Zinc Coating Paint: Applications and Benefits Explored
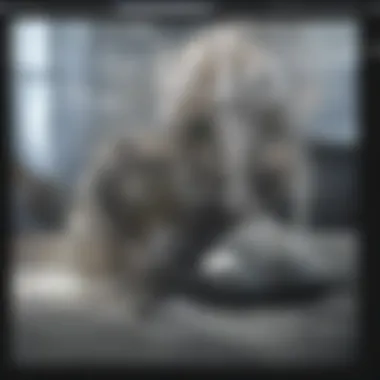
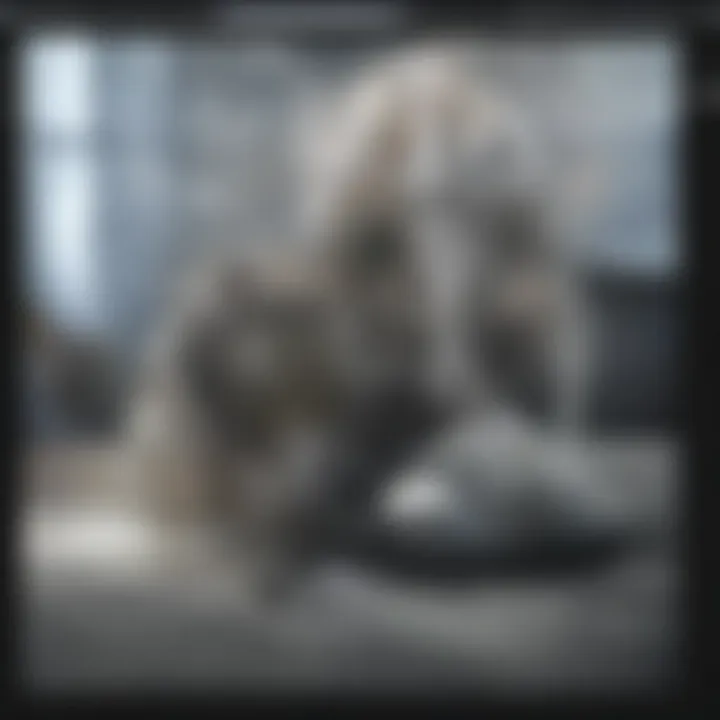
Intro
Zinc coating paint is a specialized material widely recognized for its effectiveness in providing corrosion resistance. The understanding of its properties and applications is essential for professionals across numerous industries. As the demand for durable and maintenance-free materials continues to grow, zinc coating paint has emerged as a leading solution in both industrial and commercial contexts.
This section aims to elaborate on the research context surrounding zinc coating paint, offering insight into why it has become crucial in today’s market.
Research Context
Background and Rationale
The necessity for protective coatings stems from various environmental challenges that metals face, particularly from moisture, chemicals, and extreme weather conditions. Zinc, when used as a coating, offers cathodic protection, which significantly enhances the lifespan of materials. The unique properties of zinc coatings act to prevent rust formation and corrosion, thereby reducing maintenance costs and extending service life.
Several industries, including construction, automotive, and manufacturing, utilize zinc coatings extensively. Understanding the mechanisms behind these coatings is essential for researchers and industry professionals alike, as it allows for more informed decisions regarding material selection and application. \nMoreover, advancements in paint formulations, application techniques, and environmental considerations continue to shape the landscape of zinc coating technology.
Literature Review
The body of research on zinc coating has expanded over recent decades, reflecting its growing importance. A plethora of studies focus on the effectiveness of zinc as a sacrificial anode, supported by extensive testing and empirical data. Trends in literature highlight innovative formulations that incorporate additional compounds to enhance performance.
Recent findings indicate that certain zinc coatings exhibit superior adhesion properties and higher durability compared to traditional methods. For example, researchers have examined the influence of polymer composites in zinc coating formulations, resulting in enhancements in corrosion resistance and overall performance.
"The application of zinc coatings has proven to be an invaluable strategy for combating corrosion, extending the lifespan of crucial materials across various sectors."
Overall, an extensive review of literature not only underscores the effectiveness of zinc coating paint but also fosters a deeper understanding of its applications and benefits. The combination of theoretical insights and practical implications offers valuable knowledge for both practitioners and researchers in the field.
This research context establishes a strong foundation for further exploration into the methodology utilized in studying zinc coating paints, allowing a seamless transition to subsequent sections that detail its applications and advancements.
Foreword to Zinc Coating Paint
Zinc coating paint plays a crucial role in various industries by offering significant protection against corrosion. The need for such protective measures can be seen in both everyday products and large structures. With its unique properties, zinc coating paint effectively safeguards metals from environmental damage. This article delves into the importance of understanding zinc coating paint, focusing on its fundamental aspects, benefits, and considerations.
Definition and Purpose
Zinc coating paint is a specialized protective finish that incorporates zinc as a primary ingredient. Its primary purpose is to prevent corrosion by creating a barrier that inhibits moisture and air from reaching the underlying metal. This type of coating provides both galvanic and barrier protection, which collectively enhance metal durability. The application of zinc coating paint is vital in environments where metal surfaces are exposed to harsh conditions, such as moisture or salt. This makes it particularly valuable in industries like construction and automotive, where rust and deterioration can lead to costly repairs or replacements.
Historical Context
The use of zinc as a protective material dates back several centuries. Historically, zinc was first utilized in the 18th century for galvanization processes, which laid the groundwork for modern zinc coating paint. Over time, advancements in paint formulations and application techniques significantly improved the efficacy and durability of zinc coatings. The industrial revolution further propelled the demand for solutions to combat corrosion, leading to wider adoption in various sectors. Today, zinc coating paint is not just a practical choice; it is considered an industry standard for prolonging the lifespan of metal assets, reflecting an evolution driven by both necessity and innovation.
Composition of Zinc Coating Paint
The composition of zinc coating paint is crucial to its effectiveness and performance across various applications. Understanding these components allows users to appreciate how they contribute to the paint's protective properties. Zinc coating paint typically consists of a blend of core ingredients, supplemented by specific additives designed to enhance functionality. This section explores these elements in detail, highlighting their roles and significance in achieving desired outcomes in corrosion protection.
Core Ingredients
Core ingredients in zinc coating paint primarily include zinc dust, a resin binder, and solvents.
- Zinc Dust: This is the fundamental component, providing cathodic protection against corrosion. When zinc is exposed to moisture, it reacts, sacrificing itself and thus protecting the underlying metal substrate. The zinc particles are finely milled to ensure effective coverage and distribution in the paint. This ensures optimum performance, especially in high-exposure environments.
- Resin Binder: The binder is essential for adhesion and film formation. Various types of resin such as epoxy or polyester can be used, depending on the desired characteristics. This component ensures that the paint adheres well to surfaces and provides a durable finish.
- Solvents: Solvents act to dissolve other components and facilitate application. They must be chosen to balance evaporation time and ease of application. Selecting the right solvents can also minimize environmental impact, aligning with contemporary sustainability efforts.
The combination of these core ingredients not only influences the paint’s protective qualities but also its durability and application properties.
Additives and Their Functions
In addition to core ingredients, various additives play significant roles in enhancing zinc coating paint. These additives can be categorized based on their functions:
- Thickeners: Thickeners modify the viscosity of the paint, ensuring proper application without sagging. They help maintain consistency, leading to optimal coverage and finish.
- Pigments: While zinc serves as the primary protective agent, pigments add color and aesthetic appeal. They can also contribute to UV resistance, preventing degradation due to sunlight exposure.
- Anti-settling Agents: These additives ensure that zinc particles remain evenly distributed in the paint, preventing settling over time. This feature is critical for maintaining consistent performance throughout the product's lifespan.
- Biocides: To combat mold and mildew growth, certain biocides are included. This is especially important for coatings applied in humid or wet environments where biological growth is likely.
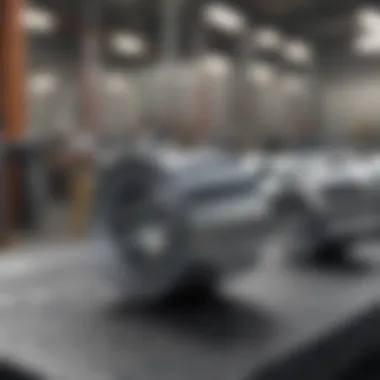
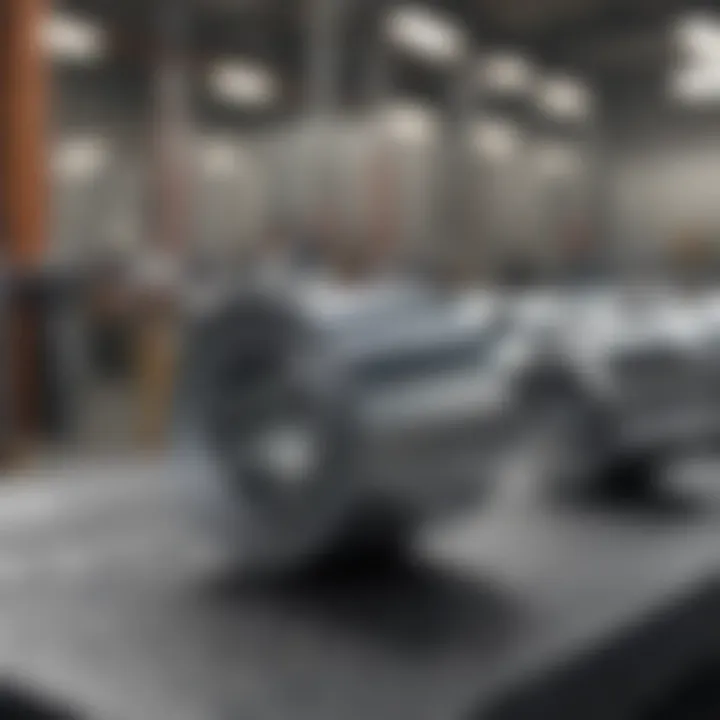
Understanding the composition of zinc coating paint—its core ingredients, and the additional benefits provided by additives—enables industries and professionals to select the right formulation for specific applications. Every element plays a role in ensuring that the protective characteristics of the paint deliver reliable performance under varied conditions.
"Zinc coating paint offers significant corrosion resistance, making it indispensable in industrial applications—not just for protection, but as a long-term investment in asset durability."
This knowledge aids in optimizing choices, from industrial coatings to consumer products, ensuring effective and sustainable usage.
Mechanism of Protection
The mechanism of protection provided by zinc coating paint cannot be overstated. This fundamental aspect forms the backbone of its effectiveness in combating corrosion, which is crucial for the longevity of various materials. Understanding this mechanism enlightens professionals on why zinc coating is a preferred choice across numerous industries. This section will detail both galvanic protection and barrier protection, shedding light on their individual contributions to corrosion resistance.
Galvanic Protection
Galvanic protection is a critical feature of zinc coating paint. It is based on the principle of electrochemistry. When zinc is exposed to the environment, it acts as an anode in a corrosive cell, sacrificing itself to protect the underlying metal, usually steel or iron. This process can be particularly vital in areas facing severe environmental stress.
When zinc corrodes, it forms a protective zinc oxide layer that effectively shields the base metal from exposure to moisture and other corrosive elements. This property makes zinc an attractive option in several applications, particularly in the automotive and construction sectors where metal components are frequently subjected to harsh conditions.
"Zinc's role as a sacrificial anode makes it an essential material in preventing rust and corrosion."
The effectiveness of galvanic protection can vary based on several factors, including the environment and the type of substrate it is applied to. It is important to note that although zinc can effectively protect various metals, the full protection relies on adequate application and maintenance of the coating. Deterioration of zinc over time necessitates regular inspections and, if necessary, reapplication to maintain this critical protective layer.
Barrier Protection
Barrier protection serves as an additional layer of defense that complements galvanic protection. It functions primarily by separating the substrate from direct contact with atmospheric elements such as oxygen and water that contribute to corrosion. Zinc coating paint achieves this through its physical properties, creating a solid, impermeable layer on the surface of the metal.
This type of protection is particularly applicable in environments where conditions are less aggressive, but the risk of corrosion remains. The layer formed by the zinc acts as a shield, preventing moisture ingress and consequently reducing the rate of corrosion significantly.
Unlike galvanic protection, barrier protection does not involve electrochemical processes. Its effectiveness can depend heavily on the thickness and integrity of the coating. Poor application methods or damaging impacts to the coating can compromise this protective state, leading to premature corrosion. Thus, regular adherence to proper maintenance and inspection routines is essential to ensure that the barrier remains intact.
Applications of Zinc Coating Paint
The applications of zinc coating paint are vast and varied, offering significant benefits in multiple industries. Understanding these practical uses not only showcases its versatility but also emphasizes its role in enhancing durability and resistance to corrosion. Zinc coating paint serves as a protective layer, extending the life of materials it covers while reducing maintenance costs. The relevance of this section lies in its exploration of how zinc coating paint is being utilized in various sectors, which is key to grasping its overall impact and significance.
Industrial Uses
Within the industrial sector, zinc coating paint is applied extensively to prevent corrosion on metal components. Industries such as manufacturing, energy generation, and heavy machinery are among the primary users. The need for robust protection in environments where equipment is exposed to moisture, chemicals, and other corrosive elements drives this application. For example, equipment used in coal and gas plants often utilizes zinc-coated materials to resist degradation over time. Additionally, machinery found in manufacturing plants frequently experiences wear; therefore, applying zinc coating minimizes repair costs.
"Zinc coating paint has become a staple in industrial applications, ensuring longer life spans for vital machinery."
Automotive Industry
The automotive industry heavily relies on zinc coating paint for enhancing vehicle longevity and performance. Automakers apply these coatings to various components, including body panels and frame parts, to guard against rust and environmental damage. This application is especially important in regions with high humidity or salted roads, which can accelerate corrosion. By using zinc coatings, manufacturers are able to significantly improve the durability of vehicles while reducing warranty claims related to corrosion issues. Furthermore, the aesthetic appeal of zinc-coated surfaces, which can be painted over, allows for a balance between functionality and appearance.
Construction and Infrastructure
In construction, zinc coating paint plays a critical role in protecting structural elements such as steel beams, bridges, and scaffolding. The strength and integrity of these structures rely on effective corrosion resistance. By applying zinc coating, construction professionals create a protective barrier, prolonging the life of materials exposed to environmental factors. Projects using zinc-coated materials often see reduced replacement costs, enhancing overall project efficiency and sustainability. In urban settings, where pollution can increase oxidation, the use of zinc coating increasingly becomes a preferred choice, ensuring that public infrastructure remains safe and reliable over time.
Marine Applications
The marine environment is particularly harsh on materials, leading to accelerated corrosion for vessels and structures. Zinc coating paint is widely utilized in this field to protect ships, docks, and offshore platforms. By preventing corrosion caused by saltwater, zinc coatings significantly extend the longevity of marine assets. These coatings provide cathodic protection, which is essential in avoiding the deterioration often seen in metal structures. The understanding of how zinc coating interacts with seawater chemistry is critical for industries that seek durability and optimized performance in marine applications.
In summary, the applications of zinc coating paint are essential across various sectors. The significance of its usage in industrial areas, the automotive industry, construction, and marine environments is paramount not only for efficiency and aesthetic value but also for ensuring sustainability and long-term investment. The ongoing advancements in zinc coating technology continue to unlock new possibilities for its application, making it a focal point in corrosion resistance strategies.
Benefits of Zinc Coating Paint
Zinc coating paint offers several advantages that make it a compelling choice for various applications. Its significance in protecting materials from corrosion cannot be overstated. This protection enhances the longevity of structures and components, ultimately leading to substantial cost savings over time. In this section, we will explore the key benefits of zinc coating paint in detail.
Corrosion Resistance
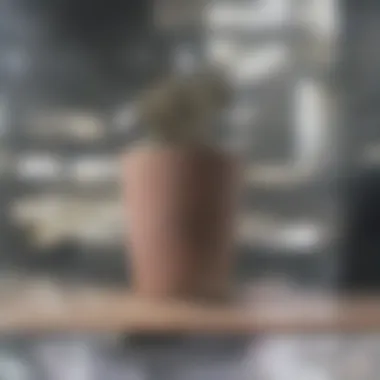
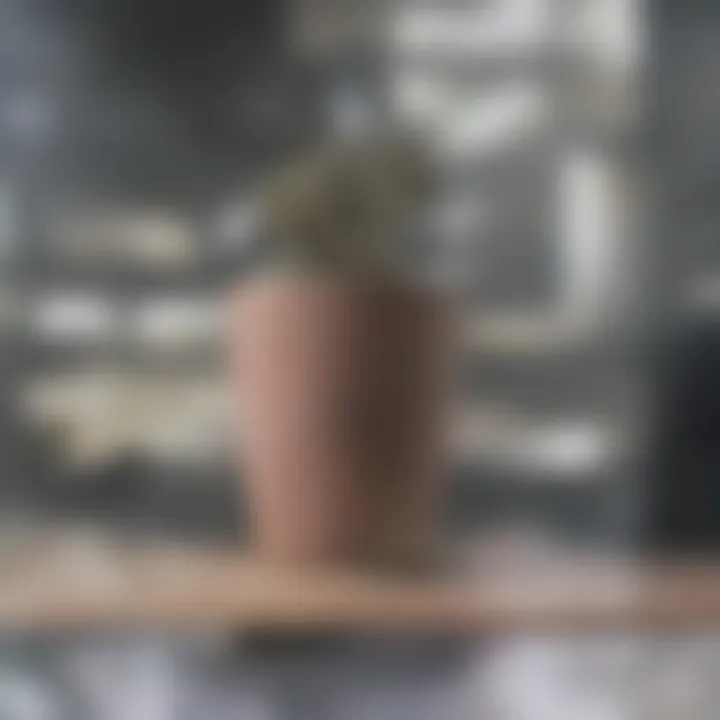
One of the standout benefits of zinc coating paint is its exceptional corrosion resistance. Zinc acts as a sacrificial anode, meaning it corrodes preferentially when exposed to oxidative environments. This property ensures that the underlying metal substrate remains protected. This quality is particularly advantageous in harsh environments such as coastal areas or industrial settings where exposure to moisture and corrosive substances is common.
"Zinc provides an electrochemical protection mechanism that prolongs the life of the substrate."
This resistance is not only a result of the sacrificial nature of zinc but also due to a protective barrier that zinc paint forms against moisture and oxygen. Over time, this significantly reduces the chances of rust formation, making zinc coating paint a vital choice for structural integrity in steel, aluminum, and iron applications.
Durability and Longevity
Zinc coating paint is well-known for its durability. The paint forms a robust layer that withstands physical abrasion and impacts. This ability to endure wear makes zinc coatings reliable in various industrial applications, including automotive and construction. Moreover, zinc’s resistance to UV degradation ensures that the coating remains intact even when exposed to sunlight for extended periods.
The longevity of zinc coatings translates into fewer maintenance interventions. Reapplication frequency is reduced, allowing industries to save on labor and material costs. As a result, structures coated with zinc paint can serve their intended purpose over many years, reducing the resources required for repairs.
Cost-Effectiveness
From an economic perspective, zinc coating paint presents a cost-effective solution for protecting metals. While the initial application cost may be higher than some conventional paints, the long-term savings are significant. The prevention of corrosion leads to lower repair and replacement costs, which can accumulate substantially over time.
When considering maintenance budgets, investing in zinc coating paint often pays off. Its longevity reduces the need for frequent reapplications, while the diminishing risk of corrosion-related failures provides peace of mind to asset managers and engineers alike. Cost analysis consistently showcases that the lifespan and performance of zinc coatings justify the initial expenditure, making it a wise financial choice in various sectors.
Challenges and Limitations
Understanding the challenges and limitations of zinc coating paint is essential for industries that rely on this protective technology. Despite its wide applications and benefits, using zinc-based coatings comes with specific concerns that need addressing. These challenges influence how effectively zinc coatings can be deployed in various settings and dictate the need for ongoing advancements in technology.
Environmental Concerns
Environmental impacts play a significant role in the discussion around zinc coating paint. One primary concern revolves around the release of zinc compounds into the ecosystem. When zinc coatings deteriorate, they can leach into soil and waterways, potentially leading to toxicity in aquatic systems. Some studies suggest that elevated zinc levels can harm aquatic life, causing toxicological effects that disrupt local ecosystems.
Additionally, the production process of zinc coating paints often involves chemicals and processes that may not be environmentally friendly. The mining of zinc ore generates waste and can contribute to land and water pollution if not managed properly. Regulatory scrutiny has increased over the years, prompting manufacturers to reconsider their practices. Efforts to introduce eco-friendly alternatives that minimize environmental footprints have become popular. Sustainable practices are needed to reconcile the benefits of zinc coatings with ecological responsibility.
Application Issues
The application of zinc coating paint is not always straightforward. Issues can arise due to surface preparation, method of application, and environmental conditions during the coating process. For one, improper surface preparation can lead to poor adhesion of the paint, resulting in premature failure of the coating. Surfaces must be clean and free of rust, grease, or oil for optimal results. Without rigorous cleaning protocols, the integrity of the zinc coating compromises.
Furthermore, the method of application matters significantly. Spray application might produce uneven coatings if the technician lacks experience. This could lead to thin spots where corrosion might more readily occur. On the other hand, brushing or rolling may not provide the same level of coverage, affecting the overall performance of the protective layer.
Lastly, environmental conditions like humidity and temperature during application are critical. High humidity can complicate the curing process, while low temperatures might slow down the drying time, diminishing the coating's durability. Adhering to manufacturer guidelines and industry best practices can mitigate these application issues, but it requires diligence and expertise from the applicators.
Addressing these environmental and application challenges is crucial for the effective use of zinc coating paint, ensuring it serves its purpose without causing additional harm to ecosystems.
Advancements in Zinc Coating Technology
The advancement of zinc coating technology is crucial in enhancing the effectiveness and applicability of zinc coatings across various industries. Innovations in materials and application methods have emerged to address the increasing demands for durability and sustainability in coating solutions. Understanding these advancements helps stakeholders make informed decisions crucial for maintaining the integrity of metal structures, reducing maintenance costs, and improving environmental outcomes.
Nano-Zinc Coatings
Nano-zinc coatings represent a significant leap forward in zinc painting technology. These coatings utilize nanoscale particles which enhance properties such as adhesion, corrosion resistance, and UV protection. The smaller particle size achieves a higher surface area, allowing for stronger bonds with the substrate material.
Some benefits of nano-zinc coatings include:
- Enhanced Corrosion Resistance: The nanomaterials provide a barrier that is more effective in preventing moisture and corrosive substances from reaching the underlying metal.
- Improved Durability: Nano-zinc coatings exhibit better wear resistance, extending the lifespan of the paint compared to traditional coatings.
- Lower Environmental Impact: The application process is more efficient, often requiring thinner layers, which reduces material consumption and waste.
These features make nano-zinc coatings increasingly popular in environments that expose structures to harsh conditions, such as coastal or industrial settings.
Eco-Friendly Alternatives
With rising environmental concerns, the coating industry is shifting toward eco-friendliness. Various innovations aim to create zinc coatings less harmful to the environment while maintaining effectiveness.
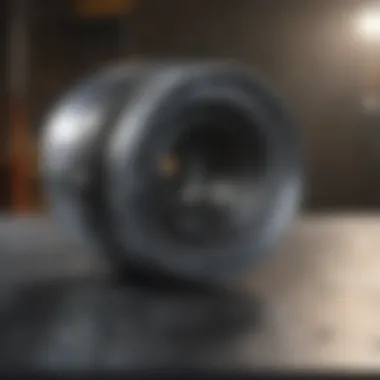
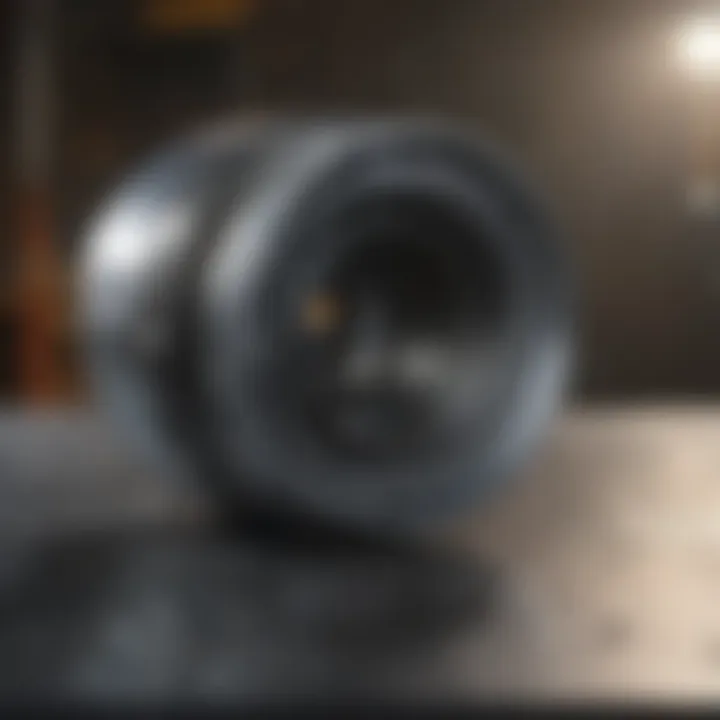
Some eco-friendly alternatives in zinc coating technology are:
- Water-Based Zinc Coatings: These coatings replace traditional solvents with water as a carrier, significantly reducing volatile organic compounds (VOCs) emissions.
- Bio-Based Additives: Natural ingredients can be incorporated into formulations, enhancing performance without the environmental impact of synthetic chemicals.
- Recyclable and Biodegradable Options: New technologies focus on creating coatings that decompose naturally or can be safely recycled at the end of their lifespan.
As regulations tighten globally regarding environmental safety, the development of eco-friendly zinc coatings will not only cater to compliance but also offer a competitive advantage in the marketplace.
"Advancements in zinc coating technology pave the way for sustainable practices in metal protection, ensuring a balance between functionality and environmental responsibility."
Regulatory Standards and Compliance
The application of zinc coating paint is influenced significantly by various regulations. Compliance with these regulations not only ensures safety but also contributes to the effective use of zinc coatings in different industries. Understanding regulatory standards is essential for manufacturers and users alike, as these guidelines shape the industry practices, dictate material properties, and impact environmental safety.
Overview of Regulations
Various regulatory bodies oversee the standards governing the use of zinc coating paint. In the United States, the Environmental Protection Agency (EPA) sets stringent regulations regarding the emission of volatile organic compounds (VOCs) from paint products. Similar regulations exist in Europe and Asia. The presence of heavy metals, such as lead and cadmium, is tightly regulated under laws like the Toxic Substances Control Act and the European Union REACH regulations. These laws aim to minimize hazardous materials while promoting safe practices in paint manufacturing and application.
In addition to environmental regulations, safety standards from organizations like the American National Standards Institute (ANSI) and Occupational Safety and Health Administration (OSHA) ensure that the application process is safe for workers. These safety regulations cover personal protective equipment (PPE) requirements and expose the need for proper ventilation in application areas, safeguarding users from health risks associated with inhaling toxic fumes.
Compliance Challenges
Despite the well-defined regulations, achieving compliance can be challenging for manufacturers. One major challenge is keeping up with changing regulations in different regions. Laws may vary significantly between countries, making it necessary for companies to adapt their formulations and practices accordingly. This variability can complicate supply chain management and increase operational costs.
Another significant hurdle is the testing and validation process required to meet regulatory standards. Paint manufacturers often face lengthy approval processes, which can delay product launches. Compliance with the regulations may demand additional resources that not all companies can afford. The testing for heavy metals, VOCs, and other hazardous components is not only expensive but can also be time-consuming.
Companies must also foster a culture of compliance among their employees. Continuous training and awareness programs are imperative to ensure that all aspects of the operation align with safety standards. This requires a commitment to regular evaluations and updates in both personnel training and production techniques.
Compliance with regulations is not only about avoiding penalties; it is about fostering trust with customers and the community.
Future Directions for Zinc Coatings
In today's rapidly evolving industrial landscape, the future of zinc coatings holds immense potential. Understanding where zinc coating technology is heading ensures relevance in fields such as construction, automotive, and marine industries. As these sectors seek improved solutions for corrosion resistance and sustainability, advancements in zinc coatings will play a critical role.
Research and Development Opportunities
The continual need for innovative materials drives research and development in zinc coatings. Areas of exploration include:
- Enhanced Performance: Researchers aim to increase the longevity and effectiveness of zinc coatings through advanced formulations that resist wear and corrosion even under extreme conditions.
- Hybrid Coating Systems: Combining zinc with other protective coatings could lead to hybrid systems that utilize the unique properties of each material, providing superior protection.
- Bio-based Additives: Investigating natural additives may offer environmentally friendly alternatives while maintaining strength and protective mechanisms.
"Research into zinc coating enhancements can significantly reduce maintenance costs in various sectors."
These advancements not only promise better performance but also the potential to reduce ecological impacts. As new methods emerge, industries will have access to coatings that are increasingly efficient and sustainable.
Market Trends
The market for zinc coatings is also adapting to changing demands and technological trends. Key factors influencing the market include:
- Sustainability: As companies aim to decrease their carbon footprint, the demand for eco-friendly zinc coatings is rising. Manufacturers are responding with formulations that use less harmful chemicals.
- Technological Integration: The incorporation of smart technologies, such as sensors embedded in coatings for real-time monitoring of corrosion, is becoming significant. These advancements allow for proactive maintenance strategies, optimizing performance.
- Global Market Growth: Emerging economies are witnessing a surge in construction and infrastructure developments. This leads to increased opportunities for zinc coatings due to their proven effectiveness in protecting structures.
Zinc coatings will remain crucial in various applications, driven by innovation and changing market dynamics. Keeping abreast of these trends will be important for industry stakeholders as they navigate new challenges and opportunities.
Culmination
Zinc coating paint serves a crucial role in various industrial applications and contributes significantly to corrosion resistance. This article has examined the multifaceted aspects of zinc coatings, highlighting their composition, mechanism of protection, benefits, and challenges. Understanding these key elements is essential not only for scientists and engineers but also for industry stakeholders who rely on durable and effective protective solutions.
Summary of Key Points
- Composition: Zinc coating paint typically consists of zinc dust or flakes, resins, and various solvents. The combination of these ingredients allows for effective adhesion and durability.
- Mechanism of Protection: The dual mechanism includes galvanic protection, where zinc acts as a sacrificial anode, and barrier protection that prevents moisture and corrosive agents from reaching the substrate.
- Applications: Zinc coating paint is widely used in industries such as automotive, construction, and marine. Each sector benefits from the protective nature of zinc paints, ensuring longevity of materials.
- Benefits: Key benefits include superior corrosion resistance, enhanced durability, and overall cost-effectiveness. These attributes make zinc coatings a preferred choice in many applications.
- Challenges: Despite the many benefits, there are environmental concerns regarding the use of zinc and application issues that must be addressed for sustainable use.
- Future Directions: The exploration of nano-zinc coatings and eco-friendly alternatives indicates a shift towards safer and more efficient zinc coating technologies.
Implications for Industry
The implications for industry are profound. Zinc coating paint not only prolongs the life of materials but also reduces maintenance costs over time. As industries face increasingly stringent regulations regarding environmental impact, adopting advanced zinc coatings can assist in compliance while providing unmatched protection against corrosion. The ability to choose from new technologies, like nano-zinc formulations, offers an opportunity for improved performance and sustainability.
Ultimately, the effective use of zinc coating paint can lead to safer and more efficient operational practices, aligning with emerging market trends that prioritize environmental and economic resilience. By keeping up with advancements in zinc technology, industries will remain competitive and capable in addressing the challenges of corrosion in diverse settings.