Understanding HFC-134a Compressors: Overview & Insights
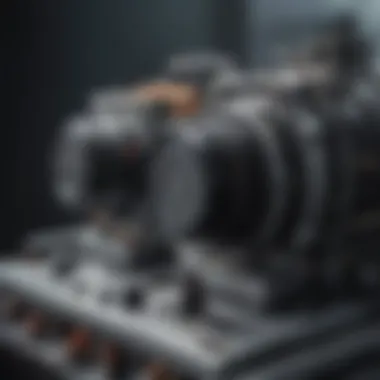
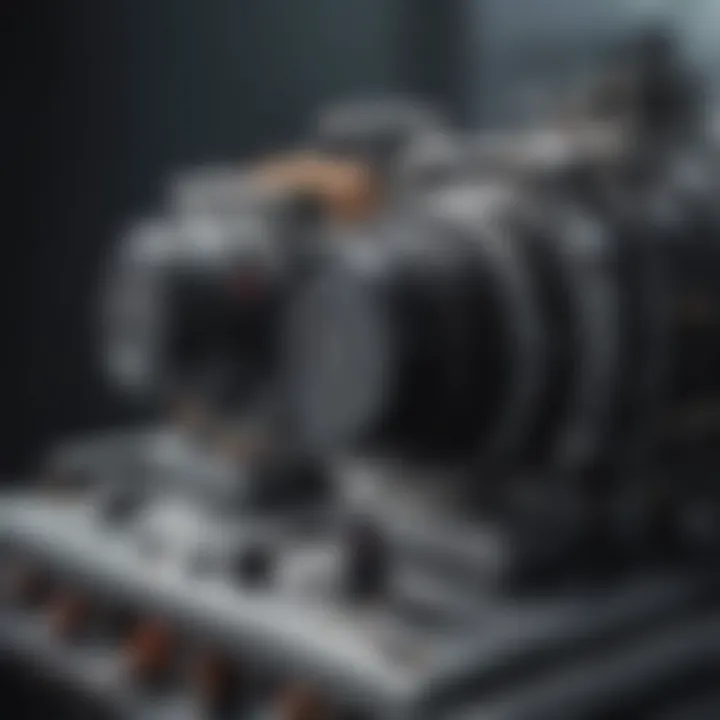
Intro
Understanding the role of HFC-134a compressors is crucial in modern HVAC systems. These compressors have become standard in the refrigeration industry. They are renowned for their efficiency and reliability. Their mechanics, however, are often overlooked in favor of general discussions about HVAC technology.
This article will delve into various aspects of HFC-134a compressors. It will explore their mechanisms, applications, and innovations that enhance their functionality. By providing comprehensive insights, we aim to illuminate the importance of HFC-134a in both past and present environmental considerations, regulatory impacts, and trends toward new alternatives.
Research Context
Background and Rationale
HFC-134a, or 1,1,1,2-tetrafluoroethane, is a synthetic refrigerant. It has been widely utilized since the late 20th century. Various factors led to its widespread adoption. It is less harmful to the ozone layer than previous refrigerants. However, its contribution to global warming has raised concerns among environmentalists and regulators.
The rationale for this study is twofold. First, to investigate the mechanics of HFC-134a compressors, which play a pivotal role in their efficiency. Second, to assess the implications of current regulations surrounding HFC-134a and its alternatives.
Literature Review
Previous studies have focused on several key areas regarding HFC-134a compressors. They include design optimization, performance metrics, and environmental impacts. Research by various authors indicates that advances in compressor technology can lead to significant gains in energy efficiency. For instance, modifications in design or operational parameters can reduce energy consumption by as much as 20%.
Additionally, literature points to an increasing shift toward natural refrigerants. These alternatives include hydrocarbons and carbon dioxide. While some studies cast doubt on the viability of transitioning away from HFC-134a, they also underline its pervasive use in the market today. Moreover, the global phasing out of HFCs under the Kigali Amendment necessitates understanding both HFC-134a's capabilities and limitations.
Methodology
Research Design
This article utilizes a qualitative research design. It synthesizes existing literature and industry reports. It also includes interviews with HVAC professionals to obtain firsthand insights. This comprehensive approach allows for a rounded perspective on HFC-134a compressors.
Data Collection Methods
Information for this study derives from multiple sources:
- Peer-reviewed journals on HVAC technologies.
- Industry reports on refrigerant regulations and advancements.
- Insights from HVAC professionals and manufacturers.
- Online resources such as articles from Wikipedia, Britannica, and discussions on platforms like Reddit to provide casual yet informative viewpoints.
Through these methods, the article aims to present an accurate depiction of HFC-134a compressors, highlighting their significance in the HVAC landscape.
Prelims to HFC-134a
HFC-134a, or 1,1,1,2-Tetrafluoroethane, plays a central role in modern refrigeration and air conditioning systems. Its significance cannot be overstated, as it provides effective thermal management while adhering to increasingly stringent environmental regulations. This refrigerant is non-flammable and has favorable thermodynamic properties, making it a standard in many applications. Understanding HFC-134a is essential to grasp both its technical functionality and the implications of its use.
The importance of HFC-134a arises not only from its chemical properties but also from broader considerations related to global warming. With rising environmental concerns, HFC-134a has come under scrutiny due to its global warming potential. This makes the study of its characteristics vital for anyone involved in the HVAC industry.
Chemical Properties of HFC-134a
HFC-134a possesses specific chemical characteristics that make it suitable for its applications. It has a boiling point of -26.1°C, which allows it to function effectively in diverse temperature ranges. The refrigerant is classified as a saturated fluid at atmospheric pressure, exhibiting properties that facilitate heat transfer processes.
Its molecular structure contributes to its low toxicity and non-corrosive behavior, making it a safer option than many alternatives. HFC-134a has a relatively low ozone depletion potential, which has provided some environmental advantage over older refrigerants like CFCs. However, despite these benefits, HFC-134a still presents environmental challenges, particularly concerning its contribution to greenhouse gas emissions. These aspects must be evaluated when considering the refrigerant's continued usage in the face of evolving regulations.
Historical Development and Usage
The historical context of HFC-134a is crucial for understanding its evolution. Developed in the late 1980s, HFC-134a was introduced as a substitute for CFC-12, which was phased out due to its harmful effects on the ozone layer. The adoption of this refrigerant was driven by regulatory frameworks such as the Montreal Protocol, which advocated for alternatives to ozone-depleting substances.
Initially, HFC-134a gained traction in the automotive sector, being widely implemented in air conditioning systems. Its reliability and efficiency solidified its position in various refrigeration applications, from domestic units to commercial refrigeration systems. As market dynamics changed, HFC-134a became a staple in many industrial refrigeration contexts, reflecting its adaptability.
In recent years, the industry has seen shifts in technology and regulation affecting HFC-134a's continued use. Proposals for HFC phase-downs and calls for adopting newer, more sustainable refrigerants reflect an ongoing evolution. This historical development underscores the importance of staying informed about both the technical attributes and the regulatory landscape surrounding HFC-134a.
"HFC-134a is not just a refrigerant; it is part of a broader narrative that includes environmental awareness and technological innovation."
In summary, the introduction to HFC-134a covers critical aspects of its chemical properties and historical significance. This foundation sets the stage for exploring the mechanics, applications, and innovations related to HFC-134a compressors throughout the remainder of the article.
Fundamentals of Compressors
The fundamentals of compressors are crucial for understanding the efficiency and functionality of systems that use HFC-134a as a refrigerant. Compressors play a critical role in the refrigeration and air conditioning cycle, allowing for the effective circulation of the refrigerant and the condensation of heat. In this context, knowing the various types of compressors and their components can lead to better selections for application-specific needs.
Types of Compressors
Different types of compressors are utilized in different applications of HFC-134a. Selecting the right type can enhance performance and longevity while optimizing energy usage.
Reciprocating Compressors
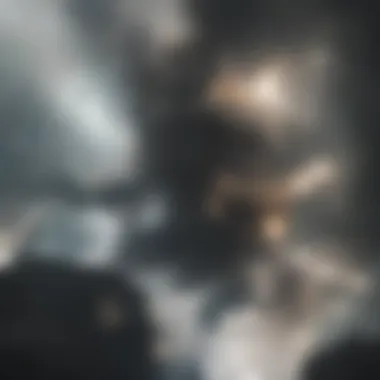
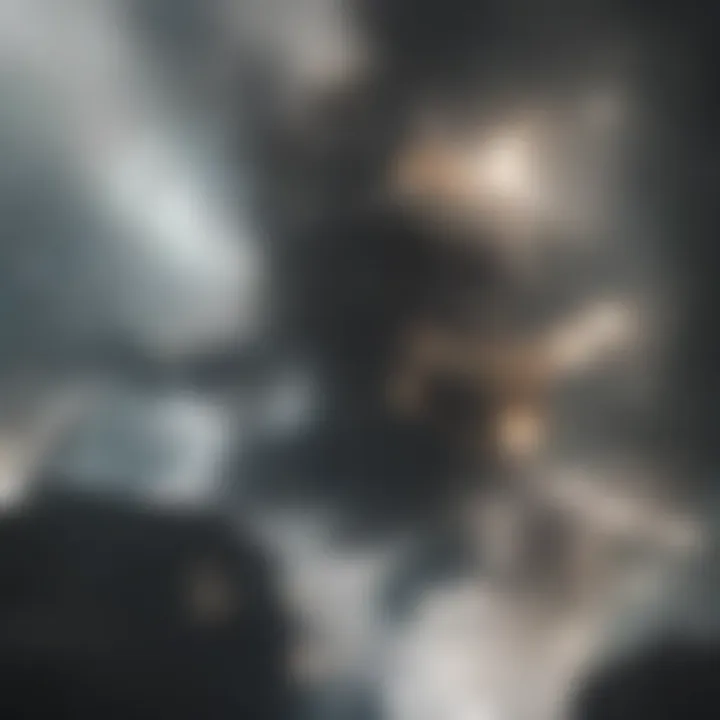
Reciprocating compressors are piston-driven units that compress refrigerant through a cycle of suction, compression, and discharge. This type is widely known for its reliability and efficiency, making it a popular choice in automotive air conditioning systems. The key characteristic of reciprocating compressors is their ability to handle varying loads effectively. This feature makes them versatile in numerous applications.
The primary advantage of reciprocating compressors is their efficiency in converting mechanical power into pressure. They can maintain performance well under changing environmental conditions. However, one downside is that they can be noisier compared to other types, which might not be ideal for residential applications.
Scroll Compressors
Scroll compressors utilize two spiral elements to compress refrigerant. This design allows for smoother and quieter operation, appealing for residential air conditioning and refrigeration systems. Their key characteristic is their compact size combined with high efficiency and low noise levels.
Scroll compressors are gaining popularity due to their simplicity and the reduced number of moving parts. This unique feature results in increased reliability and a lower chance of mechanical failures over time. On the downside, they may not be suitable for high-pressure applications, which range into the limits of the capacity they can handle.
Rotary Compressors
Rotary compressors employ rotating elements to compress refrigerant, and they are known for their compact design and high performance. A significant benefit is their ability to operate efficiently while maintaining a quiet operation. They have a consistent output, making them favorable for refrigeration and air conditioning.
The primary advantage of rotary compressors is their efficiency and size, which leads to space savings in application setups. However, the complexity of their mechanical design means that maintenance and repairs can be more complicated, potentially increasing long-term ownership costs.
Compressor Components and Functionality
The performance of a compressor highly relies on its components. Important components include the suction valve, discharge valve, and piston and cylinder design. Each of these parts contributes significantly to the airflow and overall efficiency of the compressor.
Suction Valve
The suction valve is responsible for allowing refrigerant to enter the compressor. This component should open smoothly to minimize resistance and facilitate efficient gas flow. A key characteristic of the suction valve is that it must withstand the varying pressures throughout its operational cycle.
Having a well-designed suction valve is beneficial for maintaining the efficiency of the compressor. However, if it becomes worn or faulty, it can lead to decreased performance and increased energy use.
Discharge Valve
The discharge valve performs the opposite function of the suction valve by releasing compressed refrigerant into the condenser. This component must seal tightly to maintain high pressure efficiently. The key characteristic here is the sealing capability under high pressure, which is critical for system reliability.
A properly functioning discharge valve is crucial for effective heat transfer, and any failure can result in process inefficiencies. An advantage to its design is that it can be optimized to reduce energy loss, although any malfunction could lead to significant operational costs over time.
Piston and Cylinder Design
The design of the piston and cylinder is vital to the compressor’s overall effectiveness, influencing its displacement and efficiency. In many compressors, a well-crafted cylinder allows for smooth movement and reduced friction. The key characteristic lies in the tailored dimensions for specific applications, impacting performance and efficiency directly.
When designed properly, the piston and cylinder can yield higher efficiency and longer service life. However, precision in manufacturing is essential, and any imperfections can lead to increased wear and tear. This affects overall performance negatively and can result in premature failure of the compressor.
Understanding these fundamentals equips industry professionals for making informed decisions regarding the choice and maintenance of HFC-134a compressors in various applications.
Working Principles of HFC-134a Compressors
The operating principles of HFC-134a compressors are central to their performance and efficiency in various applications. Understanding these principles allows engineers and technicians to optimize system performance, minimize energy consumption, and ensure the longevity of equipment. Thus, an exploration into these working principles sheds light on not just how these compressors function but also highlights their significance in refrigeration and air conditioning technologies.
Thermodynamic Cycles
Thermodynamic cycles are essential in understanding how HFC-134a compressors operate. A thermodynamic cycle outlines the process by which the refrigerant transitions from a gas to a liquid and back again while absorbing and releasing heat.
In the common vapor-compression cycle, HFC-134a starts in a low-pressure gaseous state. It enters the compressor, where it is subjected to compression. This compression raises the pressure and temperature of the refrigerant. The high-pressure gas then moves to the condenser, where it releases heat and transforms into a liquid state. Afterward, this liquid refrigerant flows to the expansion valve, where it undergoes a drop in pressure, cooling down before entering the evaporator. In the evaporator, it absorbs heat from its surroundings and returns to the gaseous state, completing the cycle.
Each stage is crucial:
- Compression: Raises pressure and temperature, facilitating heat rejection.
- Condensation: Releases heat, transforming the refrigerant to liquid.
- Expansion: Lowers pressure and initiates cooling.
- Evaporation: Absorbs heat, fulfilling the cooling requirement.
This cyclical process is fundamental for the efficiency and effectiveness of HFC-134a compressors in varying environments. The effectiveness of heat exchange during each of these stages directly impacts the compressor’s capacity and overall performance.
Heat Exchange Mechanisms
Heat exchange mechanisms in HFC-134a compressors involve the transfer of heat between the refrigerant and the surrounding environment. This mechanism operates through conduction, convection, and, in some cases, radiation.
In the condenser, the refrigerant dissipates heat to the ambient air or water, promoting its transition from gas to liquid. Effective heat exchange in this stage is vital. Higher ambient temperatures can hinder heat transfer efficiency, leading to reduced performance.
In the evaporator, the reverse happens. The refrigerant absorbs heat from the environment, which can significantly impact energy efficiency. Proper design and material selection in heat exchangers can optimize these mechanisms, contributing to better system performance.
- Factors affecting heat exchange include:
- Surface area: Larger areas enhance heat transfer.
- Flow rate: Adequate flow rates maintain efficiency.
- Temperature gradient: A higher difference between the refrigerant and the surroundings boosts the heat exchange rate.
In summary, understanding the thermodynamic cycles and heat exchange mechanisms is crucial for effectively utilizing HFC-134a compressors. As these compressors face evolving performance demands, advancements in material science and design hold promise for more efficient operations.
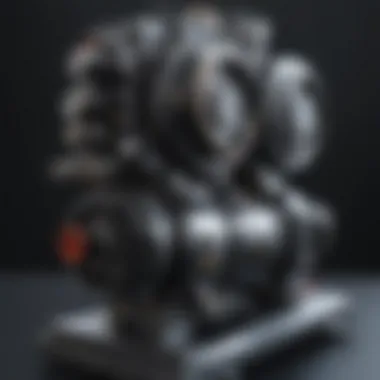
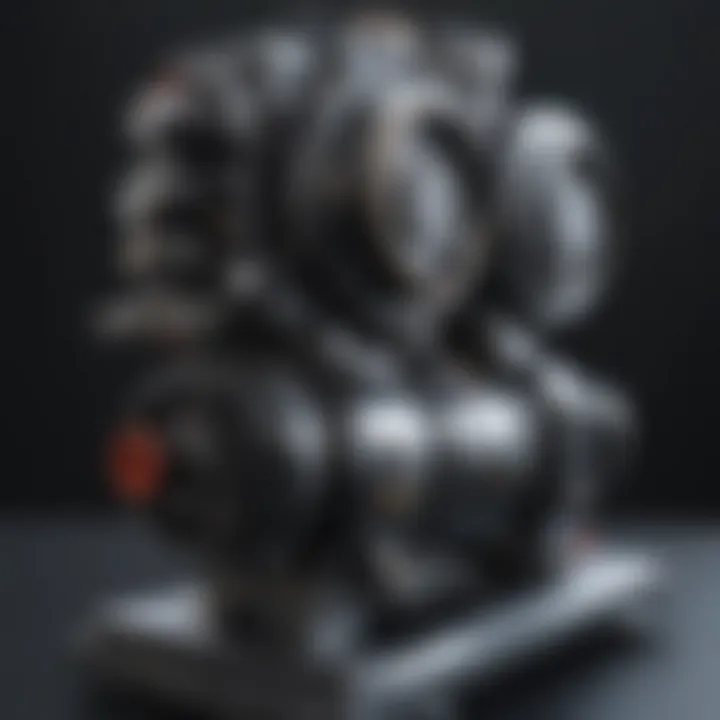
Performance Metrics
Performance metrics serve as crucial indicators when assessing the effectiveness and reliability of HFC-134a compressors. Understanding these metrics is fundamental for engineers, manufacturers, and end-users involved in the design and operation of HVAC systems. This section will explore efficiency ratings and capacity/load factors, both essential aspects that contribute to performance evaluations.
Efficiency Ratings
Efficiency ratings reflect how well HFC-134a compressors convert input energy into useful work. The most common measure of efficiency in refrigeration compressors is the Coefficient of Performance (COP), which indicates the ratio of cooling output to the energy input required.
Higher COP values signify more efficient compressors. This efficiency is vital not just to reduce operational costs but also to minimize environmental impact. By improving efficiency, facilities can reduce energy consumption, leading to lower greenhouse gas emissions associated with electricity generation.
To enhance efficiency ratings, various factors should be considered:
- Design Innovations: Newer compressor designs, such as scroll and inverter-driven technologies, show improved efficiency ratings compared to traditional reciprocating compressors.
- Regular Maintenance: Preventive maintenance can keep compressors running at their optimal efficiency, ensuring longevity and reduced operational costs.
- Operating Conditions: Maintaining appropriate temperature and pressure settings is essential for optimal efficiency.
Capacity and Load Factors
Capacity and load factors offer insights into how well an HFC-134a compressor can perform under varying operational conditions. The capacity factor refers to the actual output of the compressor versus its maximum rated capacity. A high capacity factor indicates that a compressor is operating efficiently, often across a range of loads.
The load factor, on the other hand, illustrates the proportion of the compressor's capacity being utilized over a given period. This factor is pertinent in determining if a compressor is oversized or undersized for its application, which can lead to energy wastage. To optimize performance, it is essential to match compressor capacity to the required load to avoid issues such as:
- Short Cycling: Frequent on-off cycles can lead to increased wear and energy losses.
- Increased Energy Consumption: Oversized compressors can lead to unnecessary energy expenditure.
- Reduced Service Life: Constant operation under heavy load can cause stress and shorten the longevity of the unit.
Applications of HFC-134a Compressors
HFC-134a compressors serve a significant role in various domains of refrigeration and air conditioning. Their efficiency and effectiveness make them integral to both residential and commercial applications. This section will delve into the primary uses of HFC-134a compressors, stressing the benefits and considerations inherent to each application. Understanding these applications is crucial for professionals and researchers aiming to enhance systems performance and sustainability.
Automotive Air Conditioning
In the automotive sector, HFC-134a compressors are vital for ensuring effective climate control within vehicles. They are designed to manage the temperature of the air inside cars, providing comfort to both drivers and passengers. The compressor functions by compressing the HFC-134a refrigerant, allowing it to absorb heat from the cabin and release it outside.
The benefits of using HFC-134a in automotive applications include:
- Adequate Cooling Capacity: HFC-134a compressors are capable of providing substantial cooling, essential for maintaining comfortable temperatures during warm weather.
- Reliability: Many manufacturers rely on HFC-134a due to its consistent performance in diverse climate conditions.
- Compatibility: HFC-134a is compatible with various materials used in automotive air conditioning systems, reducing the risk of system failures.
However, there are environmental concerns surrounding HFC-134a use in automotive applications. As consumers and regulators increasingly demand greener alternatives, manufacturers are investigating options that lower the global warming potential (GWP).
Refrigeration Systems
HFC-134a compressors are extensively utilized in refrigeration systems, ranging from household refrigerators to large commercial freezers. These compressors are critical for maintaining low temperatures, crucial for food preservation and various industrial processes. The operational mechanism of these compressors contributes significantly to the overall efficiency of refrigeration systems.
The primary benefits in this context are:
- Energy Efficiency: HFC-134a compressors can operate effectively at various loads, making them favorable for energy management.
- Temperature Control: They provide precise temperature regulation, necessary for applications requiring specific storage conditions, such as pharmaceuticals and perishable food.
- Reduces Energy Costs: The efficient designs often lead to lower energy consumption, which can considerably reduce operational costs.
Nevertheless, like in automotive applications, the environmental impact of HFC-134a in refrigeration is a growing concern. Efforts are underway to transition towards alternative refrigerants that can provide similar performance without the high GWP.
Commercial Uses
In commercial settings, HFC-134a compressors find their utility in systems such as commercial HVAC systems and commercial refrigeration units. These compressors are imperative in establishments like supermarkets, restaurants, and cold storage facilities. The scalability of HFC-134a compressors allows for their use in systems ranging from small ice cream cabinets to large-scale refrigeration plants.
Key advantages in commercial applications include:
- Scalability: They can be utilized in both small and large systems, adaptable to different operational scales.
- Performance: HFC-134a compressors can maintain cooling under variable load conditions, which is essential in commercial scenarios where demand can fluctuate.
- Ease of Maintenance: Many unit designs simplify maintenance processes, enhancing long-term reliability for users.
Understanding these applications can inform future design and engineering choices, especially as environmental regulations become stricter. Companies involved in HVAC and refrigeration are challenged to reevaluate their systems, striving for balance between performance and eco-friendliness.
HFC-134a compressors play a pivotal role in numerous applications, but the quest for alternative refrigerants is becoming increasingly critical due to environmental considerations.
Environmental Considerations
The discussion of HFC-134a compressors cannot be complete without addressing the environmental implications. The increasing awareness about climate change has prompted a closer examination of refrigerants, particularly HFC-134a. As a widely used refrigerant in various HVAC applications, understanding its environmental impact is crucial. This section will explore two key aspects: the global warming potential of HFC-134a and the evolving regulations surrounding its usage.
Global Warming Potential
HFC-134a has a Global Warming Potential (GWP) of 1430. This means that one kilogram of HFC-134a has a warming effect equivalent to 1430 kilograms of carbon dioxide over a time horizon of 100 years. The high GWP raises concerns as refrigerants escape into the atmosphere during usage, maintenance, or improper disposal.
The use of HFCs contributes significantly to greenhouse gas emissions, which is prompting many industries to consider alternatives.
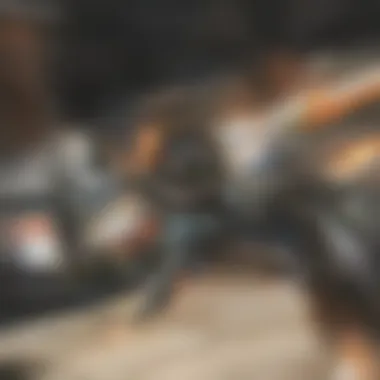
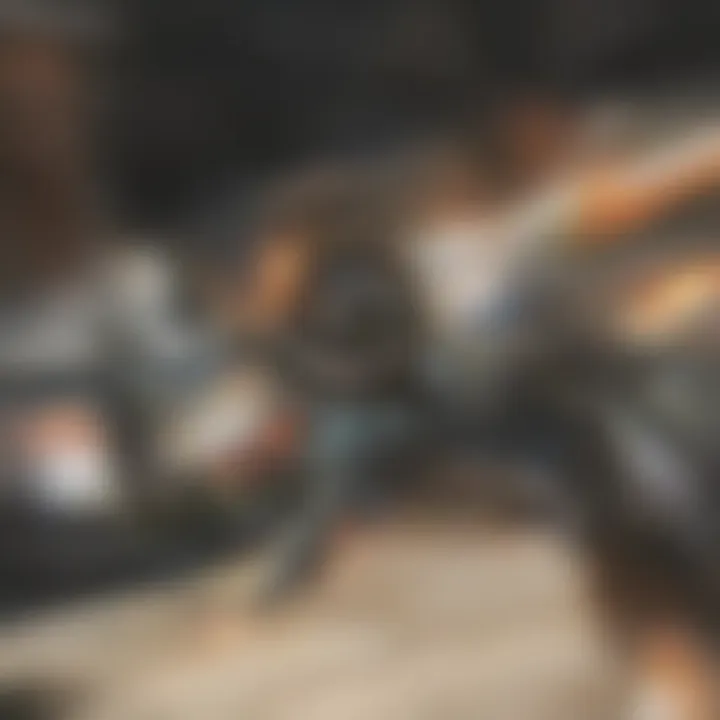
When assessing the role of HFC-134a, it's clear that its benefits in cooling and refrigeration must be weighed against its environmental risks. Industry professionals and policymakers are increasingly aware of the importance of minimizing GWP in order to meet climate targets. Therefore, many organizations are exploring low-GWP alternatives to reduce their contribution to global warming.
Regulation of HFC Usage
In response to the environmental concerns indicated by the GWP of HFC-134a, several regulations have been enacted globally. Governments are taking steps to phase down HFC use through international agreements like the Kigali Amendment to the Montreal Protocol. This agreement aims to reduce the production and consumption of HFCs and encourages shifts to more environmentally friendly alternatives.
The European Union has also implemented the F-Gas Regulation, which seeks to limit the use of refrigerants with high GWP. These regulations not only influence the market but also drive innovation in refrigerant technology. Companies are pressured to invest in research and development to find viable substitutes.
In summary, both the global warming potential of HFC-134a and the regulations governing its use highlight the necessity for change in refrigerant practices. As more stringent regulations come into play, there is a push toward sustainability and a lower environmental footprint. Understanding these factors is vital for stakeholders in the HVAC industry to adapt and stay compliant.
Alternatives to HFC-134a
In recent years, the scrutiny surrounding HFC-134a due to environmental concerns has prompted a shift toward alternative refrigerants. These alternatives aim to mitigate the global warming potential associated with traditional refrigerants and ensure compliance with increasingly stringent regulations. Understanding this topic is crucial not only for reducing environmental footprints but also for advancing technology in HVAC systems that rely on effective and efficient refrigerants.
The transition away from HFC-134a brings several important considerations:
- Environmental Impact: Many emerging refrigerants boast significantly lower global warming potential compared to HFC-134a. Using alternative refrigerants can help reduce greenhouse gas emissions.
- Regulatory Compliance: Ongoing international agreements and national policies, such as the Kigali Amendment to the Montreal Protocol, are progressively limiting the use of HFCs. Companies must adapt to these changes to avoid penalties and ensure ongoing operations.
- Performance and Safety: Alternatives must not only meet environmental criteria but also maintain or enhance system performance. Safety is also a crucial factor, especially regarding flammability and toxicity.
Emerging Refrigerants
Emerging refrigerants represent a significant advancement in the search for more sustainable options. Natural refrigerants such as propane, ammonia, and carbon dioxide are gaining attention due to their minimal environmental impact. For instance:
- Propane (R-290): This is a hydrocarbon refrigerant that offers excellent energy efficiency. However, it is flammable, which creates safety concerns that need to be managed in application.
- Ammonia (R-717): Known for its cooling efficiency, ammonia is often used in industrial refrigeration. Its environmental impact is minimal, but it poses toxicity risks that require careful handling.
- Carbon Dioxide (R-744): As a natural refrigerant, CO2 has a global warming potential of one. It operates well in low-temperature applications and is increasingly used in supermarket refrigeration.
These alternatives are being integrated into various applications, offering distinct advantages. However, the transition needs careful planning to address potential efficiency and safety issues.
Technological Innovations
Technological advancements play a vital role in establishing the efficacy of alternative refrigerants. Innovations focus on improving system designs and controls, which enable optimal performance of new refrigerant types. Some noteworthy developments in this area include:
- High-Efficiency Compressors: New designs for compressors allow them to operate efficiently with low-GWP refrigerants. This is crucial as some alternatives may not yield the same performance levels as HFC-134a.
- Advanced Heat Exchangers: Heat exchanger technology is being refined to maximize heat transfer efficiency. This adaptation ensures that systems utilizing alternative refrigerants perform effectively, even under varying load conditions.
- Smart Controls and IoT Integration: Incorporating intelligent controls can optimize energy consumption and system performance. Real-time monitoring and diagnostics can enhance the efficiency of HVAC systems using alternative refrigerants.
As the industry adapts to these alternatives, ongoing research and development will continue to drive innovation. This is necessary to ensure that these new refrigerants can be seamlessly integrated into existing systems while meeting stringent performance and safety standards.
"Adopting alternatives to HFC-134a represents not only a regulatory necessity but also an opportunity for innovation in the HVAC industry."
In summary, the exploration and adoption of alternatives to HFC-134a are significant as the HVAC industry confronts environmental challenges. By understanding the benefits and considerations of emerging refrigerants and technological innovations, stakeholders can make informed decisions that lead to sustainable outcomes.
Future of HFC-134a Compressors
The future of HFC-134a compressors is critical, considering various factors influencing their application and relevance in modern industries. As we venture further into a landscape shaped by climate concerns and technological advancement, understanding this future aids industries in adapting strategies accordingly.
Market Trends
The market for HFC-134a compressors is experiencing various shifts, primarily due to regulations aimed at minimizing global warming potential. While HFC-134a remains a significant component in air conditioning systems, industries are increasingly searching for lower-impact alternatives. In recent studies, it was observed that many companies are evaluating the remaining lifespan of their HFC-134a-dependent equipment, often leading to a transition into systems that utilize hydrofluoroolefins (HFOs) or natural refrigerants. These market trends show a keen awareness of the need for sustainable practices in engineering and HVAC sectors.
"As manufacturers innovate, the choice of refrigerant is becoming a core strategy for companies aiming to meet environmental standards and remain competitive."
Furthermore, geographical regulations impact the market trend too. Some regions are phasing out HFCs more aggressively than others, causing demand fluctuations based on local policy decisions. The adaptation to these market shifts is essential for developers and manufacturers seeking to remain viable in the long run.
Sustainability Initiatives
Sustainability initiatives involving HFC-134a compressors focus primarily on reducing emissions and enhancing energy efficiency. Many companies have begun to emphasize energy-efficient designs as a fundamental aspect of product development. Emphasizing innovation in compressor design increases overall system efficiency, prolonging equipment life and reducing energy consumption during operation.
Fostering partnerships with environmental organizations is becoming more common. These collaborations aim to establish best practices and create awareness about refrigerant management strategies among industry players. Moreover, certification programs are becoming crucial in ensuring that professionals are informed about sustainable practices in refrigerant handling, installation, and maintenance.
While HFC-134a compressors are still operational, prolonged usage must be matched with stringent protocols to manage leakages and ensure proper disposal, helping to minimize their environmental impact. When companies commit to these sustainability initiatives, they can mitigate regulatory backlash while appealing to a contemporary consumer base that values environmental responsibility. Therefore, the future landscape for HFC-134a compressors is likely to be dominated by innovations that align both with market demand and sustainability goals.
The End
Recap of Key Points
The examination of HFC-134a compressors reveals critical aspects of their design and functionality. HFC-134a, as a refrigerant, plays an important role in various applications including automotive air conditioning and refrigeration systems. The article discussed the mechanisms of HFC-134a compressors, focusing on their performance metrics, types, and environmental considerations. The importance of HFC-134a in the context of global warming potential and regulatory issues was also highlighted.
In summary, key points include the following:
- HFC-134a compressors are mainly used in HVAC systems.
- Their functioning is governed by thermodynamic cycles and heat exchange mechanisms.
- Understanding efficiency ratings and load factors is essential for evaluating performance.
- Environmental impacts linked to HFC-134a raise significant concerns for future practices.
Call for Further Research
The evolving landscape of refrigerants presents a necessity for continued inquiry. As regulations around HFCs tighten, it becomes imperative to explore alternatives and innovative technologies. Organizations and researchers must focus on sustainable practices and the development of refrigerants with lower global warming potentials.
Further studies should cover:
- The performance of emerging refrigerants as substitutes for HFC-134a.
- Innovative cooling technologies and their adaptation in existing systems.
- Long-term environmental impacts of alternative refrigerants compared to traditional HFCs.