduced strength. On the flip side, a mix that’s too dry might not bond well.
- Age of Cure: Mortar gains strength over time, particularly with proper curing conditions. The initial hardening phase happens within a few days, but peaks several months later. A rule of thumb is that it often reaches full strength around 28 days.
Ensuring strength characteristics meet project specifications means evaluating these factors carefully and making necessary adjustments during the mixing process.
Durability Factors
Durability refers to a material's ability to withstand environmental factors over time. For concrete mortar mix, durability is paramount. External elements, such as weather changes, chemical exposure, or moisture, can drastically impact structure integrity. Consider these key components:
- Resistance to Environmental Stressors: Mortars need to be resistant to freeze-thaw cycles, especially in climates subject to extreme temperatures. This can often necessitate the inclusion of specific additives that enhance freeze-thaw resistance.
- Hydration Quality: Proper hydration during the curing process ensures that the cement particles fully interact with water. Inadequate curing can lead to surface scaling and shrinkage cracking, both detrimental to durability.
- Additives: Incorporating additives can enhance durability. For instance, using pozzolanic materials like fly ash can improve the long-term durability of mortar mixes by reducing permeability and enhancing resistance to sulfate attack.
Maintaining high durability standards safeguards structures from premature degradation, ultimately saving time and resources in repairs and replacements.
Workability and Consistency
Workability and consistency describe how easily a mortar mix can be manipulated during application. These properties are crucial for achieving smooth finishes and proper adhesion to surfaces:
- Consistency: This is influenced by the mix's proportion and ingredients. A well-balanced mix should have a uniform texture that allows for easy application.
- Workability: It's essential for tasks like troweling or filling joints; if a mix is too stiff, it makes application cumbersome. However, if it's too liquid, it might not hold its shape, leading to issues in the finished product.
- Additives: Plasticizers, for instance, can enhance workability without altering the overall water content of the mix. This is particularly beneficial in dense mixes that may otherwise be challenging to work with.
"In construction, the ease at which a material can be handled without compromising its integrity is critical. It's about finding the right balance in your mix."
Mixing Process of Concrete Mortar
Understanding the mixing process of concrete mortar is like knowing the secret recipe behind a beloved dish. It’s not just about tossing ingredients together willy-nilly; the method and precision of mixing influence the overall performance of the mortar. Properly mixed mortar ensures that your construction projects stand the test of time, making quality mixing essential. This section aims to dive deep into various approaches to mixing, emphasizing the advantages and considerations for each method.
Manual vs. Mechanical Mixing
When it comes to mixing concrete mortar, one finds oneself at a crossroads: manual mixing or mechanical mixing? Both methods have their place in construction, depending on the scale and requirements of the project.
- Manual Mixing: This approach is often favored for smaller projects, where the ease and simplicity of hand mixing can be beneficial. Manual mixing involves using tools like shovels or mixing boards. It requires a keen eye to achieve the proper consistency, which can be a dual-edged sword. While it's cost-effective and allows for direct control of the mix, it can be physically demanding and time-consuming. The quality might also hinge on the skill of the mixer.
- Mechanical Mixing: For larger projects or when consistency is paramount, mechanical mixers come into play. These machines can handle larger batches efficiently, providing a homogenous mix of materials. This technique reduces the risk of human error and ensures a repeatable quality. However, one must consider the upfront investment for equipment and the potential for mechanical failure.
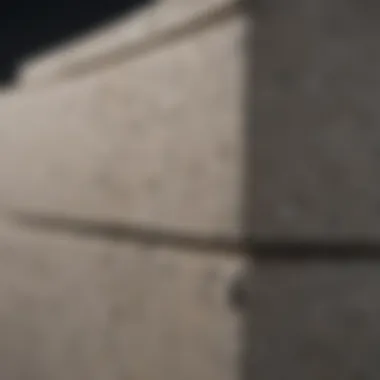
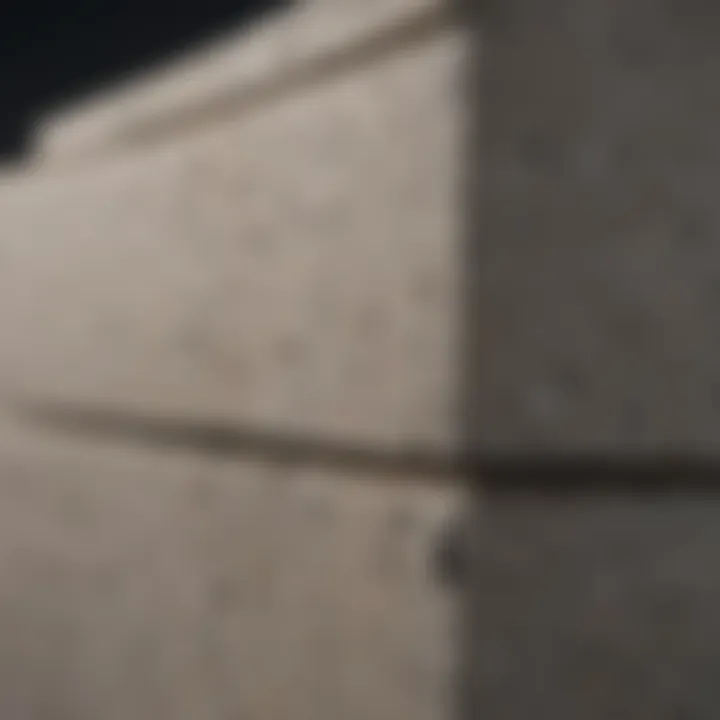
Ultimately, the choice between manual and mechanical mixing depends on project size, budget constraints, and consistency requirements.
Optimal Mixing Techniques
Achieving the right consistency in concrete mortar is akin to balancing a fine recipe. The way you mix can have a significant impact on performance and durability. Here are some optimal techniques to keep in mind:
- Pre-wet Aggregates: If you’re using dry aggregates, a good rule of thumb is to pre-wet them to achieve better hydration when mixing. This reduces the risk of segregation and promotes uniformity in the mix.
- Layering Ingredients: Start with dry ingredients, adding them in layers, then gradually mix in water. This technique helps achieve a more consistent blend and is particularly useful when hand mixing.
- Using a Mixing Ratio: Follow a mixing ratio for optimum results. A common ratio is one part cement, three parts sand, and roughly one part water, though this can vary based on specific project requirements. It’s essential to measure carefully.
- Mixing Duration: Don’t rush the mixing process. Take your time to ensure that all aggregates and ingredients are incorporated evenly. A well-mixed mortar gives you a stronger bond.
- Checking Consistency: The final test comes down to consistency. The mortar should be workable without being too wet or dry. A good test can involve taking a handful of the mix and seeing if it holds together without crumbling.
Using these optimal techniques will help you achieve a mortar mix that performs well under stress and meets the demands of your construction projects.
"Quality in a product or service is not what you put into it. It is what the customer gets out of it." - Peter Drucker
Paying keen attention to the mixing process is worth every ounce of effort. The proper mix translates directly to long-term performance, durability, and ultimately, the success of your projects.
Applications of Concrete Mortar Mix
The application of concrete mortar mix is a cornerstone of construction and renovation, as it bridges the gap between structural integrity and aesthetic appeal. Understanding its uses allows professionals to make informed decisions tailored to project demands. The versatility of concrete mortar makes it indispensable in both structural and non-structural applications. Let’s delve into specific areas where concrete mortar mix shines.
Structural Applications
Foundations
Foundations are the bedrock of any construction project, quite literally. They must withstand tremendous loads and provide stability for the entire structure. Concrete mortar mix plays a crucial role here since it offers remarkable compressive strength, ensuring that the building remains securely anchored to the ground. A defining characteristic of foundation work is the mix's ability to resist shrinkage, which helps reduce the likelihood of cracking over time.
In this context, concrete mortar's adaptability to various soil conditions makes it a sought-after choice among builders. A strong foundation can differentiate a solid structure from one that falters under stress. The unique aspect of using concrete mortar for foundations is its excellent bond with aggregates, leading to enhanced durability and longevity. However, one must not overlook the fact that poor curing practices can hinder these benefits, leading to future complications.
Load-Bearing Walls
Load-bearing walls are critical components that provide structural support, transferring loads from the roof to the foundation. Concrete mortar mix is particularly effective in this application due to its unmatched strength and resilience. An essential attribute of load-bearing walls is their ability to accommodate dynamic loads, such as wind or seismic activity, which poses a challenge in various regions.
The popularity of concrete mortar for load-bearing walls stems from its fire-resistant properties and long lifespan, contributing to building safety and lowering maintenance costs in the long term. One standout characteristic is the ease of achieving a consistent thickness—eliminating weak spots common in less competent mixes. Nonetheless, the design must carefully consider factors like thermal insulation and moisture resistance, which can be a double-edged sword if ignored.
Non-Structural Applications
Tiles and Stone Installation
The use of concrete mortar in tiles and stone installation is both practical and widespread. This application focuses on securing tiles to floors and walls, creating durable surfaces. The mix provides a robust binding quality that ensures tiles remain intact under foot traffic and exposure to moisture. A notable advantage is its flexibility in accommodating slight movements in substrate, preventing cracking.
The key feature of this application is how adjustable the mortar can be for different tile types. For instance, larger format tiles may require a different mixture to ensure adequate adhesion. Using a quality concrete mortar mix guarantees a professional finish, but it’s crucial that the installer pays attention to the right thickness and the type of notched trowel to maximize adhesion. Failure to consider these details can lead to significantly shortened lifespan for the installed tiles.
Repair Work
Repair work is where concrete mortar truly demonstrates its utility, serving as the savior for cracks and damage in various surfaces. Whether fixing a chipped driveway or mending a deteriorating patio, the right mortar mix can restore functionality while often improving aesthetics. Concrete mortar’s quick-setting properties ensure that repairs can be completed promptly, minimizing disruption.
One critical aspect of using mortar for repair is the compatibility with the existing material. A well-chosen product will expand and contract in tandem with the original substrate, mitigating the risks of further damage. While it’s a beneficial choice for maintaining structures, attention must be given to selecting the appropriate mix type for specific situations. Neglecting this aspect could result in repairs that don’t hold up against environmental factors, ultimately leading to more costly fixes in the future.
Common Challenges in Concrete Mortar Mix
In the complex world of concrete mortar mix, not everything is smooth sailing. Understanding the challenges can pave the way for effective solutions, ensuring that your projects don’t turn into a saga of mistakes. Addressing these common challenges leads to more robust structures, minimized repairs, and overall satisfaction with the final product.
Concrete mortar is a blend that caters to a variety of applications, yet the issues that arise are often too frequent for comfort. With a thorough grasp of these pitfalls, both seasoned builders and new enthusiasts can take steps to mitigate any negative impact on their work.
Shrinkage and Cracking
One of the primary concerns while working with concrete mortar mix is shrinkage and cracking. As the mortar dries, it undergoes a natural process of contraction, which, if not monitored, can lead to unsightly cracks. These cracks are more than just cosmetic issues; they can compromise the integrity of the structure.
Key Factors Contributing to Shrinkage:
- Water Content: Excessive water in the mix can lead to increased shrinkage.
- Cement Type: Some types of cement are more prone to shrinkage than others.
- Environmental Conditions: High temperatures or windy conditions can accelerate moisture loss, influencing the drying behavior.
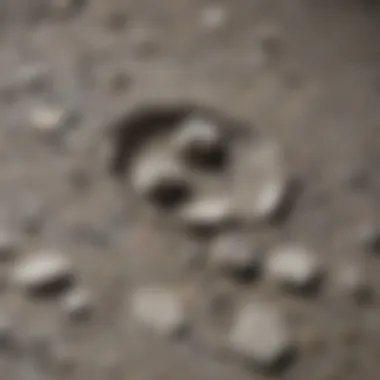
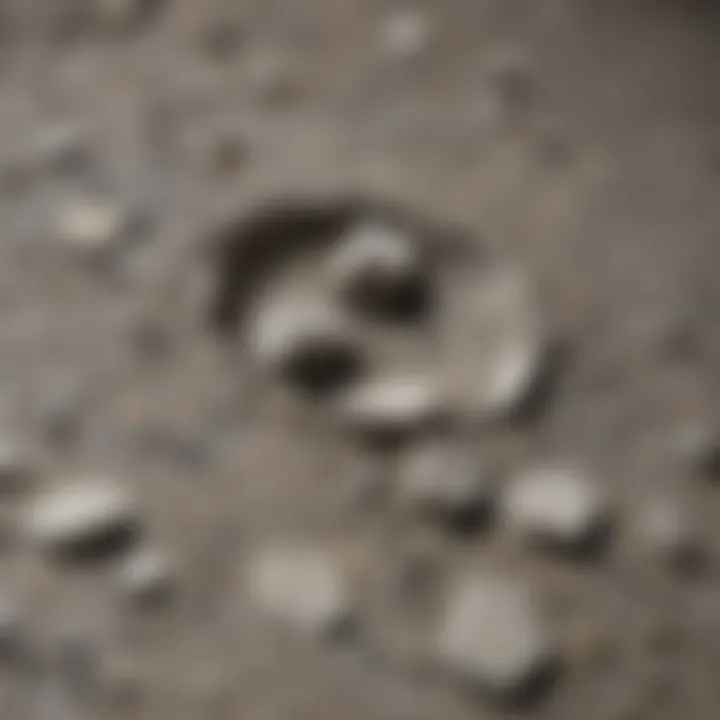
"High proportions of water can set the stage for a cracking mess. Less is often more when it comes to hydration."
To combat this issue, you can implement strategies such as incorporating shrinkage-reducing admixtures or ensuring adequate curing. Keeping the application consistently moist during the initial drying stages can also help minimize cracks and ensure a sturdy finish.
Bleeding and Segregation
This one is a real kicker! Bleeding and segregation not only affect the appearance of your mortar but can also severely impact its structural performance. Bleeding refers to the phenomenon where water rises to the surface of a freshly placed mix. This can lead to a weaker surface layer, making it susceptible to cracking and crumbling over time.
Signs of Bleeding:
- Puddles of Water: Water pooling on the surface is a clear indicator.
- Darker Spots: Areas that appear darker might be saturated with excess water.
Segregation, on the other hand, occurs when the heavier aggregates settle to the bottom, leaving a weaker mortar mix on the top. Proper mixing techniques, correct proportioning of materials, and the right choice of aggregates go a long way in preventing these issues.
Preventive Measures Include:
- Optimal Mixing: Ensure thorough mixing so components stay evenly distributed.
- Right Admixtures: Use water-reducing admixtures to control bleeding.
- Backfilling Techniques: Handle the placement of mortar with care to avoid disturbance that could cause segregation.
Ultimately, cultivating an awareness of these challenges and their implications can ensure that your projects run more smoothly. Learning to recognize and address shrinkage, cracking, bleeding, and segregation can lead to better quality control. Fine-tuning your approach in these areas will significantly elevate the quality of your work, making the difference between a mediocre project and an exceptional one.
Best Practices for Concrete Mortar Mix
Ensuring the best quality in concrete mortar mix is vital for achieving durability and effectiveness in construction projects. This section emphasizes the importance of best practices that can significantly reduce common issues while improving overall performance. When one includes thorough quality control measures and adheres to proper site preparation guidelines, it can lead to smoother mixing processes, better adherence of materials, and longer-lasting results.
Quality Control Measures
Quality control in concrete mortar mix involves several essential steps to make sure the mix is up to par with industry standards. Below are some key measures that should be taken into account:
- Material Inspection: It's crucial to verify that all ingredients meet the specified standards. Not only does this ensure performance, but it also mitigates the risk of structural failures.
- Batch Testing: Taking samples from each batch allows for ongoing monitoring of consistency. Tests can include slump tests to evaluate workability, as well as compressive strength tests.
- Environmental Conditions: It is important to be mindful of the surrounding environment during mixing and placement. High temperatures or moisture levels can adversely affect the curing process, leading to unexpected results.
These quality control measures foster a culture of diligence and rigorous attention. They also serve as foundational practices that guide the mixing and application process.
"Proper oversight minimizes errors and promotes reliability."
Site Preparation Guidelines
Before beginning any mixing process, thorough site preparation is paramount. This ensures not only effectiveness but also safety for workers involved. Here are some guidelines to consider:
- Clean Work Area: Remove debris and contaminants from the site. A clean environment reduces the chance of foreign materials interfering with the mix.
- Leveled Substrate: Ensure that the surface where the mortar will be applied is even and free of any obstructions. Uneven surfaces can negatively impact the adhesion of the mortar mix.
- Moisture Control: Assess the moisture levels of the substrate. Dry surfaces may absorb water from the mortar, while wet surfaces can lead to excess moisture, affecting bonding.
When one prepares the site thoroughly, it substantially minimizes problems during application, truly allowing the materials to shine in their intended use. Focusing on these best practices ultimately leads to more efficient construction processes and heightened structural integrity.
The Future of Concrete Mortar Mix
The progression of concrete mortar mix technology is critical for various reasons. As construction demands evolve, it becomes increasingly necessary to innovate and adapt materials and methods. The importance of this topic lies not only in enhancing performance but also in addressing sustainability concerns and meeting regulatory standards. The future focuses on developing new materials, optimizing current processes, and considering environmental impacts, all while ensuring durability and cost-effectiveness in construction projects.
Innovations in Materials Science
Innovative breakthroughs in materials science are pivotal for the future landscape of concrete mortar mix. Researchers are exploring a variety of novel ingredients that could enhance performance characteristics.
- Self-Healing Materials: This involves embedding microcapsules within cement that can release healing agents when cracks occur. The result is a longer-lasting structure that can self-repair without human intervention.
- Recycled Materials: The inclusion of recycled aggregates or recycled water in the mix not only reduces waste but also minimizes the carbon footprint of concrete production. Using up to 30% recycled materials has showed promising outcomes in maintaining strength while being environmentally friendlier.
- Nanotechnology: Introducing nanoparticles into the mortar can significantly improve strength, durability, and resistance to various environmental factors. These materials often enhance the hydration process of the mix, leading to a denser, more stable final product.
Furthermore, continuous research and testing are ongoing to fine-tune these innovations, ensuring they meet safety and compliance standards required in construction.
Sustainability Considerations
Sustainability is no longer just a buzzword; it's a fundamental aspect shaping the future of concrete mortar mix. The construction industry is largely responsible for greenhouse gas emissions, so rethinking how we mix and apply concrete is essential for a greener future.
- Eco-Friendly Additives: Utilizing additives like fly ash or slag not only increases the performance of the mix but also recycles industrial byproducts. This reduces the need for new materials and helps in lowering environmental impacts.
- Lower Carbon Cement: Developing cement that requires less energy to produce, such as geopolymer cements or alternative formulations, dramatically reduces emissions involved in concrete production.
- Reducing Waste in Mix Design: Implementing better mix designs that account for specific project requirements can minimize waste, ensuring every ingredient contributes effectively rather than contributing to excess.
Achieving sustainability in the concrete industry requires a shift in mindset. It’s about more than just measuring outcomes, it’s a commitment to altering how we build. As awareness grows, project stakeholders will be challenged to integrate these sustainable practices into their work, ensuring that what they build today will also stand firm for future generations.
"Innovating for today’s construction means remembering that tomorrow's structures need to be as thoughtful as they are durable."
By focusing on materials science innovations and sustainability considerations, the future of concrete mortar mix is poised for transformation, paving the way for a more resilient and eco-conscious construction landscape.