Understanding Overall Equipment Effectiveness in Manufacturing
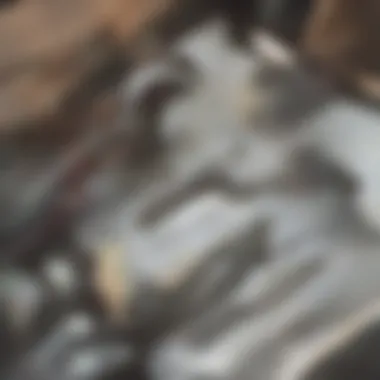
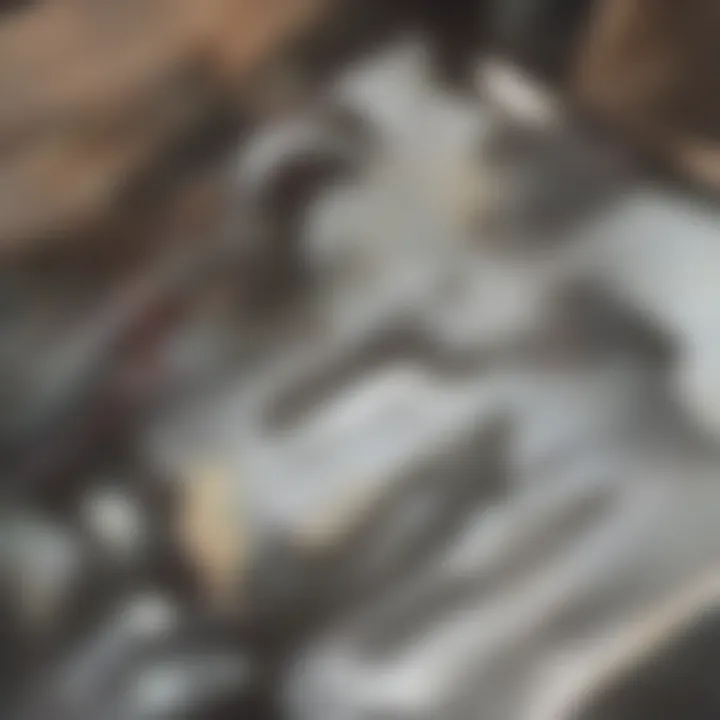
Intro
Overall Equipment Effectiveness (OEE) serves as a cornerstone metric for measuring the efficiency of manufacturing equipment. Capturing a holistic view of how well a manufacturing process is performing, OEE encompasses three critical aspects: availability, performance, and quality. Understanding these components is essential for professionals in the field, allowing them to identify inefficiencies and implement targeted improvements.
The relevance of OEE cannot be overstated. In a competitive market, manufacturers must optimize their operations to remain profitable. Effective measurement of OEE is integral to this. By analyzing how equipment behaves during various production stages, organizations can uncover significant insights about productivity levels and potential bottlenecks.
This article seeks to dissect the measurement and implications of OEE, offering a structured guide that details each step involved in understanding this vital metric. Throughout this exploration, we will touch upon critical issues like the factors affecting OEE, the relationship it shares with other performance metrics, and best practices for continuous improvement. Our intention is to provide valuable knowledge for students, researchers, educators, and professionals eager to deepen their understanding of OEE and its applications in real-world scenarios.
Research Context
Background and Rationale
The concept of OEE originated in the 1970s as a means to address productivity loss in manufacturing settings. As production processes became more complex, tracking efficiency using simple metrics proved inadequate. To truly grasp equipment performance, a nuanced and multidimensional approach became necessary. The rationale for using OEE lies in its ability to combine various performance aspects into a single, easily interpretable figure. This metric is not just a reflection of efficiency; it serves as a diagnostic tool that can highlight areas needing improvement.
Literature Review
Past studies and literature surrounding OEE emphasize its importance across various sectors of manufacturing. Research has shown that organizations which prioritize measuring and improving OEE tend to achieve better operational outcomes. Publications in the International Journal of Production Research and Journal of Operations Management stress the interplay between OEE and factors like maintenance strategies, workforce training, and technology integration. The findings indicate a direct correlation between high OEE scores and increased profitability, proving the metric invaluable.
By delving into this article, readers will see how to measure OEE effectively and how mastering this metric can revolutionize manufacturing operations.
Foreword to Overall Equipment Effectiveness (OEE)
In modern manufacturing, optimizing performance is crucial. One such metric that plays a significant role is Overall Equipment Effectiveness (OEE). Understanding OEE is essential for organizations aiming to enhance productivity and efficiency.
This metric combines several critical components: availability, performance, and quality. Each element contributes uniquely to the overall effectiveness of equipment. Proper assessment of these factors allows businesses to pinpoint inefficiencies and highlight areas for improvement.
Properly measuring OEE assists decision-makers in identifying production bottlenecks. By focusing efforts on enhancing the components of OEE, organizations can achieve substantial gains in operational efficiency.
Definition of OEE
Overall Equipment Effectiveness is defined as a measurement that evaluates the efficiency of a manufacturing process. It reflects how effectively a manufacturing entity utilizes its equipment. OEE is calculated by multiplying three factors: availability, performance, and quality. The formulation captures the essence of an operation's effectiveness, providing insights into productivity levels.
Importance of OEE in Manufacturing
The importance of OEE in manufacturing cannot be overstated. It serves various purposes:
- It identifies areas where equipment is underperforming.
- OEE benchmarks can lead to focused improvement initiatives.
- Improved OEE directly correlates with higher productivity and reduced waste.
Investing time in understanding and implementing OEE offers tangible benefits. Businesses can enhance their production processes, minimize downtime, and improve overall product quality. Thus, OEE emerges as a pivotal metric for anyone involved in manufacturing operations, from operators to managers to executives.
Components of OEE
Understanding the components of Overall Equipment Effectiveness (OEE) is crucial for optimizing manufacturing performance. The concept goes beyond mere numbers and reflects a system's efficiency and productivity. The three primary components of OEE are Availability, Performance, and Quality. Each of these elements plays a role in assessing how effectively equipment is utilized during production. Proper knowledge about these components allows companies to pinpoint areas requiring improvement, thereby enhancing their overall efficiency.
Availability
Availability is a measure of the time that equipment is operating effectively compared to the total time it is scheduled to run. In simpler terms, it reflects how often the machines are actually on and producing versus sitting idle. Factors influencing Availability include unexpected downtimes, maintenance schedules, and setup times.
To improve Availability, organizations can consider the following:
- Implementing preventive maintenance to reduce the likelihood of breakdowns.
- Analyzing downtime causes to identify recurrent issues.
- Optimizing changeover times to improve production schedules.
Addressing these factors can significantly elevate Availability rates and, therefore, the OEE score.
Performance
Performance refers to how well the equipment operates during the time it is available. It assesses whether the machinery is producing at its optimal speed compared to its designed capacity. Performance can be affected by various elements such as machine speed, operator efficiency, and material quality.
To enhance Performance, manufacturers may take several actions:
- Setting realistic speed targets based on equipment capabilities.
- Ensuring operators are well-trained to maximize workflow efficiency.
- Identifying bottlenecks in the production line and addressing them promptly.
Improving Performance will boost the overall OEE and help meet production goals more effectively.
Quality
Quality measures the degree to which the produced items meet the required specifications compared to the total items produced. It highlights the importance of minimizing defects and ensuring that finished goods are satisfactory. Quality is influenced by several factors, including raw material quality, equipment calibration, and worker skills.
To improve Quality, organizations can implement strategies like:
- Regular quality checks during production processes.
- Adopting statistical quality control methods to minimize defects.
- Training employees on quality standards and practices.
By focusing on Quality, companies can reduce rework and scrap, leading to better overall efficiency.
Enhancing each component of OEE directly impacts a manufacturing plant's performance, productivity, and profitability.
In summary, the components of OEE are interrelated and essential for revealing the true performance of manufacturing systems. Addressing each element thoroughly can lead to significant improvements and a better understanding of how equipment can be used most effectively.
Measuring OEE: Calculation and Formula
Measuring Overall Equipment Effectiveness (OEE) is not just an academic exercise; it is integral to operational insight in manufacturing segments. The calculation and formula provide a framework to quantify performance, identify areas of waste, and optimize processes. Understanding these calculations gives professionals the ability to implement changes that enhance productivity and efficiency.
OEE Calculation Formula
The OEE calculation formula is expressed as:
OEE = Availability × Performance × Quality
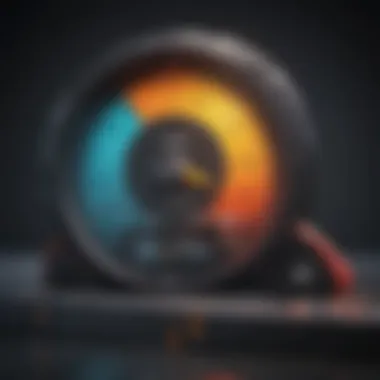
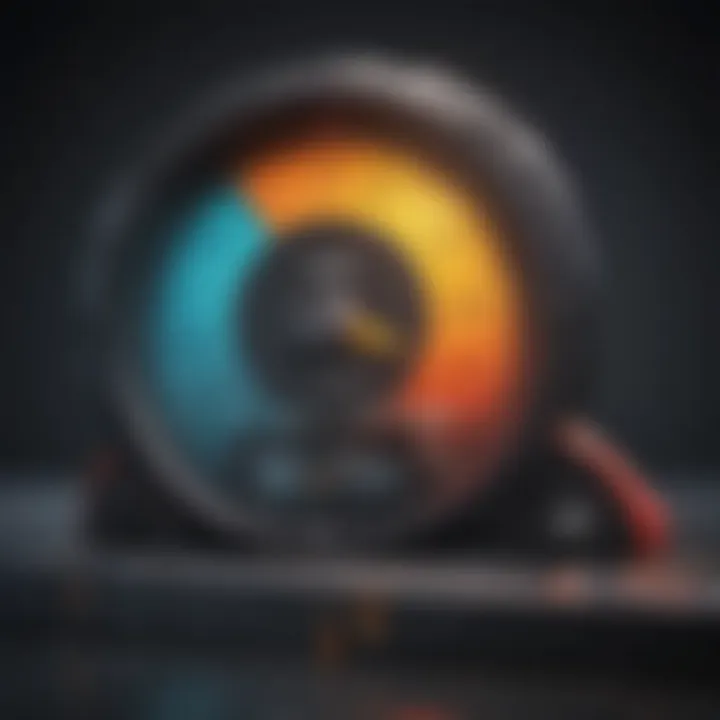
To clarify these components:
- Availability refers to the ratio of actual operating time to scheduled production time. It provides insight into the operational efficiency of equipment.
- Performance measures the speed at which the equipment operates compared to its maximum possible speed. This captures losses through inefficiencies.
- Quality assesses the proportion of produced goods that meet quality standards, thus identifying defects.
For example, if a machine is available for 8 hours (480 minutes), runs at 300 units per hour instead of 400 (max speed), and produces 250 good units, the OEE would be calculated as:
- Availability = 480 / 480 = 1.0 (100%)
- Performance = (300 / 400) = 0.75 (75%)
- Quality = (250 / 300) = 0.833 (83.3%)
Therefore, the OEE = 1.0 × 0.75 × 0.833 = 0.625 or 62.5%.
This formula condenses complex operational information into clear and actionable metrics that can drive continuous improvement processes.
Data Collection for OEE Assessment
Data collection is crucial for accurate OEE assessment. Inaccurate or incomplete data can lead to flawed measures and poor decision-making. The process includes systematically gathering information on machine uptime, production counts, and quality rates. To enable effective data collection, consider the following aspects:
- Automated Systems: Leverage sensors and productivity monitoring tools. These technologies can provide real-time data, reducing manual input errors.
- Standard Procedures: Establish a clearly defined protocol for data entry. This should include what data points to collect and how often.
- Employee Involvement: Engage operational staff in assessing and reporting issues. This multidimensional input adds depth and reliability to the collected data.
These collective efforts ensure that the assessment reflects true equipment performance, making OEE a reliable measure of production efficiency.
Frequency of OEE Measurement
Determining the frequency of OEE measurement is vital for obtaining timely insights. Regularly assessing OEE allows for prompt identification of issues and opportunities for improvement. Factors influencing measurement frequency include:
- Production Volume: High-volume operations may require daily measurement, while lower production rates can be assessed weekly or monthly.
- Purpose of Measurement: If the goal is to diagnose specific problems, more frequent evaluations may be necessary.
- Resource Availability: Employees can only measure OEE as often as they have time for; therefore, balance is crucial.
In the context of continuous improvement, consider a cycle of weekly measurements to maintain momentum in enhancing operational efficiency. This approach ensures that the data remains relevant and actionable.
"Regular OEE measurements promote a culture of continuous improvement, critical in today’s competitive landscape."
In summary, measuring OEE through its calculation formula, strategic data collection, and appropriate measurement frequency provides a cohesive framework to drive operational success. It leads managers and employees alike to a common goal of enhanced productivity and efficiency.
Methods to Measure OEE
Understanding how to measure Overall Equipment Effectiveness (OEE) is critical for any manufacturing organization seeking to enhance productivity. OEE quantifies how well a manufacturing operation is utilized compared to its full potential. Thus, effective measurement methods are essential for identifying bottlenecks, understanding equipment performance, and facilitating improvements. Accurate measurement allows for informed decision-making and strategic planning when it comes to boosting productivity and efficiency. Organizations can choose from various methods to measure OEE, each with unique advantages and considerations. This section discusses the prominent methods available: manual methods, automated tracking systems, and dedicated software tools.
Manual Methods
Manual methods for measuring OEE involve operators collecting data without the assistance of specialized technology. This approach often includes using simple tools such as spreadsheets and logbooks. Factors like downtime, production counts, and quality defects are recorded by operators during shifts.
Some significant pros of manual methods are:
- Low initial cost: Simply requires minimal resources.
- Customization: Operators can tailor the methods to their specific needs.
- Flexibility: Operators can modify data collection techniques based on real-time conditions.
Despite these advantages, manual methods entail several drawbacks:
- Time-consuming: Data collection can distract operators from their primary tasks.
- Human error: Errors in data entry can easily occur, leading to skewed results.
- Limited analysis: Manual compilation does not lend itself to in-depth analysis effortlessly.
Automated Tracking Systems
Automated tracking systems enhance the reliability of OEE measurements by capturing data directly from machines. These systems use sensors and software to monitor equipment performance in real time. They can automatically gather critical data such as operation time, production speed, and quality rates, presenting a more accurate picture of OEE.
Key advantages of automated tracking systems include:
- Real-time data acquisition: Immediate insights into machine performance.
- Data accuracy: Reduces chances of human error significantly.
- Efficient analysis: Easily consolidated data allows for advanced analytics and reporting.
On the other hand, there are considerations for implementing automated systems:
- Higher initial investment: Costs can be significant when setting up the system.
- Training needs: Staff may require time and training to adapt to new systems.
- Integration challenges: May need to be integrated with existing systems, which can involve complexities.
Use of Software Tools
Dedicated software tools to measure OEE combine various data collection and analysis techniques to provide a comprehensive overview of equipment performance. Many of these tools integrate with existing manufacturing execution systems and gather data from multiple sources. They leverage algorithms and reports to interpret and present findings in an actionable format.
The benefits of software tools are manifold:
- Comprehensive analysis: Capable of combining data from diverse sources for a complete view.
- User-friendly interfaces: Often designed with intuitive dashboards that make data accessible and understandable.
- Scalability: Many tools can grow as the organization expands, accommodating more equipment and processes.
However, it is essential to recognize potential downsides:
- Subscription or license fees: Ongoing costs may be prohibitive for some organizations.
- Complex setup: Requires time and expertise to properly implement and configure.
- Dependence on technology: If systems go down, access to vital data may be compromised.
Factors Affecting OEE Measurements
Understanding the factors that influence Overall Equipment Effectiveness (OEE) measurements is essential in manufacturing. Each of these elements plays a vital role in determining how effectively equipment is utilized. By examining the intricacies of downtime, speed loss, and quality defects, organizations can identify areas for improvement. Realizing the implications of these factors contributes to operational excellence and enhances overall productivity.
Downtime
Downtime is the period during which equipment is not operational, resulting in a direct impact on OEE scores. It can stem from various causes including machine failure, maintenance needs, or operator shortages. Addressing downtime effectively is crucial for improving OEE.
- Types of Downtime:
- Consequences of Downtime:
- Planned Downtime: Usually for scheduled maintenance.
- Unplanned Downtime: Results from unexpected equipment failures.
- Loss of production capabilities.
- Increased operational costs.
- Underutilization of resources.
By tracking and analyzing downtime, businesses can implement preventative measures to minimize its occurrence. Regular equipment checks and training for operators can decrease both planned and unplanned downtime significantly.
Speed Loss

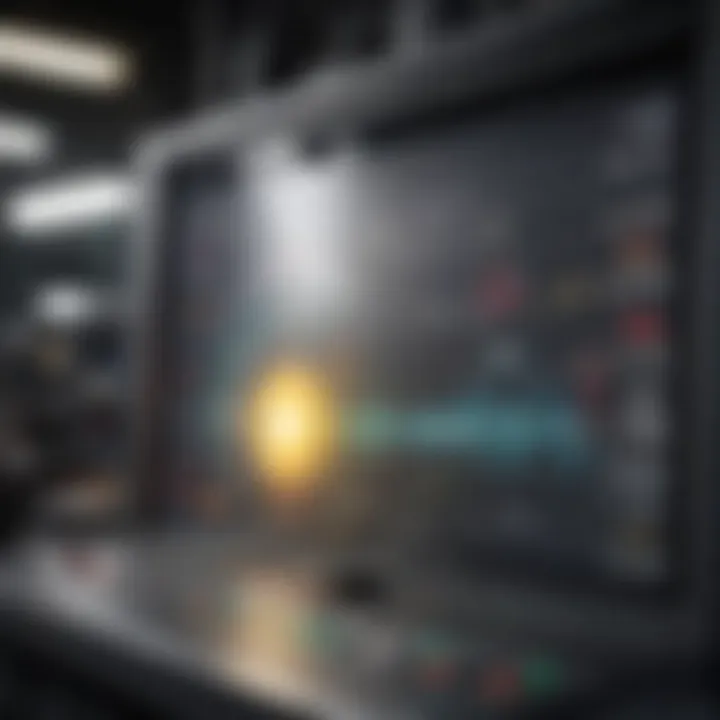
Speed loss refers to the gap between the actual operating speed of a machine and its optimal performance speed. It is a critical factor affecting OEE because it directly correlates with production output.
- Causes of Speed Loss:
- Effects of Speed Loss:
- Mechanical issues impacting performance.
- Inefficient manufacturing processes.
- Operator errors affecting machine speed.
- Reduced throughput.
- Wasted time and effort.
- Possible bottlenecks in production.
To combat speed loss, a thorough analysis of production processes is necessary. Organizations can focus on enhancing machine settings, conducting regular training of operators, and improving the workflow to maintain optimal speed.
Quality Defects
Quality defects occur when products do not meet specified standards, which affects OEE negatively. This includes any imperfection or non-conformance to predetermined specifications.
- Impact of Quality Defects:
- Managing Quality Defects:
- Increased scrap rates, leading to waste.
- Rework requirements, which consume additional time and resources.
- Customer dissatisfaction resulting from poor-quality products.
- Implementing quality control measures.
- Utilizing feedback loops in production to spot issues.
- Training staff on quality standards and best practices.
Improvement in quality directly enhances OEE. It is essential to maintain high product standards to foster both efficiency and customer satisfaction. Monitoring these aspects will ultimately lead to more accurate OEE readings and a better understanding of equipment performance.
"By focusing on these factors, organizations can develop strategies to enhance their OEE measurements and overall manufacturing efficiency."
Understanding these factors provides a foundation for better management of OEE. Addressing downtime, speed loss, and quality defects keeps machinery running smoothly, enhances production processes, and helps achieve strategic objectives.
Implications of OEE Measurement
Understanding the implications of OEE measurement is fundamental for any organization that relies on manufacturing efficiency. It is not only about quantifying performance but also about making strategic decisions that enhance overall productivity and profitability. OEE gives insights into where processes may be lagging and what can be done to improve them.
By measuring OEE, businesses can pinpoint specific areas that require attention. This includes recognizing unproductive periods and their causes. Addressing these factors helps in aligning operational goals with performance metrics, leading to improved outcomes.
Operational Efficiency
Operational efficiency defines how well an organization utilizes its resources to produce output. A high OEE score indicates that equipment is functioning optimally, which directly contributes to productivity.
Through regular OEE measurements, companies can systematically identify inefficiencies. For instance, if downtime or performance issues are prevalent, they can be targeted for resolution. Effective tracking and swift adjustments lead to better overall performance. Improvements in operational workflows often arise from OEE insights.
- Reduced waste in processes
- Enhanced resource allocation
- Better scheduling of maintenance activities
Organizations embracing OEE typically see a tangible increase in productivity metrics, setting a foundation for sustained performance.
Cost Reduction Strategies
Implementing OEE measurement contributes substantially to cost reduction strategies within manufacturing. High levels of unproductive time and material waste highlight areas where money is being lost.
By understanding the factors influencing OEE scores, companies can take specific actions to minimize costs. Strategies may include:
- Improving machine reliability to reduce downtime.
- Streamlining processes to enhance performance.
- Training employees to decrease defects and rework.
Each improvement leads to a direct impact on the bottom line. For example, reducing the time a machine is down or enhancing the quality of products allows for more effective use of resources.
Continuous Improvement Processes
Continuous improvement is essential in any manufacturing environment. OEE measurements foster a mindset focused on incremental enhancements.
By regularly analyzing OEE data, teams can engage in:
- Root cause analysis of downtime.
- Implementing corrective actions.
- Setting benchmarks for future performance.
Over time, this builds a culture of constant evaluation and refinement of processes. Employees start to recognize their role in driving improvements, leading to sustained operational success.
"Measuring OEE is not just a process but a pathway to integrating a culture of continuous improvement within the organization."
Ultimately, the implications of OEE measurement extend beyond metrics; they influence every aspect of an organization’s performance. By embracing the insights from OEE, companies can foster an environment of operational excellence that continues to evolve and adapt to manufacturing challenges.
Best Practices for Improving OEE
Improving Overall Equipment Effectiveness (OEE) is essential for enhancing productivity and efficiency in manufacturing. Implementing best practices can help organizations minimize wasted resources and maximize production output. This section discusses critical practices to improve OEE, focusing on root cause analysis, employee training, and regular maintenance. Each point addresses its significance and the impact it can have on the overall effectiveness of manufacturing processes.
Root Cause Analysis
Root cause analysis is a systematic approach that investigates the foundational factors of equipment inefficiencies. By identifying the real reasons why equipment does not perform at its best, organizations can specifically target the issues for resolution. Most of the time, equipment downtime, quality defects, and performance speed loss can be traced back to underlying causes.
- Identify Problems: An effective analysis begins with pinpointing issues related to performance. This may include understanding machine downtime or exploring production quality.
- Use Techniques: Tools like the 5 Whys or Fishbone Diagrams can help dive deep into problems. They encourage a thorough examination of each factor to understand how they contribute to inefficiency.
- Implement Solutions: Once root causes are established, solutions can be formulated. Changes could include adjusting processes, modifying equipment, or enhancing operator skills.
"A root cause analysis could save years of production time by making precise and meaningful improvements to equipment and operation strategies."
Employee Training and Engagement
The role of employees in improving OEE cannot be overstated. Skilled and engaged workers are more likely to contribute positively to operational efficiency. Training programs designed to empower workers lead to better performance outcomes.
- Skill Development: Regular training sessions can help workers understand new technologies and methodologies, allowing them to operate equipment more effectively.
- Engagement Programs: Engaging employees in decision-making fosters a sense of ownership. When they feel their input matters, motivation increases, which translates into better production quality.
- Feedback Mechanisms: Establishing channels for workers to provide feedback on operations can offer valuable insights. This can lead to unexpected improvements in processes or equipment usage.
Regular Maintenance and Upgrades
Regular maintenance plays a key role in sustaining high OEE levels. Preventive maintenance actions ensure that machines operate continuously without unexpected failures.

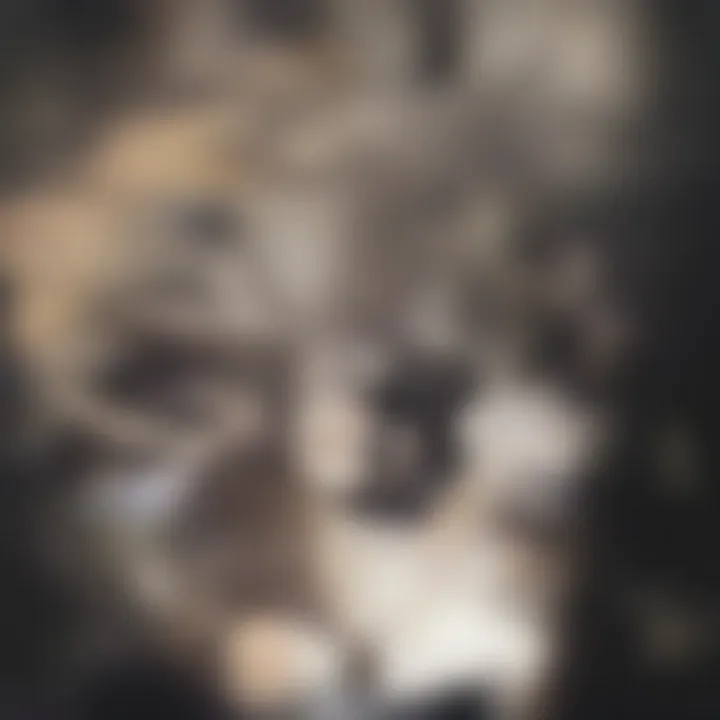
- Scheduled Maintenance: Creating a structured maintenance schedule helps prevent breakdowns, which can lead to costly downtime. Consistency is crucial.
- Upgrades: It is also necessary to evaluate technology and upgrade equipment as needed. Outdated machines often lag in performance. Ongoing investments in modern technologies can keep production lines at optimal levels.
- Monitoring Systems: Utilizing monitoring techniques to track equipment status can preemptively identify potential failures, allowing for timely intervention.
By integrating these best practices into daily operations, manufacturers can significantly enhance their OEE. Improved root cause analysis identifies issues better and ensures effective employee training enhances productivity. Additionally, consistent maintenance keeps equipment running efficiently, allowing companies to reap the full benefits of their manufacturing potential.
OEE in Relation to Other Performance Metrics
Understanding Overall Equipment Effectiveness (OEE) extends beyond its individual benefits, connecting to various performance metrics in the manufacturing landscape. This relationship is crucial as it allows organizations to foster efficiency and enhance productivity in their operations. In this section, we will explore three primary areas where OEE interacts with other performance metrics: Performance Indicators Comparison, Integration with Lean Manufacturing, and the Impact on Overall Business Performance.
Performance Indicators Comparison
OEE serves as a comprehensive measure that evaluates equipment performance by considering availability, performance, and quality. By comparing OEE with other performance indicators like Key Performance Indicators (KPIs) and Overall Performance Efficiency (OPE), organizations can pinpoint specific areas for improvement.
- KPI Relevance: KPIs often focus on specific aspects, such as production speed or quality rates. While these are important, OEE aggregates them into a single metric, providing a holistic view.
- Benchmarking: Through performance indicators, companies can benchmark their operations against industry standards or competitors. This can illuminate OEE performance and identify necessary steps to enhance it.
Establishing a clear comparison among these metrics enables organizations to create targeted strategies for improvement.
Integration with Lean Manufacturing
Lean manufacturing emphasizes waste reduction and maximizing value for customers. OEE fits seamlessly into this framework, serving as a key performance measure.
- Eliminating Waste: By measuring OEE, companies can identify inefficiencies in their processes. This helps them focus on eliminating waste in the areas of time, speed, and quality.
- Continuous Improvement: OEE and lean principles together promote a culture of continuous improvement. Regularly measuring OEE ensures that efforts to enhance operations remain on track and respond to any emerging issues.
With this integration, manufacturers can better align their OEE metrics with lean strategies to drive efficiency and productivity.
Impact on Overall Business Performance
OEE is not just a metric for equipment; it influences the overall performance of the business. Understanding this impact can guide management decisions.
- Financial Implications: Higher OEE translates to increased production efficiency, leading to higher profits. Investing in OEE can directly influence cost reductions and revenue growth.
- Decision-Making: Using OEE as a metric allows management to make informed decisions about capital expenditures, resource allocation, and workforce management. The data derived from OEE analysis can highlight the need for automation, worker training, or process changes.
In summary, a comprehensive view of OEE in relation to other performance metrics is essential for effective management. It allows organizations to evaluate their operations holistically, align objectives with lean principles, and ultimately enhance overall business performance. This nuanced understanding fosters a culture of excellence and adaptability in an ever-evolving manufacturing environment.
Challenges in OEE Measurement
Understanding the challenges in measuring Overall Equipment Effectiveness (OEE) is vital for accurate assessments of production performance. It allows organizations to identify barriers that can hinder improvement efforts. Three primary challenges often arise: data integrity issues, cultural resistance to change, and resource allocation for measurement. Addressing these challenges is essential to ensure meaningful OEE metrics and actionable insights.
Data Integrity Issues
Data integrity is a cornerstone of reliable OEE measurements. Inaccurate data can stem from incorrect data entry, lack of standardization, or malfunctioning equipment. Organizations with multiple data sources may face difficulties in maintaining consistent quality and reliability of data.
To mitigate data integrity issues, manufacturers should implement the following strategies:
- Automation of Data Collection: Reducing human involvement can minimize errors. Automated systems can continuously collect data without discrepancies.
- Standardization of Metrics: Clearly defined metrics across departments ensures everyone measures OEE using the same framework.
- Regular Audits: Scheduled reviews on data collection processes can catch errors early and maintain data quality.
By fostering data integrity, manufacturers enhance the reliability of their OEE assessments, leading to informed decision-making.
Cultural Resistance to Change
Cultural resistance poses a significant hurdle in adopting OEE measurements. Employees might be accustomed to existing processes and may view changes as threats to job security or added pressure. This mindset can delay or even sabotage OEE improvement initiatives.
To combat resistance, it is important to cultivate an environment open to change. Strategies include:
- Engaging Employees: Involve staff in discussions about OEE measurement initiatives. Their input can provide valuable insights and foster buy-in.
- Training and Support: Providing necessary training can empower employees, making them feel equipped to handle new systems or processes.
- Highlighting Benefits: Clearly communicate how improved OEE can enhance productivity and benefit everyone in the organization.
These approaches can help reduce cultural barriers and foster a collaborative spirit toward achieving better OEE.
Resource Allocation for Measurement
Resource allocation plays a critical role in the effective measurement of OEE. Without sufficient resources—whether in terms of time, personnel, or technology—efforts to measure and improve OEE can become ineffective. Organizations may struggle to gather adequate data or analyze it properly if resources are not appropriately allocated.
To optimize resource use, consider the following:
- Prioritizing Investments: Identify the most crucial areas where resources need to be allocated to ensure efficient data collection and analysis.
- Developing a Clear Plan: Formulate a strategy that outlines resource requirements and anticipated outcomes related to OEE improvements.
- Utilizing Technology: Implementing software tools that streamline the measurement process helps in maximizing existing resources.
Efficient resource allocation directly impacts the successful implementation of OEE metrics and subsequent improvements.
In summary, acknowledging and understanding these challenges is crucial for any organization aiming to enhance its OEE. Addressing data integrity issues, fostering an open culture to embrace changes, and effectively managing resources can significantly boost the reliability and accuracy of OEE measurements and lead to operational improvements.
Future of OEE Measurement
The future of Overall Equipment Effectiveness (OEE) measurement lies at the intersection of technology and management practices. As manufacturing processes evolve, the significance of accurate measurement becomes even more critical. One must understand how new methodologies and technological advancements affect OEE assessment. This section will explore innovation, integration, and predictive analytics in the context of OEE measurement.
Technological Innovations
Technological innovations are reshaping how we measure and analyze OEE. The incorporation of the Internet of Things (IoT) allows machines to communicate and relay performance data in real time. Sensors monitor equipment conditions and performance metrics continuously. This leads to immediate adjustments and fine-tuning of processes, making OEE measurement far more dynamic.
- Real-Time Data Collection: Continuous data collection enables engineers to make informed decisions on the fly, significantly improving the accuracy of OEE calculations.
- Mobile Technology: With the advent of mobile applications, workers on the floor can easily report issues or inefficiencies directly into an OEE tracking system. This direct line of communication helps maintain high data integrity.
The implications of these innovations are substantial. Manufacturers can identify inefficiencies sooner, thereby decreasing downtime and increasing overall productivity.
Integration with Industry 4.
The integration of OEE measurement with Industry 4.0 technologies offers several benefits that enhance operational performance. Industry 4.0 focuses on smart manufacturing and enables a connected environment where machinery, data, and people work harmoniously.
- Smart Factories: These are heavily reliant on interconnected equipment that autonomously adjusts and optimizes operational parameters based on OEE data. This enhances the overall decision-making process.
- AI-Driven Analytics: By utilizing artificial intelligence to analyze OEE data, manufacturers can predict equipment failures or performance drops before they occur, significantly reducing unexpected downtime.
Such integration not only boosts measurement accuracy but also supports a culture of continuous improvement within organizations, facilitating better alignment of resources and strategies.
Enhancements in Predictive Analytics
Predictive analytics plays a crucial role in enhancing OEE measurement. With the use of historical data combined with advanced analytics techniques, manufacturers can better forecast equipment performance and potential reliability issues.
- Data Models: By creating data models that include historical OEE trends, manufacturers can identify patterns and make evidence-based predictions about future performance.
- Anomaly Detection: Predictive analytics systems can detect anomalies in performance data in real time, allowing for immediate intervention.
"Predictive analytics transforms how we perceive performance metrics and helps in making proactive decisions rather than reactive ones."