Understanding Rotary Peristaltic Pumps: Features and Benefits

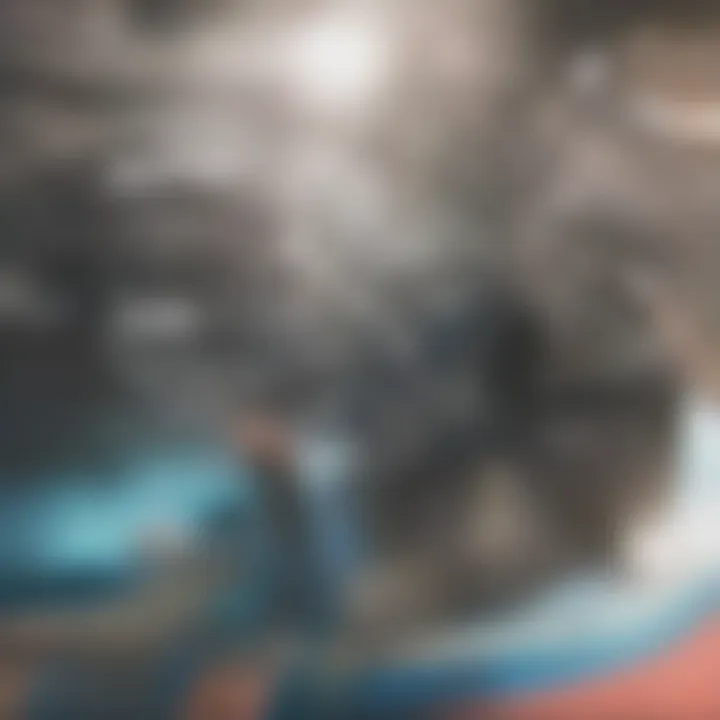
Intro
Rotary peristaltic pumps represent a vital component of modern fluid handling systems. These pumps operate on a simple yet effective principle of positive displacement. Understanding how they function, along with their diverse applications and inherent advantages, is crucial for those involved in industries that rely on the transfer of fluids.
In this article, we will delve into the mechanics of rotary peristaltic pumps. We will also explore their applications in various sectors ranging from medical to industrial. This comprehensive analysis aims to cater to students, researchers, educators, and professionals who seek to enhance their knowledge about advancements in fluid dynamics and engineering.
Research Context
Background and Rationale
The emergence of rotary peristaltic pumps can be traced back to the need for reliable fluid transfer systems that minimize contamination. Due to their design, these pumps ensure that the fluid only comes into contact with the tubing, making them ideal for various applications where hygiene is paramount. As industries evolve, the demand for effective and efficient fluid handling continues to grow.
Literature Review
Several studies have examined the performance of rotary peristaltic pumps. According to past research, these pumps are favored for their ability to handle shear-sensitive fluids without damaging them. Their usage spans multiple sectors, including pharmaceutical manufacturing, food processing, and water treatment.
Recent literature also highlights the technological advancements in materials and design. Innovations in tubing materials have improved the durability and efficiency of these pumps, allowing for a broader range of applications. Furthermore, academic journals consistently note the importance of these pumps in reducing operational costs in the long term.
Methodology
Research Design
This article employs a qualitative research design, integrating findings from previous studies and technical specifications that delineate the functionality of rotary peristaltic pumps. The objective is to gather comprehensive data that reflects their advantages and limitations.
Data Collection Methods
Data was collected through a review of existing literature, including academic journals, technical manuals, and industry reports. Insights from manufacturers and case studies regarding the practical applications of these pumps have also been incorporated.
By synthesizing information from these various sources, this article aims to present a well-rounded understanding of rotary peristaltic pumps and their significance in contemporary fluid transfer systems.
Intro to Rotary Peristaltic Pumps
Rotary peristaltic pumps play a critical role in various industrial applications. Their unique functionality ensures efficient fluid transfer without contamination. This characteristic is especially significant in sectors where purity is essential, such as pharmaceuticals and food processing. The understanding of rotary peristaltic pumps is vital for students, researchers, and professionals in engineering and fluid dynamics.
Definition and Overview
A rotary peristaltic pump is a type of positive displacement pump. It works by compressing and relaxing a flexible tubing to move fluids. This action mimics the natural peristaltic motion found in biological systems, such as human digestion. The pump's design typically features an external rotor that compresses the tubing, creating a vacuum that draws the fluid in.
This design minimizes contact between the fluid and mechanical components, reducing contamination risks. Key components include the rotor, tubing, and housing. The choice of tubing material and inner diameter significantly affects flow rates and chemical compatibility.
Historical Development
The concept of peristaltic pumps has existed for centuries. Early devices were developed in the 19th century for laboratory use. The technology evolved with advancements in materials and mechanics. In the mid-20th century, rotary peristaltic pumps gained popularity in various industries, driven by the need for reliable fluid handling solutions.
Today, these pumps are utilized in sophisticated applications, benefiting from ongoing innovation. This includes the development of high-performance tubing and automated control systems, which enhance their efficiency and accuracy. The historical journey of rotary peristaltic pumps reflects their adaptation to meet changing industry demands, underscoring their importance in modern fluid transfer systems.
Operating Principles of Rotary Peristaltic Pumps
Understanding the operating principles of rotary peristaltic pumps is crucial, as it gives insight into their functionality. These pumps utilize a rhythmic motion to move fluids, making them distinct in various applications. Their design reflects certain engineering marvels that enhance efficiency while minimizing contamination risks.
Mechanism of Fluid Transfer
The mechanism behind fluid transfer in rotary peristaltic pumps is remarkably straightforward yet effective. The process begins when rollers rotate around a flexible tube. As a roller presses down on the tube, it compresses the fluid inside. This action creates a vacuum behind the roller, allowing for the fluid to be drawn in, thus creating a continuous line of flow. Once the roller passes, the tube returns to its original shape, further propelling the fluid forward. This cycle repeats for each roller in sequence.
This mechanism offers various advantages. It allows for gentle handling of fluids, making the pump suitable for shear-sensitive materials. The sealed system means the fluid only contacts the interior of the tube. This minimizes the risk of contamination, which is especially important in industries like pharmaceuticals or food processing.
Components and Design Features
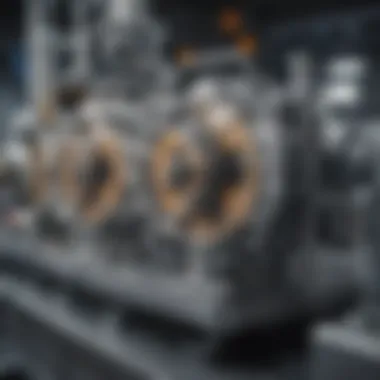
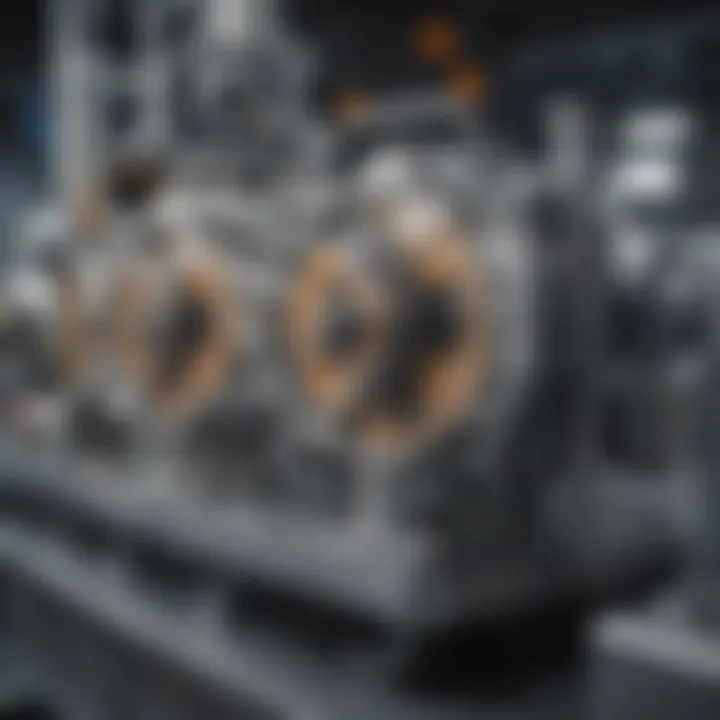
The design of rotary peristaltic pumps consists of several key components that contribute to their effectiveness. The most essential part is the flexible tube itself, usually made of materials such as silicone or thermoplastic elastomer. This material choice enhances durability and the ability to withstand various chemical environments.
Other important components include:
- Rollers: They come in different shapes and sizes to suit varied applications. Their arrangement influences the flow rate and pressure characteristics of the pump.
- Pump Head: This houses the tubing and rollers, maintaining the necessary alignment for optimal operation.
- Drive Mechanism: Often a motor drives the rollers, which can be controlled for precise flow rates.
A notable feature of many rotary peristaltic pumps is their ability to self-prime. This characteristic allows them to function well in situations where traditional pumps would struggle. Additionally, the simplicity of replacing tubing reduces downtime, facilitating straightforward maintenance.
In summary, rotary peristaltic pumps thrive on their unique operating principles, which blend simplicity and effectiveness, making them perfect for various applications across multiple industries.
Types of Rotary Peristaltic Pumps
The classification of rotary peristaltic pumps is critical for understanding their various applications and functionalities. Different types of pumps cater to specific requirements, and recognizing these distinctions can enhance efficiency and performance in fluid handling. Two main categories emerge in this context: standard rotary peristaltic pumps and advanced precision pumps. Each type has its own advantages and considerations, which contribute to their suitability in diverse industrial applications.
Standard Rotary Peristaltic Pumps
Standard rotary peristaltic pumps are among the most common types utilized in various sectors. These pumps primarily feature a simple design that includes a rotor and flexible tubing. The rotor compresses the tubing to create suction and discharge of fluids.
Key features include:
- Affordability: Standard models are generally more cost-effective compared to their advanced counterparts.
- Versatility: They can handle a range of fluids including slurries and viscous materials.
- Ease of use: Simple maintenance procedures make them user-friendly for operators.
In sectors like agriculture, wastewater treatment, and general industrial applications, standard rotary peristaltic pumps excel. However, they may not deliver the accuracy required in applications involving sensitive measurements or specific flow rates. These pumps are suitable for operations where moderate precision is enough, making them reliable choices in many environments.
Advanced Precision Pumps
Advanced precision pumps represent a significant upgrade in technology, extending the capabilities of standard pumps. These models are engineered for higher performance and greater accuracy.
Notable characteristics include:
- Greater precision: Advanced pumps are designed to ensure consistent flow rates and accurate dosage, which is essential in industries such as pharmaceuticals and biotechnical applications.
- Improved materials: High-quality materials are often used in construction, enhancing the durability and resistance to chemical degradation.
- Integration capabilities: Many advanced models allow for easy integration with monitoring systems and automated processes, leading to streamlined operations.
Applications for advanced precision pumps are prevalent in critical industries. For example, in the pharmaceutical sector, maintaining strict adherence to dosing requirements is vital. As a result, advanced pumps function optimally, maintaining product integrity and performance.
Applications in Various Industries
The applications of rotary peristaltic pumps are vast and diverse, reflecting the versatility of this technology. By understanding the specific needs of different industries, we can appreciate how these pumps enhance operational efficiency and ensure product integrity. The ability to convey viscous and abrasive fluids without contamination is a significant benefit that many sectors find invaluable. Each industry leverages rotary peristaltic pumps in unique ways, optimizing processes that demand precision and reliability.
Pharmaceutical Industry
In the pharmaceutical sector, rotary peristaltic pumps play a critical role. They are commonly used in the production of medicines, vaccines, and other health-related products. The pumps are especially valued for their non-contaminating operation, which is essential when dealing with sensitive compounds. These pumps effectively transport fluids without exposing them to outside contaminants. This is crucial in environments where sterility is paramount, like cleanrooms.
Moreover, the self-priming capabilities of these pumps allow for reliable fluid delivery. This feature is significant when processing materials that must be handled carefully to maintain their properties. Furthermore, the design of rotary peristaltic pumps permits easy adjustments to flow rates, ensuring exact dosing of active ingredients in formulations. This precision in the pharmaceutical industry not only enhances product quality but also complies with regulatory standards.
Food and Beverage Sector
In the food and beverage industry, rotary peristaltic pumps find extensive application owing to their hygienic design and ease of cleaning. They can transport a variety of liquids, including juices, sauces, and dairy products, while adhering to food safety regulations. The pumps' ability to handle shear-sensitive products is another advantage, as it prevents alterations in taste or texture during transfer.
Moreover, the ease of maintenance is a critical factor in food production facilities. Quick disassembly and reassembly of the pump components facilitate regular cleaning, reducing downtime. In addition, rotary peristaltic pumps minimize the risk of cross-contamination between different products, a significant concern in the food sector. By ensuring that each product is handled independently, manufacturers enhance both safety and quality.
Chemical Processing
The chemical processing industry benefits from rotary peristaltic pumps due to their robustness in handling harsh and corrosive substances. These pumps can manage a range of fluid types, including slurries, acids, and bases, in various concentrations. The materials used for the pump tubing are tailored to withstand severe chemical environments, preserving operational integrity.
Furthermore, the pressure limitations are addressed effectively with rotary peristaltic pumps. While they do not typically achieve high-pressure outputs, their performance is adequate for many chemical processing applications. They provide consistent flow rates needed for reactions, separations, or other processing activities. Additionally, their inherent design allows for a clear pathway for fluid movement, minimizing risks of blockages and enhancing the overall efficiency of the chemical operation.
Advantages of Rotary Peristaltic Pumps
Rotary peristaltic pumps offer a range of advantages that make them particularly valuable in various industries. Understanding these benefits is crucial for professionals who are selecting fluid transfer solutions. The main advantages include non-contaminating operation, self-priming capabilities, and ease of maintenance. These elements play a significant role in ensuring efficient and safe fluid handling without compromising the quality of the substances involved.
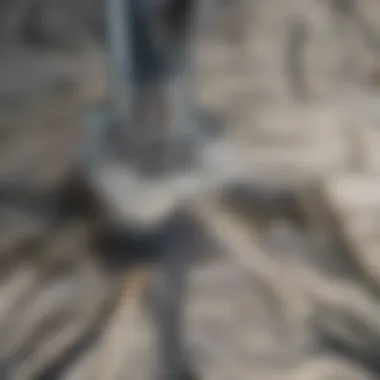
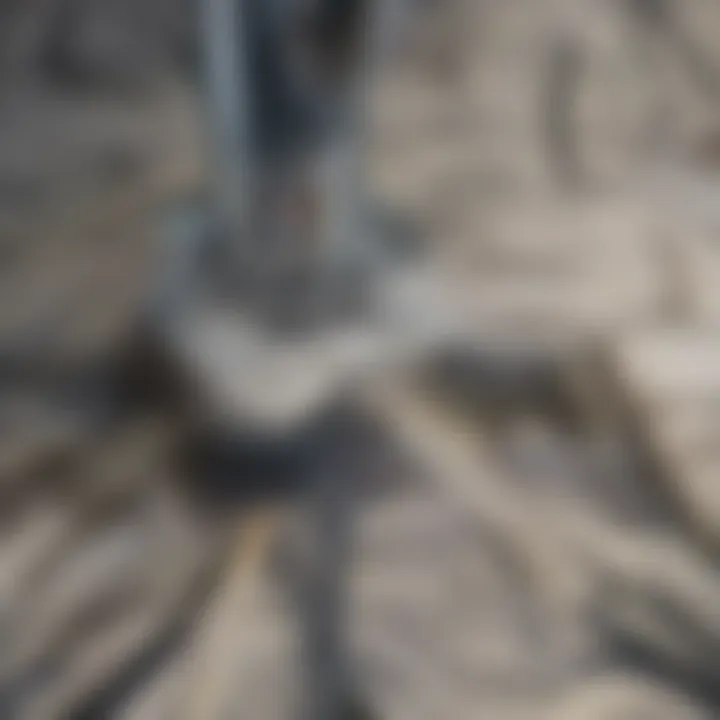
Non-Contaminating Operation
One of the standout features of rotary peristaltic pumps is their non-contaminating operation. This characteristic arises from the design of the pump itself, which isolates the fluid from the mechanical components. The fluid only comes into contact with the internal tubing or hose, leaving the pump mechanisms clean and free from contamination. This is essential in industries such as pharmaceuticals and food processing, where even minor contamination can lead to serious consequences.
The use of high-quality materials for the tubing further enhances this aspect. Materials like silicone and various thermoplastics are commonly used, as they are resistant to many chemicals and can be easily sterilized. This helps in maintaining the purity of the transferred fluids, which is vital for regulatory compliance and product safety.
Self-Priming Capabilities
Another advantage is the self-priming capability of rotary peristaltic pumps. This feature allows the pump to draw fluid into its system without requiring additional interventions. The design utilizes the peristaltic mechanism, whereby the rollers compress the tubing and create a vacuum, pulling the liquid into the pump. This results in efficient fluid transfer, especially in scenarios where fluid levels may fluctuate or when the source is lower than the pump.
Self-priming is particularly beneficial in maintaining operational efficiency. It eliminates the need for manual priming, reducing downtime and labor costs. This is especially important in continuous processes where downtime can lead to significant productivity losses.
Ease of Maintenance
Maintenance is a crucial consideration for any equipment, and rotary peristaltic pumps excel in this area as well. Their straightforward design means fewer components are involved, which simplifies maintenance tasks. The primary maintenance requirement is the periodic replacement of the tubing, which is generally a quick and uncomplicated process. Moreover, since the tubing can be replaced without the need to disassemble the entire pump unit, operators can carry out maintenance efficiently, minimizing operational disruption.
Regular checks and replacements extend the lifespan of the pump and maintain its performance. Routine maintenance practices include inspecting for wear and tear, ensuring proper alignment, and checking the torque on any fittings. Such diligence contributes to the overall reliability of the system.
"The advantages of rotary peristaltic pumps are critical in modern applications where reliability, safety, and efficiency cannot be compromised."
In summary, the advantages of rotary peristaltic pumps are significant. Non-contaminating operation ensures the integrity of the fluid being transferred. Self-priming capabilities enhance operational efficiency by reducing the need for manual intervention. Finally, the ease of maintenance allows for consistent performance and reliability. These factors make rotary peristaltic pumps a preferred choice in various industrial applications.
Limitations of Rotary Peristaltic Pumps
Understanding the limitations of rotary peristaltic pumps is crucial for selecting the right pump for specific applications. While these pumps offer various advantages, recognizing their drawbacks helps professionals make informed decisions. This section dives into the flow rate constraints and pressure limitations typical for rotary peristaltic pumps, which are key factors to consider when evaluating their overall efficiency and suitability for particular tasks.
Flow Rate Constraints
Rotary peristaltic pumps rely on the compression and release of flexible tubing to move fluids. This mechanism imposes inherent flow rate constraints. Generally, the flow rate is influenced by several parameters, including pump design, motor speed, tubing diameter, and fluid viscosity.
The typical flow rates for rotary peristaltic pumps can vary widely, but they often do not reach the high flow output achieved by centrifugal pumps. This limitation can impact their effectiveness in applications requiring rapid fluid transfer or large volumes. Moreover, pumping highly viscous fluids can further decrease flow rates, causing operational issues in industries like chemical processing and food production.
To sum up, when choosing a rotary peristaltic pump, it is important to match the pump’s flow rate capabilities with the demands of the application. A careful assessment of the desired flow rate can prevent inefficiencies and ensure optimal performance.
Pressure Limitations
Pressure limitations in rotary peristaltic pumps arise from their unique operational design. These pumps generally handle lower pressure scenarios effectively, but they lack the capability to manage high-pressure fluid transfer. The maximum pressure rating is usually dictated by the materials used in the tubing and the pump construction.
Operating rotary peristaltic pumps beyond their designed pressure can lead to tube rupture or pump failure. It is not uncommon for these pumps to function at pressures below 100 psi, especially when dealing with sensitive fluids that require gentle handling, such as biological samples or shear-sensitive materials used in pharmaceuticals.
One way to address pressure limitations is through proper pump selection based on individual application requirements. It is recommended to consider both system pressure and the characteristics of the fluid being pumped. Choosing a pump with suitable pressure ratings ensures reliable operation while extending the lifespan of the equipment.
"Evaluating the flow rate and pressure limitations of rotary peristaltic pumps is key for achieving reliable performance in diverse applications."
Selection Criteria for Rotary Peristaltic Pumps
When selecting a rotary peristaltic pump, it's crucial to consider various factors that affect its performance and suitability for specific applications. Understanding these selection criteria is essential for ensuring optimal operation and efficiency. The criteria help in assessing not only the pump’s functionality but also the long-term reliability and operational costs.
Key elements include:
- Nature of the fluid to be pumped
- Required flow rate and pressure
- System compatibility and integration
- Maintenance requirements and ease of service
- Material compatibility and hygiene standards
These considerations play a significant role in determining not just the efficiency of the pump but also its operational sustainability.
Fluid Characteristics
The fluid characteristics are foundational to how well a rotary peristaltic pump will function. The nature of the liquid, such as its viscosity, density, and chemical composition, directly influences the pump's performance. For instance, highly viscous fluids require a pump that can handle thicker substances without compromising flow rates.
Other aspects to evaluate include:
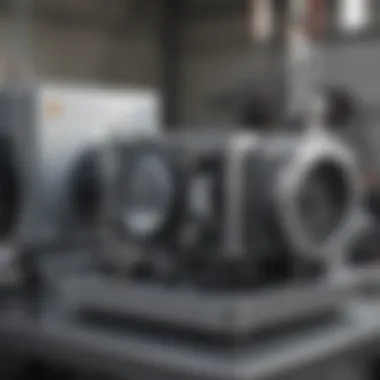
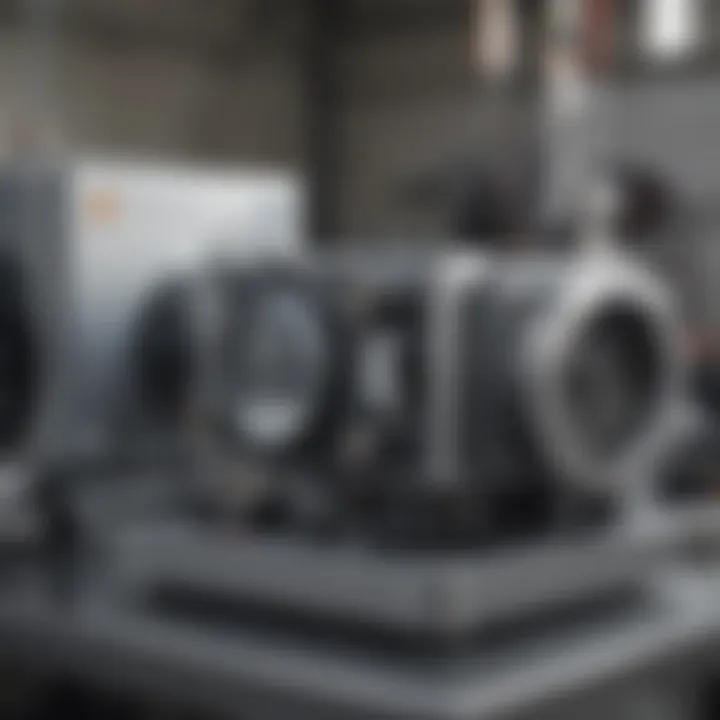
- Corrosiveness: If the fluid contains harsh chemicals, the pump materials must be resistant to corrosion. Selecting appropriate materials like silicone or thermoplastic elastomers reduces wear and extends the pump's lifespan.
- Solid Content: The presence of particles can impact the flow and may lead to blockage or wear. It's important to choose pumps designed for fluids with solid inclusions, ensuring filters or strainers are used when necessary.
In sum, evaluating fluid characteristics informs the selection of the appropriate rotary peristaltic pump, enhancing productivity and reducing maintenance needs.
Application Requirements
Application requirements involve understanding the specific conditions and settings where the pump will operate. This includes the desired flow rate, pressure levels, and how the pump integrates with existing systems. Each application can have unique demands, requiring careful assessment to ensure pump suitability.
Consider the following:
- Flow Rate and Speed: Determine the necessary flow rate for the application. Rotary peristaltic pumps are generally well-suited for varying flow requirements. Choosing a pump compatible with changes in speed and flow maintains efficiency in dynamic environments.
- Pressure Range: Evaluate the pressure requirements for the application. Different pumps have varying pressure limits and selecting a model that aligns with the intended application can prevent potential failures.
- Environment: Consider environmental factors such as temperature and humidity. These can significantly impact pump performance and longevity, necessitating pumps designed for specific environmental conditions.
Maintenance and Troubleshooting
Maintaining rotary peristaltic pumps is crucial for their optimal performance and longevity. Regular maintenance ensures that these pumps operate efficiently, reduce downtime, and ultimately lower operational costs. In this section, we will explore the best maintenance practices and address common issues that may arise, along with appropriate solutions.
Regular Maintenance Practices
Regular maintenance is essential to prevent malfunctions and ensure the reliability of rotary peristaltic pumps. Here are key maintenance practices:
- Inspection of Hoses: Hoses are critical components of peristaltic pumps. Inspect them regularly for wear and tear. Look for cracks, cuts, or any signs of degradation. Replacing damaged hoses can prevent leaks.
- Check Pump Alignment: Ensure that the pump and motor are properly aligned. Misalignment can lead to increased wear or damage to the pump's internal components.
- Lubrication: If the pump has any moving parts that require lubrication, check and apply lubrication as required. This helps to minimize friction and prolong the life of the components.
- Monitoring Performance: Keep an eye on the pump’s flow rates and pressure levels. Any significant deviation from the expected performance can indicate an underlying issue.
- Cleaning: Regularly clean pump areas to prevent buildup of contaminants and other materials. Use appropriate cleaning agents to ensure that internal components are not damaged.
Regular maintenance can save significant costs in repairs and downtime. Investing time in preventative measures enhances pump performance and durability.
Common Issues and Solutions
Despite regular maintenance, issues may still arise with rotary peristaltic pumps. Understanding these problems can help in quick identification and resolution. Here are some common issues along with their solutions:
- Flow Rate Dropping: If the flow rate decreases unexpectedly, check for blockages in the hoses or piping. Clearing any obstructions should restore normal flow.
- Increased Noise: Excessive noise can indicate that the pump is operating under stress. Check for misalignment or worn bearings as these can be adjusted or replaced.
- Leaks: If leaks are detected around the hose connections, ensure that the hoses are properly secured. Replace any damaged hoses and retighten connections.
- Overheating: Overheating can result from several factors, such as overworking the pump beyond its rated capacity. Evaluate the operating conditions and consider if a different pump with a higher capacity is needed.
Future Developments in Rotary Peristaltic Pump Technology
The field of rotary peristaltic pumps is evolving rapidly. These advancements are essential not just for improving performance but also for addressing specific industry challenges. By focusing on innovations and technological integration, the future of rotary peristaltic pumps promises enhanced operability and effectiveness in various applications.
Innovations in Pump Design
Recent innovations in pump design focus on increasing the efficiency and durability of rotary peristaltic pumps. Manufacturers are investigating new materials to extend the lifespan of tubing, which is crucial in maintaining the integrity of the pumped fluids. For instance, the use of enhanced elastomers that withstand corrosive chemicals is gaining traction. This leads to better resilience and lower maintenance costs.
Additionally, modular designs are becoming more popular. Such designs allow for easier assembly and disassembly, facilitating repairs and upgrades. Customers benefit from reduced downtime, which translates into operational continuity. Furthermore, novel technologies such as 3D printing are introduced in the design phase. This method allows for complex geometries that optimize flow characteristics, boosting overall efficiency.
Integration with Smart Technologies
The integration of smart technologies into rotary peristaltic pumps represents a significant trend shaping the future. Internet of Things (IoT) applications enable remote monitoring and control of pump operations. This development provides users with real-time data on performance metrics, such as flow rate and wear on components.
Smart sensors can alert users about potential issues before they escalate into costly failures. For example, predictive maintenance powered by AI algorithms can analyze data trends to anticipate when a pump needs servicing. This proactive approach ensures that pumps function optimally and reduces the risk of unexpected breakdowns. Moreover, automation features allow for seamless adjustments based on real-time conditions, enhancing the overall efficiency of the fluid transfer process.
The combination of innovative designs and smart technology not only simplifies operations but also paves the way for more sustainable practices in industries reliant on fluid handling. Embracing these advancements is not just beneficial, it is essential for keeping pace with the demands of modern applications.
Finale
The conclusion serves as a critical element of this article, encapsulating the essence of rotary peristaltic pumps. It synthesizes the information presented throughout the sections, highlighting key takeaways that resonate with the professional and academic audience. Understanding this technology is essential for students, researchers, educators, and industry professionals alike. The ability to analyze the advantages, limitations, and applications contextualizes the operational principles of these pumps.
In summarizing the components and their functionalities, we reinforce the significance of rotary peristaltic pumps in contemporary fluid transfer systems. Recognizing their role helps industries make informed decisions regarding pump selection and application considerations.
Furthermore, as the demand for efficient, reliable fluid mechanics increases, the awareness fostered by this conclusion empowers informed practices within various fields. Efficient design and application are paramount, and highlighting these factors through the lens of applications can significantly impact industry standards and practices.
Summary of Key Points
- Definition and Functionality: rotary peristaltic pumps operate on the mechanism of fluid transfer through variable compression.
- Applications Across Sectors: versatile use in pharmaceuticals, food and beverage, and chemical sectors.
- Advantages: offers benefits like non-contaminating operation and self-priming capabilities.
- Limitations: awareness about flow rate and pressure constraints is necessary for effective use.
- Future Innovations: integration with smart technologies is crucial for future developments.
Implications for Industry Practices
The implications of rotary peristaltic pumps extend deeply into industry practices. By applying the knowledge gained in this article, engineers and designers can enhance operational efficiency.
- Streamlined Processes: awareness of operational principles allows for better design that encourages efficiency.
- Regulatory Compliance: understanding the non-contaminating nature meets regulations in sensitive industries.
- Cost-Effectiveness: informed selection improves maintenance strategies and reduces long-term costs.
- Innovation Utilization: leveraging smart technologies can foster advancements, increasing productivity and reliability in fluid handling processes.