Understanding Spirol Disc Springs: Design and Applications
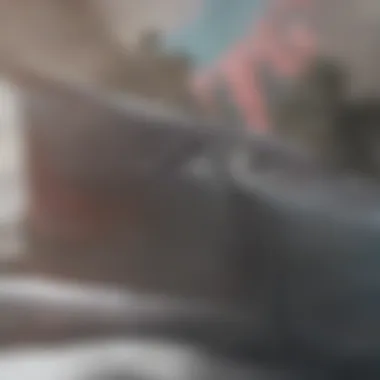
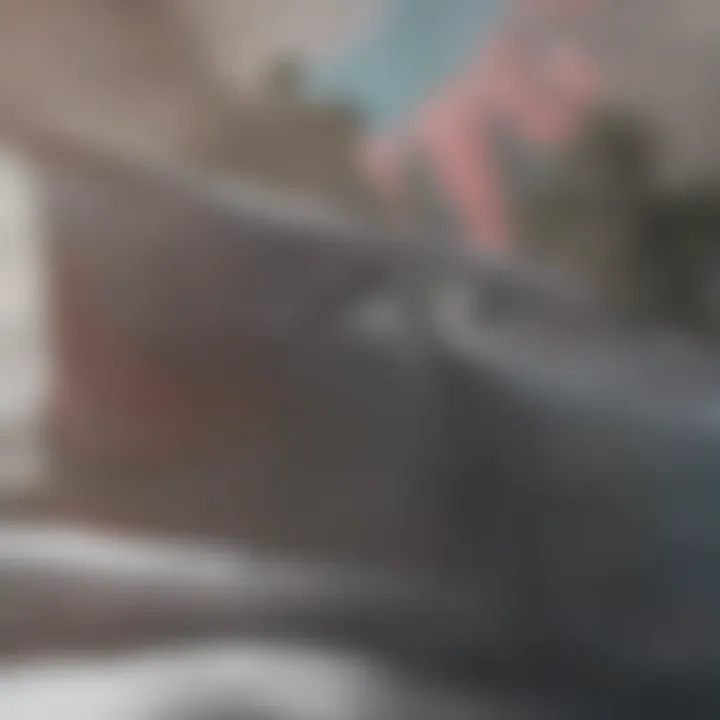
Intro
Spirol disc springs play a crucial role in various engineering applications. Their unique design and functionality make them advantageous over typical spring technologies. Understanding how these springs work involves examining their construction, the mechanics behind their performance, and the types of materials used in their fabrication. This article aims to provide a comprehensive exploration of spirol disc springs, their innovations, and future trends.
Research Context
Background and Rationale
The background of spirol disc springs traces back to advancements in spring technology, which have been essential in achieving efficient force application in mechanical systems. These springs offer high energy storage capabilities, compact design, and a wide range of configurations. The rationale for investigating this topic emerges from the increasing application of spirol disc springs in various sectors, such as aerospace, automotive, and manufacturing.
Literature Review
Several studies have analyzed disc springs' mechanical properties and applications. Research has shown that spirol disc springs can withstand high loads while maintaining a small footprint. Innovations in materials and manufacturing techniques have further enhanced their performance. Reviewing existing literature provides insights into contemporary challenges and the evolving landscape of spring technology. Notable references include articles from Encyclopaedia Britannica and other leading engineering publications available via platforms like Wikipedia and specialized forums on Reddit.
Methodology
Research Design
The approach to examining spirol disc springs combines both qualitative and quantitative methodologies. This includes reviewing existing studies and performing numerical analyses to evaluate performance metrics under different conditions. Comparing design characteristics with traditional spring types reveals significant distinctions in functionality and efficiency.
Data Collection Methods
Data for this research is collected from a variety of sources, including empirical studies, technical reports, and interviews with industry professionals. These resources help to gather information about current practices in the design and application of spirol disc springs. Key findings are then synthesized to provide a rounded understanding of the topic.
Prelude to Spirol Disc Springs
The study of spirol disc springs is crucial for understanding their role in the domain of engineered components. These springs offer distinct advantages over traditional spring mechanisms, particularly in situations that demand high efficiency and space-saving designs. Their unique construction allows for better load distribution and can significantly reduce the material used without compromising functionality. As industries advance and innovate, the need for reliable, space-efficient, and lightweight components becomes increasingly important. This article will provide a comprehensive overview of the design, applications, and innovations related to spirol disc springs.
Definition and Overview
Spirol disc springs are conical-shaped, circular spring elements designed for various applications. They consist of multiple discs arranged in a series, allowing them to compress and expand with applied force. They can absorb energy, store it temporarily, and return to their original form when the load is removed. This ability to undergo cyclic loading without permanent deformation is essential in many mechanical systems. Their design can accommodate specific load requirements and perform well under varying conditions.
Historical Development
The evolution of spirol disc springs traces back to the mid-20th century when engineers were searching for alternatives to conventional coil springs. These initial explorations led to the development of springs that could utilize limited space more effectively while achieving higher performance levels. Over time, advancements in material science and designed methodologies have improved the manufacturing processes as well. Today, spirol disc springs are utilized in diverse sectors, ranging from automotive to aerospace, showcasing their versatility and effectiveness in addressing modern engineering challenges.
"Spirol disc springs offer a unique combination of high performance, compact design, and adaptability across multiple applications."
In summary, understanding the principles, design, and historical context of spirol disc springs is fundamental for industry professionals. This knowledge not only facilitates better component selection but also fosters innovation and improvement in design practices.
Mechanics of Spirol Disc Springs
The mechanics of spirol disc springs plays a critical role in understanding their function and applications. These springs are unique due to their ability to store precise energy while compactly fitting into various designs. Understanding their mechanics includes the basic principles of operation, load and deflection characteristics, and stress distribution analysis. Each of these elements contributes to the overall effectiveness of these springs in different engineering contexts. Their importance cannot be overstated, as they enhance design flexibility and efficiency.
Basic Principles of Operation
The operation of spirol disc springs is based on several fundamental principles. Primarily, they operate by utilizing angular displacement to create forces. When a load is applied, the disc springs deflect in a manner that converts this load into potential energy. This energy can be released upon removal of the load, thereby making these springs suitable for various applications such as automotive suspensions or clamping mechanisms.
The key features of their operation include:
- Elastic behavior: Spirol disc springs exhibit elastic deformation, which allows them to return to their original shape after the load is removed.
- Stacking capabilities: They can be stacked to increase load capacity without compromising on space.
- Controlled deflection: The geometry of the spring allows designers to control deflection characteristics.
Load and Deflection Characteristics
Load and deflection characteristics determine how effectively a spirol disc spring can perform under stress. The relationship between load and deflection is not linear. This non-linear behavior is crucial in applications where precise control over spring resonance is needed. As the load increases, the spring deflection also increases, but at an accelerating rate.
Some important considerations include:
- Load capacity: Each disc spring has a specific load capacity, beyond which it may undergo permanent deformation.
- Deflection limits: Understanding the limits of deflection helps in optimizing designs to ensure functional integrity over time.
- Spring rate: The rate at which a spring responds to loading is paramount. Engineers must account for these variations when designing systems that rely on consistent performance.
Stress Distribution Analysis
Stress distribution analysis in spirol disc springs is essential for understanding how stress is transferred throughout the component during operation. When a load is applied, the stress does not remain uniform across the surface of the spring. Instead, it varies based on the spring's geometry and the load's location.
Key factors in this analysis include:
- Peak stress areas: Identifying areas where maximum stress occurs helps prevent failure due to material fatigue.
- Material selection: Different materials respond differently to stress, impacting the overall performance and longevity of the springs.
- Fatigue life estimation: Understanding where stress concentrates can inform projections about how long a spring will last before failure.
In summary, the mechanics of spirol disc springs are profound and multifaceted. Through the exploration of their operating principles, load characteristics, and stress analysis, one gains a comprehensive understanding that aids in the design and application of these critical components in various engineering fields.
Design Considerations
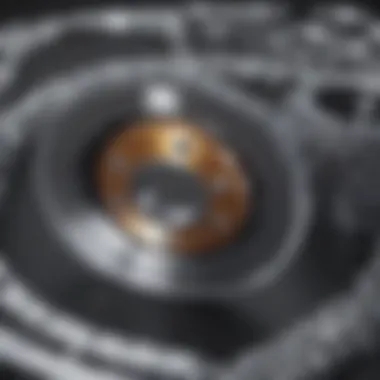
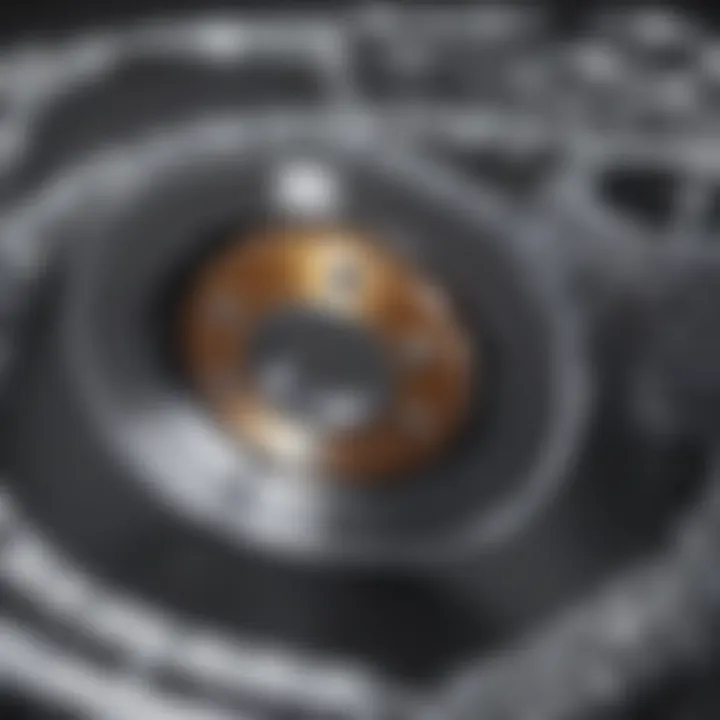
In the engineering design of spirol disc springs, several critical factors ensure optimal performance and longevity. These factors help engineers prioritize strength, flexibility, and functionality. A well-thought-out design not only influences how a disc spring performs under load, but also its reliability and adaptation to various applications.
Key Design Parameters
The design of spirol disc springs revolves around key parameters that affect their performance. These parameters include the material choice, thickness of the disc, and geometry. Material selection is foundational. Springs made from high-carbon steel, for instance, offer excellent fatigue resistance and are widely used in numerous applications. The thickness of the disc directly influences its load capacity. Thicker discs typically handle more load but are also heavier.
Geometric factors like coil diameter and height further dictate how the spring will behave. A larger diameter tends to provide softer resistance, while smaller diameters yield a stiffer experience. Understanding these parameters aids in tailoring springs to specific needs.
Geometric Configurations
When considering the design of spirol disc springs, the geometric configuration plays a substantial role. Different shapes and configurations determine how the spring will interact within its environment. The two primary forms of disc springs are the conical and flat configurations.
- Conical Disc Springs: These offer a significant advantage in applications requiring high loads with minimal space. Their slope provides a more linear engagement under load, making them efficient in shock absorption.
- Flat Disc Springs: These are generally used for applications that demand uniform load distribution. They provide predictable performance under static conditions.
Based on the application, engineers must select the right configuration to ensure the spring meets specific mechanical requirements without unnecessary bulk or complexity.
Performance Optimization Techniques
Enhancing the efficiency and functionality of spirol disc springs often involves various optimization techniques. Factors such as surface finish and heat treatment can dramatically increase performance.
Surface Treatments: Processes like shot peening and hardening improve fatigue life. A smoother finish reduces wear and enhances adaptability in operational environments, which is vital for applications in automotive and aerospace sectors.
Heat Treatment: This technique adjusts properties at the molecular level, providing improved hardness without sacrificing flexibility. This balance is critical when developing springs that operate under diverse conditions while still maintaining functional integrity.
By applying these optimization techniques, engineers can ensure that the disc springs will survive demanding conditions and perform reliably for extended periods.
"Optimizing design parameters and incorporating advanced techniques elevates the performance of spirol disc springs beyond conventional limits."
Materials for Spirol Disc Springs
Materials play a crucial role in the performance and durability of spirol disc springs. The selection of the right material can significantly influence the spring's mechanical properties, load capacity, and overall longevity. Choosing an appropriate material involves considering factors such as strength, fatigue resistance, and corrosion resistance. Each of these characteristics will affect how a disc spring operates under various conditions.
Common Material Types
Several materials are commonly used in the manufacturing of spirol disc springs. These include:
- High-Strength Steel Alloys: Often utilized due to their excellent tensile strength and fatigue resistance.
- Stainless Steel: Known for its corrosion resistance and good mechanical properties. Commonly used in applications where exposure to moisture or chemicals is likely.
- Carbon Steel: Generally used in applications where high strength is required but corrosion resistance is not critical.
- Plastic Composites: Emerging as alternatives in specific environments, they offer benefits like lightweight and resistance to corrosion.
Each material brings unique benefits and limitations, making preliminary testing essential to ensure optimal performance for intended applications.
Material Properties and Selection Criteria
The selection of materials for spirol disc springs is based on various criteria which include:
- Mechanical Properties: This encompasses yield strength, tensile strength, and fatigue life. It determines how well the spring can handle mechanical stress.
- Environmental Factors: The operating environment's conditions, like temperature and exposure to chemicals, influence material choice. For example, high temperatures may necessitate the use of special alloys or coatings.
- Manufacturing Process: The compatibility of the material with manufacturing techniques can dictate options. Some materials are easier to shape, while others may require specific methods or controls.
- Cost Considerations: Economic factors often guide material selection, balancing performance and budget.
Innovations in Material Science
Recent advancements in material science have brought forward innovative solutions for enhancing spirol disc springs. New materials, such as advanced carbon fiber composites, offer high strength with reduced weight, appealing for aerospace and automotive applications. Furthermore, the development of smart materials has led to springs that can adapt to varying loads, improving performance and durability.
Additionally, surface treatments such as coating technologies and hardening processes help in extending the lifespan of disc springs, making them more resilient to wear and environmental conditions.
In summary, the choice of materials for spirol disc springs significantly impacts their design and application, necessitating careful consideration of various factors that affect performance and sustainability in use.
For a deeper exploration of material properties, refer to resources like Wikipedia or Britannica.
Manufacturing Processes
The manufacturing processes of spirol disc springs are crucial for ensuring that they meet specific performance and durability standards. These processes determine the mechanical properties of the springs, including their load-bearing capabilities and flexibility. Understanding these processes provides insight into how design considerations directly correlate with manufacturing methodologies, which affects the overall cost and quality of the final product.
Key factors in manufacturing processes include material selection, operational techniques, and the degree of precision required during production. Every step in manufacturing affects the quality and reliability of the springs in their applications. Therefore, an awareness of manufacturing innovations can lead to enhanced performance and lifespan of spirol disc springs.
Common Manufacturing Techniques
Several techniques are widely used to manufacture spirol disc springs. These techniques include:
- Cold forming: This method shapes the material at room temperature, allowing for better control over the dimensions and mechanical properties.
- Hot forming: When higher strength materials are required, this technique is employed. Heating the metal reduces its hardness, making it easier to shape.
- Coiling: This technique is specifically useful for creating the helical form that characteristic of disc springs.
- Laser cutting: Offers precision in creating the desired shapes and sizes of the springs, thereby minimizing waste in the material.
Cold forming remains one of the most preferred methods due to its cost-effectiveness and ability to produce springs with a high degree of accuracy.
Quality Control Measures
Quality control in the manufacturing of spirol disc springs ensures that every product meets specified standards before reaching the market. Quality control measures include:
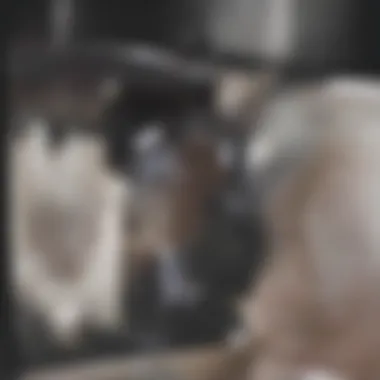
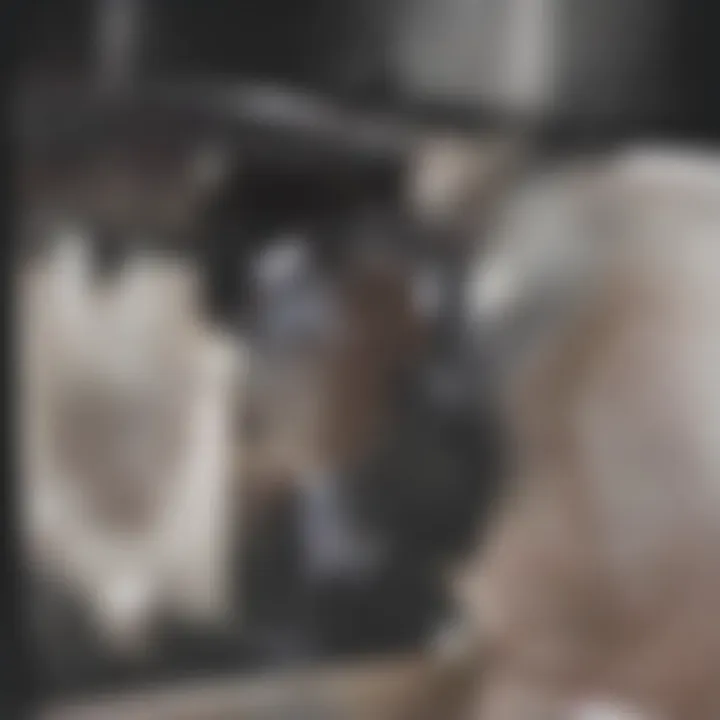
- Material inspection: Evaluating material properties before production begins to ensure they are suitable for specific applications.
- Dimensional checks: Regular measurements during production to confirm that the springs adhere to required specifications.
- Functional testing: Ensuring that the springs can achieve their intended load and deflection characteristics under normal and extreme conditions.
- Final inspections: A thorough assessment of the completed product before it is delivered is important to verify quality control processes.
Implementing these quality control measures minimizes the risk of failure and increases customer satisfaction, establishing good industry practices.
Surface Treatment and Finishing
Surface treatment and finishing play essential roles in enhancing the performance of spirol disc springs. They not only improve the aesthetic appeal but also protect against corrosion and wear. Some common treatments include:
- Galvanizing: This zinc-coating technique greatly improves the spring's resistance to environmental damage.
- Powder coating: Provides a protective layer that can also deliver color and other aesthetic properties.
- Passivation: Often used for stainless steel springs, this treatment boosts corrosion resistance by eliminating free iron from the surface.
- Shot peening: A method used to induce residual compressive stress, helping to improve fatigue strength.
These processes are vital in extending the lifespan of spirol disc springs, thereby reducing the need for frequent replacements and the overall maintenance costs for industries utilizing them.
Applications of Spirol Disc Springs
The applications of spirol disc springs showcase their versatility and significance across different sectors. This section highlights the critical roles these springs play in contemporary engineering, emphasizing the distinct advantages they offer. Their unique design allows for efficient load distribution, reduced space requirements, and effective energy storage. Understanding these applications is essential for anyone involved in mechanical design or material science.
Automotive Applications
In the automotive industry, spirol disc springs find numerous critical applications. Their primary function often includes load support in suspension systems and brake components. The compact design of these springs means they can fit into confined areas, which is vital for modern vehicles that demand optimized space management. Moreover, they provide consistent and reliable force, enhancing the overall safety and performance of vehicles.
- Suspension Systems: They are instrumental in managing vehicle dynamics and ensuring comfort. The dynamic response of cars during acceleration, braking, and cornering can greatly benefit from the properties of spirol disc springs.
- Brake Systems: In disc brakes, these springs help maintain proper clamping force, thus ensuring optimal braking performance. Their ability to absorb shock contributes to stability during operation.
With the ongoing pursuit of lightweight materials in automotive design, the use of spirol disc springs aligns with industry goals to improve fuel efficiency while maintaining safety standards.
Aerospace and Defense Uses
In aerospace and defense sectors, the need for reliable components is paramount. Spirol disc springs are designed to accommodate extreme conditions and loads. They are widely used in various systems, from landing gear to control surfaces.
- Landing Gear Mechanisms: These springs can withstand the significant impact forces during landing, providing essential shock absorption. Their resilient nature helps to enhance the durability and life cycle of critical components.
- Control Systems: In actuators and control surfaces, the precision of spirol disc springs aids in maintaining operational stability. This precision is crucial for avionics systems, where performance under duress is non-negotiable.
Such applications underline not just functionality, but also the potential for innovation. As the aerospace field advances towards increased autonomy and efficiency, the adaptability and strength of spirol disc springs will continue to play a vital role.
Industrial Equipment Integration
In industrial equipment, spirol disc springs integrate seamlessly into various machinery. Their role in achieving operational efficiency cannot be overstated. They are commonly employed in material handling equipment, automated machinery, and electronic devices.
- Material Handling Equipment: In forklifts and conveyor systems, they provide necessary support and energy storage. This enhances the machinery's reliability, leading to increased productivity.
- Automated Machinery: These springs are crucial in robotics applications where compact, yet powerful actuators are necessary. Their design allows for quick reactions to operational demands, proving essential in high-speed environments.
- Electronics: Spirol disc springs are also utilized in various electronic applications, contributing to stability and performance in devices like switches and relays.
The integration of spirol disc springs in industrial applications is a testament to their versatility. Their ability to perform reliably under various stresses and strains further amplifies their importance in the machinery sector.
In summary, the applications of spirol disc springs span critical industries, highlighting the importance of effective design in enhancing functionality and efficiency. Their unique attributes address specific challenges in automotive, aerospace, and industrial sectors, ensuring continued relevance and growth.
Comparison With Other Spring Technologies
The comparison between spirol disc springs and other spring technologies is essential for understanding their unique contributions to various applications. By analyzing coil springs, leaf springs, and reviewing the advantages of spirol disc springs, one can appreciate the nuances present in spring design and performance. This contrasts also aids engineers and designers in making informed decisions on which type of spring to utilize, based on specific mechanical requirements and constraints.
Coil Springs vs. Disc Springs
Coil springs and spirol disc springs serve different functions in engineering applications. Coil springs are typically used in scenarios where tensile strength is paramount. They are efficient in compression and tension, responding well to dynamic loads. However, they also have limitations such as requiring more space to operate effectively.
In contrast, spirol disc springs are compact and can deliver high spring forces in limited areas. Their design permits stacking, which allows for customizable load capacities without significantly increasing horizontal space.
Some key distinctions include:
- Load Transfer Efficiency: Spirol disc springs provide better load transfer, especially in confined spaces.
- Deflection Characteristics: Disc springs exhibit constant spring rates which allow for more predictable deflection under varying loads compared to coil springs.
- Installation Versatility: The disc design offers easier integration into machinery with varying spatial constraints.
Recent Innovations in Spirol Disc Springs
Recent innovations in spirol disc springs represent a critical aspect of this article, as they illuminate the advancements within spring technology. These innovations not only enhance performance, but also broaden the scope of applications significantly. With evolving industry demands and technological growth, understanding these innovations assists professionals in making informed decisions regarding design and material selection. Innovations lead to improved durability, reduced weight, and enhanced functionality, making spirol disc springs more suitable for diverse environments and uses.
Emerging Technologies
The integration of emerging technologies into the design and manufacture of spirol disc springs is pivotal. Key technological advancements involve computer-aided design (CAD) and advanced simulation tools. These technologies drastically improve the design process, allowing for precise modeling of spring behavior under various loads and stress conditions.
- Finite Element Analysis (FEA): This tool allows engineers to visualize how springs will perform in real-world scenarios. FEA helps in optimizing design parameters before physical prototypes are made, saving time and cost.
- 3D Printing: This method allows for rapid prototyping and customization. Engineers can iterate designs quickly and produce complex geometries that were not feasible with traditional methods.
Further innovations in manufacturing techniques, such as automation and robotics, lead to increased efficiency and consistent quality in production.
Smart Materials and Their Potential
The concept of smart materials in the context of spirol disc springs introduces a fascinating realm of possibilities. Smart materials can change their properties in response to external stimuli, such as temperature or pressure. This capability could revolutionize how spirol disc springs are implemented in various applications.
Some potential benefits of smart materials include:
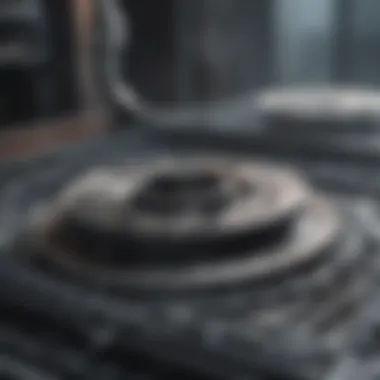
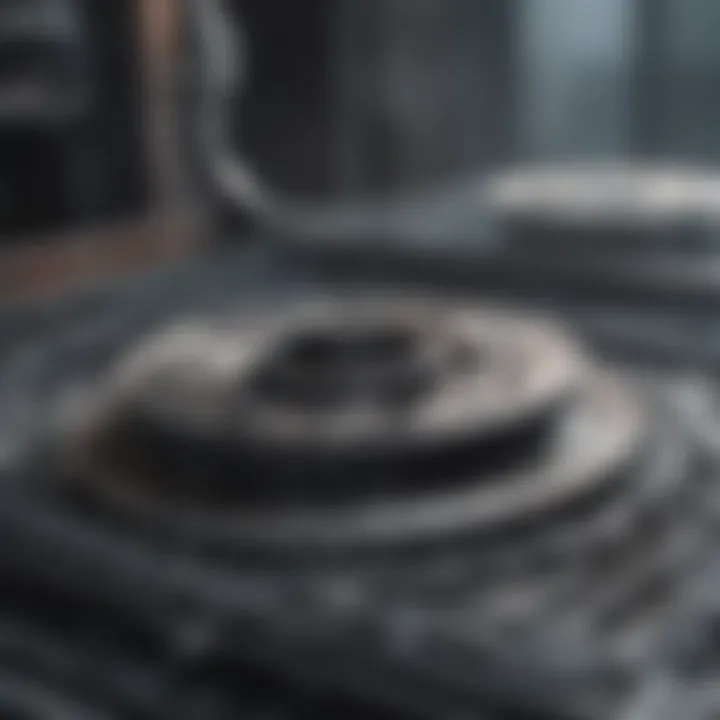
- Improved Performance: By adapting in real-time to varying conditions, smart materials can enhance operational efficiency and resilience.
- Extended Lifespan: The ability to respond to load variations can reduce wear and tear, contributing to longevity in service.
Market interest in smart materials is growing, particularly in industries that prioritize precision and responsiveness. Future research in this field could lead to spirol disc springs that not only meet traditional standards but also adapt intelligently to their environment.
"The future of spirol disc springs lies in the fusion of traditional engineering practices with cutting-edge technologies, creating components that are more efficient and capable of meeting modern demands."
By embracing these innovations, engineers and manufacturers can better address the dynamic needs of modern applications, offering users enhanced solutions that combine utility with advanced engineering.
Customization and Tailoring
Customization and tailoring of spirol disc springs play a pivotal role in enhancing their effectiveness in various applications. Since these components can serve specific purposes in distinct environments, understanding the nuances of their design and functionality is essential. Tailoring the springs involves adjusting parameters such as material selection, dimensions, loading characteristics, and geometrical configurations. Each of these elements can greatly influence the performance and longevity of the springs in real-world applications.
The benefits of customization are numerous. First, bespoke designs can significantly enhance the operational efficiency of the springs. By tailoring spring characteristics to suit specific applications, engineers can achieve optimal performance while ensuring that the components meet stringent safety standards. Beyond performance, tailored solutions also help to reduce waste during production and enhance the cost-effectiveness of projects.
When considering customization, several key factors should be taken into account. Engineers must evaluate the operational environment, including factors like temperature variations and exposure to chemicals. Additionally, load requirements should be analyzed, as different applications can demand various levels of force and deflection. A thorough understanding of these considerations helps in crafting springs that function well in their designated roles.
Bespoke Design Solutions
Bespoke design solutions provide a competitive edge in the production of spirol disc springs. Tailoring springs to unique specifications can address challenges that standard designs may not effectively meet. These custom solutions allow for adjustments in size, thickness, and coil geometry, thereby enhancing the spring's load-bearing capabilities.
Key steps in creating bespoke designs involve:
- Understanding requirements: This includes detailed discussions with end-users to gather insights into specific needs and constraints.
- Prototyping: Developing prototype designs can help in assessing functionality and making necessary modifications before mass production.
- Testing and validation: Ensuring that the custom springs meet performance expectations through rigorous testing is crucial to successful application.
Customization can also extend to aesthetic aspects, where colors or finishes are tailored to align with branding or environmental considerations.
Adjusting Properties for Specific Applications
The process of adjusting properties for specific applications involves tailoring the mechanical characteristics of spirol disc springs to suit particular load conditions and functional demands. Critical parameters such as stiffness, load capacity, and resilience can be varied systematically.
Adjustment methods can include:
- Material selection: Different materials have unique strength and flexibility profiles. Choosing the right material for a spring can enhance its performance against specific loads.
- Geometric changes: Altering the geometric configuration of the spring can improve deflection and stress distribution. This ensures that the spring effectively absorbs energy and returns to its original shape when the load is removed.
- Coating and finishing: Applying protective coatings can enhance wear resistance and reduce environmental impacts on the spring, thus prolonging its operational lifespan.
Understanding these elements contributes to designing springs that not only fulfill the necessary functional requirements, but also adapt to the evolving technology landscape. The right combination of customized features ensures that spirol disc springs are optimized for their intended use.
Future Trends and Perspectives
The evolution of spirol disc springs is closely linked to advancements in various fields such as engineering, materials science, and sustainability practices. Understanding the future trends in spirol disc springs is crucial for industry professionals, as it helps them to adapt to changing demands and continue to innovate.
Evolving Industry Standards
As technology advances, so do the standards governing the design and application of spriols disc springs. Manufacturers must stay aligned with these evolving industry standards to ensure compliance and competitiveness. Standards are often driven by regulatory requirements and market demands for safety, efficiency, and performance. Here are some key considerations:
- Safety regulations are becoming more stringent. Ensuring the reliability of spirol disc springs in various applications is essential for compliance.
- Performance metrics are evolving. The focus is shifts toward longer lifecycle, lower maintenance needs, and overall efficiency improvements.
- International standards are also influential. Manufacturers need to navigate differences in standards across global markets.
By adhering to these standards, industries can benefit from improved product quality and consumer trust.
Sustainability Considerations
Sustainability is an increasingly critical aspect of design and manufacturing. As environmental concerns grow, the need for sustainable practices in the production and application of spirol disc springs becomes paramount. Possible approaches and considerations include:
- Material sourcing: Utilizing recyclable and environmentally friendly materials can significantly reduce the carbon footprint associated with production.
- Manufacturing processes: Adopting energy-efficient manufacturing methods helps lower waste and emissions, aligning with global sustainability goals.
- Lifecycle management: Understanding and optimizing the entire lifecycle of spirol disc springs—from production to end-of-life disposal—can lead to better resource management.
By prioritizing sustainability, manufacturers can achieve not only compliance but also a competitive advantage in a market that increasingly values environmentally conscious products.
Potential Areas of Research
Looking forward, several areas show promise for future exploration and innovation in spirol disc springs:
- Advanced materials research: Investigating new materials that exhibit enhanced fatigue resistance or reduce weight can lead to significant performance improvements.
- Smart technology integration: Development of sensors and smart systems that monitor the performance of spirol disc springs in real-time could enhance reliability and maintenance schedules.
- Simulation and modeling: Improved computational models can facilitate better understanding of stress distribution and response under various loads, leading to optimized designs.
These research areas could pave the way for breakthroughs that can revolutionize the design, application, and efficiency of spirol disc springs across various industries.
The End
In summary, the exploration of spirol disc springs has illustrated their pivotal role in modern engineering. These components, characterized by their unique design and operational mechanics, demonstrate many advantages over traditional spring technologies. The discussion provided highlights specific elements such as material selection, manufacturing processes, and applications across varied industries. Understanding these facets not only enriches knowledge but also informs better engineering practices.
Summary of Key Points
- Design Principles: Spirol disc springs are designed to provide significant load-bearing capabilities while maintaining compact dimensions, making them suitable for space-constrained applications.
- Material Selection: The choice of materials impacts performance and longevity; common materials include high-carbon steel and stainless steel, each suited for differing environmental conditions.
- Applications: Their applications range from automotive systems to aerospace and various heavy machinery, showcasing versatility.
- Recent Innovations: Innovations in material science and manufacturing techniques have enhanced the efficiency and effectiveness of spirol disc springs, leading to performance improvements in many sectors.
"Understanding the mechanics and applications of spirol disc springs can lead to innovative solutions in mechanical design and engineering."
Implications for Industry Practice
The insights derived from this discussion have broad implications for engineering practices. By choosing spirol disc springs tailored to specific application requirements, manufacturers can optimize the performance of their products. Additionally, engineering teams must consider ongoing innovations in materials and manufacturing methods to stay ahead in a competitive landscape. This comprehensive understandings helps in not only achieving higher performance standards but also in promoting sustainability through better material choices.
Professionals must also remain vigilant about the latest industry standards and advancements in research. Continual learning and adaptation will serve to solidify the importance of spirol disc springs in their respective fields, ensuring that they are integrated effectively into future designs.