A Deep Dive into Semiconductor Manufacturing
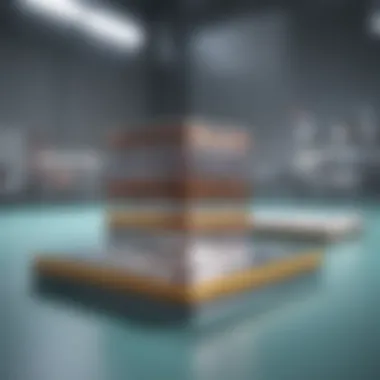
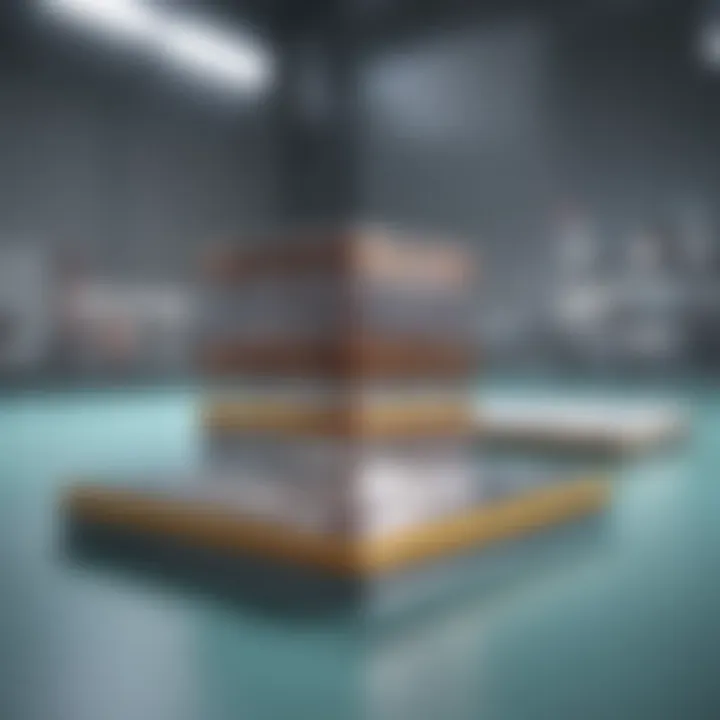
Intro
The semiconductor manufacturing process stands as a hallmark of modern technology, reflecting the interplay of science, engineering, and innovation. The world around us thrives on electronic devices, from smartphones to computers, necessitating high-performance semiconductor components. Understanding this intricate process is crucial for students, researchers, educators, and professionals who seek insight into this foundational industry.
At its core, the semiconductor fabrication process involves several carefully orchestrated stages designed to convert raw materials into sophisticated microchips. These stages are not just a sequence of steps but a dance of precision and technological prowess. Whether you’re contemplating a career in semiconductor engineering or just looking to boost your technical knowledge, grasping the essentials of this process will provide a solid foundation.
> "An understanding of semiconductor manufacturing reveals not only the complexity of the devices we rely on but also the innovation driving the industry forward."
Regulating the quality and performance of these semiconductors is indispensable. The topic offers a myriad of fascinating aspects worth dissecting, including material selection, lithography, etching, and doping, each crucial to the final product's performance. As electronic demands continue to escalate in this information age, comprehending these elements becomes paramount. Each component of this manufacturing maze contributes to overall functionality, reliability, and efficiency, ensuring that our devices operate seamlessly.
As we delve into the nitty-gritty of the semiconductor manufacturing process, it's essential to recognize the various challenges and advancements that characterize this ever-evolving field.
In the following sections, we shall explore these intricate stages of semiconductor manufacturing, shedding light on the intricate technologies used and the significance behind each process.
Prelude to Semiconductor Manufacturing
In today's fast-paced world, the semiconductor manufacturing process stands as a cornerstone of technological advancement. It involves a myriad of complex processes that transform raw materials into highly sophisticated electronic components. The significance of understanding this manufacturing process cannot be understated given that semiconductors serve as the brain behind countless devices we interact with daily.
The journey from raw silicon to a functional chip takes meticulous effort, blending science and engineering in a dance of precision. Each turn in the process contributes to determining the performance, reliability, and overall efficacy of electronic devices—from smartphones to supercomputers.
Overview of Semiconductors
Semiconductors are materials that are not quite conductors or insulators. They sit in a grey area, exhibiting unique properties based on their temperature or impurities added to them. A classic example is silicon, which conducts electricity under certain conditions while blocking it under others, making it ideal for various applications in electronics.
In semiconductor manufacturing, these materials undergo several intricate procedures that refine their properties to create functioning electronic components. The fundamental nature of semiconductors allows them to form the basis of transistors, diodes, and integrated circuits, which are essential for modern electronic functionality.
"The beauty of modern electronics is in its ability to take simple elements and turn them into complex functionalities."
Importance in Modern Electronics
The role of semiconductors in modern electronics can’t be overstated. They are fundamentally linked to the operational capabilities of countless devices. To grasp their importance, consider these key factors:
- Power Efficiency: Semiconductors manage the flow of electricity and energy, making devices more efficient. This energy management leads to longer battery life in portable devices.
- Miniaturization: Advances in semiconductor manufacturing allow for the miniaturization of electronic components—leading not just to smaller but also to faster devices. Think of how your smartphone, once the size of a brick, now fits snugly in your pocket.
- Innovation: Ongoing research into semiconductors drives innovation across industries. From automotive advancements like self-driving cars to breakthroughs in artificial intelligence, semiconductors help pave the way for future technologies.
- Economic Impact: The semiconductor industry is a massive economic force. It fuels job creation, research, and development, signifying its vital role in global markets.
Raw Materials in Semiconductor Production
When we talk about semiconductor manufacturing, the behind-the-scenes actualities are simply fascinating. One cannot overlook the key role played by raw materials. These materials serve as the fundamental building blocks for fabricating a range of electronic components, from everyday gadgets to advanced computing systems. Without high-quality raw materials, the entire production process could fall flat, leaving manufacturers struggling with unreliable or inferior products.
Silicon and Its Properties
Silicon, often dubbed the backbone of the semiconductor industry, has unique properties that make it an ideal choice for the production of electronic devices. On a physical level, silicon is a hard and brittle crystalline solid with a metallic luster. But it is its semiconducting properties that truly shine. Silicon behaves as an insulator at low temperatures but can conduct electricity when exposed to certain conditions, making it a perfect candidate for transistors and diodes. The ability to manipulate its conductive properties through processes such as doping is why silicon is central in the world of electronics.
What’s more, silicon is abundant and relatively inexpensive, which has solidified its status as the go-to material in semiconductor fabrication. The process of extracting silicon from sand, one of its most common sources, adds to its appeal. Silicon’s stability and availability allows for scalability in production, providing an economical path for manufacturers aiming to meet high demand.
Other Semiconductor Materials
While silicon leads the pack, it's worth noting that several other materials play significant roles in semiconductor manufacturing. Two notable examples are Gallium Arsenide and Silicon Carbide, each with its own unique properties and applications.
Gallium Arsenide
Gallium Arsenide (GaAs) is another formidable candidate in the semiconductor space. It’s known for its high electron mobility and direct bandgap, which means it can emit light efficiently, making it relevant in optoelectronic applications such as LEDs and laser diodes. One of the major key characteristics of GaAs is its superior efficiency compared to silicon in high-frequency and high-temperature applications. This often results in faster and more reliable performance in communication devices—including mobile phones and satellite systems.
However, GaAs comes with its own set of challenges. The production process is more complex and costly than that of silicon, limiting its use mainly to specialized applications. Nonetheless, its unique features make it a popular choice in areas where performance is paramount, despite the higher price tag.
Silicon Carbide
Silicon Carbide (SiC) is yet another material worth examining. SiC is renowned for its ability to withstand high voltages and temperatures, making it indispensable in power electronics. The key characteristic of Silicon Carbide is its high thermal conductivity and thermal stability, which helps maintain performance in extreme conditions.
In recent years, SiC has gained traction in sectors such as electric vehicles and renewable energy systems, where efficiency is crucial. Its ability to operate at higher efficiencies and temperatures leads to smaller, lighter devices—a compelling reason for its increasing adoption in the industry. However, its production is historically less mature than silicon, which results in higher costs and complexities in manufacturing.
In summary, while silicon dominates the field, materials like Gallium Arsenide and Silicon Carbide provide unique advantages that drive innovation in semiconductor technology. Understanding these materials is critical for those looking to grasp the nuances of semiconductor manufacturing and the continuous advancements that follow.
Step-by-Step Process of Semiconductor Fabrication
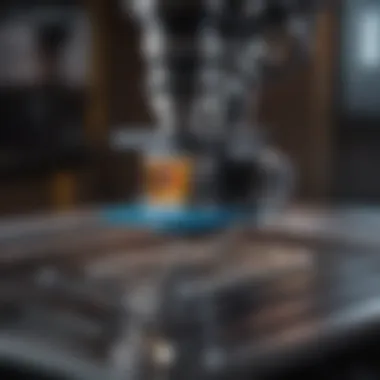
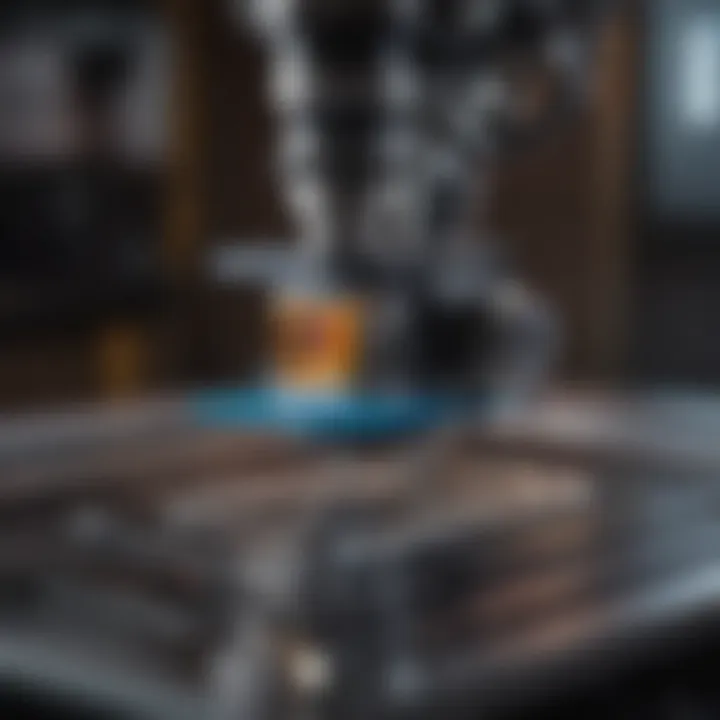
Understanding the semiconductor fabrication process is like peeking behind the curtain of modern technology. It's a complex web of steps that transform raw materials into the engines of our digital age. Each phase is not just a cog in a machine; it’s a fundamental process that affects everything, from performance to reliability.
Wafer Fabrication
Crystal Growth Techniques
When it comes to crystal growth techniques, we are talking about the foundation of semiconductor manufacturing. The most prevalent method, the Czochralski process, allows for the creation of monocrystalline silicon. This purity is critical, as the fewer the imperfections in the crystal lattice, the better the electronic properties of the semiconductor devices.
What makes this process particularly beneficial is its ability to yield large-diameter wafers, which can drastically reduce production costs over time. However, one must consider that this growth process can be time-consuming and requires precise temperature control. If you heat it too high or too low, it’s like trying to get a cake just right — too much heat, and you've got a disaster.
Wafers Cutting and Polishing
Once the wafers are formed, the next significant step is cutting and polishing. This isn't just about taking a saw to a slab of silicon. Precision is of the essence here; wafers must be sliced into thin disks with a thickness typically between 525 microns and 775 microns. A unique characteristic of this process is its reliance on diamond blades, which yield smoother surfaces and higher yield rates of usable wafers.
However, the polishing stage is what really brings it home. It eliminates any irregularities in surface flatness and roughness. Think of it as buffing a car to a showroom shine. The downside? The process can generate a fair bit of waste, particularly during the initial cutting phase.
Photolithography
Mask Design
The mask design phase is like preparing a canvas before an artist starts painting. A mask is a patterned piece that determines where on the wafer material will remain after exposure. This choice is crucial because it dictates the layout of circuits on each wafer. A well-designed mask can make production more efficient, reducing manufacturing times and costs significantly.
However, intricate designs can make the production of these masks quite challenging. If there are flaws in the mask, it can lead to defective chips. So, one must tread lightly, ensuring each design step is meticulously reviewed before moving forward.
Exposure Techniques
Once the mask is ready, exposure techniques come into play. This step uses either ultraviolet light or electron beams to create intricate patterns on the wafer surface. Their effectiveness contributes greatly to the overall design's fidelity. The main allure of these techniques lies in their resolution capabilities; they can print patterns a few nanometers across!
While these advantages are significant, they come at a price. The equipment required for high-resolution exposure can be incredibly expensive and requires constant maintenance to ensure optimal performance.
Etching Processes
Wet Etching
The following step is wet etching, a crucial process that removes the undesirable parts of the material. This technique utilizes liquid chemicals to dissolve specific areas of the wafer. One key characteristic of wet etching is its ability to achieve isotropic etching, which means it removes material uniformly from all sides.
This isotropy benefits certain designs but can also be a drawback. Since it etches in all directions, it may not create the sharp angles or precise features required for advanced circuits.
Dry Etching
On the other hand, dry etching offers a more controlled approach. Using gases, this method can achieve anisotropic etching, which allows for the creation of fine, well-defined patterns. Dry etching stands out because it can maintain the integrity of the substrate better, which is essential for features that require high aspect ratios.
However, the machinery necessary for dry etching tends to be costlier and more complex than its wet counterpart. It's a fine balancing act between precision and expense.
Doping Techniques
Ion Implantation
Ion implantation is a pivotal part of doping techniques that introduce impurities into silicon wafers to modify their electrical properties. By bombarding the substrate with ions at high speeds, it creates regions of n-type and p-type materials. The primary advantage here is the ability to precisely control the depth and concentration of dopants, enabling custom electronic properties for various applications.
Still, it comes with challenges like potential damage to the wafer’s crystal lattice, which requires further annealing to repair. It’s like adding seeds to a garden—they need care to flourish.
Differential Doping Methods
On a different note, differential doping methods involve applying varying levels of dopants across different regions of the wafer. This can lead to voltage variations in specific areas which are relevant for complex circuit functions. This technique is appreciated for its flexibility in tailoring electrical characteristics of devices across the wafer, offering a dynamic capability akin to seasoning a dish—adjusting for flavor based on needs.
However, the intricacies involved can complicate the manufacturing process, requiring a higher level of precision and care in execution.
Deposition Methods
Chemical Vapor Deposition
In terms of Chemical Vapor Deposition (CVD), this method is widely used for creating thin films on the wafers. It’s particularly famous for producing silicon dioxide or silicon nitride layers, adding essential electrical insulating properties. CVD has become a mainstay due to its uniform coverage and ability to coat complex geometries.
The downside includes the toxic byproducts generated during the process, which necessitate stringent safety protocols. It's a double-edged sword that provides powerful materials while requiring careful handling.
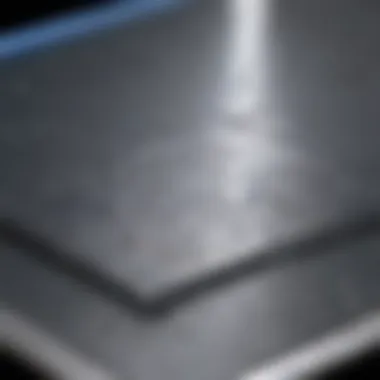
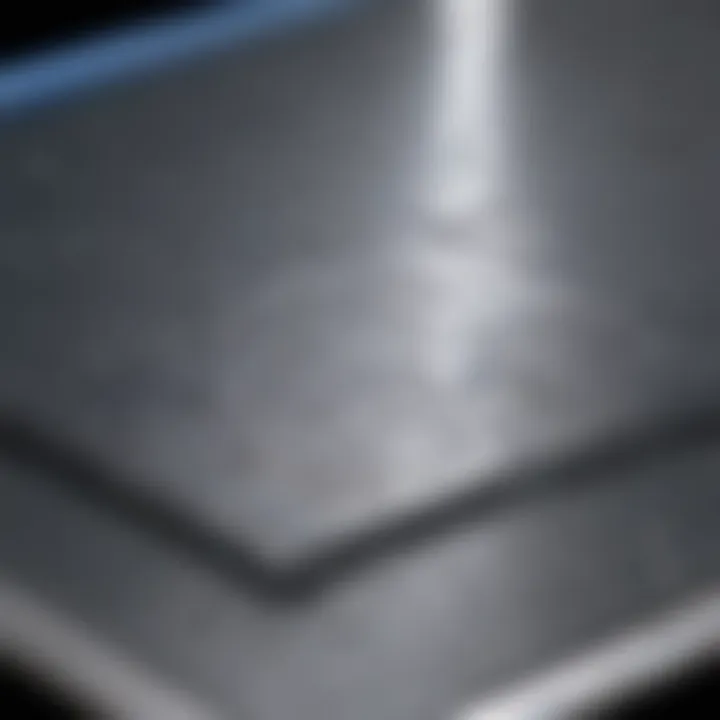
Physical Vapor Deposition
Conversely, Physical Vapor Deposition (PVD) is a process where material transitions from the solid phase to the vapor phase and back to solid, directly depositing onto the wafer. It has gained popularity due to its ability to produce high-purity films with excellent adhesion properties. It's a reliable choice for applications requiring exacting specifications in metallization.
Nevertheless, the PVD method can be slower compared to CVD, making it less suitable for large-scale production where time is of the essence.
Each step in the semiconductor fabrication process holds its own merits and challenges. Understanding these processes not only illuminates the sophisticated operations behind semiconductor manufacturing but also highlights the intricate ballet of technology that powers devices we depend on every day.
Assembly and Packaging of Semiconductors
In the semiconductor manufacturing process, the assembly and packaging of chips perform an essential role. While the earlier stages focus on fabricating the silicon wafers, this section shifts attention to ensuring that these tiny devices are ready for real-world application. It’s like putting the cherry on top of a well-baked cake; without it, the dessert just wouldn’t have the same appeal or utility. Proper assembly and packaging not only protect the semiconductor but also enhance its performance.
Die Attach Techniques
Die attach refers to the method of adhering the semiconductor die to the package substrate. This connection is the bridge between the fragile silicon chip and its encompassing package, which offers structural support and electrical connections. There are various techniques used in die attach, including:
- Adhesive Bonding: This method utilizes a special adhesive material to bond the die to the substrate. It can offer flexibility in terms of thermal expansion and ensure reliable performance.
- Soldering: Here, a solder material is melted and used to attach the die. This is commonly deemed effective for high-temperature applications due to its robust mechanical bonding.
- Epoxy: This is another popular choice. Epoxy resins provide a high level of adhesion as well as insulation, protecting the delicate semiconductor from external elements.
Using the right die attach technique is critical. The choice impacts thermal management and, ultimately, the performance of the semiconductor in single or multi-chip applications. As a modern trend, many companies are investigating thermally conductive die attach materials to improve heat dissipation.
Wire Bonding and Flip Chip
Once the die is attached, the next step often involves wire bonding and flip chip methods. These processes establish the electrical connections required for the semiconductor to function effectively.
Wire Bonding is a traditional technique that uses fine wires, typically gold or aluminum, to connect the die pads to the leads of the package. This method can be likened to weaving threads in fabric, ensuring a secure, reliable link. Benefits of wire bonding include:
- Low cost, making it a popular choice among manufacturers
- The ability to achieve high density in chip design
- Flexibility in design, allowing for various package types
However, it comes with its own set of limitations like a potentially larger footprint and reduced ability for thermal efficiencies compared to more modern methods.
On the other hand, Flip Chip technology flips the semiconductor die upside down. Electrical connections are made directly to the substrate. This technology has some advantages:
- Compact design leading to a smaller package size
- Improved thermal management and performance due to direct connection
- Better alignment and less risk of defects in manufacturing
"In semiconductor packaging, evolution is key, and keeping an eye on emerging methods remains crucial in the race towards efficiency and performance."
Both wire bonding and flip chip methods have their unique benefits and challenges. The decision to utilize one over the other often hinges on specific application needs, performance requirements, and cost considerations. With the rapid evolution of semiconductor technology, understanding these assembly techniques is paramount for those in the industry.
Testing and Quality Control in Semiconductor Manufacturing
In semiconductor manufacturing, the stakes are high. Every tiny imperfection can lead to catastrophic failure of electronic devices, making testing and quality control essential components of the production process. This segment not only ensures that each product meets rigorously defined standards, but it also enhances reliability and performance for end users. Ranging from electrical characteristics to physical integrity, a strategic quality control plan can significantly mitigate risks associated with mass production.
The importance of rigorous and consistent testing cannot be overstated; it underpins the integrity of the entire semiconductor industry. The global demand for high-performing devices, like smartphones and data servers, means that manufacturers have to adhere to strict quality norms, ensuring that each semiconductor chip operates at peak efficiency.
Electrical Testing
Electrical testing serves as the backbone of quality assurance in semiconductor manufacturing. Once the chips are fabricated, it is imperative to check their electrical properties such as voltage, current flow, and resistance. These parameters are crucial for verifying that the chips function according to their design specifications.
Some key aspects of electrical testing include:
- Functional Testing: This checks if the semiconductor performs its intended task under real-world conditions.
- Parametric Testing: Focuses on measuring specific electrical parameters like threshold voltage and leakage current, which are critical for performance.
- Spot-Checking: Although not exhaustive, it allows for quick assessments of random samples to monitor overall production quality.
By identifying defective chips early, manufacturers avoid costly mistakes down the line. Moreover, effective electrical testing reduces the risk of field failures that can tarnish a company's reputation.
Reliability Assessment Methods
Reliability assessment is aimed at predicting how well a semiconductor will perform over time and under various conditions. Here, it's not just about instant performance; it's about ensuring long-lasting functionality in the face of everyday usage and environmental stresses.
Common methods employed in reliability testing include:
- Accelerated Life Testing (ALT): This technique simulates aging and stress via increased temperature, humidity, or voltage to predict a semiconductor's life span.
- Temperature Cycling: Chips undergo rapid temperature changes to test how well they can handle thermal expansions and contractions, mimicking real operational environments.
- Burn-In Testing: Semiconductors are subjected to prolonged electrical stress at high temperatures, identifying early failures before the product reaches consumers.
"The key to longevity in semiconductor devices lies in rigorous testing and unwavering quality standards."
Through these techniques, manufacturers can identify weak points in their products, ensuring that only the most reliable chips are sent out into the market. Ultimately, comprehensive electrical testing combined with robust reliability assessment forms a protective barrier against market failures and enhances customer satisfaction.
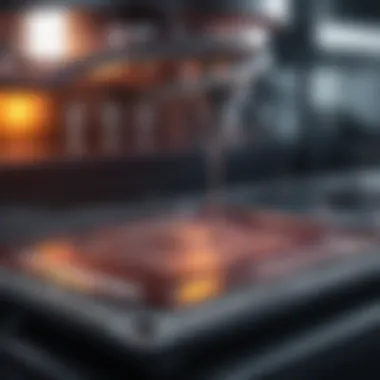
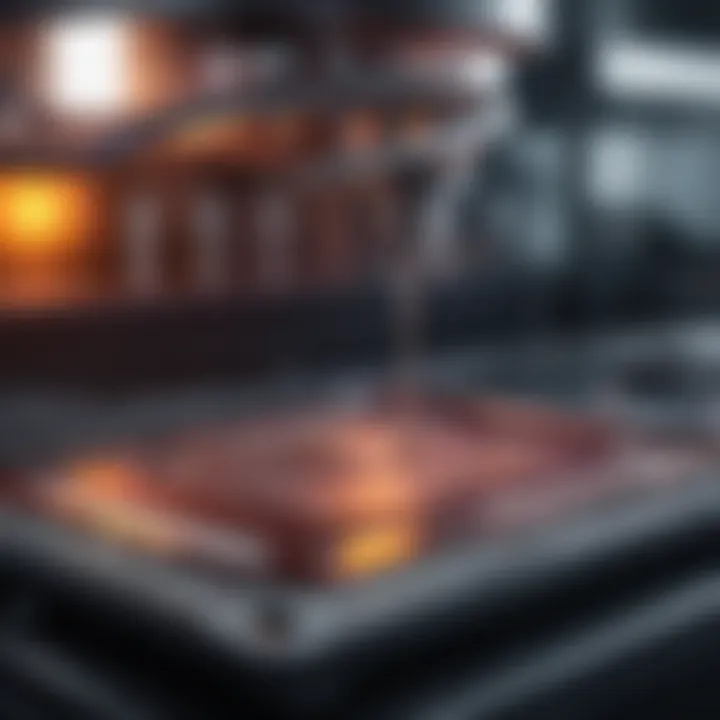
Challenges in Semiconductor Manufacturing
The semiconductor manufacturing landscape is riddled with challenges that can significantly impact production efficiency and product quality. Understanding these challenges is vital for stakeholders in the industry, including engineers, manufacturers, and researchers. These challenges span from environmental regulations to the continuous evolution of technology. In this section, we will delve deeper into two main challenges: environmental and economic factors and the necessity for technological advancements and innovation.
Environmental and Economic Factors
In today’s world, the semiconductor industry faces mounting pressure to align with environmental sustainability goals and economic realities. Production processes can lead to significant waste and emissions that impact our planet. In particular, the chemicals involved in semiconductor fabrication raise alarms regarding their effects on health and nature. For instance, materials like hydrofluoric acid, used during wafer cleaning, can be hazardous, pushing companies to adopt stricter safety protocols as well as waste management practices.
Additionally, the production facilities require large amounts of energy and water, which are critical elements that can drive costs higher. The regulator's hoops companies face to meet environmental standards can lead to delays and increased operational expenses. Therefore, optimizing energy consumption and water usage is not simply a good practice but also a necessity for maintaining competitive advantage. Companies like Intel and TSMC have begun pioneering in energy-efficient technologies, focusing on greener production methods, solidifying an industry standard for sustainable practices.
Not to forget, the global semiconductor market operates within a volatile economic environment shaped by trade policies, tariffs, and geopolitical tensions. Fluctuating prices for raw materials can squeeze margins and compel manufacturers to stay nimble regarding their supply chains. Companies' effectiveness in navigating these complexities can be a differentiator, allowing them to thrive despite economic headwinds.
Technological Advancements and Innovation
The drive for innovation and technological advancement in semiconductor manufacturing is relentless. As consumer demand escalates for faster, smaller, and more efficient electronic devices, manufacturers are continually pushed to refine their processes and technologies. This pressure to innovate brings about a plethora of challenges, not the least of which includes the need for significant investment in research and development.
Consider the evolution from traditional 3D semiconductor structures to 3D NAND memory technologies. This shift requires not only novel materials but also advanced techniques like extreme ultraviolet lithography (EUV). The upfront costs associated with adopting such technologies can be daunting. Businesses must weigh the risks and benefits carefully, deciding wisely where and when to invest.
Additionally, the speed of technological change means that manufacturers need to remain agile. Legacy processes that once dominated the scene may quickly become obsolete with newer innovations. Failure to keep up can lead to a loss of competitive advantage. Thus, ongoing education and training for workers become imperative, ensuring that they possess the necessary skills to handle cutting-edge equipment and methodologies.
"The semiconductor industry is like a high-stakes race, where innovation is the fuel, and agility can make or break success."
As we navigate through these complex challenges, it's clear that the path forward requires not only robust solutions but also a willingness to embrace change. In doing so, companies stand a better chance of succeeding in the fast-paced world of semiconductor manufacturing.
Future Trends in Semiconductor Manufacturing
The semiconductor industry is at a pivotal juncture, with rapid advancements reshaping the landscape in which it operates. As technology continues to advance at lightning speed, understanding the future trends in semiconductor manufacturing becomes crucial. These trends not only define the course of the industry but also have significant implications for various sectors, such as consumer electronics, automotive, and artificial intelligence. Embracing emerging technologies and adapting to global dynamics are essential for stakeholders aiming to maintain a competitive edge.
Emerging Technologies
Quantum Computing
Quantum computing stands out in the realm of emerging technologies, presenting both an exciting and challenging prospect for semiconductor manufacturing. This next-generation computing paradigm harnesses the peculiarities of quantum mechanics, enabling calculations that classical computers can hardly manage. For instance, processing speed and accuracy reach unparalleled heights, making quantum computing a game-changer for complex problem-solving in financial modeling, drug discovery, and cryptography.
A notable characteristic of quantum computing is its ability to perform multiple calculations simultaneously through superposition. This could significantly enhance data processing capabilities, thereby tackling previously insurmountable challenges in various fields. However, quantum computing also brings unique hurdles, such as the need for extreme cooling conditions and sophisticated error correction methods. These factors could complicate the path of integration within current semiconductor manufacturing processes and necessitate tailored solutions to optimize production.
2D Materials
2D materials, like graphene and transition metal dichalcogenides, are our next hot topic. These materials, consisting of a single or few atomic layers, have sparked immense interest due to their unique electronic and mechanical properties. Notably, they boast excellent conductivity and flexibility, which can pave the way for novel applications, including faster chips, flexible electronics, and advanced sensors.
A defining feature of 2D materials is their high surface area to volume ratio, which translates into improved reactivity and performance in electronic devices. Integrating 2D materials into semiconductor devices offers the potential to create smaller, more efficient components that meet the growing demand for miniaturization in tech gadgets. On the downside, the challenges associated with their widespread adoption include synthesis scalability and integration with traditional semiconductor processes, which could slow down the pace at which these materials become mainstream.
Global Market Dynamics
As we gaze into the crystal ball of semiconductor manufacturing, one cannot overlook the importance of global market dynamics. The interplay of supply chains, trade policies, and economic trends significantly impact how the semiconductor ecosystem evolves. For instance, the current emphasis on regional supply chain resilience—prompted by disruptions due to geopolitical tensions and pandemics—encourages a shift toward local sourcing and manufacturing capabilities.
Moreover, the demand for semiconductors is surging across multiple sectors. The proliferation of Internet of Things devices, AI applications, and electric vehicles underscores the need for innovative and high-quality semiconductor solutions.
"Understanding these trends helps predict the industry's future trajectory and shapes strategic planning for businesses within and outside the semiconductor landscape."
The next wave of innovations hinges on the capability to master emerging technologies like quantum computing and 2D materials while navigating complex global market dynamics. This proactive approach will determine the path towards a robust and resilient semiconductor industry.
Epilogue
In concluding this exploration of semiconductor manufacturing, it is crucial to reflect on the multitude of factors contributing to the ever-evolving landscape of this industry. The semiconductor sector is a backbone of modern electronics, feeding into nearly every device we use daily, from smartphones to supercomputers. By comprehensively examining the processes of fabrication, assembly, and testing, we have outlined the precision required at each stage to ensure reliable performance in the final products.
Recap of Key Points
Throughout this article, we underscored several key points:
- Raw Materials: The selection of materials, particularly silicon, remains foundational. Silicon's unique properties make it an ideal semiconductor, but other materials like gallium arsenide also play specialized roles.
- Fabrication Process: Each step—from wafer fabrication to doping—requires extreme accuracy. Techniques such as photolithography are vital for creating the intricate patterns essential for device functionality.
- Challenges and Innovations: Factors, both environmental and economic, pose significant obstacles. Yet, technological advancements, like the development of quantum computing and the exploration of 2D materials, are paving the way for future solutions.
- Global Market Dynamics: The semiconductor market is intensely competitive and subject to shifts influenced by geopolitical dynamics and supply chain realities.
The Importance of Ongoing Research
The semiconductor realm does not stand still. Ongoing research is paramount, fueling innovation and addressing challenges that arise. As devices become ever more complex, the need for advanced manufacturing techniques and materials is clear. Moreover, the rise of novel areas like quantum computing suggests a shift in focus, which demands a re-evaluation of established practices in the industry.
In the grand scheme, investing in research and development not only enhances the capabilities of semiconductor devices but can also lead to advances that mitigate the environmental impact of manufacturing processes. The aim is to create a balance between industrial growth and sustainable practices—a challenging yet vital endeavor for the industry.
“Innovation distinguishes between a leader and a follower.”
—Steve Jobs
With new knowledge comes new challenges, but also new opportunities for growth and discovery. In a world increasingly reliant on sophisticated electronics, the discourse on semiconductors is more relevant than ever.