Understanding Shore Hardness Meters: An In-Depth Exploration
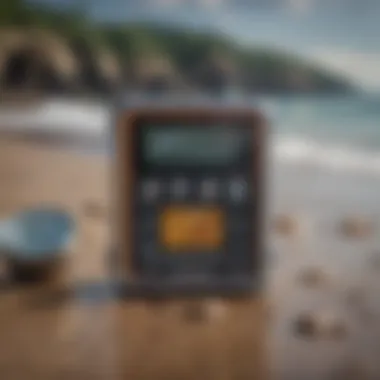
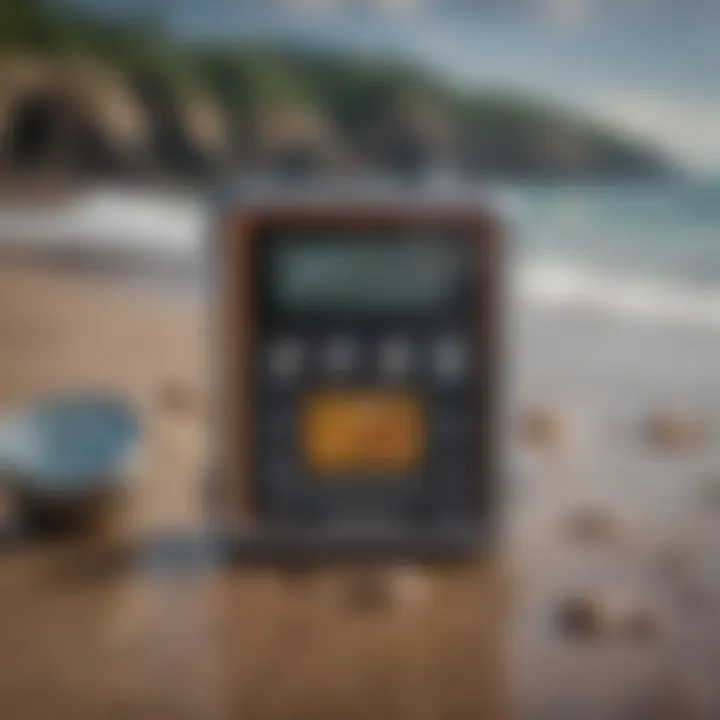
Intro
Shore hardness meters are vital tools for measuring the hardness of materials, particularly polymers and elastomers. These devices are essential in various industries, including manufacturing and material science, where precise measurement of hardness can influence quality control and performance. Understanding how shore hardness meters work, their variations, and their applications will inform not only students and researchers but also professionals in related fields who rely on accurate testing for their work.
Research Context
Background and Rationale
The measurement of hardness has a rich historical context. Historically, hardness tests date back to the early 19th century, with methods evolving to accommodate different material types and testing needs. Shore hardness meters were developed to provide a quick and reliable means of assessing the hardness of materials like rubber and plastics, which is crucial for industries where material performance is closely tied to hardness levels. As technology improves, so does the need to understand the principles and functionalities behind these measurements. Accurate hardness testing helps prevent defects in products and ensures safety and reliability.
Literature Review
A survey of literature reveals a significant breadth of research surrounding hardness testing. Numerous studies focus on the reliability and accuracy of various hardness testing methods, including the Shore test. Comprehensive reviews outline the principles of different shore hardness scales, such as Shore A, Shore D, and others. Many researchers also discuss the practical and theoretical implications of hardness measurements in production processes. Notable publications, including articles on platforms like Britannica, provide in-depth analyses of materials and their characteristics, reinforcing the need for precise hardness measurement.
Methodology
Research Design
To provide a holistic view of shore hardness meters, a mixed-methods approach can be beneficial. This design allows for both qualitative and quantitative assessments, offering a comprehensive understanding of the topic. Quantitative methods can include statistical analyses of hardness measurement data, while qualitative insights could come from expert opinions and case studies in industrial applications.
Data Collection Methods
Data can be gathered from multiple sources. Surveys can target industry professionals to glean their experiences with shore hardness meters. Additionally, reviewing case studies where hardness tests have been crucial in product development will offer insight into real-world applications. Academic journals and articles, particularly those found on Wikipedia, can serve as valuable resources in this research. Emphasizing accuracy and measurement in our exploration reveals the prevalent issues facing quality control in various fields.
Preface to Shore Hardness Meters
Shore hardness meters serve a crucial role in material science and engineering. Understanding these devices is essential for professionals who work with materials and their properties daily. These meters help quantify hardness, a fundamental property that influences material selection, processing, and performance in various applications. The importance of accurately measuring hardness cannot be overstated, as it affects items used in everyday life, from rubber soles to high-performance engineering materials.
Definition and Purpose
A Shore hardness meter is a tool used to measure the hardness of materials, primarily polymers, elastomers, and rubbers. The measurement is based on the depth of penetration of an indenter under a specific load. Different scales, especially Shore A and Shore D, correspond to materials of varying hardness. For instance, Shore A is commonly used for softer materials, while Shore D suits harder substances. The purpose of these meters extends beyond simple measurement; they aid in quality control, material selection, and ensuring product reliability.
This measurement process aids manufacturers and researchers in assessing materials accurately, ensuring that the products meet required specifications. Hence, understanding the definition and purpose of Shore hardness meters recognizes their critical role in various industries, including automotive, aerospace, and consumer goods.
Historical Development
The evolution of Shore hardness meters traces back to the need for standardized measurements in materials science. Originally, hardness testing methods were qualitative at best, lacking precision and reproducibility. In the 1920s, the Shore scale was developed by Albert Shore, introducing a more systematic approach to measuring hardness. This innovation marked a significant turning point, paving the way for consistent and repeatable results.
Over the decades, technological advancements have further refined these meters. The introduction of digital displays and improved calibration methods has enhanced usability and accuracy. Additionally, the development of various testing scales caters to a broader range of materials. These historical milestones explain not only the progress but also the relevance of Shore hardness meters in today's scientific and industrial landscape. Their continued evolution speaks to the ongoing pursuit of precision and reliability in material assessments.
Mechanics of Shore Hardness Measurement
The mechanics of shore hardness measurement play a vital role in comprehending how materials react to applied pressure. This section highlights the fundamentals that contribute to understanding the relationship between material properties and the methodologies used to assess these properties. Accurate measurements are crucial for various applications, ensuring the quality and consistency of products across industries.
Operating Principles
The operating principle of shore hardness measurements centers around the concept of deformation. When a specific force is applied to a material, the extent of its deformation indicates its hardness level. This mechanics relies on a standardized procedure where a durometer, holding a spring-loaded indenter, is pressed against the surface of the tested material.
For instance, the depth of indentation is measured, which directly correlates to the material’s hardness. The harder the material, the less it will deform under pressure. The readings obtained from various shore hardness tests help engineers and researchers determine material suitability for specific applications.
Types of Shore Hardness Tests
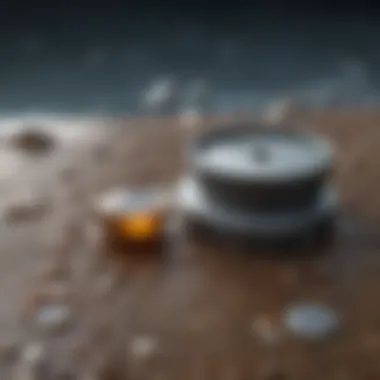
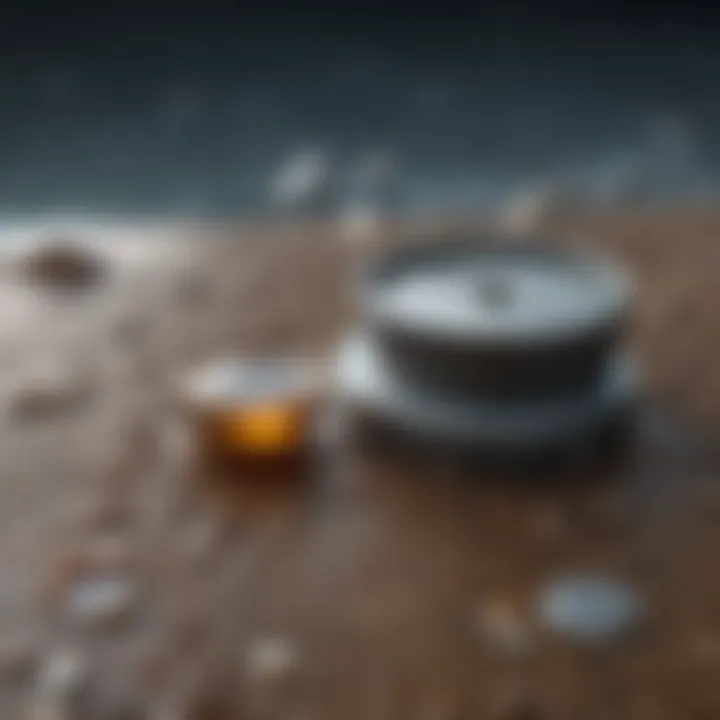
Different types of shore hardness tests cater to various materials and desired accuracy levels. These tests are critical in applications ranging from quality control to material development. Each test type is designed with unique characteristics:
- Shore A Hardness Test: This test is primarily used for softer materials, including rubber and flexible plastics. The key characteristic of the Shore A hardness test is its relatively low force applied by the indentor, making it suitable for softer samples. This test is popular due to its ability to provide precise readings in materials that exhibit elasticity. A unique feature is its scale range, which allows for nuanced differentiation between various levels of softness. However, one drawback is its limited application to harder materials.
- Shore D Hardness Test: Designed for harder materials, this test employs a higher force, making it suitable for rigid plastics and hard rubber. The key characteristic of Shore D is its ability to deliver robust readings for materials that other tests may not accurately assess. It is beneficial for industries focusing on harder compounds. A distinctive aspect of this test is how it handles the hardness profile, ensuring that even subtle differences in hardness are captured. Nevertheless, the heavy force can lead to inaccuracies in softer materials, limiting its versatility.
- Shore O Hardness Test: This test is relatively less common but incredibly useful for thin materials or soft elastomers. One of its key characteristics is the unique indenter design, allowing for accurate measurement in delicate samples without causing excessive deformation. The Shore O hardness test serves as a crucial option for specialized applications. A notable advantage is its ability to provide detailed information on very soft materials. However, its limited applicability can be a challenge in certain contexts, as it is not suitable for materials with higher hardness levels.
Understanding these diverse testing methods enables professionals to select the right approach for their specific industry or research needs. Each hardness test contributes uniquely to the landscape of material science and quality assurance, underlining the importance of tailored measurement techniques.
Shore Hardness Instrumentation
Shore hardness instrumentation forms a critical component in the realm of material testing. The choice between various types of hardness meters is vital for accurate assessment. Both digital and analog meters possess unique advantages and certain limitations. Understanding these differences aids in selecting the right tool for specific applications. Furthermore, proper calibration and maintenance of these devices ensure reliable results over time.
Digital vs. Analog Meters
Digital meters represent the forefront of technology with their ease of use and precision. They often display readings electronically, which reduces the potential for human error. Features such as data logging, connectivity options, and ease of interpretation make digital meters suitable for both testing labs and field usage. However, they rely on batteries and may be dependent on software updates, which could be a consideration in environments where reliability is paramount.
On the other hand, analog meters maintain a strong place in the market due to their simplicity and ruggedness. They do not require batteries, making them dependable in remote areas or extreme conditions. However, reading analog scales can sometimes lead to inaccuracies, as interpretations rely more on the user's skill. Each type has its context, and understanding the environment of use is essential when selecting between digital and analog options.
"Having the right shore hardness instrument is not just a matter of preference; it significantly impacts the accuracy and reliability of material assessments."
Calibration and Maintenance
Regular calibration is essential for any hardness meter to maintain its accuracy and longevity. Calibration ensures that the meter provides precise readings, taking into account any shifts in measurements that can occur over time. Most manufacturers provide specific guidelines on the intervals and methods of calibration. Users should not overlook this aspect to maintain a high standard of measurement integrity.
Maintenance practices vary between digital and analog meters. For digital meters, ensuring that the device remains charged and updating software if applicable is crucial. Cleaning the probe and housing is also important to prevent any dirt or residual material from interfering with measurements.
With analog meters, careful handling is necessary to avoid physical damage. Regular cleaning of the dial and needle mechanism can significantly improve the accuracy of readings. Furthermore, storing these instruments in appropriate conditions protects them from environmental factors that may affect their performance.
Interpreting Shore Hardness Values
Interpreting shore hardness values is crucial for ensuring the reliability and quality of materials in various applications. These values reflect the hardness of a material, which directly influences its mechanical properties. Understanding how to read and analyze these values is vital for professionals in material science, engineering, and manufacturing.
The significance of shore hardness values extends beyond mere numbers; they serve as benchmarks in quality control processes. Proper interpretation informs decisions regarding material selection and processing methods. Misunderstanding these values can lead to failures in product performance and durability.
Understanding Hardness Scales
Shore hardness scales are designed to quantify the hardness of materials, particularly polymers and elastomers. The Shore A scale is commonly used for softer materials like rubber, while the Shore D scale is more suited for harder materials such as hard plastics. Each scale utilizes a different durometer, enabling accurate measurements based on the sample's characteristics.
For practical understanding:
- Shore A Hardness: It ranges from 0 to 100. A higher number indicates a harder material.
- Shore D Hardness: It measures from 0 to 100, but is used for harder substances.
It is essential for users to familiarize themselves with the scale applicable to their specific material. Each scale operates on distinct principles, affecting how hardness is measured.
Factors Influencing Readings
Several factors affect the shore hardness readings, and awareness of these factors is essential for precise measurement and interpretation:
- Material Composition: The chemical makeup of a material can greatly influence its hardness. For example, additives may soften or harden a product.
- Sample Thickness: Thicker samples may yield different readings compared to thinner ones. This is particularly important in flexible materials, where thickness impacts the penetration of the durometer.
- Temperature: Hardness can vary depending on temperature. Measurements taken at elevated temperatures might not accurately represent the material's hardness at room temperature or other conditions.
- Surface Conditions: The surface finish of a material can affect measurements. Rough or smooth surfaces may present different hardness readings, so it is important to standardize how samples are prepared for testing.
"Understanding the interplay of these factors is essential for accurate shore hardness testing and quality assurance."
Professionals must consider these elements when interpreting the results, as they can significantly skew the understanding of a material's true hardness. Proper training and experience in hardness measurement techniques enhance the reliability of the readings and the overall quality control in manufacturing.
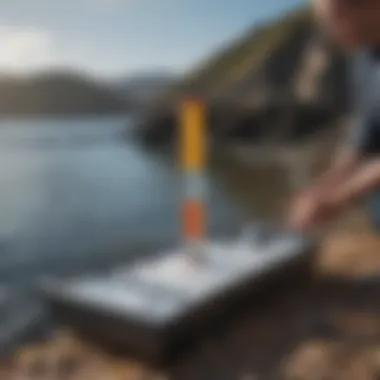
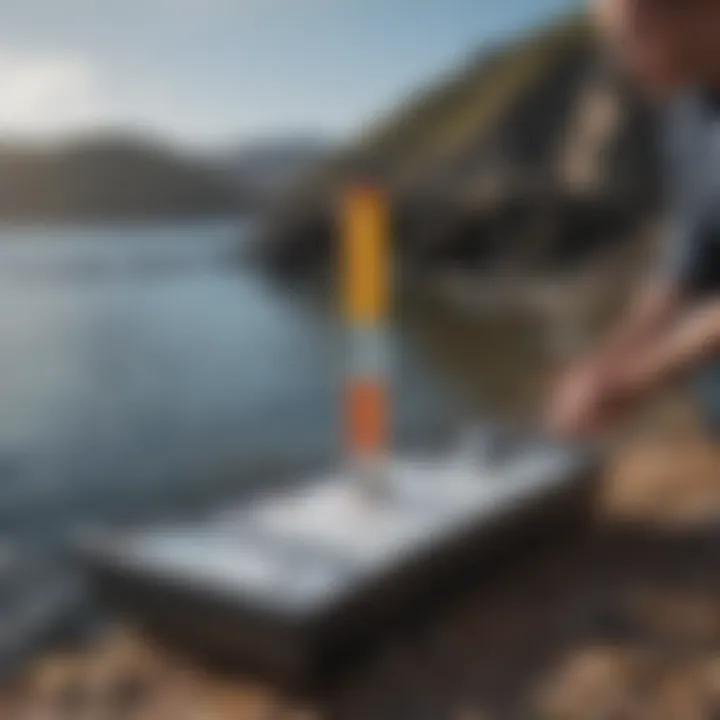
Applications of Shore Hardness Testing
The applicability of shore hardness testing extends to various disciplines, making it a critical factor in multiple industries. Shore hardness meters serve not only as instruments for simple measurement but also enhance the understanding of material properties and functional behaviors in practical applications. Companies and researchers rely on precise hardness testing to establish standards, improve processes, and ensure product durability. Key benefits of shore hardness testing include accurate assessments of material quality, consistency in manufacturing processes, and informed decision-making in product development and engineering.
Material Science and Engineering
In material science and engineering, shore hardness testing is vital to evaluating the attributes of different materials. Engineers use these measurements to select the appropriate materials for specific applications, which influences the performance of the final product. For instance, the hardness of polymers, elastomers, and similar materials can indicate their resilience, wear resistance, and overall durability. By characterizing materials' hardness, engineers can predict how they will behave under stress, which is essential for applications ranging from automotive components to medical devices.
Obtaining precise shore hardness values helps to:
- Select materials accurately: Understanding the hardness of materials allows engineers to choose the right one for an application, optimizing functionality and longevity.
- Analyze phase transformations: Changes in hardness can signify transformations in material structure, informing researchers about the effects of different treatments.
- Predict material performance: Hardness correlates with other properties, so it serves as a predictor for how materials will perform in real-world conditions.
Quality Control in Manufacturing
Quality control is another significant area where shore hardness testing plays an integral role. In manufacturing, maintaining high standards is paramount, and inconsistent hardness measurements can result in defective products. Regular hardness testing ensures that materials meet the required specifications, thus preventing faulty items from entering the supply chain. This aspect is particularly crucial in industries such as automotive, aerospace, and plastics, where precision impacts safety and functionality.
Industries apply shore hardness testing by:
- Performing routine checks: Implementing hardness testing as a part of the quality assurance process to ensure that products consistently meet established standards.
- Facilitating compliance with regulations: Many industries must adhere to national and international standards that specify hardness parameters; testing aids in compliance.
- Identifying batch issues: Regular measurements help pinpoint anomalies in production that could affect the overall quality of materials.
Research and Development
In the realm of research and development, understanding material properties through shore hardness testing is essential for innovation. Scientists and researchers leverage hardness values to explore new materials, studying how variations in composition affect hardness. This exploration can lead to the development of advanced materials that offer superior performance for various applications.
The contributions of shore hardness testing in R&D include:
- Experimentation with new composites: Hardness testing aids researchers in developing and refining composite materials, influencing applications in electronics and construction.
- Evaluating material degradation: Understanding hardness over time allows researchers to study how materials degrade, influencing decisions regarding lifespan and performance degradation.
- Enhancing product functionalities: Insights gained from hardness testing direct product enhancements, leading to innovations that improve user experiences.
"Shore hardness testing is not merely about measurement; it embodies a comprehensive understanding of materials, significantly shaping industries and innovations."
This connection between shore hardness testing and application across disciplines underscores its importance as a tool for ensuring material performance, reliability, and advancement in technology. By harnessing the precision of shore hardness meters, professionals can drive quality and innovation forward.
Advanced Techniques in Shore Hardness Measurement
Advanced techniques in shore hardness measurement play a crucial role in enhancing the accuracy and reliability of hardness testing across various industries. As materials evolve, the need for precise measurement techniques has increased. These innovations ensure that manufacturers and researchers obtain consistent and meaningful data, which is essential for quality control and product development. Understanding these advanced techniques allows users to make informed choices in their testing processes.
Emerging Technologies
Emerging technologies are reshaping the landscape of shore hardness testing. New devices utilize advanced sensors and automation, which bring various benefits to measurement practices. For instance, digital Shore hardness meters now come equipped with improved display features and real-time data transmission. This capability supports immediate analysis and more informed decision-making on production lines.
Some of the key advancements include:
- Laser-based hardness testing: Offers non-destructive measures that ensure minimal impact on the material.
- Ultrasonic methods: Facilitate testing without direct contact, which is advantageous for delicate surfaces.
- Smart sensors: These collect data through comprehensive interfaces, often integrating with cloud storage for remote access.
Each of these technologies brings about greater accuracy and reduces the likelihood of human error in measurement, which is especially critical in high-stakes industries such as aerospace and automotive manufacturing.
Integration with Digital Systems
The integration of shore hardness testers with digital systems represents a significant shift in measurement capabilities. Many modern meters now come equipped with software that allows seamless connection with laboratory information management systems (LIMS) and quality control databases. This synergy facilitates the following:
- Data Analytics: Integrated systems enable statistical analysis of hardness values, allowing trends to be identified easily.
- Reporting and Documentation: Automatic generation of reports reduces administrative time and helps maintain quality assurance records.
- Customization: Users can configure settings specific to their testing needs, enhancing the equipment’s versatility.
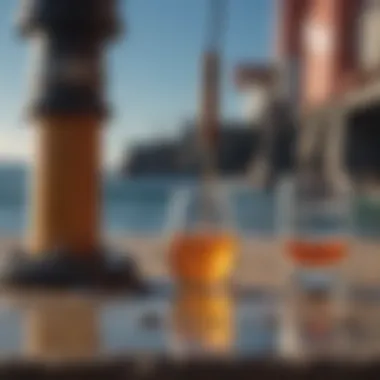
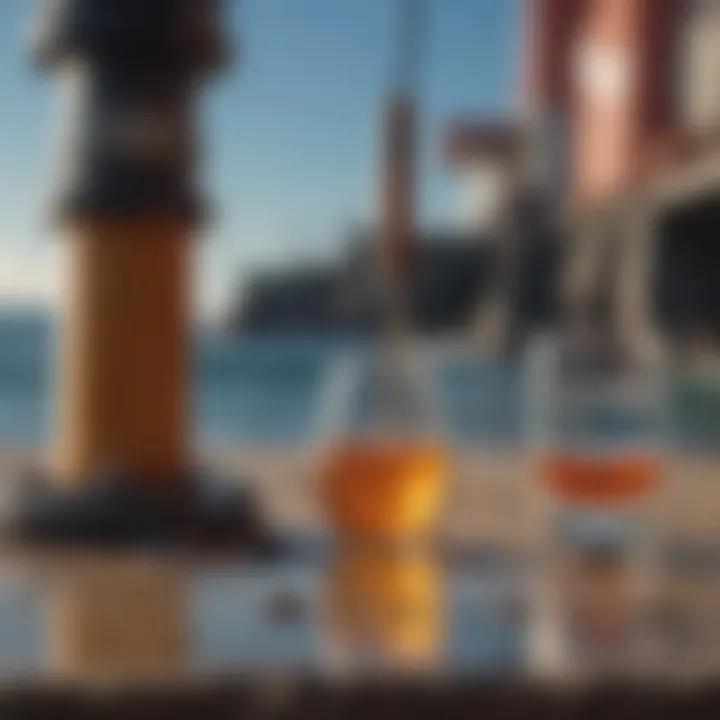
This integration not only streamlines operations but also enhances traceability of measurements, essential for compliance with industry standards.
Digital connectivity ultimately contributes to more robust data management practices, thereby improving overall efficiency in production environments. Optimizing hardness testing through the use of advanced techniques and technologies will continue to pave the way for quality improvements across numerous applications.
Challenges in Shore Hardness Testing
In the realm of shore hardness testing, understanding the challenges is crucial for ensuring accurate and reliable measurements. These challenges not only affect the readings obtained but also have implications on research, development, and quality control processes. Awareness of these difficulties enables users to adopt necessary precautions, improving accuracy in results. The following subsections elucidate key challenges in shore hardness testing, focusing on common measurement errors and limitations related to specific materials.
Common Measurement Errors
Obtaining precise hardness measurements requires diligence and knowledge. Some of the common measurement errors include:
- User Variability: The skill and technique of the operator can significantly influence readings. Variances in how pressure is applied or the angle of the meter can lead to inconsistent results.
- Calibration Issues: Regular calibration of shore hardness meters is essential. If meters are not calibrated properly, they can provide faulty readings, undermining the reliability of tests.
- Environmental Factors: Temperature and humidity can affect material properties and, subsequently, hardness measurements. Changes in these conditions may lead to readings that do not accurately reflect the actual hardness.
- Material Surface Conditions: The surface finish of the material can significantly influence the accuracy of hardness tests. Rough or uneven surfaces may yield inconsistent readings due to the meter not making uniform contact with the sample.
It is critical to be aware of these errors to minimize their impact. Ensuring consistent technique, adequate calibration, and controlled testing environments can significantly improve the accuracy of measurements.
Material-Specific Limitations
Different materials possess unique properties that can pose challenges during hardness testing. Some limitations include:
- Hardness Range: Shore A meters are designed for softer materials like rubber, while Shore D meters are used for harder substances like plastics. Using the wrong type can result in inaccurate readings.
- Material Composition: Certain composites or blends may have variations within the material, leading to inconsistent hardness values across samples. For instance, a rubber compound with additives may exhibit a broader range of hardness.
- Anisotropic Properties: Some materials, such as certain plastics or composites, have directional properties. This means hardness can vary based on the orientation of the material. Taking multiple readings at different angles is crucial for accurate assessments.
Understanding these limitations is vital for selecting appropriate testing methods and interpreting results correctly. When testing materials, one must carefully consider their specific behavior to ensure valid outcomes.
Future Trends in Shore Hardness Measurement
The future of shore hardness measurement is evolving rapidly, with advancements in technology and growing market demand. This section highlights the importance of staying informed about the latest trends and developments in this field. Understanding these trends is crucial for professionals and researchers who work with materials that require precise hardness assessments.
Research Developments
Research in shore hardness measurement is focusing primarily on enhancing accuracy and efficiency. New materials and methods are being developed to improve measurement reliability. For example, innovative sensors and digital technologies are emerging. These advancements allow for faster and more accurate readings, minimizing operator error and increasing reproducibility.
- Micro and Nano-Hardness Testing:Researchers are creating miniaturized shore hardness tests for smaller materials. This is particularly useful in the semiconductor and electronics industries.
- Non-Destructive Testing Techniques:New methods are emerging that allow for shore hardness measurement without damaging the material. This is especially valuable for quality control processes where preserving integrity is essential.
- Automated Systems:Integration of automated systems is becoming more common. Automation can streamline hardness testing in manufacturing environments, increasing productivity and consistency.
Market Demand and Potentials
The demand for shore hardness testing is likely to increase across various industries, demonstrating its critical role in quality control and product development. Several factors contribute to this growing market.
- Increased Regulations: As industries face stricter regulations regarding material properties, the demand for accurate shore hardness testing has risen. Manufacturers must comply with these regulations to ensure product safety and performance.
- Emerging Industries: New industries, such as advanced materials and renewable energy sectors, require significant hardness testing. For instance, materials utilized in battery production must undergo precise hardness assessments for performance reliability.
- Technological Integration: As industries adopt more digital solutions, there is potential for integrating shore hardness meters with existing digital systems. This can enhance data management and analysis, providing deeper insights into material properties.
Culmination
In this final section, it is vital to reflect on the role that shore hardness meters play not just in measurement but in the broader context of material sciences and manufacturing. Shore hardness testing provides critical data that informs quality control processes, ensuring that materials meet necessary standards for performance and safety. This means that any lapses in precision can directly impact production outcomes and product reliability.
Summary of Key Points
The previous sections have outlined several important aspects of shore hardness meters. Key points include:
- Definition and Purpose: Shore hardness meters are instruments designed to measure the hardness of materials, particularly polymers, elastomers, and soft metals.
- Types of Tests: Different shore hardness tests, such as Shore A, D, and O, cater to various materials and hardness ranges, showcasing the versatility of these instruments.
- Challenges: Common errors in measurement and material-specific limitations can affect accuracy, necessitating a commitment to careful testing procedures and proper calibration.
- Emerging Technologies: Advancements in technology continue to enhance measurement precision, integrating hardware with digital systems that streamline data collection and analysis.
These elements underscore the relevance of shore hardness meters, highlighting their essential role in various industries from manufacturing to research and development.
The Future of Shore Hardness Testing
The future of shore hardness testing looks promising, with continuous research developments aimed at enhancing measurement techniques. As industries increasingly emphasize quality control, the demand for precise and reliable shore hardness measurements will likely grow. This may lead to:
- Integration with Advanced Technologies: The merging of shore hardness testing with smart technology could transform data handling and increase efficiency.
- Material Innovations: As materials evolve, new standards and testing methods will be necessary to ensure compatibility and performance.
- Educational Advancements: Growing interest in material sciences and engineering may boost educational programs focused on instrumentation, ensuring that future professionals are well-equipped with knowledge about hardness testing techniques.
In summary, understanding the nuances of shore hardness meters is imperative for researchers, students, and professionals working in related fields. Their importance in achieving quality assurance and driving material innovation will undoubtedly shape future practices in multiple industries.