Understanding Surface Speed in Aluminum Processing
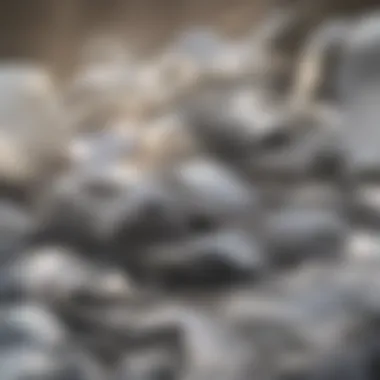
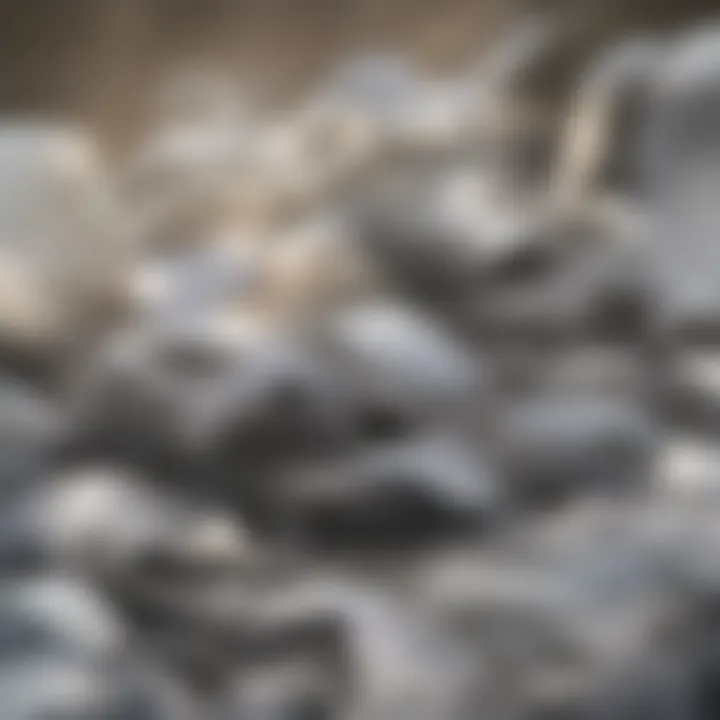
Intro
Understanding surface speed is vital for professionals working with aluminum. In machining, surface speed, which refers to the speed at which the surface of the workpiece moves past the cutting tool, directly impacts efficiency and quality. The significance of this concept is often underestimated. However, recognizing its implications can lead to improved manufacturing processes and reduced tool wear.
This article aims to untangle the complexities surrounding surface speed in aluminum processing, emphasizing its relevance in various industrial applications. By dissecting its definitions and associated factors, we provide a comprehensive overview that will benefit students and professionals alike in the field of material science and manufacturing.
Research Context
Background and Rationale
In the realm of materials engineering and manufacturing, aluminum is one of the most commonly used metals, admired for its lightweight and malleable properties. As industries evolve, the precision in processing aluminum becomes increasingly important. Surface speed plays a pivotal role in determining the overall effectiveness of machining operations. Understanding this concept not only helps in improving productivity but also reduces costs associated with tooling and labor.
Furthermore, with the rise of advanced manufacturing technologies and automation, knowledge of surface speed is becoming essential. Various factors, such as tool geometry, material properties, and machining conditions, all influence the ideal surface speed for aluminum. Thus, this discussion provides a necessary platform for professionals engaged in improving production standards.
Literature Review
Current literature reveals a growing interest in the optimization of surface speed and its direct correlation with machining efficiency. Numerous studies highlight how inappropriate surface speed can lead to increased tool wear and poor surface finishes. The implications of these findings are vast, as they influence overall operational costs and product quality.
Research by various authors indicates optimal surface speed values that vary with different aluminum alloys and machining techniques. Scholars also identify challenges in real-time measurement, pointing towards a need for improved methods in applying surface speed principles effectively.
In summary, the literature establishes a foundation of knowledge essential for mastering surface speed in aluminum processing. This context invites further exploration into the methodologies that drive optimization in industrial applications.
Intro to Surface Speed
Surface speed is a critical factor in machining processes, particularly when working with aluminum. Understanding it allows manufacturers to optimize their operations, improve efficiency, and enhance product quality. In this section, we will highlight key aspects of surface speed and its relevance in the context of aluminum machining.
Surface speed refers to the distance traveled by a cutting tool or workpiece in a specific time frame, often expressed in surface feet per minute (SFM) or meters per minute (MPM). This measurement is crucial for determining the cutting conditions best suited for a specific material, notably aluminum due to its unique properties.
The importance of surface speed in machining aluminum cannot be understated. Correctly setting the surface speed impacts the tool's performance, including its wear rate, life span, and the surface finish achieved on the machined part.
Definition of Surface Speed
Surface speed, simply put, is the linear speed at which the surface of a rotating tool or workpiece moves through the air. The formula to calculate surface speed is:
Surface Speed (S) = π × Diameter × RPM
Where:
- S = surface speed
- π (Pi) = approximately 3.14
- Diameter = diameter of the workpiece in inches or millimeters
- RPM = revolutions per minute
This definition is essential in machining environments, as it affects the cutting operation's overall effectiveness. Knowing how to determine surface speed accurately allows machinists to select appropriate cutting tools and parameters for specific aluminum grades and applications.
Importance of Surface Speed in Machining
Understanding surface speed is not just a theoretical exercise; it has practical applications that significantly impact the overall machining process. Here are some important considerations:
- Tool Wear: The rate of wear on cutting tools increases with improper surface speed settings. Too high or too low settings can cause excessive wear, leading to frequent tool changes and increased costs.
- Machining Efficiency: Appropriate surface speed can enhance productivity. Higher speeds often lead to reduced machining time, although this must be balanced with quality requirements.
- Quality of Finish: Surface speed affects the surface finish quality of the machined part. Optimal speeds contribute to smoother finishes, which are crucial in many applications.
- Heat Generation: Incorrect surface speeds can generate excess heat, potentially damaging both the tool and the workpiece. Managing surface speed helps keep temperatures in check.
- Material Removal Rates: Matching surface speed to aluminum characteristics ensures an efficient material removal rate, vital for competitive manufacturing processes.
In the following sections, we will explore the fundamentals of aluminum processing, factors influencing surface speed, and practical considerations for optimizing machining operations.
Fundamentals of Aluminum Processing
Understanding the fundamentals of aluminum processing is vital to grasp the broader concept of surface speed. Aluminum is a prevalent material in various industries because of its unique properties, such as lightweight nature and excellent corrosion resistance. Processing aluminum efficiently enhances its application in manufacturing, construction, and transportation.
Properties of Aluminum
Aluminum possesses several key properties that make it a favored choice for many applications.
- Lightweight: Aluminum is significantly lighter than many metals, making it ideal for aerospace, automotive, and portable applications.
- Corrosion Resistance: The natural oxide layer formed on aluminum helps it resist rust and corrosion. This property is critical for products exposed to harsh environments.
- Ductility and Malleability: These characteristics allow aluminum to be easily shaped and formed into various designs without fracturing, enhancing its versatility.
- Strength-to-Weight Ratio: Although lighter, aluminum can be alloyed to achieve strength comparable to heavier metals, making it suitable for structural applications.
Common Forms and Uses
Aluminum is available in several forms, each serving specific functions across different sectors. Understanding these forms and their uses is essential.
- Sheets and Plates: Commonly used in manufacturing and construction for walls, roofs, and transport vehicles.
- Extrusions: Used in frames, structural components, and geometric shapes essential for various machinery.
- Castings: Used to create complex shapes, particularly in automotive parts and industrial products.
- Alloys: There are more than 150 aluminum alloys, tailored for specific performance requirements in fields such as aerospace or military applications.
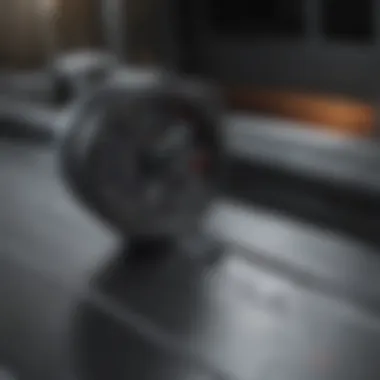
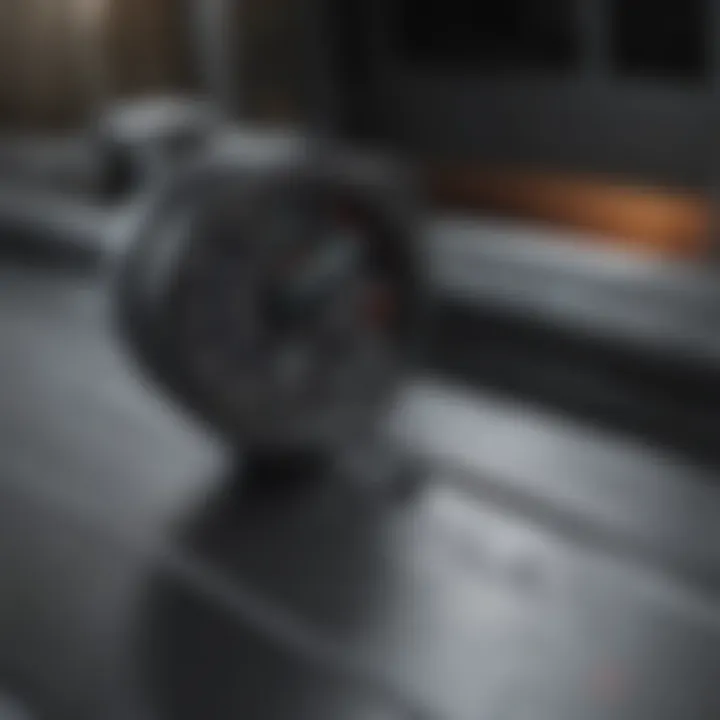
In general, the processing of aluminum and its properties converges at the point of machining. The efficiency of machining operations directly links back to surface speed, which is vital in optimizing performance and tool life.
Factors Influencing Surface Speed
Understanding the factors influencing surface speed is essential for optimizing machining processes involving aluminum. Surface speed can significantly affect the quality of the machining operation, the longevity of tools, and the efficiency of production. Therefore, a thorough understanding of these factors enables manufacturers to achieve specific outcomes and improve overall productivity.
Material Characteristics
The inherent properties of aluminum, such as its hardness, thermal conductivity, and ductility, play a significant role in determining the optimal surface speed. Generally, softer materials allow for higher surface speeds, whereas harder alloys require more cautious handling. The aluminum alloy composition can also influence its machinability. For instance, 6061 aluminum is easier to machine compared to 7075 aluminum due to its lower hardness. This characteristic needs to be assessed during the planning stage to avoid tool wear and ensure uniformity in the final product.
Key considerations about material characteristics:
- Hardness: Softer alloys can typically endure higher speeds.
- Thermal properties: Good thermal conductivity helps dissipate heat, reducing the risk of tool damage.
- Ductility: A more ductile material may resist cracking under high speeds but can create challenges in cutting if not managed properly.
Tool Material and Geometry
The selection of tool material and its geometry also significantly affect surface speed. Tool materials such as carbide, high-speed steel, and ceramic have distinct wear rates and thermal resistances. For example, carbide tools can operate at higher surface speeds than high-speed steel. The geometry, including rake angle, clearance, and cutting edge shape, directly impacts the cutting action and thus can influence the maximum efficient surface speed.
Important aspects to consider:
- Material type: Tool materials with higher wear resistance support higher speeds.
- Geometry: Optimized angles and edge designs reduce cutting forces, allowing for better surface speed management.
- Coating: Some tools have coatings that enhance their performance by reducing friction and increasing tool life.
Machining Environment
The conditions of the machining environment are another critical factor influencing surface speed. Variables such as temperature, humidity, and presence of coolant affect the machining process. Coolant, for example, helps manage heat generation that arises from friction. An inadequately cooled environment can lead to thermal deformation, which can affect dimensional accuracy and tool longevity.
Considerations for a machining environment:
- Coolant usage: Effective cooling helps maintain optimal operating temperatures, enabling higher surface speeds.
- Cleanliness: The presence of contaminants can adversely affect tool life and surface integrity.
- Workpiece fixtures: Properly securing the workpiece reduces vibrations and enhances machining effectiveness, allowing for better control over surface speed.
"Optimizing surface speed not only boosts production efficiency but also extends tool life, creating a win-win scenario for manufacturers."
By addressing these factors and their respective implications, professionals can effectively tailor their machining processes. Doing so ensures that they achieve the best possible outcomes while enhancing productivity and maintaining quality standards.
Calculating Surface Speed
Calculating surface speed is essential in understanding the machining process for aluminum. Surface speed refers to the speed at which the cutting tool engages with the material. This speed significantly influences the efficiency and quality of the machining operation. By calculating the proper surface speed, machinists can achieve optimal performance while minimizing tool wear. This calculation is not only vital for economic reasons but also for maintaining safety during machining operations.
Mathematical Formulas
The formula for calculating surface speed is straightforward and provides vital information for operators. The fundamental equation is:
[ S = \frac\pi D N12 ]\
Where:
- S = Surface Speed (in feet per minute)
- D = Diameter of the cutting tool (in inches)
- N = Revolutions per minute (RPM) of the tool or workpiece.
This formula shows the direct relationship between the diameter of the tool and the speed at which it operates. As the diameter increases, the surface speed will also increase, assuming the RPM remains constant. Conversely, reducing the RPM will decrease the surface speed, which is critical to prevent overheating and excessive wear on tools.
Understanding the correct surface speed increases efficiency and extends tool life.
Units of Measurement
Surface speed is typically measured in various units depending on the industry standards. The most common units include:
- Feet per minute (FPM): Popular in machining operations in the United States.
- Meters per minute (MPM): Commonly used in other parts of the world.
- Surface meters (m/s): This is sometimes used for precision applications.
It is crucial for operators to work within the specified surface speed ranges for aluminum machining. Each material has its recommended operating speeds. For aluminum, higher speeds are generally preferred to promote better chip formation and surface finish.
Proper calculations and understanding of surface speed can lead to better machining practices and improved overall productivity.
Measuring Surface Speed
Measuring surface speed is essential in aluminum processing. Accurate measurements help ensure that machining is efficient and meets material specifications. Understanding how to measure surface speed allows professionals to assess the performance of machining operations directly and comprehensively. This section will present techniques and tools for measuring surface speed alongside data acquisition methods, highlighting their significance in maximizing productivity and maintaining quality.
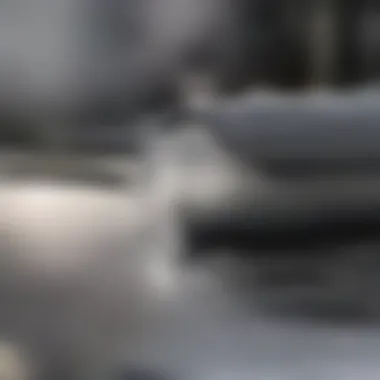
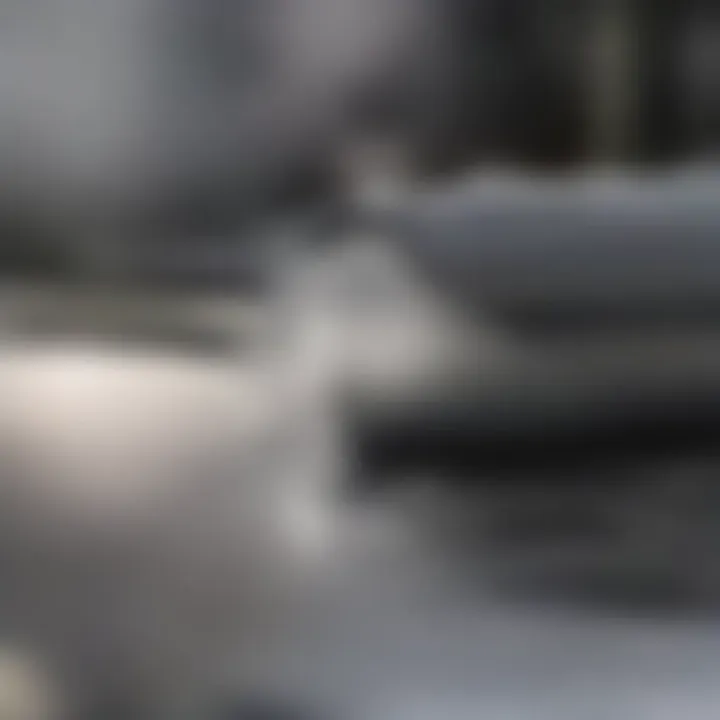
Techniques and Tools
Various techniques are available for measuring surface speed in aluminum machining. Among these, two methods stand out due to their accuracy and reliability:
- Touch Probes
Touch probes connect to a control system and measure the position along the workpiece. The direct contact provides an accurate surface speed reading as the rting point moves across the machining surface. This technique is particularly useful for precision jobs. - Laser Doppler Vibrometry
This non-contact technique uses laser beams to measure surface movement. It calculates surface speed by analyzing the frequency shift of the reflected light. It is effective for surfaces that need high-precision readings, such as those produced in high-speed machining applications.
When choosing a method, consider factors like the required accuracy, the scale of production, and material characteristics. Suitable tools, such as tachometers and encoders, can also play a vital role in taking accurate measurements and maintaining consistency throughout various operations.
Data Acquisition Methods
Data acquisition methods in surface speed measurement involve collecting, analyzing, and interpreting data generated during the machining process. Several techniques integrate with machining systems to optimize results:
- Real-Time Monitoring Systems
These systems provide continuous feedback about the surface speed during the machining process. By integrating sensors and software, operators can adjust parameters in real time to improve overall outcomes. - Statistical Process Control (SPC)
SPC uses data from specific sampling intervals to analyze trends and anomalies. This method helps in making informed decisions by providing the necessary data on surface speed variation and its effects on tool wear and product quality.
Effective data acquisition allows companies to enhance their operational efficiencies and address discrepancies caused by inconsistent surface speeds. Ultimately, measuring surface speed accurately contributes toward achieving optimal machining conditions, reducing waste material, and prolonging tool life.
"Accurate measurement of surface speed is integral to efficient aluminum processing, ensuring that tools operate within specified limits to maintain quality standards."
Surface Speed and Tool Wear
The relationship between surface speed and tool wear is paramount in the machining of aluminum. Understanding this connection is essential for anyone working with this versatile metal. The performance and lifespan of cutting tools depend significantly on the operational surface speed. Surface speed refers to the speed at which the cutting edge of the tool moves across the workpiece surface. If not properly adjusted, it can lead to excessive wear and reduce tool life.
Impact on Tool Longevity
When surface speed is too high, it often leads to rapid tool wear, characterized by abrasive wear, adhesive wear, and thermal fatigue. Abrasive wear occurs due to the friction between the tool and the material being machined. In contrast, adhesive wear happens when the tool material welds to the aluminum, leading to a transfer of material. Finally, thermal fatigue results from the heat produced at high speeds, weakening the tool and making it more susceptible to failure.
In general, maintaining a balanced surface speed is crucial. When set correctly, cutting tools, such as end mills from brands like Kennametal or Iscar, can enjoy longer life spans, reducing the costs associated with frequent replacements. Studies show that optimal surface speeds can extend the life of a tool by as much as 50%, which is significant for both productivity and cost efficiency.
Optimizing Tool Life
To optimize tool life, it is essential to find the right balance between surface speed, feed rate, and depth of cut. Operators can achieve this through a few strategies.
- Selecting the Appropriate Tool Material: Using high-speed steel or carbide tools, for instance, can enhance durability. High-speed steel is generally less expensive and easier to sharpen, whereas carbide tools offer superior hardness and wear-resistance.
- Adjusting Cutting Parameters: Constant analysis of machining parameters can lead to improvements. For example, lowering the surface speed slightly during operations can give tools a new lease on life.
- Monitoring Tool Wear: Regularly inspecting tools for signs of wear helps in making timely adjustments. This can involve switching tools before they become too worn, thus ensuring consistent machining quality.
- Implementing Coolants: Introducing cutting fluids can reduce heat buildup and friction, prolonging tool life significantly. Coolants commonly used are mineral oils and synthetic fluids. These reduce the thermal load on the tool and improve the surface finish of the machined part.
"Optimizing surface speed is not just about efficiency; it’s also about preserving the longevity of tools used in aluminum processing."
Industrial Applications of Surface Speed
Understanding surface speed is essential in the domain of aluminum processing. Industrial applications of surface speed significantly influence efficiency, cost-effectiveness, and the quality of the finished product. When professionals apply the correct surface speeds for machining operations, they can achieve optimal performance, prolong tool life, and ensure precision in finished components.
Utilizing the right surface speed is not just about maximizing output but also about maintaining a balance between operating parameters. This balance minimizes wear on tools and ensures end products meet required specifications while adhering to safety standards.
CNC Machining
CNC (Computer Numerical Control) machining is one of the key industrial processes that benefits greatly from the concept of surface speed. In CNC machining, operators can adjust surface speed based on the type of alloy, tooling used, and desired finish. Properly calculated surface speeds enhance efficiency in production and can reduce cycle times.
Key Considerations for CNC Machining:
- Material Type: Different alloys of aluminum may require different surface speeds to achieve optimal results.
- Tool Geometry: The design of the cutting tools influences how effectively it interacts with the aluminum.
- Programming Parameters: The CNC machines can be programmed to adjust surface speed dynamically, allowing for adaptability in machining.
Turning and Milling Processes
Turning and milling are traditional yet crucial operations in the machining of aluminum. Each process demands specific surface speeds to achieve the best cutting conditions.
In turning processes, surface speed directly affects the cutting tool’s performance. Higher surface speeds can be used for lighter cuts, which leads to better surface finishes and reduces tool wear.
In milling processes, correct surface speed ensures good chip formation and prevents issues like chatter, which can result in surface imperfections.
Surface Speed Impact:
- Tool Wear: Higher surface speeds can lead to increased temperatures, affecting tool life.
- Surface Finish: Achieving the required finish often depends on the correct speed applied during milling or turning.
- Productivity: Optimizing surface speed can significantly enhance production efficiency, reducing operating costs.
Fabrication Techniques
Surface speed plays an essential role not just in machining but also in various fabrication techniques, including bending and cutting processes. In these applications, the speed at which the tool interacts with the aluminum sheet impacts material stress and deformation.
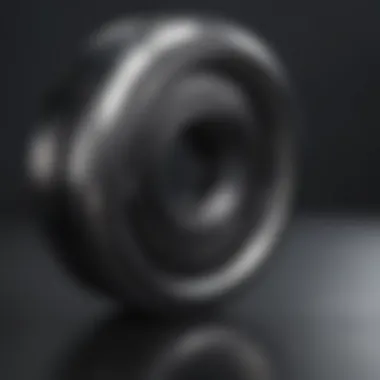
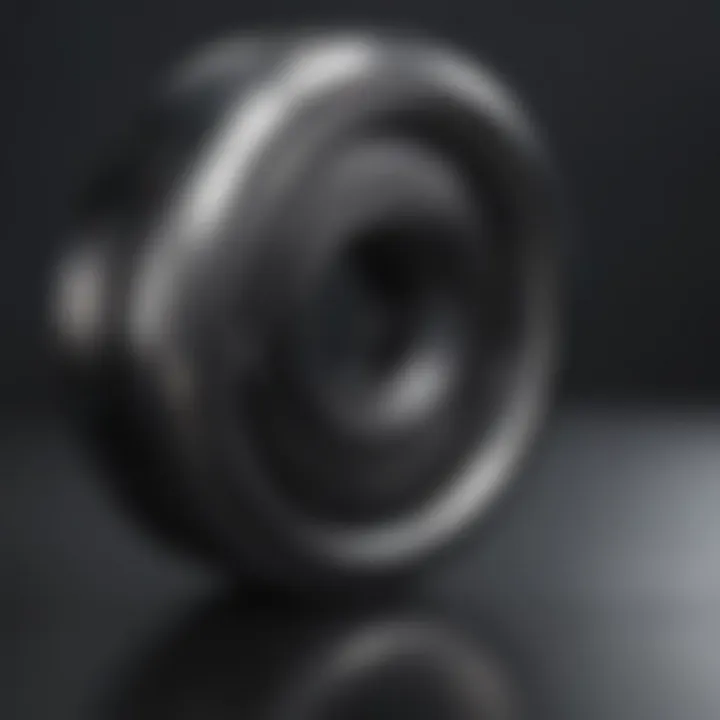
In techniques like laser cutting, ensuring the right surface speed is crucial. Too slow can lead to excessive heat, warping the material, while too fast can impair the quality of cut.
Working with recommended surface speeds also aids in maintaining the metallurgical integrity of the material. For instance, using appropriate surface speeds during welding ensures the welded joints maintain strength and resilience against fatigue.
Summary: Achieving the right surface speed across various industrial applications of aluminum processing is essential for maximizing efficiency, ensuring product quality, and extending tool life. The subtleties involved in how surface speed is applied in CNC machining, turning, milling, and fabrication techniques require both knowledge and practice. As industries evolve, continued focus on surface speed optimization will drive improvements in manufacturing practices.
Common Challenges in Surface Speed Optimization
The process of optimizing surface speed in aluminum machining presents various challenges that must be understood and addressed. It is not simply about adjusting the speed; factors such as durability, quality of output, and efficiency play critical roles. Addressing these challenges can lead to significant benefits, including improved productivity and extended tool life. An understanding of these hurdles is essential for students, researchers, educators, and professionals in machining fields.
High-Speed Machining Risks
High-speed machining can enhance productivity but introduces risks that can quickly offset the benefits. The increase in rotational speeds generates more friction and heat, potentially leading to thermal damage. Overheating can deform the aluminum or the cutting tool, impacting precision. Moreover, the likelihood of tool failure escalates, which can cause tool breakage or even catastrophic machine failures.
Balancing Speed and Quality
Finding the equilibrium between speed and quality is a complex but necessary challenge. Rapid machining may compromise the surface finish of aluminum components, leading to rough edges or dimensional inaccuracies. It is crucial to define acceptable quality metrics before setting machining speeds. Different applications may require different balances. For instance, high aesthetic demands in some industries might call for more gradual speeds. Proper calibration of machinery to maintain quality while optimizing speed can be key.
"A thoughtful approach to surface speed optimization is paramount to maintaining both quality and efficiency in machining processes."
Material Limitations
Lastly, the inherent limitations of aluminum must be recognized. While it is a versatile and lightweight material, its properties can vary greatly depending on the alloy grade. Some aluminum alloys may not withstand high speeds without degrading or distorting. Understanding these limitations is crucial for tailor-making machining strategies that yield the best results without risking material integrity.
Future Trends in Surface Speed Research
The examination of future trends in surface speed research for aluminum processing is a fundamental part of this article. As industries evolve and competition intensifies, the focus on enhancing efficiency and efficacy in machining becomes paramount. Surface speed stands at the center of this transition, particularly in its implications for productivity and quality. Understanding how surface speed interacts with emerging technologies directly impacts production output and cost-effectiveness. This section aims to shed light on those critical progressions and their potential returns on investment.
Innovations in Machining Technology
In recent years, several innovations have emerged in machining technology that have reshaped the landscape of surface speed optimization. These advancements include the development of precision machining tools, enhanced tool materials, and automation technologies.
- High-Performance Cutting Tools: Modern cutting tools made from advanced materials like polycrystalline diamond or cubic boron nitride can endure higher surface speeds without failure, increasing operational efficiency.
- Adaptive Machining Systems: These systems incorporate real-time monitoring of cutting conditions, allowing adjustments to be made on-the-fly. This results in optimized surface speed, which can lead to decreased tool wear and improved workpiece quality.
- Digital Twins Technology: This concept allows for the creation of digital models of the machining process. By simulating different surface speeds, engineers can identify the optimum conditions before actual machining begins. This reduces material wastage and improves overall efficiency.
The integration of these technologies promotes a shift toward more precise control and better outcomes in aluminum processing, thereby signifying a critical trend within this domain.
Sustainability and Efficiency
The relationship between surface speed, sustainability, and efficiency has garnered attention as environmental awareness increases globally. The optimization of surface speed plays a significant role in reducing resource consumption and waste generation. This addresses not just economic pressures but also the urgent need for responsible manufacturing practices.
Key aspects of this trend include:
- Minimized Energy Consumption: By optimizing surface speed, manufacturers can significantly reduce the energy required to process aluminum. Lower energy usage translates directly into decreased carbon emissions, which is crucial in combating climate change.
- Material Waste Reduction: Enhanced surface speed can also improve the yield of finished products. When machining processes are efficient, less material is wasted, which is economically advantageous and supports sustainability goals.
- Recyclability of Components: Focusing on maintaining optimal surface speed can contribute to the long-term viability of recyclable aluminum. This can lead to closed-loop systems, where materials are reused rather than discarded, thus supporting a circular economy.
"Innovative approaches to surface speed optimization lead to better performance, longer tool life, and a positive impact on environmental sustainability."
The ongoing research in these areas promises not only to improve the efficiency of aluminum machining processes but also to align them with global sustainability objectives. As industries continue to adapt, a focus on surface speed will be a guiding principle in shaping the future of aluminum processing.
Epilogue
Understanding surface speed in aluminum processing embodies a complex intersection of various elements that are vital for effective machining practices. This article presents an in-depth analysis of surface speed, highlighting significant factors influencing efficiency and tool longevity.
A clear recognition of key takeaways from this discussion demonstrates the necessity for precision in both calculations and applications. The importance of surface speed cannot be overstated, as it directly impacts material removal rates and overall productivity in machining operations. Moreover, inadequately addressed surface speeds can lead to premature tool wear, adversely affecting quality and increasing operational costs.
In the rapidly advancing field of materials science and manufacturing, the insights gained from this overview can guide professionals in optimizing techniques tailored to specific requirements. With the knowledge on how surface speed can be effectively managed, it becomes easier to strike a balance between speed and quality, fostering better production outcomes.
"A thorough comprehension of surface speed contributes significantly to enhancing machining efficiency and extending tool life."
As aluminum continues to gain significance in various industrial applications, understanding its machining implications will remain invaluable. Continuous research is essential for staying ahead of challenges and harnessing future innovations in this arena.
Summary of Key Takeaways
- Surface speed is crucial for optimizing the machining process of aluminum and impacts efficiency.
- Proper calculations and measurements of surface speed are essential for prolonging tool life and maintaining product quality.
- This knowledge is applicable across various machining techniques such as CNC machining, turning, and milling.
- Understanding the relationship between surface speed and tool wear can lead to improved production outcomes and reduced costs.
The Importance of Continued Research
Continued research in the field of surface speed for aluminum processing is vital for several reasons. First, the advancing technology in machining processes demands more refined and efficient systems. Research can uncover new methodologies that enhance the understanding of optimal surface speed ranging for different operations and materials.
Secondly, the sustainability aspect surrounding manufacturing processes must not be overlooked. Innovations may lead to breakthroughs in reducing waste and energy consumption while using aluminum in various applications. As industries adapt to more stringent environmental regulations, ongoing exploration in this area will be paramount.
Finally, collaboration among researchers, educators, and industry professionals serves to share insights and address gaps in current knowledge. By fostering a culture of inquiry and dialogue, the industry can ensure that surface speed optimization remains at the forefront of machining strategies, ultimately resulting in better efficiency and performance in operations.