Water Jet Cutting of Stainless Steel: Techniques and Innovations
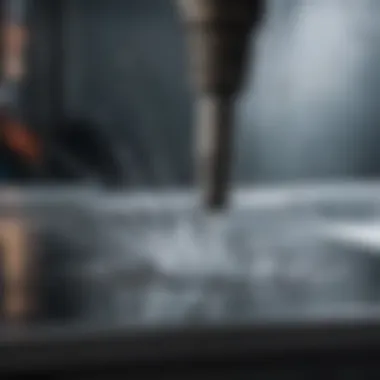
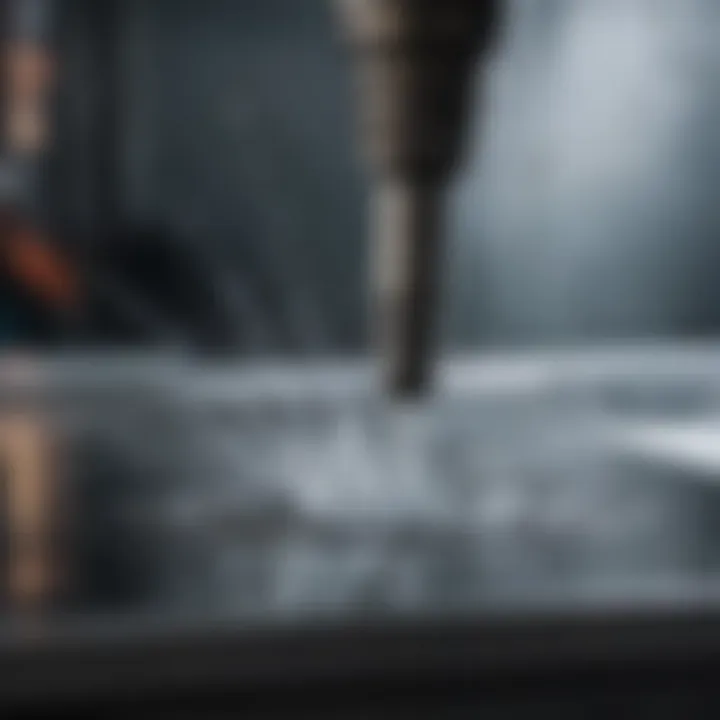
Intro
Water jet cutting has emerged as a noteworthy technique in the realm of manufacturing and material processing. Particularly with stainless steel, it demonstrates exceptional performance that traditional cutting methods often struggle to match. Understanding how this technology works, its myriad applications, and the innovations that continue to reshape its course can be crucial for those navigating the industry, whether they’re students, researchers, or seasoned professionals.
Let's delve into the finer points that make water jet cutting stand out, beyond merely its mechanics. This exploration will also take a closer look at the methodologies employed, supported by relevant studies and practices from industry leaders who have mastered the craft.
Research Context
Background and Rationale
Water jet cutting isn’t just a passing trend—it’s a transformative technique that leverages the power of high-pressure water to execute clean and precise cuts. The method originated in the 1930s and has since evolved to become a mainstay in various sectors like aerospace, automotive, and even artistic applications. The rationale for utilizing water jets, especially on materials like stainless steel, lies in several key advantages such as reduced thermal distortion, minimal material waste, and the capability to cut complex shapes without the need for secondary operations.
One can clearly see how industries have turned towards this technology to improve efficiencies and maintain competitive edges in highly demanding markets.
Literature Review
The extensive research surrounding water jet cutting indicates a consistent trend toward refinement in techniques and applications. A variety of studies have been documented in reputable journals, showcasing experiments with cutting parameters, abrasives, and even eco-friendly practices. For example, research published in Journal of Materials Processing Technology outlines how varying water pressure affects the kerf width and overall cut quality. This kind of information can often be sidestepped by those new to the field, making it all the more critical for practitioners to stay updated.
In addition, case studies demonstrate successful implementations. One standout instance is the use of water jet technology by NASA for cutting complex shapes in aerospace components, illustrating not only the capabilities of this method but also its relevance in high-stakes environments.
Through this backdrop of engagement and discovery, we can further appreciate the significance of water jet cutting in today’s manufacturing landscape. In subsequent sections, we’ll dissect how the methodology unfolds, shedding light on various techniques and their applicability in real-world settings.
Prelims to Water Jet Cutting
Water jet cutting has emerged as a pivotal technology in industrial fabrication, particularly for materials like stainless steel. As industries move towards more precise and efficient methods of fabrication, understanding water jet cutting becomes essential for any professional or researcher involved in material processing. This section lays the groundwork by examining what water jet cutting is, tracing its historical journey, and emphasizing the significance of its role in modern manufacturing.
Definition of Water Jet Cutting
Water jet cutting is essentially the use of high-pressure water, often mixed with abrasives, to slice through materials. Picture a river flowing with enough force to carve through rock—that’s the basic idea here. The core mechanism relies on a focused stream of water that, when propelled at speeds exceeding 2,500 feet per second, can effortlessly cut through thick metal sheets, including stainless steel. Its ability to cut intricate shapes without distorting the material makes it an attractive option in varied applications. This precision is one of the key motivations for businesses to adopt this method over others.
In technical terms, a water jet cutter uses a nozzle to create a narrow jet of water, where pressures can reach up to 90,000 pounds per square inch! This makes it capable of producing precise cuts with minimal kerf, or the width of material removed during the cutting process. The result? Clean edges with little to no thermal deformation, preserving the integrity of the material.
Historical Development
The saga of water jet cutting dates back several decades, but its real evolution took shape in the late 20th century. In the 1930s, the concept was simple enough—a stream of water could erode materials—yet it was not until the 1970s that technological advances began to exploit this principle on a commercial scale. Companies started using water jets for cutting softer materials, but it wasn’t until the introduction of abrasive water jet technology that the method gained traction in cutting tougher materials like metals.
Looking back at the developments, the pioneering efforts of researchers motivated significant investments into enhancing cutting technology. By the time the 1990s rolled around, manufacturers began to recognize water jet cutting as a viable alternative to traditional methods like laser cutting. This spurred innovations that improved both the efficiency and reliability of the process. Today, with ongoing advancements in robotics and software integration, water jet cutting continues to evolve, solidifying its place in various industries.
"Advancements in water jet cutting are not just about capability—they're about redefining how we think about precision manufacturing."
This brief glimpse into the definition and historical backdrop of water jet cutting sets the stage for a deeper exploration of how this technology operates and the breadth of its applications in modern manufacturing. The journey from its early conceptualization to its current sophisticated form illustrates not just a technological evolution but also a crucial shift in technique that has major implications for various industries.
Mechanics of Water Jet Cutting
Understanding the mechanics of water jet cutting is essential for anyone seeking to grasp how this innovative technology operates, especially when it comes to stainless steel. At its core, water jet cutting utilizes a concentrated stream of water, often mixed with abrasives, to slice through materials. This process stands out in many respects, primarily due to its versatility and precision. It’s like having a Swiss Army knife for industrial applications.
Formation of Water Jet
Water jet cutting begins with the formation of the actual jet, which is often considered the lifeblood of the whole process. High-pressure pumps typically generate water jets at pressures upwards of 60,000 psi. The water is forced through a tiny orifice, generally measuring around 0.01 inches in diameter. This narrow passage causes the water to accelerate drastically, transforming it into an extremely fine and focused stream.
When a water jet exits the nozzle, it takes on a narrow cross-section, sometimes perceptibly invisible to the naked eye. This is pivotal as a well-formed jet ensures greater cutting efficiency. If you think about it, it’s all about directing energy efficiently – the sharper the jet, the less energy lost to friction and turbulence. A properly fashioned water jet not only enhances efficacy but plays a significant role in achieving cleaner edges on stainless steel.
Abrasive vs. Pure Water Jets
Water jet cutting can be generally divided into two distinct categories: abrasive and pure water jets. Each has its unique features and applications.
- Pure Water Jets: These utilize only high-pressure water, making them best suited for softer materials like rubber or foam. While they can operate effectively, they often struggle with tougher substances like stainless steel.
- Abrasive Water Jets: These leverage a mixture of water and abrasives — usually garnet particles — to cut through harder materials. This hybrid approach can easily slice through stainless steel with unparalleled precision. On a basic level, the introduction of abrasives into the water jet enhances its cutting power significantly.
Each choice brings its own merits, so selecting between them often comes down to the thickness of the target material and the desired outcome. In the realm of stainless steel cutting, abrasive jets reign supreme due to their unmatched capability.
Pressure Requirements
Pressure is the driving force behind the effectiveness of water jet cutting. The pressure to which the water is subjected is critical in determining the process’s success. Generally, pressures in the range of 30,000 to 90,000 psi are commonplace, with higher pressures yielding more profound cuts and faster processing times.
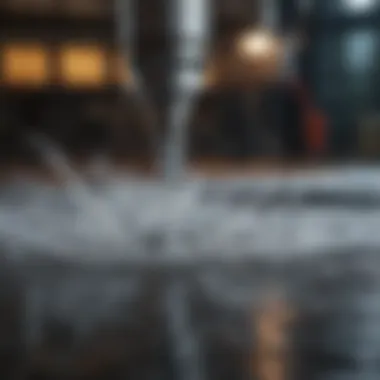
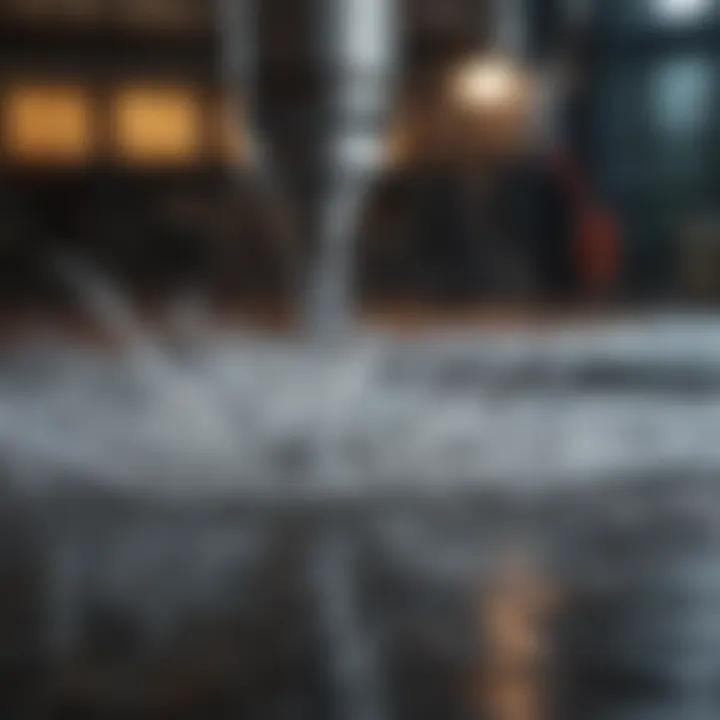
This pressure not only affects the cutting speed but also impacts the quality of the finish. Higher pressures facilitate deeper penetration into materials – think of it like a hot knife through butter: the more heat (or in this case, pressure) you apply, the easier it is to slice through any resistance. Additionally, the pressure must be well-managed to avoid any unwanted burrs or jagged edges on the stainless steel.
"The amount of pressure applied in water jet cutting is truly the crux of achieving both precision and speed. It’s not just about cutting through material; it’s about cutting it right."
In summary, understanding the mechanics behind water jet cutting can significantly benefit practitioners in the field. The art of creating a precise water stream, deciding between pure or abrasive jets, and comprehending the vital role of pressure lays a strong foundation for mastering this technology. This knowledge is indispensable for those striving to optimize their cutting processes in industries ranging from aerospace to design.
Advantages of Water Jet Cutting Stainless Steel
Water jet cutting technology presents a wealth of advantages when it comes to working with stainless steel. This method stands out for its ability to deliver precision, retain material integrity, and offer versatile techniques. In this section, we will delve into these key benefits, which make water jet cutting an essential process in various industries.
Precision and Accuracy
Water jet cutting is renowned for its impressive precision and accuracy in shaping stainless steel. With tolerances as tight as 0.001 inches, manufacturers can create intricate designs with striking detail. This level of accuracy is largely achieved through computer-controlled cutting heads, which follow predetermined paths meticulously. The narrow kerf width of the water jet contributes to minimizing waste and maximizing resource efficiency. Moreover, complex geometries that would typically be difficult—if not impossible—to achieve with traditional cutting methods are now routine with water jets.
In practical terms, consider a situation where you need to create custom parts for a precision-engineered machine. Using water jet cutting enables you to produce parts that fit perfectly without the need for extensive post-processing, unlike methods that might compromise the dimensional accuracy due to thermal deformation.
"Precision is the bedrock of high-quality production—water jet cutting exemplifies this principle in stainless steel fabrication."
Material Integrity Preservation
One of the standout features of water jet cutting is its capacity to preserve the integrity of materials. Traditional cutting methods often generate excessive heat, leading to warping or altering the metallurgical properties of stainless steel. However, water jet cutting operates at relatively low temperatures, effectively eliminating the heat-affected zone that can compromise material quality.
This capability is particularly crucial when working with aerospace components, where even minor defects can have catastrophic consequences. The method’s cold cutting action ensures that the mechanical properties of stainless steel remain intact, allowing for high performance in demanding applications. The fact that water jet cutting produces minimal burrs and surface stress also aids in maintaining surface quality, which is paramount in industries requiring stringent standards.
Versatility in Cutting Techniques
Water jet cutting’s versatility is yet another advantage that appeals to many sectors. The technology can cut through various materials, from metals to plastics to glass, using either pure water or an abrasive mixture. This flexibility allows for creative approaches, whether in art and design or high-precision industrial applications.
For instance, when designing architectural features, artists can leverage the unique capabilities of water jet cutting to explore intricate patterns that blend functionality with aesthetics. In contrast, engineers can utilize the same technology for cutting robust components needed in machinery.
Additionally, the ability to switch between cutting techniques is valuable. You can adjust parameters like pressure and speed seamlessly to optimize cutting based on material thickness or type. This adaptability highlights the cutting-edge nature of this technology while showcasing its relevance in both high-tech and creative industries.
In summary, the advantages of water jet cutting stainless steel—precision, material integrity preservation, and versatility in cutting techniques—make this process a vital element in modern manufacturing and beyond. The exploration of these benefits not only highlights its importance but also underscores the transformative power of water jet cutting within various industries.
Applications in Industry
The sphere of water jet cutting in the industry is vast, functioning across various sectors where precision and adaptability are crucial. Water jet cutting stands out for its ability to manipulate materials with utter precision while preserving the chemical and structural integrity of the material. For stainless steel, a widely used alloy in construction, aerospace, and artistic design, this technology has proven to be invaluable. By examining its applications in these key sectors, we reveal the compelling advantages and considerations that water jet cutting offers.
Aerospace Applications
In the aerospace industry, the demand for lightweight yet durable materials is paramount. Water jet cutting allows for intricate designs that do not compromise the strength of stainless steel components. This is especially important in sectors such as jet engine manufacturing and component creation for spacecraft. The ability to cut materials without introducing heat dislocation means that parts can withstand the intense conditions they face.
Matte finish or polished edges produced by water jet cutting can also contribute to aerodynamic efficiency in various components. Moreover, shorter lead times and decreased waste during fabrication directly impact operational efficiency and bottom lines. Thus, companies in aviation find themselves utilizing water jet technology not just for its capabilities but also to remain competitive in a rapidly evolving market.
Construction Sector
Turning to the construction sector, water jet cutting has become a go-to method for executing clean cuts in stainless steel structures. With the construction of skyscrapers and bridges, the precision that water jet cutting provides can translate into safer and more architecturally sound designs. The ability to work with large sheets of stainless steel, creating precise angles and intricate patterns, is crucial during the fabrication of various components such as girders and frames.
Additionally, the ability to cut complex shapes means less waste generated during the process, promoting economic and environmental sustainability. For builders and architects, this method not only accelerates project timelines, but also offers considerable flexibility, adapting to the changing demands of designs without the need for extensive rework. In a field where every second and every cut counts, water jet technology represents a significant leap forward.
Art and Design
Lastly, the world of art and design has found a passionate ally in water jet cutting technology. Artists appreciate the opportunity to manipulate stainless steel with precision that traditional methods cannot match. From creating sculptures to intricate wall designs, artists can produce pieces that stand out both in aesthetic value and in structural integrity.
Moreover, custom signage and installations are being produced at an increasing rate using this technology. The clean edges and complex geometries allow for unique visual expressions, transforming design concepts into reality. The versatility to work with different thicknesses and textures of stainless steel gives artists and designers a creative edge that fuels innovation in contemporary art.
Water jet cutting opens doors to creativity, merging artistry with engineering finesse.
Recent Innovations in Water Jet Technology
In the realm of manufacturing and material processing, recent innovations in water jet technology have made waves—no pun intended. These advancements not only bolster efficiency but also enhance the overall cutting capabilities of stainless steel. Finding ways to optimize this technology allows industries to adapt to ever-changing demands while maintaining a focus on precision and sustainability.
Automation and Robotics
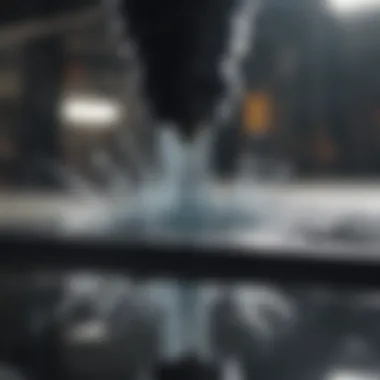
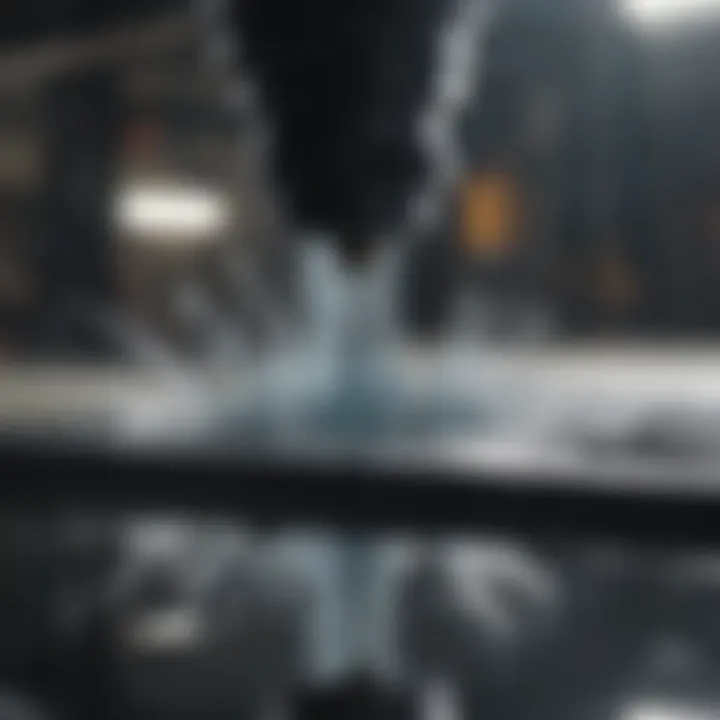
The introduction of automation and robotics in water jet cutting has redefined what is possible in this sector. Automated systems streamline operations, reduce human error, and improve safety on the job floor. With robotic arms performing the cutting process, tasks that were once tedious and time-consuming can now be completed with remarkable speed and accuracy. These automated systems are designed to work continuously, which means they can produce intricate cuts without the fatigue that a human operator might experience.
Some precise advantages include:
- Efficiency: Automated water jet systems can maintain consistent speeds and pressures, ensuring that every cut remains uniform.
- Flexibility: Robots equipped with programmable software can easily switch between different cutting patterns or materials, enhancing their adaptability to various projects.
- Cost Reductions: Although the initial investment in robotic technology can be substantial, the long-term savings from decreased labor costs and reduced material waste can be quite significant.
Moreover, advancements in sensors and AI allow for real-time adjustments during the cutting process. This tech promises to enhance the quality of cuts, preserving the integrity of the stainless steel and reducing the need for secondary finishing processes. By incorporating precision robotics into the cutting technique, industries are also noticing a decrease in downtime, making production lines leaner and leaner.
Software Developments for Cutting Efficiency
Accompanying automation is the surge in software developments aimed at maximizing cutting efficiency. Innovative programs analyze various factors—such as material thickness, jet pressure, and type of abrasive material used—to determine the optimal settings for each cutting job. This data-driven approach not only streamlines the process but also can significantly reduce waste.
Key features of modern cutting software include:
- Parametric Design Integration: This allows engineers and designers to import complex geometric designs directly into the cutting software, minimizing the time spent on manual input.
- Simulation Capabilities: Before the actual cutting begins, the software can simulate the cutting process, helping to predict challenges and refine settings for the best outcome.
- Maintenance Alerts: Advanced software can monitor the performance of the water jet system, notifying operators of necessary maintenance and reducing the risk of unexpected downtime.
As we can see, these innovations in both automation and software development are not just enhancing the efficacy of water jet cutting but also gearing the industry toward a more sustainable future. With an eye on environmental impacts, manufacturers are finding new ways to minimize water usage and manage waste effectively.
"Innovations in water jet technology illustrate how the industry blends traditional cutting techniques with modern advancements to meet today’s demanding manufacturing environment."
This evolution of water jet cutting technology stands as a beacon for what is possible when creativity meets engineering—paving the way not just for enhanced production but also for a sustainable future. Understanding these innovations is crucial for anyone involved in the field, as they represent the cutting-edge trends that are likely to shape the landscape of manufacturing for years to come.
Environmental Considerations
Water jet cutting has garnered attention not only for its precision but also for its environmental merits compared to traditional cutting methods. This technology, known for its clean cutting capabilities, offers significant benefits that must be taken into account in discussions surrounding manufacturing processes. Understanding these environmental considerations allows industries to gauge the long-term sustainability of their operations.
Water Usage and Conservation
Utilization of water in cutting processes might seem counterintuitive given global concerns over water scarcity. However, water jet cutting often uses recycled water, which reflects a proactive approach to resource management. Recycling water reduces waste and lessens the demand for fresh supplies, embodying efficient practices that industries should adopt.
For example, many modern systems incorporate filtration processes that enable the reuse of cutting water, enabling an efficient cycle rather than a simple discard. The environmental impact thus is cut down substantially as this helps save both water and energy.
Additionally, certain technologies allow for the optimization of the water volume used during the cutting process. By adjusting the pressure and flow rate, companies can fine-tune water usage without sacrificing cutting efficiency. Prospective business owners should weigh these practices while considering investments in water jet technology, as this not only upholds corporate responsibility but can also enhance organizational reputation.
Waste Management Practices
Having sustainable waste management techniques in place is vital when dealing with water jet cutting. The cutting process produces various residual materials, including abrasive garnet particles and metal shavings. A savvy approach to handling these wastes is imperative.
Efficient disposal or recycling systems are often established to handle these materials. For instance, garnet abrasives can be collected, cleaned, and reused in subsequent cutting jobs, significantly reducing the demand for new materials and minimizing landfill contributions.
Furthermore, many waterjet facilities consider using specialized containers or systems that segregate different waste types, making the recycling process easier and more effective.
"In the world of cutting technology, it’s not just about what you cut, but how you cut it and what happens to the leftovers. Waste matters, and good habits can lead the way to a greener future."
Additionally, an aligned philosophy on waste management can also foster a culture of sustainability within the organization. Training employees on proper disposal and recycling can lead to heightened awareness around environmental stewardship, paving the path for more eco-friendly operational practices.
By focusing on innovative waste management practices, the water jet cutting industry stands at a crossroads where it can reinforce its commitment to sustainability while minimizing its ecological footprint. The mutual interest of environmental conservation and technology advancement can lead to better methodologies in the years to come.
Challenges in Water Jet Cutting
Understanding the challenges in water jet cutting is crucial for anyone involved in manufacturing and industrial applications. While it's a formidable technique for cutting stainless steel, several factors can influence its effectiveness and adoption. Specifically, cost implications and technical limitations are two main concerns that must be carefully assessed. These challenges not only affect operational efficiency but also the overall viability of water jet cutting as a competitive option in diverse markets. Let's delve into these specific difficulties.
Cost Implications
When looking at water jet cutting technology, the initial investment can be daunting. Setting up a water jet cutting system often involves substantial capital outlay on equipment and installation. The machinery itself comes with a hefty price tag, and potential buyers need to weigh that against long-term benefits. Here are several key considerations regarding the costs:
- Equipment Purchase: A high-quality water jet machine like the Omax or Flow Waterjet can easily range into six figures. While it offers precision and versatility, it isn't pocket change.
- Maintenance and Running Costs: Regular maintenance is crucial to ensure the longevity of the machinery. Replacement parts, especially consumables like nozzles and garnet (abrasive material), can add up quickly.
- Skilled Labor: Operating water jet cutting systems requires trained personnel, and that’s another cost layer. Finding skilled workers who understand the intricacies of the system can be like looking for a needle in a haystack.
Despite these challenges, many businesses find the trade-off worthwhile. Once the machine is operational, the efficient cutting process can often lead to reduced waste, making it a cost-effective option in the long run. Still, though, figuring out if it suits your business's financial landscape is essential.
Technical Limitations
While water jet cutting presents a range of advantages, it is not without its technical limitations. Understanding these limitations can help firms make more informed choices about whether this cutting method aligns with their production needs. Here are key technical challenges to consider:
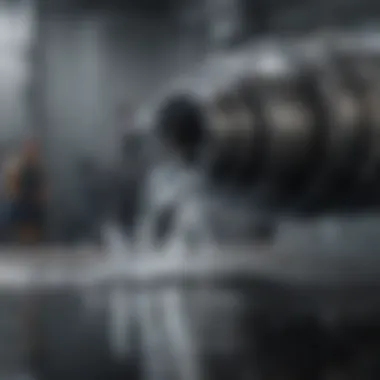
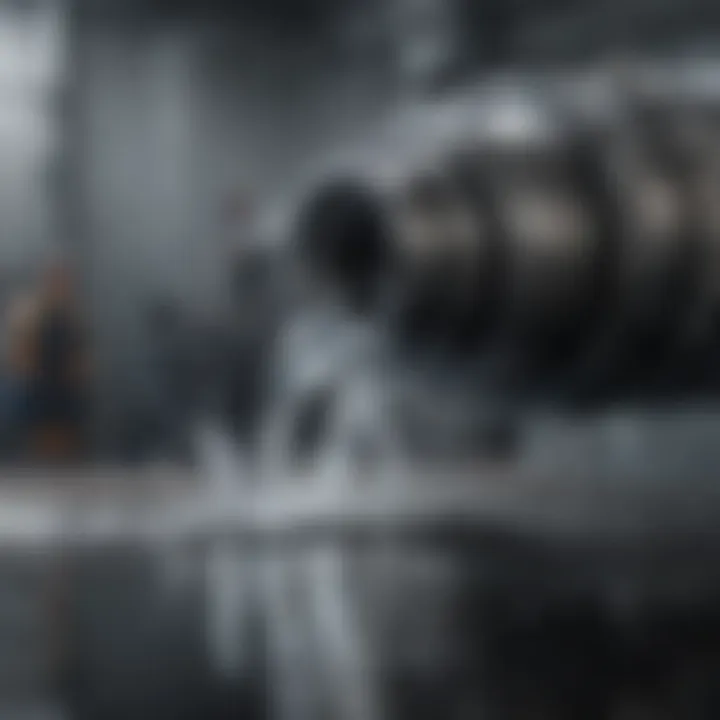
- Thickness Limitations: Water jet cutting, while powerful, has its limits regarding material thickness. Cutting through extremely thick stainless steel can sometimes result in a lack of precision or, worse, operational breakdown.
- Speed of Cutting: Compared to laser cutting or plasma cutting, water jet technology may be slower for certain applications. This discrepancy can lead to longer production times in high-demand situations.
- Quality Trade-Offs: If the cutting parameters are not meticulously calibrated, the final finish may not meet the desired standards. The possibility of rough edges or burrs can necessitate additional finishing processes, which adds time and cost.
"Navigating the waters of water jet cutting requires a good grasp of its limitations and intricacies."
These technical challenges should never be overlooked. They play a significant role in determining whether water jet cutting is the right solution for particular projects, especially in sectors where precision and speed are vital. By being aware of these issues, businesses can devise strategies to mitigate them and harness the full potential of water jet technology.
Future Trends in Water Jet Cutting
The future of water jet cutting is a compelling subject to explore, particularly when applied to stainless steel. As industries evolve and technology advances, staying abreast of these trends is crucial for manufacturers and researchers. This section will look into the integration with other technologies and sustainability advancements, both key areas that could significantly enhance water jet cutting's role in various sectors.
Integration with Other Technologies
The integration of water jet cutting with other advanced technologies is gaining traction and reshaping the industry landscape. For instance, the synergy between water jet cutting and computer numerical control (CNC) systems allows for increased precision and speed in manufacturing processes. By merging these two technologies, operators can pre-program complex cutting patterns, thus minimizing human error and maximizing output efficiency.
Moreover, we see a trend towards integration with additive manufacturing techniques. This hybrid approach can leverage the strengths of both processes, making it possible to achieve intricate designs that were previously challenging to produce. For instance, combining water jet cutting with 3D printing can lead to the creation of customized parts that meet specific engineering requirements, particularly in fields like aerospace and automotive.
“The future of manufacturing lies in the ability to adapt and combine disparate technologies for enhanced performance.”
In this regard, bigger focus on automation and robotics is changing how water jet machines are operated. Automated systems can carry out precise cuts with minimal human intervention, which is not just safer but also opens up more opportunities for mass production with consistent quality.
Sustainability Advances
Sustainability is not merely a buzzword; it's becoming a crucial consideration in all manufacturing processes, including water jet cutting. Cutting through metal generates waste and consumes resources, thus, advancements are underway to make this process more eco-friendly. Companies are now investing in technologies that reduce water consumption significantly without compromising cutting quality.
Water recycling systems, for instance, allow for the reuse of water used during the cutting process. By implementing closed-loop systems, manufacturers can cut down on fresh water usage and minimize waste. This not only is beneficial for the environment but also reduces operational costs over time.
Additionally, the introduction of biodegradable abrasives presents another trend in sustainability. Traditional abrasive materials can be harmful to the environment, but new alternatives are emerging that are less detrimental. These innovations reflect a shift in mindset where environmental responsibility is now an integral part of business strategies.
Comparison with Traditional Cutting Methods
In the realm of cutting technologies, water jet cutting stands out as a contemporary approach that offers unique benefits compared to traditional methods such as laser, plasma, and mechanical cutting. Understanding how water jet cutting compares with these methods is crucial for making informed decisions in material processing.
Water jet cutting utilizes a high-pressure stream of water, often mixed with abrasive substances, to efficiently slice through materials like stainless steel. This technique not only preserves the material's integrity but also enhances precision in cuts. In contrast, traditional methods can sometimes lead to thermal distortion or warping due to heat generated during the cutting process.
Cost-Effectiveness Analysis
When evaluating the cost-effectiveness of water jet cutting versus traditional cutting methods, several aspects merit consideration.
- Initial Investment: Water jet cutting systems can require higher up-front costs as they are complex machines needing specialized technology. However, many manufacturers find that the return on investment is favorable over time.
- Operational Costs: Water jet cutting generally has lower operating costs since it does not consume large amounts of energy like plasma or laser cutters. The water itself is relatively inexpensive, and abrasive materials for cutting can be sourced economically.
- Material Waste: Traditional cutting methods often produce more waste due to the nature of their cutting processes. For example, laser cutting may result in kerf losses, while mechanical cutting can generate scrap. Water jet cutting, on the other hand, offers a tighter kerf and reduces overall waste, making it more eco-friendly and cost-effective in the long run.
- Maintenance Costs: The maintenance of water jet cutters can be less taxing on finances than that of traditional systems, with fewer consumable parts requiring replacement.
This cost analysis indicates that while initial hardware costs might give some pause, the ongoing savings in operational and material costs often make water jet cutting a financially savvy choice for many industries.
Quality of Finish
The quality of the finish achieved through different cutting methods can greatly influence the final application of the parts produced. Water jet cutting delivers unparalleled advantages in this area, specifically concerning stainless steel.
- Edge Quality: Unlike traditional cutting methods that might leave a rough edge or require secondary operations for smoothing, water jet cutting tends to produce clean, burr-free edges. This results in a less labor-intensive post-processing phase, saving both time and costs.
- Heat-Affected Zone: Water jet cutting minimizes the heat-affected zone, reducing the risk of warping and altering material properties that can occur with thermal cutting processes. Typically, materials cut by water jets retain their original mechanical properties, an important factor for many applications, particularly those requiring precision.
- Precision: The accuracy facilitated by water jet cutting often allows for intricate designs not easily achievable through more traditional methods. This is especially beneficial in fields like aerospace or art, where detail matters a great deal.
The precision and finish of water jet cutting can elevate the quality of finished products to new heights, satisfying the demands of even the most discerning clients.
In summary, when weighing the comparison between water jet and traditional cutting methods, there’s much to consider. Cost-effectiveness and superior quality are substantial factors prompting industries to adopt water jet technology, making it a wise choice for both short-run and production-scale cutting needs.
Closure
The topic of water jet cutting, especially in the context of stainless steel, holds significant importance in today’s industrial and technological landscape. This cutting method is a game-changer for various sectors, providing unparalleled precision and versatility while maintaining the integrity of the material. As explored throughout the article, water jet cutting is not just limited to aesthetic finishes; it plays a crucial role in enhancing productivity and efficiency in manufacturing processes.
Summarizing Key Points
In summary, several key aspects underscore the relevance of water jet cutting in the modern age:
- Precision and Accuracy: This technology allows for intricate cuts without the distortion common in other methods, which is essential for high-stakes industries like aerospace and automotive.
- Material Integrity Preservation: One of the foremost benefits is the ability to cut stainless steel without altering its structural properties, crucial for high-quality applications.
- Environmental Considerations: Unlike some traditional methods, water jet cutting produces minimal waste and can be more eco-friendly, aligning with global sustainability efforts.
- Innovations in Technology: The integration of automation and advanced software has made water jet cutting more efficient, allowing for complex designs not previously possible.
"Water jet cutting proves that modern technology doesn’t have to come at the expense of material quality or environmental responsibility."
Call for Further Research
While the advancements in water jet cutting technology thus far are impressive, there remains an area ripe for exploration: the merging of water jet technology with other cutting-edge technologies. Future studies could delve into:
- Combining Water Jet with Laser Cutting: Investigating how these two methods can complement each other could yield innovative applications.
- Enhancing Automation: Pushing the boundaries of what's possible with robotics and AI in the water jet cutting space warrants thorough research.
- Eco-innovation in Water Management: Understanding how to further reduce water consumption and improve recycling processes within this cutting technique is essential for sustainable practices.