Understanding Rota Linear Transducers: A Detailed Guide
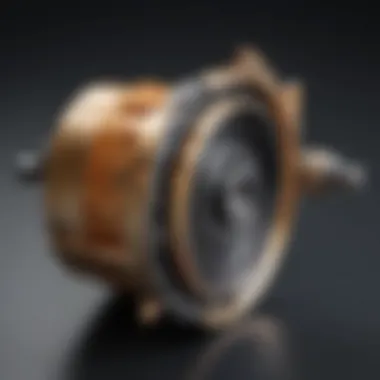
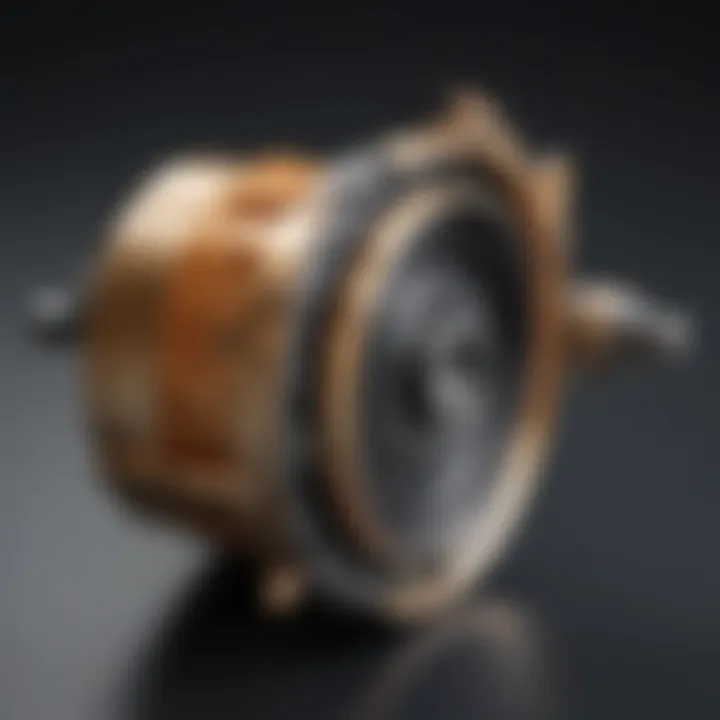
Intro
Rota linear transducers represent a specialized field of technology that is critical in measuring and control applications across various industries. These devices convert rotary motion into a linear output, making them essential in systems where accurate position feedback is necessary. Understanding their design and operation involves delving into the complexities of their mechanisms and the environments in which they operate.
The increasing reliance on automation in sectors like manufacturing, robotics, and aerospace underscores the importance of these transducers. They enable precise control and monitoring, enhancing efficiency and reliability in systems. A comprehensive exploration of rota linear transducers not only sheds light on their functionality but also enhances our grasp on their practical applications and future development.
Research Context
Background and Rationale
The development of rota linear transducers has evolved significantly since their inception. Originating as simple mechanical devices, they have transformed through advances in materials, sensors, and data processing technologies. This evolution speaks to the need for robust, accurate, and efficient measurement systems in modern engineering practices.
Many industries now depend on these transducers to provide real-time feedback, ensuring systems operate within defined parameters. The rationale behind this article is to clarify the operational principles of rota linear transducers. By presenting various applications, readers can grasp their relevance and potential impact in diverse fields.
Literature Review
Existing literature on rota linear transducers reveals a range of applications and technological advancements. Numerous research studies examine the specifics of different types of transducers, their designs, and functionality.
Some critical sources include:
- Books on Sensor Technology: These provide foundational knowledge on the principles of transducer operation.
- Research Articles: Scholarly articles often explore innovations and real-world applications, showcasing case studies of successful implementations.
- Industry Reports: These documents shed light on market trends and emerging technologies, allowing professionals to understand the competitive landscape.
Understanding the background through these varied resources helps illuminate the current state and future directions for rota linear transducers. This synthesis of information equips researchers, students, and engineers with vital knowledge for further explorations or applications in their practices.
Prelims to Rota Linear Transducers
Rota linear transducers represent a critical component in the field of measurement technology. Their fundamental role is to convert mechanical motion into an electrical signal. This process gives engineers and researchers accurate data for various applications, thus helping in the development of systems that rely heavily on precise measurements.
The significance of understanding rota linear transducers lies in their versatility. Used in industries ranging from automotive to industrial automation, these devices help in monitoring the position, speed, and acceleration of moving parts. With the growing reliance on automation and data-driven decisions, the importance of these transducers only increases.
Key elements that define rota linear transducers include:
- Mechanical Configuration: They often feature a rotating element that translates linear movement into an electrical output.
- Signal Output: Most of them produce analog or digital signals, which allows easy integration with modern control systems.
- Calibration Procedures: Calibration ensures that the transducer provides accurate readings, making it essential to know how to implement this correctly.
The benefits of using rota linear transducers are numerous. First, their ability to provide precise measurements can improve safety and efficiency in various applications. Second, understanding the design and functionality of these transducers allows engineers to address specific challenges in their projects.
Historical Context of Transducer Development
The evolution of transducer technology is essential for understanding the contemporary applications of rota linear transducers. By tracing the historical roots, one can appreciate how innovations in measurement technology paved the way for these sophisticated devices. This historical context gives insight into the objectives that have driven advancements in this field.
Early Innovations in Measurement Technology
Measurement technology has seen a transformative journey from its earliest days. The introduction of simple devices like the lever and wheel set a foundation. Early scientists and engineers strived for greater precision in measurement, particularly in mechanical systems.
The need for accurate data in fields such as engineering and physics drove foundational breakthroughs. Devices such as the pendulum and later gauges were critical in enhancing measurement accuracy. These developments established a framework that later allowed for advanced transducer forms. Throughout the 18th and 19th centuries, innovations focused on mechanical components. The transition was gradual, driven by a necessity for efficiency and exactness. Engineers began integrating electrical concepts with mechanical designs, leading towards the development of electromechanical devices which eventually became crucial for understanding modern transducer designs.
The Emergence of Rota Linear Transducers
Rota linear transducers emerged in the mid-20th century as technological demands increased. With the rise of automation and complex systems, industries required more efficient and reliable measurement solutions. The mechanical concepts from earlier innovations were reimagined to suit this need.
Electromechanical transducers adapted rotational motion into a linear format, which allowed for more versatile applications. Their development was closely linked to advancements in materials science and electronics. The marriage between precision engineering and electronics resulted in devices that could translate motion into electrical signals accurately.
Rota linear transducers are pivotal in multiple sectors. They support automation by allowing machines to perform tasks with precision. Their emergence marked a significant transition from purely mechanical systems to ones that could incorporate electronic feedback. This evolution has enabled industries to operate with greater efficiency and interoperability, showing the importance of understanding their history.
"The understanding of the historical development of transducers reveals the innovations needed to meet modern technological demands."
In summary, exploring the historical context of transducer development showcases a rich evolution. Early innovations laid the groundwork for advanced devices like rota linear transducers. Recognizing this evolution is fundamental for anyone engaging with the field today, ranging from students to seasoned professionals.
Fundamentals of Rota Linear Transducer Operation
The operation of rota linear transducers is crucial to understand. Their mechanisms dictate how motion and position are measured accurately across various applications. A strong grasp of the fundamentals will enable users to optimize the performance of these devices while ensuring appropriate implementations that align with industrial standards.
Mechanics of Motion Sensing
Motion sensing is the core function of rota linear transducers. These devices work by converting mechanical motion into an electrical signal. Depending on the design, motion can be linear or rotational. The choice of sensing mechanism often depends on the application needs. There are two prominent types of mechanics involved in motion sensing for these transducers:
- Potentiometric Sensing: This method utilizes variable resistors. As the shaft or arm moves, it alters the resistance, leading to a change in voltage. This voltage change reflects the position of the moving component.
- Inductive Sensing: Inductive methods employ coils and magnetic fields to detect motion. The change in the inductance as the object moves is measured, providing a high level of precision in position sensing.
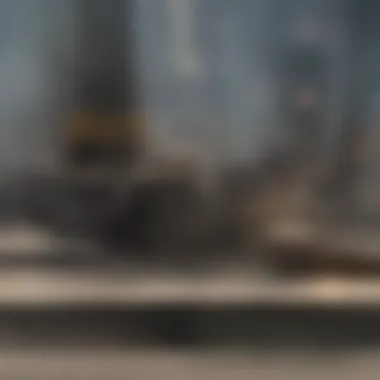
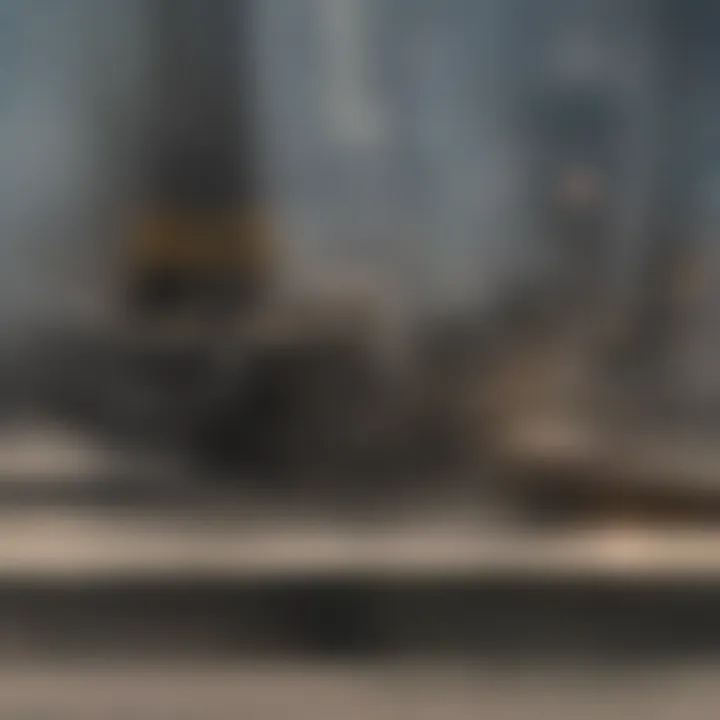
Both methods come with their benefits. Potentiometric sensing is straightforward and cost-effective, while inductive sensing offers better durability and resistance to environmental factors. Thus, the choice hinges on the specific use case and desired performance.
Signal Processing Techniques
After motion is sensed, the subsequent processing of signals is vital. Signal processing involves a series of techniques that enhance the raw data collected from the motion sensing components. This step is essential for ensuring the accurate interpretation of the data for further action or analysis.
Key techniques in signal processing include:
- Filtering: Noise reduction is necessary in any signal processing. Filters, both low-pass and high-pass, are used to eliminate unwanted frequencies that may obscure the true signal.
- Analog-to-Digital Conversion: Most modern systems require the conversion of analog signals to digital formats. This enables easier computation, storage, and transmission of data.
- Signal Conditioning: Enhancing the quality of the signal ensures that it meets the required specifications for the target application. This may involve amplification or other modifications to ensure clarity and integrity.
Robust signal processing ensures that the data retrieved from rota linear transducers can be utilized effectively, improving overall system performance and reliability.
In addition, integrating advanced algorithms can yield better results in interpreting the sensor data. The development of user-friendly interfaces further enhances accessibility for professionals who may not specialize in sensor technologies.
Understanding the fundamentals of operation for rota linear transducers is not merely academic. It is foundational for practical applications in fields such as industrial automation and automotive engineering. The mechanics of motion sensing and the critical role of signal processing define the success of these devices in real-world scenarios.
Types of Rota Linear Transducers
Understanding the various types of rota linear transducers is essential in grasping their applications and operational efficiencies. Each type serves a unique purpose influenced by the principles of operation, environmental constraints, and material properties. This section addresses three primary categories: Electromechanical, Optical, and Magnetic Transducers. Each category presents distinct advantages and use-cases, making it vital for professionals and researchers to recognize these differences when selecting a transducer for specific applications.
Electromechanical Transducers
Electromechanical transducers convert mechanical motion into electrical signals. This transformation is crucial in applications that require precise motion detection. They typically involve components such as potentiometers and strain gauges. Potentiometers measure angular displacement, while strain gauges are used to assess mechanical stress in various materials.
One significant advantage of electromechanical transducers is their robustness. They perform well even in challenging conditions. This reliability is essential for industries like aerospace and automotive engineering, where failure is not an option. Compatibility with a wide range of systems enhances their usefulness in automation processes.
Despite their strong points, they have limitations. Calibration of these devices is critical. If not set properly, measurement inaccuracies can arise. Another challenge is their susceptibility to wear and tear over time, resulting in reduced lifespan and reliability.
Optical Transducers
Optical transducers utilize light to measure displacement or position. These devices can be highly sensitive and are often used in applications requiring high precision. They operate using principles of light reflection and absorption, making them suitable for a variety of settings, including industrial and medical.
One key benefit of optical transducers is their non-contact measurement capability, allowing them to function without physical contact with the object. This minimizes wear on both the transducer and the target surface. Applications in fields like robotics, industrial automation, and even consumer electronics showcase their versatility and efficiency.
However, environmental factors can affect the performance of optical transducers. Dust, moisture, and other contaminants can obstruct the light path, leading to inaccuracies. Proper enclosure and maintenance are essential to ensure reliable operation.
Magnetic Transducers
Magnetic transducers are devices that gauge movement or position through magnetic fields. They often employ Hall-effect sensors to detect changes in magnetic fields associated with movement. These transducers are common in applications where durability and long operational life are needed.
The strength of magnetic transducers lies in their resistance to environmental factors like dirt and humidity. They generally require low maintenance once installed. Their robustness makes them an ideal choice in automotive applications and industrial machinery, where exposure to harsh conditions is a normal occurrence.
Nonetheless, their use is limited in environments with high magnetic interference, which can distort measurements. The design must consider magnetic field sources to minimize performance issues.
In summary, selecting the right type of rota linear transducer depends on the specific needs of an application, including environmental conditions and required precision. Understanding these categories provides researchers and engineers with a clear perspective on transducer options that align with their project demands.
Design Considerations for Rota Linear Transducers
The design of rota linear transducers is crucial for optimizing their functionality and performance. This section will explore two key aspects: Material Selection and Specification and Geometry and Size Impacts. Each of these elements plays an important role in ensuring reliability and accuracy in transducer applications.
Material Selection and Specification
Choosing the right material for rota linear transducers directly influences their performance and durability. Various materials have distinct physical and chemical properties that can enhance or limit the transducer's effectiveness. Commonly selected materials include metals, plastics, and ceramics.
- Metals are often used for their strength and resistance to wear. For instance, stainless steel provides robustness while also resisting corrosion.
- Plastics can offer lightweight alternatives, which may facilitate easier installation and reduce the overall weight of the equipment in which the transducer is housed.
- Ceramics are sometimes utilized for their high temperature tolerance and insulating properties.
When selecting materials, it is vital to consider environmental factors, such as temperature fluctuations and exposure to corrosive substances. Material specifications must also align with the intended application, ensuring the transducer meets necessary performance criteria. Failure to select appropriate materials can lead to premature wear or malfunction of the transducer.
Geometry and Size Impacts
The geometry and size of rota linear transducers are equally important considerations that influence their operation and integration into systems. The design must accommodate the spatial constraints of the equipment while preserving the accuracy of motion sensing.
- Size plays a role in the installation and overall effectiveness of the transducer. A smaller transducer may fit better in limited spaces but could potentially sacrifice performance. Conversely, a larger unit might provide better resolution but may be impractical in compact designs.
- Geometry, meanwhile, often impacts the mechanical interaction with other components. An optimized shape can ensure efficient energy transfer and simplify the assembly process.
In summary, attention to both material selection and geometric design is essential in constructing effective rota linear transducers. These considerations not only enhance the accuracy and efficiency of measurement but also influence the longevity and reliability of the devices in various applications.
Applications of Rota Linear Transducers
Rota linear transducers play a crucial role in various sectors due to their unique ability to provide real-time and accurate measurements. Their applications span across industries, enabling enhanced automation, precision control, and effective measurements in critical systems. In this section, we will focus on three main fields where these transducers are especially significant: industrial automation, medical devices, and automotive engineering. Each application area will highlight specific benefits and considerations related to the use of rota linear transducers.
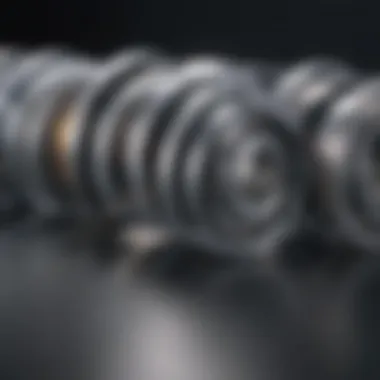
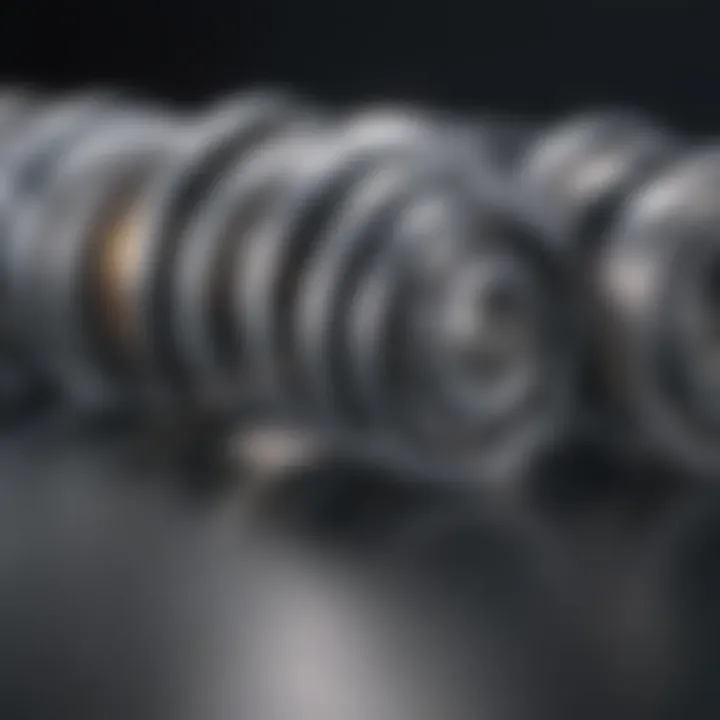
Industrial Automation
In industrial automation, rota linear transducers are essential for monitoring and controlling machinery. They translate linear displacement into an electrical signal, allowing for precise measurement of movement. This capability is vital for applications such as conveyor belt systems, robotic arms, and CNC machines.
The key benefits of utilizing rota linear transducers in this sector include:
- Increased Efficiency: The real-time data they provide helps in optimizing operational processes.
- Improved Safety: With accurate measurement, systems can quickly detect anomalies, reducing risks of accidents.
- Enhanced Quality Control: Continuous monitoring ensures that production lines maintain high standards.
"In automation, precision is not just an advantage; it is a necessity. Rota linear transducers ensure that operators have the data they require at every stage of the process."
When incorporating these devices, engineers must consider factors such as environmental conditions, expected lifespan, and compatibility with existing systems. Proper integration can significantly elevate productivity and reliability in manufacturing processes.
Medical Devices
The healthcare industry benefits immensely from rota linear transducers, as they are integral to various medical devices. For instance, in imaging systems such as MRI and ultrasound machines, these transducers help achieve accurate positioning and movement control.
Their application in medical devices is characterized by:
- Precision: Accurate measurements are critical for diagnoses and treatment planning.
- Miniaturization: Modern medical devices often require compact and precise components, which rota linear transducers can provide.
- Real-Time Feedback: They allow for immediate monitoring of patient parameters, enhancing treatment effectiveness.
Implementing rota linear transducers in medical technology also necessitates adherence to strict safety regulations and standards. This ensures that the devices are reliable, efficient, and safe for patient use.
Automotive Engineering
In the automotive sector, rota linear transducers are used predominantly for systems requiring precise measurement of position and motion. Examples include electronic throttle control systems, vehicle stability controls, and advanced driver assistance systems (ADAS).
Some of the critical advantages of these transducers in automotive engineering include:
- Enhanced Performance: They contribute to improved vehicle performance and handling by providing real-time data directly from the components.
- Increased Safety: With accurate feedback, these systems can react swiftly to changing conditions, enhancing overall safety.
- Integration with Emerging Technologies: They can be integrated into electric and autonomous vehicle systems, supporting innovations in driving technologies.
It is essential for automotive engineers to value not only the precision but also the robustness of the transducers used in various applications. The challenges of durability and environmental conditions, such as temperature fluctuations and vibrations, must be addressed to maintain efficacy.
Advantages of Using Rota Linear Transducers
Rota linear transducers have become vital in modern engineering and technology due to their remarkable benefits. Understanding these advantages enables better selection and application of transducers in various industries. This section addresses two primary benefits: precision and accuracy, and versatility in applications.
Precision and Accuracy
Precision and accuracy are indispensable in measurement systems. Rota linear transducers deliver high precision in determining linear or rotational positions. This characteristic makes them suitable for applications requiring meticulous measurements, such as robotics and aerospace engineering.
The efficacy of these devices stems from their construction. For instance, optical transducers utilize the interference of light to gauge position, yielding extremely accurate outputs. Electromechanical models combine mechanical components with electrical sensors, achieving robust performance in various environments. The ability to measure with high fidelity minimizes errors, which is critical in sensitive applications.
Moreover, the calibration process of these transducers can help maintain their accuracy over time. Regular calibration ensures that devices adhere to industry standards, thus enhancing reliability and trust in the collected data. This reliability is essential for sectors like healthcare, where patient safety may depend on the accuracy of measurements taken.
Versatility in Applications
Rota linear transducers possess a significant advantage: versatility. Their design allows application across diverse fields including industrial automation, automotive engineering, and medical devices. The adaptability comes from their ability to be integrated into various systems without extensive alterations.
For example, in industrial automation, rota linear transducers can monitor equipment performance, ensuring machines operate at optimal levels. In automotive engineering, they play a crucial role in position sensing within automated driving systems, contributing to safety and efficiency.
Similarly, in the medical field, their use in devices ensures precise monitoring of patient vitals. This adaptability not only enhances performance but also reduces costs associated with the development of separate devices for distinct applications. The possibility to use one type of transducer across multiple platforms significantly simplifies engineering processes.
The versatility of rota linear transducers is vital for engineers seeking efficient and effective solutions across different domains.
Limitations and Challenges
Understanding the limitations and challenges of rota linear transducers is crucial for professionals working in fields where accuracy and reliability are paramount. Despite their many advantages, such as precision and versatility, these devices are not without their pitfalls. Being aware of these issues can help engineers and researchers design better systems and mitigate risks in practical applications.
Calibration Difficulties
Calibration is a key aspect in the functioning of rota linear transducers. It involves adjusting the device to ensure measurement accuracy. However, calibration can present difficulties due to several reasons.
- Drift Over Time: Transducers may experience drift, leading to inaccuracies in measurement during prolonged use. Regular calibration is necessary to correct these errors.
- Temperature Influence: Changes in temperature can affect sensor readings, complicating the calibration process. Maintaining a consistent environment is often essential.
- Difficulty in Setting-Up: Setting up calibration procedures can be complicated. It typically requires specific knowledge and may involve specialized tools, increasing the chances of human error.
Addressing these calibration challenges is important. Advanced calibration strategies like auto-calibration and temperature compensation can help improve accuracy and reduce the frequency of manual adjustments.
Environmental Sensitivities
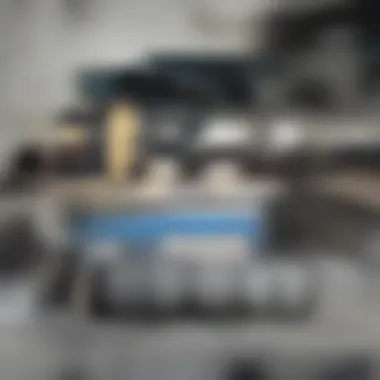
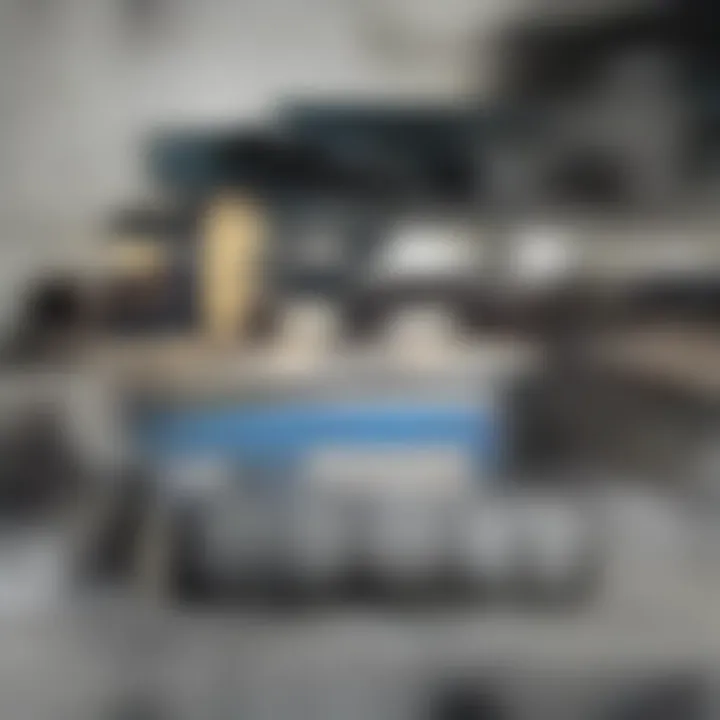
Rota linear transducers are often sensitive to environmental conditions. These sensitivities can impact performance and reliability in various industries.
- Humidity: Excessive moisture can lead to electrical failures and corrosion, affecting signal output. Ensuring that devices are well-sealed can mitigate such risks.
- Vibration: External vibrations from machinery or foot traffic may disrupt the precision of readings. It is important to consider the installation environment when deploying these devices.
- Electromagnetic Interference: Nearby electrical equipment can introduce noise that disrupts signal integrity. Shielding and proper placement away from interfering sources are critical.
Being aware and addressing these environmental sensitivities is vital for ensuring that roto linear transducers operate effectively in diverse applications. By doing so, stakeholders can uphold the integrity of their systems while optimizing performance.
Future Trends in Rota Linear Transducer Technology
The rapid advancement in technology has significant implications for the future of rota linear transducers. As industries evolve, so do the demands on the transducer technology. This section explores emerging trends that are shaping the future. Emphasis is placed on the importance of these trends, how they enhance the functionality of transducers, and elaborate on the implications for various sectors.
Integration with IoT
The integration with the Internet of Things (IoT) represents a revolutionary shift in how rota linear transducers operate. By embedding these sensors in a networked environment, data collection becomes seamless and efficient. With live data availability, real-time monitoring allows for immediate response to changing conditions.
Consider some key benefits of this integration:
- Enhanced Connectivity: Rota linear transducers can communicate wirelessly with other devices. This reduces the need for complex wiring and allows flexibility in installation and usage.
- Data-Driven Insights: Analytical tools can be applied to the data collected by these sensors. This enables predictive maintenance and optimization of operational processes.
- Improved User Experience: Users can access data via applications or cloud platforms, allowing for a better understanding of system performance.
As industries focus on smart operations, the role of IoT in rota linear transducers will likely expand.
"The convergence of IoT and transducer technology is set to change how we approach measurements and data analysis in real-time."
Advancements in Sensor Technology
Advancements in sensor technology are critical to the development of rota linear transducers. Innovations in materials, miniaturization, and sensing principles are enhancing their performance.
Some notable advancements include:
- Silicon-Based Sensors: The use of silicon in manufacturing sensors contributes to increased miniaturization. This allows for smaller, more precise transducers that can be easily integrated into various applications.
- Enhanced Sensitivity: Improved sensitivity in sensors leads to greater accuracy in measurements. This is crucial in sectors where minute variations can significantly impact performance, such as in medical or aerospace applications.
- Adaptive Algorithms: The use of adaptive algorithms in sensor technology allows for self-calibration and adjustment based on environmental conditions. This leads to more consistent performance, reducing the need for frequent recalibrations.
These advancements prepare the ground for a future where rota linear transducers are smarter and more adaptable to the changing landscape of technology.
Regulatory and Safety Standards
Understanding regulatory and safety standards is crucial for the effective utilization and deployment of rota linear transducers in various industries. These standards ensure that the devices function reliably and safely, thus increasing user confidence and satisfaction. Compliance with these standards can also minimize legal risks for manufacturers and users alike. Standards can vary significantly based on the application, but they all aim to promote safety, quality, and performance reliability.
Key Considerations:
- Legal Compliance: Adhering to regulations is mandatory in many regions. Failure to comply can result in penalties or recalls.
- Quality Assurance: Standards define thresholds for product quality, which helps in maintaining a consistent output.
- User Safety: Regulatory frameworks often include guidelines designed to protect consumers from malfunctioning or unsafe devices.
- Market Access: Meeting regulatory standards is often required for entering international markets.
These elements highlight the importance of understanding how different regulations can affect the design and usage of rota linear transducers.
Standards for Industrial Use
Regulatory standards for industrial use of rota linear transducers primarily focus on performance, reliability, and environmental safety. They ensure that these devices can withstand harsh operating conditions typical in industrial settings. Common standards may include those from organizations like the International Electrotechnical Commission (IEC) and Institute of Electrical and Electronics Engineers (IEEE).
Common Standards Include:
- IEC 61000 Series: Addresses electromagnetic compatibility.
- ISO 9001: Pertains to quality management systems.
- UL 508: Covers industrial control equipment safety.
Adhering to these standards not only assures performance quality but also safeguards equipment and personnel, which is essential for operational integrity.
Medical Device Compliance
In the medical field, the compliance of rota linear transducers is even more stringent due to the potential health implications of their failures. Standards set forth by the Food and Drug Administration (FDA) in the United States and the European Medicines Agency (EMA) are significant. These regulations require rigorous testing and thorough documentation before a device can be marketed.
Key Regulatory Aspects for Medical Devices:
- Risk Management: Follow ISO 14971 for risk assessment and management.
- Documentation: Maintain a thorough technical file as required by Medical Device Regulation (MDR) in Europe.
- Quality Control: Utilize Good Manufacturing Practices (GMP) to ensure product reliability.
Ensuring compliance with medical device regulations is not just about meeting legal requirements; itβs about safeguarding patient well-being.
In summary, understanding regulatory and safety standards for rota linear transducers is imperative across various sectors. This not only enhances the device's reliability and safety but also assures users of its performance integrity.
Finale
In this article, we have examined the multifaceted world of rota linear transducers. We explored the intricate aspects of their design, operation, and varied applications across multiple industries. Understanding the significance of rota linear transducers is vital for students, researchers, educators, and professionals alike.
Rota linear transducers provide essential data that is used in monitoring and controlling mechanisms. Their adaptability makes them suitable for various fields including industrial automation, medical devices, and automotive engineering. The precision and accuracy of these transducers lead to improvements in system efficiencies and reliability.
An important consideration is the ongoing evolution of technology. As industries increasingly integrate these transducers into complex systems, the demand for enhanced performance and functionality grows. Furthermore, the integration of IoT and advancements in sensor technology signify a future where these devices play a pivotal role in data collection and system responsiveness.
The challenges outlined, such as calibration difficulties and environmental sensitivities, remind us that while these devices offer significant benefits, they are not without their limitations. Ensuring adherence to regulatory and safety standards is equally crucial for their successful implementation in sensitive industries like healthcare.
In summary, the comprehensive exploration of rota linear transducers stresses not only their current applications and advantages but also highlights the necessary considerations that must be addressed moving forward. By understanding these factors, practitioners can better leverage this technology for improved outcomes in their respective fields.