Understanding Pressure Reducing Valves: A Comprehensive Guide
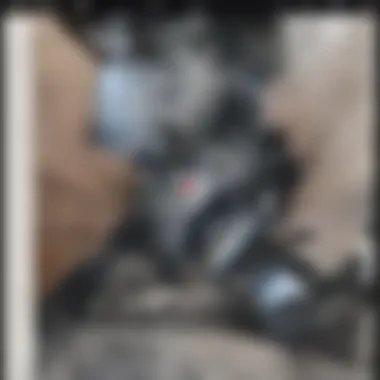

Intro
Pressure reducing valves (PRVs) play a crucial role in fluid control systems. These devices ensure that the pressure in a system remains within desired limits. They provide stability and protection, preventing potential damages caused by excessive pressure. Understanding how PRVs function and their significance in various applications is essential for engineers, technicians, and anyone involved in fluid dynamics.
The following sections will dissect the components and mechanisms of PRVs. Additionally, this article will explore different types available, alongside installation guidance, maintenance practices, and troubleshooting steps to enhance their performance.
Research Context
Background and Rationale
In a world where industries rely heavily on precise fluid management, the importance of pressure control cannot be overstated. Pressure reducing valves serve as integral components in various systems, from water supply lines to hydraulic systems. They mitigate the risks associated with high pressure that can lead to system failure or safety hazards.
As industries evolve, understanding the intricacies of pressure management becomes paramount. This article provides an in-depth examination of these valves, paving the way for improved practices in installation and maintenance.
Literature Review
Previous studies have highlighted the effectiveness of PRVs in maintaining optimal operational conditions. Research emphasizes their role in enhancing the reliability and longevity of equipment. Numerous sources, including Wikipedia and Britannica, document various applications and types of PRVs, but there remains a need for a comprehensive synthesis that addresses both theory and practical insights effectively. This article aims to fill that gap by providing rich, detailed information on the topic.
Methodology
Research Design
The exploratory method is utilized in this article to gather and analyze relevant information on pressure reducing valves. A combination of qualitative research and technical documentation allows for a well-rounded understanding.
Data Collection Methods
Data is collected through various means, including:
- Reviewing technical manuals from manufacturers of pressure reducing valves
- Analyzing industry case studies to observe practical implementation
- Engaging with professional forums such as Reddit and Facebook to gather anecdotal evidence and community insights
This diverse approach ensures a thorough analysis of PRVs by integrating both theoretical and practical perspectives.
Defining Pressure Reducing Valves
Defining pressure reducing valves (PRVs) is essential for grasping their roles in various systems. PRVs are mechanisms designed to regulate pressure levels, ensuring that downstream systems do not experience excessive pressure. This regulation is important in both residential and industrial applications. Without proper management of pressure, systems can face damages, inefficiencies, or even accidents. Thus, understanding PRVs is not just a technical necessity; it is also a matter of safety and efficiency in any relevant system, contributing significantly to operational integrity.
The Purpose of Pressure Reducing Valves
The primary purpose of pressure reducing valves is to maintain consistent output pressure regardless of fluctuations in the upstream pressure. This consistency is crucial in systems that depend on stable pressure for optimal performance. For instance:
- Water Supply: In residential plumbing, maintaining stable water pressure ensures comfort and functionality in daily tasks.
- Industrial Applications: In manufacturing processes, consistent pressure can affect product quality and equipment lifespan.
By moderating high-pressure bursts, PRVs protect sensitive equipment and help maintain the integrity of various systems. They essentially act as gatekeepers that prevent damaging pressure levels from reaching critical system components.
How PRVs Function
Understanding how PRVs function is key to appreciating their significance. A PRV typically consists of several components working together:
- Inlet and Outlet Ports: These ports allow fluid to enter the valve and exit, thereby controlling flow through pressure regulation.
- Diaphragm Mechanism: This flexible membrane plays a central role in modulating the incoming pressure. It reacts to pressure changes, adjusting the spring mechanism accordingly.
- Spring Mechanism: The spring counterbalances the diaphragm. As the pressure increases, the diaphragm moves, compressing the spring and allowing the PRV to open or close as needed.
- Adjustment Screws: These can be regulated to set the desired output pressure level, allowing customization based on specific system requirements.
As fluid flows through the PRV, the spring and diaphragm collaborate to prevent excessive pressure from passing through. This functionality makes PRVs a vital aspect of many operational systems.
Importance of Pressure Control
Pressure control is a crucial aspect of many engineering systems, particularly in those involving fluids. Managing pressure effectively helps ensure system longevity, safety, and efficiency. High pressure can lead to a series of issues that can compromise the performance and integrity of the system. Understanding the relevance of pressure control can significantly enhance the operational capabilities of various applications.
Effects of High Pressure on Systems
Excessive pressure can have detrimental consequences on mechanical systems. For example, in pipelines, high pressure can lead to ruptures or leaks, causing hazardous spills and potential environmental damage. Additionally, the integrity of materials can be compromised. This often results in increased maintenance costs and equipment downtime. The risks associated with high pressure compel industries to implement effective pressure control measures.
Some of the most critical issues arising from high pressure include:
- Increased risk of equipment failure: Excessive pressure can cause wear and tear on valves, pumps, and pipe fittings, leading to failures that can halt operations.
- Safety hazards: Systems operating under pressure beyond their design specifications can pose serious risks to workers and the environment.
- Operational inefficiency: High pressure can lead to energy losses and increased operational costs as systems may work harder to maintain desired flow rates.
Benefits of Managing Pressure
Implementing effective pressure management practices yields numerous benefits for organizations and industries. Properly controlling pressure helps prevent system failures, reduces maintenance costs, and enhances overall efficiency. Here are a few key advantages of managing pressure:
- Improved system reliability: When systems operate at optimal pressure levels, they function better and have a longer lifespan.
- Enhanced safety: By maintaining pressure controls, organizations can minimize risks associated with accidents and equipment failures.
- Cost savings: Proper pressure management leads to reduced maintenance and operational costs, thus improving overall profitability.
- Environmental protection: Controlling pressure reduces the chances of leaks and spills, which can harm the environment.
In summary, it is essential to recognize the significance of pressure control. The impacts of high pressure on systems are far-reaching, and taking proactive measures can drastically improve operational capabilities and safety standards.
Key Components of a Pressure Reducing Valve
The performance and reliability of pressure reducing valves (PRVs) rely heavily on their key components. Each element plays a distinct role in ensuring that the valve operates effectively. Understanding these components not only enhances operational efficiency but also assists in troubleshooting and maintenance efforts. The main components include inlet and outlet ports, diaphragm functionality, spring mechanism, and adjustment screws. I will discuss each one of these in detail to equip you with a comprehensive understanding of their importance.
Inlet and Outlet Ports
Inlet and outlet ports are fundamental to the functioning of PRVs. The inlet port is where the pressurized fluid enters the valve, while the outlet port is where the regulated fluid exits. The size and configuration of these ports are critical aspects to consider during installation. If the ports are too small, it may lead to pressure drops and reduced flow rates. Conversely, oversized ports could cause instability in pressure regulation.
Proper alignment of both ports is also essential for the valve to operate smoothly. Any obstructions or misalignments can result in backflow or inefficiencies, which can jeopardize system performance. Regular inspections of the ports are necessary to ensure they remain clean and free of debris. Seals around these ports should be examined periodically for wear, as leaks can occur over time. This basic component significantly influences the overall efficiency of the pressure reducing valve.
Diaphragm Functionality


The diaphragm inside a PRV is another crucial component that ensures smooth operation. The diaphragm acts as a barrier between the high-pressure inlet and the low-pressure outlet. When pressure from the inlet side increases, it pushes the diaphragm against a spring. This action determines the amount of fluid allowed to pass through.
A well-functioning diaphragm can effectively adjust the flow and pressure. Conversely, a damaged or worn diaphragm may lead to erratic pressure regulation. It is important to check the diaphragm regularly for signs of fatigue or damage. Replace it if necessary to maintain the system's stability. Education on this component helps ensure optimal performance and prolongs the valve's lifespan.
Spring Mechanism
The spring mechanism is an integral part of pressure control in PRVs. Located behind the diaphragm, this spring resists the diaphragm's movement when pressure is applied. The tension of the spring dictates how much pressure can be released downstream. Therefore, selecting the correct spring is crucial for achieving the desired pressure settings.
Springs come in various sizes and strengths. The choice of spring depends on the application and the pressures involved. Too stiff a spring might restrict fluid flow, while a spring that is too weak might not be able to control pressure effectively. Regular servicing of the spring is essential to ensure that its characteristics remain consistent. Any wear or change in the spring's performance can greatly impact the operation of the valve.
Adjustment Screws
Adjustment screws are user-accessible components that enable fine-tuning of the valve's pressure settings. By turning these screws, operators can increase or decrease the tension on the spring, thus modifying the outlet pressure. The ability to adjust the pressure is particularly valuable in dynamic systems where demand may fluctuate.
While adjustment screws provide essential flexibility, they should be used with caution. Over-tightening can lead to undue stress on the diaphragm and spring, possibly resulting in mechanical failure. Operating personnel should be trained in the correct procedures for adjusting these screws to avoid damage and maintain effective pressure control. Additionally, it is wise to record adjustment settings and changes for future reference. This practice aids in both troubleshooting and maintaining consistent operation across different scenarios.
Regular monitoring and maintenance of the components of a pressure reducing valve are crucial for sustainable operations.
Types of Pressure Reducing Valves
The assortment of pressure reducing valves (PRVs) available is vital in ensuring appropriate pressure management across various applications. Understanding the distinctive types can enhance decision-making for engineers, installers, and maintenance personnel. Each category presents unique features and benefits, thereby influencing performance effectiveness in specific scenarios.
Direct Acting Pressure Reducing Valves
Direct acting pressure reducing valves are designed with a straightforward mechanism. They directly respond to pressure fluctuations with minimal delay. The operational principle relies on the diaphragm, which reacts to changes in inlet pressure. When the pressure rises above a set threshold, the valve closes. This type provides reliable pressure control in smaller systems where quick response is crucial.
Benefits include:
- Simplicity in Design: Fewer components mean less chance for failures.
- Cost-Effectiveness: Usually less expensive than other types.
- Compact Size: Suitable for installations with space limitations.
Considerations also include limited capacity and not being optimal for highly fluctuating conditions. A well-tuned direct acting valve provides consistent performance but may struggle with larger systems requiring extensive control.
Pilot Operated Pressure Reducing Valves
Pilot operated pressure reducing valves function through a two-stage process. A smaller pilot valve controls a larger main valve, allowing for precise pressure regulation. This type can manage significant flow rates with enhanced stability, making it ideal for demanding environments.
Key advantages include:
- Improved Sensitivity: The pilot mechanism offers precise control, ideal for applications where pressure variations are minimal.
- High Capacity: Capable of handling larger volumes while maintaining controlled pressure.
- Flexibility: Offers adaptability in terms of settings and configurations.
However, the increased complexity may lead to higher maintenance needs. Installation requires careful alignment and calibration to ensure optimal function.
Electric Pressure Reducing Valves
As technology advances, electric pressure reducing valves have emerged. These valves employ electronic controls for pressure adjustments. Their ability to integrate with smart systems provides significant versatility in operation. They are particularly useful in applications requiring real-time pressure monitoring and adjustment.
Advantages include:
- Automation and Control: Can easily be integrated into automated systems for precise pressure management.
- Real-Time Data: Capable of gathering data for analysis, enhancing decision-making.
- Remote Monitoring: Allows for off-site control, improving operational efficiency.
Despite these benefits, they often come with higher costs and require a reliable power source. Dependency on electronics may raise concerns regarding failure in extreme conditions or power lapses.
Applications of Pressure Reducing Valves
The application of pressure reducing valves (PRVs) is fundamental to various fields, ensuring optimal performance and safety in systems that require precise pressure control. Understanding how and where PRVs are utilized is critical for students, researchers, educators, and professionals. It enhances the knowledge base for making informed decisions regarding their implementation in real-world scenarios.
PRVs play a key role in enhancing system efficiency, protecting equipment, and minimizing energy consumption. Their benefits can be significant in various applications, reduce wear and tear on infrastructure and extend the lifespan of devices connected to the system. The following sections outline the main areas where pressure reducing valves are vital, along with the specific considerations and advantages each application presents.
Water Supply Systems
Water supply systems depend heavily on pressure control to ensure efficient and safe operation. PRVs contribute to maintaining the appropriate pressure within these systems, protecting distribution networks from high pressure that could lead to leaks or burst pipes. A well-regulated pressure also prevents backflow, which can introduce contaminants into the water supply.
By installing PRVs in municipal water systems and residential environments, utilities can manage peak flow demands during high usage times. Through preventive measures and routine maintenance, these valves can offer a long-term solution that promotes sustainability and resource conservation in water supply management.
Gas Distribution
In gas distribution systems, pressure regulation is critical for safety and performance. High-pressure situations can result in hazardous conditions, including explosions or leaks. PRVs ensure that the gas is delivered at a safe working pressure to residential and industrial consumers.
Moreover, integrating PRVs into gas distribution helps manage fluctuations in pressure caused by demand changes. This capability reduces the potential for gas supply interruptions and enhances system reliability. Regular checks and maintenance routines are necessary for ensuring the effective operation of these valves in gas applications.
Industrial Processes
Industries often require strict pressure regulations for optimal operation. In manufacturing processes, for example, the pressure needs to be controlled meticulously to meet quality standards. Industrial applications that involve steam, chemicals, or fluids heavily rely on PRVs to maintain the necessary pressure levels.
Effective use of PRVs in these settings can lead to increased operational efficiency, improved safety, and better control of process variables. Industries that invest in the right type of PRVs can potentially see lower operational costs and reduced maintenance needs, which directly correlates to improved profitability.
PRVs are often underestimated but are integral components across multiple applications, providing benefits that extend beyond mere pressure control.
In summary, the applications of pressure reducing valves are diverse and crucial. They serve essential functions across water supply systems, gas distribution, and industrial processes. A comprehensive understanding of these applications fosters awareness of the valves' significance in maintaining system reliability, safety, and efficiency.
Installation Considerations of PRVs
The significance of installation considerations cannot be overstated when dealing with pressure reducing valves (PRVs). Proper installation directly impacts the performance and longevity of PRVs in any system. Ensuring that the installation is both methodical and precise often translates into efficiency and reliability in operations. From site assessment to the correct sizing and positioning, each aspect plays a crucial role in how effectively a PRV will function within its designated application.
Site Assessment
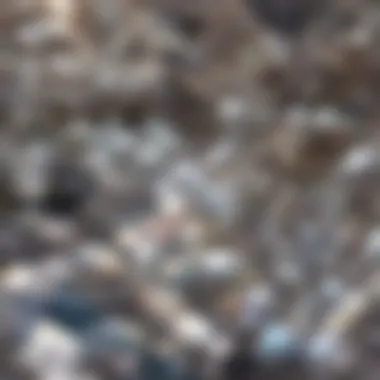

Before any installation can begin, a thorough site assessment is necessary. This involves analyzing the existing system's conditions and requirements. Factors like the pressure background, flow rates, and pipe diameters need to be evaluated.
A careful site assessment can reveal potential challenges. For instance, locations with elevated temperatures may affect valve materials, requiring specific consideration of material compatibility. Furthermore, understanding the immediate environment can aid in planning for maintenance access later on. Identifying these nuances upfront can help mitigate issues down the line, resulting in a more seamless installation process.
Correct Sizing
Choosing the right size for a PRV is fundamental. An undersized valve may fail to handle the required flow rates, leading to inefficiencies or system failures. Conversely, an oversized valve can cause system lag, leading to fluctuating pressures and potential wear and tear on the entire system.
Key sizing elements include:
- Flow requirements: Analyze the maximum flow rates the system expects to handle.
- Pressure settings: Identify the input and desired outlet pressures.
- Pipe dimensions: Match the valve size with existing piping for optimal function.
Accuracy in sizing will significantly enhance both safety and performance. It invites a more predictable response from the system during normal operation. The cascading effects of poor sizing can eventually lead to costly damage and inefficiencies.
Positioning and Orienting
The positioning and orientation of PRVs is another crucial installation consideration. Proper positioning affects how the valve interacts with the flow of fluid. It is generally recommended to install PRVs in a vertical position; however, in certain applications, horizontal configurations may be appropriate.
Considerations for positioning include:
- Proximity to equipment: Installing the PRV close to the point of use can help maintain desired pressure levels in downstream systems.
- Ease of maintenance: Ensure the valve is accessible for inspections and servicing without needing extensive disruption or disassembly of nearby equipment.
- Flow direction: Adhere to the manufacturer’s guidelines regarding the correct flow direction through the valve.
Correct positioning can minimize loss of pressure and enhance overall efficiency, ensuring that the valve operates within its ideal parameters.
In summary, focusing on installation considerations—site assessment, correct sizing, and optimal positioning—forms the backbone of effective pressure reducing valve integration. Neglecting these details can compromise not only the valve’s function but also the broader operational dynamics of interconnected systems.
Maintenance and Care for PRVs
Maintaining pressure reducing valves (PRVs) is vital for ensuring their longevity and operational efficiency. These components not only help in managing pressure but also serve as safeguards against potential failures in various systems. Regular maintenance minimizes unexpected downtime and enhances reliability, thereby optimizing overall system performance.
Regular Inspections
Conducting regular inspections is one of the key practices in maintaining pressure reducing valves. These inspections allow for the early detection of any abnormalities. During an inspection, the following aspects should be considered:
- Visual checks: Look for leaks, corrosion, or any visible wear on the valve.
- Functional testing: Verify if the valve responds appropriately to set pressures. This includes ensuring that it opens and closes appropriately under variable conditions.
- Pressure measurements: Regular monitoring of the input and output pressures is critical. It helps identify if the valve is performing its function efficiently.
Regularly scheduled inspections help in avoiding long-term damage and costly repairs. They can also provide valuable data that informs future maintenance practices.
Cleaning Protocols
Implementing effective cleaning protocols is equally important. Dirt and contaminants can significantly affect the performance of PRVs. A well-defined cleaning process ensures:
- Maintained flow: Keeping the valve clean prevents blockage that may result from accumulated debris.
- Reduced wear: Cleaning reduces the likelihood of wear caused by contaminants entering the internal mechanisms of the valve.
- Improved lifespan: Regularly cleaning components can significantly extend the valve's operational life.
Cleaning should occur following manufacturers' guidelines. It is advisable to use non-corrosive cleaning agents and follow a systematic approach to disassemble, clean, and reassemble the valve.
Component Replacement
Component replacement is crucial for maintaining the efficacy of pressure reducing valves. Some components, such as diaphragms and springs, may experience fatigue over time and require replacement. Key considerations include:
- Recognizing wear signs: Be vigilant to signals that components are degrading, including unusual noises or inconsistent pressure control.
- Using quality parts: Always replace components with manufacturer-approved parts to ensure compatibility and performance standards are met.
- Scheduling replacements: Integrate component checks into your regular inspection routine. Planning ahead helps prevent system failure during critical operations.
Maintaining a systematic approach to inspections, cleaning, and replacements will ensure that pressure reducing valves continue to operate effectively. The integration of these maintenance practices lays a solid foundation for reliability and performance, which is essential in any application where pressure control is necessary.
Troubleshooting Common Issues with PRVs
Troubleshooting common issues with pressure reducing valves (PRVs) is an essential aspect of maintaining effective pressure control in various systems. Properly functioning PRVs prevent unnecessary harm to systems and ensure consistent performance. As pressure fluctuations and other issues can negatively impact performance, identifying and resolving these problems is crucial for reliability and efficiency.
Identifying Pressure Fluctuations
Pressure fluctuations can occur due to various factors, making it essential to recognize the signs. Such fluctuations may indicate upstream pressure changes, valve malfunctions, or air trapped in the system. To identify these fluctuations, it is vital to monitor system pressure over time, using pressure gauges to observe sudden changes. Additionally, pressure recordings can help identify patterns, indicating when fluctuations occur. By analyzing data, one can make informed decisions about maintenance and repairs, avoiding larger system failures.
Leak Detection Methods
Detecting leaks in a PRV is necessary for maintaining system integrity. There are various methods, such as listening for hissing sounds around the valve or visually inspecting for moisture accumulation. A more systematic approach includes using soap solutions that create bubbles around the valve if there is a leak. Additionally, ultrasonic leak detectors can pinpoint the exact location of leaks. Regular monitoring ensures that even minor leaks are addressed promptly, reducing overall maintenance costs and improving system performance.
Valve Seizing Issues
Valve seizing is a significant issue that can lead to complete system failure. Causes of valve seizing often include debris accumulation, corrosion, or improper installation. To prevent seizing, regular maintenance is recommended. This includes cleaning the valve and the surrounding area and ensuring that the valve is correctly lubricated. If seizing has already occurred, troubleshooting involves attempting to free the valve through careful manual pressure or replacement if necessary. It is important to address these issues decisively to safeguard overall system performance.
"Regular maintenance and effective troubleshooting of those common PRV issues are key to a trusted and efficient system."
In summary, troubleshooting common issues with PRVs ensures that systems operate smoothly and prevents costly failures. Proper identification of pressure fluctuations, timely leak detection, and addressing valve seizing are steps that every professional should be familiar with for optimal performance.
Energy Efficiency Considerations
Energy efficiency in pressure reducing valves (PRVs) is vital for effective resource management and operational sustainability. By regulating and reducing high pressure, PRVs help to maintain systems that operate within optimal thresholds. In this section, we explore how energy efficiency is integrated into the design and operation of PRVs and why it is crucial for various sectors.
Impact on Operational Costs
The role of PRVs in cutting operational costs cannot be understated. High pressure in pipelines often leads to wastage of resources and energy. When these valves operate efficiently, they help minimize energy consumption and reduce wear on equipment. Here are key elements to consider regarding operational costs:
- Reduction of Energy Waste: Effective PRVs limit pressure levels, which translates to lower energy expenditure in pumps and compressors.
- Long-term Savings: Investing in high-quality PRVs ensures reduced operational costs over time due to decreased breakdowns and maintenance needs.
- Lower Maintenance: When the system pressure is appropriately maintained, there is less likelihood of damage to pipes and machinery, translating into direct savings.
Optimizing Performance
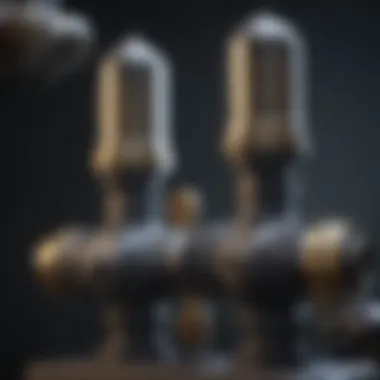

Optimizing the performance of PRVs enhances energy efficiency, leading to a more sustainable operation. Several strategies are employed to achieve this optimization:
- Regular Calibration: Regular checks and adjustments of PRVs can guarantee they function within designed parameters, thereby improving efficiency.
- Choosing the Right Valve Type: Selecting between direct acting and pilot-operated valves based on system needs can significantly impact the effectiveness of pressure regulation.
- Monitor System Parameters: Continuous monitoring of pressure and flow can help in adjusting operations promptly for peaks in demand.
- Integration with Automation: Aligning PRVs with automation systems can enhance responsiveness and energy management.
In summary, integrating energy efficiency considerations into PRV operations not only helps save costs but can also lead to a more sustainable use of resources. Investing in the right technology and maintenance practices is essential to ensure that the benefits of energy efficiency in PRVs are fully realized.
"Energy efficiency is doing more with less. By optimizing PRV function, industries can achieve significant savings and sustainability."
For additional information on pressure control systems, you may visit Wikipedia or Britannica.
Regulatory Standards and Guidelines
In the realm of pressure reducing valves (PRVs), regulatory standards and guidelines play a crucial role. These regulations ensure that PRVs operate safely and efficiently, preventing failures that could lead to significant problems in various systems. Understanding these standards is important for professionals involved in installation and maintenance, as it informs them of the baseline requirements that need to be met to ensure compliance and safety.
Industry Regulations
Industry regulations encompass a set of rules established by governmental and standardizing bodies that govern the design, manufacture, and installation of pressure reducing valves. These regulations are typically based on several factors, including material selection, pressure ratings, and testing protocols.
Common regulatory bodies include the American National Standards Institute (ANSI), the American Society of Mechanical Engineers (ASME), and the International Organization for Standardization (ISO).
Some essential aspects covered by industry regulations are:
- Material Compliance: Ensuring that the materials used in the PRV are suitable for the intended application and can withstand the operational pressures.
- Performance Testing: Mandating that valves undergo rigorous testing to verify their functioning under specified conditions. This often includes tests for leakage, pressure drop, and overall operational performance.
- Labeling Requirements: Establishing clear labeling on PRVs to indicate their specifications and certifications, facilitating easier identification and compliance verification for users and inspectors.
Adhering to these regulations not only enhances safety and performance but also promotes consumer confidence in the products used.
Certification Requirements
Certification requirements serve to validate that a pressure reducing valve conforms to established industry standards. These certifications are typically provided by third-party testing organizations and are crucial in ensuring that products meet safety and efficacy benchmarks. Certifications promote not only the reliability of PRVs but also compliance with relevant sector standards.
Some key considerations regarding certification include:
- Third-Party Validation: Independent organizations perform extensive evaluations of the PRVs to determine if they meet defined performance and safety standards. This instills trust in operators and buyers.
- Periodic Reevaluation: Certifications often require regular testing and reevaluation to ensure that manufacturers continue to comply with the standards over time, promoting ongoing safety during a product’s lifecycle.
- Documentation: Certifications come with documentation proving compliance, which is essential during inspections and for maintaining regulatory compliance.
Adhering to industry standards creates a culture of safety and reliability in the usage and maintenance of pressure reducing valves.
Future Trends in Pressure Reducing Valve Technology
The realm of pressure reducing valve technology is evolving rapidly, driven by advancements in materials, automation, and connectivity. Understanding these trends is critical for professionals across various sectors that rely on effective and efficient pressure management systems. The future of PRVs is not only about optimizing performance but also about improving sustainability and interoperability with existing technologies. As systems trend towards smarter solutions, integrating various components into cohesive networks that communicate efficiently becomes increasingly vital. This section discusses innovations in design and the integration of smart systems.
Innovations in Design
Recent innovations in the design of pressure reducing valves focus on improving their functionality and longevity. Manufacturers are exploring advanced materials to increase resistance to corrosion and wear. For example, employing stainless steel or specialized polymers can enhance the durability of components exposed to harsh environments.
Moreover, the design of PRVs is becoming more compact. Smaller design allows for easier installation and integration into existing systems without significant modifications. Additionally, manufacturers are incorporating modular designs, where parts can be easily replaced without needing to replace the entire valve. This not only reduces maintenance costs but also minimizes downtime during repairs.
Some notable innovations include:
- Self-Adjusting Mechanisms: Certain models use built-in sensors to automatically adjust to changing pressure conditions. This feature increases efficiency and responsiveness.
- Enhanced Flow Paths: Optimized internal geometries can minimize turbulence and improve flow efficiency, leading to better performance across a range of operating conditions.
These advancements not only aim to enhance the performance of pressure reducing valves but also contribute to improved energy efficiency and reduced operational costs in various applications.
Integration with Smart Systems
The rise of smart technology cannot be overlooked in the context of pressure reducing valves. With the growing demand for automation in industry, PRVs are increasingly being designed with smart capabilities for improved monitoring and control.
Integrating pressure reducing valves with smart systems allows for real-time data collection and analysis. This data can include metrics like pressure readings, flow rates, and operational status, which can be accessed remotely through the Internet of Things (IoT). Benefits of this integration include:
- Predictive Maintenance: Monitoring systems can alert operators to potential issues before they escalate, ensuring timely maintenance and reducing the risk of failures.
- Optimized Performance: Advanced algorithms can analyze collected data to determine optimal operating settings, leading to enhanced efficiency and energy savings.
- Data Analytics: Historical data can provide insights into operational trends, helping organizations to make informed decisions about system changes or upgrades.
By adopting these smart solutions, companies can improve not only the functionality of pressure reducing valves but also their overall system performance. These trends reflect a shift towards greater efficiency, automation, and reliability in pressure management systems.
"As we embrace technological advancements, the potential for enhancing pressure management through smart systems is vast and promising."
Case Studies on PRV Implementations
Case studies of pressure reducing valve implementatons are crucial in understanding their role and effectiveness within various industries. Through real-world examples, we can evaluate how these devices handle unique challenges, influencing overall system performance and operational efficiency. Analyzing these case studies not only provides insight into practical applications but also highlights the technical considerations and benefits realized by industries integrating PRVs.
Public Water Systems
In public water systems, PRVs serve a foundational role. They are utilized to maintain consistent downstream pressure while protecting infrastructure components from damage due to pressure surges. For instance, a case in a mid-sized city demonstrated the significance of installing PRVs in reducing the occurrences of pipe bursts. The municipality recorded a 30% decrease in such incidents after implementing PRVs, showcasing their effectiveness at managing demand fluctuations during peak usage times.
The installation of these valves reduced maintenance costs significantly. Prior to PRV deployment, the city spent substantial resources on emergency repairs. Post-implementation, the annual maintenance budget was cut by nearly 15%, reflecting the financial benefits extending from these devices.
Some critical takeaways from this case are:
- Pressure Stability: PRVs can stabilize fluctuating pressures from water supply sources, providing a steady flow to end-users.
- Asset Protection: Infrastructure longevity improves as PRVs mitigate the risk of water hammer and associated damages.
- Cost Efficiency: Reduced maintenance needs contribute significantly to operational savings over time.
Oil and Gas Industries
The oil and gas industry presents complex challenges that demand precise control of pressure levels. A notable case involved a major exploration and production company that faced substantial losses due to fluctuating pipeline pressures. These fluctuations risked leaks and environmental hazards. By integrating PRVs into their pipeline systems, the company was able to successfully control the output pressure of gas being transported.
The results were compelling. Within months, incidents of overpressure alarms dropped by over 80%, demonstrating enhanced operational safety and reliability. Furthermore, the implemented PRVs allowed for better compliance with industry regulations, which are increasingly stringent regarding environmental protection.
The benefits realized by the oil and gas sector include:
- Safety Improvements: With consistent pressure maintenance, potential leaks and failures can be drastically reduced.
- Regulatory Compliance: PRVs aid in adhering to laws that govern environmental safety.
- Operational Efficiency: Continuous operations without interruptions minimize downtime and enhance productivity.
Proper use of pressure reducing valves can lead to remarkable reductions in operational risk and improve overall performance in critical industries.
These case studies emphasize the utility of PRVs across diverse applications, from public utilities managing urban water systems to highly regulated environments in oil and gas. The integration of smart pressure management not only fulfills immediate operational needs but also establishes a proactive approach toward problem-solving in infrastructure management.