Understanding DFAM in Modern Additive Manufacturing
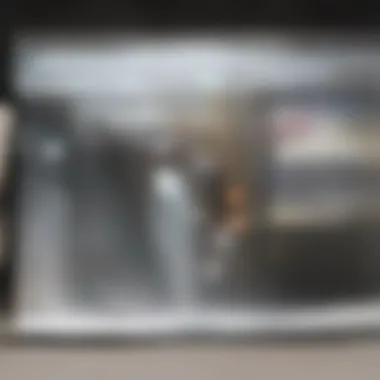
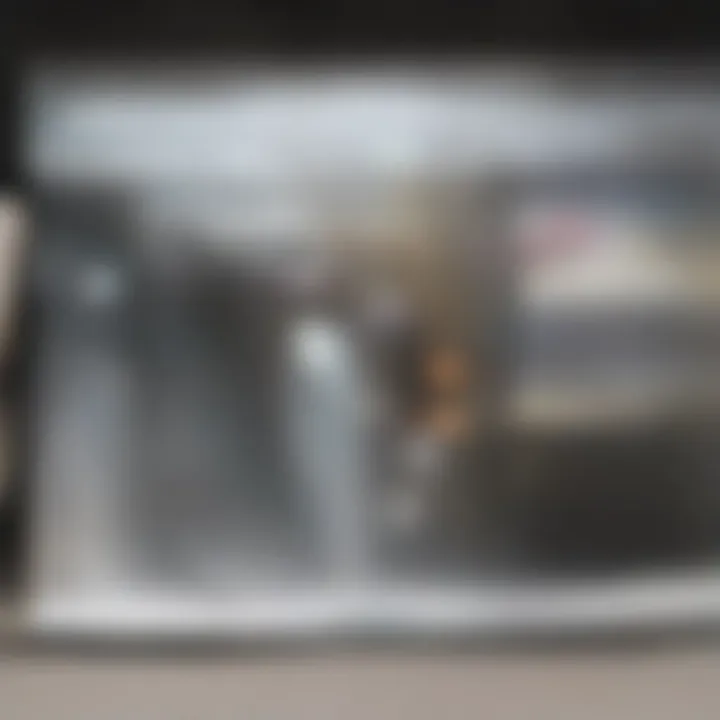
Intro
Design for Additive Manufacturing (DFAM) has emerged as a significant area of study in the realm of modern manufacturing. As industries increasingly adopt additive techniques, understanding and optimizing designs for these processes becomes vital. This section will shed light on the importance of DFAM and set the stage for a deeper exploration into its principles and applications.
DFAM refers to the process of designing products specifically for additive manufacturing. The approach differs from traditional manufacturing methods due to the unique capabilities and constraints of additive processes. With a focus on optimizing designs for 3D printing, DFAM seeks to enhance product performance while also reducing material waste and production costs.
As the field of additive manufacturing continues to grow, the relevance of DFAM cannot be overstated. It facilitates innovation in product design, leading to more efficient manufacturing workflows and more sustainable practices. Understanding DFAM's principles can empower professionals and students alike to harness the full potential of additive manufacturing techniques.
In the sections that follow, we will examine the larger context of DFAM through a review of existing literature, explore its foundational principles, and discuss the methodologies used to implement effective DFAM practices.
Understanding DFAM
Design for Additive Manufacturing (DFAM) presents a pivotal framework within the realm of modern manufacturing. It emphasizes the integration of design parameters with the capabilities of additive manufacturing technologies. This alignment not only enhances the efficacy of the production process but also mitigates potential pitfalls in design and manufacturing. By grasping the core principles of DFAM, stakeholders can unlock numerous benefits that influence both the design process and the eventual output of products.
The importance of DFAM can be encapsulated in its ability to enable more innovative designs that traditional manufacturing processes may not accommodate. The iterative nature of design inherent in additive manufacturing presents a unique opportunity for designers. They can explore complex geometries and structures while maintaining an efficient production cycle. This flexibility leads to significant cost savings and shorter timeframes, thereby allowing for a faster time to market and a competitive edge.
Furthermore, understanding DFAM entails recognizing specific design considerations that arise during the additive manufacturing process. Designers need to think about support structures, material properties, and potential design limitations, which may differ vastly from conventional production methods. This understanding fosters a more profound respect for the manufacturing process itself and enhances coordination between design and production teams.
Definition and Importance
DFAM refers to the strategic approach to designing parts and products in a way that maximizes the advantages of additive manufacturing technologies. It involves understanding the characteristics of 3D printing, such as layer-by-layer construction and the use of varied materials, to inform design decisions.
The importance of DFAM lies in its direct link to manufacturing efficiency. When designed with additive methods in mind, products can exhibit reduced weight, improved performance, and lower material waste. Examples in industries like aerospace demonstrate that DFAM can lead to components that are not only lighter but also stronger, thereby improving overall product functionality.
Historical Context
The concept of DFAM did not evolve overnight. It emerged alongside the advancement of additive manufacturing technologies, which began gaining traction in the late 1980s. Originally, 3D printing was primarily utilized for rapid prototyping, allowing designers to quickly visualize their concepts. However, as the technology matured, the potential applications expanded.
The historical timeline showcases a gradual recognition of the need for design principles tailored to additive manufacturing. In the 1990s, early adopters began experimenting with more intricate designs, realizing that traditional design methods often fell short of utilizing the full capabilities of 3D printing. Multiple industries recognized the necessity of educating designers on best practices specific to additive manufacturing.
Developments over the past two decades have led to more sophisticated tools and software that facilitate DFAM. As educational institutions and companies have integrated these concepts into their curriculums and training programs, a body of knowledge has emerged. Consequently, practitioners in the field now have access to resources that emphasize the interplay between design and additive technologies.
In summary, understanding DFAM is essential for leveraging the advantages offered by additive manufacturing. As the landscape continues to evolve, staying abreast of the historical context helps design professionals prepare for future innovations while marketplace demands shift.
Principles of DFAM
Understanding the principles of Design for Additive Manufacturing (DFAM) is essential for maximizing the benefits of additive manufacturing processes. It lays the foundation for creating optimized designs that can be efficiently manufactured, thereby enhancing productivity and reducing costs. The principles guide designers in integrating the unique capabilities of additive technologies into their workflows. They help to underline the importance of rethinking traditional design approaches to fully exploit the advantages offered by these advanced manufacturing methods.
Key Design Considerations
When engaging with DFAM, several key design considerations should be addressed. These include:
- Functionality: The design must serve its intended purpose effectively. This requirement should be at the forefront of any additive manufacturing project.
- Build Orientation: The orientation in which a part is printed affects its strength, surface finish, and overall quality. Understanding how different orientations can impact the final product is critical.
- Support Needs: Identifying areas of a part that will require supports during printing is crucial to streamline the building process. Minimizing unnecessary supports can save material and decrease post-processing time.
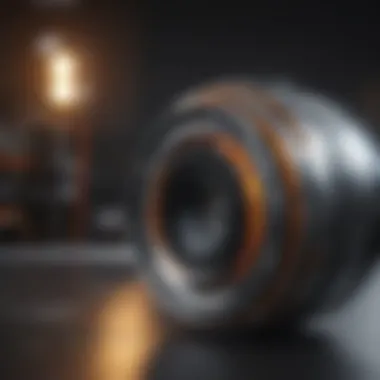
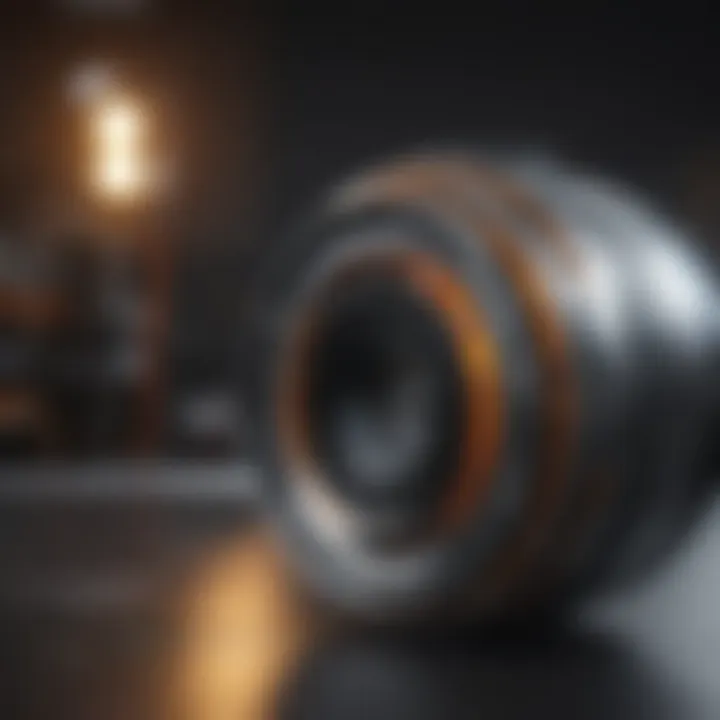
These considerations help drive more efficient and effective design choices that result in better end-products.
Material Selection
Material selection is another pivotal element of DFAM. Different materials behave differently during the additive manufacturing process. Factors to consider include:
- Material Properties: Understanding the physical and mechanical properties of materials is essential. Key attributes like tensile strength, flexibility, and thermal stability need careful evaluation.
- Cost of Materials: Budget constraints must be factored into the material selection. Some advanced materials, like titanium or certain polymers, may be costly compared to conventional materials.
- Compatibility with Technology: Not all materials can be used with every type of additive manufacturing technology. It is important to ensure that the chosen material is compatible with the specific printing method utilized.
Effective material selection can significantly influence the performance and viability of the final product.
Geometric Freedom
One of the most significant advantages of additive manufacturing compared to traditional methods is geometric freedom. This principle allows for:
- Complex Geometries: Designers are not limited by the constraints of traditional manufacturing processes. They can create intricate shapes and structures that would be impossible or prohibitively expensive to achieve using conventional methods.
- Internal Features: Additive manufacturing allows the inclusion of internal channels or structures which can enhance performance. For example, complex cooling channels in aerospace components can be designed to improve efficiency.
- Reduced Weight: Parts can be designed to be lighter without sacrificing strength, which is particularly beneficial in sectors such as aerospace and automotive.
This geometric freedom is a game changer in product design, enabling innovation that directly correlates with manufacturing efficiency and performance enhancement.
In summary, mastering the principles of DFAM is vital. Key design considerations, meticulous material selection, and leveraging geometric freedom all contribute to producing high-quality parts that meet or exceed performance standards. By embracing these principles, industries can significantly improve their production capabilities.
Techniques in DFAM
The role of techniques in Design for Additive Manufacturing (DFAM) cannot be overstated. These techniques dictate how designs are optimized for production using additive methods. By employing various approaches, manufacturers can significantly enhance the functionality and efficiency of their products. As industries continue to evolve, understanding these techniques provides a competitive edge.
Topology Optimization
Topology Optimization minimizes material use while maintaining structural integrity. This method calculates the best possible layout for a component based on performance criteria. It takes into account factors like loads, constraints, and manufacturing methods. As a result, companies can produce lighter and stronger parts, which translates into savings in both materials and costs.
Implementing topology optimization leads to designs that traditional manufacturing would struggle to create. The software simulates stresses and allows designers to visualize material flow. With a focus on functionality, topology optimization enables new opportunities, especially in fields like aerospace and automotive industries.
Lattice Structures
Utilizing lattice structures in designs is an innovative approach inherent to DFAM. Lattices are lightweight and can provide superior strength-to-weight ratios. They consist of repeating patterns that create a web-like geometry. Their design can be tailored to fit specific applications, providing necessary support while minimizing excess material.
Lattice structures also enhance thermal management and airflow, making them ideal for applications in industries like automotive and HVAC. This adaptability allows for customization in the final product, which can be crucial in fields such as biomedical applications where precise specifications are needed. The design flexibility of lattice structures is one of the key advantages of DFAM techniques.
Support Structures
Support structures are essential in additive manufacturing. These structures assist during the printing process, especially when creating complex geometries. They provide stability and prevent deformation of the primary component. Once printing is complete, these supports can often be removed easily, leaving a clean and functional part.
Choosing the right type and amount of support can impact the overall quality of the final product. Striking a balance between adequate support and material efficiency is crucial. Different materials may require varying approaches to support structures. Understanding the dynamics here enhances the outcome of the print.
"The right support structure can make or break an additive manufacturing project."
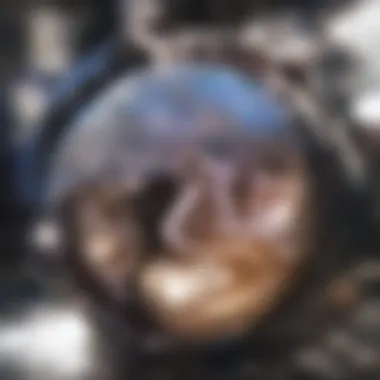
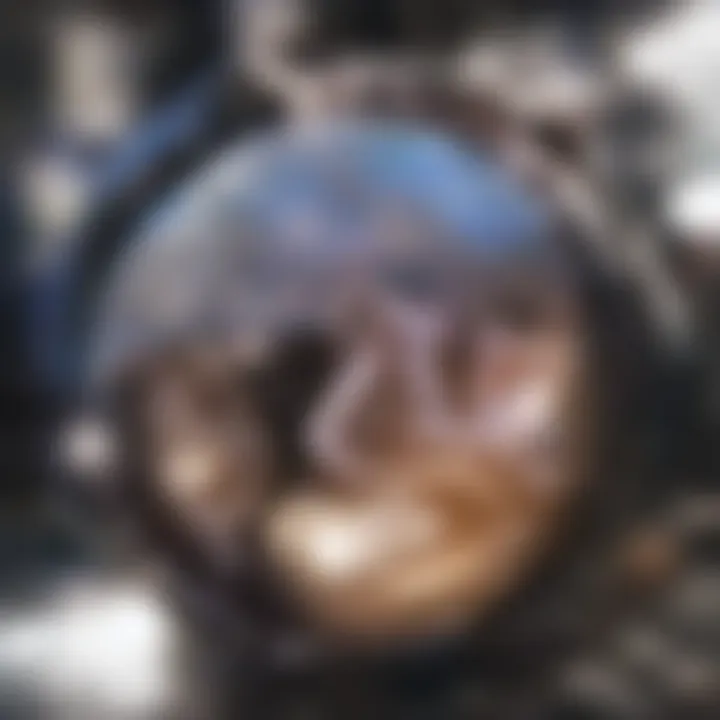
In summary, techniques like topology optimization, lattice structures, and support structures form the backbone of effective DFAM. By mastering these elements, professionals can produce high-quality components efficiently, leading to advancements across many industries.
Applications of DFAM
Design for Additive Manufacturing (DFAM) has transcended from a theoretical framework to a practical necessity across various industries. Its applications are vital because they can drastically enhance the efficiency of manufacturing processes, optimize material use, and reduce lead times. By leveraging DFAM principles, companies can create components that were previously impossible to produce using traditional methods. This section outlines the specific applications of DFAM in key sectors, emphasizing their unique benefits and considerations.
Aerospace Industry
The aerospace sector significantly benefits from DFAM practices. Parts produced with additive manufacturing can be lighter in weight while retaining strength, which is essential for enhancing fuel efficiency. For instance, GE Aviation manufactures fuel nozzles using DFAM techniques, which has resulted in parts that are 25 percent lighter than before without compromising structural integrity. Additionally, DFAM allows for the integration of complex geometries that help in reducing part count and assembly time.
DFAM strategies lead to significant weight reductions in aerospace components, contributing directly to lower emissions and operational costs.
Automotive Sector
In the automotive industry, DFAM enables rapid prototyping and the production of intricate parts. Manufacturers like Audi utilize DFAM to produce prototypes quickly, allowing for faster iterative design processes. It enables customization of components tailored to specific customer needs, which is increasingly becoming a priority in today's automotive market. Moreover, the reduction in material waste and lead times provides a competitive edge in the highly dynamic automotive landscape.
- Customization: Tailored components for performance.
- Reduced Waste: Efficient use of materials leads to cost savings.
- Faster Prototyping: Accelerates the development cycle.
Medical Devices
The medical device industry is another area where DFAM demonstrates transformative potential. Custom implants and prosthetics can be manufactured using technique that factors in the specific anatomy of individual patients. For example, companies like 3D Systems have developed tailored surgical guides and implants that fit patients more accurately than standard options. This customization helps improve patient outcomes and satisfaction while reducing the risk of complications during surgeries.
Consumer Products
In the consumer products sector, DFAM has allowed for the production of personalized items with complex designs. Brands like Nike have utilized 3D printing to create customized footwear, which caters to individual styles and requirements. DFAM facilitates smaller production runs, allowing businesses to test new concepts without large upfront investments. The direct-to-consumer model becomes more viable when products can be tailored quickly and precisely.
- Personalization: Products that reflect individual tastes.
- Cost-effective Prototyping: Small runs and adjustments are feasible.
- Innovative Designs: Ability to explore complex structures.
Challenges in DFAM
The concept of Design for Additive Manufacturing (DFAM) must address several challenges. Understanding these obstacles is critical for optimizing design processes and ensuring effective implementation within various industries. The journey into DFAM brings forth unique design limitations, material constraints, and cost implications. These challenges, while formidable, also present opportunities for innovation and improvement in additive manufacturing practices.
Design Limitations
In DFAM, the design limitations often stem from the inherent characteristics of additive manufacturing technologies. Traditional design principles may not easily translate into the 3D printing domain. The shape complexity allowed by additive manufacturing can lead to unexpected challenges. For example, overhangs that seem feasible in virtual designs may not hold during the printing process. Geometric intricacies must be understood to avoid print failures, which could otherwise waste time and resources.
Another significant aspect is the orientation of the part during printing. Different orientations can affect the strength and quality of a printed component in a pronounced way. Designers often must experiment with multiple orientations to find the most effective one, which can complicate the design workflow. Additionally, material bonding properties change based on layer by layer deposition, influencing the final structure. Thus, designers must embrace a new set of limitations not traditionally found in subtractive manufacturing.
Material Constraints
The material selection in DFAM is a crucial determinant of the process's success. Each additive manufacturing method has specific compatible materials. For example, Fused Deposition Modeling typically uses thermoplastics, while Powder Bed Fusion can utilize metals or polymers. Designers need to have an in-depth understanding of the material properties, such as tensile strength, flexibility, and thermal resistance.
Furthermore, the choice of material can impose limits on design adaptability. Some materials may not lend themselves well to intricate designs due to their flow properties during printing or their post-processing requirements. Different materials behave distinctly under similar stresses, so selecting the correct material is paramount. Designers must keep in mind the end-functional requirements while choosing materials.
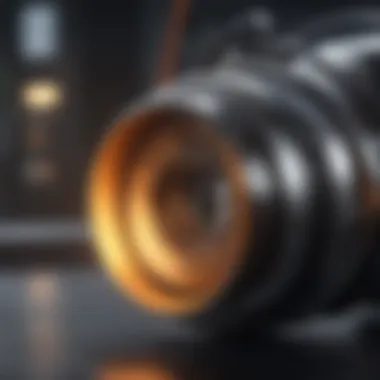
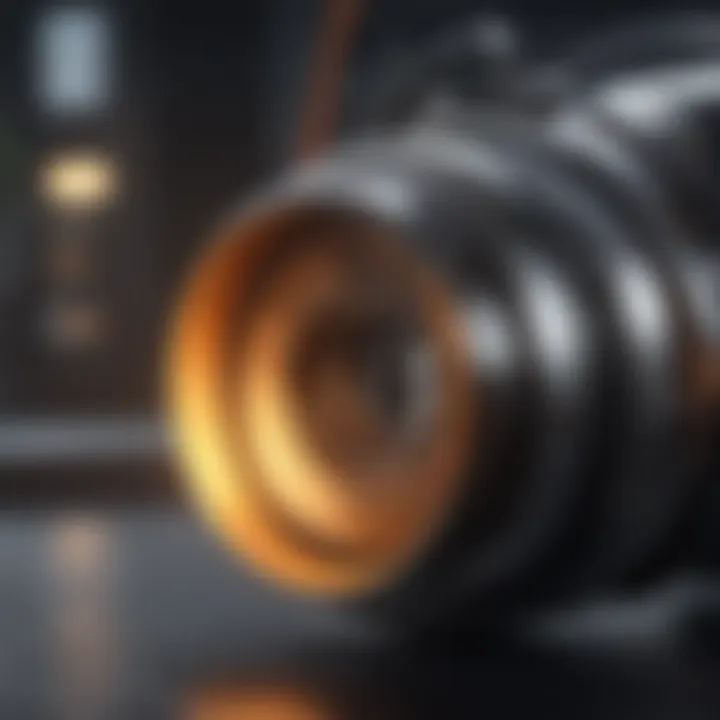
Cost Considerations
Economics play an essential role in the decision-making process for implementing DFAM. While additive manufacturing can potentially reduce costs by minimizing waste and shortening lead times, there are also factors that can end up being expensive. The initial setup costs can be substantial. Specialized equipment, such as high-end 3D printers, requires significant investments, particularly for industries like aerospace and medical devices.
Moreover, more complicated designs may lead to longer print times. While traditional methods often rely on minimum material removal, additive techniques can introduce new efficiencies as well as unforeseen costs. Maintaining a balance between creating optimized designs for performance and controlling production expenses is crucial for businesses. In projects where the cost exceeds budget expectations, evaluating design strategies becomes necessary to ensure the viability of projects.
"Successful implementation of DFAM hinges on understanding and overcoming design limitations, material constraints, and cost considerations collectively."
Future of DFAM
The future of Design for Additive Manufacturing (DFAM) is an essential component in the ongoing evolution of additive manufacturing technologies. As industries increasingly realize the advantages of 3D printing, DFAM will play a pivotal role in shaping design methodologies that can leverage these technologies. Understanding the future of DFAM means recognizing the potential benefits such as increasing design complexity, reducing material waste, and facilitating more sustainable manufacturing practices. Overall, it is crucial for advancing product development processes across various sectors.
Emerging Trends
Several emerging trends are influencing the future of DFAM. One notable trend is the integration of artificial intelligence in design processes. AI algorithms can analyze historical design data to suggest optimal structures and configurations. This leads to faster design iterations and improved efficiency in the development process.
Another trend is the growing emphasis on sustainability. Manufacturers are now more aware of their environmental footprint. In response, they are adopting practices that not only minimize waste but also incorporate recyclable materials into their designs. This shift towards eco-conscious design is becoming a norm in the industry.
Additionally, customization is becoming increasingly significant. Consumers today prefer products tailored to their needs, and DFAM enables manufacturers to provide customized solutions without overwhelming production timelines. As end-users demand personalization, manufacturers must adapt their design approaches to incorporate DFAM techniques.
Technological Innovations
Technological innovations are crucial in advancing DFAM practices. Continuous developments in printer technology have led to improved precision and the ability to work with a broader range of materials. For instance, advancements in metal 3D printing technologies, such as Direct Metal Laser Sintering, are expanding capabilities in industries like aerospace and medical devices.
Moreover, software tools that simplify the design process are evolving. Tools such as CAD (Computer-Aided Design) software specifically tailored for additive manufacturing allow designers to visualize complex geometries effectively. This streamlining improves productivity and enables a smoother transition from design to production.
The cloud-based platforms for collaborative design also represent an important innovation. These platforms allow teams to work together on designs remotely, sharing insights and feedback in real-time. This fosters collaboration and leads to better design outcomes across geographically dispersed teams.
Overall, the future of DFAM is rife with opportunities. By embracing emerging trends and leveraging technological innovations, industries have the potential to optimize their manufacturing processes, achieving greater efficiency and responsiveness to market demands. The development of DFAM will undoubtedly reshape how products are designed and produced in the years to come.
End
The conclusion of this article serves as an important recap and reflection on the significance of Design for Additive Manufacturing (DFAM). This concept plays a pivotal role in shaping the future of additive manufacturing, making it essential to understand the benefits and considerations associated with it.
DFAM enhances production by streamlining the design process, which ultimately leads to greater efficiency. By embracing key principles like geometric freedom and optimized material selection, manufacturers can achieve superior results while minimizing waste and costs. This topic is vital as it combines theoretical knowledge with practical implications, showcasing the transformative power of additive manufacturing techniques across various industries.
Summary of Key Points
- Understanding DFAM: The concept of DFAM revolves around optimizing designs for additive manufacturing processes, ensuring materials and shapes are efficient for production.
- Principles and Techniques: Key considerations include topology optimization, effective material selection, and the use of lattice structures that promote strength while reducing weight.
- Applications Across Industries: DFAM has made significant contributions to industries like aerospace, automotive, and medical devices, showcasing its adaptability and essential role in innovation.
- Challenges and Future Directions: While there are challenges such as design limitations and cost constraints, emerging trends and technological innovations promise to overcome these barriers and enhance its application.
The discussions documented in this article highlight the ongoing evolution of DFAM as a crucial element in the additive manufacturing landscape.
Final Thoughts on DFAM
The examination of DFAM reveals that this approach is not just relevant, but critical to the sustainability and growth of additive manufacturing. As industries continue to evolve, those adopted with DFAM principles are likely to maintain a competitive edge.
Understanding DFAM fosters better dialogue among students, researchers, and professionals. It encourages a forward-thinking approach towards design and manufacturing that is adaptable and innovative. For anyone involved in additive manufacturing, grasping DFAM is essential in navigating the complexities of modern production landscapes. The future promises to be shaped by these insights, providing a framework for success in design and manufacturing endeavors.
"As the manufacturing landscape shifts, embracing DFAM is indispensable for anyone looking for efficiency and excellence in production."
By thoroughly understanding the principles and practices of DFAM, stakeholders can position themselves at the forefront of this ever-changing field, ensuring that they play an impactful role in the next chapter of additive manufacturing.